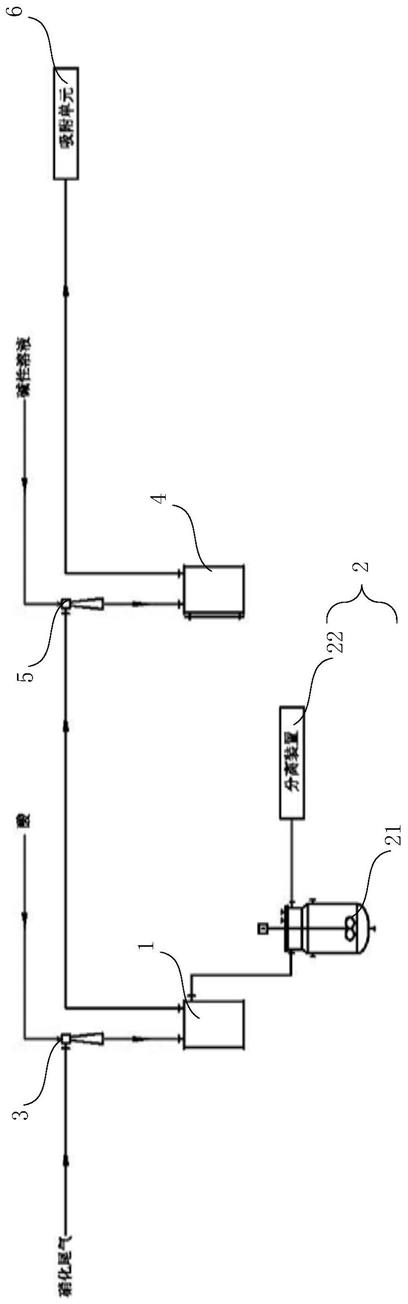
[0001]
本发明涉及环境工程技术领域,特别是涉及一种硝化尾气的处理方法和系统。
背景技术:[0002]
随着国内经济的快速发展,氮氧化物(no
x
)污染物的排放量迅速增加,严重污染了生态环境,已成为制约社会经济发展的重要因素之一。氮氧化物的控制已成为国家经济可持续发展和环境保护的紧迫要求。目前硝化尾气中的氮氧化物处理方法有:采用固体吸附剂结合再生手段处理含氮氧化物的尾气;采用两级双氧水串联吸收氮氧化物;采用液碱吸收塔吸收氮氧化物,将气相中的nox转移到液相中,生成硝酸盐和亚硝酸盐。制备硝基苯的硝化系统尾气中氮氧化物(no
x
)含量较高,利用上述方法处理成本较高,需要消耗大量的吸附剂或碱液,处理后一般直接排放,会导致硝化系统的硝酸消耗量高,浪费硝酸原料。
技术实现要素:[0003]
鉴于以上所述现有技术的缺点,本发明的目的在于提供一种硝化尾气的处理方法和系统,用于解决现有技术中的问题。
[0004]
为实现上述目的及其他相关目的,本发明第一方面提供一种硝化尾气的处理方法,包括如下步骤:
[0005]
1)将硝化尾气与酸混合反应,得到第一尾气和第一混合液;
[0006]
2)将步骤1)得到的第一混合液与萃取剂混合萃取,分离,得到油相和酸相。
[0007]
优选地,所述硝化尾气的处理方法还包括步骤3):将步骤1)得到的第一尾气与碱性溶液混合反应,得到第二尾气和第二混合液。
[0008]
更优选地,还包括如下技术特征中的至少一项:
[0009]
1)所述碱性溶液选自氢氧化钠水溶液、氢氧化钾水溶液、碳酸钠水溶液和碳酸氢钠水溶液中的一种或多种;
[0010]
2)所述碱性溶液中碱含量为10wt%~15wt%,如10wt%~12wt%、12wt%~13wt%或13wt%~15wt%;
[0011]
3)所述碱性溶液与所述第一尾气的体积比为(10~15):(30~50),如(10~13):(30~50)、(13~14):(30~50)、(14~15):(30~50)、(10~15):(30~34)、(10~15):(34~37)、(10~15):(34~40)或(10~15):(40~50);
[0012]
4)混合反应的温度为20℃~40℃,如20℃~25℃、25℃~30℃、30℃~35℃或35℃~40℃;
[0013]
5)所述硝化尾气的处理方法还包括步骤4):将步骤3)得到的第二尾气经吸附剂吸附。
[0014]
进一步更优选地,特征5)中,还包括如下技术特征中的至少一项:
[0015]
51)所述吸附剂为活性炭,如可以采用的柱状活性炭;
[0016]
52)所述第二尾气中氮氧化物含量为100mg/m3~200mg/m3,如100mg/m3~110mg/
m3、110mg/m3~130mg/m3、130mg/m3~150mg/m3、150mg/m3~180mg/m3或180mg/m3~200mg/m3;
[0017]
53)吸附温度为15℃~40℃,如15℃~25℃、25℃~30℃、30℃~35℃或35℃~40℃。
[0018]
优选地,还包括如下技术特征中的至少一项:
[0019]
1a)步骤1)中,所述硝化尾气为制备硝基苯产生的硝化尾气;
[0020]
