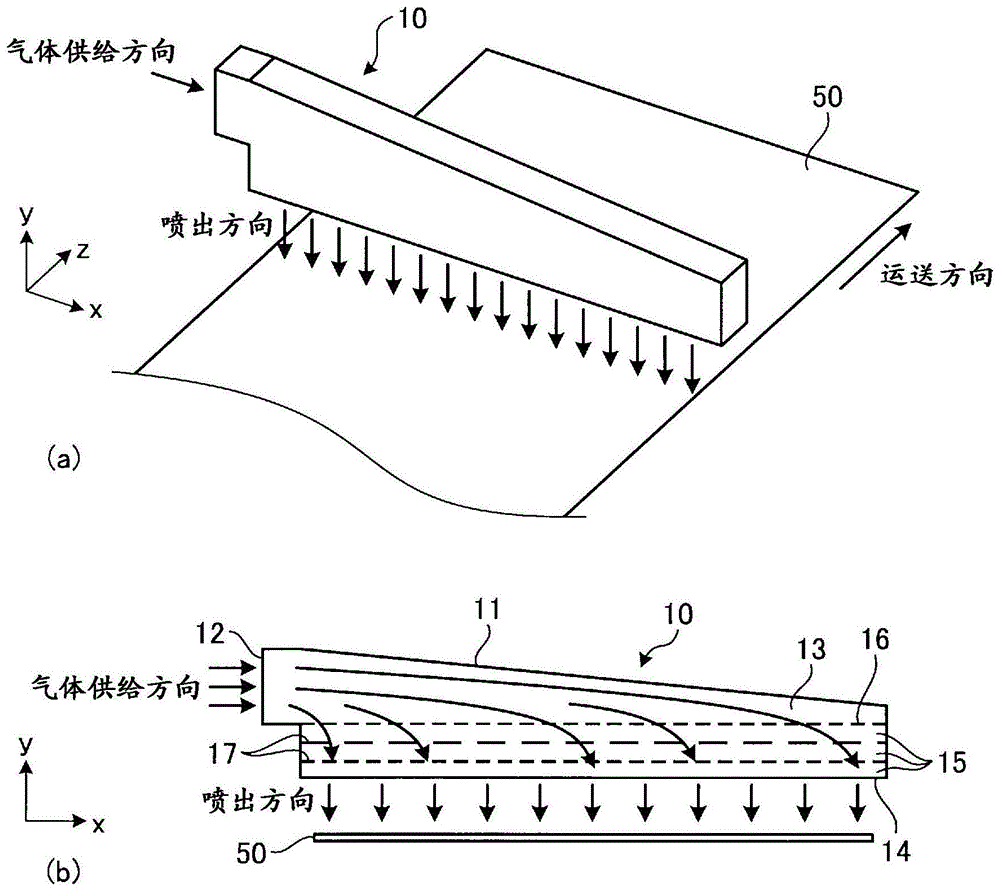
本发明涉及用于对树脂膜的表面吹喷气体的气体喷出喷嘴、具备气体喷出喷嘴的炉、和加工膜的制造方法。
背景技术:
:在对树脂膜实施了表面加工的加工膜的制造工序中,例如有时在长条或网状树脂膜原材上涂布液体,然后在干燥炉等炉的内部运送树脂膜的同时对树脂膜的表面吹喷空气、氮气等气体。在对所运送的树脂膜吹喷气体时,通常大多使用在与树脂膜的运送方向正交的方向、即树脂膜的宽度方向延伸、且朝向树脂膜的表面垂直地喷出气体的气体喷出喷嘴。针对在膜宽度方向延伸的气体喷出喷嘴,在膜宽度方向(即喷嘴长度方向)供给气体。这样的气体喷出喷嘴使喷嘴长度方向上所供给的气体朝向与供给方向正交的方向弯曲而对树脂膜进行吹喷。为了改变气流的朝向而在喷嘴内设置折流板(buffle)等,但有时因气体与折流板碰撞而产生湍流、且因该湍流而使吹喷对象树脂膜受到损伤。作为防止这样的损伤的产生而吹喷同样的气流的气体喷出喷嘴,在专利文献1中公开了具有沿着气体喷出喷嘴的长度方向(即工件的宽度方向)重复凹凸而形成波状或锯齿状的凹凸面盖的气体喷出喷嘴。沿着喷嘴长度方向的凹凸面盖的截面形状为三角波状。该气体喷出喷嘴具有以与工件相对的面作为气体喷出面的喷嘴箱、和设置于喷嘴箱内且在工件的宽度方向延伸且供气体朝向气体喷出面而通过的狭缝状的开口,凹凸面盖被设置成在喷嘴箱内覆盖开口。凹凸面盖虽然覆盖开口,但由于截面形状为三角波状,因此气体可从与喷嘴长度方向正交的方向(气体喷出喷嘴的宽度方向)上的凹凸面盖的端部侧(盖侧方一侧)朝向开口流动。而且,在喷嘴宽度方向上,在凹凸面盖和喷嘴箱的内壁之间形成有缝隙。供给至气体喷出喷嘴的气体从该缝隙流向凹凸面盖的侧方一侧而在凹凸面盖和开口之间的空间内流动,再经过开口而从气体喷出面朝向工件喷出。进而,专利文献1还公开了将开口和气体喷出面之间的空间作为使气流稳定的稳定室或均压室。在专利文献2中也公开了具有凹凸面盖的气体喷出喷嘴。专利文献2中所记载的气体喷出喷嘴是凹凸面盖的截面形状为正弦波状或梯形形状的气体喷出喷嘴。现有技术文献专利文献专利文献1:日本特开昭56-126442号公报专利文献2:英国专利申请公告第1558548号说明书技术实现要素:发明要解决的课题在干燥炉等炉中吹喷气体所制造的加工膜的特性受到从炉内部通过时的热历程影响,为了得到在膜的宽度方向上具有均质特性的加工膜,需要使从气体喷出喷嘴喷出的气体与树脂膜之间的热交换在树脂膜的宽度方向上均匀。因此,在气体喷出喷嘴上需要设置整流机构,使得该气体喷出速度沿着树脂膜的宽度方向恒定。但是,从膜宽度方向即喷嘴长度方向供给喷出用气体的气体喷出喷嘴包括从喷嘴长度方向的两侧供给气体的类型和仅从喷嘴长度方向的一侧供给气体的类型。如专利文献1、2那样,在仅从喷嘴长度方向的一侧供给气体的气体喷出喷嘴中产生下述现象:对于喷嘴长度方向而言,在与气体的供给侧相反侧的位置的气体喷出速度变得大于气体供给侧的气体喷出速度。