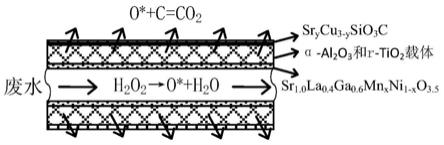
[0001]
本发明属于废水处理领域,具体涉及一种处理含过氧化物废水的催化剂及其制备和使用方法。
背景技术:[0002]
环氧丙烷是国家重点鼓励发展的高端石化产品,是支撑聚氨酯新材料、精细化工等产业发展非常重要的基础有机化工原料,其生产工艺主要有氯醇化法、共氧化法和直接氧化法。随着我国精细化工和聚氨酯工业的发展,环氧丙烷产品市场前景日益广阔,但是目前我国环氧丙烷生产主要采用的是氯醇法生产工艺,该工艺存在对设备腐蚀严重、产生的含氯化钙废水严重污染环境等缺点。乙苯共氧化法环氧丙烷生产技术具有三废少、联产物附加值高、能耗低、经济性好等综合优点。但其产生的废水中含有乙苯过氧化氢(ebhp)和小分子过氧化氢,还有醛、酚、酸、酯等物质,废水中的过氧化物自身发生分解释放出氧气而与有机物蒸汽形成爆炸性混合物,是一种威胁安全生产的潜在危险因素。
[0003]
目前,行之有效的方法是对过氧化物废水进行及时的分解处理,降低废水的停留时间,采用催化分解的形式分解过氧化物,同时产生的羟基自由基破坏难降解物质的分子结构,提升废水的生化性。其中,催化过氧化氢氧化废水技术具有良好的处理效果,开发高效、价廉且稳定的催化剂是促进该技术工业化应用的关键。过渡金属、贵金属、稀土金属是20世纪以来研究最多的催化剂活性组分。贵金属催化剂的催化活性和稳定性都相当高,但由于贵金属的储存量比较稀少且价格昂贵,所以很难在工业上大规模应用。在非贵金属催化剂中,mn基催化剂缺点是催化剂不稳定,形成锰酸根和高锰酸根溶解,溶出量大,容易失活且造成二次污染。另外,在催化过氧化氢氧化废水技术中,作为氧化剂的过氧化氢在中性或碱性条件下容易分解成氧气,与溶液中的有机物形成爆炸混合物,无法保证生产装置的本质安全。
[0004]
综上所述,目前含过氧化物有机废水的处理方法中,催化剂成本高或易流失并造成二次污染,同时过氧化物分解形成的氧气与有机物混合后可能会达到爆炸极限,影响装置运行的本质安全。
技术实现要素:[0005]
本发明的目的在于提供一种处理含过氧化物废水的催化剂,该催化剂采用非贵金属活性组分,不易流失且不会造成二次污染,并通过两次催化不同的反应,避免过氧化物分解成氧气所带来的本质安全问题。
[0006]
为了达到以上发明目的,本发明采用如下技术方案:
[0007]
一种处理含过氧化物废水的膜催化剂,所述膜催化剂载体的两侧分别为活性组分sr
1.0
la
0.4
ga
0.6
mn
x
ni
1-x
o
3.5
膜和sr
y
cu
3-y
sio
3
c膜,其中x为0.4-0.7,优选0.55-0.65,y为0.3-0.6,优选0.4-0.5;所述膜催化剂中,sr
1.0
la
0.4
ga
0.6
mn
x
ni
1-x
o
3.5
膜占比1.0-5.0%,优选2.0-3.0%,sr
y
cu
3-y
sio
3
c膜占比5.0-10.0%,优选6.0-7.0%,以催化剂总质量计。
[0008]
当含过氧化物的有机废水流经所述膜催化剂时,过氧化物在载体的一侧被sr
1.0
la
0.4
ga
0.6
mn
x
ni
1-x
o
3.5
膜催化分解生成氧物种,而具有钙钛矿型结构载体的晶体结构中有氧空穴,具备传输氧物种的能力,氧物种通过载体的有氧空穴后,在载体的另一侧经sr
y
cu
3-y
sio
3
c膜催化与同时透过膜催化剂的短链小分子有机物反应生成co
2
。所述催化剂能够快速分解处理含过氧化物的废水,且避免过氧化物分解形成氧气与有机物混合后达到爆炸极限,从而提升装置运行的本质安全。其中的氧物种是指在催化剂作用下将过氧化物转变为羟基自由基。
[0009]
本发明中,所述载体为钙钛矿型结构,优选α-al
2
o
3
和r-tio
2
形成的钙钛矿型结构;优选的,所述α-al
2
o
3
和r-tio
2
的质量比为(0.2-0.8):1,优选(0.5-0.6):1。
[0010]
本发明的另一目的在于提供一种制备所述膜催化剂的方法。
