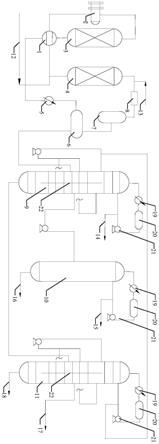
[0001]
本发明属于石油化工技术领域,本文涉及一种粗己烷的精细加工方法。
背景技术:[0002]
原油的重质化、劣质化导致石油产品工艺也在不断变化,现阶段粗己烷中己烷含量降低,c5组分及c7、c8等组分含量增加,原有的加工工艺已不能满足生产需求。同时,原有的加工装置负荷增加,加工成本增加。为生产出高质量的己烷产品,同时增加副产品的利用率,提高经济效益,很多厂家对粗己烷的加工工艺进行改进、优化调整。
技术实现要素:[0003]
本发明针对现有技术的上述不足,提供一种能获得高质量己烷产品,同时增加副产品利用率、提高经济效益的粗己烷的精细加工方法。
[0004]
为了解决上述技术问题,本申请采用的技术方案如下:一种粗己烷的精细加工方法,其包括以下步骤:
[0005]
(1)首先将原料粗己烷与氢气充分混合后与反应产物换热,再经换热器加热至130~190℃,进入到载有催化剂的加氢反应器内,在加氢精制催化剂的作用下,进行加氢精制反应,脱除原料中的芳烃和不饱和烃;
[0006]
(2)反应后产物经过低压分离器进行气液分离,然后进入到分馏系统进行精细切割;反应产物首先进入到分馏系统的第一隔板塔中进行分离,塔顶出石油醚ⅰ产品;侧线出混合碳六,然后混合碳六进入到脱正己烷塔中进行进一步切割,得到石油醚ⅱ(异己烷)和正己烷产品;第一隔板塔的塔底产品至第二隔板塔进行分离,得到石油醚ⅲ和w1-30产品。
[0007]
本发明所述的粗己烷:初馏点为20~60℃,终馏点为100~210℃,20℃时的密度为600~780kg/m3,庚烷含量12~50%。
[0008]
本发明所述的加氢精制的工艺条件为:反应温度为100~240℃、反应压力为1.3~6.0mpa、体积空速为0.5~5.0h-1
、氢油体积比为200~1500:1。
[0009]
本发明所述的进行加氢精制反应的催化剂为镍系催化剂,外观为球形,催化剂比表面积为50~120m2/g,孔容为0.15~0.5ml/g,堆比重:0.6
±
0.02g/ml,径向耐压强度15~60n/粒。催化剂对粗己烷的加氢饱和及脱芳效果好。
[0010]
本发明所述的一种粗己烷的精细加工方法是将原料与氢气混合后经反应进料/产物换热器进行换热后,经加热器加热至反应温度,在催化剂作用下进行加氢精制反应,脱除原料中的不饱和烃和芳烃等杂质。
[0011]
本发明所述的分馏系统中包含两个隔板塔即第一隔板塔和第二隔板塔,一个板式塔即脱正己烷塔。
[0012]
本发明所述的隔板塔,一塔可实现两塔功能,在提高热力学效率的同时降低装置的能耗,分馏精度大幅度提高。
[0013]
本发明所述的一种粗己烷的精细加工方法是反应产物经过气液分离后进入到第
一隔板塔中进分馏,得到轻组分、混合碳六和重组分,轻组分作为石油醚ⅰ产品出装置;混合碳六在脱正己烷塔中分离得到高含量的石油醚ⅱ(异己烷)和正己烷产品;重组分进入到第二隔板塔中进行切割得到石油醚ⅲ和w1-30产品,第二隔板塔塔顶的产品重新进入到分馏系统进行切割。
[0014]
本发明所述的一种粗己烷的精细加工方法,反应产物通过分馏系统的精细切割可以得到五种不同牌号的产品。
[0015]
由于采用如上所述的技术方案,本发明具有如下优越性:
[0016]
1、本发明一种粗己烷的精细加工方法,催化剂为镍系催化剂,其低温活性、稳定性及再生性能良好,反应条件温和,脱不饱和烃和脱芳效果好,可以满足长周期运转的要求。