专利文献1、2所示的气体喷出喷嘴虽然能够抑制局部湍流的产生,但在就气体喷出速度而言的沿着喷嘴长度方向的均匀性方面还称不上是充分的。本发明的目的在于提供用于对树脂膜吹喷气体且沿着喷嘴长度方向的气体喷出速度均匀的气体喷出喷嘴、具备这样的气体喷出喷嘴的炉、和使用这样的气体喷出喷嘴的加工膜的制造方法。用于解决课题的手段本申请的发明人经实验及模拟的结果发现,在使用如专利文献1所示那样的截面为三角波形状的凹凸面盖的情况下,构成凹凸面盖而相邻的2个斜面中,沿着朝向气体供给口的斜面流动的气流的速度大于不朝向气体供给口的斜面的气流的速度,由此,研究了针对斜面的倾斜和沿着喷嘴长度方向的气体喷出速度的均匀性的最佳角度,从而完成本发明。本发明的气体喷出喷嘴是用于对树脂膜的表面吹喷气体的气体喷出喷嘴,所述气体喷出喷嘴具有:壳体,其被设置成前述气体喷出喷嘴的长度方向沿着前述树脂膜的宽度方向延伸,并且在与前述树脂膜相对的侧面具有喷出气体的气体喷出面;气体供给口,其设置于前述壳体的一个端部,并且沿着喷嘴长度方向供给气体;和1个以上的均压室,其从前述气体供给口连通至气体喷出面,前述1个以上的均压室中的至少1个均压室的前述气体喷出面一侧的面由隔板构成,并且在前述隔板上沿着前述喷嘴长度方向配置两端具有开口的多个筒状体,所述多个筒状体被配置成各筒状体的轴方向与前述喷嘴长度方向正交,前述筒状体的从前述隔板立起的壁面中接近前述气体供给口一侧的壁面与前述隔板所形成的角θ为前述筒状体的截面形状的内角且其角度为55°以上且120°以下的范围,在前述筒状体的与前述隔板接触的面上设有还贯通前述隔板的气体流通孔。本发明的炉具备本发明的气体喷出喷嘴,从气体喷出喷嘴对树脂膜吹喷加热气体而进行加热处理。本发明的加工膜的制造方法包括利用本发明的气体喷出喷嘴对树脂膜吹喷气体的工序。本发明的加工膜的制造方法中优选前述气体为加热气体。本发明的加工膜的制造方法中,在沿着喷嘴长度方向的前述气体的喷出速度分布中,相对于平均喷出速度而言的喷出速度的最大值与最小值之差优选为11%以内。发明效果根据本发明,可以得到从气体喷出面喷出的气体的流速沿着喷嘴长度方向均匀的气体喷出喷嘴。通过使用具备该气体喷出喷嘴的炉而实行对树脂膜的加热处理,从而可以得到沿着膜的宽度方向具有均质特性的加工膜。附图说明图1是表示通常的气体喷出喷嘴的图,(a)是立体图,(b)是剖面图。图2是表示本发明的一个实施方式的气体喷出喷嘴的剖面图。图3是图2所示的气体喷出喷嘴的概略透视立体图。图4是表示筒状体的构成和配置的例子的立体图。图5是表示筒状体的构成和配置的例子的立体图。图6是表示筒状体的构成和配置的例子的立体图。图7是表示本发明的另一实施方式的气体喷出喷嘴的剖面图。图8是图7所示的气体喷出喷嘴的概略透视立体图。图9的(a)~(c)是表示筒状体的各部的尺寸、角度的图。具体实施方式接下来,参照附图对本发明的优选实施方式进行说明。在对基于本发明的气体喷出喷嘴进行说明之前,使用图1对通常的气体喷出喷嘴进行说明。图1所示的气体喷出喷嘴10是在例如干燥炉、拉伸加工用的拉幅烘箱等炉的内部用于对在炉内所运送的树脂膜50的表面吹喷空气等气体的气体喷出喷嘴。