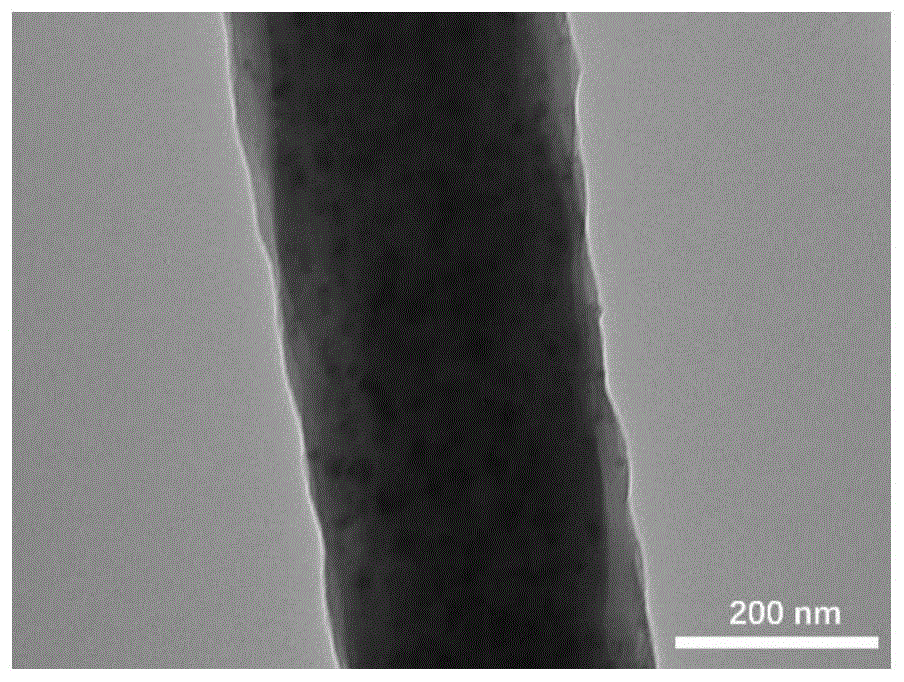
本发明涉及甲醛净化
技术领域:
,具体涉及一种室温甲醛净化用非贵金属掺杂碳纤维膜及其制备方法和应用。
背景技术:
:在现有的甲醛净化方法中,甲醛室温催化氧化分解是净化最为彻底、设备要求低、能耗小的一种方式。因此,室温甲醛氧化催化是最具有大规模应用潜力的甲醛净化技术,也是近年来甲醛分解催化材料的研究热点之一。目前,具有低温催化甲醛氧化性能的催化活性材料主要有贵金属(如铂、钯、金、银等)及其合金以及过渡金属氧化物(如二氧化钛、二氧化锰、氧化铜等)两类。通常,贵金属催化材料,尤其基于铂的催化剂,在常温下具有比金属过氧化物高很多的催化活性,也是近年来备受关注,被深入、广泛研究的一类甲醛降解催化材料。zhang等(参见catalysiscommunications6(3)(2005),211~214)通过浸泡、煅烧获得了二氧化钛负载铂(pt/tio2)粉末状催化剂,其在室温下甲醛的催化转化率高达100%,并且具有较好的稳定性。此外,通过简单的浸泡以及硼氢化钠还原,许多研究者们也在不同的负载材料上获得了高甲醛转化率的负载型铂催化剂。然而,贵金属昂贵的成本使其很难满足日常室内甲醛净化材料或设备使用时限长、使用成本有限的要求,因此极大地限制了负载型贵金属催化剂在实际空气净化或甲醛净化领域的应用。相对于贵金属催化剂,过渡金属氧化物催化剂虽然成本相对较低,但其对甲醛氧化分解反应的催化性能偏低,因而过渡金属氧化物催化剂更多地被应用于光催化甲醛分解。例如,基于tio2的催化颗粒被广泛地应用于甲醛分解喷雾的制备中,利用悬浮于空气中的催化剂颗粒对环境中的甲醛进行光催化降解。但这类光催化材料活性时效较短,应用于空气净化设备时需要额外添高耗能的光源。因此,开发一种既高效又经济、实用的室温甲醛降解催化材料仍然是空气净化领域亟待解决的难题之一。技术实现要素:本发明的目的在于提供一种室温甲醛净化用非贵金属掺杂碳纤维膜及其制备方法和应用,本发明提供的非贵金属掺杂碳纤维膜能够在室温条件下高效地将甲醛分解成无害的二氧化碳和水;而且避免了使用昂贵的贵金属,能有效地降低产品成本。为了实现上述发明目的,本发明提供以下技术方案:本发明提供了一种室温甲醛净化用非贵金属掺杂碳纤维膜的制备方法,包括以下步骤:(1)将聚丙烯腈、非贵金属盐和氮配位物溶于n,n-二甲基甲酰胺中,得到纺丝液;(2)采用静电纺丝法将所述纺丝液制备成纳米纤维膜;(3)将所述纳米纤维膜进行碳化,得到非贵金属掺杂碳纤维膜。优选地,所述聚丙烯腈、非贵金属盐和氮配位物的摩尔比为(6~20):1:(1~4)。优选地,所述非贵金属盐包括非贵金属醋酸盐和/或非贵金属乙酰丙酮盐;所述非贵金属醋酸盐为钴、镍或锌的醋酸盐;所述非贵金属乙酰丙酮盐为钴、镍或锌的乙酰丙酮盐。优选地,所述氮配位物为吡啶、10-邻菲咯啉、咪唑、邻苯二胺和4-二甲氨基吡啶中的一种或几种。