1b)步骤1)中,所述硝化尾气包括氮氧化物;
[0021]
1c)步骤1)中,所述硝化尾气中氮氧化物含量为1000mg/m3~1500mg/m3,如1000mg/m3~1200mg/m3、1200mg/m3~1300mg/m3或1300mg/m3~1500mg/m3;
[0022]
1d)步骤1)中,所述酸为制备硝基苯产生的废酸;
[0023]
1e)步骤1)中,所述酸与所述硝化尾气的体积比为(8~15):(30~50),如(8~9):(30~50)、(9~11):(30~50)、(11~12):(30~50)、(12~13):(30~50)、(13~15):(30~50)、(8~15):(30~34)、(8~15):(34~37)、(8~15):(37~40)、(8~15):(40~50);
[0024]
1f)步骤1)中,混合反应的温度20℃~45℃,如20℃~30℃、30℃~38℃或38℃~44℃;
[0025]
1g)步骤1)中,所述第一尾气中氮氧化物含量为500mg/m3~900mg/m3,如500mg/m3~584mg/m3、584mg/m3~744mg/m3、744mg/m3~806mg/m3或806mg/m3~900mg/m3;
[0026]
2a)步骤2)中,所述萃取剂为苯;
[0027]
2b)步骤2)得到的油相作为原料制备硝基苯;所述油相可以包括99.7wt%~99.8wt%的苯和0.2wt%~0.3wt%的硝基苯,可进入硝化系统作为原料使用,如99.7wt%~99.75wt%、99.75wt%~99.76wt%、99.76wt%~99.78wt%或99.78wt%~99.8wt%的苯,0.2wt%~0.22wt%、0.22wt%~0.24wt%、0.24wt%~0.25wt%或0.25wt%~0.3wt%的硝基苯;
[0028]
2c)步骤2)得到的酸相浓缩后作为制备硝基苯的催化剂;所述酸相可以包括68wt%~68.2wt%的硫酸、0.2wt%~0.3wt%的硝酸和31.6wt%~31.8wt%的水,将所述酸相浓缩后硫酸含量可为82wt%~84wt%,可作为催化剂进入硝化系统回用,如68wt%~68.13wt%、68.13wt%~68.15wt%、68.15wt%~68.16wt%、68.16wt%~68.2wt%的硫酸,0.2wt%~0.22wt%、0.22wt%~0.24wt%、0.24wt%~0.26wt%、0.26wt%~0.28wt%、0.28wt%~0.3wt%的硝酸;
[0029]
2d)步骤2)中,所述第一混合液与所述萃取剂的体积比为1.8:1~2.2:1;1.8:1~2:1或2:1~2.2:1
[0030]
2e)步骤2)中,混合萃取的温度为20℃~45℃,如20℃~30℃、30℃~35℃、35℃~38℃或38℃~40℃。
[0031]
更优选地,还包括如下技术特征中的至少一项:
[0032]
1d1)特征1d)中,所述废酸包括如下质量百分比的各组分:硫酸67.95wt%~68.05wt%,如67.95wt%~68.0wt%、68.0wt%~68.03wt%、68.03wt%~68.05wt%,硝酸0.5wt%~0.6wt%,如0.5wt%~0.53wt%、0.53wt%~0.55wt%、0.55wt%~0.6wt%,水31.4wt%~31.5wt%,如31.4wt%~31.44wt%或31.44wt%~31.5wt%;
