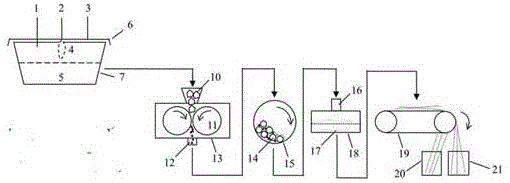
本实用新型涉及冶金渣资源回收再利用
技术领域:
,具体是指一种冶金渣中多种金属元素的回收系统。
背景技术:
:我国是世界冶金大国,每年生产了大量的冶金材料。2018年,仅生铁、粗钢、不锈钢粗钢的产量就已经分别达到了7.71、9.28、0.27亿吨,同比增长了3%、6.6%、3.62%。此外还有大量的有色冶金材料被生产出来。在生产这些冶金材料的过程中,产生了大量的冶金渣,排渣量以每年上亿吨递增。渣中含有很多金属元素,如mg、fe、co、mn、cu、zn、ni、al、cr等。这些金属元素多以氧化物的形式存在于渣中,很难回收再利用,这也使得冶金渣成分非常复杂,循环利用更加困难,常常被堆存处理,污染了生态环境。目前,渣包仅具有冶金渣盛放功能,尚未具备温控功能,包括升温速率、冷却速率、恒温时间等的控制,制约了冶金渣的改质。直接对冶金渣破碎、磁选,只能回收具有磁性的金属,如金属铁。但是对于无磁性的金属和金属氧化物中的金属元素,无法进行有效地回收,造成了多种金属资源的浪费。技术实现要素:本实用新型的目的是提供一种冶金渣中多种金属元素的回收系统,具有操作便捷、资源利用率高和废渣处理量少的特点。本实用新型可以通过以下技术方案来实现:本实用新型公开了一种冶金渣中多种金属元素的回收系统,包括渣包和与其组合使用的可分离式包盖,回收系统还包括:用于对渣包进行加热实现冶金渣熔化的加热装置;用于对熔融后冶金渣冷却至室温实现ab2o4磁性尖晶石结构转变得到块状冶金渣的冷却装置;用于对渣包进行加热控制的温控装置;用于对块状冶金渣进行破碎形成颗粒状冶金渣的破碎装置;用于对颗粒状冶金渣进行粉磨形成粉末状冶金渣的粉磨装置;用于对粉末状冶金渣进行筛下料的过筛装置;用于对筛下料进行磁选得到ab2o4磁性尖晶石的磁选装置;加热装置、温控装置、冷却装置设置在包盖上。本实用新型的技术方案通过在包盖上设置加热装置、温控装置和冷却装置,突破渣包仅具有的冶金渣盛放功能,实现温控加热和冷却,对升温速率、冷却速率、恒温时间、恒温温度等的控制,实现了冶金渣的改质使之具有磁性,然后进行破碎、粉磨、过筛、磁选,既回收具有磁性的金属,又回收无磁性的金属和金属氧化物中的金属元素,提高资源的利用率。进一步地,包盖上设有加热管道和冷却管道,加热装置通过加热管道对渣包进行升温,冷却装置通过冷却管道进行降温。进一步地,温控装置设在包盖上,温控装置的测温触点深入渣包内部在冶金渣上方20~30cm处。进一步地,加热装置为可燃性气体燃烧器或者电阻加热丝。进一步地,温控装置为热电偶或测温仪,测温仪与加热电阻丝电性连接。进一步地,破碎装置为双辊式破碎机、颚式破碎机、反击式破碎机、圆锥式破碎机、冲击式破碎机或锤式破碎机。进一步地,粉磨装置为球磨机或棒磨机。进一步地,过筛装置为直线振动筛、圆振动筛或精细筛分机。进一步地,磁选装置为干式磁选机或湿式磁选机。进一步地,磁选装置为一级磁选或多级磁选。本实用新型的另外一个方面,是利用上述系统,提出一种冶金渣中多种金属元素的回收方法,包括以下步骤:碱度调节:在渣包中对冶金渣加入改质剂调整其碱度;冶金渣未改质前没有ab2o4磁性尖晶石,通过调节碱度使冶金渣形成ab2o4磁性尖晶石,从而磁选选出;ab2o4磁性尖晶石结构改质处理:在空气气氛下使用加热装置和温控装置通过渣包对改质后的冶金渣进行升温至1100~1500℃使之完全熔化并恒温保持0.25~3h,然后通过缓慢冷却冶金渣至1000~1400℃恒温保持0.1~5h