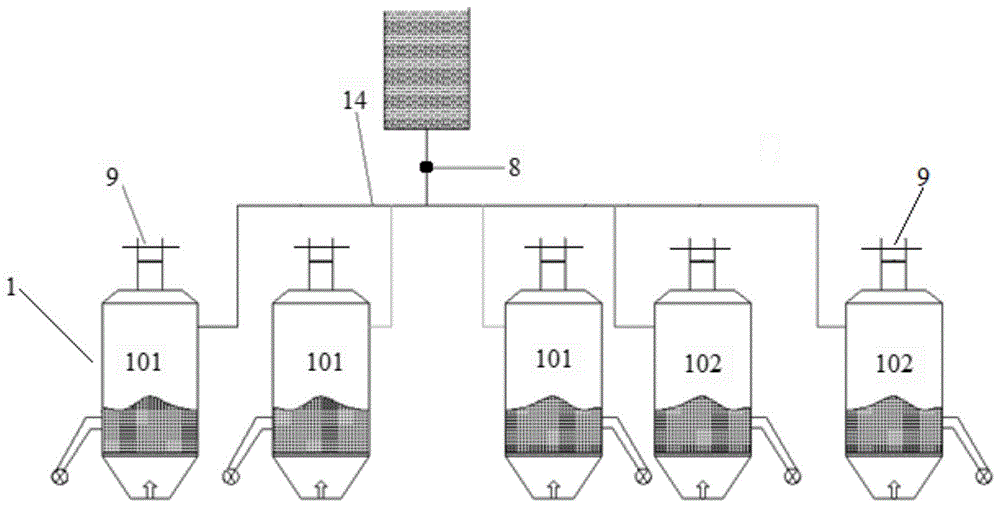
本实用新型涉及活性炭粉尘的净化,具体涉及一种间歇式活性炭粉尘净化系统,属于粉尘净化
技术领域:
。
背景技术:
:活性炭烟气净化技术具有多污染物协同高效净化的优势,适应烧结烟气组分复杂(so2、nox、粉尘、o2、水蒸气、重金属)、温度波动大(110-180℃)的特点,已经成功应用到烧结烟气净化系统中,同时也推广到焦化、电力等多行业中,具备非常好的多污染物去除效果,在当前环保形势极其严峻的条件下,具有很大的推广空间。活性炭烟气净化工艺包括吸附塔、再生塔、输送机三大主题设备,吸附塔塔体有效高度在30m左右,活性炭作为吸附剂与催化剂在吸附塔内完成对污染物的高效吸附,吸附了污染物的活性炭从上往下移动,通过输送系统送往再生塔进行加热再生,活性炭在移动的过程中由于自摩擦、解析磨损的作用,不可避免的产生损坏,由初始的具有完整形态的柱状活性炭变为不同粒径大小的较细活性炭混合物,这些活性炭在解析塔内经过加热再生后经过振动筛筛分去除粒径较小的部分,但不可避免的仍有较细粒径活性炭会进入吸附系统,同时,由于静电效应,大颗粒活性炭表面会覆盖超细炭粉,也会进入吸附系统。现有技术中,对活性炭内普通粉粒体的分级通常是采用筛分法,然而目前最细的筛网孔径也只有20μm左右(即600目左右),而对于直径1μm以上的粒子可通过直接拦截效果进行捕捉。而不到1μm的粒子要通过惯性撞击以及扩散拦截效果进行捕捉。根据上述活性炭的工艺原理,从吸附塔出来的活性炭吸附后,通过直接拦截,惯性撞击以及扩散拦截等过程,活性炭表面及孔隙中夹杂大量粉尘等细微颗粒。进入解析塔后经过高温解析的作用还会产生大量的活性炭超细颗粒,例如不到1μm的粒子。解析之后经过筛分去除了一部分细微颗粒(筛网的孔隙1.2mm),但是附着在活性炭表面及孔隙中的超细颗粒在活性炭的吸附作用下很难去除,导致活性炭烟气净化的粉尘排放浓度较高。这些超细炭粉在吸附塔内会影响系统安全、增加运行成本,同时可能提高出口粉尘含量,因此控制进入吸附塔内的炭粉含量成为活性炭法烟气净化系统运行稳定及高效实现粉尘超低排放的关键。因此,如何降低活性炭烟气净化的粉尘排放浓度,是本领域技术人员亟待解决的技术问题。技术实现要素:针对上述现有技术中存在的问题,本实用新型的目的在于提供一种具有粉尘去除功能的间歇式活性炭粉尘净化系统及其净化方法。本实用新型利用活性炭颗粒流化,采用多个活性炭净化罐,通过多个间歇式净化罐组合来实现活性炭中超细粉尘的连续净化,保证活性炭的粉尘净化效果。根据本实用新型的第一种实施方案,提供一种间歇式活性炭粉尘净化系统。一种间歇式活性炭粉尘净化系统,该系统包括多个并联设置的净化罐。净化罐内的上部设有风洗室,下部设有风腔室。风洗室与风腔室之间设有多孔分布板。净化罐的底部中心位置设有中心布风器。风洗室的侧壁上部设有活性炭进料口,风洗室的侧壁下部设有活性炭排料口。净化罐的顶部设有排烟通道。在本实用新型中,各个净化罐的活性炭进料口分别与活性炭输送管道连接。优选的是,活性炭输送管道上设有温度检测装置。作为优选,所述净化罐包括并联设置的普通净化罐和高温净化罐。优选的是,在各个净化罐顶部排烟通道的烟气出口位置,还设有粉尘浓度检测装置。优选的是,在各个净化罐的活性炭排料口处还设有星型卸料阀。优选的是,在各个净化罐顶部的排烟通道上,且位于粉尘浓度检测装置的上游位置还设有筛板。作为优选,筛板的孔径为1.4~3mm,优选为1.5~2.5mm。优选的是,所述多孔分布板的开孔率为0.2~1.2%,更优选为0.3~1%。