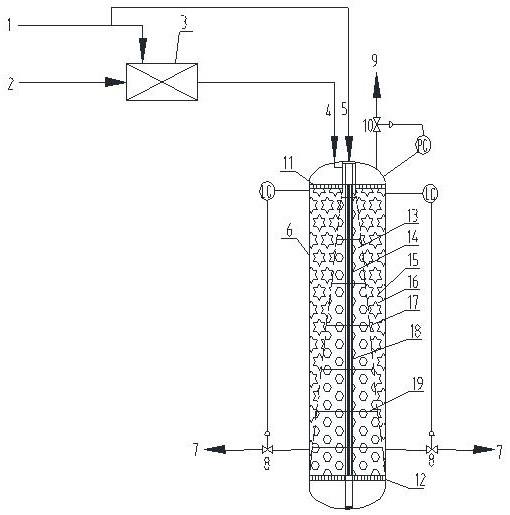
1.本发明属于化工及石油化工领域,具体为一种液相加氢反应器及加氢工艺。
背景技术:2.液相加氢技术是一种新型的加氢技术,是预先将氢气溶解于原料油中,通过液相大量循环来满足加氢反应所需氢气,克服了常规滴流床加氢反应中氢气扩散传质的影响,使加氢反应在动力学控制区进行,因此相比于传统的固定床气/液/固三相加氢工艺而言,液相加氢工艺具有加氢反应速率快、反应效率高、能耗低、投资少等诸多优势,得到广泛认可和应用。
3.液相加氢反应器主要分为上流式固定床加氢反应器和下流式固定床加氢反应器,其中下流式固定床反应器由于反应物料在催化剂表面能够反应完迅速离开,一方面有效减少催化剂表面的催化剂结焦,另一方面能够将热量及时的带走,因此应用较为普遍。但是,常规的下流式液相加氢反应器及反应工艺中仍然存在如下问题:(1)反应前期新鲜物料中反应物浓度高、氢气含量高,反应的过程推动力大,催化剂初活性也高,而物料与催化剂在液相加氢过程中的接触也较为充分,因此存在反应放热剧烈、温升大、过程不易控制的问题;(2)反应后期,由于反应温度高,若仍然在高活性催化剂上发生加氢反应,造成反应速率快、副反应和裂解反应严重的问题,因此反应后期应采用适当活性的催化剂,以控制反应速率,提高反应收率,从解决反应产物对加氢反应的抑制作用的角度,改善加氢反应深度;(3)由于反应后期仍为液相加氢反应过程,反应生成的气体产物仍然溶解在液体物料中,即液相加氢反应过程中采用常规反应器汽提的方式很难分离出来,需要较大的汽提表面积,如果反应生成气体没有被及时的汽提出来而移走,会降低反应后期的反应转化率,从而达不到理想的加氢反应深度;(4)反应过程中随着物料在加氢反应器内的流动和氢气的消耗,氢气在油品中的溶解分散状态已经逐渐发生了变化,导致油品分子周围溶解的氢气气泡已经发生了反应,那些没有发生反应的气泡逐渐聚结为大气泡,使油品在加氢反应过程中不能持续的提供氢气,也会增加副反应或裂解反应。因此,对于常规的下流式液相加氢反应过程来说,采用有效的手段,如开发新的加氢方法及反应器形式,控制反应物料的活性及物料与催化剂的接触方式,既能够控制反应前期集中放热、后期反应转化率低的问题,又能够保证加氢反应速率和反应深度,具有重要意义。
4.cn203389622u提出了一种液相加氢反应装置,其包括至少一液相加强反应器,设置在所述液相加强反应器外部的静态混合器及氢气补充装置。该专利的目的是将现有的反应器内设置复杂结构内构件的方法,改进为采用静态混合器,并将静态混合器设置在反应器外部。
[0005] cn203389623u提出了一种液相加氢反应系统,包括原料油缓冲罐、反应进料加热炉、气液混合器、液相加氢反应器、减压设备及低压分离器,其中的液相加氢反应器出口通过减压设备与低压分离器相连,目标是使反应产物中大部分的硫化氢和氨闪蒸出来。
[0006]
cn202063881u公开了一种液相加氢反应器,反应器顶部封头内设置混合器,混合
器有混合油进料口和氢气入口,溶氢混合物出口和气体出口,混合物溶氢混合物出口插到反应器液相中。该专利的目的是通过混氢器在反应器内的结构,来增加气液相接触面积,使氢气溶解在混合油中,来提高加氢反应效率。
[0007]
cn105713659a提出了一种烃类连续液相加氢工艺方法,是烃类原料和氢气经气液混合器充分混合形成溶解氢气饱和的液相物流,在包含至少的两级催化剂的反应器中,从上往下先后与各级催化剂下部的氢气分配器中注入氢气,产物从反应器引出后续处理。该方法的目的是在催化剂床层间补充新鲜氢气,同样是用来提高反应效率。
[0008]