[0017]
2、本发明一种粗己烷的精细加工方法,原料不经加热炉加热,同氢气混合后,与反应产物进行换热后经进料加热器加热至反应温度,能耗低且换热效率高。
[0018]
3、本发明一种粗己烷的精细加工方法,是针对这种初馏点为20~60℃,终馏点为100~210℃,20℃时的密度为600~780kg/m3的粗己烷进行的加工。加工过程首次在分馏系统引入了两个隔板塔,隔板塔将多塔系统进行内部能量集成,在塔的中间设置一隔板,隔板的设置可使单塔实现两塔的功能,消除了中间组分的返混,降低进料段附近的混合效应,提高热力学效率,降低了过程所需的能耗,采用隔板塔技术,节省一个精馏塔及附属设备,降低了设备投资和占地面积;采用本申请这种设置了两个隔板塔即第一隔板塔和第二隔板塔,以及一个板式塔即脱正己烷塔的工艺,可以实现分离五种产品,且分离精度高的技术效果。
[0019]
4、本发明的方法生产灵活,可根据市场需求选用不同的生产方案,得到的石油醚ⅱ(异己烷)≥95%,生产含量为60%、70%、80%、95%正己烷产品。
[0020]
5、本发明所述的一种粗己烷的精细加工方法,其选用隔板塔精馏技术和ctst立体传质塔板系列,形成隔板塔技术,得到合格产品。
附图说明
[0021]
图1实施例采用的粗己烷的精细加工的设备图。
[0022]
图中:1—换热器;2—加热器;3—加氢反应器;4—循环氢脱硫反应器;5—反应产物冷却器,6—低压分离器;7—循环氢分液罐;8—循环氢压缩机;9—第一隔板塔;10—脱正己烷塔;11—第二隔板塔;12—原料进口(进料管道);13—新氢进气口(进料管道);14—石油醚ⅰ出装置管线;15—石油醚ⅱ(异己烷)出装置管线;16—正己烷出装置管线;17—石油醚ⅲ出装置管线;18—w1-30出装置管线,19—冷却器,20—回流罐,21—回流泵,22—隔板。
具体实施方式
[0023]
下面通过实施例进一步详细描述本申请,但是本申请不仅仅局限于以下实施例。
[0024]
实施例1
[0025]
一种粗己烷的精细加工方法,其包括以下步骤:
[0026]
步骤1、原料粗己烷同氢气混合后与反应产物换热后温度为73℃,经加热器加热至144℃进入到反应器内与催化剂接触,在加氢精制催化剂作用下进行加氢精制反应,催化剂ⅰ为ni系催化剂,外观为球形,催化剂比表面积为50~90m2/g,孔容为0.15~0.3ml/g,堆比
重:0.6
±
0.02g/ml,径向耐压强度24~38n/粒。
[0027]
步骤2、反应产物在低压分离器进行气液分离后进入到第一隔板塔中进行分馏,塔顶出石油醚ⅰ产品;侧线出混合碳六,混合碳六进入到脱正己烷塔中进行分离,脱正己烷塔塔顶出石油醚ⅱ(异己烷)产品,塔底出正己烷产品;第一隔板塔塔底出重组分油进入到第二隔板塔中,第二隔板塔中的塔顶产品回到第一隔板塔进行再次分馏,侧线出石油醚ⅲ产品,塔底出w1-30产品。
[0028]
原料性质见表1,产品性质见表2。
[0029]
表1原料粗己烷性质1
[0030][0031]
表2产品性质1
[0032][0033][0034]
从上述结果可知,本申请这种特定方法工艺和处理步骤制备的产品,分离精度高,产品中各个成分分离的比较彻底,而且收率也比较高。
[0035]
实施例2
[0036]
一种粗己烷的精细加工方法,其包括以下步骤:
[0037]
