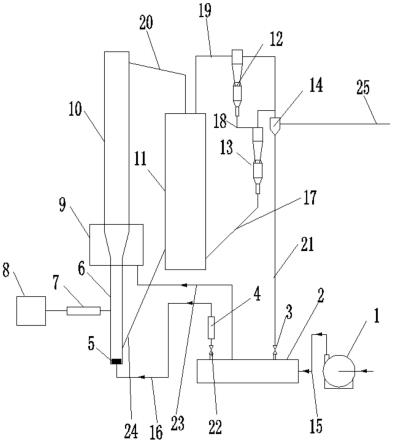
1.本发明属于循环流化床技术领域,具体来说涉及一种新型组合小直径段提升管流化床反应装置。
背景技术:2.流化床具有优良的传质、传热特性以及高效快速的运输能力,在能源、化工、制药、食品以及环境等各个行业均有广泛应用。然而传统的循环流化床内颗粒浓度较低、气固接触效率低、轴径向流动特性不均匀,导致反应不充分、不均一,产品的转化率较低;而高密度流化床或者湍动流化床虽然床内颗粒浓度较高,但流化床反应器内会出现严重的返混现象,导致催化剂焦化严重,催化剂失效,并对连续反应产生不利影响。
技术实现要素:3.针对现有技术的不足,本发明的目的在于提供一种新型组合小直径段提升管流化床反应装置,该新型组合小直径段提升管流化床反应装置能够充分解决循环流化床反应不均匀及湍动流化床高返混等问题。
4.本发明的目的是通过下述技术方案予以实现的。
5.一种新型组合小直径段提升管流化床反应装置,包括:流化床、气体分布器、压缩机、补气装置、伴床和缓冲罐,所述压缩机通过第一管道与所述缓冲罐的进气口连通,所述气体分布器设置在所述流化床内,所述缓冲罐的第一排气口通过第二管道与所述流化床内的气体分布器连通,所述流化床的顶部通过第十管道与所述伴床的第一入口连通,用于经过所述第十管道向所述伴床内通入催化剂和气体产物,所述伴床的第一出口通过第九管道与所述流化床连通,用于向所述流化床内通入催化剂,所述伴床的第二出口通过第三管道与一第一旋风分离器的进气口连通,用于对第三管道内的物质进行气固分离,所述第一旋风分离器的排灰口通过第四管道与一第二旋风分离器的进气口连通,用于对第四管道内的物质进行气固分离,所述第二旋风分离器的排灰口通过第五管道与所述伴床的第二入口连通,用于向所述伴床内通入气固分离后的催化剂,所述第一旋风分离器和第二旋风分离器的排气口均与外界相通;
6.在所述伴床上设置有催化剂投入口,所述催化剂投入口上安装有盖体;
7.所述补气装置安装在所述流化床上,所述缓冲罐的第二排气口通过第八管道与所述补气装置连通。
8.在上述技术方案中,所述补气装置包括:上补气舱和下补气舱,所述上补气舱和下补气舱均为环状腔体且套在所述流化床外,所述流化床从上至下依次为大直径段提升管、变径段以及小直径段提升管,所述上补气舱套在所述大直径段提升管的下部且变径段的上部位于所述上补气舱内,所述下补气舱套在所述小直径段提升管的上部且变径段的下部位于所述下补气舱内,在所述上补气舱上形成有第一补气进口,在所述下补气舱上形成有第二补气进口;在所述上补气舱内的流化床上设置有多个第一喷嘴,在所述下补气舱内的流
化床上设置有多个第二喷嘴,所述第一喷嘴和第二喷嘴均位于所述变径段。
9.在上述技术方案中,在所述上补气舱上形成有第一补气舱排灰口,第一补气舱排灰口上安装有盖体,在所述下补气舱上形成有第二补气舱排灰口,第二补气舱排灰口上安装有盖体。
10.在上述技术方案中,所述变径段的内壁上形成有多个凸起的棱锥。
11.在上述技术方案中,所述棱锥为三棱锥。
12.在上述技术方案中,所述第一喷嘴的数量为4~12个且沿圆周方向设置在所述流化床上,所述第二喷嘴的数量为4~12个且沿圆周方向设置在所述流化床上。
13.在上述技术方案中,所述变径段的斜面与所述水平面的夹角θ为40~89
°
。
14.在上述技术方案中,每个所述棱锥最靠上的斜面与所述该棱锥所在变径段的内壁之间的夹角为5~θ
°
。
15.在上述技术方案中,所述上补气舱的高度为0.25~1m,所述下补气舱的高度为0.25~1m。