如图1(a)所示设想将树脂膜50的运送方向设为z轴方向、将与膜运送方向正交的树脂膜50的宽度方向设为x轴方向的xyz正交坐标系。y轴方向设为气体喷出喷嘴10的高度方向。气体喷出喷嘴10被设置成相对于树脂膜50的表面而言保持恒定的间隔,并且在树脂膜50的整个宽度的膜宽度方向、即x轴方向上延伸。因此,喷嘴长度方向也称为x轴方向。对于气体喷出喷嘴10而言,如图1(a)中“气体供给方向”所示,从喷嘴长度方向(x轴方向)的一方供给气体,并且如“喷出方向”所示,在树脂膜50的整个宽度与垂直于树脂膜50的表面的方向即y轴平行地喷出气体。将与喷嘴长度方向正交且与树脂膜50平行的方向(即z方向)称作喷嘴宽度方向。图1(b)示出与喷嘴长度方向平行且与树脂膜50的表面垂直的方向上的气体喷出喷嘴10的截面构成。气体喷出喷嘴10具有长度方向在树脂膜50的宽度方向上延伸的壳体11,在壳体11的图示左端设有气体供给口12。在壳体11的内部以连接于气体供给口12的方式形成有上部均压室13。上部均压室13的高度随着远离喷嘴长度方向的气体供给口而减少。即形成为锥形形状。在气体喷出喷嘴10中,与树脂膜50的表面相对的面为气体喷出面14。在上部均压室13和气体喷出面14之间设有3个下部均压室15。在图1(b)中,以设有3个下部均压室15的气体喷出喷嘴10为例进行了图示,但是,下部均压室15的数量并不限定于此。在设有多个下部均压室15的情况下,这些下部均压室15在气体喷出喷嘴10的高度方向上排列,下部均压室15的相互间被冲孔金属板等多孔性且通气性的隔板17分隔。另外,上部均压室13和下部均压室15之间也被冲孔金属板等多孔性且通气性的隔板16分隔。隔板16、17均被设置成与树脂膜50的表面平行、即与x轴及z轴平行。上部均压室13及下部均压室15的外壁的整体构成气体喷出喷嘴10的壳体11(即喷嘴壳体),并且在壳体11的与树脂膜50相对的侧面形成有气体喷出面14。在图1所示的气体喷出喷嘴10中,使用了多孔性且通气性的隔板16、17,因此从气体供给口12到气体喷出面14经由上部均压室13及下部均压室15而连通。被气体供给口12供给的气体在上部均压室13中沿着大致图示x方向流动,同时从隔板16通过而进入下部均压室15,并且从隔板17通过而缓缓地改变流动方向,以与树脂膜50的表面垂直的气流的形式从气体喷出面14喷出。接下来,对本发明的一个实施方式的气体喷出喷嘴进行说明。图2是本发明的一个实施方式的气体喷出喷嘴20的剖面图,图3是用于说明该气体喷出喷嘴20的构成的概略透视立体图。对于图2及图3所示的气体喷出喷嘴20而言,壳体11、气体供给口12、上部均压室13、下部均压室15、隔板17的结构与图1所示的气体喷出喷嘴10同样,作为分隔上部均压室13和下部均压室15的隔板,使用与图1所示的隔板不同的隔板21,而且,在隔板21的上部均压室13侧的面配置多个筒状体22,这几点与图1所示不同。以下,对隔板21及筒状体22进行详细地说明。