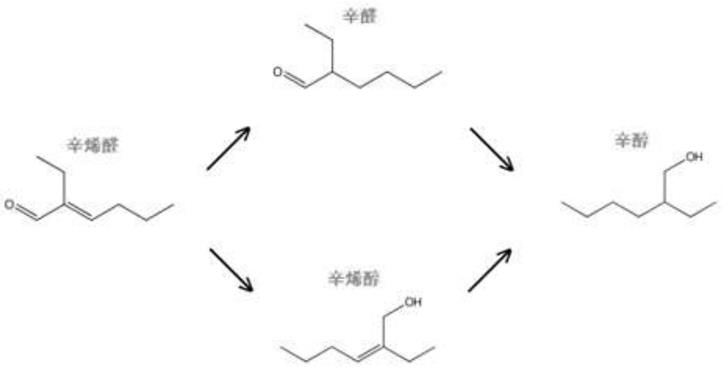
1.本发明涉及催化剂领域,更进一步说,涉及一种选择性制备辛醛或辛烯醇的催化剂及其制备方法和应用。
背景技术:2.辛醛和辛烯醇是辛烯醛加氢过程中的中间产物,由于辛烯醛是一种α、β不饱和醛,因此在不同催化剂的作用下,可选择性的生成辛醛或辛烯醇,由于两者自身含有c=c双键或c=o双键,因而可继续与氢气反应最终生成辛醇。反应历程如下:
[0003][0004]
辛醛和辛烯醇均为重要的化工产品,辛醛是一类重要的有机原料或香料,广泛存在于植物精油中,具有潜在的抑菌作用,该类化合物香气类型较多,具有令人愉快的甜橙香味,留香时间长,可增加香精的天然感,同时辛醛可作为饮料、冰激凌中柑橘类的香料,具有广泛应用的领域。但辛醛极易受氧化生成辛酸,使得香气遭到破坏,从而导致完全变质。
[0005]
辛醛的工业生产主要由辛烯醛加氢反应获得。辛烯醛是一种α,β-不饱和醛,分子中既含有c=c键又含有c=o键。c=c键的键能为615kj/mol,c=o键的键能为715kj/mol,因而在计算化学的数据对比下,通常认为c=c双键比c=o双键更容易加氢。辛烯醛与氢气经过一次加氢可选择性得到辛醛,如果未能精确控制反应条件,导致辛醛在反应过程中的停留时间过长,则辛醛会发生再次加氢生成辛醇。因此辛醛作为该反应的中间产物,需要催化剂具有极高的选择性。
[0006]
目前,研究多集中于辛烯醛加氢制备辛醇,对选择性制备辛醛的研究却鲜有报道。cn107930647a公开了一种制备辛醛的催化剂,该催化剂采用贵金属活性组分pd与ag、co、rh中的至少一种,负载于al2o3上,然而采用贵金属组分,会导致催化剂整体成本过高。同时在气相的条件下进行反应,首先要将辛烯醛加热至180~220℃使其全部气化而后通入氢气,因而采用气相法能耗过大。
[0007]
辛烯醇同样作为辛烯醛加氢制备辛醇过程中的中间产物,可用作重要的化学中间体从而生产下游产物,因此被广泛应用于制药工业、化妆品、食品加工以及化学工业等方面,尤其在制药工业中,由于辛烯醇已经被证实具有良好的致畸作用,因而在药物合成方面
备受关注。辛烯醇由于自身作为不饱和产物具有c=c双键,因此在进行反应过程中具有较高的活性。
[0008]
辛烯醇通常可由辛烯醛与氢气反应在催化剂的作用下,经过一次加氢选择性的生成,在反应过程中所生成的辛烯醇也可与氢气继续反应,最终生成辛醇。该反应可在气相或液相的条件下进行反应,在气相反应过程中,首先要将辛烯醛全部气化,使其与氢气进行充分接触,而后进行反应生成产物;而液相反应则不需要高能耗,同时反应条件更加温和。cn 103288597 a公开了一种制备辛醇的方法,在制备的过程中采用铑的络合物,将辛烯醛转化为辛烯醇。
[0009]
贵金属催化剂一般用于各种工业催化反应,尤其是被广泛用于石油、化工、医药等领域,其中包括au、ag、pt、pd、ru等金属等。但是,由于贵金属的资源稀少,并且受国际市场价格影响较大,更容易受到地缘政治风险事件的影响,从而大大限制了其广泛应用。同时贵金属催化剂虽然起活温度较非贵金属更低,活性更高,但是在较高的温度下贵金属更容易烧结或是由于升华导致其流失,从而导致催化剂失活。
[0010]
