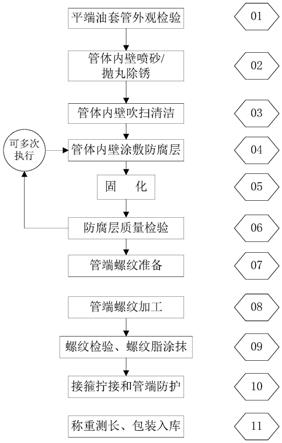
[0001]
本发明属于油套管内防腐领域,涉及一种油套管内防腐涂敷工艺。
背景技术:[0002]
油套管及其他井下管柱构件(如钻杆)以碳钢和低合金钢为主,腐蚀是造成其功能降低或失效的主要原因之一。油套管等产品的腐蚀主要发生在两个环节:第一类是在运输和储存过程中的大气环境腐蚀,尤其是在高温、高湿、高盐环境;第二类是在应用环境中的腐蚀性介质(如h2s、co2和srb等)腐蚀。油套管的腐蚀损坏轻者造成生产作业的迟滞、停顿,重者将导致油气井的报废等重大经济损失和严重的环境破坏事故。由于油套管内壁往往需要长期接触各种腐蚀介质,内壁腐蚀尤为普遍、严重,内防腐则显得更为迫切、重要。
[0003]
目前,油套管内涂层防腐是业界普遍采用的经济、有效的内防腐方式。形成了较为成熟的内防腐涂敷工艺,甚至有了行业规范,如sy/t 6717《油管和套管内涂层技术条件》。该传统方法采取的工艺路线为:成品油套管入厂检验
→
卸除两端螺纹保护帽
→
清洗现场端螺纹脂
→
两端安装临时螺纹保护帽
→
内壁喷砂除锈
→
内壁吹扫清洁
→
内壁涂敷防腐层
→
烘干固化(若需要)
→
防腐层质量检验
→
卸除临时螺纹保护帽
→
现场端螺纹清洁、检查
→
现场端螺纹脂重新涂抹
→
两端螺纹保护帽重新安装。该工艺路线实现了油套管内涂层的涂敷要求,但螺纹保护帽的反复装卸、螺纹脂的反复清洗和涂抹等繁琐工序不仅造成工艺复杂、成本居高,而且效率低下,差错率高(主要是人工实施)。更为重要的是,尽管在喷砂和涂敷阶段,油套管两端安装有临时螺纹保护帽,但细小砂粒的强穿透性经常导致砂粒嵌入螺纹牙隙内,对后续的人工清理和检查螺纹提出了很大的挑战,一旦有砂粒未被及时清理,则会对后续的油套管连接和密封造成极大地威胁,后果严重!由于上述诸多大大限制了油套管内涂层防腐工艺的实际应用,尤其是耐高温涂料的油套管内涂敷以及用于储存运输过程中低端防腐材料的油套管内涂敷。
[0004]
因此,如何通过合理的优化、简化涂敷工艺,达到有效提高涂敷效率、降低涂敷成本,降低甚至避免次生质量风险、改善涂敷质量,则成为目前的关键油套管内防腐研究的关键。
技术实现要素:[0005]
针对现有技术的不足,本发明的目的在于提供一种流程简单、油套管次品产生概率低的油套管内防腐涂敷工艺。该工艺能够很好的适用于耐高温防腐涂料的油套管内涂敷,并低价实现临时储存及运输用等低端涂料的油套管内涂敷。
[0006]
为了实现上述目的,本发明提供了一种油套管内防腐涂敷工艺,该工艺包括如下步骤:
[0007]
1)将平端油套管(即未进行螺纹加工的油套管)进行将平端油套管进行内壁清洁处理;所述油套管包括油管和套管中的至少一种;
[0008]
2)所述油套管进行内壁吹扫清洁后进行管体内壁防腐层涂敷处理及防腐层固化
处理;
[0009]
3)所述油套管进行管体内壁防腐层涂敷处理及防腐层固化处理后进行油套管管端螺纹加工;在进行螺纹加工过程中,以摄氏度计,螺纹加工部位内壁最高温度不超过管体防腐层耐温上限值的90%;螺纹加工所用切削液不伤害油套管内壁涂敷的防腐层;
[0010]
4)所述油套管进行油套管管端螺纹加工后进行接箍拧紧和管端保护,完成整个油套管内防腐涂敷工艺。
[0011]
在上述油套管内防腐涂敷工艺中,优选地,所述平端油套管在进行内壁清洁处理前,先进行外观检查,所述外观检查包括检查油套管管体是否存在损伤、油套管内壁是否存在污垢和油套管内壁是否存在异物;如果油套管管体存在损伤,则该油套管不再进行后续步骤;如果油套管内壁存在污垢,则进行污垢清理;如果油套管存在异物,则进行异物清除;所述损伤可以包括磕碰损伤、凹坑损伤、划伤损伤、弯曲损伤中的至少一种,但不限于此;所述污垢可以包括油污,但不限于此;所述异物可以包括嵌入型氧化皮,但不限于此。