[0033]
2c1)特征2c)中,浓缩后的酸相中硫酸含量为82wt%~84wt%,如82wt%~83wt%或83wt%~84wt%。
[0034]
本发明第二方面提供一种硝化尾气的处理系统,包括:
[0035]
酸吸收单元,用于将硝化尾气与酸混合反应,得到第一尾气和第一混合液;
[0036]
萃取分离单元,用于将所述第一混合液与萃取剂混合萃取,分离,得到油相和酸相;
[0037]
所述酸吸收单元与所述萃取分离单元流体连通。
[0038]
优选地,所述萃取分离单元包括萃取装置和分离装置;
[0039]
所述酸吸收单元与所述萃取装置流体连通;所述萃取装置与所述分离装置流体连通。
[0040]
优选地,所述硝化尾气的处理系统还包括:
[0041]
第一混合器,用于将所述硝化尾气与所述酸混合;
[0042]
所述第一混合器与所述酸吸收单元流体连通。
[0043]
优选地,所述硝化尾气的处理系统还包括:
[0044]
碱性溶液吸收单元,用于将所述第一尾气与碱性溶液混合反应,得到第二尾气和第二混合液;
[0045]
所述碱性溶液吸收单元与所述酸吸收单元流体连通。
[0046]
更优选地,所述硝化尾气的处理系统还包括:
[0047]
第二混合器,用于将所述第一尾气与所述碱性溶液混合;
[0048]
所述酸吸收单元经所述第二混合器与所述碱性溶液吸收单元流体连通。
[0049]
更优选地,所述硝化尾气的处理系统还包括:
[0050]
吸附单元,用于将所述第二尾气经吸附剂吸附;
[0051]
所述吸附单元与所述碱性溶液吸收单元流体连通。
[0052]
上述技术方案具有如下有益效果中的至少一项:
[0053]
1)本发明可利用制备硝基苯产生的废酸对硝化尾气进行吸收,将硝化尾气中的氮氧化物no
x
转移到废酸中,得到第一混合液,再将第一混合液与萃取剂如苯混合萃取、分离后可回用到制备硝基苯的生产系统中,即得到的油相可作为原料制备硝基苯,得到的酸相浓缩后可作为制备硝基苯的催化剂。
[0054]
2)本发明可采用制备硝基苯产生的废酸吸收硝化尾气中的氮氧化物,有效利用废酸,减少硝化尾气处理成本。
[0055]
3)本发明通过萃取第一混合液中的硝酸,并分离出来,将其作为原料回用到硝化系统,降低硝化系统的硝酸消耗量。
[0056]
4)本发明可将硝化尾气中的no
x
由1500mg/m3降低到约200mg/m3,大部分no
x
被废酸和碱性溶液吸收。
[0057]
5)本发明处理成本低,碱性溶液或吸附剂消耗量低,经处理后的尾气可直接排放。
附图说明
[0058]
图1显示为本发明硝化尾气的处理系统示意图。
[0059]
附图标记
[0060]1ꢀꢀꢀꢀꢀꢀꢀꢀꢀꢀꢀꢀꢀꢀꢀꢀꢀꢀꢀꢀꢀꢀꢀ
酸吸收单元
[0061]2ꢀꢀꢀꢀꢀꢀꢀꢀꢀꢀꢀꢀꢀꢀꢀꢀꢀꢀꢀꢀꢀꢀꢀ
萃取分离单元
[0062]
21
ꢀꢀꢀꢀꢀꢀꢀꢀꢀꢀꢀꢀꢀꢀꢀꢀꢀꢀꢀꢀꢀꢀ
萃取装置
[0063]
22
ꢀꢀꢀꢀꢀꢀꢀꢀꢀꢀꢀꢀꢀꢀꢀꢀꢀꢀꢀꢀꢀꢀ
分离装置
[0064]3ꢀꢀꢀꢀꢀꢀꢀꢀꢀꢀꢀꢀꢀꢀꢀꢀꢀꢀꢀꢀꢀꢀꢀ
第一混合器
[0065]4ꢀꢀꢀꢀꢀꢀꢀꢀꢀꢀꢀꢀꢀꢀꢀꢀꢀꢀꢀꢀꢀꢀꢀ
碱性溶液吸收单元