隔板21构成上部均压室13中的气体喷出面14侧的面。作为隔板21,使用通常的板构件而并非冲孔金属板等多孔性的材料。筒状体22以使作为筒的轴方向成为喷嘴宽度方向即z方向的方式配置于上部均压室13。若以在与作为筒的轴方向正交的面切断筒状体22时的形状作为筒状体22的截面形状,则筒状体22的截面形状为例如三角形或四角形等多角形形状。图3所示的筒状体22的截面形状为四角形。筒状体22的作为筒的两端成为开口23。筒状体22的长度(在喷嘴宽度方向上的长度)比气体喷出喷嘴20的喷嘴宽度方向的长度小,由此在上部均压室13的侧壁(喷嘴宽度方向两端侧的壁)与筒状体22的开口23之间形成间隔,从气体供给口12供给的气体可从该间隔经由开口23流入筒状体22的内部。在筒状体22中,在开口23可以配置冲孔金属板、网(网络)这样的多孔性且通气性的构件。另外,开口23所形成的面的朝向并无特别限定,但优选为与喷嘴长度方向平行、且与隔板21大致垂直的面。图4是用于说明筒状体22的内部构成的图,其示出隔板21和筒状体22。在图4中,箭头表示从气体供给口12向上部均压室13供给的气体的流动方向。为了便于显示筒状体22的内部,在图4中,筒状体22描绘成高度比图3所示的高度大。不过,只要能收容于上部均压室13内,则筒状体22的高度可适当地设定,因此不论是使用如图3所示的筒状体22还是使用如图4所示高度的筒状体22,都可发挥本发明的效果。在筒状体22的内部的、沿着气体喷出喷嘴20的长度方向中心线的位置以贯通筒状体22的与隔板21接触的面即筒状体22的底面和隔板21这两者的方式形成气体流通孔24。气体流通孔24的位置未必需要沿着气体喷出喷嘴20的长度方向中心线,但优选配置于长度方向中心线。在图4所示的构成中,气体流通孔24在筒状体22的底面沿着喷嘴长度方向的整个长度形成狭缝状。在未设置筒状体22的位置处的隔板21未形成贯通孔。其结果,在气体喷出喷嘴20中,从气体供给口12向上部均压室13供给的气体经由各筒状体22的开口23而流入筒状体22的内部,并经由气体流通孔24流入下部均压室15,从气体喷出面14喷出。由于每个筒状体22都设置气体流通孔24,因此若从隔板21的整体来看,则沿着喷嘴长度方配置有多个气体流通孔24。此时,气体流通孔24优选沿着喷嘴长度方向均匀地配置,因此,在隔板21上筒状体22优选以相互接触的方式配置、或者在喷嘴长度方向上相互等间隔地配置。在本实施方式的气体喷出喷嘴20中,各筒状体22具有从隔板21立起的2个壁面,其中,关于气体供给口12侧的壁面25,作为筒状体22的截面形状的内角的、壁面25与隔板21所形成的角θ优选为90°左右。更详细而言,θ为55°以上且120°以下,优选为60°以上且110°以下,更优选为75°以上且95°以下。根据本申请的发明人的研究,由后述的实施例可以明确的是:如果壁面25和隔板21所形成的角θ为该角度范围内,则从气体喷出面14喷出的气体的速度分布在喷嘴长度方向的整个长度上变得均匀。在上述的子中,在上部均压室13中设置了筒状体22,但是,设置筒状体22的均压室不一定要限定为上部均压室13。