贵金属本身价格昂贵,例如贵金属中的pd,国际价格为480-490元/克,而非贵金属ni只有120000元/吨,如果采用相同单位(元/克)进行比较,两者的价格相差几千倍,因此许多学者正致力于研究如何降低贵金属催化剂的成本。同时贵金属的回收存在一系列的问题,主要有技术落后、环境污染、规模小等问题,因此贵金属作为一种稀缺资源,导致其自身价格高攀不下。非贵金属从价格方面较贵金属具有更加突出的优势。然而采用非贵金属催化辛烯醛选择性制备辛醛或辛烯醇的过程还鲜有报道。因此,开发一种成本低、转化率高、选择性好的催化剂尤为必要。
技术实现要素:[0011]
为了解决现有技术中存在的上述问题,本发明提出一种选择性制备辛醛或辛烯醇的催化剂。具体地说涉及一种选择性制备辛醛或辛烯醇的催化剂及其制备方法和应用。
[0012]
本发明目的之一是提供一种选择性制备辛醛或辛烯醇的催化剂,以所述催化剂总重量为百分比计,可包含以下组分:
[0013]
活性组分:3~25wt%;优选5~22wt%;
[0014]
碱土金属组分:1~10wt%;优选1~6wt%;
[0015]
稀土金属和/或过渡金属组分:1~10wt%;优选1~8wt%;
[0016]
载体:55~95wt%;优选64~93wt%;
[0017]
其中,
[0018]
所述活性组分的用量可为3~25wt%(如3wt%、4wt%、5wt%、6wt%、7wt%、8wt%、9wt%、10wt%、11wt%、12wt%、13wt%、14wt%、15wt%、16wt%、17wt%、18wt%、19wt%、20wt%、21wt%、22wt%、23wt%、24wt%、25wt%或上述数值之间的任意值)。
[0019]
所述载体的用量可为55~95wt%(如55wt%、56wt%、57wt%、58wt%、59wt%、60wt%、61wt%、62wt%、63wt%、64wt%、65wt%、66wt%、67wt%、68wt%、69wt%、70wt%、71wt%、72wt%、73wt%、74wt%、75wt%、76wt%、77wt%、78wt%、79wt%、80wt%、81wt%、82wt%、83wt%、84wt%、85wt%、86wt%、87wt%、88wt%、89wt%、90wt%、91wt%、92wt%、93wt%、94wt%、95wt%或上述数值之间的任意值)。
[0020]
所述活性组分可选自非贵金属组分;优选地,所述活性组分可选自cu、fe、ni、co、zn中的至少一种;
[0021]
所述碱土金属组分可优选自mg、ca、ba中的至少一种;
[0022]
所述稀土金属和/或过渡金属组分可优选自la、ce、mn、mo中的至少一种。
[0023]
在本发明的一些具体实施中,
[0024]
所述活性组分可选自cu、fe、ni、co、zn中的至少一种,其中,ni和co不同时存在;优选地,其中所述活性组分可包含ni或者co。
[0025]
在本发明的一些具体实施中,
[0026]
所述活性组分可选自cu、fe、ni、co、zn中的至少两种;优选地,其中所述活性组分可包含ni或者co。
[0027]
在本发明的一些具体实施中,
[0028]
所述活性组分可包含ni和来自cu、fe、zn中的至少一种。
[0029]
在本发明的一些具体实施中,
[0030]
所述活性组分可包含co和来自cu、fe、zn中的至少一种。
[0031]
在本发明的一些具体实施中,
[0032]
所述活性组分可选自cu、ni、co、zn中的一种;优选自ni或co。
[0033]
所述载体可选自al2o3、sio2、zro2、tio2、al2o
3-sio2、al2o
3-zro2、zro