16.在上述技术方案中,所述第一喷嘴与流化床中心轴的距离为r1,所述第二喷嘴与流化床中心轴的距离为r2,所述大直径段提升管的半径为r,则0.75《r1/r《1,0.5《r2/r《0.75。
17.在上述技术方案中,所述第八管道由两根分支管道组成,每一根分支管道上安装有第二气体流量计和第二阀门,第一补气进口和第二补气进口上各连通有一根所述分支管道。
18.在上述技术方案中,所述第二出口位于所述伴床的上部,所述第一出口位于所述伴床的下部。
19.在上述技术方案中,在所述流化床上设置有压力传感器,在所述流化床上设置有温度传感器,在所述流化床上设置有催化剂浓度传感器,在所述流化床上设置有速度传感器,速度传感器用于检测催化剂的速度。
20.在上述技术方案中,所述第一旋风分离器和第二旋风分离器的排气口与一吸收装置连通,所述吸收装置用于对从第一旋风分离器和第二旋风分离器的排气口排出的有害气体和部分催化剂进行吸收。
21.在上述技术方案中,所述气体分布器设置在所述流化床的小直径段提升管的底部。
22.在上述技术方案中,所述第二旋风分离器的排灰口通过第五管道与所述伴床连通。
23.在上述技术方案中,所述缓冲罐的放空口通过第六管道与所述吸收装置连通,在所述第六管道上设置有放空阀。
24.在上述技术方案中,在所述第二管道上设置有第一气体流量计和第一阀门。
25.在上述技术方案中,所述吸收装置通过一第七管道与外界相通,用于排出除去有害气体后的气体和部分催化剂。
26.本发明新型组合小直径段提升管流化床反应装置的有益效果如下:
27.1.伴床为催化剂存储的中间载体,伴床的设置在竖直方向上高于小直径段提升管,因此为催化剂进入小直径段提升管提供了动力,进而提高了小直径段提升管循环强度,
提高气固接触效率,增强小直径段提升管内气固流动轴径向均匀性,增大生产能力。
28.2.小直径段提升管在补气装置的作用下,小直径段提升管的上部形成负压区,提高小直径段提升管下部内气固流体的拉拽作用,从而抑制小直径段提升管下部内噎塞现象的发生,使小直径段提升管下部内气固流动特性获得较高的颗粒浓度及轴径向流动均一效果;
29.3.大直径段提升管上部在补气装置的作用下,为大直径段提升管上部内的气固流体提供提升作用,加快气固流体运输,并降低大直径段提升管上部边壁区的气固返混。
30.4.在补气装置的作用下,可以将流化床内固流体流型分区,小直径段提升管为实现固气比较大的浓相区,呈现湍动流态化流型或高密度流态化流型,大直径段提升管为固气比较小的稀相区,呈现快速流态化或气力输送流型。
31.5.补气装置的设置可以对大直径段提升管以及小直径段提升管分别进行灵活控制,从而减少了大直径段提升管以及小直径段提升管发生副反应和过度反应的几率,进而提高了总反应目标产物的产率。
32.6.在变径段斜边设置均匀分布的锥棱,可以使沿变径段表面向下流动的气固混合物形成阻碍作用,并能将其导流进入大直径段提升管中心高速向上的气固主流中,在加速油、剂混合的同时也有效地抑制了催化剂的返混。
附图说明
33.图1是本发明新型组合小直径段提升管流化床反应装置的结构示意图;
34.图2为补气装置的结构示意图;
35.图3为补气装置的结构示意图(带棱锥)。
