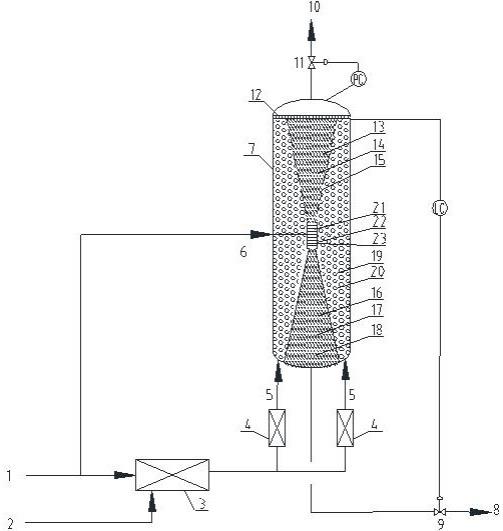
1.本发明属于石油化工领域,具体地涉及为一种重油加氢反应器及加氢方法。
背景技术:2.随着原油重质化、劣质化趋势的加氢,重质原油、二次加工油的比例越来越高,因此重油加氢处理技术成为加氢过程研究的热点之一。重油加氢反应器分为多种类型,如固定床加氢反应器、悬浮床加氢反应器、沸腾床加氢反应器等,以固定床加氢反应器的应用最为广泛,能够处理多种类型的重质油品。
3.在重油加氢工艺中,液相加氢工艺过程相比于传统的固定床气/液/固三相加氢工艺而言,具有加氢反应速率快、反应效率高、催化剂利用率高、能耗低、投资少等诸多优势,得到广泛应用。但是,重油液相加氢反应器及反应过程中中仍然存在如下问题:(1)重油黏度大,氢油传质速率低,导致加氢反应速率低;(2)重油加氢过程的催化剂一般需要级配,即需要多种功能和多种活性的催化剂之间组合,但是无论是选择低活性和高活性催化剂,仍然存在催化剂活性高的催化剂表面由于停留时间和热量转移的问题而使副反应或裂解反应严重,导致催化剂容易结焦、液体收率低的问题;(3)重油加氢过程比轻质油加氢过程的难度大很多,尤其是杂质如硫、氮、金属含量都非常高,反应器尤其在反应前期,反应物杂质浓度高,反应推动力大,反应剧烈,造成集中放热、温升不均匀的问题,因此控制原料与催化剂缓慢接触非常重要;(4)基于重油原料的杂质含量高,达到深度脱除非常困难,尤其到反应后期,气体产物对转化率的抑制作用更加明显。因此,对于重油液相加氢反应过程来说,采用有效的手段,如开发新的加氢工艺及反应器结构,提高加氢反应速率和反应转化深度,解决集中放热、温升不均匀的问题,减少副反应或裂解反应,提高液体收率,具有重要意义。
4.cn 109306272a提出了一种重油加氢处理系统,该重油加氢处理系统包括主反应器和至少一个子反应器,主反应器包括第一筒体,第一筒体用于盛放物料,子反应器包括:混合单元,用于将物料和氢气混合,混合单元包括第二筒体,第二筒体上设置有物料入口、氢气入口和第一出口,物料入口与第一筒体的出口连通;强化装置,强化装置的入口与第二筒体的第一出口连通,强化装置的出口与第一筒体的容纳腔连通,强化装置用于给物料提供能量以使物料发生裂化反应。
5.cn 108659882 a提出了一种重油加氢方法及其加氢系统,其中,所述重油加氢方法包括:将重油、循环油、硫化剂和催化剂混合,与氢气在第一反应器中进行加氢裂化,得到第一反应产物;将第一反应产物的部分物料返回第一反应器中,将其余物料在第二反应器中进行加氢裂化,得到第二反应产物;将第二反应产物分离为轻组分和重组分,将部分重组分返回第二反应器中,将其余重组分分离得到馏分油做为循环油;将轻组分在第三反应器中进行加氢精制得到轻油产品。该发明方法主要是为了提高传热、传质效率,保证物料在反应器内足够的停留时间,提高重油转化率和轻质油收率,但只是通过常规的加氢反应器结构,更不能有效的控制催化剂与原料的接触时间,也不能保证重油转化率和轻质油收率。
6.综上所述,现有技术中的重质油加氢反应器,大多思路都是通过现有设备改进工艺、增加物料停留时间等方法来提高加氢反应效率,没有解决重油液相加氢反应过程存在的反应速率低、转化深度不足、温升不均匀的问题,以及停留时间长造成的液体收率低、副反应及裂解反应严重等问题。
