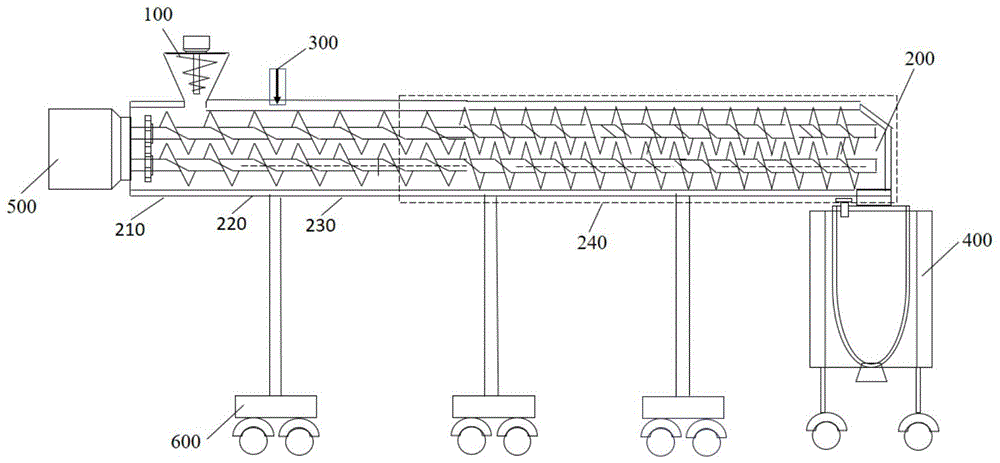
本发明涉及一种超轻质材料连续制备系统,还涉及利用所述系统制备超轻质材料的方法。
背景技术:
超轻质材料是一种将可发泡微球加热发泡后制备的密度为0.015-0.3kg/m3的空心塑料微球填料,其直径在10至500um。
可发泡微球是一种经悬浮聚合合成的塑料颗粒,由气密性外壳和密封在内的发泡剂组成。当微球被加热时产生不可逆发泡,进而生成预发泡微球(超轻质材料)。超轻质材料作为轻质填料被广泛应用于航空航天、高铁、汽车等工业领域、涂料、保温材料和密封材料等。汽车工业在车身底部涂层、轮胎、复合材料和粘合剂中使用超轻质材料。
微球的合成与发泡技术在us3615972、ep486080、ep566367、cn201610792097.3、cn201510483687.3、cn201280073857.5、cn2012100109302.3等专利中均有所报道。由于合成工艺的差异,根据微球的可发泡温度范围,可将微球分为低温、中高温、高温及超高温微球。快思瑞科技(上海)有限公司可以提供干粉和滤饼的各种不同形式的可发泡微球,包括已发泡和未发泡的形式,其中以低温wu1501与高温du608两种牌号微球最为著名。
可发泡微球的未发泡形式和发泡形式在市场均有销售,但是由于已发泡微球(超轻质材料)密度小,是超轻的粉体,其生产、运输以及销售多有不便,使用者一般现场制备已发泡的微球,即购买未发泡形式的可发泡微球滤饼加入到生产设备中用于连续制备最终产品。
从水相中收集可发泡微球后,经过脱水得到滤饼并进一步干燥以形成自由流动的可分散粉末。由于球体对温度敏感(取决于聚合物壳壁的软化点),因此通常不能使用高温蒸发干燥来及时除去水分。而且,由于含水浆料含有许多来自悬浮聚合过程的污染物和添加剂,因此在脱水形成滤饼时倾向于聚集和结块,导致在最终无法得到分散性良好的预发泡微球。
许多专利对发泡微球发泡剂的干燥方法和装置均有提及。如美国专利us8247465和us8329298均提到了将颗粒状填料粘附在微球壳的外表面上的步骤,粘附在微球壳外表面上的颗粒状填料有助于改善微球在干燥时的分散性和流动性,但是这种操作对设备要求非常大,程序难以控制,并且难以保持产品的质量和均匀性。cn105396524b提供了一种已发泡微球发泡剂制备装置;所述装置通过设置加入湍流装置、设置开放式筒体结构和弧形汇聚段,可有效防止微球发泡剂在发泡过程中结块,但是其生产效率低,可操作性差,设备利用率低,不能随时调整不同温度区间的预发泡微球生产过程。cn105150494a提出了一种连续制备超轻质填料的设备和方法,很好地解决了加料时原料的架桥、堵塞和流动性差等问题,其中使用了双螺杆实现了由湿饼连续制备干粉超轻质填料。但是,上述专利提及的装置和方法是对含水量低的湿饼进一步加热发泡来制备超轻质材料,而这些装置和方法在加热发泡微球滤饼时的团聚和发泡不充分问题得不到解决。
因此,迫切需要一种能克服上述缺点的超轻质材料连续制备系统和方法。
技术实现要素:
为了克服上述现有技术的缺点,本发明提供了一种超轻质材料制备系统和利用所述系统制备超轻质材料的方法,其能实现超轻质材料的连续制备,并有效防止可发泡微球在加热发泡过程中相互粘结。
为了实现上述目的,根据本发明的一个方面,提供一种超轻质材料制备系统,其包括:
(1)进料装置;
(2)双螺杆混合加热装置,所述双螺杆混合加热装置在横向上依次包括:
进料区,
混合分散区,
预热区,
加热区,所述加热区在横向上依次包括第一加热段、第二加热段、第三加热段,
其中,所述进料区、混合分散区、预热区、加热区包括同轴的双螺杆结构;
其中,所述进料装置设置于所述进料区,且所述进料装置的内部与所述进料区的内部联通;
(3)助剂添加装置,采用定量泵定量加入,所述助剂添加装置设置于所述混合分散区,且所述助剂添加装置的内部与所述混合分散区的内部联通;以及
(4)保温发泡装置,所述保温发泡装置设置于所述第三加热段,且所述保温发泡装置的内部与所述第三加热段的内部联通。
