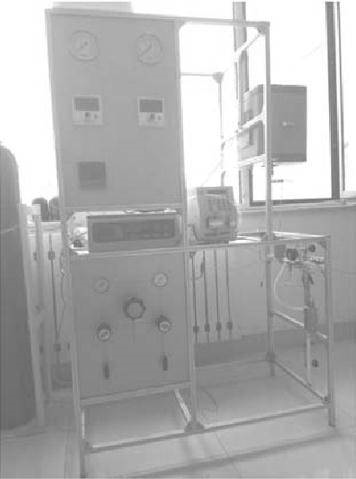
本发明涉及新型催化材料及助剂
技术领域:
,尤其涉及一种用以2-甲基四氢呋喃生产所用的镍系新型催化材料,以及利用该材料进行2-甲基四氢呋喃生产的方法。
背景技术:
:2-甲基四氢呋喃是一种有机化合物,分子结构式为在工业生产,目前是一种重要的原料,常用作有机中间体和优良的溶剂,在有机金属反应、汽车燃油添加剂、以及用于医药磷酸氯喹中间体方面,得到了广泛的应用。2-甲基四氢呋喃的制备方法有很多,主要有二元醇法、内酯法以及糠醛法等。从上世纪五十年代开始,proskuryakovva,shikinni,baikovazhg等人就开始陆续研究在催化剂的作用下,将糠醇还原得到2-甲基四氢呋喃的方法和具体工艺,但是用糠醛作原料所需反应条件苛刻,尤其是压力要求较大,设备投资高,并且糠醛的反应效率很低,且容易使催化剂造成焦化、失活等问题。现在2-甲基四氢呋喃的主流生产方法为通过2-甲基呋喃催化加氢而得,在由2-甲基呋喃催化加氢制备2-甲基四氢呋喃的反应中,可用的催化剂种类较多,工业生产中常用镍作为催化剂。近年来,cn201210431363.1、cn201910264902.9、cn201911365546.6、cn201811500771.1、cn201410226289.9等专利文献均对2-甲基呋喃催化加氢制备2-甲基四氢呋喃过程中,所用的催化剂进行了研究,但是上述文献往往集中对催化剂的组分、载体以及制备方法进行研究,所制备的催化剂适用于实验室或小试过程中的制备。但对于大规模的工业生产而言,即便是同样组分的催化剂,其形态、用量、反应条件,以及对反应时间和反应效率的影响是巨大的,但现有技术中尚未见对上述问题进行研究的文献。技术实现要素:为了解决上述技术问题,本发明提供一种用以2-甲基四氢呋喃生产所用的镍系新型催化材料,以及利用该材料进行2-甲基四氢呋喃生产的方法。本发明完整的技术方案包括:一种2-甲基四氢呋喃生产用镍系催化材料的制备方法,包括如下步骤:(1)采用质量比为42%的镍粉、质量比为54%的铝粉、质量比为6%的钴粉进行混合;(2)取80~100重量份步骤(1)得到的混合物和150~320重量份的有机溶剂,加入球磨机内,球磨至浆料粒径为30~50μm后,在120~150℃内进行加热干燥,至有机溶剂挥发完毕;(3)取100~150重量份步骤(2)得到的混合物,加入20~50重量份的alooh·h2o和20~80重量份的聚乙烯,在剪切搅拌混合机中,以1000~2000rpm的速度进行高速剪切搅拌1.5~2h,随后挤出成直径为3.2~3.6mm的条状成型物;(4)在650~850℃下烧结2小时,采用碱溶液进行活化,冲洗后得到所用的催化剂。优选的,利用催化剂进行2-甲基四氢呋喃制备的方法,采用上述催化剂进行2-甲基四氢呋喃制备的生产线包括:2-甲基呋喃储罐,该2-甲基呋喃储罐连接2-甲基呋喃预热器,2-甲基呋喃预热器后连接2-甲基呋喃蒸发器,2-甲基呋喃蒸发器后连接气液分离器;2-甲基呋喃蒸发器同时连接氢气和氮气气源;气液分离器通过换热器连接列管反应器,气液分离器同时还通过回流管路连接到2-甲基呋喃储罐;列管反应器随后顺序串联连接第一换热器、第二换热器和第三换热器,第三换热器后连接吸收塔;第一换热器在其支路上连接重组分接收罐,第二换热器在其支路上连接第一粗品接收罐,第三换热器在其支路上连接第二粗品接收罐;优选的,具体制备方法为:所用的原料2-甲基四氢呋喃位于2-甲基呋喃储罐中,2-甲基呋喃首先进入2-甲基呋喃预热