但是,由设置筒状体22所带来的整流效果最受期待的是在与气体供给口12相邻的均压室设置筒状体22的情况,因此,优选在上部均压室13配置筒状体22。当在上部均压室13设置筒状体22的情况下,未必需要在气体喷出喷嘴20中设置下部均压室15,也可以为将隔板21本身作为气体喷出面14而对树脂膜50直接吹喷从气体流通孔24流出的气体。但是,从对从气体喷出面14喷出的气流的控制性的观点考虑,优选设置下部均压室15。在图2、图3及图4所示的构成中,将截面为四角形的筒状体22相互隔离地配置于隔板21,但是,筒状体22的构成、配置并不限定于此。图5示出筒状体22的构成、配置的其它例。在图5所示的构成中,将截面形状为四角形的筒状体22以相互接触的方式在喷嘴长度方向上配置于隔板21上。气体流通孔24在筒状体22的底面的大致中心部形成为圆形,气体流通孔24的直径小于筒状体22的底面的沿着喷嘴长度方向的长度。在图5所示的筒状体22中,其壁面中处于气体供给口12一侧且从隔板21立起的壁面25与隔板21所形成的角θ为55°以上且120°以下,优选为60°以上且110°以下,更优选为75°以上且95°以下。图6示出筒状体22的构成、配置的又一其它例。图6所示的构成是下述构成:在图4所示的构成中,将筒状体22的截面形状从四角形变更为三角形。在图6所示的筒状体22中,其壁面中处于气体供给口12一侧且从隔板21立起的壁面25与隔板21所形成的角θ为55°以上且120°以下,优选为60°以上且110°以下,更优选为75°以上且95°以下。接下来,对本发明的其它实施方式的气体喷出喷嘴进行说明。在上述的实施方式的气体喷出喷嘴20中,上部均压室13被形成为从气体供给口12侧来看高度沿着喷嘴长度方向减少的锥形形状。但是,在本发明中,上部均压室的形状并不限定于锥形形状。图7所示的本发明的其它实施方式的气体喷出喷嘴30具有与图2及图3所示的气体喷出喷嘴20同样的构成,但是,具备沿着喷嘴长度方向的高度恒定的上部均压室32,这一点与图2及图3所示的气体喷出喷嘴20不同。另外,与图5所示的气体喷出喷嘴同样,相邻的筒状体22以相互接触的方式来设置。图8是用于说明图7所示的气体喷出喷嘴30的构成的概略透视立体图。在以上说明的基于本发明的气体喷出喷嘴20及30中,气体流通孔24的形状只要是从上部均压室13连通至下部均压室15或气体喷出面14的形状,就没有特别限定,但优选如图4或图6所示的、在喷嘴长度方向延伸的狭缝状的形状。另外,每1个筒状体22中,将气体流通孔24的开口面积设为s1、并且将筒状体22的除壁面22、25与隔板接触的面以外的与隔板21接触的面的面积设为s2时,开口率s1/s2优选为0.85以下。基于本发明的气体喷出喷嘴20及30中,被构成为沿着喷嘴长度方向求出气体的喷出速度的分布时的喷出速度的最大值与最小值之差相对于平均喷出速度而言大致为14%以下、优选为11%以下,但根据用作吹喷气体的对象的树脂膜50的品种的不同,喷出速度的最大值与最小值之差也可以大于该值,并无特别限定。