,使冶金渣生成ab2o4磁性尖晶石,最后通过冷却装置快速冷却ab2o4磁性尖晶石结构的冶金渣至室温得到块状的冶金渣;就其反应机理而言,升温过程是让冶金渣熔化,原有渣相消失,全部变成液相,缓慢冷却过程中形成ab2o4磁性尖晶石和其他相,快速冷却是让冶金渣快速冷却,已形成的ab2o4磁性尖晶石不发生改变;破碎处理:通过破碎装置对块状的冶金渣进行破碎处理,得到颗粒状冶金渣;粉磨处理:通过粉磨装置对颗粒状冶金渣进行粉磨处理得到粉末状的冶金渣;过筛处理:通过过筛装置对粉末状的冶金渣进行过筛得到筛下料;磁选处理:通过磁选装置对筛下料进行磁选得到ab2o4磁性尖晶石;ab2o4磁性尖晶石中,a为fe、mg、co、mn、cu、zn、ni、al、cr中的两种或以上,b为fe、mg、co、mn、cu、zn、ni、al、cr中的两种或以上。进一步地,在ab2o4磁性尖晶石结构改质处理中,对冶金渣进行升温的升温速率为5℃/min~100℃/min;缓慢冷却的冷却速率为1℃/min~5℃/min;快速冷却为随炉冷却、空气冷却或水冷却。冷却速率的控制主要是基于以下考虑:缓冷越慢效果越好,形成的ab2o4磁性尖晶石粒度越大,易于磁选。反之则形成的粒度小,不易磁选。进一步地,碱度调节中,改质剂为cao和/或sio2,在本实用新型中碱度r=cao/sio2,改质后冶金渣的碱度为1.0~4.0,若在此范围之外,最终的产品无法形成ab2o4磁性尖晶石。进一步地,用于改质的冶金渣为转炉渣、高炉渣、电炉渣、不锈钢渣、铁水预处理渣、炉外精炼渣和/或中间包渣中的一种或两种以上。进一步地,冶金渣的主要成分的质量分数为:cao20%~60%、sio210%~40%、tfe5%~40%、mgo0%~20%、coo0%~10%、mno0%~20%、cuo0%~20%、zno0%~20%、nio0%~20%、al2o30%~20%、cr2o30%~20%。进一步地,过筛装置的筛目为400目。进一步地,ab2o4磁性尖晶石结构改质处理中,升温的过程为使用可燃性气体燃烧器或者电阻加热丝。本实用新型一种冶金渣中多种金属元素的回收系统,具有如下的有益效果:第一、操作便捷,通过设置加热装置、温控装置、冷却装置对渣包进行温度控制,利于碱度调节后的改质处理;第二、资源利用率高,本实用新型可回收冶金渣中的多种金属元素,尤其是无磁性金属和金属氧化物中的金属元素,如磁选后mg、al、fe、cr、mn的品位较原始冶金渣提高了1~10%、1~5%、7~20%、0~5%、1~5%,实现了金属资源回收再利用,具有较高的资源利用率;第三、废渣处理量小,包盖与渣包的分离式设置,同时集成加热装置、温控装置、冷却装置、破碎装置、粉磨装置、过筛装置,只需要对筛下料进行磁选处理即可实现磁选分离回收,磁选尾渣的处理量可降低10%~20%。附图说明附图1为本实用新型一种冶金渣中多种金属元素的回收系统的实施例1的结构示意图;附图2为本实用新型一种冶金渣中多种金属元素的回收系统实施例2的结构示意图;附图中的标记包括:1.温控装置;2.加热装置;3.冷却装置;4.可燃气体燃烧火焰;5.冶金渣;6.包盖;7.渣包;8.电阻丝;10.块状冶金渣;11.破碎辊;12.颗粒状冶金渣;13.破碎装置;14.磨球;15.球磨装置;16.粉状冶金渣;17.筛下料;18.过筛装置;19.磁选装置;20.ab2o4磁性尖晶石;21.磁选尾渣。具体实施方式为了使本
技术领域:
的人员更好地理解本实用新型的技术方案,下面结合实施例及附图对本实用新型产品作进一步详细地说明。本实用新型公开了一种冶金渣中多种金属元素的回收系统,包括渣包和与其组合使用的可分离式包盖,回收系统还包括:用于对渣包进行加热实现冶金渣熔化的加热装置;用于对熔融后冶金渣冷却至室温实现ab2o4磁性尖晶石结构转变得到块状冶金渣的冷却装置;用于对渣包进行加热控制的温控装置;用于对块状冶金渣进行破碎形成颗粒状冶金渣的破碎装置;用于对颗粒状冶金渣进行粉磨形成粉末状冶金渣的粉磨装置;用于对粉末状冶金渣进行筛下料的过筛装置;用于对筛下料进行磁选得到ab2o4磁性尖晶石的磁选装置;加热装置、温控装置、冷却装置设置在包盖上。进一步地,包盖上设有加热管道和冷却管道,加热装置通过加热管道对渣包进行升温,冷却装置通过冷却管道进行降温。进一步地,温控装置设在包盖上,温控装置的测温触点深入渣包内部在冶金渣上方20~30cm处。进一步地,加热装置为可燃性气体燃烧器或者电阻加热丝。进一步地,温控装置为热电偶或测温仪,测温仪与加热电阻丝电性连接。进一步地,破碎装置为双辊式破碎机、颚式破碎机、反击式破碎机、圆锥式破碎机、冲击式破碎机或锤式破碎机。进一步地,粉磨装置为球磨机或棒磨机。进一步地,过筛装置为直线振动筛、圆振动筛或精细筛分机。进一步地,磁选装置为干式磁选机或湿式磁选机。进一步地,磁选装置为一级磁选或多级磁选。本实用新型的另外一个方面,是利用上述系统,提出一种冶金渣中多种金属元素的回收方法,包括以下步骤:碱度调节:在渣包中对冶金渣加入改质剂调整其碱度;ab2o4磁性尖晶石结构改质处理:在空气气氛下使用加热装置和温控装置通过渣包对改质后的冶金渣进行升温至1100~1500℃使之完全熔化并恒温保持0.25~3h,然后通过缓慢冷却冶金渣至1000~1400℃恒温保持0.1~5h,使冶金渣生成ab2o4磁性尖晶石,最后通过冷却装置快速冷却ab2o4磁性尖晶石结构的冶金渣至室温得到块状的冶金渣;破碎处理:通过破碎装置对块状的冶金渣进行破碎处理,得到颗粒状冶金渣;粉磨处理:通过粉磨装置对颗粒状冶金渣进行粉磨处理得到粉末状的冶金渣;过筛处理:通过过筛装置对粉末状的冶金渣进行过筛得到筛下料;磁选处理:通过磁选装置对筛下料进行磁选得到ab2o4磁性尖晶石;ab2o4磁性尖晶石中,a为fe、mg、co、mn、cu、zn、ni、al、cr中的两种或以上,b为fe、mg、co、mn、cu、zn、ni、al、cr中的两种或以上。进一步地,在ab2o4磁性尖晶石结构改质处理中,对冶金渣进行升温的升温速率为5℃/min~100℃/min;缓慢冷却的冷却速率为1℃/min~5℃/min;快速冷却为随炉冷却、空气冷却或水冷却。进一步地,碱度调节中,改质剂为cao和/或sio2,改质后冶金渣的碱度为1.0~4.0。进一步地,用于改质的冶金渣为转炉渣、高炉渣、电炉渣、不锈钢渣、铁水预处理渣、炉外精炼渣和/或中间包渣中的一种或两种以上。进一步地,冶金渣的主要成分的质量分数为:cao20%~60%、sio210%~40%、tfe5%~40%、mgo0%~20%、coo0%~10%、mno0%~20%、cuo0%~20%、zno0%~20%、nio0%~20%、al2o30%~20%、cr2o30%~20%。进一步地,过筛装置的筛目为400目。进一步地,ab2o4磁性尖晶石结构改质处理中,升温的过程为使用可燃性气体燃烧器或者电阻加热丝。实施例1如图1所示,本实用新型公开了一种冶金渣中多种金属元素的回收系统,包括温控装置1、加热装置2、冷却装置3、包盖6、渣包7、破碎装置13、球磨装置15、过筛装置18、磁选装置19。