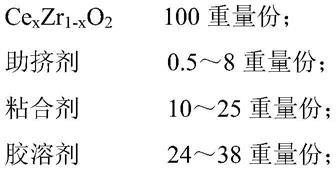
1.本发明涉及一种催化剂载体和催化剂及其制备方法和应用,尤其涉及该催化剂在去除甲烷氧化偶联制乙烯的尾气中含有的一氧化碳和氢气的应用。
背景技术:2.甲烷氧化偶联(ocm)技术,是以甲烷为原料,在催化剂和高温(>600℃)作用下,直接氧化脱氢制乙烯的工艺。甲烷氧化偶联制乙烯技术在石油化工领域中具有潜在的应用价值。在该技术方法中,各原料物料单次通过催化剂床层后,约50wt%的甲烷会转化成主产物乙烯、乙烷以及副产物氢气、一氧化碳和二氧化碳等。反应器输出的物料经去除二氧化碳和分离乙烯、乙烷后,主要的副产物是一氧化碳、氢气和未反应的甲烷。本领域的关注点主要在于如何提高原料甲烷的利用效率。
3.cn109456139a公开了一种甲烷制乙烯反应产物的油吸收分离方法,其将ocm反应产物进行急冷冷却、压缩升压、脱除杂质、气液分离工序处理,采用膜分离技术将不凝气中的甲烷分离出来并返回到ocm反应器中进行循环使用,工序复杂且操作成本较高。
4.cn111004081a公开了一种甲烷氧化偶联制乙烯反应气体的分离方法及装置。该分离方法包括以下步骤:(1)压缩:利用压缩机对反应气体升压;(2)净化:对步骤(1)升压后的反应气体进行脱酸、干燥处理;(3)冷却:经步骤(2)得到的净化气体冷却至-40℃至-10℃;(4)吸收:吸收剂从吸收塔顶部进入,吸收反应气体中的碳二馏分及以上组分,吸收塔塔釜物流送至解吸塔,塔顶气体送往冷量回收系统;(5)解吸:来自吸收塔塔釜的物流进入解吸塔,解吸塔塔釜得到的贫溶剂经过冷却降温后,返回吸收塔顶部,塔顶得到的气体送往脱乙烷塔;(6)脱乙烷:来自解吸塔塔顶的气体进入脱乙烷塔,塔顶得到富含乙烯乙烷的碳二组分,塔釜得到富含丙烯丙烷的碳三组分;(7)乙烯精馏:来自脱乙烷塔塔顶的气体先送往碳二加氢反应器脱除炔烃,然后送往乙烯精馏塔,乙烯精馏塔侧线采出乙烯产品,塔顶气体返回压缩机段间,塔釜物流送往裂解炉;(8)丙烯精馏:来自脱乙烷塔塔釜的物料先送往碳三加氢反应器脱除炔烃、二烯烃,然后送往丙烯精馏塔,丙烯精馏塔侧线采出丙烯产品,塔顶气体返回压缩机段间,塔釜物流送往裂解炉;(9)裂解:将步骤(7)和步骤(8)的塔釜物流送至裂解炉,得到的裂解气经废热锅炉回收热量后,进入油洗塔/水洗塔,然后送往压缩机一段吸入罐。
5.目前,针对ocm尾气的净化技术较少,通常采用选择性催化氧化技术来净化ocm尾气。即,ocm尾气在一定温度下通过催化剂床层后,一氧化碳和氢气被氧化,甲烷不消耗或消耗很少。甲烷净化后和新鲜甲烷一起进料,从而提高甲烷的利用效率。但是工业多相催化剂必须具备必要的机械强度。催化剂成型过程是工业催化剂制备工序的重要步骤之一。迄今为止,适用于ocm尾气净化处理的催化剂载体,其成型方式并未见报道。
技术实现要素:6.针对现有技术存在的上述问题,本发明提供了一种催化剂载体和催化剂,及其制
备方法和应用。本发明提供的催化剂载体具有比较大的机械强度,当其负载活性组分后所得到的催化剂也具有较高的机械强度,且能够较好的去除ocm尾气中的一氧化碳和氢气,对甲烷的转化率较低。
7.本发明第一方面提供了一种催化剂载体,所述催化剂载体的制备原料包括:
[0008][0009]
所述胶溶剂的质量浓度为2.9%~8%。
[0010]
根据本发明所述的催化剂载体的优选实施方式,其制备原料包括:
[0011][0012]
所述胶溶剂的质量浓度为2.9%~8%。
[0013]