36.其中,1:压缩机,2:缓冲罐,3:放空阀,4:第一气体流量计,5:气体分布器,6:小直径段提升管,7:压力传感器,8:计算机,9:补气装置,9-1:第二补气舱排灰口,9-2:第二补气进口,9-3:第一补气进口,9-4:第一补气舱排灰口,10:流化床,10-1:第一喷嘴,10-2:第二喷嘴,11:伴床,12:第一旋风分离器,13:第二旋风分离器,14:吸收装置,15:第一管道,16:第二管道,17:第五管道,18:第四管道,19:第三管道,20:第十管道,21:第六管道,22:第一阀门,23:第八管道,24:第九管道,25:第七管道。
具体实施方式
37.下面结合具体实施例进一步说明本发明新型组合小直径段提升管流化床反应装置的技术方案。
38.气体分布器5可以采用cn201210405627.6中的气固分布器。
39.实施例1
40.如图1所示,包括:流化床10、气体分布器5、压缩机1、补气装置9、伴床11和缓冲罐2,压缩机1通过第一管道15与缓冲罐2的进气口连通,气体分布器5设置在流化床10内,缓冲罐2上设置有2个排气口:第一排气口和第二排气口,缓冲罐2的第一排气口通过第二管道16与流化床10内的气体分布器5连通,流化床10的顶部通过第十管道20与伴床11的第一入口连通,用于经过第十管道20向伴床11内通入催化剂和气体产物,伴床11的第一出口通过第九管道24与流化床10连通,用于向流化床10内通入催化剂,伴床11的第二出口通过第三管
道19与一第一旋风分离器12的进气口连通,用于对第三管道19内的物质进行气固分离,其中,第二出口位于伴床11的上部,第一出口位于伴床11的下部。
41.第一旋风分离器12的排灰口通过第四管道18与一第二旋风分离器13的进气口连通,用于对第四管道18内的物质进行气固分离,第二旋风分离器13的排灰口通过第五管道17与伴床11的第二入口连通,用于向伴床11内通入气固分离后的催化剂,第一旋风分离器12和第二旋风分离器13的排气口均与外界相通;
42.在伴床11上设置有催化剂投入口,催化剂投入口上安装有盖体;
43.补气装置9安装在流化床10上,缓冲罐2的第二排气口通过第八管道23与补气装置9连通。
44.压缩机将原料气输送至缓冲罐中,从而进入到流化床内的气体分布器内或进入至补气装置内;固体颗粒状态的催化剂与原料气在流化床内反应完毕后进入伴床,伴床内大部分催化剂经第九管道24循环回料返回至流化床内,少部分催化剂与原料气经第一旋风分离器和第二旋风分离器进行气固分离;操作中,补气装置可以实现将流化床状态分区调控,将小直径段提升管6形成固气比比较大的浓相区(固含率在0.25-0.3之间),大直径段提升管形成固气比比较小的稀相区(固含率在0.03-0.08之间)。
45.实施例2
46.如图2和3所示,在实施例1的基础上,补气装置9包括:上补气舱和下补气舱,上补气舱和下补气舱均为环状腔体且套在流化床10外,流化床10从上至下依次为大直径段提升管、变径段以及小直径段提升管6,上补气舱套在大直径段提升管的下部且变径段的上部位于上补气舱内,下补气舱套在小直径段提升管6的上部且变径段的下部位于下补气舱内,在上补气舱上形成有第一补气进口9-3,在下补气舱上形成有第二补气进口9-2;在上补气舱内的流化床10上设置有多个第一喷嘴10-1,在下补气舱内的流化床10上设置有多个第二喷嘴10-2,第一喷嘴10-1和第二喷嘴10-2均位于变径段。补气装置内布置的第一喷嘴和第二喷嘴将流化床进行上下部流型分区,小直径段提升管6为实现固气比比较大的浓相区,呈现湍动流态化流型或高密度流态化流型,大直径段提升管为固气比比较小的稀相区,呈现快速流态化或气力输送流型。
47.气体先经过第八管道23进入上补气舱和下补气舱,再经过第一喷嘴和第二喷嘴进入流化床内。