如图1所示,在本实施例中,分离式的包盖6设置在渣包7上,加热装置2使用可燃性气体燃烧器,破碎装置13使用双辊式破碎机,粉磨装置15使用球磨机,过筛装置18使用旋振筛,磁选装置19采用干式磁选机。可燃性气体燃烧器燃烧产生可燃性气体火焰4贯穿包盖6的加热通道对渣包7进行加热升温,冷却管道设置在包盖6上方便进行冷却,渣包7内的冶金渣5在改质后得到块状冶金渣10,块状冶金渣10进入破碎装置13在破碎辊11的作用下进行破碎得到颗粒状冶金渣12,颗粒状冶金渣12进入球磨机在磨球14的作用下得到粉末状冶金渣16,粉末状冶金渣16进入旋振筛18得到筛下料17,筛下料17进入干式磁选机19进行磁选,得到ab2o4磁性尖晶石20和磁选尾渣21。在本实施例中,温控装置设在包盖上,温控装置的测温触点深入渣包内部在冶金渣上方20~30cm处。温控装置为热电偶。实施例2如图2所示,本实用新型公开了一种冶金渣中多种金属元素的回收系统,包括温控装置1、加热装置2、冷却装置3、包盖6、渣包7、破碎装置13、球磨装置15、过筛装置18、磁选装置19。如图2所示,在本实施例中,分离式的包盖6设置在渣包7上,加热装置使用电阻丝8,破碎装置13使用双辊式破碎机。粉磨装置15使用球磨机,过筛装置18使用旋振筛,磁选装置19采用干式磁选机;电阻丝8在包盖6的下部对渣包7进行加热升温,冷却管道设置在包盖6上方便进行冷却,渣包7内的冶金渣5在改质后得到块状冶金渣10,块状冶金渣10进入破碎装置13在破碎辊11的作用下进行破碎得到颗粒状冶金渣12,颗粒状冶金渣12进入球磨机在磨球14的作用下得到粉末状冶金渣16,粉末状冶金渣16进入旋振筛18得到筛下料17,筛下料17进入干式磁选机19进行磁选,得到ab2o4磁性尖晶石20和磁选尾渣21。在本实施例中,温控装置设在包盖上,温控装置的测温触点深入渣包内部在冶金渣上方20~30cm处。温控装置为测温仪,测温仪与加热电阻丝电性连接。实施例3本实用新型公开了一种冶金渣中多种金属元素的回收系统,本实施例与实施例2的差异在于:破碎装置为颚式破碎机;粉磨装置为棒磨机;过筛装置为直线振动筛;磁选装置为湿式磁选机;磁选装置为一级磁选。实施例4本实用新型公开了一种冶金渣中多种金属元素的回收系统,本实施例与实施例2的差异在于:破碎装置为反击式破碎机;粉磨装置为球磨机;过筛装置为圆振动筛;磁选装置为干式磁选机;磁选装置为多级磁选。实施例5本实用新型公开了一种冶金渣中多种金属元素的回收系统,本实施例与实施例2的差异在于:破碎装置为圆锥式破碎机;粉磨装置为球磨机或棒磨机;过筛装置为精细筛分机;磁选装置为干式磁选机;磁选装置为多级磁选。实施例6本实用新型公开了一种冶金渣中多种金属元素的回收系统,本实施例与实施例2的差异在于:破碎装置为冲击式破碎机或锤式破碎机;粉磨装置为球磨机;过筛装置为精细筛分机;磁选装置为湿式磁选机;磁选装置为多级磁选。实施例7本实用新型公开了一种冶金渣中多种金属元素的回收系统,本实施例与实施例2的差异在于:破碎装置为锤式破碎机;粉磨装置为棒磨机;过筛装置为精细筛分机;磁选装置为湿式磁选机;磁选装置为一级磁选。应用实施例1应用本实用新型的回收系统,以转炉渣作为冶金渣原料,转炉渣主要成分如表1所示,将转炉渣和sio2按照质量比100:6.4进行混合,改质后渣碱度由4.7降为2.7。随后在空气气氛下以10℃/min的速率进行升温,升温至1400℃并保温0.25h。然后以1℃/min的速率进行降温,降温至1270℃并保温0.25h。