[0011]
一种制备所述膜催化剂的方法,所述方法包含以下步骤:
[0012]
(1)将载体原料混合后压合得到载体a;
[0013]
(2)将硝酸锶和硝酸铜溶解得到水溶液,混入sic粉,涂覆在载体a一侧,高温焙烧后得到膜催化剂b;
[0014]
(3)将硝酸锶、硝酸镧、硝酸镓、硝酸锰和硝酸镍溶解得到水溶液,涂覆在膜催化剂b的另一侧,高温焙烧后得到膜催化剂c。
[0015]
本发明中,所述步骤(1)将载体原料压合成中空圆柱形载体a;优选的,所述中空圆柱形载体的外径20-200mm,优选50-60mm,壁厚1-10mm,优选3-5mm。
[0016]
本发明中,所述步骤(2)中焙烧温度800-1500℃,优选1000-1100℃,焙烧时长3-8h;优选的,步骤(2)将活性组分原料涂敷在中空圆柱形载体a的外侧。
[0017]
本发明中,所述步骤(3)中焙烧温度400-800℃,优选500-600℃,焙烧时长3-8h;优选的,步骤(3)将活性组分原料涂敷在中空圆柱形载体a的内侧。
[0018]
本发明的再一目的在于提供一种处理含过氧化物废水的方法。
[0019]
一种处理含过氧化物废水的方法,所述方法采用上述的催化剂或上述方法制备的催化剂。
[0020]
本发明中,所述废水中的过氧化物在载体的一侧被sr
1.0
la
0.4
ga
0.6
mn
x
ni
1-x
o
3.5
膜催化分解生成氧物种,氧物种通过载体的有氧空穴后,在载体的另一侧被sr
y
cu
3-y
sio
3
c膜催化与同时透过膜催化剂的短链小分子有机物反应生成co
2
;优选的,所述废水从中空圆柱形膜催化剂的内部通过,废水中的过氧化物在载体内侧被sr
1.0
la
0.4
ga
0.6
mn
x
ni
1-x
o
3.5
膜催化分解生成氧物种,氧物种通过载体的有氧空穴后,在载体外侧被sr
y
cu
3-y
sio
3
c膜催化与同时透过膜催化剂的短链小分子有机物反应生成co
2
。
[0021]
本发明中,所述废水ph值为6-11。
[0022]
本发明中,所述废水温度20-80℃,废水体积空速1-3h-1
。
[0023]
在一种实施方案中,所述方法可以处理过氧化物浓度为2000-4000mg/l(以h
2
o
2
计)、cod浓度为20,000-30,000mg/l的难处理废水。
[0024]
本发明的又一目的在于提供一种膜催化剂的用途。
[0025]
一种膜催化剂的用途,上述的催化剂、或上所述的方法制备的催化剂、或上述废水处理方法使用的催化剂,用于处理含过氧化物的废水,优选用于处理乙苯共氧化法制环氧丙烷形成的含过氧化物的有机废水。
[0026]
与现有技术相比,本发明的积极效果在于:
[0027]
(1)所述催化剂采用非贵金属活性组分,不易流失且不会造成二次污染;
[0028]
(2)所述催化剂通过两次催化不同的反应,高效处理含过氧化物的废水,避免过氧化物分解成氧气所带来的本质安全问题;
[0029]
(3)所述催化剂可在ph=6-11的宽ph范围内处理任何含有过氧化物的有机废水,处理条件温和,对设备要求低。
附图说明
[0030]
图1为所述中空圆柱形催化剂的轴向剖面示意图;
[0031]
图2为膜催化反应装置流程示意图,反应器中有竖立的中空圆柱形催化剂。
具体实施方式
[0032]
为了更清楚地说明本发明,列举以下实例,但其对本发明的保护范围无任何限制。
[0033]
本发明采用固定床反应器进行催化剂活性评价,反应器直径250mm,长度150mm,上下两端带有四氟管板,形式见附图2。
[0034]
采用gb重铬酸钾法测定废水cod,哈希公司仪器,dr6000型号,参考标准为gb11914-89。
[0035]
采用碘量测试过氧化氢含量,梅特勒公司仪器,905titrando型号,参考标准为gb/t32102-2015。
[0036]
采用oes-icp测定活性组分的流失,岛津公司仪器,2030series型号,参考标准为gb11911-1989。
[0037]