器并在此进行预热后,进入2-甲基呋喃蒸发器进行蒸发,蒸发后的气态2-甲基呋喃进入气液分离器,在气液分离器中与进入气液分离器的h2进行混合,该过程中被分离出的液态2-甲基呋喃通过回流管路回到2-甲基呋喃储罐中,混合后的气体进入列管反应器6中,并在此处在催化剂的作用下进行加氢反应;反应后的气体依次通过第一换热器、第二换热器和第三换热器,在第一换热器中冷凝出的重组分进入重组分接收罐,在第二换热器和第三换热器中冷凝得到的组分分别进入第一粗品接收罐和第二粗品接收罐,从第三换热器中排出的尾气进入吸收塔,在放置于冰水浴中的二甲基甲酰胺溶剂中进行吸收后排空。一种2-甲基四氢呋喃的制备方法,列管反应器中,在列管反应器中,发生的主反应为:主要副反应为:附图说明图1为本发明公开的2-甲基四氢呋喃生产线流程图。图2为本发明列管反应器实物图。图中:1—2-甲基呋喃储罐;2—2-甲基呋喃预热器;3—2-甲基呋喃蒸发器;4—气液分离器-5—换热器;6—列管反应器;7—第一换热器;8—第二换热器;9—第三换热器;10—重组分接收罐;11—第一粗品接收罐;12—第二粗品接收罐;13—吸收塔。具体实施方式下面将结合本申请实施方式中的附图,对本申请的实施方式中的技术方案进行清楚、完整的描述,显然,所描述的实施方式仅仅是作为例示,并非用于限制本申请。下面对采用本发明的催化剂,利用固定床反应器对2-甲基呋喃加氢制备2-甲基四氢呋喃的整个工艺过程进行说明。首先,本发明所用的催化剂的制备过程为,采用质量比为42%的镍粉、质量比为54%的铝粉、质量比为6%的钴粉进行混合,得到混合物a。随后取80~100重量份的混合物a和150~320重量份的有机溶剂,加入球磨机内,球磨至浆料粒径为30~50μm后,在120~150℃内进行加热干燥,至有机溶剂挥发完毕后得到混合物b。随后取100~150重量份的混合物b,20~50重量份的一水合氧化铝和20~80重量份的聚乙烯,在剪切搅拌混合机中,以1000~2000rpm的速度进行高速剪切搅拌1.5~2h,随后挤出成直径为3.2~3.6mm的条状物,然后在650~850℃下烧结2小时,采用碱溶液进行活化,冲洗后得到所用的催化剂。采用该方法制备的条状ni系催化剂,比表面积大于250m2/g,直径约为3mm,长度约为4-10mm,强度大于50n/cm,堆密度为0.50~0.55g/cm3。在上述催化剂的设计过程中,首先,根据反应的特性,选择镍、钴作为复合活性组分,兼顾生产成本和催化效率,随后,采用球磨的方式细化原料以提高催化效果,在球磨过程中加入有机溶剂以避免氧化,同时,采用铝系和高分子聚合物作为复合粘结剂,采用剪切搅拌的方式使粘结剂和活性组分得到充分均匀混合,使催化剂非常容易成型,并且避免了在碱活化过程中对氧化铝载体的过多腐蚀,提高了强度,实现了催化剂强度和催化活性的平衡,提高了催化剂的综合性能。利用本发明的催化剂,可以使2-甲基呋喃的收率≧98.0%,每吨催化剂可生产高达600-800吨2-甲基四氢呋喃。采用上述催化剂进行2-甲基四氢呋喃制备的生产线如图1所示,包括2-甲基呋喃储罐1,该2-甲基呋喃储罐1连接2-甲基呋喃预热器2,并使2-甲基呋喃在此预热,2-甲基呋喃预热器2后连接2-甲基呋喃蒸发器3,2-甲基呋喃蒸发器3后连接气液分离器4;2-甲基呋喃蒸发器3同时连接氢气和氮气气源。气液分离器4通过换热器5和列管反应器6,气液分离器4同时还通过回流管路连接到2-甲基呋喃储罐1。列管反应器6随后顺序串联连接第一换热器7、第二换热器8和第三换热器9,第三换热器9后连接吸收塔。