[0012]
在上述油套管内防腐涂敷工艺中,优选地,所述内壁清洁处理包括内壁除锈处理和内壁吹扫清洁。
[0013]
在上述油套管内防腐涂敷工艺中,在进行内壁除锈处理时,优选地,当待涂敷的防腐层为临时储存用防腐层时,所述内壁除锈处理通过手工和动力工具除锈中的至少一种实现,例如可根据涂层要求和涂料性能采用钢刷等动力工具除锈;更优选地,所述内壁除锈处理的除锈等级不低于gb/t 8923.1和/或iso 8501-1中的st 2.0。
[0014]
在上述油套管内防腐涂敷工艺中,在进行内壁除锈处理时,优选地,当待涂敷的防腐层为除临时储存用防腐层外的其他防腐层时,所述除锈处理通过喷砂除锈和抛丸除锈中的至少一种实现;更优选地,所述内壁除锈处理的除锈等级不低于gb/t 8923.1和/或iso 8501-1中的sa 2.5。除锈用磨料(如喷砂除锈所有砂、抛丸处理所用丸)应当保持干净无杂物。在进行喷砂除锈和/或抛丸除锈时,磨料应当按照合适的频率进行添加及更换,当磨料同时包括砂及丸时应当保持合适的砂丸比。
[0015]
在上述油套管内防腐涂敷工艺中,在进行内壁吹扫清洁时,优选地,当待涂敷的防腐层为临时储存用防腐层时,所述内壁吹扫清洁后的灰尘度满足gb/t 18570.3和/或iso8502-3的2级以上的要求即满足gb/t 18570.3和/或iso8502-3的2级要求或更高标准的要求。
[0016]
在上述油套管内防腐涂敷工艺中,在进行内壁吹扫清洁时,优选地,当待涂敷的防腐层为除临时储存用防腐层外的其他防腐层时,所述内壁吹扫清洁后的灰尘度应满足gb/t 18570.3和/或iso8502-3的1级以上的要求即满足gb/t 18570.3和/或iso8502-3的1级要求或更高标准的要求。
[0017]
在上述油套管内防腐涂敷工艺中,在进行内壁吹扫清洁时,所述内壁吹扫清洁可以通过利用压缩空气吹扫油套管的管体内壁的方式实现,但不限于此。
[0018]
在上述油套管内防腐涂敷工艺中,优选地,油套管进行管体内壁防腐层涂敷处理在返锈前进行,一般要求除锈处理至涂敷的间隔时间不超过4小时(根据温湿度可进行调整)。
[0019]
在上述油套管内防腐涂敷工艺中,在进行管体内壁防腐层涂敷处理时,通常在满足喷涂环境要求的情况下,根据防腐层涂层技术要求和防腐层涂料特性设置喷涂参数,进
行管体内防腐涂敷作业。涂敷过程优选定期对参数进行监控,更有利于确保喷涂参数合格。当在油套管管体内壁涂敷的防腐层不为耐高温防腐层时,涂敷温度优选为不高于200℃;当在油套管管体内壁涂敷的防腐层为耐高温防腐层时,在进行防腐层涂敷处理时,可以先对油套管管体进行预热,然后再进行防腐层的涂敷,其中预热温度优选为不低于260℃,涂敷温度优选为220-250℃或不低于涂料玻璃转化温度加20℃(即涂敷温度优选为220-250℃或不低于第一温度,涂料玻璃转化温度加20℃即为第一温度)。
[0020]
在上述油套管内防腐涂敷工艺中,根据需要,在进行防腐层涂敷时可进行多遍多层涂敷,各层的涂料和涂敷参数根据需要具体确定,每遍或每层涂敷后可以根据需要进行固化。根据防腐层要求和防腐涂料性能特点,在每遍和/或每层和/或所有层涂敷完成后,可安排全管体进入固化炉进行高温固化或在空气中静置进行常温固化。
[0021]