[0066]5ꢀꢀꢀꢀꢀꢀꢀꢀꢀꢀꢀꢀꢀꢀꢀꢀꢀꢀꢀꢀꢀꢀꢀ
第二混合器
[0067]6ꢀꢀꢀꢀꢀꢀꢀꢀꢀꢀꢀꢀꢀꢀꢀꢀꢀꢀꢀꢀꢀꢀꢀ
吸附单元
具体实施方式
[0068]
须知,下列实施例中未具体注明的工艺设备或装置均采用本领域内的常规设备或装置。
[0069]
此外应理解,本发明中提到的一个或多个方法步骤并不排斥在所述组合步骤前后还可以存在其他方法步骤或在这些明确提到的步骤之间还可以插入其他方法步骤,除非另有说明;还应理解,本发明中提到的一个或多个设备/装置之间的组合连接关系并不排斥在所述组合设备/装置前后还可以存在其他设备/装置或在这些明确提到的两个设备/装置之间还可以插入其他设备/装置,除非另有说明。而且,除非另有说明,各方法步骤的编号仅为鉴别各方法步骤的便利工具,而非为限制各方法步骤的排列次序或限定本发明可实施的范围,其相对关系的改变或调整,在无实质变更技术内容的情况下,当亦视为本发明可实施的范畴。
[0070]
一种硝化尾气的处理系统,如图1所示,包括:
[0071]
酸吸收单元1,用于将硝化尾气与酸混合反应,得到第一尾气和第一混合液;
[0072]
萃取分离单元2,用于将所述第一混合液与萃取剂混合萃取,分离,得到油相和酸相;
[0073]
所述酸吸收单元1与所述萃取分离单元2流体连通。
[0074]
在一优选的实施方式中,所述萃取分离单元2包括萃取装置21和分离装置22;
[0075]
所述酸吸收单元1与所述萃取装置21流体连通;所述萃取装置21与所述分离装置22流体连通。
[0076]
在一优选的实施方式中,所述硝化尾气的处理系统还包括:
[0077]
第一混合器3,用于将所述硝化尾气与所述酸混合;
[0078]
所述第一混合器3与所述酸吸收单元1流体连通。
[0079]
在一优选的实施方式中,所述硝化尾气的处理系统还包括:
[0080]
碱性溶液吸收单元4,用于将所述第一尾气与碱性溶液混合反应,得到第二尾气和第二混合液;
[0081]
所述碱性溶液吸收单元4与所述酸吸收单元1流体连通。
[0082]
在一优选的实施方式中,所述硝化尾气的处理系统还包括:
[0083]
第二混合器5,用于将所述第一尾气与所述碱性溶液混合;
[0084]
所述酸吸收单元1经所述第二混合器5与所述碱性溶液吸收单元4流体连通。
[0085]
在一优选的实施方式中,所述硝化尾气的处理系统还包括:
[0086]
吸附单元6,用于将所述第二尾气经吸附剂吸附;
[0087]
所述吸附单元6与所述碱性溶液吸收单元4流体连通。
[0088]
所述吸附单元6可以包括两个吸附罐,其中一个吸附罐中的吸附剂失活后,进行吸附剂活化,使用另外一个吸附罐进行吸附,两个吸附罐交替活化、使用。
[0089]
实施例1至实施例4中,硝化尾气中nox的去除率=(硝化尾气中no
x
的量-经活性炭吸附后尾气中的no
x
的量)/硝化尾气中no
x
的量*100%;硝化尾气中nox的回收率=(硝化尾气中no
x
的量-第一尾气中的no
x
的量)/硝化尾气中no
x
的量*100%;每立方米尾气的处理成本=处理每立方米尾气的碱液用量+处理每立方米尾气的吸附剂用量+动力消耗+活化活性炭蒸汽量。
[0090]
实施例1
[0091]
硝化尾气即硝化反应产生的尾气中no
x
