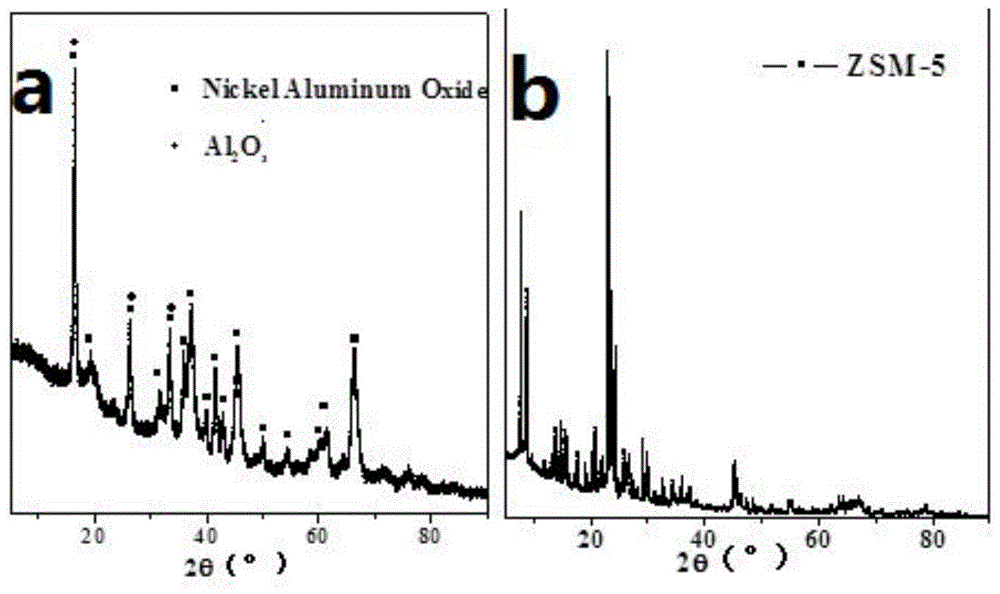
本发明涉及石油化工领域。更具体地,涉及一种临氢降凝催化剂及其制备方法和应用。
背景技术:
:“临氢降凝”也称“催化脱蜡”,是指在氢气存在的条件下,含蜡的烃油原料在催化剂表面反应,其中倾点较高的蜡分子发生裂化反应,生成小分子,从油品中分离除去从而降低油品的凝点(倾点)。其脱蜡原理是在一定的操作条件下,使原料与氢气混合与临氢降凝催化剂接触,原料中的链烷烃、带短侧链烷烃、带长侧链的环烷烃和带长侧链的芳烃等高凝点组分选择性地裂解成小分子,而其它组分基本不发生变化,最终达到降低油品凝点(倾点)的目的。临氢降凝技术的关键是具有择形作用的分子筛催化剂。临氢降凝催化剂是双功能催化剂,金属组分提供加氢脱氢活性中心,分子筛提供择形裂解反应必须的孔结构和酸性中心。zsm-5分子筛具有择型裂化的催化性能,它的晶内孔道具有裂解烃分子的酸中心,又具有特殊的孔道结构,只允许正构烷烃和带较少侧链的异构烷烃进入孔道,进行裂解反应,可实现降低凝点(倾点)的目的。中国专利cn1102642c公开了一种润滑油催化脱蜡催化剂,以晶粒大小为0.1~0.5μm、sio2/al2o3摩尔比为50~120的小晶粒zsm-5分子筛为催化材料,粘结剂为碳化法氧化铝,其中,分子筛含量为65wt%~85wt%,氧化铝含量15wt%~35wt%。中国专利cn1152947c公开了一种催化脱蜡催化剂,其特征是在zsm系列分子筛中引入锆元素,锆的加入量是0.1~10%。本方法制备的催化剂对馏分油催化脱蜡具有较高的活性。中国专利cn101143333a公开了一种临氢降凝催化剂及其制备方法,是先将含有加氢活性组分的化合物与氧化铝干胶混合制备胶粘剂,然后再与择形裂化分子筛混捏成型,经干燥和焙烧后,得到催化剂载体,浸渍含剩余部分活性组分和助剂的浸渍液,再经干燥和焙烧制得,其组成如下:氧化镍含量为1%~4%,氧化钼或氧化钨含量为1%~9%,择形裂化分子筛为60.0%~75.0%,氧化铝15.0%~30.0%,助剂为0.2%~2.0%。中国专利cn1352231a公开了临氢降凝催化剂及其制备方法,催化剂以硅铝酸盐分子筛为基质,添加少量粘合剂挤条成型制成载体,以viii族和vib族金属为加(脱)氢组分,采用高温焙烧的方式降低催化剂的酸量。其中,择形裂化分子筛60~90%,粘合剂9~39%。中国专利cn102451752a公开了一种加氢脱蜡催化剂及其制备方法和应用,催化剂组成为:择形裂化分子筛的含量30%~70%,β分子筛的含量3%~20%,活性金属氧化物的含量为1%~15%,粘合剂的含量为10%~30%。中国专利cn100457868c公开了一种润滑油临氢催化脱蜡催化剂,该催化剂包含一种经过特殊改性的具有ton和mfi结构特征的复合分子筛和活性组分,能够使石蜡烃发生择形裂解和-异构化反应,改善产品性能、提高产品收率。上述临氢降凝催化剂均是先以氧化铝制成粘合剂,再与分子筛混合挤条成型,分子筛与粘合剂机械混合,分子筛易被粘合剂包裹,降低了分子筛的利用率。