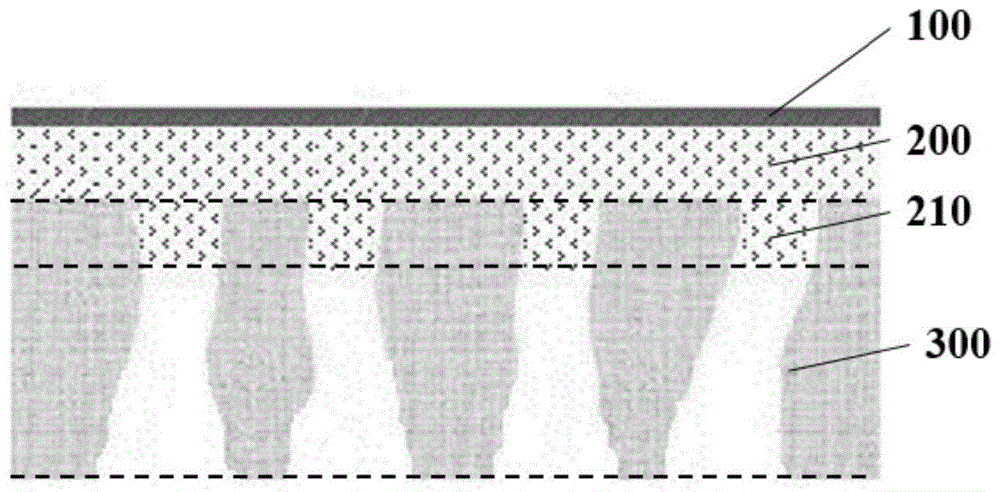
本发明属于污水处理领域,具体涉及一种中空纤维复合膜、其制备方法及其应用。
背景技术:
膜曝气式生物反应器(membraneaerationbio-filmreactor,简称mabr)是将传统生物膜法反应器过程与气体膜分离技术有机耦合而成的一种新型高效污水处理工艺。mabr技术具有氧气传输效率高、过程能耗低、操作灵活性好、模块化易集成等优势,在污水处理、水体修复等领域受到越来越多的关注。
mabr过程区别于传统的鼓泡曝气方式,利用气体膜进行无泡曝气,氧气通过膜后直接被覆盖在膜表面的微生物所利用。在保持气体压力低于膜泡点压力的情况下,空气或纯氧可以以分子的形式进入水体中,因而微生物对氧的利用效率较传统曝气过程高很多。
气体膜在mabr过程主要起两个方面的作用,即为微生物生长提供载体,并为附在膜表面的微生物提供氧气来源,因此mabr用膜需具备如下基本性能:低的传质阻力和高的氧气透过性能、适中的泡点压力、良好的机械性能以及生物亲和性(cn203139913u,一种mabr用复合膜)。
目前,实际用于mabr过程的膜主要有两类:
(1)疏水性微孔膜,代表性的为ptfe中空纤维膜和聚丙烯(pp)中空纤维膜。由于疏水性,膜孔不被水润湿,即水不能自发进入疏水微孔膜的膜孔内,但气相主体中的氧气可直接扩散进入生物膜内被微生物利用。疏水微孔膜具有传质阻力低、氧气传输效率高等优势,但缺点是曝气压较低,且随着使用时间的增长,微孔可能会被微生物的分泌物附着堵塞,造成膜孔润湿和污染,气体传质阻力剧增,进而影响mabr过程的高效进行;
(2)均质致密膜,致密膜一般由具有选择透过性的材料制备,如聚二甲基硅氧烷(pdms)。由于致密膜结构无微孔,不存在担心污染和堵塞问题,但其致命弱点是氧气的传递完全依靠膜材料的溶解扩散系数控制,氧气的传质效率较低。此外,pdms材料还具有成本高、机械强度差、使用过程中易出现断丝等缺点,限制了其大规模实际应用;
鉴于以上问题,人们尝试将上述两种膜的结构进行耦合开发复合膜,即由选择透过性皮层和多孔性支撑层组成的具有高透过性的选择透过性膜(cn203139913u,一种mabr用复合膜;cn103182254b,一种mabr用复合膜及制备方法)。从理论上说,复合膜是最适合mabr过程的膜。选择透过性皮层材料可为pdms,其透气性能好,也具有一定的氧氮分离性能;多孔性支撑层最优选择为ptfe,其疏水性好、机械强度高,同时透气压力低,有助于降低操作能耗。但由于ptfe微孔膜的表面孔径一般较大(>0.1μm),通过溶液涂覆、加热、交联法制备pdms层时,由于基膜膜孔过大,涂覆的pdms溶液极易渗漏到膜孔内,导致交联产物无法完成架桥出现塌陷,从而制备的pdms层有大量缺陷,无法形成致密结构。此外,使用过程中pdms层极易破裂和脱落,很难制得实用性和稳定性好的中空纤维复合膜。
技术实现要素:
1.要解决的问题
针对现有技术中的复合膜的表皮层的强度差的问题,本发明提供一种中空纤维复合膜,表皮层嵌入中间层的渗透层占表皮层的厚度的0.01-0.5,渗透层提高了两层之间的结合强度,使得表皮层不易破裂和脱落,解决了表皮层的强度差的问题。
进一步地,本发明还提供一种中空纤维复合膜在mabr工艺中的应用,使用了机械强度和稳定性更佳的复合膜,延长了装置的使用寿命。
进一步地,本发明还提供一种中空纤维复合膜的制备方法,依次对支撑层、中间层和表皮层进行制备,表皮层嵌入中间层的渗透层厚度控制为表皮层的0.01-0.5,工艺简单,容易制得实用性和稳定性好的中空纤维复合膜,成品率高。