根据本发明的另一方面,提供一种利用上述超轻质材料制备系统对可发泡微球进行发泡来制备超轻质材料的方法,所述方法包括如下步骤:
进料:将微球滤饼加入所述进料装置中,并输送到所述双螺杆混合加热装置的进料区;
混合分散:将所述微球滤饼从所述进料区输送到所述混合分散区,同时通过所述助剂添加装置向所述混合分散区添加表面处理剂,使得所述微球滤饼和所述表面处理剂混合,得到微球湿粉;
预热:将所述微球湿粉从所述混合分散区输送到所述预热区,在所述预热区中对所述微球湿粉进行预热并进一步混合分散;
加热:将所述微球湿粉从预热区向所述加热区输送,在所述加热区中对所述微球湿粉进行加热,得到热微球湿粉;
发泡:将所述热微球湿粉从所述加热区的第三加热段输送到保温发泡装置,同时调节泄压装置进行泄压,在保温发泡装置内微球瞬时发泡。
本发明的超轻质材料制备系统,通过双螺杆混合加热装置-保温发泡装置的组合形式,并通过添加表面处理剂,实现了超轻质材料的连续化制备,可有效防止超轻质材料在制备过程中粘结,提高生产效率,同时达到节能环保的目的。另一方面,本发明通过在滤饼中添加表面处理剂,还解决了超轻质材料在使用时的分散性问题。
此外,本发明通过采用螺旋搅拌的定量进料装置和连续的双螺杆结构,可以进行不同发泡温度区间和状态的超轻质材料的制备。通过控制螺杆的温度,可以制备不同发泡温度的预发泡微球的超轻质材料。
本发明提高了超轻质材料的制备的可靠性和简便性,有效提高了操作效率,且便于加工、成本低,有利于实现批量化生产。
与现有技术相比,本发明的制备系统和方法很好地解决了超轻质材料制备时无法连续操作、聚集结块等问题。根据本发明,可以从滤饼开始直接经螺杆混合分散、预热、加热发泡直至最后成为分散性良好的超轻质材料。
本发明相对于现有技术具有如下的优点及效果:
1、本发明首次利用螺杆的搅拌及推动作用,通过设计了双螺杆混合加热装置及保温发泡装置的串联装置,提供了一种由滤饼经上述装置直接制备超轻质材料的方法,大幅度提高了超轻质材料的生产效率,可以防止预发泡制备时的不充分问题,实现连续制备。
2、本发明通过采用螺旋搅拌的进料装置,很好地解决了原料下料时的堵塞和架桥等问题,能把分散不好的物料连续、均匀、稳定地喂入双螺杆混合加热装置。
3、本发明通过添加表面处理剂的方式,将表面处理剂包覆在微球表面,便于高效并均匀地加热,从而使物料能更好地发泡,使生产出来的产品不易粘结,可以有效提高微球发泡后的分散性。
4、本发明中螺旋搅拌的定量加料装置和连续的双螺杆结构,通过控制加热时的温度,可以使本发明适用于不同发泡温度区间和状态的超轻质材料的制备。
附图说明
图1为根据本发明一个实施方式的超轻质材料制备系统的示意图。
图2为根据本发明一个实施方式的加热区的示意图。
图3为根据本发明一个实施方式的保温发泡装置的示意图。
图4为根据本发明一个实施方式制备的超轻质材料(预发泡微球)的示意图。
附图标记
100:滤饼进料装置
200:双螺杆混合加热装置
210:进料区
220:混合分散区
230:预热区
240:加热区
240-1:第一加热段
240-2:第二加热段
240-3:第三加热段
300:助剂添加装置
400:保温发泡装置
401:输入口
402:输入阀
403:泄压装置
404:浴液入口
405:浴液出口
406:出料口
500:横向联轴器
600:移动装置
具体实施方式
为使本发明的目的、技术方案和优点更加清楚明白,以下结合具体实施例,并参照附图,对本发明进一步详细说明。
1.超轻质材料制备系统
在本发明的一个实施方式中,如图1所示,提供一种超轻质材料制备系统,其包括:
(1)进料装置100;
(2)双螺杆混合加热装置200,所述双螺杆混合加热装置200在横向上依次包括:
进料区210,
混合分散区220,
预热区230,
加热区240,
其中,所述加热区240如图2所示,在横向上依次包括第一加热段240-1、第二加热段240-2和第三加热段240-3,