采用雷磁phs-3c精密ph计测定水样ph值,参考标准为gb6920。
[0038]
主要原料信息如下:
[0039]
试剂名称厂家规格或纯度α-al
2
o
3
苏州优锆99.99%r-tio
2
泉汇化工99%sic粉福斯曼科技99%硝酸锶阿拉丁99.5%硝酸铜,三水阿拉丁99.99%硝酸镧,六水阿拉丁99.99%硝酸镓,八水阿拉丁99.9%硝酸锰(50%)阿拉丁50wt.%硝酸镍,六水阿拉丁98%
[0040]
实施例1
[0041]
将200gα-al
2
o
3
和800g的r-tio
2
混合均匀后经成型机压合得到外径40mm、壁厚2mm、高度100mm的中空圆柱形载体a,将19.1g硝酸锶和142g三水合硝酸铜,溶解在107g去离子水中,配制得到60%盐溶液,然后与9.0g的sic粉混合均匀,涂覆在载体a外侧上,经高温焙烧得到膜催化剂b,焙烧温度1400℃,焙烧时间5h。称取硝酸锶、六水合硝酸镧、八水合硝酸镓、硝酸锰(50%溶液)和六水合硝酸镍分别为21.3g、17.4g、24.1g、14.4g和17.5g,溶解在
58.4g去离子水中,涂覆在催化剂b内侧上,经高温焙烧得到催化剂c,焙烧温度400℃,焙烧时间6h。
[0042]
环氧丙烷共氧化反应产生的过氧化物废水在温度40℃,体积空速2h-1
的条件下,使用所述催化剂催化处理共氧化反应过氧化物废水,ph为6,水样过氧化物浓度2000mg/l(以h
2
o
2
计),水样cod浓度为20,000mg/l。经处理后,废水mn含量为25mg/l,出水cod为19,106mg/l,过氧化物浓度(以h
2
o
2
计)降低至100mg/l。
[0043]
实施例2
[0044]
将550gα-al
2
o
3
和450g的r-tio
2
混合均匀后经成型机压合得到外径55mm、壁厚3mm、高度100mm的中空圆柱形载体a,将21.4g硝酸锶和138.4g三水合硝酸铜,溶解在106.5g去离子水中,配制得到60%盐溶液,然后与9.0g的sic粉混合均匀,涂覆在载体a外侧上,经高温焙烧得到膜催化剂b,焙烧温度1050℃,焙烧时间5h。称取硝酸锶、六水合硝酸镧、八水合硝酸镓、硝酸锰(50%溶液)和六水合硝酸镍分别为19.9g、16.3g、22.6g、20.2g和10.9g,溶解在53.2g去离子水中,涂覆在催化剂b内侧上,经高温焙烧得到催化剂c,焙烧温度550℃,焙烧时间5h。
[0045]
环氧丙烷共氧化反应产生的过氧化物废水在温度50℃,体积空速1h-1
的条件下,使用所述催化剂催化处理共氧化反应过氧化物废水,ph为9.5,水样过氧化物浓度4000mg/l(以h
2
o
2
计),水样cod浓度为30,000mg/l。经处理后,废水mn含量为0.2mg/l,出水cod为28,136mg/l,过氧化物浓度(以h
2
o
2
计)降低至40mg/l。
[0046]
实施例3
[0047]
将500gα-al
2
o
3
和500g的r-tio
2
混合均匀后经成型机压合得到外径50mm、壁厚8mm、高度100mm的中空圆柱形载体a,将15.5g硝酸锶和160g三水合硝酸铜,溶解在117g去离子水中,配制得到60%盐溶液,然后与9.8g的sic粉混合均匀,涂覆在载体a外侧上,经高温焙烧得到膜催化剂b,焙烧温度1100℃,焙烧时间6h。称取硝酸锶、六水合硝酸镧、八水合硝酸镓、硝酸锰(50%溶液)和六水合硝酸镍分别为14.2g、11.6g、16.1g、13.2g和8.8g,溶解在38.2g去离子水中,涂覆在催化剂b内侧上,经高温焙烧得到催化剂c,焙烧温度800℃,焙烧时间4h。
[0048]
环氧丙烷共氧化反应产生的过氧化物废水在温度60℃,体积空速3h-1
的条件下,使用所述催化剂催化处理共氧化反应过氧化物废水,ph为8,水样过氧化物浓度3000mg/l(以h
2
o
2
计),水样cod浓度为28,000mg/l。经处理后,废水mn含量为1.2mg/l,出水cod为26,899mg/l,过氧化物浓度(以h
2
o
2