含量为1000mg/m3,将硝化尾气经过第一混合器3与来源为硝基苯生产系统内循环的废酸混合后,进入酸吸收单元1,得到第一尾气和第一混合液。其中废酸的具体成分为68.0wt%硫酸、0.60wt%的硝酸、水31.4wt%。硝化尾气流量为30m3/h,废酸流量为9m3/h,废酸与硝化尾气的体积比为9:30,废酸吸收温度为20℃,第一尾气流量为30m3/h。硝化尾气中的no
x
被废酸吸收转化为硝酸,第一尾气中no
x
含量降低到584mg/m3,第一混合液的具体成分为67.99wt%硫酸、0.63wt%的硝酸、31.38wt%的水。
[0092]
将第一混合液用苯在萃取装置21中萃取,第一混合液与苯的体积比为2.2:1,萃取剂苯的流量为4m3/h,第一混合液的流量为8.8m3/h,萃取温度为30℃。萃取后再在分离装置22中进行分离回用,分离得到的上层油相具体成分为99.75wt%苯、0.25wt%硝基苯,油相作为原料进入硝化系统;下层酸相中的硫酸含量没有变化,硝酸含量由0.63wt%降低到0.28%,将68.13wt%硫酸浓缩至82wt%后进入硝酸系统中作为催化剂使用。
[0093]
将第一尾气经过第二混合器5与碱性溶液混合,再进入碱性溶液吸收单元4得到第二尾气和第二混合液,采用的碱性溶液为10wt%的氢氧化钠水溶液。碱性溶液流量为10m3/h,第一尾气流量为30m3/h,第二尾气流量为30m3/h,碱性溶液与第一尾气的体积比为10:30,碱性溶液吸收温度为25℃,碱性溶液可循环使用,并不断补充碱性溶液中消耗掉的氢氧化钠,氢氧化钠的消耗量为2kg/h。第二尾气中no
x
含量降低到150mg/m3。经过酸碱吸收后的第二尾气进入吸附单元6经吸附剂吸附,使用的吸附剂为柱状活性炭,活性炭的具体参数为的柱状活性炭,吸附温度为25℃。吸附单元6可以包括两个吸附罐,每个吸附罐装有200kg的吸附剂,其中一个吸附罐中的吸附剂失活后,进行吸附剂活化,使用另外一个吸附罐进行吸附,两个吸附罐交替活化、使用。最后尾气中的no
x
含量为50mg/m3,达到排放标准。硝化尾气中nox的回收率为41.60%,nox的去除率为95%,每立方米尾气的处理成本为0.042元。
[0094]
实施例2
[0095]
硝化尾气即硝化反应产生的尾气中no
x
含量为1500mg/m3,将硝化尾气经过第一混合器3与来源为硝基苯生产系统内循环的废酸混合后,进入酸吸收单元1,得到第一尾气和第一混合液。其中废酸的具体成分为68.0wt%硫酸、0.5wt%的硝酸、水31.5wt%。硝化尾气流量为34m3/h,废酸流量为11m3/h,废酸与硝化尾气的体积比为11:34,废酸吸收温度为30℃,第一尾气流量为34m3/h。硝化尾气中的no
x
被废酸吸收转化为硝酸,第一尾气中no
x
含量降低到900mg/m3,第一混合液的具体成分为68wt%硫酸、0.54wt%的硝酸、31.46wt%的水。
[0096]
将第一混合液用苯在萃取装置21中萃取,第一混合液与苯的体积比为2.0:1,萃取
剂苯的流量为5m3/h,第一混合液的流量为10m3/h,萃取温度为35℃。萃取后再在分离装置22中进行分离回用,分离得到的上层油相具体成分为99.7wt%苯、0.3wt%硝基苯,油相作为原料进入硝化系统;下层酸相中的硫酸含量没有变化,硝酸含量由0.54wt%降低到0.26wt%,将68.2wt%硫酸浓缩至84wt%后进入硝酸系统中作为催化剂使用。