综上所述,现有技术中的液相加氢反应器,大多思路都是通过溶氢方法或溶氢组件来进行溶氢,通过补充氢的方法来提高反应效率,然后通过将反应产物至外面的汽提设施将反应生成气体硫化氢和氨闪蒸出来,这些方法没有解决液相加氢反应过程中反应放热剧烈、温升不均匀、后期反应转化率低、达到需要的转化率时停留时间长等问题,因此需要进一步开发新型的液相加氢反应器及液相加氢反应工艺。
技术实现要素:[0009]
针对现有技术的不足,本发明提供一种液相加氢反应器及加氢工艺,通过在液相加氢反应器内设置锥形内筒和氢气扩散组件,有效控制加氢反应整个过程中物料与催化剂的接触时间,使催化剂床层温升更加均匀,解决反应过程中放热剧烈、反应产物抑制反应转化率的问题,使整个反应过程都达到较高的加氢反应速率和反应转化率。本发明所述的“上”、“下”是指沿反应器的轴向方向。
[0010]
本发明的液相加氢反应器,包含内筒和反应器外壳,内筒为锥形,内筒顶部和底部敞口,底部边缘与反应器内壁密闭连接,内筒筒壁开设若干小孔;内筒和反应器外壳之间构成横截面积逐渐增加的环形腔体;反应器轴向上从反应器顶部到内筒底部之间竖直设置陶瓷膜管束,陶瓷膜管束连通外部氢气;所述的内筒装填加氢催化剂i,环形腔体装填加氢催化剂ii,加氢催化剂i的活性高于加氢催化剂ii的活性;反应器原料入口与内筒顶部连通,内筒顶部与环形腔体不连通,反应器产物出口与环形腔体下部连通;物料在内筒的流动方式为由上而下,同时由中心向四周;物料在环形腔体的流动方式为由上而下。
[0011]
本发明的液相加氢反应器中,所述的“锥形”实际为“截头圆锥”,“锥形”内筒的顶部平面直径与反应器的直径之比为1:1.05~1:50,优选1:1.5~1:5。
[0012]
本发明的液相加氢反应器中,内筒筒壁的开孔率为30%~95%,优选55%~75%;孔可以为长方形、正方形、菱形、圆形、六角形等中的任意一种,优选圆形;孔径大小为0.1mm~50mm,优选5~15mm。
[0013]
本发明的液相加氢反应器中,所述的陶瓷膜管束竖直放置在反应器的中心轴线上,上、下两端分别通过刚结构支撑件固定在反应器上、下封头的内表面,内筒由上至下均匀设置固定支撑卡件,将陶瓷膜管束固定在内筒内表面,外部氢气管线与陶瓷膜膜管连通;陶瓷膜管束能够形成的纳/微米气泡的尺寸一般为10~1000nm,优选为50~500nm。
[0014]
所述的陶瓷膜管束中,反应进料经内筒由上而下流动,氢气由氢气管线进入陶瓷膜膜管管内,在反应过程中氢气由陶瓷膜膜管管内渗透扩散至管外,主要作用是补氢溶氢、推动物料扩散和汽提的作用,一方面增强反应过程中加氢反应过程推动力,以维持整个过程较高的反应速率;另一方面,由氢气扩散组件的膜管内向四周扩散出的氢气气泡,在氢气
氛围下推动内筒物料穿过内筒筒壁进入环形腔体,可以缩短物料在内筒的停留时间,起到控制反应活性、防止催化剂结焦、带走反应热的作用;第三,实现了边反应、边汽提,大幅度降低了反应气体产物对反应的抑制作用,改善了加氢反应深度,提高总反应效率。
[0015]
本发明的液相加氢反应器中,反应器顶部为反应器上封头,底部为反应器下封头,原料入口处优选设置物料分布器,用于均匀分布物料进入内筒。
[0016]
本发明的液相加氢反应器中,所述的反应器顶部有气体空间,反应器顶部封头设置气体出口,用于连续或间断排放反应过程中汽提出的反应气体。
[0017]
本发明的液相加氢工艺,包括如下内容:含有氢气的原料经反应器顶部进料口进入液相加氢反应器的“锥形”内筒,向下流动与内筒装填的加氢催化剂i进行加氢反应,物料反应过程中在陶瓷膜管束扩散出的氢气推动下,部分物料经内筒筒壁上的开孔流入环形腔体,与环形腔体内装填的加氢催化剂ii发生进一步加氢反应,最终的反应产物自环形腔体下部的反应物出口排出。