在上述油套管内防腐涂敷工艺中,优选地,所述油套管在进行管体内壁防腐层涂敷处理及固化处理后,在油套管管端螺纹加工前,进行防腐层质量检验,当油套管的防腐层质量检验合格时,油套管进行后续油套管管端螺纹加工,当防腐层质量检验不合格时,油套管重新进行管体内壁防腐层涂敷处理及防腐层固化处理;所述防腐层质量检验可以包括进行是否存在漏涂、真空、流挂等缺陷的检查以及防腐层厚度是否合格的检查,但不限于此。进行防腐层质量检验,可以通过本领域技术人员所知晓的检验方法;判断防腐层质量检验合格的标准可以为本领域技术人员所知晓的判断防腐层是否合格的标准。在进行防腐层质量检验过程中,由于油套管管端为平端没有螺纹及接箍,极大的增加了检验的便捷性、可靠性。
[0022]
在上述油套管内防腐涂敷工艺中,优选地,在进行管端螺纹加工时,在油套管的管端内部加装防护塞(即防护堵头),所述防护塞用以避螺纹加工过程中的切屑进入油套管管体内部损伤防护层。在传统工艺中,管端螺纹加工过程中的切屑带来的管体内部划伤以及有这些切削在管体内部沉积导致的诸多问题从未被本领域技术人员正式,本发明利用防护塞有效避免了切屑进入罐体内部,有利于保证最终制品的低次品率。
[0023]
在上述油套管内防腐涂敷工艺中,优选地,所述防护塞由柔性材料制备得到;更优选地,所述柔性材料为橡塑;例如,可以采用聚四氟乙烯制作该防护塞。
[0024]
在上述油套管内防腐涂敷工艺中,优选地,所述防护塞包括位于后端的密封部和位于前端的摩擦部,所述密封部用于与油套管内壁密封贴合,所述摩擦部用于与油套管内壁卡接。
[0025]
在一优选实施方案中,所述密封部上还开有把手,所述把手设置于所述密封部的后端;更优选地,所述密封部在把手设置部位设有凹槽以便于把手的手握和/或使用工具进行防护塞的拆卸。在防护塞的使用过程中,为避免对外部螺纹加工以及其他工序的干扰,可以适当将防护塞深入油套管端面0.5cm-1cm,为方便防护塞从油套管中取出,可以设置把手;把手的位置可以设置在从油套管外部便于发现并接触的位置。例如将把手开设在密封部的尾部,且设置在密封部端面中心处。另一方面密封部和油套管内壁产生过盈配合,把手的开设还可以进一步考虑便于与把手适配的置入和取出共聚的使用,以方便防护塞的使用,例如在把手设置位置设置合适的凹槽。
[0026]
在一优选实施方案中,所述密封部为圆柱形,所述密封部的外壁用于与油套管内壁贴合。
[0027]
在一优选实施方案中,所述摩擦部上设置有倒齿形结构;更优选地,所述倒齿形结构具有m个倒齿,所述倒齿的齿顶用于与油套管内壁接触;m为大于1的正整数;其中所述倒齿形结构的齿顶圆直径优选等于所述密封部的直径。倒齿形结构,即方向为与油套管延伸方向相反的锯齿形结构。倒齿的数量可以根据工作所需摩擦强度确定,例如倒齿形结构具有4个倒齿。倒齿的齿顶接触油套管内壁,通过倒齿齿隙中的气压,以及倒齿与油套管内壁线接触产生的摩擦力增大防护塞与油套管内壁的摩擦。
[0028]
在一优选实施方案中,所述摩擦部上设置有螺纹形结构;更优选地,所述螺纹形结构的表面螺旋线用于与油套管内壁接触;进一步优选地,所述螺纹形结构的外径等于所述密封部的直径。螺纹结构的螺距可以根据工作所需摩擦强度确定。螺纹的表面螺旋线接触油套管内壁,通过螺纹之间的气压,以及螺纹与油套管内壁线接触产生的摩擦力增大防护塞与油套管内壁的摩擦。
[0029]
倒齿形结构或螺纹结构的设计,在减小密封部与油套管内壁因圆度不同产生过大摩擦的同时,保证防护塞的摩擦强度。
[0030]
在一优选实施方案中,所述密封部与所述摩擦部一体成型。因油套内部真实情况的原因,拔出和塞入油套管时密封部与摩擦部的受力不同且均较大,若采用分别制造后连接的方法,较易造成防护塞的损坏,且不方便制造,故密封部与摩擦部较佳被设置为一体成型。