[0097]
将第一尾气经过第二混合器5与碱性溶液混合,再进入碱性溶液吸收单元4得到第二尾气和第二混合液,采用的碱性溶液为15wt%的氢氧化钠水溶液。碱性溶液流量为13m3/h,第一尾气流量为34m3/h,第二尾气流量为34m3/h,碱性溶液与第一尾气的体积比为13:34,碱性溶液吸收温度为30℃,碱性溶液可循环使用,并不断补充碱性溶液中消耗掉的氢氧化钠,氢氧化钠的消耗量为3kg/h。第二尾气中no
x
含量降低到180mg/m3。经过酸碱吸收后的第二尾气进入吸附单元6经吸附剂吸附,使用的吸附剂为柱状活性炭,活性炭的具体参数为的柱状活性炭,吸附温度为30℃。吸附单元6可以包括两个吸附罐,每个吸附罐装有200kg的吸附剂,其中一个吸附罐中的吸附剂失活后,进行吸附剂活化,使用另外一个吸附罐进行吸附,两个吸附罐交替活化、使用。最后尾气中的no
x
含量为50mg/m3,达到排放标准。硝化尾气中nox的回收率为40%,nox的去除率为96.67%,每立方米尾气的处理成本为0.062元。
[0098]
实施例3
[0099]
硝化尾气即硝化反应产生的尾气中no
x
含量为1300mg/m3,将硝化尾气经过第一混合器3与来源为硝基苯生产系统内循环的废酸混合后,进入酸吸收单元1,得到第一尾气和第一混合液。其中废酸的具体成分为67.95wt%硫酸、0.55wt%的硝酸、水31.5wt%。硝化尾气流量为37m3/h,废酸流量为12m3/h,废酸与硝化尾气的体积比为12:37,废酸吸收温度为38℃,第一尾气流量为37m3/h。硝化尾气中的no
x
被废酸吸收转化为硝酸,第一尾气中no
x
含量降低到806mg/m3,第一混合液的具体成分为67.94wt%硫酸、0.58wt%的硝酸、31.48wt%的水。
[0100]
将第一混合液用苯在萃取装置21中萃取,第一混合液与苯的体积比为1.8:1,萃取剂苯的流量为6.5m3/h,第一混合液的流量为11.7m3/h,萃取温度为40℃。萃取后再在分离装置22中进行分离回用,分离得到的上层油相具体成分为99.76wt%苯、0.24wt%硝基苯,油相作为原料进入硝化系统;下层酸相中的硫酸含量没有变化,硝酸含量由0.58wt%降低到0.24wt%,将68.16wt%硫酸浓缩至83wt%后进入硝酸系统中作为催化剂使用。
[0101]
将第一尾气经过第二混合器5与碱性溶液混合,再进入碱性溶液吸收单元4得到第二尾气和第二混合液,采用的碱性溶液为12wt%的氢氧化钠水溶液。碱性溶液流量为14m3/h,第一尾气流量为37m3/h,第二尾气流量为37m3/h,碱性溶液与第一尾气的体积比为14:37,碱性溶液吸收温度为35℃,碱性溶液可循环使用,并不断补充碱性溶液中消耗掉的氢氧化钠,氢氧化钠的消耗量为3kg/h。第二尾气中no
x
含量降低到130mg/m3。经过酸碱吸收后的第二尾气进入吸附单元6经吸附剂吸附,使用的吸附剂为柱状活性炭,活性炭的具体参数为的柱状活性炭,吸附温度为30℃。吸附单元6可以包括两个吸附罐,每个吸附罐装有300kg的吸附剂,其中一个吸附罐中的吸附剂失活后,进行吸附剂活化,使用另外一个吸附罐进行吸附,两个吸附罐交替活化、使用。最后尾气中的no