2.技术方案
为了解决上述问题,本发明所采用的技术方案如下:
本发明提供一种中空纤维复合膜,包括由内到外依次设置的支撑层、中间层和表皮层;中间层远离支撑层的一侧的平均孔径为p1,中间层与支撑层相接触的一侧的平均孔径为p2,p1<p2;表皮层嵌入中间层的渗透厚度为h1,表皮层的厚度为h2,h1:h2=0.05-0.5。
优选地,支撑层的孔径为1-5μm,孔隙率60%-85%,和/或中间层远离支撑层的一侧的平均孔径为p1,且p1=10-50nm。
优选地,中间层嵌入支撑层的渗透厚度为h3,中间层的厚度为h4,h3:h4=0.1-0.5。
优选地,中间层的厚度为h4,h4=20-100μm,表皮层的厚度为h2,h2=0.5-10μm。
优选地,支撑层与中间层的制作材料均为含氟化合物。
优选地,表皮层的制作材料为聚二甲基硅氧烷。
优选地,支撑层的制作材料为聚四氟乙烯;中间层的制作材料为疏水材料,疏水材料为聚偏氟乙烯。
本发明还提供一种上述mabr用中空纤维复合膜在mabr工艺中的应用。
本发明还提供一种中空纤维复合膜的制备方法,具体步骤如下,
s100、支撑层的制备:将原料和溶剂混合后熟化,再将熟化后的混合物依次经过糊状挤出、拉伸和烧结工艺制得支撑层;支撑层的平均孔径为1-5μm,孔隙率60%-85%;
s200、支撑层/中间层复合膜的制备,将上述支撑层进行溶液涂覆、相转化凝固并成形,制得支撑层/中间层复合膜;支撑层/中间层复合膜的中间层远离支撑层的一侧的平均孔径为p1,中间层与支撑层相接触的一侧的平均孔径为p2,p1<p2,且p1=10-50nm;
s300、支撑层/中间层/表皮层复合膜的制备,将涂层液涂覆于上述支撑层/中间层复合膜,加热后得到支撑层/中间层/表皮层复合膜;支撑层/中间层/表皮层复合膜的表皮层嵌入中间层的渗透厚度为h1,表皮层的厚度为h2,h1:h2=0.05-0.5。
优选地,s200的溶液涂覆还包括施加压力,施加的压力值为0.05-0.5atm。
3.有益效果
相比于现有技术,本发明的有益效果为:
(1)本发明的一种中空纤维复合膜,支撑层起机械支撑作用,中间层起中间过渡作用,表皮层为致密功能皮层,起氧气传输和生物膜载体的作用;中间层牢固结合支撑层和表皮层,表皮层具有一定的渗透厚度,提高了两层之间的结合强度,避免在实际使用过程会出现剥离、脱落行为,增强了复合膜使用性能,延长使用寿命,解决了现有技术中的复合膜的表皮层的强度差的问题。
(2)本发明的一种中空纤维复合膜,支撑层的孔径限定了其大孔结构,其多孔特性有利于降低气体传递阻力;而当孔径为1-5μm时,中间层相对于支撑层具有一定的渗透厚度,增强了复合膜的机械强度,避免中间层脱落;而表皮层的厚度决定了复合膜的传氧渗透通量。
(3)本发明的一种中空纤维复合膜,支撑层和中间层均采用疏水材料制成,可防止使用过程中水蒸气冷凝导致的膜孔润湿,不会导致氧气传质阻力的增加;中间层与支撑层均为含氟化合物,亲和性好,两层间不会发生剥离问题;不仅如此,当表皮层为聚二甲基硅氧烷、中间层为聚偏氟乙烯时,中间层与表皮层也有很好的结合能力,避免剥落。
(4)本发明的一种中空纤维复合膜在mabr工艺中的应用,使用了机械强度和稳定性更佳的复合膜,延长了装置的使用寿命。
(5)本发明的一种中空纤维复合膜的制备方法,制备过程简单,通过施加不同程度的压力制备复合膜,成品率高。
附图说明
图1为本发明的结构示意图;