其中,所述进料区210、混合分散区220、预热区230和加热区240包括同轴的双螺杆结构,
其中,所述进料装置100设置于所述进料区210,且所述进料装置100的内部与所述进料区210的内部联通;
(3)助剂添加装置300,所述助剂添加装置300设置于所述预热区230,且所述助剂添加装置300的内部与所述预热区230的内部联通;以及
(4)保温发泡装置400,所述保温发泡装置400设置于所述第三加热段240-3,且所述保温发泡装置400的内部与所述第三加热段240-3的内部联通。
1.1进料装置
在一个实施方式中,进料装置100包括锥形加料斗,所述锥形加料斗的顶部设有电机,所述电机与所述进料装置100的中心轴固定连接,所述中心轴上设有锥形螺旋桨,所述锥形螺旋桨从上至下的圆周半径依次减少。通过采用螺旋搅拌的进料装置,很好地解决了原料下料时的堵塞和架桥等问题,能使分散不好的物料连续、均匀、稳定地进入干燥装置。
在一个实施方式中,进料区210与进料装置100的连接可以为垂直连接,优选垂直固定连接。所述进料段210可以为带有金属螺杆的结构,用于输送由进料装置100加入的滤饼。
1.2双螺杆混合加热装置
在一个实施方式中,在所述双螺杆混合加热装置200中,
所述进料区210包括第一双螺杆结构,
所述混合分散区220包括第二双螺杆结构,
所述预热区230包括第三双螺杆结构,
在所述加热区240中,所述第一加热段240-1、第二加热段240-2、第三加热段240-3包括第四双螺杆结构,
其中所述进料区210、混合分散区220、预热区230、加热区240各自包括的双螺杆结构是相同的或不同的。
在一个实施方式中,在所述双螺杆混合加热装置200中,所述进料区210的内部、所述混合分散区220的内部、所述预热区230的内部、所述加热区240的内部是联通的。
在一个实施方式中,所述混合分散区220和所述预热区230的温度可以是相同或者不同的,但是需低于微球最低发泡温度(微球的开始发泡温度tstart)
在所述加热区240中,
所述第一加热段240-1用于将滤饼与表面处理剂混合后形成的微球湿粉加热;
所述第二加热段240-2用于提高微球湿粉的受热;
所述第三加热段240-3用于进一步提高微球湿粉的受热;并进一步输送至保温发泡装置400的输入口401。
其中,所述第一加热段240-1、第二加热段240-2、以及第三加热段240-3的设置温度可以是相同的或者不同的,温度需高于微球最低发泡温度(微球的开始发泡温度tstart)
在一个实施方式中,在所述双螺杆混合加热装置的所述预热区230上设置有助剂添加装置300。所述双螺杆混合加热装置200与所述助剂添加装置300的连接可以为垂直连接,优选垂直固定连接。
1.3助剂添加装置
所述助剂添加装置300可以是助剂料斗。所述助剂料斗内可以存在提高加料速度的联轴器。所述助剂料斗用于添加表面处理剂。
表面处理剂的加入可以防止可发泡微球在后期加热段出现团聚。表面处理剂有固体和液体两种。表面处理剂可以有效防止微球的附聚和表面结合;通过控制加热和平衡温度以及混合实现微球发泡,增大螺杆与微球湿饼间的热传导效果,促进微球的发泡速率。
在一个实施方式中,表面处理剂优选为固体制品。固体制品可以使用滑石粉,碳酸钙,钛白粉,氧化铝,特别是三水合氧化铝,二氧化硅,二氧化钛,氧化锌等。其它的材料包括陶瓷,石英或玻璃的球形珠或空心珠。优选使用钛白粉作为固体制品。
表面处理剂也可以是液体制品,可以使用甘油,硅油,液体石蜡,硅烷偶联剂,聚乙烯醇,邻苯二甲酸二甲酯,拉开粉水溶液(30%)等。优选使用甘油作为液体制品。
1.4保温发泡装置
在一个实施方式中,如图3所示,所述保温发泡装置400是可自由拆卸的容器,可以为塑料或金属材质,与第三加热段240-3之间有法兰连接,其包括:
输入口401,
输入阀402,
泄压装置403,
浴液入口404,
浴液出口405,
出料口406,