根据本发明所述的催化剂载体的一些实施方式,所述催化剂载体的平均机械强度>40n/粒。在本发明中,催化剂的机械强度的测试方法可以为:采用颗粒强度仪对50个长度为3mm、直径为2mm的催化剂载体的机械强度进行测试,计算得到平均机械强度。
[0014]
根据本发明所述的催化剂载体的一些实施方式,所述ce
x
zr
1-x
o2由水溶性铈盐和水溶性锆盐通过共沉淀法或溶胶-凝胶法或水热法制备得到。
[0015]
根据本发明所述的催化剂载体的优选实施方式,所述水溶性铈盐选自硝酸铈、硝酸铈铵、硫酸铈和氯化铈中的至少一种。
[0016]
根据本发明所述的催化剂载体的优选实施方式,所述水溶性锆盐选自氧氯化锆、氯化锆、硫酸锆和硝酸锆中的至少一种。
[0017]
根据本发明所述的催化剂载体的优选实施方式,ce
x
zr
1-x
o2中x=0.1~0.7。例如0.1、0.3、0.4、0.5、0.7,以及它们之间的任意值。
[0018]
根据本发明所述的催化剂载体的优选实施方式,ce
x
zr
1-x
o2中x=0.1~0.5。
[0019]
根据本发明所述的催化剂载体的一些实施方式,所述助挤剂选自滑石粉、石墨、硬脂酸、硬脂酸盐、淀粉和田菁粉中的至少一种。
[0020]
根据本发明所述的催化剂载体的具体实施方式,所述助挤剂为田菁粉。
[0021]
根据本发明所述的催化剂载体的一些实施方式,所述粘合剂选自水玻璃、硅溶胶和铝溶胶中的至少一种。
[0022]
根据本发明所述的催化剂载体的优选实施方式,所述粘合剂为铝溶胶。
[0023]
根据本发明所述的催化剂载体的具体实施方式,所述粘合剂为拟薄水铝石。
[0024]
根据本发明所述的催化剂载体的一些实施方式,所述胶溶剂选自盐酸、硝酸、甲酸、乙酸、柠檬酸、丙二酸和三氯乙酸中的至少一种。
[0025]
根据本发明所述的催化剂载体的具体实施方式,所述胶溶剂为硝酸。
[0026]
根据本发明所述的催化剂载体的优选实施方式,所述胶溶剂的质量浓度为2.9%~8%。例如2.9%、4.5%、5.1%、6.2%、7.7%、8%,以及它们之间的任意值。
[0027]
在本发明的不同实施方式中,可根据不同的需要制备不同规格的催化剂载体。例如本发明的催化剂载体的直径可以为2mm,长度可以为3mm,采用颗粒强度仪测试该催化剂载体的机械强度,可以达到40n/粒以上。本发明的催化剂载体具有足够的机械强度,在后续的尾气催化转化过程中有足够的稳定性,并且可以重复使用。
[0028]
本发明第二方面提供了一种催化剂载体的制备方法,包括步骤:
[0029]
步骤a、将ce
x
zr
1-x
o2、助挤剂、粘合剂和胶溶剂,以及任选的水进行捏合,得到混合料;
[0030]
步骤b、将所述混合料挤出成型,得到湿成型体;
[0031]
步骤c、所述湿成型体干燥后进行焙烧,得到所述催化剂载体。
[0032]
根据本发明所述的制备方法的一些实施方式,所述焙烧条件为:温度为200~1000℃,时间为2~10h。
[0033]
根据本发明所述的制备方法的优选实施方式,所述焙烧条件为:温度为400~700℃,时间为4~8h。
[0034]
根据本发明所述的制备方法的具体实施方式,所述焙烧条件为:温度为600℃,时间为5h。
[0035]
根据本发明所述的制备方法的一些实施方式,ce
x
zr
1-x
o2、助挤剂、粘合剂、胶溶剂的重量配比为100:0.5~8:10~25:24~38。
[0036]
根据本发明所述的制备方法的优选实施方式,ce
x
zr
1-x
o2、助挤剂、粘合剂、胶溶剂的重量配比为100:2~6:12~20:26~34。
[0037]
根据本发明所述的制备方法的一些实施方式,ce
x
zr
1-x