图2为本发明的截面示意图。
其中:100、支撑层;200、中间层;210、渗透层ⅱ;300、表皮层;400、空腔。
具体实施方式
下面结合附图对本发明进行进一步说明。下文中结合具体的示例性实施例详细描述了本发明。但是,应当理解,可在不脱离由所附权利要求限定的本发明的范围的情况下进行各种修改和变型。详细的描述和附图应仅被认为是说明性的,而不是限制性的,如果存在任何这样的修改和变型,那么它们都将落入在此描述的本发明的范围内。此外,背景技术旨在为了说明本技术的研发现状和意义,并不旨在限制本发明或本申请和本发明的应用领域。
实施例1
本发明提供一种中空纤维复合膜,可用于mabr工艺。如图1所示,该中空纤维复合膜包括支撑层300、中间层200和表皮层100,中间层200设置于支撑层300与表皮层100之间,用于解决表皮层100直接覆盖于支撑层300时易剥落的问题。如图2所示,该中空纤维复合膜中设置有使气体通过的空腔400,支撑层300、中间层200和表皮层100由空腔400至外部依次设置。
支撑层300为大孔支撑基膜层,起机械支撑作用,避免使用过程中的断丝现象,其拉伸强度>20mpa。当孔径为1-5μm,孔隙率60%-85%时,疏水和多孔特性有利于降低气体传递阻力。支撑层300与中间层200均由含氟化合物制成,进一步说明,支撑层300一般为聚四氟乙烯(ptfe)。
中间层200为介孔膜过渡层,起中间过渡作用,牢固结合支撑层300和表皮层100,实现表皮层100的均匀无缺陷制备。中间层200的制作材料为疏水材料,一般使用聚偏氟乙烯(pvdf)制备。中间层200的疏水特性也避免水蒸气冷凝导致的润湿,从而增加氧气传质阻力等问题。中间层200的厚度为h4,h4=20-100μm,中间层200与支撑层300之间设置有渗透层ⅱ210,渗透层ⅱ210为中间层200嵌入支撑层300的部分。渗透层的厚度限定了两层膜之间的连接形式,决定了两层之间的结合强度。如果无渗透层,则两层膜在实际使用过程中会出现剥离、脱落行为,影响复合膜的使用性能和寿命。渗透层ⅱ210的厚度为h3,中间层200的厚度为h4,h3:h4=0.1-0.5。不仅如此,中间层200为不对称结构,中间层200远离支撑层300的一侧为介孔结构,其平均孔径为p1,中间层200与支撑层300相接触的一侧为指状大孔结构,其平均孔径为p2,p1<p2,且p1=10-50nm。如果平均孔径p1太大则无法实现表皮层材料在中间层200上的均匀制备,如果平均孔径p1太小则中间层200本身气体渗透性能差,无法满足mabr膜传氧要求。
表皮层100为致密功能层,一般为聚二甲基硅氧烷(pdms),起氧气传输和生物膜载体的作用,其致密结构防止mabr膜的润湿和污染。值得说明的是,当表皮层100为pdms层,中间层200为pvdf层时,二者具有极好的结合能力,防止剥落现象。表皮层100的厚度为h2,h2=0.5-10μm。表皮层100的厚度决定了复合膜的传氧渗透通量,即mabr过程的处理效率。表皮层100与中间层200之间设置有渗透层ⅰ,渗透层ⅰ为表皮层100嵌入中间层200的部分,渗透层ⅰ的厚度为h1,表皮层100的厚度为h2,h1:h2=0.05-0.5。此设计可以提高两层之间的结合强度,避免在实际使用过程出现剥离、脱落行为,增强了复合膜使用性能,延长使用寿命。
本发明的一种中空纤维复合膜的制备方法,具体步骤如下,
s100、支撑层100的制备:将原料和溶剂混合后熟化,再将熟化后的混合物依次经过糊状挤出、拉伸和烧结工艺制得支撑层100;支撑层100的平均孔径为1-5μm,孔隙率60%-85%;