2-sio2、al2o
3-tio2中的至少一种。所述载体可为本技术领域常用载体类型。
[0034]
本发明所述的选择性制备辛醛或辛烯醇的催化剂中,所述活性组分优选包含ni或co;当选择ni作为活性组分,会选择性生成更多辛醛,同时辛烯醇生成量很少;当选择co作为活性组分,会生成辛醛和辛烯醇,其中辛烯醇含量会得到提高。本发明所述的催化剂中,所述活性组分与其他组分之间存在协同作用,例如所述碱土金属,具有很好的导热性,添加以后会与活性组分在晶格中形成固溶体,虽然难以被还原,但是可以抑制活性组分的团聚;处于活性组分与载体之间,由于其具有优良的热稳定性,可以抑制活性组分与载体结合,从而生成难以还原的尖晶石结构,具有良好的稳定性,同时添加碱土金属后,可以调节载体的酸碱度,从而抑制其他副反应的发生。所述的稀土金属以及mn和mo,稀土金属具有独特的价电子层结构,能与过渡金属显示出良好的协同效应,可以参与反应,又可以与活性组分相互作用,促进活性组分的还原与分散,降低活性组分的还原温度,提升活性组分的分散度;mn的加入也可以促进活性组分的分散,从而提高催化剂的活性,mo的加入可以有效地抑制活性组分与载体之间的强相互作用,避免生成尖晶石等结构,同时具有一定的耐硫性,可以避免催化剂硫中毒。
[0035]
本发明目的之二是提供所述的选择性制备辛醛或辛烯醇的催化剂的制备方法,可包括以下步骤:
[0036]
将包含所述活性组分对应的可溶性盐、所述碱土金属组分对应的可溶性盐、所述稀土金属和/或过渡金属组分对应的可溶性盐、以及氧化石墨烯在内的组分的溶液浸渍在载体上后经干燥焙烧而得到。
[0037]
具体地,
[0038]
所述制备方法,可包括以下步骤:
[0039]
1)将所述活性组分对应的可溶性盐配置成溶液a;将所述碱土金属组分对应的可
溶性盐配置成溶液b;将所述稀土金属和/或过渡金属组分对应的可溶性盐配置成溶液c;
[0040]
2)将包含溶液a、溶液b、溶液c在内的组分与氧化石墨烯完全混合、搅拌均匀后,浸渍到载体上,经干燥焙烧后制得所述的催化剂。
[0041]
其中,
[0042]
配制溶液a、溶液b、溶液c的溶剂均为水,优选为去离子水;按最大溶解度进行溶解,溶剂的用量满足将活性组分对应的可溶性盐、碱土金属组分对应的可溶性盐、稀土金属和/或过渡金属组分对应的可溶性盐完全溶解即可。
[0043]
活性组分对应的可溶性盐及碱土金属组分、稀土金属和/或过渡金属组分对应的可溶性盐具体可选择本领域常见的水溶性盐,具体可选硝酸盐、碳酸盐等中的至少一种,优选硝酸盐。
[0044]
所述浸渍方法可使用浸渍法,具体可将溶液a、溶液b、溶液c加入到载体中即可。
[0045]
所述的氧化石墨烯的用量可为所述活性组分、碱土金属组分、稀土金属和/或过渡金属组分中的单质和载体的总重量的0.05~1wt%,优选0.05~0.6wt%,更优选0.1~0.3wt%。
[0046]
其中,
[0047]
所述干燥温度可为80~140℃,干燥时间可为3~10h;
[0048]
和/或,
[0049]
所述焙烧过程可包括以下步骤:首先于室温升温至200~250℃,保持5~10h,其中升温速率为100~200℃/h;而后升温至350~450℃,保持5~10h,其中升温速率为50~100℃/h。
[0050]
本发明的制备方法步骤中使用的设备均为现有技术中通常的设备。
[0051]
本发明目的之三是提供所述的制备方法制备而成的催化剂。
[0052]