同时,催化剂中分子筛含量高,也造成了催化剂较高的成本。技术实现要素:针对现有技术中的不足,本发明的一个目的在于提供一种临氢降凝催化剂,该催化剂贵金属含量低,活性组分高度分散,且具有优异的催化加氢活性、选择性、稳定性。本发明的第二个目的在于提供一种临氢降凝催化剂的制备方法。本发明的第三个目的在于提供一种临氢降凝催化剂的应用。为达到上述第一个目的,本发明采用下述技术方案:一种临氢降凝催化剂,包含有活性金属氧化物以及负载所述活性金属氧化物的催化剂载体;所述催化剂载体包含表面具有通孔的催化剂载体支撑体和位于该支撑体孔道表面的分子筛膜,且所述表面具有通孔的催化剂载体支撑体中包含氧化铝和金属氧化物助剂,其中所述氧化铝和金属氧化物助剂形成尖晶石结构。可选地,所述通孔均匀分布在所述催化剂载体支撑体上,优选为微孔和/或介孔,更优选为铂基微孔-介孔。可选地,所述催化剂载体支撑体的长度为1mm~10mm,优选3mm~8mm、外径为4mm~8mm、内孔直径为2mm~4mm、表面通孔直径为1mm~3mm。可选地,所述通孔直径为1mm~3mm,通孔形状可为圆形、矩形、多边形等,优选圆形。可选地,所述催化剂载体呈颗粒状,其支撑体孔容>0.750ml/g,比表面积>150m2/g。可选地,所述分子筛具有择形作用,可选自zsm-5、β型中的一种或几种。可选地,按质量百分比计,所述临氢降凝催化剂中,包含活性金属氧化物1~21%、分子筛8~40%、金属氧化物助剂1.0%~5.4%。可选地,所述金属氧化物助剂选自nio、cuo中的一种或两种。可选地,所述临氢降凝催化剂的孔容0.35~0.50ml/g,比表面积为230~260m2/g。可选地,所述活性金属氧化物为第ⅷ族和/或ⅵb族金属氧化物,优选为nio和wo3中的一种或几种。可选地,按质量百分比计,所述临氢降凝催化剂中,包含nio1.0~6.0%,wo30~15%、分子筛8~40%、金属氧化物助剂1.0%~5.4%。具体地,wo3的质量百分比包括但不限于0、0.5~15%、0.5~10%等。可选地,该临氢降凝催化剂中,分子筛的添加量可包括但不限于8~20%、8~25%、8~30%、8~40%等。其中,该临氢降凝催化剂中,可在较少的分子筛的含量的条件下,依然具有很好的催化含蜡的烃油原料临氢降凝。可选地,按质量百分比计,所述临氢降凝催化剂中,包含nio1.0~6.0%,wo30.5~15%、分子筛8~40%、金属氧化物助剂1.0%~5.4%。为达到上述第二个目的,本发明采用下述技术方案:临氢降凝催化剂的制备方法,包括如下步骤:1)配制分子筛母液并对催化剂载体支撑体进行浸渍,将浸渍后的物料进行晶化,经洗涤、干燥、焙烧得催化剂载体;2)配制活性金属的盐溶液并对所述催化剂载体进行浸渍,经干燥、焙烧后得所述临氢降凝催化剂。