计)降低至660mg/l。
[0049]
实施例4
[0050]
将600gα-al
2
o
3
和400g的r-tio
2
混合均匀后经成型机压合得到外径80mm、壁厚5mm、高度100mm的中空圆柱形载体a,将20.6g硝酸锶和152.6g三水合硝酸铜,溶解在115.4g去离子水中,配制得到60%盐溶液,然后与9.7g的sic粉混合均匀,涂覆在载体a外侧上,经高温焙烧得到膜催化剂b,焙烧温度1000℃,焙烧时间3h。称取硝酸锶、六水合硝酸镧、八水合硝酸镓、硝酸锰(50%溶液)和六水合硝酸镍分别为21.4g、17.5g、24.2g、23.5g和10.27g,溶解在56.7g去离子水中,涂覆在催化剂b内侧上,经高温焙烧得到催化剂c,焙烧温度480℃,焙烧时间3h。
[0051]
环氧丙烷共氧化反应产生的过氧化物废水在温度70℃,体积空速2.5h-1
的条件下,
使用所述催化剂催化处理共氧化反应过氧化物废水,ph为9.5,水样过氧化物浓度4000mg/l(以h
2
o
2
计),水样cod浓度为27,000mg/l。经处理后,废水mn含量为1.8mg/l,出水cod为25,475mg/l,过氧化物浓度(以h
2
o
2
计)降低至760mg/l。
[0052]
实施例5
[0053]
将800gα-al
2
o
3
和200g的r-tio
2
混合均匀后经成型机压合得到外径200mm、壁厚10mm、高度100mm的中空圆柱形载体a,将36.4g硝酸锶和207.8g三水合硝酸铜,溶解在115.4g去离子水中,配制得到60%盐溶液,然后与13.8g的sic粉混合均匀,涂覆在载体a外侧上,经高温焙烧得到膜催化剂b,焙烧温度1500℃,焙烧时间8h。称取硝酸锶、六水合硝酸镧、八水合硝酸镓、硝酸锰(50%溶液)和六水合硝酸镍分别为7.1g、5.8g、8.07g、8.4g和2.93g,溶解在18.8g去离子水中,涂覆在催化剂b内侧上,经高温焙烧得到催化剂c,焙烧温度450℃,焙烧时间5h。
[0054]
环氧丙烷共氧化反应产生的过氧化物废水在温度20℃,体积空速3h-1
的条件下,使用所述催化剂催化处理共氧化反应过氧化物废水,ph为6,水样过氧化物浓度2500mg/l(以h
2
o
2
计),水样cod浓度为25,000mg/l。经处理后,废水mn含量为20mg/l,出水cod为23,929mg/l,过氧化物浓度(以h
2
o
2
计)降低至225mg/l。
[0055]
实施例6
[0056]
将700gα-al
2
o
3
和300g的r-tio
2
混合均匀后经成型机压合得到外径20mm、壁厚1mm、高度100mm的中空圆柱形载体a,将21.7g硝酸锶和98.9g三水合硝酸铜,溶解在80.4g去离子水中,配制得到60%盐溶液,然后与6.8g的sic粉混合均匀,涂覆在载体a外侧上,经高温焙烧得到膜催化剂b,焙烧温度800℃,焙烧时间4h。称取硝酸锶、六水合硝酸镧、八水合硝酸镓、硝酸锰(50%溶液)和六水合硝酸镍分别为28.4g、23.2g、32.2g、19.2g和23.4g,溶解在77.8g去离子水中,涂覆在催化剂b内侧上,经高温焙烧得到催化剂c,焙烧温度700℃,焙烧时间6h。
[0057]
环氧丙烷共氧化反应产生的过氧化物废水在温度80℃,体积空速2h-1
的条件下,使用所述催化剂催化处理共氧化反应过氧化物废水,ph为8,水样过氧化物浓度3500mg/l(以h
2
o
2
计),水样cod浓度为24,000mg/l。经处理后,废水mn含量为1mg/l,出水cod为22,386mg/l,过氧化物浓度(以h
2
o
2
计)降低至70mg/l。
[0058]
实施例7
[0059]
将300gα-al
2
o
3
和700g的r-tio
2