第一换热器7在其支路上连接重组分接收罐10,第二换热器8在其支路上连接第一粗品接收罐11,第三换热器9在其支路上连接第二粗品接收罐12。生产所用的原料2-甲基呋喃位于2-甲基呋喃储罐1中,2-甲基呋喃首先进入2-甲基呋喃预热器2在此进行预热后,进入2-甲基呋喃蒸发器3进行蒸发,蒸发后的气态2-甲基呋喃进入气液分离器4,在气液分离器中与进入气液分离器的h2进行混合,该过程中被分离出的液态2-甲基呋喃通过回流管路回到2-甲基呋喃储罐1中,混合后的气体进入列管反应器6中,并在此处在催化剂的作用下进行加氢反应。在该反应过程中,反应的速度和反应程度是直接影响生产效率的两个关键因素,在实际工业生产中,需要对上述两个因素统筹协同考虑,反应的速度主要取决于通入的气体流速或流量,而在本发明中,经过研究发现,在该过程中,对于不同的气体流速流量,在反应器中的催化剂温度、催化剂堆装高度、堆装密度,催化剂形状特点均会产生不同的影响,不同的组合参数下,甚至能使2-甲基呋喃的收率在60%~98.5%之间波动。因此,根据实际工业需要,设计出合理的反应参数,既能保证工业用的产量,又能使收率维持在一个较高的水平,提高产率,是一个相当关键的问题。因此,针对上述问题,本发明在实际生产中,分别研究了反应过程中的温度压力等参数,以及催化剂的各相关参数对反应速度和反应程度的各自影响,以及其对上述因素的综合影响,经过分析拟合以及实际的生产验证。得到如下的反应关系:式中:s为单位时间内送入的2-甲基呋喃流量,范围为40~90kg/h。m为混合气体中,氢气与2-甲基呋喃的摩尔比,取值范围为1.8~2.2。h为催化剂床层的高度与列管反应器的高度之比,取值范围为0.4~0.8。s为催化剂的比表面积,取值范围为250~280m2/g。ρ为本发明催化剂的堆密度,取值范围为0.50~0.55g/cm3,。n为单位换算系数,取值范围为0.45~0.48。针对上述2-甲基呋喃流量使用,在生产中进行了实际验证,结果如表1所示,可以看出,根据实际生产的参数设计选用合理的原料流量,可以比较明显地提高原料的收率,在保证催化效率的同时提高了产量。表1生产参数与收率的关系序号2-甲基呋喃流量氢气/2-甲基呋喃床层/反应器高度催化剂比表面积催化剂堆密度收率实施例1721.80.62500.594.4%实施例2672.00.52500.598.3%对比例1851.80.62500.584.2%对比例2772.00.52500.582.1%此外本发明为了使该条件下的催化剂能取得更好的催化效率,还限定了在上述条件下,催化剂的形状为条状,直径约为3mm,长度约为4-10mm,强度大于50n/cm。在列管反应器中,发生的主反应为:主要副反应为:此外本发明为了获得更高的反应效率和速度,还限定了在前述条件的基础上,反应器中反应温度为90-120℃,反应压力为10-20kpa。反应后的气体依次通过第一换热器7、第二换热器8和第三换热器9,在第一换热器中冷凝出的重组分进入重组分接收罐,在第二换热器和第三换热器中冷凝得到的组分分别进入第一粗品接收罐和第二粗品接收罐12,从第三换热器中排出的尾气进入吸收塔13,在放置于冰水浴中的dmf溶剂中进行吸收后排空。根据上述的工艺,2-甲基四氢呋喃的收率≧98.0%,副产物为2-戊醇和2-戊酮,每吨催化剂可生产600-800吨2-甲基四氢呋喃,极大地提高了生产效率,适合大规模的工业应用。以上申请的仅为本申请的一些实施方式。对于本领域的普通技术人员来说,在不脱离本申请创造构思的前提下,还可以做出若干变型和改进,这些都属于本申请的保护范围。当前第1页12