可选地,步骤1)中,所述分子筛母液优选为zsm-5母液,具体成分可为:摩尔比为al2o3:sio2:na2o:模板剂:h2o=(0.025~0.25):(4~25):(0.03~0.3):(0.02~0.2):(10~150),其中,al2o3由硫酸铝、硝酸铝和氯化铝中的一种或几种提供,优选硫酸铝;sio2由硅溶胶和正硅酸乙脂中的一种提供,na2o由氢氧化钠提供;模板剂为三乙胺、四乙基氢氧化铵、二乙胺、二丙胺和三丙胺中的一种或几种,优选三乙胺;所述晶化优选在气相反应釜中进行,更优选为浸渍后物料置于气相反应釜的上部,气相反应釜底部加入去离子水,在160~230℃下反应24~72小时;可选地,步骤1)中所述洗涤是将晶化后物料用去离子水洗涤至中性;可选地,步骤1)中,所述干燥的温度为120~150℃,时间为6~10小时;可选地,步骤1)中,所述焙烧的温度为500~650℃,时间为2~6小时。可选地,步骤1)中,也可根据催化剂对分子筛含量要求重复浸渍、晶化、洗涤和干燥,最后焙烧得到含有分子筛膜的催化剂载体。可选地,步骤2)中,活性金属的盐溶液为ⅷ族和/或ⅵb族金属盐溶液,优选硝酸镍溶液和/或硝酸镍-偏钨酸铵溶液,溶液的nio浓度为0.0126g/ml~0.095g/ml,wo3浓度为0~0.237g/ml;所述干燥的温度为120~150℃,时间为6~10小时;所述焙烧的温度为400~550℃,时间为2~6小时。可选地,所述晶化在气相反应釜中进行。利用气相反应釜中蒸汽加热反应,确保合成的分子筛全部聚集在支撑体孔内,不会造成分子筛的浪费可选地,所述催化剂载体支撑体的制备包括如下步骤:a.将拟薄水铝石、胶溶剂、助挤剂、扩孔剂、金属氧化物助剂前躯物和水经混合挤条成型后进行浅度干燥,再经造粒、干燥、焙烧得所述催化剂载体支撑体。扩孔剂的加入使制备的支撑体具有较大的孔容和孔径,为后续分子筛合成预留了较大的空间。金属氧化物助剂前躯物的加入,经高温焙烧后与氧化铝形成尖晶石结构,提高了支撑体强度和骨架稳定性的同时也降低了支撑体的酸性,利于提高产品收率。可选地,所述拟薄水铝石为目前工业普遍使用的硫酸铝法、碳化法、氯化铝法等生产的拟薄水铝石;所述拟薄水铝石的孔容>0.95ml/g,比表面积为280~330m2/g。可选地,所述拟薄水铝石与金属氧化物助剂前躯物的质量比为1:0.02~0.06。可选地,所述金属氧化物助剂前躯物选自硝酸镍、硝酸铜中的一种或几种。可选地,步骤a中,所述干燥的温度为120-150℃,时间为6-10小时;所述焙烧的温度为800-1000℃,时间为2-6小时。可选地,步骤a中,所述拟薄水铝石、胶溶剂、助挤剂、扩孔剂、金属氧化物助剂前躯物和水的质量比为1:0.01~0.06:0.01~0.04:0.1~0.3:0.02~0.06:1.0~1.5。可选地,所述胶溶剂选自硝酸、醋酸、柠檬酸中的一种或几种。可选地,所述助挤剂为田菁粉、甲基纤维素中的一种或几种。可选地,所述扩孔剂的粒度>30μm,选自碳黑、石墨、淀粉中的一种或几种。可选地,所述浅度干燥是指在恒湿恒温条件下将条形物干燥至固含量55%~75%,且保证里外湿度一致。可选地,所述挤条成型为挤出内部中空,外面呈圆柱形、三叶草形、四叶草形的条形物,优选外形为圆柱形,其中,条形物外径为4mm~8mm,内部中空直径为2mm~4mm,中空形状可为圆形、矩形、多边形等,优选圆形。