技术实现要素:7.针对现有技术的不足,本发明提供一种重油加氢反应器及加氢方法,通过在特殊结构的反应器设置以及在不同位置匹配加氢活性不同的催化剂,提高了重油液相加氢反应过程的传质推动力和反应速率,减缓催化剂表面结焦,减少副反应和裂解反应。
8.本发明的重油加氢反应器,包含反应器外筒、内筒i、补氢组件和内筒ii;所述的反应器外筒包括上封头、直筒段和下封头,内筒i、补氢组件和内筒ii自上而下沿反应器轴向设置,内筒i由上而下横截面积逐渐减小,内筒ii由上至下横截面积逐渐增大,内筒i、内筒ii和反应器外筒之间构成环形空腔;内筒i顶部敞口经上封头与环形空腔连通,内筒ii底部反应器下封头内壁密闭连接;所述的内筒i装填加氢催化剂i,内筒ii装填加氢催化剂ii,环形空腔装填加氢催化剂iii,加氢催化剂的活性顺序为加氢催化剂iii>加氢催化剂ii>加氢催化剂i;所述补氢组件为管壳式陶瓷膜管,陶瓷膜管侧与氢气管线连通,管外空腔与内筒i底部和内筒ii顶部分别连通;反应器进料口与环形空腔底部连通,反应器产物出口与内筒ii底部连通。
9.本发明的重油加氢反应器,所述的内筒i最大横截面直径与反应器的直径之比为1:1.05~1:50,优选1:1.5~1:5;所述的内筒ii底部最大横截面直径与反应器的直径之比为1:1.05~1:50,优选1:1.5~1:5。
10.本发明的重油加氢反应器中,所述的补氢组件内的陶瓷膜管的数量可以根据需要进行设置,所述的陶瓷膜管能够将外部通入的氢气由管内向管外通过管壁形成的纳/微米气泡,气泡尺寸一般为10~1000nm,优选为50~500nm。
11.本发明的重油加氢反应器中,内筒i的筒壁优选设置若干开孔,开孔均匀分布,内筒开孔面积与内筒i表面积的比为1:1.05~1:10,优选1:1.15~1:3;孔径大小一般为0.1mm~50mm,优选5~15mm。
12.本发明的重油加氢反应器,顶部为反应器上封头,底部为反应器下封头,反应进料首先进入环形空腔,由下而上在环形空腔发生加氢反应;内筒i筒壁开孔,物料在环形空腔经过一定的反应停留时间后,经由内筒i的筒壁和顶部封头处扩散至内筒,目的是使重油加氢反应在高活性催化剂表面的停留时间不宜过长,即达到了需要的转化深度,又减少了副反应和裂解反应,提高液体收率。
13.本发明的重油加氢反应器中,所述的反应器顶部有气体空间,反应器顶部封头最高点处设置气体出口,用于连续或间断排放反应过程中汽提出的反应气体。
14.本发明的重油加氢反应器中,反应器上部通过液位控制出料,保证重油加氢反应过程为全液相加氢。
15.本发明的重油加氢方法,包括如下内容:含有氢气的重油原料经减黏处理后自反应器底部进料口进入环形空腔,自下而上与环形空腔装填的加氢催化剂iii进行加氢反应,反应后的物料经内筒i筒壁和反应器上封头进入内筒i,自上而下与内筒i内装填的加氢催
化剂i发生进一步加氢反应,反应后的物料进入补氢组件中管壳式陶瓷膜管的管外空腔,与管内扩散出的氢气混合,进行补充氢气和对反应物料汽提,然后进入内筒ii装填的加氢催化剂ii发生深度加氢反应,最终的反应产物自反应器内筒ii底部的产物出口排出。
16.本发明方法中,所述的重油主要是指重质油品,一般是指比重≥0.91、黏度大且流动性差的稠油,如减压渣油、蜡油、煤焦油、润滑油、蒽油、脱沥青油、生物柴油、动物油或植物油等油品。