o2中,x=0.1~0.7。例如0.1、0.3、0.4、0.5、0.7,以及它们之间的任意值。
[0038]
根据本发明所述的制备方法的优选实施方式,ce
x
zr
1-x
o2中,x=0.1~0.5。
[0039]
根据本发明所述的制备方法的一些实施方式,所述ce
x
zr
1-x
o2由水溶性铈盐和水溶性锆盐通过共沉淀法或溶胶-凝胶法或水热法制备得到。
[0040]
根据本发明所述的制备方法的优选实施方式,所述水溶性铈盐选自硝酸铈、硝酸铈铵、硫酸铈和氯化铈中的至少一种。
[0041]
根据本发明所述的制备方法的优选实施方式,所述水溶性锆盐选自氧氯化锆、氯化锆、硫酸锆和硝酸锆中的至少一种。
[0042]
根据本发明所述的制备方法的一些实施方式,捏合过程中所加入的水的量为一个较宽的范围,可根据实际需要调整所加入的水的量。
[0043]
根据本发明所述的制备方法的一些实施方式,所述助挤剂选自滑石粉、石墨、硬脂酸、硬脂酸盐、淀粉和田菁粉中的至少一种。
[0044]
根据本发明所述的制备方法的具体实施方式,所述助挤剂为田菁粉。
[0045]
根据本发明所述的制备方法的一些实施方式,所述粘合剂选自水玻璃、硅溶胶和铝溶胶中的至少一种。
[0046]
根据本发明所述的制备方法的优选实施方式,所述粘合剂为铝溶胶。
[0047]
根据本发明所述的制备方法的具体实施方式,所述粘合剂为拟薄水铝石。
[0048]
根据本发明所述的制备方法的一些实施方式,所述胶溶剂选自盐酸、硝酸、甲酸、乙酸、柠檬酸、丙二酸和三氯乙酸中的至少一种。
[0049]
根据本发明所述的制备方法的具体实施方式,所述胶溶剂为硝酸。
[0050]
根据本发明所述的制备方法的一些实施方式,所述胶溶剂的质量浓度为2.9%~8%。例如2.9%、4.5%、5.1%、6.2%、7.7%、8%,以及它们之间的任意值。
[0051]
本发明第三方面提供了一种根据上述制备方法得到的催化剂载体。
[0052]
根据本发明所述的催化剂载体的一些实施方式,所述催化剂载体的平均机械强度>40n/粒。
[0053]
本发明第四方面提供了一种催化剂,所述催化剂包括上述的催化剂载体和活性组分。
[0054]
根据本发明所述的催化剂的优选实施方式,所述活性组分选自vb族金属氧化物、vib族金属氧化物、viib族金属氧化物、viii族金属氧化物和ib族金属氧化物中的至少一种。
[0055]
根据本发明所述的催化剂的优选实施方式,所述活性组分选自氧化铁、氧化铜、氧化锰、氧化钴、氧化镍和氧化铬中的至少一种。
[0056]
根据本发明所述的催化剂的优选实施方式,所述活性组分选自氧化铁、氧化锰和氧化铜中的至少一种。
[0057]
根据本发明所述的催化剂的具体实施方式,所述活性组分为氧化铜。
[0058]
在本发明的不同实施方式中,可根据不同的需要制备不同规格的催化剂。例如本发明的催化剂直径可以为2mm,长度可以为3mm。催化剂载体负载活性组分制备催化剂的过程,对其机械强度影响较小,用颗粒强度仪测试该催化剂的机械强度>40n/粒。
[0059]
本发明提供的催化剂具有较高的机械强度,且在负载活性组分后,能够较好的去除甲烷氧化偶联反应尾气中的一氧化碳和氢气。当反应尾气单次通过催化剂床层时,一氧化碳的转化率>90%,氢气的转化率>90%,甲烷的转化率<2%。进而能够使得未反应的甲烷作为原料再循环送至反应釜中继续进行反应。
[0060]
本发明第五方面提供了一种催化剂的制备方法,所述制备方法为:在上述的催化剂载体上负载含有活性元素的化合物并进行干燥和焙烧。
[0061]
根据本发明所述的制备方法的一些实施方式,所述活性元素选自vb族金属、vib族金属、viib族金属、viii族金属和ib族金属中的至少一种。