[0031]
在实际应用中,油套管横截面的实际形状并非完整的圆,其具有一定的圆度公差,在将密封部放入油套管内部时会因为圆度不同难以配合,进而产生过大的摩擦力;故横截面为完整的圆的密封部可以设计得较短,以减小不同圆度带来的过大摩擦力;并且在防护塞的前端设置变形程度较强,产生摩擦力较大的摩擦部,进而保证防护塞的隔离质量。
[0032]
在上述油套管内防腐涂敷工艺中使用上述防护塞,通过密封部与油套管内壁的过盈配合,以及摩擦部与油套管内壁产生的静摩擦力,在油套管进行螺纹加工过程中对于油套管内部空间与外部环境进行了较好的隔离效果,防止油套管进行螺纹加工时产生的切屑进入油套管内部划伤已经涂敷的防腐涂层,影响防腐涂层的防腐效果。
[0033]
在上述油套管内防腐涂敷工艺中,在进行螺纹加工过程中,以摄氏度计,螺纹加工部位内壁最高温度不超过管体防腐层耐温上限值的90%,可以通过优化管螺纹成型刀具切削的温度控制方案如切削速度、切削量控制,优化切削液配方等方式实现;具体可采用常规切削过程中控制切削温度的方式来实现螺纹加工部位内壁最高温度不超过管体防腐层耐温上限值的90%。可以通过试验,建立起不同规格的油套管不同最高温度的切削控制参数系列(切削速度、最大切削量),采用水基切削液既避免损伤涂层又可快速带走热量。螺纹加工部位内壁最高温度不超过管体防腐层耐温上限值的90%,能够更好的保护防腐层,更有利于保证最终成品的高质量、低次品率。
[0034]
在上述油套管内防腐涂敷工艺中,优选地,各尺寸油套管螺纹加工过程中的切削速度、单次切削量、切削液配方控制如下表1:
[0035]
表1
[0036]
油套管尺寸(mm)切削速度(rpm)单次最大切削量(mm)切削液≥60.32,<168.2855-155首刀:0.3,末刀:0.1全合成水基型≥168.28,<298.4530-60首刀:0.4,末刀:0.2全合成水基型
≥298.45,<406.4020-35首刀:0.5,末刀:0.2全合成水基型≥406.4,<508.0016-25首刀:0.5,末刀:0.2全合成水基型
[0037]
其中,油套管尺寸指油套管外径。
[0038]
在上述油套管内防腐涂敷工艺中,在进行管端螺纹加工过程中,除了做好温度控制外,还应当做好切屑的清理和防护工作,避免因为切屑导致损伤已经涂敷的防腐层的机械损伤;当防腐层不具有一定机械损伤自修复功能时,优选在油套管的管端内部加装防护塞,所述防护塞用以避螺纹加工过程中的切屑进入油套管管体内部损伤防护层,其中所述防护塞优选为安装拆卸方便快捷的防护塞。
[0039]
在上述油套管内防腐涂敷工艺中,优选地,所述油套管在进行接箍拧紧和管端保护前在油套管螺纹处涂抹螺纹脂。
[0040]
在上述油套管内防腐涂敷工艺中,优选地,所述油套管在进行所述油套管在进行油套管管端螺纹加工后、进行接箍拧紧和管端保护前,进行螺纹检验;当螺纹检验合格时,所述油套管进行后续步骤,当螺纹检验不合格时,采取机械冷切割的方式去除不合格螺纹段后重新进行油套管管端螺纹加工。所述螺纹检验可以包括对螺纹的尺寸和外观进行检验,但不限于此。所述螺纹检验可以采用常规的螺纹检验方法进行,螺纹检验是否合格可以采用常规的螺纹检验的标准,但不限于。
[0041]
在上述油套管内防腐涂敷工艺中,所述油套管进行接箍拧紧和管端保护可以通过以下方式进行:将所述油套管进行接箍拧接,并根据需要安装接箍间隙防护环,随后进行螺纹脂和/或储存脂涂抹并安装螺纹保护帽。
[0042]
在上述油套管内防腐涂敷工艺中,优选地,所述油套管在进行接箍拧紧和管端保护后,对油套管全管体以及接箍端进行通径检验,通径检验应符合api spec.5ct的要求;其中通径检验所用通径棒较佳选用塑料材质的通径棒;更有利于避免金属通径棒损伤已经涂敷的防腐层。