[0018]
本发明方法中,所述的含氢气的原料一般通过氢油混合设备进行混合的方式获得,如采用静态混合器、溶气泵、胶体磨、微孔板纳/微米氢分散组件、陶瓷膜纳/微米氢分散组件等具有气液混合功能的设备;含氢气的原料中,氢气质量含量一般为重油原料质量的0.01wt%~20%,优选0.03wt%~2.0wt%。
[0019]
本发明工艺中,陶瓷膜管束扩散出的氢气一方面用于反应过程消耗的氢气补充,另一方面起到推动物料向环形腔体移动的作用,还有对气体产物进行汽提的作用;根据整个过程需要,陶瓷膜管束的氢气通入量为反应进料中液体原料的0.01wt%~5.0wt%,优选0.05wt%~2.0wt%。
[0020]
本发明工艺中,物料在内筒和环形腔体的停留时间比为1:0.05~1:10,优选1:0.5~1:2。
[0021]
本发明工艺中,液相加氢反应器上部通过液位控制出料,保证加氢反应过程为全液相加氢。
[0022]
本发明工艺中,所述内筒的加氢反应条件为:反应温度 60℃~360℃,优选120℃~340℃;反应压力0.5mpa~20.0mpa,优选1.0mpa~6.0mpa;新鲜进料液时体积空速0.5h-1
~20.0h-1
,优选4.0h-1
~15.0h-1
。
[0023]
本发明工艺中,所述环形腔体的加氢反应条件为:反应温度100℃~400℃,优选120℃~380℃;反应压力0.5mpa~20.0mpa,优选1.0mpa~6.0mpa;新鲜进料液时体积空速0.5h-1
~15.0h-1
,优选3.0h-1
~10.0h-1
。
[0024]
本发明的液相加氢反应器,可用于石油化工领域能够与氢气发生加氢反应的多种原料,可以为如原油、汽油、煤油、柴油、渣油、重质油、蜡油、润滑油、脱沥青油、生物柴油、动物油或植物油、煤焦油、蒽油等原油和二次加工油,在加氢过程中发生硫/氮/氧/金属等的加氢转化、烯烃及二烯烃加氢饱和、芳烃部分加氢饱和、加氢裂化等反应;也可以为化工领域能够发生加氢反应的多种原料,可以为含有炭炭双键、炭炭三键以及有机官能团的原料,如烯烃加氢、炔烃加氢、醛类化合物加氢、酮类化合物加氢、酯类化合物加氢、硝基化合物加氢、腈类化合物加氢等反应。
[0025]
本发明工艺中,所述的加氢催化剂i的活性高于加氢催化剂ii的活性。其中所述的活性高低是针对内筒和环形腔体发生的化学反应而言的,是以每单位容积(或质量)催化剂
在单位时间内转化原料反应物的数量来表示,催化活性的高低可以通过催化剂载体比表面积的大小、表面上活性中心的性质和单位表面积上活性中心的数量等进行选择或制备过程中进行调控。
[0026]
本发明工艺中,所述的液相加氢反应器采用的催化剂可以根据反应的需要使用适宜的加氢催化剂,实现不同的加氢目的,如加氢精制催化剂、预加氢精制催化剂、加氢改质催化剂、选择性加氢催化剂、加氢处理催化剂、加氢裂化催化剂、补充加氢催化剂等,各种催化剂可以选择商品催化剂,也可以根据现有技术制备。催化反应可以脱除部分或全部烃类原料中的硫、氮、氧、砷、金属、残碳等杂质,或饱和/部分饱和烯烃、芳烃、二烯烃,或发生烃类分子异构化、烷基化、环化、芳构化、裂化、裂解等反应;催化剂活性组分包括但不局限于贵金属、co、mo、ni、w、mg、zn、稀土元素等一种或多种组合。
[0027]
本发明工艺中,所述的液相加氢反应器内环形腔体可以装填活性全部或部分低于内筒活性的加氢催化剂,催化剂可以使用市售产品,也可以根据本领域常规知识制备;如加氢脱硫活性高的催化剂可以使用一般以氧化铝或含硅氧化铝为载体,mo、co为加氢活性组分。以催化剂的重量为基准,金属mo含量以氧化物计为6wt%~20wt%,金属co含量以氧化物计为1wt%~12wt%。