17.本发明方法中,所述的含氢气的重油原料一般通过氢油混合设备进行混合然后将氢油混合物料进行减黏处理得到的,氢油混合设备如采用静态混合器、溶气泵、胶体磨、微孔板纳/微米氢分散组件、陶瓷膜纳/微米氢分散组件等具有气液混合功能的设备;含氢气的重油原料中,氢气质量含量一般为重油原料质量的0.01wt%~20%,优选1.0wt%~10.0wt%。
18.本发明方法中,所述的减黏处理,可以采用加入一定量减黏剂的方法进行减黏,如三聚磷酸钠、六偏磷酸钠、水玻璃、聚丙烯酰胺、水解聚丙烯酰胺、胍胶、聚氧化乙烯、羧甲基纤维素钠盐、羟乙基纤维素等等任意一种减黏剂或多种配制成复合减黏剂,也可以利用水力空化设备进行减黏。水力空化设备的原理是物料首先溶解大量的氢气气体,而后将气体释放出来,在此过程中气泡破裂,在气泡破裂过程中产生能量极大的冲击波,从而降低物料的黏度,改善物料的流动性;采用水力空化设备可以采用管径或物料流道截面积有急剧变化的管道或设备。
19.本发明方法中,补氢组件的氢气通入量(nm3/h)与进料原料油通入量(m3/h)的体积比为1:1~1000:1,优选1:10~1:150。
20.本发明方法中,反应器内筒设置的补氢组件中,氢气进入陶瓷膜管后由管内向管外空腔扩散,扩散出的氢气与来自内筒i的物料接触,一方面氢气溶解分散到该物料中作为补充氢气,再进入内筒ii发生深度加氢反应,另一方面,氢气可以将该物料中的反应气体进行汽提,汽提出的反应气体扩散至反应器顶部而排出,经汽提后的物料进入内筒下段发生深度加氢反应,有利于提高加氢反应深度。
21.本发明方法中,所述的环形空腔的加氢反应条件为:反应温度120~500℃,优选280~430℃;反应压力0.5~20.0mpa,优选6.0~15.0mpa;新鲜进料液时体积空速0.1~15.0h-1
,优选0.5~10.0h-1
。
22.本发明方法中,所述内筒i的加氢反应条件为:反应温度 120~550℃,优选300~450℃;反应压力0.5~20.0mpa,优选6.0~15.0mpa;新鲜进料液时体积空速0.1~10.0h-1
,优选0.5~6.0h-1
;所述内筒ii的加氢反应条件为:反应温度 150~600℃,优选320~480℃;反应压力0.5~20.0mpa,优选6.0~15.0mpa;新鲜进料液时体积空速0.01~6.0h-1
,优选0.1~4.0h-1
。
23.本发明方法中,优选加氢催化剂i的活性与加氢催化剂ii和iii的活性之比为1:1.05:1.1~1:10:100。其中所述的活性高低是针对内筒i、内筒ii和环形空间发生的化学反应而言的,是以每单位容积(或质量)催化剂在单位时间内转化原料反应物的数量来表示,催化活性的高低可以通过催化剂载体比表面积的大小、表面上活性中心的性质和单位表面积上活性中心的数量等进行选择或制备过程中进行调控。催化剂活性的评价方法如下:在相同的原料组成和反应条件下,同体积催化剂在同一套装置上进行加氢反应,经过相同的
停留时间后测定产物组成数据,计算转化率比较大小,作为判断活性高低的依据。