优选地,所述聚丙烯腈与n,n-二甲基甲酰胺的用量比为5~10g:100ml。优选地,步骤(2)所述静电纺丝法的具体参数为:纺丝电压为15~28kv;纺丝距离为8~20cm;纺丝液流速为0.5~3ml/h;纺丝收集筒旋转速率为50~150rpm;纺丝温度为20~30℃;纺丝相对湿度为40~60%。优选地,所述碳化的温度为600~700℃,升至碳化所需温度的升温速率为1~5℃/min,所述碳化的时间为30~60min。优选地,在进行所述碳化之前,将所述纳米纤维膜先进行预氧化;所述预氧化的温度为180~300℃,升至预氧化所需温度的升温速率为1~5℃/min,预氧化的时间为10~30min。本发明提供了上述技术方案所述制备方法制备得到的室温甲醛净化用非贵金属掺杂碳纤维膜,厚度为0.1~0.3mm。本发明还提供了上述技术方案所述室温甲醛净化用非贵金属掺杂碳纤维膜在分解甲醛中的应用。本发明提供了一种室温甲醛净化用非贵金属掺杂碳纤维膜的制备方法,包括以下步骤:(1)将聚丙烯腈、非贵金属盐和氮配位物溶于n,n-二甲基甲酰胺中,得到纺丝液;(2)采用静电纺丝法将所述纺丝液制备成纳米纤维膜;(3)将所述纳米纤维膜进行碳化,得到非贵金属掺杂碳纤维膜。本发明采用非贵金属盐与氮配位体所构成的有效催化剂成分能够有效地通过室温氧化反应,快速地将甲醛分解为二氧化碳和水,同时避免了昂贵贵金属的使用,有效提高了产品的可使用性。与现有的室温甲醛处理方法相比,本发明能够采用一种成本低、柔性好、质量轻、空气阻力小、且易操作使用的非贵金属掺杂碳纤维膜实现在室温下快速、高效地分解甲醛;而且本发明制备的非贵金属掺杂碳纤维膜易于回收再利用,具有显著的进步。附图说明图1为本发明实施例1制备的室温甲醛净化用非贵金属掺杂碳纤维膜的透射电镜图;图2为室温甲醛转化率测试设备示意图。具体实施方式本发明提供了一种室温甲醛净化用非贵金属掺杂碳纤维膜的制备方法,包括以下步骤:(1)将聚丙烯腈、非贵金属盐和氮配位物溶于n,n-二甲基甲酰胺中,得到纺丝液;(2)采用静电纺丝法将所述纺丝液制备成纳米纤维膜;(3)将所述纳米纤维膜进行碳化,得到非贵金属掺杂碳纤维膜。在本发明中,若没有特殊说明,所采用的原料均为本领域技术人员所熟知的市售商品。本发明将聚丙烯腈、非贵金属盐和氮配位物溶于n,n-二甲基甲酰胺中,得到纺丝液。在本发明中,所述聚丙烯腈、非贵金属盐和氮配位物的摩尔比优选为(6~20):1:(1~4),更优选为6:1:4。在本发明中,所述聚丙烯腈的平均分子量mw优选为8.5×104~20×104,更优选为15×104;所述非贵金属盐优选包括非贵金属醋酸盐和/或非贵金属乙酰丙酮盐;所述非贵金属醋酸盐优选为钴、镍或锌的醋酸盐;所述非贵金属乙酰丙酮盐优选为钴、镍或锌的乙酰丙酮盐;在本发明的具体实施例中,所述非贵金属盐具体优选为醋酸钴。