本发明目的之四是提供所述的催化剂在辛烯醛选择性制备辛醛或辛烯醇反应中的应用。优选地,所述应用的反应条件可为:液相加氢方式,反应压力2~4mpa,温度80~120℃,空速为0.5~2.5h-1
。
[0053]
本发明催化剂中所述活性组分采用非贵金属,相对于贵金属具有更佳的经济性,同时拥有很好的活性,在促进反应物催化加氢方面发挥了重要作用,碱土金属、稀土金属和/或过渡金属的存在使得活性组分能够更好的发挥作用,例如添加la或ce,能够降低活性组分的晶粒尺寸,增加活性分子的比表面积,添加碱土金属mg等能够增加催化剂整体的热稳定性,使得催化剂在较高的温度下依然能发挥稳定的作用,添加mn助剂能够促进活性组分的分散,从而提高催化剂的活性。同时由于氧化石墨烯的存在,使得活性组分彼此之间不容易团聚,在载体中更容易分散,同时在高温焙烧阶段,氧化石墨烯会被完全分解,因此催化剂最终仅包含活性组分与碱土金属、稀土金属和/或过渡金属组分。然而在焙烧阶段,为了防止氧化石墨烯过快分解从而导致活性组分聚集,因此应采用缓慢升温步骤。
[0054]
本发明所述的催化剂具有良好的活性和经济性,适用于辛烯醛选择性制备辛醛或辛烯醇的反应,在不同催化剂的作用下,辛烯醛具有良好的转化率和选择性。
具体实施方式
[0055]
下面结合具体实施例对本发明进行具体的描述,有必要在此指出的是以下实施例
只用于对本发明的进一步说明,不能理解为对本发明保护范围的限制,本领域技术人员根据本发明内容对本发明做出的一些非本质的改进和调整仍属本发明的保护范围。
[0056]
在本文中所披露的范围的端点和任何值都不限于该精确的范围或值,这些范围或值应当理解为包含接近这些范围或值的值。对于数值范围来说,各个范围的端点值之间、各个范围的端点值和单独的点值之间,以及单独的点值之间可以彼此组合而得到一个或多个新的数值范围,这些数值范围应被视为在本文中具体公开。
[0057]
原料来源
[0058]
实施例与对比例中采用的原料,如果没有特别限定,那么均是现有技术公开的,例如可直接购买获得或者根据现有技术公开的制备方法制得。
[0059]
氧化石墨烯,2mg/ml,先丰纳米材料科技有限公司。
[0060]
实施例1
[0061]
将20g硝酸铜、4g硝酸钙、2g硝酸镧、溶于去离子水中,与25ml氧化石墨烯搅拌均匀,采用浸渍法负载于20g氧化锆(zro2)上,将浸渍后的产物置入100℃的烘箱中,干燥5h,将干燥后的催化剂置入马弗炉中,于室温升温至200℃,升温速率100℃/h,保持7h;而后升温至400℃,升温速率80℃/h保持10h。最终得到催化剂产品。
[0062]
实施例2
[0063]
将15g硝酸铁、5g硝酸镁、1g硝酸铈、溶于去离子水中,与25ml氧化石墨烯搅拌均匀,采用浸渍法负载于20g氧化铝-氧化硅(al2o
3-sio2)上,将浸渍后的产物置入110℃的烘箱中,干燥6h,将干燥后的催化剂置入马弗炉中,于室温升温至230℃,升温速率150℃/h,保持7h;而后升温至350℃,升温速率70℃/h保持8h。最终得到催化剂产品。
[0064]
实施例3
[0065]
将5g硝酸铜、1g硝酸钡、2g高锰酸钾、溶于去离子水中,与25ml氧化石墨烯搅拌均匀,采用浸渍法负载于20g氧化铝(al2o3)上,将浸渍后的产物置入120℃的烘箱中,干燥7h,将干燥后的催化剂置入马弗炉中,于室温升温至220℃,升温速率140℃/h,保持8h;而后升温至380℃,升温速率60℃/h保持8h。最终得到催化剂产品。