[0062]
根据本发明所述的制备方法的优选实施方式,所述活性元素选自铁、铜、锰、钴、镍和铬中的至少一种。
[0063]
根据本发明所述的制备方法的优选实施方式,所述含有活性元素的化合物选自硝酸铜、氯化铜、醋酸铜和硫酸铜中的至少一种。
[0064]
根据本发明所述的制备方法的具体实施方式,所述含有活性元素的化合物为氧化铜。
[0065]
根据本发明所述的制备方法的优选实施方式,所述焙烧条件为:温度为200~1000℃,时间为2~10h。
[0066]
根据本发明所述的制备方法的优选实施方式,所述焙烧条件为:温度为400~700℃,时间为4~8h。
[0067]
根据本发明所述的制备方法的具体实施方式,所述焙烧条件为:温度为600℃,时间为5h。
[0068]
本发明第六方面提供了一种甲烷氧化偶联反应尾气的净化处理方法,包括:将尾气通过上述的催化剂或由上述的制备方法得到的催化剂。
[0069]
根据本发明所述的净化处理方法的一些实施方式,所述甲烷氧化偶联反应尾气的组成为:甲烷、一氧化碳、氢气的体积比为12~18:2~5:1。
[0070]
根据本发明所述的净化处理方法的优选实施方式,所述甲烷氧化偶联反应尾气的组成为:甲烷、一氧化碳、氢气的体积比为15~17:2~4:1。
[0071]
根据本发明所述的净化处理方法的一些实施方式,所述净化处理方法的条件包括:空速为10~200l/h
·
g催化剂,温度为200~700℃。在本发明中,“l/h
·
g催化剂”是指“l/(h
·
g催化剂)”。
[0072]
根据本发明所述的净化处理方法的优选实施方式,所述净化处理方法的条件包括:空速为13~150l/h
·
g催化剂,温度为350~600℃。
[0073]
根据本发明所述的净化处理方法的优选实施方式,所述尾气中一氧化碳的转化率>90%,氢气的转化率>90%,甲烷的转化率<2%。
[0074]
上述的催化剂对甲烷氧化偶联反应尾气中各物质的转化率是在尾气单次通过催化剂床层后的数据,在本发明的不同实施方式中,根据不同的净化需求可选择将尾气多次通过催化剂床层。
[0075]
本发明第七方面提供了一种上述催化剂载体及制备方法、催化剂及制备方法在甲烷氧化偶联反应尾气处理中的应用,更优选为在去除甲烷氧化偶联反应尾气中的一氧化碳和氢气中的应用。但并不限于此。
[0076]
根据上述应用的优选实施方式,所述尾气中一氧化碳的转化率>90%,氢气的转化率>90%,甲烷的转化率<2%。
[0077]
本发明的有益效果:
[0078]
本发明制备的催化剂载体具有足够的机械强度,在其上负载活性组分后所得到的催化剂也具有较高的机械强度,且该催化剂能够去除甲烷氧化偶联反应尾气中一氧化碳和氢气,去除率可达到90%以上,并且对甲烷的转化率很小,进而能够将其中未反应完全的甲烷输送至反应釜中继续进行反应。
具体实施方式
[0079]
为使本发明更加容易理解,下面将结合实施例来详细说明本发明,这些实施例仅起说明性作用,并不局限于本发明的应用范围。
[0080]
本发明的测试方法以及测试中所用设备如下:
[0081]
(1)一氧化碳、甲烷和氢气的转化率测试采用气相色谱法。
[0082]
(2)挤条机为购自华南理工大学科技实业总厂制造公司、生产型号为f-26型的双螺杆挤条机。
[0083]
(3)颗粒强度仪为购自江苏姜堰市分析仪器厂制造公司、型号为kc-2a的数显颗粒强度仪。
[0084]
本发明中所用到的各种原料试剂均可通过市售途径获得。
[0085]
【实施例1】
[0086]
称取50g由共沉淀法制备得到的ce