x
含量为52mg/m3,达到排放标准。硝化尾气中nox的回收率为38%,nox的去除率为96%,每立方米尾气的处理成本为0.061元。
[0102]
实施例4
[0103]
硝化尾气即硝化反应产生的尾气中no
x
含量为1200mg/m3,将硝化尾气经过第一混合器3与来源为硝基苯生产系统内循环的废酸混合后,进入酸吸收单元1,得到第一尾气和第一混合液。其中废酸的具体成分为68.03wt%硫酸、0.53wt%的硝酸、水31.44wt%。硝化尾气流量为40m3/h,废酸流量为13m3/h,废酸与硝化尾气的体积比为13:40,废酸吸收温度为44℃,第一尾气流量为40m3/h。硝化尾气中的no
x
被废酸吸收转化为硝酸,第一尾气中no
x
含量降低到744mg/m3,第一混合液的具体成分为68.02wt%硫酸、0.55wt%的硝酸、31.43wt%的水。
[0104]
将第一混合液用苯在萃取装置21中萃取,第一混合液与苯的体积比为1.8:1,萃取剂苯的流量为7m3/h,第一混合液的流量为12.6m3/h,萃取温度为38℃。萃取后再在分离装置22中进行分离回用,分离得到的上层油相具体成分为99.78wt%苯、0.22wt%硝基苯,油相作为原料进入硝化系统;下层酸相中的硫酸含量没有变化,硝酸含量由0.55wt%降低到0.22wt%,将68.15wt%硫酸浓缩至84wt%后进入硝酸系统中作为催化剂使用。
[0105]
将第一尾气经过第二混合器5与碱性溶液混合,再进入碱性溶液吸收单元4得到第二尾气和第二混合液,采用的碱性溶液为13wt%的氢氧化钠水溶液。碱性溶液流量为15m3/h,第一尾气流量为40m3/h,第二尾气流量为40m3/h,碱性溶液与第一尾气的体积比为15:40,碱性溶液吸收温度为30℃,碱性溶液可循环使用,并不断补充碱性溶液中消耗掉的氢氧化钠,氢氧化钠的消耗量为3kg/h。第二尾气中no
x
含量降低到110mg/m3。经过酸碱吸收后的第二尾气进入吸附单元6经吸附剂吸附,使用的吸附剂为柱状活性炭,活性炭的具体参数为的柱状活性炭,吸附温度为35℃。吸附单元6可以包括两个吸附罐,每个吸附罐装有300kg的吸附剂,其中一个吸附罐中的吸附剂失活后,进行吸附剂活化,使用另外一个吸附罐进行吸附,两个吸附罐交替活化、使用。最后尾气中的no
x
含量为42mg/m3,达到排放标准。硝化尾气中nox的回收率为38%,nox的去除率为96.50%,每立方米尾气的处理成本为0.060元。
[0106]
硝化尾气不经过废酸吸收和萃取回收处理,直接用碱液吸收,硝化尾气中no
x
的去除率是90-92%、尾气处理成本为1.2-1.5元。
[0107]
硝化尾气不经过废酸吸收和萃取回收处理,只使用活性炭吸附,硝化尾气中no
x
的去除率在91-95%,尾气处理成本1.8-2.5元。
[0108]
综上所述,本发明有效克服了现有技术中的种种缺点而具高度产业利用价值。
[0109]
上述实施例仅例示性说明本发明的原理及其功效,而非用于限制本发明。任何熟悉此技术的人士皆可在不违背本发明的精神及范畴下,对上述实施例进行修饰或改变。因此,举凡所属技术领域中具有通常知识者在未脱离本发明所揭示的精神与技术思想下所完成的一切等效修饰或改变,仍应由本发明的权利要求所涵盖。