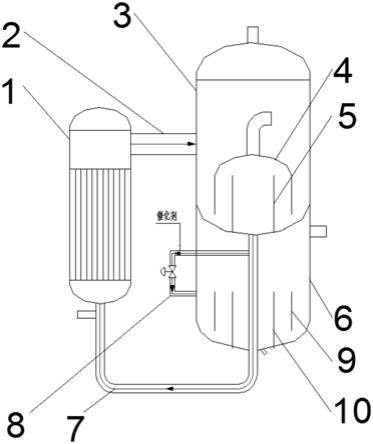
[0001]
本实用新型涉及聚酯生产领域,尤其涉及一种生产单体的外循环多级酯化反应器。
背景技术:[0002]
在聚酯生产中,采用乙二醇(eg)和对苯二甲酸(pta)进行酯化反应生成单体即对苯二甲酸乙二醇酯(bhet),然后通过缩聚反应合成聚对苯二甲酸乙二醇酯即聚酯(pet),bhet的酯化反应器往往采用两个反应器,第一个反应器主要是用于对苯二甲酸(pta)的溶解,第二个反应器则主要用于提高转化率或值化率,酯化率需要达到缩聚工艺的指标,本实用新型的一个酯化反应器可以高效的完成上述两个功能。
[0003]
现有的酯化反应器有几种不同的类型,其中内循环全混酯化反应器是聚酯工艺中常用的一种酯化反应装置,这种反应器内设有搅拌器和用于内加热的盘管或列管束及导流筒,以形成物料的上下循环,增强传热系数,获得/保持反应温度,提高酯化反应的速率,满足酯化反应的需要,所述搅拌器可以采用上装式,搅拌器的驱动装置通常安装在反应器的顶部,与搅拌器主轴的上端驱动连接,带动搅拌器工作。
[0004]
随着聚酯工程的大型化,酯化反应器的容积越来越大,大容量的反应器不仅降低了反应器运行的成本,而且提供了非常稳定的反应过程,但也给反应器的制造和运输提出了新的问题:例如,反应器过大可能超出一般公路、铁路运输的尺寸限度;所容纳的反应物增加,对反应所需热量的需求量大幅增加,如何制造加热量巨大的盘管或者说如何提供大量的热以满足反应要求;以及如何保证搅拌器的稳定运行,如何抑制因搅拌器线性尺寸变大可能导致的刚性变差和反应物剧烈反应引起的不平衡扰动等成为制约上述酯化反应器超大型化的一个技术瓶颈。
[0005]
cn1248777c公开了一种采用外循环加热的用于反应或分离的容器装置,包括容器和外置换热器,容器可以为塔或釜。容器为具有内外室的双室结构,内室位于容器的底部,容器中内室外部的连续空间为外室。内室顶部位于从容器底向上连续空间高度的1/2以下部位。容器连接换热器进口的管道连接口位于内室底部与内室相通,容器连接换热器出口的管道连接口位于容器下部与外室相通。内室与外室相互隔离,两者通过一种u形管相通作为液相物料的通道,此种酯化反应器酯化率一般只有92%左右,增加后续反应器的负担。
[0006]
cn203389633u公开了一种酯化反应器,包括反应器筒体和设置于所述反应器筒体内的加热装置和上装式搅拌器,所述上装式搅拌器设有主轴,所述主轴的上端连接搅拌器驱动装置,所述反应器筒体由上封头、中间筒体和下封头依次连接而成,所述上封头、中间筒体和下封头之间相互连接的方式为通过设有制口结构的法兰连接,所述各制口结构采用大型立车加工,所述加热装置采用若干竖向加热筒,所述加热筒通过相应的进、出导管连接蒸发器,所述加热筒、导管和蒸发器构成无动力循环热媒真空系统。然而,这种装置仍然是利用化学反应平衡的原理,反应效率低,能耗高。
[0007]
因此,有针对性的对聚酯生产领域提供一种高效能的、进一步提高反应效率的多
级酯化反应器及其使用方法,是亟待解决的技术问题。
技术实现要素:[0008]
本实用新型的目的在于提供一种外循环多级酯化反应器,物料通过两个设备之间的全混和设备内部的平推流流动,实现反应原料向反应产物的更大程度的转化,更有利于酯化反应的进行,得到更高纯度的产物,以解决传统反应器所存在的反应效率低和产物浓度低的技术缺陷。
[0009]
