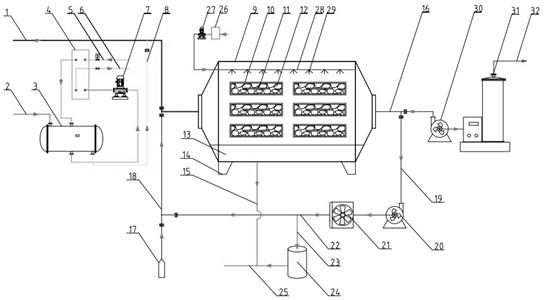
[0001]
本实用新型涉及废气处理技术领域,具体为一种强化可再生的活性炭吸附设备。
背景技术:[0002]
随着近年来废气污染物治理领域的不断革新和发展,在提高技术水平的同时,也伴随着不可避免的二次污染和资源浪费问题。活性炭吸附工艺以其占地面积小、投入成本低、运维简单及效率较高等优势,普遍应用于污水厂及化工厂恶臭气体处理、工业vocs治理等环保领域。但由于活性炭具有一定的饱和吸附量,设备运行达到一定吸附量后,需对活性炭进行整体更换,在造成二次污染的同时,也大大提高了设备运维成本,且活性炭回炉再生的工艺也会造成飞灰等粉尘污染。
[0003]
近年来针对活性炭吸附再生的研究逐年增多,主要为药剂再生法、生物再生法、化学氧化再生法及高温再生法等,为解决以上活性炭解吸再生过程中产生的问题,本实用新型提出一种强化可再生的活性炭吸附设备,通过前端通入臭氧气体,同时提高废气去除效率,并同步氧化活性炭孔道内的小分子有机物,并配套安置蒸汽再生装置,采用低温再生法对活性炭进行定期再生处理,脱附后的蒸汽可冷凝、回收再用,大大降低了运维成本。
技术实现要素:[0004]
为解决现有技术存在的缺陷,本实用新型提供一种强化可再生的活性炭吸附设备。
[0005]
为了解决上述技术问题,本实用新型提供了如下的技术方案:
[0006]
一种强化可再生的活性炭吸附设备,包括臭氧发生单元、活性炭吸附单元、蒸汽再生回收单元、反洗单元以及臭氧破坏单元,所述臭氧发生单元产生的气体通入风管,风管与所述活性炭吸附单元相连,出风管支管与所述蒸汽再生回收单元相连,蒸汽通过回收后与新鲜蒸汽源混合,与进风管相连完成循环,通过反洗系统进行反冲洗,出风管主管与引风机和所述臭氧破坏单元相连。
[0007]
所述臭氧发生器包括循环水泵和板式换热器,循环水通过板式换热器进行冷却降温后,重新打入臭氧发生器中。
[0008]
进一步的,所述臭氧发生器前包含空气过滤器和空气压缩机,采用的气源为空气。
[0009]
进一步的,所述臭氧发生器产生的臭氧通过风管,通过斜插管道连接到进风管,两侧各设置风阀。
[0010]
所述活性炭除臭箱为卧式结构,材质为碳钢。
[0011]
进一步的,活性炭颗粒可选用多种类型和粒径,以适应不同的除臭及再生需求。
[0012]
进一步的,所述活性炭除臭箱为抽屉式,抽屉底部承托板采用孔隙结构钢材,可供蒸汽及反洗水通过,在增大活性炭层之间的间隙同时,也方便检修及更换。
[0013]
进一步的,所述活性炭除臭箱下部设置污水层,用于积存反洗水以及非干燥空气源进入活性炭箱中的水分,保证活性炭填料的干燥度。
[0014]
进一步的,所述污水层下方设置排水口,通过管路与溶剂回收桶的排水管相连。
[0015]
进一步的,所述活性炭除臭箱底部设置支腿,保证箱体底部和地面的距离,一方面方便排水,另一方面可防止渗漏液污染腐蚀箱体底部。
[0016]
所述蒸汽再生回收单元由新鲜蒸汽源、高温风机、冷凝组件及溶剂回收桶组成。
[0017]
进一步的,所述蒸汽再生回收单元由高温风机对蒸汽进行负压收集,支管与出风主管之间通过斜插管道连接,两侧各设置风阀。
[0018]
进一步的,收集到的废蒸汽进入冷凝组件,采用热交换原理将含溶剂蒸气冷凝成液体,进入溶剂回收桶中。
[0019]