可选地,所述造粒为将所述挤条成型后的结构制成长度为1mm~10mm的颗粒,优选3mm~8mm。如无特殊说明,上述比表面积、孔容均采用低温氮吸附法测定。本发明的有益效果如下:本发明提供的临氢降凝催化剂的催化剂载体因为具有该特定的结构,从而使得该催化剂空隙率高、通透性好,利于反应物和产物的扩散;另外,结构中具有的尖晶石结构在提高了支撑体强度和骨架稳定性的同时也降低了支撑体的酸性,利于提高产品收率。此外,本发明催化剂中分子筛含量少、利用率高、贵金属含量低、活性组分高度分散、成本低。本发明催化剂的制备方法中,采用分子筛母液浸渍支撑体,优选利用气相反应釜中蒸汽加热反应,确保合成的分子筛全部聚集在支撑体孔内,不会造成分子筛的浪费;同时,在支撑体孔道内合成分子筛并涂膜在支撑体孔道表面,使得分子筛裸露在外面,提高了分子筛的利用率,克服了传统方法中因分子筛被包裹无法发挥作用的问题;且该制备方法简单,易操作。附图说明下面结合附图对本发明的具体实施方式作进一步详细的说明。图1中a和b依次示出了得到的催化剂载体及zsm-5分子筛的xrd图。图2示出实施例1催化剂分子筛膜的sem图。图3中a和b依次示出实施例1催化剂载体及催化剂的tem图。具体实施方式为了更清楚地说明本发明,下面结合优选实施例和附图对本发明做进一步的说明。附图中相似的部件以相同的附图标记进行表示。本领域技术人员应当理解,下面所具体描述的内容是说明性的而非限制性的,不应以此限制本发明的保护范围。实施例1分别称取硫酸铝法生产的孔容1.095ml/g、比表面积328m2/g、干基71%的拟薄水铝石500g、浓度65%的硝酸18.4g、田菁粉10g、碳黑71g、硝酸镍助剂60g和去离子水754g加入碾压机中碾压混合,挤成外径6mm、内部中空直径2.5mm的圆柱形条,并在恒湿恒温条件下将条形物干燥至固含量为65%。采用打孔设备在圆柱形条表面打成直径为1.5mm均匀排列的圆形通孔,并制成长度为3mm~10mm的颗粒,在130℃下干燥8小时后,经900℃焙烧3小时得到载体支撑体。分别称取硫酸铝7.52g、含氧化硅30%的硅溶胶320g、氢氧化钠2.15g、三乙胺1.81g和水80g配制成zsm-5分子筛母液;用配制的分子筛母液浸渍上述载体支撑体,浸渍后物料置于气相反应釜上部,气相反应釜底部加入去离子水,在180℃下反应36小时,反应结束用去离子水洗涤至中性,在130℃下干燥8小时,再经550℃焙烧3小时得含有的zsm-5分子筛膜的催化剂载体。图1中a和b依次示出了得到的催化剂载体及zsm-5分子筛的xrd图。从图1可以看出,通过碾压-挤条工艺制备的催化剂载体的主要晶型为镍铝尖晶石组分及氧化铝组分。通过水热合成制备的分子筛膜的晶型为zsm-5分子筛,不含杂晶相。图2示出催化剂分子筛膜的sem图,从图中可知,zsm-5分子筛具有典型的六边形形状,分子筛的尺寸属于微米级别,在1~4um之间。