[0043]
在上述油套管内防腐涂敷工艺中,优选地,该工艺进一步包括步骤5),将接箍拧紧和管端保护后地油套管进行称重测长、包装入库;其中所述包装包括在油套管管体外表面喷漆和管体标志喷涂。
[0044]
本发明从油套管内防腐涂敷工艺的流程出发,首次打破了先螺纹加工后防腐层涂敷的既定方式,提供了一种新型的油套管内防腐涂敷工艺流程。与传统工艺相比,本发明提供的技术方案具备以下有益效果:
[0045]
(1)本发明提供的技术方案省去了螺纹脂清洗和重新涂抹、螺纹保护帽多次装卸等诸多依靠人力实现的工序,有效降低了生产线人工配置(每条生产线节约人工数量5-8人/班次),提高了涂敷生产效率(比传统方法提高生产效率30%左右)、降低了总生产成本(每平米节约成本约5-10元),完全避免了传统工艺容易造成管端螺纹损伤和夹砂等导致的螺纹连接风险,避免了螺纹保护措施对管端涂敷质量的不良影响。
[0046]
(2)本发明提供的技术方案具有更广泛的适用性,特别是实现了耐高温防腐层的涂敷以及临时储存用等低端防腐层的涂敷;
[0047]
对于更好的解决高温井矿下(例如高于150℃的高温)的防腐,通常需要对油套管内部进行耐高温防腐层的涂敷;耐高温防腐涂料的涂敷,往往需要更高温度的管体预加热和涂敷温度,而过高的预加热和涂敷温度则会对油套管的螺纹精度和连接、密封性能产生
较大的负面影响,传统工艺在耐高温防腐层的涂敷上有着显著的缺陷,残次品产生率极高,本发明的技术方案在进行耐高温防腐层的涂敷时具有很好的适用性,大大降低了残次品产生的可能;
[0048]
传统工艺通常被应用于适应井矿条件防腐层(即比较高端的防腐层,用于避免在井下工况环境中的腐蚀)的涂敷;然而,油套管作为油田用大宗物资往往需要在油田现场进行长期的储存,因此除了井况条件下的防腐外,存储及运输条件下的常规防腐具有极高的必要性。目前油套管在储存运输条件下通常只能保证在三个月时间内不会出现大面积锈蚀。对于超过三个月的地面临时储存,尚未有合适的处理方式,虽然采用低端防腐层的涂敷即可解决存储运输过程中的油套管腐蚀问题,但是采用传统工艺进行低端临时储存用防腐层的涂敷由于流程复杂成本太高等原因不具实用性的;本发明提供的方案此工艺大大降低了涂敷的经济性,适用于低端临时储存用防腐层的涂敷,大大拓宽了临时储存用等低端防腐层的应用。
[0049]
(3)本发明提供的技术方案避免了传统工艺中防腐层涂敷过程中,由于螺纹以及接箍等异形物的存在对除锈、吹扫、防腐层涂敷等出多操作中带来的不便以及对涂敷的防腐层质量的影响。
附图说明
[0050]
图1为油套管内防腐涂敷工艺流程图。
[0051]
图2为防护塞a的剖面图。
[0052]
图3为防护塞a的右视图。
[0053]
图4为防护塞b的剖面图。
[0054]
图5为防护塞c的剖面图。
具体实施方式
[0055]
为了对本发明的技术特征、目的和有益效果有更加清楚的理解,现对本发明的技术方案进行以下详细说明,但不能理解为对本发明的可实施范围的限定。
[0056]
在一具体实施方式中,油套管内防腐涂敷工艺如图1所示,该工艺包括:
[0057]
步骤01、外观检验:平端油套管进入涂敷厂后,进行平端油套管外观检验,具体包括检查油套管管体是否存在损伤、油套管内壁是否存在污垢和油套管内壁是否存在异物;如果油套管管体是否存在损伤,则该油套管不在进行后续步骤;如果油套管内壁存在污垢,则进行污垢清理;如果油套管存在异物,则进行异物清除;其中所述损伤包括磕碰损伤、凹坑损伤、划伤损伤、弯曲损伤中的至少一种;所述污垢包括油污;所述异物可以包括嵌入型氧化皮,但不限于此。