所述输入口401、输入阀402、泄压装置403、出料口406与保温发泡装置400内部联通;内部与外部之间为夹套形式,浴液入口404与浴液出口405分别与夹套内部联通;
浴液可以通过在夹套内部流动,实现对保温发泡装置400的温度调节。
在一个实施方式中,浴液可以是水,酒精,硅油,优选水作为浴液。
1.5其他装置
在一个实施方式中,本发明的超轻质材料制备系统还包括横向联轴器500,所述横向联轴器500设置在所述进料区,且与双螺杆结构本体固定连接。所述横向联轴器500用于将两根双螺杆结构通过减速齿轮连接起来,带动双螺杆进行转动。
在一个实施方式中,本发明的超轻质材料制备系统还包括移动装置600,便于根据生产需求,随时移动制备装置。
2.超轻质材料制备的方法
下面对本发明的超轻质材料的制备方法进行详细描述。
根据本发明的一个实施方式,本发明的超轻质材料的制备方法包括如下步骤:
进料:将微球滤饼加入所述进料装置100中,并输送到所述双螺杆混合加热装置200的进料区210;
混合分散:将所述微球滤饼从所述进料区210输送到所述混合分散区220,同时通过所述助剂添加装置300向所述混合分散区220添加表面处理剂,使得所述微球滤饼和所述表面处理剂在所述混合分散区220中混合分散,由此得到微球湿粉;
预热:将所述微球湿粉从所述混合分散区220输送到所述预热区230,在所述预热区230中对所述微球湿粉进行预热并进一步混合分散,形成混合的热微球湿粉;
加热:将所述混合的热微球湿粉从所述预热区230输送到所述加热区240,经所述第一加热段240-1、第二加热段240-2和第三加热段240-3对所述混合的热微球湿粉进一步加热,得到未完全发泡的微球湿粉;
发泡:将所述未完全发泡的微球湿粉从所述第三加热段240-3输送到所述保温发泡装置400,在所述保温发泡装置400内完成发泡,从而得到所述超轻质材料。
2.1进料步骤
在一个实施方式中,在所述进料步骤中,所述进料装置100的锥形螺旋桨的转速可以为100-150rpm,优选90-100rpm。锥形加料斗内的加料速度可以为100-200公斤/小时。所述进料段的温度可以为室温。
2.2混合分散步骤
在一个实施方式中,在所述混合分散步骤中,所得到的混合热微球湿粉的固含量可以为70%以上,优选为70%-75%。
2.3预热步骤
在一个实施方式中,在所述预热步骤中,所述横向联轴器500的转速为50-100rpm,优选80-90rpm,这要与进料装置100的锥形螺旋桨的转速匹配。所述预热区230的温度可以根据微球发泡温度进行调整:
对于低温发泡微球,预热区的温度可以为60-100℃,优选70-95℃,更优选80-90℃;
对于高温发泡微球,预热区的温度可以为120-180℃,优选150-175℃,更优选160-170℃。
在一个实施方式中,在所述预热步骤中,可以根据实际操作情况设定所述横向联轴器500的转速。如果转速过大,会导致微球湿粉与表面处理剂混合的速度太快,进一步导致微球表面的表面处理剂包覆太少,引起微球受热不均匀;如果转速过小,会导致输送微球湿粉的速度太慢,进一步导致微球湿粉中混合的表面处理剂不均匀,微球受热时间长,引起壳变软而导致相互粘结。
在一个实施方式中,在所述预热步骤中,表面处理剂与微球湿粉混合后可以防止在发泡过程中微球之间产生粘连。此外,表面处理剂也有助于微球湿粉受热均匀,在机筒内螺杆剪切下,微球外壳受热粘连的几率大大降低。
2.4加热步骤
在一个实施方式中,在所述加热步骤中,对混合有表面处理剂的微球湿粉进行加热。混合的微球湿粉依次通过加热区240的第一加热段240-1、第二加热段240-2、第三加热段240-3,使混合的微球湿粉在输送到保温发泡装置400之前,达到足够的发泡温度。
本发明通过添加表面处理剂来防止微球湿粉在加热步骤中受热不均。所述表面处理剂包括固体制品和液体制品。从传热以及操作的简单程度,优选固体制品。所述固体制品和液体制品的具体实例如上所述。