[0066]
实施例4
[0067]
将5g硝酸镍、4g硝酸钙、2g硝酸镧溶于去离子水中,与15ml氧化石墨烯搅拌均匀,采用浸渍法负载于20g氧化钛(tio2)上,将浸渍后的产物置入90℃的烘箱中,干燥9h,将干燥后的催化剂置入马弗炉中,于室温升温至200℃,升温速率160℃/h,保持9h;而后升温至440℃,升温速率50℃/h保持10h。最终得到催化剂产品。
[0068]
实施例5
[0069]
将20g硝酸镍、7g硝酸钙、3g钼酸铵溶于去离子水中,与35ml氧化石墨烯搅拌均匀,采用浸渍法负载于20g氧化铝-氧化锆(al2o
3-zro2)上,将浸渍后的产物置入140℃的烘箱中,干燥5h,将干燥后的催化剂置入马弗炉中,于室温升温至250℃,升温速率200℃/h,保持5h;而后升温至410℃,升温速率60℃/h保持7h。最终得到催化剂产品。
[0070]
实施例6
[0071]
将25g硝酸镍、5g硝酸镁、3g硝酸铈溶于去离子水中,与25ml氧化石墨烯搅拌均匀,采用浸渍法负载于20g氧化铝(al2o3)上,将浸渍后的产物置入140℃的烘箱中,干燥5h,将干燥后的催化剂置入马弗炉中,于室温升温至250℃,升温速率200℃/h,保持5h;而后升温至
380℃,升温速率90℃/h保持8h。最终得到催化剂产品。
[0072]
实施例7
[0073]
将20g硝酸铁、4g硝酸镁、2g硝酸锰溶于去离子水中,与20ml氧化石墨烯搅拌均匀,采用浸渍法负载于20g氧化钛(tio2)上,将浸渍后的产物置入90℃的烘箱中,干燥8h,将干燥后的催化剂置入马弗炉中,于室温升温至240℃,升温速率150℃/h,保持10h;而后升温至400℃,升温速率100℃/h保持9h。最终得到催化剂产品。
[0074]
实施例8
[0075]
将4g硝酸铜、1g硝酸钡、2g硝酸镧溶于去离子水中,与25ml氧化石墨烯搅拌均匀,采用浸渍法负载于20g氧化锆(zro2)上,将浸渍后的产物置入90℃的烘箱中,干燥9h,将干燥后的催化剂置入马弗炉中,于室温升温至240℃,升温速率170℃/h,保持9h;而后升温至450℃,升温速率50℃/h保持7h。最终得到催化剂产品。
[0076]
实施例9
[0077]
将10g硝酸锌、4g硝酸钙、2g硝酸铈、溶于去离子水中,与25ml氧化石墨烯搅拌均匀,采用浸渍法负载于20g氧化铝(al2o3)上,将浸渍后的产物置入100℃的烘箱中,干燥8h,将干燥后的催化剂置入马弗炉中,于室温升温至240℃,升温速率150℃/h,保持8h;而后升温至420℃,升温速率70℃/h保持9h。最终得到催化剂产品。
[0078]
实施例10
[0079]
将4g硝酸钴、6g硝酸镁、1g钼酸铵溶于去离子水中,与15ml氧化石墨烯搅拌均匀,采用浸渍法负载于20g氧化铝-氧化钛(al2o
3-tio2)上,将浸渍后的产物置入100℃的烘箱中,干燥8h,将干燥后的催化剂置入马弗炉中,于室温升温至210℃,升温速率140℃/h,保持9h;而后升温至360℃,升温速率70℃/h保持8h。最终得到催化剂产品。
[0080]
实施例11
[0081]
将30g硝酸钴、5g硝酸钙、4g硝酸镧、溶于去离子水中,与10ml氧化石墨烯搅拌均匀,采用浸渍法负载于20g氧化锆(zro2)上,将浸渍后的产物置入120℃的烘箱中,干燥8h,将干燥后的催化剂置入马弗炉中,于室温升温至240℃,升温速率140℃/h,保持7h;而后升温至370℃,升温速率90℃/h保持6h。最终得到催化剂产品。