[0058]
步骤02、管体内壁喷砂/抛丸除锈:进行完外观检验的平端油套管进行管体内壁进行喷砂和/或抛丸除锈处理,确保油套管的管体内壁除锈质量符合要求(例如sa 2.5或其他要求),喷砂和/或抛丸除锈所用磨料应保持干净无杂物且应按一定频率添加更换,以保持必要的清洁度。
[0059]
步骤03、管体内壁吹扫清洁:除锈处理后,利用压缩空气彻底吹扫油套管的管体内壁,确保灰尘度满足要求(例如二级或其他要求)。
[0060]
步骤04、管体内壁涂敷防腐层:内壁吹扫清洁后的油套管在返锈前进行防腐涂敷,一般要求喷砂/抛丸除锈至涂敷的间隔时间不超过4小时(可适当根据温湿度调整)。在满足喷涂环境要求的情况下,根据防腐层涂层技术要求和防腐层涂料特性设置喷涂参数,进行管体内防腐涂敷作业。涂敷过程应定期对参数进行监控,确保喷涂参数合格。根据需要,可进行多遍多层涂敷,各层的涂料和涂敷参数根据需要具体确定。
[0061]
步骤05、固化:根据防腐层要求和防腐层涂料性能特点,在每遍或每层或所有层防腐层涂敷后,可安排全管体进入固化炉进行高温固化或在空气中静置进行常温固化。
[0062]
步骤06、防腐层质量检验:根据要求逐根或按一定的检验批次检查管体内防腐层表面,确保无漏涂、针孔、流挂等缺陷,测量防腐层厚度等满足技术要求。
[0063]
步骤07、涂敷合格产品转运至油套管螺纹加工生产线:将防腐层质量检验合格的油套管转移至螺纹加工生产线,准备螺纹加工和接箍拧接等工作。
[0064]
步骤08、管端螺纹加工:进行油套管管端螺纹加工;在该过程中,应避免局部过热损伤已经涂敷的防腐层,通过优化管螺纹成型刀具切削的温度控制方案(如切削速度、切削量控制,切削液配方和喷淋姿态优化等),要求螺纹加工部位内壁最高温度不得超过管体防腐层耐温上限值的90%(以摄氏度计);做好切削液与防腐层的相干性选择,避免切削液侵蚀损伤已经涂敷的防腐层;做好切屑的清理和防护,避免铁屑机械损伤已经涂敷的防腐层,必要时对油套管加装防护塞,避免切屑进入管体内部。
[0065]
步骤09、螺纹检验、螺纹脂涂抹:油套管管端螺纹加工完成后,进行螺纹尺寸和外观检查,螺纹检验合格的油套管进行螺纹脂涂抹。
[0066]
步骤10、接箍拧接和管端防护:螺纹脂涂抹后的油套管进行接箍拧接,并根据需要安装接箍间隙防护环,随后进行螺纹脂和/或储存脂涂抹并安装螺纹保护帽;接箍拧接后,根据需要对油套管全管体或接箍端进行通径检验,通径检验使用塑料材质的通径棒,避免金属通径棒损伤已经涂敷的防腐层。
[0067]
步骤11、称重测长、包装入库:完成成品油套管的称重、测长,然后进行全管体外表面喷漆和管体标识喷涂(含色标和字标),包装后入库待运。
[0068]
实施例1
[0069]
本实施例提供一种套管内防腐涂敷工艺
[0070]
该工艺所用原料为244.48mm外径,11.99mm壁厚,n80q钢级的平端套管。
[0071]
所述套管内防腐涂敷工艺包括:
[0072]
(1)进入涂敷厂的平端套管进行管体外观检查后方可进入涂敷生产线,包括损伤检查、污垢检查、异物检查;避免存在磕碰损伤、凹坑损伤、划伤损伤、弯曲损伤等损伤的套管进入涂敷生产线;对于内壁存在油污的套管,进行手工清洗后方可进入涂敷生产线;对于内壁存在嵌入型氧化皮的套管,进行嵌入型氧化皮清楚后方可进入涂敷生产线。
[0073]
(2)对进入涂敷生产线的套管进行管体内壁除锈,采用钢刷动力工具除锈,确保除锈质量等级不低于st 2.0,表面粗糙度值不低于50μm。
[0074]