[0028]
加氢反应过程大多数属于放热反应,加氢过程主要存在如下问题:(1)由于反应进料中反应物浓度高,所以前期反应的过程推动力较大,因此存在反应放热剧烈、放热不均匀、温升大、过程不易控制等问题,因此需要解决反应前期集中放热的问题;(2)而在反应后期,由于反应温度高,若仍然在高活性催化剂上发生加氢反应,造成副反应速率快、裂解反应严重、催化剂结焦等问题,因此反应后期应采用适当稍低活性的催化剂,以控制反应速率;(3)由于加氢反应过程放热,物料在催化剂表面的停留时间与副反应及裂解反应程度有着很大的关系,停留时间长,则副反应及裂解反应严重,因此有效控制物料在催化剂表面的停留时间的合理停留时间十分重要;(4)反应气体是随着加氢反应的逐渐进行而不断产生的,只要反应发生,就产生反应气体,而反应气体对反应转化率又具有一定的抑制作用,因此反应过程实现边反应、边汽提有利于提高反应转化率和加氢反应深度;(6)加氢反应过程不断消耗氢气,原料中原来溶解的氢气随着反应的进行,其分散状态已经逐渐发生了变化,导致油品分子周围溶解的氢气气泡已经发生了反应,那些没有发生反应的气泡逐渐聚结为大气泡,使油品在加氢反应过程中不能持续的提供氢气,而降低反应氢的持续推动力,降低反应速率,因此在反应过程中需要全程补充高分散状态的溶解氢。
[0029]
本发明通过特殊的液相加氢反应器结构及加氢工艺,有效控制加氢反应整个过程中物料与催化剂的接触时间,使催化剂床层温升更加均匀,解决反应过程中放热剧烈、反应产物抑制反应转化率的问题,实现整个反应过程都达到较高的加氢反应速率和反应转化率,提高液相加氢反应器的整体反应效率。液相加氢反应器中,利用“锥形”结构由上而下截面积逐渐增加的特点,实现随着反应的进行,内筒截面积逐渐增加,物料与催化剂呈渐进式接触,防止反应前期加氢原料浓度较高时发生剧烈反应而造成放热不均的问题;“锥形”内筒筒壁开孔,内筒由上而下竖直设置陶瓷膜管束用于补氢和氢气扩散,扩散氢气推动内筒物料向环形腔体扩散,控制物料在内筒催化剂表面的停留时间,并使物料及时带走反应热,有利于减缓催化剂表面结焦,使反应过程温升均匀,减少副反应和裂解反应;另外,在“锥形”内筒中处于反应前期阶段,由于反应原料浓度高,反应推动力大,因此采用适当偏高活
性的催化剂,进一步提高反应速率;在整个加氢反应过程中,通过陶瓷膜管束持续补充氢气,达到整个反应过程中消耗的氢气能够及时得到补充,增加整个加氢反应过程推动力和高加氢反应速率;而环形腔体内,由于反应物浓度低,反应推动力小,但反应温度高,因此采用活性低于内筒的催化剂,控制副反应和裂解反应;环形腔体内,在扩散氢气推动内筒物料至环形腔体的过程的同时,对物料进行了汽提,达到同时进行反应和汽提的效果,提高加氢反应深度。
附图说明
[0030]
图1是本发明的液相加氢反应器及加氢工艺的示意图。
[0031]
1为氢气,2为原料油,3为氢油混合器,4为液相加氢反应器进料,5为与陶瓷膜管束连接的氢气管线,6为液相加氢反应器,7为加氢反应产物,8为反应产物出料阀;9为排放气,10为排气控制阀,11为催化剂压盖格栅,12为催化剂支撑格栅,13为锥形内筒,14为加氢催化剂i,15为环形腔体,16为加氢催化剂ii,17位内筒筒壁;18为陶瓷膜管束,19为陶瓷膜管束支撑构件。
具体实施方式
[0032]
下面结合附图说明和实施例对本发明进行详细说明,但不因此限制本发明。
[0033]