0.1
zr
0.9
o2,向其中加入3.05g田菁粉、5.99g拟薄水铝石和14.99g浓度为5.1wt%的硝酸,然后在挤条机中捏合20min,并通过φ=2mm的孔板挤出成型,得到长条状湿成型体。湿成型体在空气中干燥后,以5℃/min的速率升温至600℃并保持5h进行焙烧,得到催化剂载体。
[0087]
称取1.49g三水合硝酸铜,溶于30ml水中,向其中加入5.12g长度为3mm的催化剂载体,然后在旋转蒸发仪上于常温常压条件下旋转5h,旋蒸至干,在80℃下干燥,再以5℃/min的速率升温至600℃,保持5h进行焙烧,得到催化剂。
[0088]
利用颗粒强度仪测试催化剂的强度。对50个长度为3mm、直径为2mm的催化剂机械强度进行了测试,计算得到的平均机械强度为40.7n/粒。
[0089]
在内径为8mm的石英玻璃管反应器中,装入0.21g催化剂。并且,催化剂上下均填充20~40目的石英砂。通入流速为40ml/min的氮气和4ml/min的氧气,以10℃/min的速率升温至600℃并保持30min,对催化剂进行活化。
[0090]
将氮气和氧气切换成副产物反应气进行催化转化。其中,副产物反应气中包含co 15vol%、h
2 5vol%,余量为甲烷。催化转化反应进行60min后,通过气相色谱法测定co转化率、ch4转化率和h2转化率,测试结果见表1。
[0091]
【实施例2】
[0092]
称取50g由溶胶-凝胶法制备得到的ce
0.3
zr
0.7
o2,向其中加入2.98g田菁粉、8.02g拟薄水铝石和15.16g浓度为5.1wt%的硝酸,然后在挤条机中捏合20min,并通过φ=2mm的孔板挤出成型,得到长条状湿成型体。湿成型体在空气中干燥后,以5℃/min的速率升温至600℃并保持5h进行焙烧,得到催化剂载体。
[0093]
称取1.49g三水合硝酸铜,溶于30ml水中,向其中加入5.06g长度为3mm的催化剂载体,然后在旋转蒸发仪上于常温常压条件下旋转5h,旋蒸至干,在80℃下干燥,再以5℃/min的速率升温至600℃,保持5h进行焙烧,得到催化剂。
[0094]
利用颗粒强度仪测试催化剂的强度。对50个长度为3mm、直径为2mm的催化剂机械强度进行了测试,计算得到的平均机械强度为47.3n/粒。
[0095]
在内径为8mm的石英玻璃管反应器中,装入0.2g催化剂。并且,催化剂上下均填充20~40目的石英砂。通入流速为40ml/min的氮气和4ml/min的氧气,以10℃/min的速率升温至600℃并保持30min,对催化剂进行活化。
[0096]
将氮气和氧气切换成副产物反应气进行催化转化。其中,副产物反应气中包含co 15vol%、h
2 5vol%,余量为甲烷。催化转化反应进行60min后,通过气相色谱法测定co转化率、ch4转化率和h2转化率,测试结果见表1。
[0097]
【实施例3】
[0098]
称取50g由水热法制备得到的ce
0.5
zr
0.5
o2,向其中加入3.01g田菁粉、10.01g拟薄水铝石和15.07g浓度为5.1wt%的硝酸,然后在挤条机中捏合20min,并通过φ=2mm的孔板挤出成型,得到长条状湿成型体。湿成型体在空气中干燥后,以5℃/min的速率升温至600℃并保持5h进行焙烧,得到催化剂载体。
[0099]
称取1.49g三水合硝酸铜,溶于30ml水中,向其中加入5.1g长度为3mm的催化剂载体,然后在旋转蒸发仪上于常温常压条件下旋转5h,旋蒸至干,在80℃下干燥,再以5℃/min
15vol%、h