s200、支撑层/中间层复合膜的制备,将上述支撑层100进行溶液涂覆、相转化凝固并成形,制得支撑层/中间层复合膜;支撑层/中间层复合膜的中间层200远离支撑层100的一侧的平均孔径为p1,中间层200与支撑层300相接触的一侧的平均孔径为p2,p1<p2,且p1=10-50nm;溶液涂覆过程还包括施加压力,施加的压力值为0.05-0.5atm;
s300、支撑层/中间层/表皮层复合膜的制备,将涂层液涂覆于上述支撑层/中间层复合膜,加热后得到支撑层/中间层/表皮层复合膜;支撑层/中间层/表皮层复合膜的表皮层100嵌入中间层200的渗透层的厚度为h1,表皮层100的厚度为h2,h1:h2=0.05-0.5。
在本实施例中,具体的制备方法如下:
1)将ptfe分散树脂和溶剂油均匀混合,质量分数分别为76%和24%;
2)将上述均匀混合后的物料在40℃下熟化12h;
3)将熟化后的上述混合物装入预压设备,在2.0mpa下预压脱气5min,制得ptfe坯体;
4)将制备的ptfe坯体装入糊状挤出设备,60℃下推挤制得初生ptfe中空纤维膜;
5)初生ptfe中空纤维膜在200℃下热处理10min进行脱脂以除去溶剂油;
6)将脱脂后的ptfe中空纤维膜在250℃下长度方向拉伸5.0倍,拉伸速度10m/min;
7)将拉伸后的ptfe中空纤维膜在360℃进行烧结5min,制得ptfe支撑层,其内径0.8mm、外径1.6mm、平均孔径5.0μm,孔隙率85%,拉伸强度32mpa;
8)将pvdf溶于n,n-二甲基乙酰胺中,其中pvdf质量分数为10%,在80℃下机械搅拌12h制得均匀透明的铸膜液;
9)利用自制纺丝设备将铸膜液涂覆于ptfe支撑层外表面,涂覆过程中施加0.2atm压力使铸膜液部分渗于ptfe中空纤维膜孔中,随后浸入水凝胶体系进行相转化,从而制得ptfe/pvdf复合膜。pvdf总厚度h4为50μm,在ptfe基膜中的渗透层ⅱ210的厚度h3为20μm,pvdf中间层为不对称结构,靠近ptfe支撑层的一侧为指状大孔结构,而远离ptfe支撑层的一侧表面孔更小,平均孔径p1为10nm;
10)将乙烯基pdms、含氢硅油交联剂和铂催化剂溶于正己烷,质量浓度分别为2.0%、0.5%和500ppm,机械搅拌均匀,制得涂层液;
11)将ptfe/pvdf复合膜表面水珠用气刀除去,浸入pdms涂层液,停留时间为1min,重复次数为3次;空气干燥5min后,在75℃下热处理120min,制得ptfe/pvdf/pdms中空纤维复合膜;pdms渗于pvdf膜孔的渗透层ⅰ的厚度h1为0.5μm;pdms表皮层的总厚度h2为5.0μm。
实施例2
本实施例的基本内容同实施例1,其不同之处在于,涂覆过程中施加0.05atm压力,制备得到的复合膜中的ptfe支撑层的平均孔径3.0μm,孔隙率70%。pvdf总厚度h4为20μm,在ptfe基膜中的渗透层ⅱ210的厚度h3:h4=0.5,pvdf中间层为不对称结构,靠近ptfe支撑层的一侧为指状大孔结构,而远离ptfe支撑层的一侧表面孔更小,平均孔径30nm。pdms表皮层的总厚度h2为10μm;渗透层ⅰ的厚度h1:h2=0.05。
实施例3