步骤1、原料粗己烷同氢气混合后与反应产物换热后温度为72℃,经加热器加热至147℃进入到反应器内与催化剂接触,在加氢精制催化剂作用下进行加氢精制反应,催化剂ⅰ为ni系催化剂,外观为球形,催化剂比表面积为60~85m2/g,孔容为0.18~0.35ml/g,堆比重:0.6
±
0.02g/ml,径向耐压强度32~40n/粒。
[0038]
步骤2、反应产物在低压分离器进行气液分离后进入到第一隔板塔中进行分馏,塔
顶出石油醚ⅰ产品;侧线出混合碳六,进入到脱正己烷塔中进行分离;塔底出重组分油,进入到第二隔板塔中进行分馏。脱正己烷塔塔顶出石油醚ⅱ(异己烷)产品,塔底出正己烷产品。第二隔板塔中塔顶产品回到第一隔板塔进行再次分馏,侧线出石油醚ⅲ产品,塔底出w1-30产品。
[0039]
原料性质见表3,产品性质见表4。
[0040]
表3原料粗己烷性质2
[0041][0042]
表4产品性质2
[0043][0044]
本申请上述两个实施例采用的设备图如附图1所示的粗己烷的精细加工装置:该装置包括换热器1,加热器2,加氢反应器3,循环氢脱硫反应器4,反应产物冷却器5,低压分离器6,循环氢分液罐7,循环氢压缩机8,第一隔板塔9,脱正己烷塔10和第二隔板塔11;
[0045]
所述换热器1的原料进口12通过管线与原料泵连接(原料泵设置于原料进料管道上,图中未示出,即为能够给介质提供输送动力的泵均可以满足本申请)、且原料进口管线进入的是原料与氢气的混合,换热器1的原料出口与加热器2的进料口通过管线连接,加热器2的出料口与加氢反应器3的进料口通过管线连接,加氢反应器3的出料口与换热器1的产物进料口通过管线连接,换热器1的产物出料口与反应产物冷却器5的进料口通过管线连接,反应产物冷却器5的出料口与低压分离器6的进料口通过管线连接;
[0046]
所述低压分离器6的出气口与循环氢分液罐7的进气口连接,循环氢分液罐7的出气口与循环氢压缩机8的进气口连接,新氢进气口13(与外部的氢源连通为系统提供新注入的氢气)与循环氢压缩机8的出气口管线连接,循环氢压缩机8的出气口与循环氢脱硫反应
器4入口连接,循环氢脱硫反应器4的出口与原料泵出口管线连接;
[0047]
所述的第一隔板塔9进料口与低压分离器6的出油口连接,第一隔板塔9的顶部与石油醚ⅰ出装置管线14连接,第一隔板塔的侧线抽出口与脱正己烷塔的10的进料口连接,第一隔板塔9的底出油口与第二隔板塔11的进料口连接;所述的脱正己烷塔10的塔顶与石油醚ⅱ(异己烷)出装置管线15连接,脱正己烷塔10的塔底与正己烷出装置管线16连接;所述的第二隔板塔11的塔顶与第一隔板塔9的进料口连接,第二隔板塔11的侧线抽出口与石油醚ⅲ出装置管线17连接,第二隔板塔的塔底与w1-30出装置管线18连接;所述的第一隔板塔和第二隔板塔均为行业中的具有隔板结构的隔板塔。
[0048]
本申请所述的第一隔板塔9、脱正己烷塔10、第二隔板塔11的塔顶均通过管道分别连接冷却器19和回流罐20,冷却器19通过管道与回流罐20相连,回流罐20通过管道与回流泵21相连;回流泵21的出口连接两条管道:一条管道与塔顶回流线连接,另一条管道与产品出装置管线连接。
[0049]
如附图1所示,本申请所述的第一隔板塔和第二隔板塔为隔板塔,具体的在上述两个塔内各设置一块竖向的隔板22,从而将上述的两个塔均分成主塔区和副塔区两个部分构成;第一隔板塔9和第二隔板塔11副塔区上设置了侧线抽出口、该侧线抽出口与主塔区设置的回流管线连接。