来自气体喷出面14的气体的喷出速度优选大于0m/s且为20m/s以下的范围内,更优选大于0m/s且为7m/s以下的范围内。基于本发明的气体喷出喷嘴20及30设置于例如干燥炉内或拉幅烘箱内,并且在制造加工膜时用于对树脂膜50的表面吹喷空气或氮气等气体。作为具体例,在树脂膜50上涂布涂液、之后在干燥炉内对树脂膜50吹喷空气而将涂膜干燥时,使用气体喷出喷嘴20及30。通过在制造加工膜时在干燥炉或拉幅烘箱内使用基于本发明的气体喷出喷嘴20及30,从而得到下述等优点中的至少一者,即(1)得到表面粗糙度在膜宽度方向上均匀的加工膜;(2)得到厚度在膜宽度方向上均匀的加工膜;(3)在形成有微多孔的膜的情况下得到在膜宽度方向形成有均匀的微多孔的加工膜;(4)膜运送时的抖动得以减少,膜破裂的发生得以减少,成品率得以提高;(5)得到干燥的涂膜与树脂膜的密合性在膜宽度方向上均匀的加工膜;(6)得到无外观不良的加工膜。实施例以下,利用实施例对本发明进行更详细地说明。[实施例1]在图2及图3所示构成的气体喷出喷嘴20中,通过模拟对作为筒状体22的图6所示那样的截面形状为三角形的筒状体进行了解析。在解析中,使用作为市售的通用热流体解析软件的“star-ccm(ver.11.04)”(株式会社idaj制),进行了稳态计算。紊流的处理使用k-ε紊流模型,壁附近的紊流边界层的处理使用壁法则。上述软件是利用有限体积法对作为流体的运动方程式的纳维-斯托克斯方程式(navier-stokesequations)进行解析的软件。当然,只要能够进行同样的解析,则也可以使用任意的热流体解析软件。设定模拟了喷嘴壳体内部的流路的解析空间,将上部均压室13的喷嘴长度方向的长度设为1530mm,将喷嘴宽度方向的长度设为100mm,将气体供给口12的高度设为200mm。对于气体供给口12设定边界条件,使常温(300k)的干燥空气以3.0m/s的流速流入解析空间内。另外,对于气体喷出面14,设定压力边界,在边界条件中设定了大气压(0.1mpa)。在模拟中,筒状体22沿着喷嘴长度方向连续地配置,如图9(b)所示将在喷嘴长度方向上相邻的筒状体的相互间的距离l2设为0mm,且将筒状体配置于喷嘴长度方向的整个长度。如图9(a)所示,将筒状体22中从隔板21立起的2个壁面与隔板21(在图9(a)中以单点划线来表示)所形成的内角分别设为θ及α。筒状体22具有从隔板21立起的2个壁面,角θ为气体供给口侧的壁面25与隔板所形成的内角,角α为不是气体供给口侧的一方的壁面22与隔板所形成的内角。将各筒状体22的沿着喷嘴长度方向的长度l1设为15mm。另外,由于是模拟,因此2个壁面22、25的厚度设为零。而且,在改变角θ及角α时,沿着喷嘴长度方向求出从气体喷出面喷出的气体速度的分布。然后,将这样得到的气体速度的最大值与最小值之差除以平均喷出速度所得的值设为偏差r。速度的偏差r小时,表示结果良好。