混合均匀后经成型机压合得到外径20mm、壁厚6mm、高度100mm的中空圆柱形载体a,将24.7g硝酸锶和159.6g三水合硝酸铜,溶解在99.1g去离子水中,配制得到60%盐溶液,然后与10.4g的sic粉混合均匀,涂覆在载体a外侧上,经高温焙烧得到膜催化剂b,焙烧温度800℃,焙烧时间4h。称取硝酸锶、六水合硝酸镧、八水合硝酸镓、硝酸锰(50%溶液)和六水合硝酸镍分别为35.5g、29.0g、40.3g、30.0g和24.4g,溶解在96.2g去离子水中,涂覆在催化剂b内侧上,经高温焙烧得到催化剂c,焙烧温度750℃,焙烧时间8h。
[0060]
环氧丙烷共氧化反应产生的过氧化物废水在温度70℃,体积空速1h-1
的条件下,使用所述催化剂催化处理共氧化反应过氧化物废水,ph为11,水样过氧化物浓度4000mg/l(以h
2
o
2
计),水样cod浓度为26,000mg/l。经处理后,废水mn含量为0.5mg/l,出水cod为24,494mg/l,过氧化物浓度(以h
2
o
2
计)降低至800mg/l。
[0061]
对比例1
[0062]
与实施例2比较,区别在于本对比例仅含有活性组分膜sr
1.0
la
0.4
ga
0.6
mn
x
ni
1-x
o
3.5
。
[0063]
将550gα-al
2
o
3
和450g的r-tio
2
混合均匀后经成型机压合得到外径55mm、壁厚3mm、高度100mm的中空圆柱形载体a,焙烧温度1050℃,焙烧时间5h。称取硝酸锶、六水合硝酸镧、八水合硝酸镓、硝酸锰(50%溶液)和六水合硝酸镍分别为19.9g、16.3g、22.6g、20.2g和10.9g,溶解在53.2g去离子水中,涂覆在催化剂b内侧上,经高温焙烧得到催化剂c,焙烧温度550℃,焙烧时间5h。
[0064]
环氧丙烷共氧化反应产生的过氧化物废水在温度50℃,体积空速1h-1
的条件下,使用所述催化剂催化处理共氧化反应过氧化物废水,ph为9.5,水样过氧化物浓度4000mg/l(以h
2
o
2
计),水样cod浓度为30,000mg/l。经处理后,废水mn含量为1mg/l,出水cod为24,435mg/l,过氧化物浓度(以h
2
o
2
计)降低至800mg/l。
[0065]
对比例2
[0066]
与实施例7比较,区别在于不含活性组分。
[0067]
将300gα-al
2
o
3
和700g的r-tio
2
混合均匀后经成型机压合得到外径20mm、壁厚6mm、高度100mm的中空圆柱形载体a,经高温煅烧得到膜催化剂b,焙烧温度1100℃,焙烧时间3h。
[0068]
环氧丙烷共氧化反应产生的过氧化物废水在温度70℃,体积空速1h-1
的条件下,使用所述催化剂催化处理共氧化反应过氧化物废水,ph为11,水样过氧化物浓度4000mg/l(以h
2
o
2
计),水样cod浓度为26,000mg/l。经处理后,出水cod为25,765mg/l,过氧化物浓度(以h
2
o
2
计)降低至2000mg/l。
[0069]
对比例3
[0070]
与实施例2比较,采用专利cn 106140186a的实施例1的复合金属氧化物催化剂,环氧丙烷共氧化反应产生的过氧化物废水在温度50℃,体积空速1h-1
的条件下,使用所述催化剂催化处理共氧化反应过氧化物废水,ph为9.5,水样过氧化物浓度4000mg/l(以h
2
o
2
计),水样cod浓度为30,000mg/l。经处理后,出水cod为28,306mg/l,过氧化物浓度(以h
2
o
2
计)降低至400mg/l。
[0071]
通过上述实施例和对比例的比较可知,采用本发明方法经两次催化不同的反应可将环氧丙烷共氧化反应产生的废水中的过氧化物分解得到co
2
,避免过氧化物分解成氧气所带来的本质安全问题,在优选的条件下,共氧化反应产生的过氧化氢的含量低于40mg/l,分解效率高达99%。所述催化剂采用非贵金属活性组分,成本低且不会造成二次污染,在优选的条件下,mn流失仅0.2mg/l。所述催化剂可在ph=6-11的宽ph范围内处理任何含有过氧化物的有机废水,处理条件温和,对设备要求低。
[0072]
本领域技术人员可以理解,在本说明书的教导之下,可对本发明做出一些修改或调整。这些修改或调整也应当在本发明权利要求所限定的范围之内。