为达到上述目的,本实用新型的解决方法是提供一种外循环多级酯化反应器,包括:反应釜装置和管式加热器,所述反应釜装置和管式加热器之间通过管路连接;
[0010]
所述反应釜装置包括通过反应釜封头上、下分割开的一级反应釜和二级反应釜,所述一级反应釜位于所述二级反应釜上部。
[0011]
进一步地,一级反应釜下部设置有嵌套式的反应腔室,包括,位于所述一级反应釜底部中心位置通过内腔筒体围成的环形导流筒和罩于所述环形导流筒上部、通过反应外室壁围成的内室罩;其中,所述环形导流筒、内室罩以及所述一级反应釜的内部空间为连通状态,反应物料能够通过环性流动的方式在各腔室内部流动;所述一级反应釜的顶部设有排气口,所述内室罩的顶部设有第一出气口;所述一级反应釜的底部设有循环管,所述循环管穿过所述二级反应釜的底部将来自所述一级反应釜的物料通入所述管式加热器的底部,所述管式加热器的侧边通过连接管与所述一级反应釜的侧壁连通,将物料循环回所述一级反应釜。
[0012]
进一步的,所述二级反应釜的下部设有外环形导流筒和内环形导流筒,所述外环形导流筒和所述内环形导流筒均为夹套结构,可以为反应提供热量,热量来自有机热载体,所述循环管进入所述二级反应釜后,分出一根支管,所述支管将位于所述循环管中的物料穿过所述反应釜装置的侧壁引出到所述反应釜装置的外部,再通过支管从所述反应釜装置位于二级反应釜位置的侧壁返回至所述二级反应釜中,进行二级酯化反应,所述二级反应釜底部设有出料口,所述二级反应釜的侧壁上设有第二出气口。
[0013]
进一步的,所述管式加热器,用于为加热管中的物料提供加热,使其满足反应温度的要求,优选的,所述管式加热器设有流入口和出流口,用于有机热载体的进出。
[0014]
优选的,所述二级反应釜外部设有夹套,所述夹套内流动有有机热载体。
[0015]
进一步的,所述支管上设有催化剂进口。
[0016]
进一步的,所述支管位于所述反应釜装置外部的部分,设有阀门,用于控制物料的流量。
[0017]
进一步地,所述循环管位于所述管式加热器下的部分,设置有原料进口,用于向反应体系中补充原料。
[0018]
本实用新型优点:
[0019]
1、本实用新型的外循环多级酯化反应器在装置内设有二个反应釜,并且两个反应釜连为一体,省去了传统酯化工序中,两个反应器的连接设备,也节省了反应釜装置的占地空间;
[0020]
2、本实用新型通过一级反应釜产生的物料持续不断的进行外循环输出,使一级反应釜中的化学反应始终处于不平衡状态,促使一级反应釜中的化学反应持续进行,使原料
转化率大大提高;
[0021]
3、本实用新型通过支管将来自一级反应釜的物料循环进入二级反应釜内,在二级反应釜内继续进行二级酯化反应,进一步提高最终反应产物中目标产物的纯度。
附图说明
[0022]
图1是本实用新型提供的一种外循环多级酯化反应器示意图;
[0023]
如图所述,1-管式加热器,2-连接管,3-一级反应釜,4-内室罩,5-环形导流筒,6-二级反应釜,7-循环管,8-支管,9-外环形导流筒,10-内环形导流筒。
具体实施方式
[0024]
为使本实用新型实施例的目的、技术方案和优点更加清楚,下面将结合本实用新型实施例中的附图,对本实用新型实施例中的技术方案进行清楚、完整地描述。
[0025]
制作对苯二甲酸乙二醇酯的方法:
[0026]