在本发明中,所述氮配位物优选为吡啶、10-邻菲咯啉、咪唑、邻苯二胺和4-二甲氨基吡啶中的一种或几种,更优选为邻苯二胺或10-邻菲咯啉。在本发明中,所述聚丙烯腈与n,n-二甲基甲酰胺的用量比优选为5~10g:100ml,更优选为8g:100ml。在本发明中,所述聚丙烯腈、非贵金属盐和氮配位物溶于n,n-二甲基甲酰胺中优选在搅拌条件下进行,所述搅拌的速度优选为50~150rpm,更优选为90rpm;所述搅拌的时间优选为12~30h,更优选为24h。在本发明中,所得纺丝液优选为紫色透明溶液。得到纺丝液后,本发明采用静电纺丝法将所述纺丝液制备成纳米纤维膜。在本发明中,优选将所述纺丝液置于注射器中,然后将盛装有纺丝液的注射器固定在纺丝机上,进行静电纺丝。在本发明中,所述静电纺丝用的针头内径优选为0.16~0.51mm,更优选为0.21mm。在本发明中,所述静电纺丝过程中,纺丝电压优选为15~28kv,更优选为22kv;纺丝距离优选为8~20cm,更优选为15cm;纺丝液流速优选为0.5~3ml/h,更优选为1ml/h;纺丝收集筒旋转速率优选为50~150rpm,更优选为100rpm;纺丝温度优选为20~30℃,更优选为25℃;纺丝相对湿度优选为40~60%,更优选为50%。本发明通过限定上述静电纺丝参数,能够得到直径分布均匀的纳米纤维膜。得到纳米纤维膜后,本发明将所述纳米纤维膜进行碳化,得到非贵金属掺杂碳纤维膜。本发明在所述碳化过程中,纳米纤维膜发生交联,形成稠环结构。在本发明中,所述碳化的温度优选为600~700℃,更优选为650~700℃;升至碳化所需温度的升温速率优选为1~5℃/min,更优选为2℃/min;所述碳化的时间优选为30~60min,更优选为30min。在本发明中,所述碳化优选在氮气气氛条件下进行,能够防止材料氧化。本发明在进行所述碳化之前,优选将所述纳米纤维膜先进行预氧化。在本发明中,所述预氧化的温度优选为180~300℃,更优选为220℃;升至预氧化所需温度的升温速率优选为1~5℃/min,更优选为1~3℃/min;预氧化的时间优选为10~30min,更优选为15min。本发明在所述预氧化过程中,聚丙烯腈通过环化、脱氢及氧化反应形成梯形结构,纤维膜颜色由白色逐渐转化为黄色,最后变成黑色,利于纤维制备过程中的石墨化。本发明提供了上述技术方案所述制备方法制备得到的室温甲醛净化用非贵金属掺杂碳纤维膜,厚度为0.1~0.3mm,优选为0.2mm;所述非贵金属均匀分布在碳纤维中,所述非贵金属的掺杂量优选为2~15wt.%,更优选为9wt%。本发明还提供了上述技术方案所述室温甲醛净化用非贵金属掺杂碳纤维膜在分解甲醛中的应用。本发明优选将所述非贵金属掺杂碳纤维膜用于新风系统中,在室温下即可高效地将甲醛分解为二氧化碳和水,避免了贵金属的使用,能够有效降低生产成本。下面将结合本发明中的实施例,对本发明中的技术方案进行清楚、完整地描述。