进一步的,溶剂回收桶采用防腐材质,桶上方设置水箱盖和检修口,一侧设置出水管及溢流管。
[0020]
进一步的,水蒸气再生温度为150~250℃,循环蒸汽与新鲜蒸汽源混合后在所述活性炭除臭箱内进行循环脱附处理,温度降低至100℃以下时,停止循环。
[0021]
所述反洗单元由反洗水箱、循环水泵以及喷淋管路组成。
[0022]
进一步的,喷淋管路上设置喷嘴,喷嘴材质为陶瓷。
[0023]
所述引风机一侧与所述活性炭除臭箱相连,另一侧出风口连接所述臭氧破坏单元。
[0024]
所述进风管、臭氧出风管、出风主管、新鲜蒸汽源、蒸汽管路(18)、蒸汽回收管道、蒸汽循环管道上均设置风阀开关,控制整个系统的分路运行。
[0025]
与现有技术相比,本实用新型的突出优势为:
[0026]
1. 本实用新型中,采用抽屉式活性炭除臭箱,加大了活性炭层之间的间距,增大气体与活性炭的接触面积,提高处理效率,方便更换活性炭填料及设备内部检修。
[0027]
2. 本实用新型中,采用前置臭氧发生器单元产生的臭氧对未达到吸附饱和的活性炭进行长期脱附,通过将臭氧打入进风管中,可对臭气进行预氧化作用,将大分子有机物分解为小分子有机物,同时还可利用臭氧的强氧化性,对活性炭孔隙结构内的有机气体进行初步的氧化去除。
[0028]
3. 本实用新型中,设置配套的循环蒸汽再生单元,利用热蒸汽作用对活性炭空隙内的有机物进行脱附,采用低温脱附法使小分子有机物随蒸汽进入冷凝组件,还可对其中的有机物进行冷却回收。
[0029]
4. 本实用新型中,首次采用臭氧与蒸汽联用的方式,大大延长了活性炭吸附剂的使用寿命,其中日常使用时可分时段使用臭氧发生器,对活性炭进行持续氧化脱附,还可利用臭氧的强氧化性,提高活性炭除臭箱的除臭效果;当活性炭达到吸附饱和时,可采用配套蒸汽脱附的方式对活性炭进行彻底的再生。
附图说明
[0030]
图1为一种强化可再生的活性炭吸附设备组合装置。
[0031]
图1中:1-进风管,2-空气源,3-臭氧发生器,4-板式换热器,5-循环进水管,6-循环出水管,7-循环水泵,8-臭氧出风管,9-活性炭除臭箱,10-碳钢抽屉,11-把手,12-活性炭填料,13-污水层,14-支腿,15-活性炭箱排水管,16-出风主管,17-蒸汽源,18-蒸汽管路,19-蒸汽回收管道,20-耐高温风机,21-冷凝组件,22-蒸汽循环管道,23-冷却溶剂回收管道,
24-溶剂回收桶,25-废水排水管,26-反洗水箱,27-喷淋水泵,28-反洗喷淋管路,29-喷嘴,30-引风机,31-臭氧破坏装置,32-排风管。
具体实施方式
[0032]
以下结合附图对本实用新型的优选实施例进行说明,应当理解,此处所描述的优选实施例仅用于说明和解释本实用新型,并不用于限定本实用新型。
[0033]
请参阅图1,本实用新型实施例中,一种强化可再生的活性炭吸附设备,进风管1与活性炭除臭箱9进风口相连,臭氧出风管8通过斜插管道与进风管1相连,支管上安装风阀,臭氧出风管8与臭氧发生器3相连,新鲜空气源2通过进风口进入臭氧发生器3,出水口与循环水泵7相连,另一端连接板式换热器4,板式换热器4设置循环进水管5和循环出水管6。
[0034]