以附图1说明本发明的液相加氢反应器及加氢工艺:原料油2与氢气1经氢油混合器3混合后,作为液相加氢反应器进料4从加氢反应器6的顶部进入液相加氢反应器6后,首先进入锥形内筒13,由下而上依次经过加氢催化剂i进行加氢反应;氢气5经液相加氢反应器6的上部进入陶瓷膜管束18,液相加氢反应器6轴向上从反应器顶部到锥形内筒13底部之间竖直设置陶瓷膜管束18,陶瓷膜管束18连通外部氢气5,陶瓷膜管束18。加氢反应过程中,液相加氢反应器进料4经内筒13由上而下流动,与内筒13装填的加氢催化剂i 14进行加氢反应,氢气5由氢气管线进入陶瓷膜膜管管束18的管内,在反应过程中氢气由陶瓷膜膜管18的管内渗透扩散至管外,,物料反应过程中在陶瓷膜管束18扩散出的氢气推动下,部分物料经内筒筒壁上的开孔流入环形腔体,与加氢催化剂ii 16发生进一步的加氢反应,反应过程中扩散氢气同时进行了汽提作用,汽提出来的反应气体在排气控制阀10的压控下经排放气9排出;最终的反应产物8在反应产物出料阀8的控制下离开加氢反应器6。其中,陶瓷膜管束18包含多根陶瓷膜膜管,膜管的上、下两端分别通过刚结构支撑件固定在液相加氢反应器6的上、下封头的内表面,内筒13由上至下均匀设置固定支撑卡件,将陶瓷膜管束18固定在内筒13的内表面。
[0034]
本发明对比例及实施例中采用的原料油1为来自某厂连续重整装置的重整生成油,将重整生成油与氢气引入本发明的液相加氢反应器发生加氢脱烯烃反应;原料2为来自某厂的直馏柴油,将直馏柴油与氢气引入本发明的液相加氢反应器发生脱硫脱氮反应,具体性质分别见表1和表2。
[0035]
表1 原料油1的组成
表2 原料油2的性质对比例1采用常规固定床液相加氢反应器及加氢方法,氢油混合设备采用静态混合器,型号为:sx-2.3-10.0-500;反应器进料中氢气的给量为原料油(新鲜原料油与循环油之和)质量的0.11%。液相加氢反应器内物料为上进下出,内部填装的催化剂为抚顺石油化工研究院的fhdo-18。
[0036]
固定床液相加氢反应条件如下:反应温度为121~131.6℃,反应压力为1.8mpag,液时体积空速为10.0h-1
。
[0037]
以表1中的重整生成油为原料,经过固定床液相加氢脱烯烃后得到反应产品,反应条件及产品性质见表3。
[0038]
对比例2采用常规固定床液相加氢反应器及加氢方法,氢油混合设备采用静态混合器,型号为:sx-2.3-10.0-500;反应器进料中氢气的给量为原料油(新鲜原料油与循环油之和)质量的0.63%。液相加氢反应器采用的催化剂为抚顺石油化工研究院的fhuds-5。
[0039]
固定床液相加氢反应条件如下:反应温度为330~375℃,反应压力为6.0mpag,液时体积空速为4.0h-1
,循环比为1.5~2.0。
[0040]
以表2中的直馏柴油为原料,经过固定床液相加氢后得到反应产品,反应条件及产品性质见表4。
[0041]
实施例1采用附图1所述的方法,液相加氢反应器锥形内筒采用的催化剂为抚顺石油化工研究院的fhdo-18,环形腔体采用的催化剂为fhdo-10;液相加氢反应器进料中含有的氢气为原料油质量的0.015%,液相加氢反应器氢气扩散组件的补氢量为进料原料油的质量的0.112%;液相加氢反应器锥形内筒的反应条件如下:反应温度为121.2~124.7℃,反应压力为1.8mpag,液时体积空速为15.0h-1
;环形腔体的反应条件如下:反应温度为124.7~128.1℃,反应压力为1.75mpag,液时体积空速为7.0h-1
。反应器内锥形内筒的顶部平面直径与反应器的直径之比为1:1.5。
[0042]
原料油从加氢反应器顶部进入锥形内筒,由下而上依次经过加氢催化剂fhdo-18发生加氢反应,氢气自氢气扩散组件进入后扩散至锥形内筒,推动锥形内筒的物料向环形腔体流动,进入环形腔体的物料在加氢催化剂fhdo-10发生进一步的加氢反应,反应过程中同时进行了汽提,汽提出的反应气体在反应器顶部排出。