24.本发明方法中,所述的重油加氢反应器采用的催化剂可以根据反应的需要使用适宜的加氢催化剂,实现不同的加氢目的,如加氢精制催化剂、预加氢精制催化剂、加氢改质催化剂、选择性加氢催化剂、加氢处理催化剂、加氢裂化催化剂、补充加氢催化剂等,各种催化剂可以选择商品催化剂,也可以根据现有技术制备。加氢反应可以脱除部分或全部烃类原料中的硫、氮、氧、砷、金属、残碳等杂质,或饱和/部分饱和烯烃、芳烃、二烯烃,或发生烃类分子异构化、烷基化、环化、芳构化、裂化、裂解等反应加氢催化剂i和加氢催化剂ii中均各自独立地含有载体和活性组分,所述活性组分选自第vib族和/或第viii族金属元素中的至少一种,所述载体为氧化铝和/或含硅氧化铝,第vib族金属元素一般为mo和/或w,第viii族金属元素一般为co和/或ni。优选地,加氢催化剂i和加氢催化剂ii中,以加氢催化剂的总量为基准,以氧化物计,第vib族金属元素的含量为5~40wt%,第viii族金属元素的含量为3~15wt %。
25.本发明方法中,所述环形空间可以装填活性全部或部分高于内筒i活性的加氢催化剂,内筒i可以装填活性全部或部分高于内筒ii活性的加氢催化剂。所述反应器填装的加氢催化剂i、加氢催化剂ii、加氢催化剂iii优选采用现有重油加氢装置所采用的催化剂,如抚顺石油化工研究院研制开发的3936、3996,ff-16、ff-24、ff-26、ff-36、ff-46、ff-56加氢处理、uop公司的hc-k、hc-p催化剂、topsoe公司的tk-555、tk-565催化剂、akzo公司的kf-847、kf-848催化剂。
26.一般的重质油加氢反应过程来说,首先,重质油具有密度大、粘稠的特点,在加氢过程中由于氢油传质界面阻力大,造成反应速率低、脱杂质深度不足的缺点,因此如何减小氢油传质界面阻力是提高重油加氢反应速率的关键因素;第二,在加氢反应前期,基于原料中杂质组份浓度最高,加氢反应的推动力大,因此应采用高活性的催化剂,尽量提高反应前期的加氢反应速率;第三,在加氢反应中、后期,反应温度高,重质油加氢原料在催化剂表面的停留时间长会导致副反应及裂解反应严重、液体收率低的问题,因此反应物在反应达到一定的停留时间后要及时离开催化剂表面,减少进一步的副反应和深度裂解反应;第四,反应最后阶段,反应生成的抑制转化率的气体要及时的汽提出来,物料补充氢气后再继续发生深度加氢反应,有利于提高加氢反应深度。在催化剂选择方面,反应前期采用高活性的催化剂,发生低温快速反应,可以尽量提高反应前期的加氢反应速率;反应中期采用低偏低活性催化剂,发生高温慢速反应,防止高温阶段副反应及裂解反应严重;反应后期采用比前期活性低、中期活性高的催化剂,可以在汽提出反应产物发生深度加氢反应。
27.本发明通过特殊的重油加氢反应器结构及加氢反应方法,使物料黏度降低后依次经过环形空间、内筒i、内筒ii发生加氢反应,能够提高重油液相加氢反应的传质过程推动力和反应速率,控制反应物料与不同活性催化剂的接触时间,减缓催化剂表面结焦,减少轻质油深度裂解反应,促进重质油的加氢转化率,提高重油液相加氢反应过程的液体收率和重质脱杂质转化率。加氢反应器包含反应器外筒、内筒i、补氢组件和内筒ii,内筒与反应器外壳之间为环形空腔,环形空腔与内筒i通过内筒i筒壁开孔的方式相连通,物料经环形空间腔的高活性催化剂接触反应达到一定的停留时间后,能够及时扩散至内筒i,减少副反应和深度裂解反应;内筒i由上而下横截面积逐渐减小,可以减少物料在内筒上段的停留时间,进一步减高温区域的副反应和深度裂解反应;物料经过内筒i、内筒ii连接处设置的补
氢构件进行补氢和汽提后,一方面为深度加氢反应进行补氢,另一方面将抑制反应转化率的气体汽提出来,有利于后续的深度加氢反应;最后,物料进入内筒下段发生深度加氢反应。