(3)除锈后的套管利用压缩空气吹扫管体内壁,确保灰尘度不低于一级。
[0075]
(4)压缩空气吹扫后的套管采用气压液体喷涂方式进行防腐层涂敷,涂敷速度约为6米/分钟,单层涂敷,涂敷车间空气相对湿度90%,温度20-30℃,要求喷砂除锈至涂敷的间隔时间不超过2小时;所述防腐层的涂料为国产718涂料(《油井管临时性内防护涂料的国
产化试验研究》,高进伟等,《现代涂料与涂装》,2015年第2期,第32-36页),也可换用其他同类产品;该防腐层为憎水性自愈合的储存用防腐层。
[0076]
(5)将防腐层涂敷后的套管转运至固化旋转台架进行防腐层固化,管体在周向旋转速度为1转/分钟的转动状态下在空气中进行常温固化,固化时间不低于30分钟,固化至内防腐层表面初干(手轻触不沾手)即可。
[0077]
(6)对防腐层固化后的套管进行防腐层质量检验,确保无漏涂和明显流挂,每五根测量一组防腐层厚度,防腐层厚度不低于70μm。
[0078]
(7)防腐层质量检验合格的平端套管进入套管车丝厂的螺纹加工生产线,准备螺纹加工和接箍拧接等工作。
[0079]
(8)对套管管端进行偏梯型螺纹加工;在进行管端螺纹加工过程中,使用全合成水基型切削液,避免损伤防腐层(本实施例所用防腐层的涂料属于防水油溶性);由于该防腐层耐温性良好,而且具有一定的损伤自愈性,螺纹加工过程并未进行特殊的温度控制和切屑清理、防护措施,切削速度采用常规切削速度200转/分左右即可。
[0080]
(9)完成螺纹检验、螺纹脂涂抹、接箍拧接、保护帽安装、称重测长、喷漆喷标、包装、入库等工作。
[0081]
(10)于套管车丝厂完成该产品的成品发运。
[0082]
使用本实施例的成本与使用传统工艺进行防腐层涂敷的成本的对比如表2所示:
[0083]
表2
[0084][0085]
传统方法中,辅助工序(螺纹前处理、后处理、包装防护等)占总成本的比例超过12%;本方法较传统方法节约成本超过30%,约7.7元。仅实施例1制备的产品每年仅在国外某一市场的供应量大约20万米,采用本方法可节约成本约118万元。
[0086]
实施例2
[0087]
本实施例提供一种油管耐高温型抗co2防腐层内防腐涂敷工艺
[0088]
该工艺所用原料为73.02mm外径,5.51mm壁厚,l80-1钢级平端油管,油管使用工况温度达180℃。
[0089]
所述油管内防腐涂敷工艺包括:
[0090]
(1)进入涂敷厂的平端油管进行管体外观检查后方可进入涂敷生产线,包括损伤检查、污垢检查、异物检查;避免存在磕碰损伤、凹坑损伤、划伤损伤、弯曲损伤等损伤的油管进入涂敷生产线;对于内壁存在油污的油管,进行手工清洗后方可进入涂敷生产线;对于内壁存在嵌入型氧化皮的油管,进行嵌入型氧化皮清除后方可进入涂敷生产线。
[0091]
(2)对进入涂敷生产线的油管进行管体内壁抛丸除锈,确保除锈质量等级不低于sa 2.5,表面粗糙度值不低于60μm。
[0092]
(3)除锈后的油管利用压缩空气吹扫管体内壁,确保灰尘度不低于二级。
[0093]
(4)压缩空气吹扫后的油管进行防腐层涂敷;
[0094]
4.1首先进行基层涂敷:采用无气旋转液体喷涂方式进行基层涂敷,采用两遍双层喷涂,喷头旋转速度不低于3000转/分钟,涂敷速度约为6米/分钟,涂敷车间空气相对湿度70%,温度15-25℃,要求喷砂除锈至底层涂敷的间隔时间不超过4小时;
[0095]
4.2将基层涂敷后的油管转运至固化旋转台架进行基层固化:管体在周向旋转速度为1转/分钟的转动状态下在空气中进行常温固化,固化时间不低于30分钟,固化至内防腐层表面初干(手轻触不沾手)即可;
[0096]