48.第一喷嘴10-1的数量为4~12个且沿圆周方向设置在流化床10上,第二喷嘴10-2的数量为4~12个且沿圆周方向设置在流化床10上。
49.第一喷嘴10-1与流化床10中心轴的距离为r1,第二喷嘴10-2与流化床10中心轴的距离为r2,大直径段提升管的半径为r,则0.75《r1/r《1,0.5《r2/r《0.75。
50.在上补气舱上形成有第一补气舱排灰口9-4,第一补气舱排灰口9-4上安装有盖体,在下补气舱上形成有第二补气舱排灰口9-1,第二补气舱排灰口9-1上安装有盖体。设置第一补气舱排灰口9-4和第二补气舱排灰口9-1的目的是遇到突发状况后,排出上补气舱和下补气舱内的固体颗粒。在补气过程中,第一补气舱排灰口9-4和第二补气舱排灰口9-1上的盖体关闭,当出现异常情况时,停止补气,打开第一补气舱排灰口9-4和第二补气舱排灰口9-1上的盖体进行清灰。
51.变径段的内壁上形成有多个凸起的棱锥。作为优选,棱锥为三棱锥。每个棱锥最靠
上的斜面与该棱锥所在变径段的内壁之间的夹角为5~θ
°
。
52.变径段的斜面与水平面的夹角θ为40~89
°
。
53.上补气舱的高度为0.25~1m,下补气舱的高度为0.25~1m。
54.伴床11的第一出口的高度高于小直径段提升管6的高度,使从第一出口排出的催化剂能够在重力的作用下重新进入流化床内。
55.实施例3
56.在实施例2的基础上,第八管道23由两根分支管道组成,每一根分支管道上安装有第二气体流量计和第二阀门,第一补气进口9-3和第二补气进口9-2上各连通有一根分支管道。2根分支管道可以单独调控流速。
57.在流化床10上设置有压力传感器7,在流化床10上设置有温度传感器,在流化床10上设置有催化剂浓度传感器,在流化床10上设置有速度传感器,速度传感器用于检测催化剂的速度。压力传感器7、温度传感器、催化剂浓度传感器和速度传感器均与计算机8电连接。
58.第一旋风分离器12和第二旋风分离器13的排气口与一吸收装置14连通,吸收装置14用于对从第一旋风分离器12和第二旋风分离器13的排气口排出的有害气体和部分催化剂进行吸收。吸收装置14通过一第七管道25与外界相通,用于排出除去有害气体后的气体和部分催化剂。吸收装置14内由改性纤维材料进行填装,实现对有害气体和部分催化剂的吸收,进而改善环境,例如改性纤维材料可以采用申请号2018113390028中的可再生纤维球。
59.气体分布器5设置在流化床10的小直径段提升管6的底部。
60.第二旋风分离器13的排灰口通过第五管道17与流化床10的小直径段提升管6连通。
61.在第二管道16上设置有第一气体流量计4和第一阀门22。
62.缓冲罐2的放空口通过第六管道21与吸收装置14连通,在第六管道21上设置有放空阀3。本发明新型组合小直径段提升管流化床反应装置在开车前应打开放空阀3,避免缓冲罐压力过大;当新型组合小直径段提升管流化床反应装置运行时,调控放空阀3(当第一阀门22和第二阀门调节大气体流量时,关闭放空阀3;当第一阀门22和第二阀门调节小气体流量时,开启放空阀3,避免缓冲罐压力过大),通过与第二管道16上的第一阀门22配合操作,使流化床内的气固流动达到特定流型;新型组合小直径段提升管流化床反应装置停车前,再次打开放空阀3。
63.以上对本发明做了示例性的描述,应该说明的是,在不脱离本发明的核心的情况下,任何简单的变形、修改或者其他本领域技术人员能够不花费创造性劳动的等同替换均落入本发明的保护范围。