显然,所描述的实施例仅仅是本发明一部分实施例,而不是全部的实施例。基于本发明中的实施例,本领域普通技术人员在没有做出创造性劳动前提下所获得的所有其他实施例,都属于本发明保护的范围。实施例1将0.8g聚丙烯腈(平均分子量mw=15×104)、0.4448g醋酸钴和0.0544g邻苯二胺溶解在6mln,n-二甲基甲酰胺(dmf)中,室温下搅拌10h后,获得紫色透明的纺丝液;吸取2ml所述纺丝液于2.5ml的注射器中,并将注射器固定在纺丝机上,选用直径为0.2mm的针头,进行静电纺丝,得到直径分布均匀的纳米纤维膜,具体纺丝参数如下:纺丝电压为22kv;纺丝距离为15cm;纺丝液流速为1ml/h;纺丝收集筒旋转速率为100rpm;纺丝温度为25℃;纺丝相对湿度为50%;将所述纳米纤维膜放入马弗炉中进行预氧化,预氧化的温度为220℃,从室温升至预氧化所需温度的升温速率为1℃/min,保温时间为10min,获得预氧化纤维膜;将所述预氧化纤维膜置于管式气氛炉(cvd)中,在氮气的保护下进行碳化,碳化的温度为650℃,管式气氛炉从室温升至碳化所需温度的升温速率为2℃/min,保温时间为30min,得到厚度为0.18mm的室温甲醛净化用非贵金属掺杂碳纤维膜;所得室温甲醛净化用非贵金属掺杂碳纤维膜的透射电镜图如图1所示,由图1可以看出本发明制备的碳纤维膜呈均匀、规整的线性一微纤维结构,并且非贵金属纳米颗粒均匀的分布在碳纤维中。实施例2将0.8g聚丙烯腈(平均分子量mw=15×104)、0.4448g醋酸钴和0.0906g10-邻菲咯啉溶解在6mldmf中,室温下搅拌10h后,获得紫色透明的纺丝液;吸取2ml所述纺丝液于2.5ml的注射器中,并将注射器固定在纺丝机上,选用直径为0.2mm的针头,进行静电纺丝,得到直径分布均匀的纳米纤维膜,具体纺丝参数如下:纺丝电压为22kv;纺丝距离为15cm;纺丝液流速为1ml/h;纺丝收集筒旋转速率为100rpm;纺丝温度为25℃;纺丝相对湿度为50%;将所述纳米纤维膜放入马弗炉中进行预氧化,预氧化的温度为220℃,从室温升至预氧化所需温度的升温速率为1℃/min,保温时间为10min,获得预氧化纤维膜;将所述预氧化纤维膜置于管式气氛炉(cvd)中,在氮气的保护下进行碳化,碳化的温度为650℃,管式气氛炉从室温升至碳化所需温度的升温速率为2℃/min,保温时间为30min,得到厚度为0.21mm的室温甲醛净化用非贵金属掺杂碳纤维膜。