称取30.3g硝酸镍配制成含氧化镍0.019g/ml的溶液并浸渍上述催化剂载体,浸渍结束后物料在120℃下干燥8小时,并在450℃下焙烧3小时即得到本发明催化剂a-1,催化剂性质见表1。图3示出实施例1催化剂载体的tem图(a),催化剂的tem图(b)。利用tem对催化剂及载体进行形貌分析,从图中a可以看出载体具有规整的网状孔道结构,属于zsm-5分子筛固有孔道。从图中b可以看出,负载金属后,金属晶粒为纳米级,均匀分布在载体晶粒的表面及内部。实施例2制备过程如实施例1,只是将硫酸铝法生产的拟薄水铝石改为碳化法生产的孔容1.061ml/g、比表面积320m2/g、干基71%的拟薄水铝石,硝酸加入量改为21.5g,去离子水加入量改为742g,得到本发明催化剂a-2,催化剂性质见表1。实施例3分别称取硫酸铝法生产的孔容1.095ml/g、比表面积328m2/g、干基71%的拟薄水铝石500g、浓度65%的硝酸18.4g、田菁粉10g、淀粉89g、三水硝酸铜助剂43.7g和去离子水754g加入碾压机中碾压混合,挤成外径6mm、内部中空直径2.5mm的圆柱形条,并在恒湿恒温条件下将条形物干燥至固含量为65%。采用打孔设备在圆柱形条表面打成直径为1.5mm均匀排列的圆形通孔,并制成长度为3mm~10mm的颗粒,在130℃下干燥8小时后,经900℃焙烧3小时得到载体支撑体。分别称取硫酸铝15.53g、含氧化硅30%的硅溶胶663g、氢氧化钠4.45g、三乙胺3.75g和水165.6g配制成zsm-5分子筛母液;用配制的分子筛母液的二分之一浸渍上述载体支撑体,浸渍后物料置于气相反应釜上部,气相反应釜底部加入去离子水,在180℃下反应36小时,反应结束用去离子水洗涤至中性,在130℃下干燥8小时,再用剩余的分子筛母液浸渍干燥后物料,浸渍后物料置于气相反应釜上部,气相反应釜底部加入去离子水,在180℃下反应36小时,反应结束用去离子水洗涤至中性,在130℃下干燥8小时,再经550℃焙烧3小时得到含有zsm-5分子筛膜的催化剂载体。称取73g硝酸镍配制成含氧化镍0.038g/ml的溶液并浸渍上述催化剂载体,浸渍结束后物料在120℃下干燥8小时,并在450℃下焙烧3小时即得到本发明催化剂a-3,催化剂性质见表1。实施例4分别称取硫酸铝法生产的孔容1.095ml/g、比表面积328m2/g、干基71%的拟薄水铝石500g、浓度65%的硝酸18.4g、田菁粉10g、碳黑71g、硝酸镍助剂60g和去离子水754g加入碾压机中碾压混合,挤成外径8mm、内部中空直径3mm的圆柱形条,并在恒湿恒温条件下将条形物干燥至固含量为65%。采用打孔设备在圆柱形条表面打成直径为2mm均匀排列的圆形通孔,并制成长度为3mm~10mm的颗粒,在130℃下干燥8小时后,经950℃焙烧3小时得到载体支撑体。分别称取硫酸铝8.62g、正硅酸乙酯333.3g、氢氧化钠3.18g、四乙基氢氧化铵2.64g和水100g配制成zsm-5分子筛母液;用配制的分子筛母液浸渍上述形体支撑体,浸渍后物料置于气相反应釜上部,气相反应釜底部加入去离子水,在200℃下反应48小时,反应结束用去离子水洗涤至中性,在130℃下干燥8小时,再经550℃焙烧3小时得含有的zsm-5分子筛膜的催化剂载体。