在一个实施方式中,在所述加热步骤中,所述第一加热段240-1、第二加热段240-2、第三加热段240-3的温度可以是相同或不同的,均高于微球的最低发泡温度。
具体地,加热区240的温度可根据微球发泡的tstart选择。原则上,加热区240的温度比微球的tstart高20-50℃。
对于低温发泡微球,加热区240的温度可以为120-170℃,优选140-160℃,更优选140-150℃。
对于高温发泡微球,加热区240的温度可以为170-250℃,优选170-200℃,更优选180-190℃。
2.5发泡步骤
在一个实施方式中,所述方法在加热步骤后还包括:将所述混合的热微球湿粉从所述加热区240输送到保温发泡装置400进行发泡,并从出料口406收集得到的超轻质材料(预发泡微球);
其中,保温发泡装置400内的压力可以通过泄压装置403进行调节,保温发泡装置400内的压力为0.1-0.5mpa,可根据实际需求,选择发泡压力,一般来说,为了充分发泡,发泡压力优选为0.1-0.2mpa;
其中,浴液选择水,浴液温度可以为25-70℃,优选25-50℃,优选30-40℃;
特别地,所述微球发泡通过可以随时拆卸的密封的保温发泡装置进行收集,减少了所述粉末的粉尘环境污染。
实施例1
使用图1所示的超轻质材料制备系统实施本实施例的方法,所述方法包括如下步骤:
(1)首先向进料装置100(弘煜机械有限公司,psa)的锥形加料斗内加入微球滤饼wu1501(其中所述微球为低温微球),加料速度为200kg/h,所述进料装置100中的垂直加料螺旋装置的转速为50rpm。
然后将所述微球滤饼wu1501输送到所述双螺杆混合加热装置200的进料区210。与所述双螺杆混合加热装置200的双螺杆结构的双螺杆本体固定连接的横向联轴器500(来自泰鑫精密塑胶机械有限公司)的转速为50rpm。
(2)然后将所述微球滤饼从所述进料区210输送到所述混合分散区220(温度为100℃),在混合分散区220中的螺杆的作用下,完成滤饼的加热,形成热滤饼。
(3)在预热区230中的螺杆的推动下,使热滤饼进入到预热区230,同时从助剂添加装置300向所述预热区230添加硅油表面处理剂(上海阿拉丁生化科技股份有限公司),添加量为0.3kg/h,得到热湿粉。
(4)所述热湿粉从所述预热区230输送到加热区240的第一加热段240-1(温度为120℃),其中随着微球壳体软化,导致微球表面粘连表面处理剂;然后将所述热湿粉依次通过第二加热段240-2(温度为130℃)、第三加热段240-3(温度为140℃),得到未完全发泡的混合热湿粉。
(5)将所述未完全发泡的混合热湿粉输送到保温发泡装置400,发泡后得到预发泡的且分散性良好的超轻质材料(预发泡微球),最后在所述保温发泡装置400的出料口406进行收集。
由此较好地使用上述设备实现了超轻质材料(预发泡微球)的连续制备。
实施例2
实施例2的工艺流程与实施例1的工艺流程基本相同,不同之处在于:
在步骤(1)中,向进料装置100的锥形加料斗内加入滤饼wu608(其中所述微球为高温微球),加料速度为250kg/h,进料装置100中的垂直加料螺旋装置的转速为40rpm;
在步骤(2)中,混合分散区220的温度为120℃;
在步骤(3)中,来自助剂添加装置300的表面处理剂为甘油(上海阿拉丁生化科技股份有限公司),添加量为0.3kg/h;
在步骤(4)中,所述热湿粉从所述预热区230输送到加热区240的第一加热段240-1(温度为140℃),其中随着微球壳体软化,导致微球表面粘连表面处理剂;然后将所述热湿粉依次通过第二加热段240-2(温度为150℃)、第三加热段240-3(温度为160℃)。
最终,在保温发泡装置400中得到了发泡充分且分散性良好的超轻质材料(预发泡微球),如图4所示。
以上所述仅是本发明的优选实施方式,需要理解的是,本发明并不局限于上述特定的实施方式。应当指出,对于本技术领域的普通技术人员来说,在不脱离本发明技术原理的前提下,还可以做出若干改进和变型,这些改进和变型也应视为本发明的保护范围。