4.3将基层固化后的油管进行基层质量检验:确保无流挂,每五根测量一组基层总厚度,基层总厚度不低于120μm,逐根对基层进行全覆盖电火花漏点检测,确保无漏点;
[0097]
4.4将基层质量检验合格的油管进行面层涂敷:首先采用渐进式中频加热的方式将喷涂段管体预热至260-280℃(由于管体没有螺纹等精密结构,无需担心加热温度对螺纹精度产生影响),采用静电喷涂方式进行面层涂敷,确保涂敷温度为220-240℃,涂敷速度约为2米/分钟;
[0098]
4.5将面层涂敷后的油管转运至烘干固化炉进行全管体烘干固化:管体固化炉内周向旋转速度约为3转/分钟,固化温度控制在180-190℃,固化时间不低于30分钟,确保防腐层全部固化;
[0099]
防co2腐蚀防腐层包括上述基层与面层,基层为双组分液态改性环氧涂料(上海赛能公司的tc3000f专用底漆),面层为熔融型环氧粉末涂料(上海赛能公司的tc3000f涂料),也可换用其他同类产品。
[0100]
(5)对全管体烘干固化后的油管进行防腐层质量检验,确保无流挂,每五根测量一组防腐层总厚度,总厚度不低于120μm,逐根对防腐层进行全覆盖电火花漏点检测,确保无漏点。
[0101]
(6)防腐层质量检验合格的平端油管进入油管车丝厂的螺纹加工生产线,准备螺纹加工和接箍拧接等工作。
[0102]
(7)对油管管端进行螺纹加工;在进行管端螺纹加工过程中,使用水基或油基切削液均可(本实施例所用防腐层的涂料属于耐水耐油性);由于该防腐层耐温性极限为180℃,螺纹加工过程中控制好切削温度(切削速度控制在130转/分钟,单次切削量/进刀量不超过0.3mm);该涂层容易遭受机械损伤,螺纹加工前在管端安装专用快装式防护塞(具体结构如图2-图3所示),避免切屑进入管体内部;
[0103]
所述防护塞任选防护塞a、防护塞b中和防护塞c中的一个,防护塞a、防护塞b和防护塞c均是由橡塑制成。
[0104]
防护塞a(如图2、图3所示)包括位于后端的密封部2和位于前端的摩擦部3;其中,
密封部2为圆柱形,密封部的外壁用于与油套管内壁贴合从而实现密封部2与油套管内壁密封贴合;摩擦部3用于与油套管内壁卡接,摩擦部3上设置有倒齿形结构,倒齿形结构具有至少一个倒齿,倒齿的齿顶用于与油套管内壁接触,倒齿形结构的齿顶圆直径等于密封部2的直径,以确保防止螺纹加工过程中切屑渗漏;密封部2上还开有把手1:把手1设置于所述密封部的后端,把手1设置部位设有凹槽以便于把手的手握和/或使用工具进行防护塞的拆卸;密封部与所述摩擦部一体成型。
[0105]
防护塞b(如图4所示)包括位于后端的密封部2和位于前端的摩擦部3;其中,密封部2为圆柱形,密封部的外壁用于与油套管内壁贴合从而实现密封部2与油套管内壁密封贴合;摩擦部3用于与油套管内壁卡接,摩擦部3上设置有螺纹形结构,螺纹形结构的表面螺旋线用于与油套管内壁接触,螺纹形结构的外径等于密封部2的直径,以确保防止螺纹加工过程中切屑渗漏;密封部2上还开有把手1:把手1设置于所述密封部的后端,把手1设置部位设有凹槽以便于把手的手握和/或使用工具进行防护塞的拆卸;密封部与所述摩擦部一体成型。
[0106]
防护塞c(如图5所示)包括位于后端的密封部2和位于前端的摩擦部3;其中,密封部2为圆柱形,密封部的外壁用于与油套管内壁贴合从而实现密封部2与油套管内壁密封贴合;摩擦部3用于与油套管内壁卡接,以确保防止螺纹加工过程中切屑渗漏;密封部与所述摩擦部一体成型。
[0107]
(8)完成螺纹检验、螺纹脂涂抹、接箍拧接、保护帽安装、称重测长、喷漆喷标、包装、入库等工作。
[0108]
(9)于油管车丝厂完成该产品的成品发运。