[0043]
以表1中的重整生成油为原料,经过固定床液相加氢脱烯烃后得到反应产品,反应条件及产品性质见表3。
[0044]
实施例2采用附图1所述的方法,液相加氢反应器锥形内筒采用的催化剂为抚顺石油化工研究院的fhdo-10,环形腔体采用的催化剂为fhdo-6;液相加氢反应器进料中含有的氢气为原料油质量的0.012%,液相加氢反应器氢气扩散组件的补氢量为进料原料油的质量的0.117%。液相加氢反应器锥形内筒的反应条件如下:反应温度为122.4~125.8℃,反应压力为1.8mpag,液时体积空速为12.0h-1
;环形腔体的反应条件如下:反应温度为125.8~129.2℃,反应压力为1.75mpag,液时体积空速为8.8h-1
。反应器内锥形内筒的顶部平面直径与反应器的直径之比为1:3。
[0045]
原料油从加氢反应器顶部进入锥形内筒,由下而上依次经过加氢催化剂fhdo-10发生加氢反应,氢气自氢气扩散组件进入后扩散至锥形内筒,推动锥形内筒的物料向环形腔体流动,进入环形腔体的物料在加氢催化剂fhdo-6发生进一步的加氢反应,反应过程中同时进行了汽提,汽提出的反应气体在反应器顶部排出。
[0046]
以表1中的重整生成油为原料,经过固定床液相加氢脱烯烃后得到反应产品,反应条件及产品性质见表3。
[0047]
实施例3采用附图1所述的方法,液相加氢反应器锥形内筒采用的催化剂为抚顺石油化工研究院的fhdo-18,环形腔体采用的催化剂为fhdo-6;液相加氢反应器进料中含有的氢气为原料油质量的0.025%,液相加氢反应器氢气扩散组件的补氢量为进料原料油的质量的0.104%。液相加氢反应器锥形内筒的反应条件如下:反应温度为120.7~124.2℃,反应压力为1.8mpag,液时体积空速为12.0h-1
;环形腔体的反应条件如下:反应温度为124.2~127.5℃,反应压力为1.75mpag,液时体积空速为6.0h-1
。反应器内锥形内筒的顶部平面直径与反应器
的直径之比为1:5。
[0048]
原料油从加氢反应器顶部进入锥形内筒,由下而上依次经过加氢催化剂fhdo-18发生加氢反应,氢气自氢气扩散组件进入后扩散至锥形内筒,推动锥形内筒的物料向环形腔体流动,进入环形腔体的物料在加氢催化剂fhdo-6发生进一步的加氢反应,反应过程中同时进行了汽提,汽提出的反应气体在反应器顶部排出。
[0049]
以表1中的重整生成油为原料,经过固定床液相加氢脱烯烃后得到反应产品,反应条件及产品性质见表3。
[0050]
表3 反应条件及产品性质实施例4采用附图1所述的方法,液相加氢反应器锥形内筒采用的催化剂为抚顺石油化工研究院的fhuds-2,环形腔体采用的催化剂为fh-40c;液相加氢反应器进料中含有的氢气为原料油(新鲜原料油与循环油之和)质量的0.18%,液相加氢反应器氢气扩散组件的补氢量为进料原料油的质量的0.48%。加氢反应器锥形内筒的反应条件如下:反应温度为305~325℃,反应压力为6.0mpag,液时体积空速为6.0h-1
;环形腔体的反应条件如下:反应温度为325~346℃,反应压力为5.8mpag,液时体积空速为4.5h-1
。反应器内锥形内筒的顶部平面直径与反应器的直径之比为1:1.8。
[0051]
液相加氢反应器的进料从反应器顶部进入锥形内筒,由上而下依次经过加氢催化剂fhuds-2上发生加氢反应后,氢气自氢气扩散组件进入后扩散至锥形内筒,推动锥形内筒的物料向环形腔体流动,进入环形腔体的物料在加氢催化剂fh-40c发生进一步的加氢反应,反应过程中同时进行了汽提,汽提出的反应气体在反应器顶部排出。