2 5vol%,余量为甲烷。催化转化反应进行60min后,通过气相色谱法测定co转化率、ch4转化率和h2转化率,测试结果见表1。
[0115]
【对比例1】
[0116]
称取50g由共沉淀法制备得到的ce
0.1
zr
0.9
o2,向其中加入1.39g田菁粉、5.02g拟薄水铝石和17.01g浓度为2.5wt%的硝酸,然后在挤条机中捏合20min,并通过φ=2mm的孔板挤出成型,得到长条状湿成型体。湿成型体在空气中干燥后,以5℃/min的速率升温至600℃并保持5h进行焙烧,得到催化剂载体。
[0117]
称取1.49g三水合硝酸铜,溶于30ml水中,向其中加入5.12g长度为3mm的催化剂载体,然后在旋转蒸发仪上于常温常压条件下旋转5h,旋蒸至干,在80℃下干燥,再以5℃/min的速率升温至600℃,保持5h进行焙烧,得到催化剂。
[0118]
利用颗粒强度仪测试催化剂的强度。对50个长度为3mm、直径为2mm的催化剂机械强度进行了测试,计算得到的平均机械强度为32.6n/粒。
[0119]
在内径为8mm的石英玻璃管反应器中,装入0.21g催化剂。并且,催化剂上下均填充20~40目的石英砂。通入流速为40ml/min的氮气和4ml/min的氧气,以10℃/min的速率升温至600℃并保持30min,对催化剂进行活化。
[0120]
将氮气和氧气切换成副产物反应气进行催化转化。其中,副产物反应气中包含co 15vol%、h
2 5vol%,余量为甲烷。催化转化反应进行60min后,通过气相色谱法测定co转化率、ch4转化率和h2转化率,测试结果见表1。
[0121]
【对比例2】
[0122]
称取50g由共沉淀法制备得到的ce
0.1
zr
0.9
o2,向其中加入4.25g田菁粉、11.21g拟薄水铝石和14.91g浓度为9.7wt%的硝酸,然后在挤条机中捏合20min,并通过φ=2mm的孔板挤出成型,得到长条状湿成型体。湿成型体在空气中干燥后,以5℃/min的速率升温至600℃并保持5h进行焙烧,得到催化剂载体。
[0123]
称取1.49g三水合硝酸铜,溶于30ml水中,向其中加入5.12g长度为3mm的催化剂载体,然后在旋转蒸发仪上于常温常压条件下旋转5h,旋蒸至干,在80℃下干燥,再以5℃/min的速率升温至600℃,保持5h进行焙烧,得到催化剂。
[0124]
利用颗粒强度仪测试催化剂的强度。对50个长度为3mm、直径为2mm的催化剂机械强度进行了测试,计算得到的平均机械强度为57.2n/粒。
[0125]
在内径为8mm的石英玻璃管反应器中,装入0.21g催化剂。并且,催化剂上下均填充20~40目的石英砂。通入流速为40ml/min的氮气和4ml/min的氧气,以10℃/min的速率升温至600℃并保持30min,对催化剂进行活化。
[0126]
将氮气和氧气切换成副产物反应气进行催化转化。其中,副产物反应气中包含co 15vol%、h
2 5vol%,余量为甲烷。催化转化反应进行60min后,通过气相色谱法测定co转化率、ch4转化率和h2转化率,测试结果见表1。
[0127]
表1催化剂性能测试结果
[0128][0129]
通过实施例和对比例能够看出,本发明制备得到的催化剂具有较高的机械强度,同时对于甲烷氧化偶联尾气中的一氧化碳和氢气均具有较高的转化率,且对其中甲烷的转化率又很低,使得尾气中未反应完全的甲烷能够作为原料气继续进行反应。
[0130]
以上所述的仅是本发明的优选实例。应当指出对于本领域的普通技术人员来说,在本发明所提供的技术启示下,作为本领域的公知常识,还可以做出其它等同变型和改进,也应视为本发明的保护范围。