附图说明
28.图1是本发明的重油加氢反应器及加氢方法的示意图。
29.1为氢气,2为原料油,3为氢油混合器,4为减黏设备,5为加氢反应器进料,6为与陶瓷膜管连接的氢气管线,7为重油加氢反应器,8为反应产物,9为反应产物出料阀,10为反应器排放气,11为排气控制阀,12为催化剂压盖格栅,13为内筒i,14为加氢催化剂i,15为内筒i的筒壁,16为内筒ii,17为内筒ii的筒壁,18为加氢催化剂ii,19为外筒,20为加氢催化剂iii,21为补氢组件,22补氢组件的壳体,23为陶瓷膜管。
具体实施方式
30.下面结合附图说明和实施例对本发明进行详细说明,但不因此限制本发明。
31.以附图1说明本发明的重油加氢反应器及加氢方法:原料油2与氢气1经氢油混合器3混合后,进入减黏设备4降低物料黏度后,作为加氢反应器进料5自重油加氢反应器7的底部进入重油加氢反应器6,首先进入环形空间19,由下而上经过加氢催化剂iii 20进行加氢反应,经过一定的停留时间后经由内筒i13的筒壁15扩散至外筒19;进入内筒i13的物料,由上而下与内筒i的加氢催化剂i 14发生进一步的加氢反应;反应物料进入补氢组件21,氢气经与陶瓷膜管连接的氢气管线6进入补氢组件21中的陶瓷膜管,来自于内筒i的物料进行补氢和汽提后进入内筒ii16,由上而下与内筒ii填装的加氢催化剂ii 18发生深度加氢反应,最终的反应产物8经反应产物出料阀9的控制下离开重油加氢反应器7;反应过程汽提出的反应气体在反应器顶部排气控制阀11的作用下作为排放气10排出。
32.本发明对比例及实施例中采用的原料油为来自某厂的蜡油混合原料,具体性质见表1。
33.表1 蜡油原料性质
对比例1以表1所示的蜡油混合原料作为加氢反应进料,采用常规气、液、固三相固定床加氢反应器及加氢方法,催化剂采用3个床层,两个床层高度相同,第一床层填装抚顺石油化工研究院开发的fzc保护剂/3996催化剂,第二床层填装抚顺石油化工研究院开发的3936催化剂,第三床层填装抚顺石油化工研究院开发的ff-46催化剂,其中第一床层中的fzc保护剂为3996催化剂床层高度的15%,3996和ff-26催化剂分别占总催化剂床层高度的45%和40%。
34.加氢反应条件如下:平均反应温度为380~427℃,反应压力为15mpag,液时体积空速为0.80h-1
,反应器入口氢油体积比为400。
35.以表1中的混合蜡油为原料,经过气、液、固三相固定床加氢反应器加氢后得到反应产品,催化剂床层温度分布见表2,液体产品性质见表3。
36.实施例1采用附图1所述的方法,重油加氢反应器外筒填装的催化剂iii采用抚顺石油化工研究院开发的fzc保护剂/ff-46催化剂,其中fzc保护剂为外筒总催化剂体积的15%,内筒i填装的催化剂i采用抚顺石油化工研究院开发的3936催化剂,内筒ii填装的催化剂ii采用抚顺石油化工研究院开发的3996催化剂。
37.重油加氢反应器进料中含有的氢气为原料油(新鲜原料油与循环油之和)质量的8.66%;加氢反应器补氢组件中氢气通入量为原料油(新鲜原料油与循环油之和)质量的3.28%;循环比为2.5。
38.加氢反应器外筒的反应条件如下:反应温度为380~390℃,反应压力为15.0mpag,液时体积空速为2.5h-1
;加氢反应器内筒i的反应条件如下:反应温度为390~396℃,反应压