如图1所示,一种外循环多级酯化反应器,包括:反应釜装置和管式加热器1,所述反应釜装置和管式加热器1之间通过管路连接;所述反应釜装置包括一级反应釜3和二级反应釜6,所述一级反应釜3位于所述二级反应釜6上部;所述管式加热器1,用于为管道中的物料提供加热,使其满足反应温度的要求,所述管式加热器1设有入流口和出流口,用于有机热载体的进出。
[0027]
一级反应釜3内部设置有嵌套式的反应腔室,包括,位于所述一级反应釜 3底部中心位置通过内腔筒体围成的环形导流筒5和罩于所述环形导流筒5上部、通过反应外室壁围成的内室罩4;其中,所述环形导流筒5、内室罩4以及所述一级反应釜3的内部空间为连通状态,反应物料能够通过环性流动的方式在各腔室内部流动;所述一级反应釜3的顶部设有排气口,所述内室罩4的顶部设有第一出气口;所述一级反应釜3的底部设有循环管7,所述循环管7穿过所述二级反应釜6的底部将来自所述一级反应釜3的物料通入所述管式加热器1 的底部,所述管式加热器1的侧边通过连接管2与所述一级反应釜3的侧壁连通,将物料循环回所述一级反应釜3;所述循环管7位于所述管式加热器1下的部分,设置有原料进口,用于向反应体系中补充原料。
[0028]
所述二级反应釜6的下部设有外环形导流筒和内环形导流筒,所述外环形导流筒9和所述内环形导流筒10均为夹套结构,可以为反应提供热量,热量来自有机热载体,所述循环管7进入所述二级反应釜6后,分出一根支管8,所述支管8将位于所述循环管7中的物料穿过所述反应釜装置的侧壁引出到所述反应釜装置的外部,再通过支管8从所述反应釜装置位于二级反应釜6位置的侧壁返回至所述二级反应釜6中,进行二级酯化反应,所述二级反应釜6底部设有出料口,所述二级反应釜6的侧壁上设有第二出气口;所述二级反应釜6外部设有夹套,所述夹套内流动有有机热载体;所述支管8位于所述反应釜装置外部的部分,设有阀门,用于控制物料的流量。
[0029]
方案一、制作对苯二甲酸乙二醇酯的方法:
[0030]
原料为苯二甲酸(pta)和乙二醇(eg)以醇酸比1:1.6制成的浆料,并在浆料中加有100ppm/反应产物的ti和sb2o3系复合催化剂,以流量1000kg/hr.,浆料从原料进口加入,管式加热器1出口温度260℃,管式加热器1被310℃的有机热载体进行加热。
[0031]
来自管式加热器1的酯化产物和副产物水,通过连接管2进入一级反应釜 3内,反应温度260℃,压力0.05mpa,反应物在一级反应釜3内进行了闪蒸分离,副产物水和部分乙二醇通过上排气口进入后续的分离塔进行分离,酯化产物依次通过一级反应釜3的内部空间、内室罩4和环形导流筒5,酯化产物进入环形导流筒5继续进行酯化反应,副产物水经过环形导流筒5上部的第一出气口进入一级反应釜3的上部与闪蒸分离的水蒸汽一同从排气口移出;酯化产物通过环形导流筒5呈平推流流动,流入循环管7,与从原料进口进入的原料进行混合后,进入管式加热器1。其中一小部分反应物通过支管8流入二级反应釜6;
[0032]
反应物在流入二级反应釜6后,控制反应温度265℃,压力0.02mpa,经过环形折流板,环形折流板采用夹套结构,反应物在二级反应釜6内环形折流板的引导下,呈平推流流动,在流动过程中被夹套中有机热载体加热,反应物在被加热的条件下继续反应,反应产生的水通过第二出气口引入到分离塔进行分离。
[0033]
在二级反应釜6充分反应的反应物达到酯化率要求后,如:经过离线分析,二级反应釜6的酯化率达到99%,反应物从反应器底部的出料口流出,用泵送入到后续的缩聚工序。
[0034]
方案二、制作己二酸/对苯二甲酸丁二醇酯的方法
[0035]