分别称取66.4g硝酸镍和54.3g偏钨酸铵,配制成含氧化镍0.043g/ml、含三氧化钨0.128g/ml的混合溶液,并浸渍上述催化剂载体,浸渍结束后物料在120℃下干燥8小时,并在450℃下焙烧3小时即得到本发明催化剂a-4,催化剂性质见表1。比较例1以中国专利cn1352231a作为比较例,制备过程如下:(1)称取小孔氧化铝(孔容0.49ml/g、比表面积229m3/g)40.5g,加入69.4g净水和8.1ml浓硝酸,混合均匀,做成粘合剂;(2)分别称取zsm-5分子筛126.3g,田菁粉3.0g和上述粘合剂混捏,挤条成型;(3)湿条在100±10℃条件下干燥4小时,在730℃条件下焙烧4小时,制成载体;(4)取24.9g硝酸镍用净水溶解,配成200ml溶液;(5)将上述载体100g放入浸渍液中,浸渍2小时,然后过滤,100℃条件下干燥4小时,480℃焙烧3小时,制成催化剂b-1,催化剂性质见表1,催化剂评价结果见表3。表1本发明催化剂及比较例催化剂性质实施例5将以上实施例催化剂和比较例1催化剂性能评价是以某厂加氢改质装置柴油馏分为原料,要求将原料中>280℃馏分倾点降至-50℃以下,用于生产倾点小于-50℃的变压器油。催化剂性能评价在20ml微反装置上进行,催化剂的装填量为20毫升,原料油性质见表2,催化剂评价的工艺条件及产品性质见表3。表2原料油性质表3催化剂评价工艺条件及产品性质从产品性质看出,相比较对比例1,本发明催化剂在大幅度降低分子筛用量的情况下,仍然保持很高的降凝活性,产品倾点仍能满足需求。实施例6将以上实施例催化剂和比较例1催化剂性能评价是以某厂加氢柴油馏分为原料,要求将其凝点降至-35℃以下,用于生产-35#柴油。催化剂性能评价在20ml微反装置上进行,催化剂的装填量为20毫升,原料油性质见表4,催化剂评价的工艺条件及产品性质见表5。表4加氢柴油性质分析项目加氢柴油密度(20℃),kg/m3853.1馏程,℃ibp/10%183.5/235.030%/50%260.5/285.570%/90%315.5/350.595%255.0s,μg/g<1.0n,μg/g<1.0凝点,℃-15运动粘度(40℃),mm2/s3.25质谱组成,%饱和烃84.9芳烃15.1表5催化剂评价工艺条件及产品性质从产品柴油的凝点和冷滤点可以看出,相比较对比例1,本发明催化剂分子筛含量降低,仍然具有较高的降凝活性,可以将柴油凝点及冷滤点指标满足-35#柴油的要求。显然,本发明的上述实施例仅仅是为清楚地说明本发明所作的举例,而并非是对本发明的实施方式的限定,对于所属领域的普通技术人员来说,在上述说明的基础上还可以做出其它不同形式的变化或变动,这里无法对所有的实施方式予以穷举,凡是属于本发明的技术方案所引伸出的显而易见的变化或变动仍处于本发明的保护范围之列。当前第1页12