本实施例的基本内容同实施例1,其不同之处在于,涂覆过程中施加0.5atm压力,制备得到的复合膜中的ptfe支撑层的平均孔径1.0μm,孔隙率60%。pvdf总厚度h4为100μm,在ptfe基膜中的渗透层ⅱ210的厚度h3:h4=0.1,其pvdf中间层为不对称结构,靠近ptfe支撑层的一侧为指状大孔结构,而远离ptfe支撑层的一侧表面孔更小,平均孔径50nm。pdms表皮层的总厚度h2为2μm;渗透层ⅰ的厚度h1:h2=0.5。
对比例1
本对比例的基本内容同实施例1,其不同之处在于,具体制备步骤如下:
1)将ptfe分散树脂和溶剂油均匀混合,质量分数分别为76%和24%;
2)将上述均匀混合后的物料在40℃下熟化12h;
3)将熟化后的上述混合物装入预压设备,在2.0mpa下预压脱气5min,制得ptfe坯体;
4)将制备的ptfe坯体装入糊状挤出设备,60℃下推挤制得初生ptfe中空纤维膜;
5)初生ptfe中空纤维膜在200℃下热处理10min进行脱脂以除去溶剂油;
6)将脱脂后的ptfe中空纤维膜在250℃下长度方向拉伸5.0倍,拉伸速度10m/min;
7)将拉伸后的ptfe中空纤维膜在360℃进行烧结5min,制得ptfe中空纤维支撑基膜,其内径0.8mm、外径1.6mm、平均孔径5.0μm,孔隙率85%,拉伸强度32mpa;
8)将乙烯基pdms、含氢硅油交联剂和铂催化剂溶于正己烷,质量浓度分别为2.0%、0.5%和500ppm,机械搅拌均匀,制得涂层液;
9)将ptfe膜表面水珠用气刀除去,浸入pdms涂层液,停留时间为1min,重复次数为3次;空气干燥5min后,在75℃下热处理120min,制得ptfe/pdms中空纤维复合膜。
对比例2
本对比例的基本内容同实施例1,其不同之处在于,具体制备步骤如下:
1)将pvdf溶于n,n-二甲基乙酰胺中,其中pvdf质量分数为10%,在80℃下机械搅拌12h制得均匀透明的铸膜液;
2)利用自制纺丝设备将铸膜液纺制成中空纤维膜,随后浸入水凝胶体系进行相转化制得pvdf基膜。pvdf基膜内径0.8mm、外径1.2mm,壁厚度为200μm,其为不对称结构,内表面一侧为指状大孔结构,外表面一侧表面孔更小,平均孔径10nm;
3)将乙烯基pdms、含氢硅油交联剂和铂催化剂溶于正己烷,质量浓度分别为2.0%、0.5%和500ppm,机械搅拌均匀,制得涂层液;
4)将pvdf基膜表面水珠用气刀除去,浸入pdms涂层液,停留时间为1min,重复次数为3次;空气干燥5min后,在75℃下热处理120min,制得pvdf/pdms中空纤维复合膜。pdms渗于pvdf膜孔的深度为0.5μm;pdms致密膜表皮层的总厚度5.0μm。
在本对比例中,将实施例1、对比例1和本对比例中制得的ptfe/pdms、pvdf/pdms和ptfe/pvdf/pdms中空纤维复合膜进行性能表征,具体见下表1:
表1中空纤维复合膜的性能表征
由表可知,本发明制备的中空纤维复合膜具有良好的机械强度、氧气传输性能和生物亲和性,非常适合用于无泡曝气供氧的mabr过程。
更具体地,尽管在此已经描述了本发明的示例性实施例,但是本发明并不局限于这些实施例,而是包括本领域技术人员根据前面的详细描述可认识到的经过修改、省略、例如各个实施例之间的组合、适应性改变和/或替换的任何和全部实施例。权利要求中的限定可根据权利要求中使用的语言而进行广泛的解释,且不限于在前述详细描述中或在实施该申请期间描述的示例,这些示例应被认为是非排他性的。在任何方法或过程权利要求中列举的任何步骤可以以任何顺序执行并且不限于权利要求中提出的顺序。因此,本发明的范围应当仅由所附权利要求及其合法等同物来确定,而不是由上文给出的说明和示例来确定。