如果偏差r为7%以下,则评价为“◎”(优),如果偏差r大于7%且为11%以下,则评价为“○”(良),如果偏差r大于11%且为14%以下,则评价“△”(在实用上没有问题),如果偏差r大于14%,则评价为“×”(不良)。将结果示于表1中。【表1】(表1)θ[°]α[°]r[%]判定454514.0×5554.112.5△6054.110.3○7054.19.2○7554.16.0◎8054.16.3◎9054.16.0◎9554.16.2◎10054.17.8○11054.19.3○12054.111.3△由表1可知,对于角θ而言,如果为55°以上且120°以下,则在实用上没有问题,优选为60°以上且110°以下,更优选为75°以上且95°以下。[实施例2]在图2及图3所示构成的气体喷出喷嘴20中,与实施例1同样地通过模拟对作为筒状体22的图6所示那样的截面形状为三角形的筒状体进行了解析。关于角θ、角α及长度l1,与实施例1同样地进行了定义。而且,如图9(b)所示,改变在喷嘴长度方向上相邻的筒状体的相互间的距离l2,与实施例1同样地求出偏差r,进行了评价。将结果示于表2中。【表2】(表2)θ[°]α[°]l1[mm]l2[mm]l2/l1r[%]判定9053.115006.0◎9053.1157.50.56.3◎9053.115120.88.7○9053.11515110.3○9053.11522.51.211.8△9053.115301.513.6△由表2可知,关于在喷嘴长度方向上的筒状体的长度l1和筒状体的相互间的距离l2,如果l2/l1为1.5以下,则在实用上没有问题,l2/l1优选为1以下,l2/l1更优选为0.5以下。[实施例3]通过与实施例1同样的模拟进行解析,对筒状体22的底面上的气体流通孔的开口率进行了研究。在实施例1所使用的气体喷出喷嘴(其中,θ=90°,α=53.1°,l1=15mm)中,如图9(c)所示,将喷嘴宽度方向上的筒状体22的宽度w设为60mm,将作为狭缝状的开口而形成的气体流通孔24的宽度设为ws。与实施例1同样地求出改变了ws时的速度的偏差r,并进行了判定。气体流通孔24在喷嘴长度方向上在筒状体22的底面的整个长度上形成,因此ws/w成为每1个筒状体22中的、气体流通孔24的面积s1相对于筒状体22的底面的面积s2(底面中的开口部与非开口部的面积之和)的比率(s1/s2)即开口率。将结果示于表3中。【表3】(表3)ws[mm]w[mm]开口率(s1/s2)r[%]判定8600.136.0◎16600.275.6◎30600.505.6◎50600.835.8◎55600.928.4○60601.0010.0○由表3可知,即使在开口率为1.0、即筒状体22的底面的整体为气体流通孔24的情况下,流速的偏差r也为10%,结果为“良”,如果开口率为0.85以下,则r为7%以下,结果为“优”。即,可知开口率优选为0.85以下。附图标记说明10、20、30气体喷出喷嘴11壳体12气体供给口13、32上部均压室14气体喷出面15下部均压室16、17、21隔板22筒状体23开口24气体流通孔25壁面当前第1页12