[0082]
实施例12
[0083]
将25g硝酸钴、8g硝酸镁、2g高锰酸钾溶于去离子水中,与20ml氧化石墨烯搅拌均匀,采用浸渍法负载于20g氧化铝(al2o3)上,将浸渍后的产物置入120℃的烘箱中,干燥8h,将干燥后的催化剂置入马弗炉中,于室温升温至240℃,升温速率180℃/h,保持8h;而后升温至390℃,升温速率90℃/h保持10h。最终得到催化剂产品。
[0084]
实施例13
[0085]
将20g硝酸镍、5g硝酸铁、4g硝酸镁、1g钼酸铵溶于去离子水中,与20ml氧化石墨烯搅拌均匀,采用浸渍法负载于20g氧化铝(al2o3)上,将浸渍后的产物置入100℃的烘箱中,干燥10h,将干燥后的催化剂置入马弗炉中,于室温升温至240℃,升温速率140℃/h,保持9h;而后升温至380℃,升温速率70℃/h保持8h。最终得到催化剂产品。
[0086]
实施例14
[0087]
将20g硝酸钴、4g硝酸铜、5g硝酸镁、1g硝酸镧溶于去离子水中,与15ml氧化石墨烯搅拌均匀,采用浸渍法负载于20g氧化锆(zro2)上,将浸渍后的产物置入90℃的烘箱中,干
燥10h,将干燥后的催化剂置入马弗炉中,于室温升温至210℃,升温速率140℃/h,保持7h;而后升温至370℃,升温速率70℃/h保持5h。最终得到催化剂产品。
[0088]
对比例1
[0089]
将1g硝酸镍、5g硝酸镁、3g硝酸铈溶于去离子水中,与25ml氧化石墨烯搅拌均匀,采用浸渍法负载于20g氧化铝(al2o3)上,将浸渍后的产物置入140℃的烘箱中,干燥5h,将干燥后的催化剂置入马弗炉中,于室温升温至250℃,升温速率200℃/h,保持5h;而后升温至380℃,升温速率90℃/h保持8h。最终得到催化剂产品。
[0090]
对比例2
[0091]
将1g硝酸钴、5g硝酸钙、4g硝酸镧、溶于去离子水中,与10ml氧化石墨烯搅拌均匀,采用浸渍法负载于20g氧化锆(zro2)上,将浸渍后的产物置入120℃的烘箱中,干燥8h,将干燥后的催化剂置入马弗炉中,于室温升温至240℃,升温速率140℃/h,保持7h;而后升温至370℃,升温速率90℃/h保持6h。最终得到催化剂产品。
[0092]
催化剂性能评价
[0093]
量取10ml催化剂装入不锈钢固定床反应器,通入高纯n2,流量为300ml/min,升温至120℃,将高纯n2切换为h2,流量为200ml/min,升温至400~450℃并保持4h,对催化剂进行还原,而后缓慢降低至室温,打开反应器卸出催化剂,取还原后的1g催化剂置入反应釜中,在反应原料20g(辛烯醛20wt%/辛醇余),反应温度100~120℃,反应压力3~4mpa,反应时间5~15h进行反应评价。
[0094]
按照上述评价方法,对实施例1~14和对比例1~2制备的催化剂分别进行了反应评价,表1给出了详细评价结果。
[0095]
表1实施例1~14和对比例1~2的催化剂的反应评价结果
[0096]
(反应温度110℃、压力3mpa、反应时间10h)
[0097][0098][0099]
由表1的结果可见,本发明实施例催化剂在相同条件下,含ni或co组分的催化剂在活性以及选择性方面具有更佳的效果。从对比例1和对比例2可见,当活性组分含量降低的时候,催化剂所具有的活性不足以促进反应的发生,因此反应的转化率降低,选择性下降。