[0052]
以表2中的直馏柴油为原料,经过固定床液相加氢后得到反应产品,反应条件及产品性质见表4。
[0053]
实施例5采用附图1所述的方法,液相加氢反应器锥形内筒采用的催化剂为抚顺石油化工研究院的fhuds-5,环形腔体采用的催化剂为fh-40c;液相加氢反应器进料中含有的氢气为原料油(新鲜原料油与循环油之和)质量的0.20%,液相加氢反应器氢气扩散组件的补氢量为进料原料油的质量的0.45%。加氢反应器锥形内筒的反应条件如下:反应温度为305~325℃,反应压力为6.0mpag,液时体积空速为7.0h-1
;环形腔体的反应条件如下:反应温度为325~345℃,反应压力为5.8mpag,液时体积空速为4.0h-1
。反应器内锥形内筒的顶部平面直径与反应器的直径之比为1:3。
[0054]
液相加氢反应器的进料从反应器顶部进入锥形内筒,由上而下依次经过加氢催化剂fhuds-5发生加氢反应后,氢气自氢气扩散组件进入后扩散至锥形内筒,推动锥形内筒的物料向环形腔体流动,进入环形腔体的物料在加氢催化剂fh-40c发生进一步的加氢反应,反应过程中同时进行了汽提,汽提出的反应气体在反应器顶部排出。
[0055]
以表2中的直馏柴油为原料,经过固定床液相加氢后得到反应产品,反应条件及产品性质见表4。
[0056]
实施例6采用附图1所述的方法,液相加氢反应器锥形内筒采用的催化剂为抚顺石油化工研究院的fhuds-5,环形腔体采用的催化剂为fhuds-2;液相加氢反应器进料中含有的氢气为原料油(新鲜原料油与循环油之和)质量的0.20%,液相加氢反应器氢气扩散组件的补氢量为进料原料油的质量的0.44%。加氢反应器锥形内筒的反应条件如下:反应温度为310~330℃,反应压力为6.0mpag,液时体积空速为7.0h-1
;环形腔体的反应条件如下:反应温度为330~349℃,反应压力为5.8mpag,液时体积空速为6.5h-1
。反应器内锥形内筒的顶部平面直径与反应器的直径之比为1:5。
[0057]
液相加氢反应器的进料从反应器顶部进入锥形内筒,由上而下依次经过加氢催化剂fhuds-5发生加氢反应后,氢气自氢气扩散组件进入后扩散至锥形内筒,推动锥形内筒的物料向环形腔体流动,进入环形腔体的物料在加氢催化剂fh-40c发生进一步的加氢反应,反应过程中同时进行了汽提,汽提出的反应气体在反应器顶部排出。
[0058]
以表2中的直馏柴油为原料,经过固定床液相加氢后得到反应产品,反应条件及产品性质见表4。
[0059]
表4反应条件及产品性质由本实施例及对比例的加氢反应效果可以看出,当本发明的液相加氢反应器用于重整生成油液相加氢脱烯烃反应时,反应器温升明显降低,产品溴指数和芳烃损失都明显减小;当本发明的液相加氢反应器用于柴油液相加氢时,温升和产品中硫氮含量都显著降低。可以看出,本发明的液相加氢反应器,利用“锥形”内筒由上而下截面积逐渐增加的特点,控制物料与催化剂成渐进式接触,防止反应前期加氢原料浓度较高时发生剧烈反应而造成放热不均的问题,既能保证反应速率又能有效控制反应活性;通过氢气扩散组件扩散出的氢气推动物料由内筒向环形腔体扩散,有利于缩短内筒物料在催化剂表明的停留时间,减少副反应和裂解反应,并及时带走反应热,使温升更加均匀;反应过程中氢气扩散组件扩散出的氢气同时起到了汽提作用,实现边反应、边汽提的功能,提高反应深度和转化率。另外,在“锥形”内筒的反应前期,由于反应原料浓度高,反应推动力大,因此反应前期阶段采用适当偏高活性的催化剂,进一步提高反应速率,反应过程中通过陶瓷膜纳/微米氢分散组件提供氢气,使反应过程中消耗的氢气及时得到补充,增加加氢反应过程推动力,保持整个反应过程都达到较高的加氢反应速率。