实施例3将0.8g聚丙烯腈(平均分子量mw=15×104)、0.4448g醋酸钴和0.0906g10-邻菲咯啉溶解在6mldmf中,室温下搅拌10h后,获得紫色透明的纺丝液;吸取2ml所述纺丝液于2.5ml的注射器中,并将注射器固定在纺丝机上,选用直径为0.2mm的针头,进行静电纺丝,得到直径分布均匀的纳米纤维膜,具体纺丝参数如下:纺丝电压为22kv;纺丝距离为15cm;纺丝液流速为1ml/h;纺丝收集筒旋转速率为100rpm;纺丝温度为25℃;纺丝相对湿度为50%;将所述纳米纤维膜放入马弗炉中进行预氧化,预氧化的温度为220℃,从室温升至预氧化所需温度的升温速率为3℃/min,保温时间为10min,获得预氧化纤维膜;将所述预氧化纤维膜置于管式气氛炉(cvd)中,在氮气的保护下进行碳化,碳化的温度为700℃,管式气氛炉从室温升至碳化所需温度的升温速率为2℃/min,保温时间为60min,得到厚度为0.2mm的室温甲醛净化用非贵金属掺杂碳纤维膜。对比例1将0.8g聚丙烯腈(平均分子量mw=15×104)、0.4366g醋酸亚铁和0.0544g邻苯二胺溶解在6mldmf中,室温下搅拌10h后,获得紫色透明的纺丝液;吸取2ml所述纺丝液于2.5ml的注射器中,并将注射器固定在纺丝机上,选用直径为0.2mm的针头,进行静电纺丝,得到直径分布均匀的纳米纤维膜,具体纺丝参数如下:纺丝电压为22kv;纺丝距离为15cm;纺丝液流速为1ml/h;纺丝收集筒旋转速率为100rpm;纺丝温度为25℃;纺丝相对湿度为50%;将所述纳米纤维膜放入马弗炉中进行预氧化,预氧化的温度为220℃,从室温升至预氧化所需温度的升温速率为1℃/min,保温时间为10min,获得预氧化纤维膜;将所述预氧化纤维膜置于管式气氛炉(cvd)中,在氮气的保护下进行碳化,碳化的温度为650℃,管式气氛炉从室温升至碳化所需温度的升温速率为2℃/min,保温时间为30min,得到厚度为0.13mm的碳纤维膜。将实施例1~3和对比例制备的碳纤维膜在室温下对甲醛的分解效率进行测试(测试装置如图2所示)。测试方法为:将0.02g的碳纤维膜置于直径为7mm的玻璃管中,然后向玻璃管中通入对浓度为50ppm的甲醛/空气混合气体,测量气体通过玻璃管后气体中甲醛的含量,最后通过甲醛浓度的改变计算获得甲醛在不同碳纤维上的转化率;甲醛通过不同碳纤维膜后的转化率如表1所示:表1分解甲醛测试结果编号甲醛转化率实施例1>93%实施例260%实施例3>30%对比例1<2%由表1可以看出,实施例1~3制备的负载有钴金属的钴-氮掺杂碳纤维膜具有明显的甲醛催化效果,而负载金属为铁金属时碳纤维膜几乎没有催化性能(对比例1)。此外,邻苯二胺作为氮配位体时能与钴盐有较好的相互作用,其对应的掺杂碳纤维的催化性能较优,甲醛在该纤维膜上的转化率大于90%(实施例1);而10-邻菲咯啉配位体,效果较低,甲醛的转化率为30~60%(实施例2和实施例3);对于醋酸钴与10-邻菲咯啉配位体体系,碳化温度为650℃时,纤维产物的催化性能优于碳化温度为700℃的纤维膜。以上所述仅是本发明的优选实施方式,应当指出,对于本
技术领域:
的普通技术人员来说,在不脱离本发明原理的前提下,还可以做出若干改进和润饰,这些改进和润饰也应视为本发明的保护范围。当前第1页1 2 3