采用高压空气对冶金渣快速冷却,然后破碎、粉磨、过400目筛。通过干法磁选ab2o4磁性尖晶石,磁感应强度为0.5t。碱度调节后生成的ab2o4磁性尖晶石的eds结果如表2所示。ab2o4磁性尖晶石富集了多种金属元素,包括mn、al、mg、cr、fe。磁选后这些金属元素的品位较原始转炉渣提高了1.34%、1.32%、2.02%、0.27%、15.80%,实现了金属资源回收再利用,同时磁选尾渣的处理量减少了16.3%。应用实施例2应用本实用新型的回收系统,以转炉渣作为冶金渣原料,转炉渣主要成分如表1所示,将转炉渣和sio2按照质量比100:9.9进行混合,改质后渣碱度由4.7降为2.2。随后在空气气氛下以10℃/min的速率进行升温,升温至1400℃并保温0.25h。然后以1℃/min的速率进行降温,降温至1140℃并保温0.25h。采用高压空气对冶金渣快速冷却,然后破碎、粉磨、过400目筛。通过干法磁选ab2o4磁性尖晶石,磁感应强度为0.5t。碱度调节后生成的ab2o4磁性尖晶石的eds结果如表2所示。ab2o4磁性尖晶石富集了多种金属元素,包括mn、al、mg、fe。磁选后这些金属元素的品位较原始转炉渣提高了1.50%、1.02%、3.02%、7.80%,磁选后实现了金属资源的回收再利用,磁选尾渣的处理量减少了13.4%。对比例以转炉渣作为冶金渣原料,转炉渣未经改质,无ab2o4磁性尖晶石,eds结果如表3所示。金属元素mn、al、mg、cr、fe主要富集于ro相和c4af内。但是,这两相磁性很弱甚至没有磁性,无法通过磁选回收金属元素。表转炉渣主要成分,wt%tfecaosio2mnoal2o3mgocr2o3v2o5其他21.240.78.583.591.128.370.536.519.40表ab2o4磁性尖晶石原子百分比,%omnalmgcrfe其他应用实施例152.663.271.3912.620.5328.870.66应用实施例251.053.832.3616.26-24.641.86表金属元素主要富集相原子百分比,%omnalmgcrfeca其他ro54.512.72-22.170.2819.181.060.08c4af60.230.232.080.430.1312.7719.874.26通过表1、表2、表3,可以看到,转炉渣中的金属元素主要包括mn、al、mg、cr、fe,这些金属元素以弱磁性或无磁性的ro相和c4af存在于渣中,无法回收再利用,同时又由于这些金属元素的存在,使得转炉渣成分复杂,难以处理。通过本实用新型的技术方案,将转炉渣改质后生成了ab2o4磁性尖晶石,富集了mn、al、mg、cr、fe,磁选后各元素的品位较原始转炉渣提高了1~5%、1~5%、1~10%、0~5%、7~20%,实现了金属资源回收再利用,同时磁选尾渣的处理量降低了10%~20%。由于各种冶金渣成分不同,本应用实施例中ab2o4磁性尖晶石主要富集了mn、al、mg、cr、fe。此外可富集的金属元素还包括co、cu、zn、ni。以上所述,仅为本实用新型的较佳实施例而已,并非对本实用新型作任何形式上的限制;凡本行业的普通技术人员均可按说明书附图所示和以上所述而顺畅地实施本实用新型;但是,凡熟悉本专业的技术人员在不脱离本实用新型技术方案范围内,可利用以上所揭示的技术内容而作出的些许更动、修饰与演变的等同变化,为本实用新型的等效实施例;同时,凡依据本实用新型的实质技术对以上实施例所作的任何等同变化的更动、修饰与演变等,均仍属于本实用新型的技术方案的保护范围之内。当前第1页12