力为14.7mpag,液时体积空速为1.5h-1
;加氢反应器内筒ii的反应条件如下:反应温度为396~400℃,反应压力为14.5mpag,液时体积空速为0.8h-1
。
39.加氢反应器内筒i最大横截面直径与反应器的直径之比为1:2,内筒i筒壁上部均匀开设φ10的圆孔,开孔面积与内筒i表面积的比为1:1.15。
40.以表1中的混合蜡油为原料,经过本发明的重油加氢反应器加氢后得到反应产品,催化剂床层温度分布见表2,液体产品性质见表4。
41.实施例2采用附图1所述的方法,重油加氢反应器外筒填装的催化剂iii采用抚顺石油化工研究院开发的fzc保护剂/ff-46催化剂,其中fzc保护剂为外筒总催化剂体积的15%,内筒i填装的催化剂i采用抚顺石油化工研究院开发的3996催化剂,内筒ii填装的催化剂ii采用抚顺石油化工研究院开发的ff-26催化剂。
42.重油加氢反应器进料中含有的氢气为原料油(新鲜原料油与循环油之和)质量的9.66%;加氢反应器补氢组件中氢气通入量为原料油(新鲜原料油与循环油之和)质量的2.75%;循环比为2.8。
43.加氢反应器外筒的反应条件如下:反应温度为378~389℃,反应压力为15.0mpag,液时体积空速为2.5h-1
;加氢反应器内筒i的反应条件如下:反应温度为389~397℃,反应压力为14.7mpag,液时体积空速为1.8h-1
;加氢反应器内筒ii的反应条件如下:反应温度为397~400℃,反应压力为14.5mpag,液时体积空速为1.0h-1
。
44.加氢反应器内筒i最大横截面直径与反应器的直径之比为1:1.5,内筒i筒壁上部均匀开设φ8的圆孔,开孔面积与内筒i表面积的比为1:1.2。
45.以表1中的混合蜡油为原料,经过本发明的重油加氢反应器加氢后得到反应产品,催化剂床层温度分布见表2,液体产品性质见表5。
46.实施例3采用附图1所述的方法,重油加氢反应器外筒填装的催化剂iii采用抚顺石油化工研究院开发的fzc保护剂/ff-46催化剂,其中fzc保护剂为外筒总催化剂体积的15%,内筒i填装的催化剂i采用抚顺石油化工研究院开发的3996催化剂,内筒ii填装的催化剂ii采用topsoe公司开发的tk-555催化剂。
47.重油加氢反应器进料中含有的氢气为原料油(新鲜原料油与循环油之和)质量的8.80%;加氢反应器补氢组件中氢气通入量为原料油(新鲜原料油与循环油之和)质量的3.15%;循环比为2.5。
48.加氢反应器外筒的反应条件如下:反应温度为378~388℃,反应压力为15.0mpag,液时体积空速为2.5h-1
;加氢反应器内筒i的反应条件如下:反应温度为388~397℃,反应压力为14.7mpag,液时体积空速为1.8h-1
;加氢反应器内筒ii的反应条件如下:反应温度为397~400℃,反应压力为14.5mpag,液时体积空速为1.2h-1
。
49.加氢反应器内筒i最大横截面直径与反应器的直径之比为1:2,内筒i筒壁上部均匀开设φ6的圆孔,开孔面积与内筒i表面积的比为1:1.1。
50.以表1中的混合蜡油为原料,经过本发明的重油加氢反应器加氢后得到反应产品,催化剂床层温度分布见表2,液体产品性质见表6。
51.表2催化剂床层温度分布
表3 液体产品性质(对比例1)表4 液体产品性质(实施例1)表5 液体产品性质(实施例2)
表6 液体产品性质(实施例3)