原料为己二酸、对苯二甲酸和1,4-丁二醇以酸醇比1:1.4制成的浆料,并在浆料中加有150ppm/反应产物的钛酸四丁酯催化剂,以流量1324.0kg/hr.,浆料从原料进口加入,管式加热器1出口温度210℃,管式加热器1被260℃的有机热载体进行加热。
[0036]
来自管式加热器1的酯化产物和副产物水和四氢啡喃(thf),通过连接管 2进入一级反应釜3内,反应温度210℃,压力-10.0kpa,反应物在一级反应釜3 内进行了闪蒸分离,副产物水、thf和部分丁二醇通过上排气口进入后续的分离塔进行分离,酯化产物依次通过一级反应釜3的下部的内室罩4和环形导流筒5,酯化产物进入环形导流筒5继续进行酯化反应,副产物水、thf经过环形导流筒 5上部的第一出气口进入一级反应釜3的上部与闪蒸分离的水蒸汽一同从排气口移出;酯化产物通过环形导流筒5呈平推流流动,流入循环管7,与从原料进口进入的原料进行混合后,进入管式加热器1。其中一部分反应物通过支管8流入二级反应釜6;
[0037]
反应物在流入二级反应釜6后,控制反应温度215℃,压力-20.0kpa,经过环形折流筒,环形折流筒采用夹套结构,反应物在环形折流筒的引导下,呈平推流流动,在流动过程中被夹套中有机热载体加热,反应物在被加热的条件下继续反应,反应产生的水通过第二出气口引入到分离塔进行分离。
[0038]
在二级反应釜6充分反应的反应物达到酯化率要求后,如:经过离线分析,二级反应釜6的酯化率达到98.0%,反应物从二级反应釜底部的出料口流出,用泵送入到后续的缩聚工序。
[0039]
方案三、制作对苯二甲酸丁二醇酯的方法
[0040]
原料为对苯二甲酸和1,4-丁二醇以酸醇比1:1.4制成的浆料,并在浆料中加有150ppm/反应产物的钛酸四丁酯催化剂,以流量1324.0kg/hr.,浆料从原料进口加入,管式加热器1出口温度245℃,管式加热器1被280℃的有机热载体进行加热。
[0041]
来自管式加热器1的酯化产物和副产物水和四氢啡喃(thf),通过连接管 2进入一级反应釜3内,反应温度240℃,压力-30.0kpa,反应物在一级反应釜3 内进行了闪蒸分离,
副产物水、thf和部分丁二醇通过上排气口进入后续的分离塔进行分离,酯化产物依次通过一级反应釜3的下部的内室罩4和环形导流筒5,酯化产物进入环形导流筒5继续进行酯化反应,副产物水、thf经过环形导流筒 5上部的第一出气口进入一级反应釜3的上部与闪蒸分离的水蒸汽一同从排气口移出;酯化产物通过环形导流筒5呈平推流流动,流入循环管7,与从原料进口进入的原料进行混合后,进入管式加热器1。其中一部分反应物通过支管8流入二级反应釜6;
[0042]
反应物在流入二级反应釜6后,控制反应温度250℃,压力-60.0kpa,经过环形折流筒,环形折流筒采用夹套结构,反应物在环形折流筒的引导下,呈平推流流动,在流动过程中被夹套中有机热载体加热,反应物在被加热的条件下继续反应,反应产生的水通过第二出气口引入到分离塔进行分离。
[0043]
在二级反应釜6充分反应的反应物达到酯化率要求后,如:经过离线分析,二级反应釜6的酯化率达到98.5%,反应物从二级反应釜底部的出料口流出,用泵送入到后续的缩聚工序。
[0044]
显然,所描述的实施例是本实用新型一部分实施例,而不是全部实施例。基于本实用新型的实施例,本领域普通技术人员在没有作出创造性劳动前提下所获得的所有其他实施例,都属于本实用新型保护的范围。