活性炭除臭箱9可根据臭气风量和浓度改变尺寸,设置碳钢抽屉10和把手11,抽屉内放入活性炭填料12,可改变不同的粒径和形式,除臭箱9下方设置污水层13,一侧开设活性炭箱排水管15,与废水排水管25相连,除臭箱9箱体最下方设置支腿14,保证箱体下方干燥,上方设置反洗系统,箱体上方安装反洗喷淋管路28和喷嘴29,另一端与喷淋水泵27及反洗水箱26相连。出风口连接出风主管16,出风主管16与引风机30相连,后置臭氧破坏装置31,通过尾气处理后的气体通过排风管32排出。
[0035]
蒸汽再生旁路系统设置新鲜蒸汽源17入口,进入蒸汽管路18与进风管1通过斜插管道相连,管路上设置风阀控制开关,蒸汽回收管道19通过斜插管道与出风主管16连接,支管上安装风阀,蒸汽回收管道19与耐高温风机20连接,另一端连接冷凝组件21,组件设置出风口及出水口,出风口与蒸汽循环管道22连接,回到蒸汽管路18进行循环,出水口连接冷却溶剂回收管道23,进入溶剂回收桶24,溶剂回收桶24设置排水口和溢流阀,与废水排水管25相连。
[0036]
本实用新型的工作原理是:
[0037]
本实用新型运行过程中,空气源2通过前端过滤器和空气压缩机处理后进入臭氧发生器3中,温度升高的循环水通过出水口通过循环水泵7进入板式换热器4,冷却循环水自循环进水管5进入板式换热器4,循环水降温后通过板式换热器4出口回到臭氧发生器3,用于降温的循环冷却水使用后通过循环出水管6排出。
[0038]
臭氧发生器3产生的臭氧通过臭氧出风管8通过斜插管道连接到进风管1,通过支管风阀控制气体开关和通量。采用与进风管相连的方式可对臭气分子进行预氧化作用,裂解臭气中的大分子有机物,使游离状态的污染物分子结合成小分子无害化合物,还可将臭气中一般氧化剂难以破坏的有机物分解,还可降解硫化物、氨、氰化物等。裂解后的小分子有机物通过进风口进入活性炭除臭箱9中,利用活性炭自身独特的孔隙结构和分子之间相互吸附的范德华力吸附臭气中的有机分子。臭氧分子进入活性炭除臭箱9后,可在氧化臭气分子的同时,对活性炭填料12孔隙结构内的有机物进行持续不断的氧化去除,以保证活性炭材料具有持续高效的吸附性能,大大提高了臭气去除效率和活性炭寿命。经o3-bac反应处理后的废气通过出风主管16在引风机30的作用下排出,经过臭氧破坏装置31的尾气处理后,通过排风管32排入大气。
[0039]
在活性炭填料通过多次运行达到饱和吸附后,本实用新型启动蒸汽再生系统,首先新鲜的蒸汽源17进入蒸汽管路18,通过进风管1进入活性炭除臭箱9,同时关闭臭氧系统
风阀,蒸汽进入除臭箱9后通过低温脱附的作用,活性炭孔道内的小分子有机物随着蒸汽作用被脱附带走,通过出风主管16进入蒸汽回收管道19,在耐高温风机20的作用下在管道内循环,经过冷凝组件21后一部分含有机溶剂蒸汽被冷却进入冷却溶剂回收管道23,进入溶剂回收桶24,随活性炭除臭箱9废液一同进入废水排水管25,另一方面一部分蒸汽进入蒸汽循环管道22与新鲜蒸汽源17回到活性炭除臭箱9进行蒸汽循环,同时开启反洗系统,反洗水进入反洗水箱26,在喷淋水泵27作用下打入反洗喷淋管路28,通过喷嘴29对活性炭除臭箱9进行反洗及降温,冲洗活性炭表面有机物残留,并对箱体内蒸汽进行降温,直至蒸汽的温度由150℃降至100℃以下停止循环。
[0040]
最后值得说明的是:以上所述仅为本实用新型的优选实施例,但对其他任何熟悉本技术领域的技术人员来说并不受限,均可在本实用新型记述的技术范围内,对该技术方案机器实用新型构思进行等同替换及更改,凡在本实用新型的精神和原则之内,所作的任何修改、等同替换、改进等,均应包含在本实用新型的保护范围之内。