优选,多孔分布板的开孔孔径小于3mm,优选为小于1.4mm,更优选为小于1mm。在本实用新型中,该系统包括m个普通净化罐,其中,1≤m≤10,优选为2≤m≤8,更优选为3≤m≤6。在本实用新型中,该系统包括n个高温净化罐,其中,1≤n≤10,优选为2≤n≤8,更优选为3≤n≤6。在本实用新型中,净化罐的布置原则为:系统的活性炭处理量≥单个净化罐的净化量(根据进料量和净化时间计算)×数量×k,k的取值为1~1.5,例如k=1.2,如此设置是为了保证本实用新型的活性炭粉尘净化系统能够满足整个系统的连续净化要求。优选的是,各个净化罐的进料量为该净化罐罐体体积的0.1~0.6,优选为0.2~0.5。作为优选,高温净化罐顶部排烟通道的烟气出口经由烟气输送管道连接至该高温净化罐底部中心布风器的进风口。优选的是,烟气输送管道上还设有烟气除尘装置和循环风机。优选,烟气除尘装置位于循环风机的上游。优选的是,该系统还包括设置在活性炭输送管道上的布料装置,且布料装置位于温度检测装置的下游。作为优选,所述布料装置为旋转布料器。在本实用新型中,该系统还包括设置在净化罐底部的风机。优选的是,所述普通净化罐通过底部的风机和中心布风器布入空气。优选的是,所述高温净化罐通过底部的风机和中心布风器布入氮气。根据本实用新型的第二种实施方案,提供一种间歇式活性炭粉尘净化方法。一种间歇式活性炭粉尘净化方法或使用第一种实施方案中所述的系统来净化活性炭的方法,该方法包括以下步骤:1)底部风机通过中心布风器布风进入各个净化罐的风腔室,风腔室的风再通过多孔分布板自下而上穿过风洗室,形成除尘气流;2)解析筛分后的活性炭通过布料装置依次布入各个净化罐内;3)活性炭进入风洗室与除尘气流均匀接触;控制除尘气流的流速,形成活性炭颗粒的流化状态,实现活性炭中超细粉尘的去除,超细粉尘随着气流从排烟通道排出;4)经过流化风吹后的活性炭从风洗室的活性炭排料口排出,排料完成后,重复步骤2)-4)。优选的是,步骤2)中,解析筛分后的活性炭在布料前先经过温度检测;当温度检测装置检测到的解析筛分后的活性炭温度小于等于165℃,优选小于等于160℃时,该温度下的活性炭通过布料装置进入普通净化罐,普通净化罐内布入空气净化粉尘;反之,相应温度下的活性炭则通过布料装置进入高温净化罐,高温净化罐内布入氮气净化粉尘。优选的是,解析筛分后的活性炭依次布料到各个净化罐内,且各净化罐的进料量为该净化罐罐体体积的0.1~0.6,优选为0.2~0.5。在本实用新型的步骤4)中,粉尘浓度检测装置对各个净化罐顶部排烟通道排出的气流进行粉尘浓度检测;当检测到的粉尘浓度小于等于10mg/s,优选小于等于5mg/s时,即为满足活性炭净化要求,此时打开星型卸料阀进行活性炭卸料;优选,卸料时间为0.5~2min。作为优选,所述控制除尘气流的流速,具体为:控制除尘气流进入风洗室的流速u为:其中:u为除尘气流进入风洗室的流速,d为待去除的活性炭中超细粉尘的粒径,d的取值为1.4~5.6mm,ρ为流体密度,μ为流体黏度,ρp为待去除的活性炭中超细粉尘的密度,g为重力加速度。优选的是,步骤3)中,气流携带超细粉尘经过排烟通道的筛板后,再通过烟气除尘装置除尘后循环至该高温净化罐底部中心布风器的进风口。从普通净化罐顶部的排烟通道排出的气流在经过筛板后经烟气除尘后排放,或,循环至相应普通净化罐底部中心布风器的进风口。在本实用新型中,所述间歇式活性炭粉尘净化系统包括多个并联设置的净化罐,净化罐为箱体或壳体。净化罐内自上而下设有风洗室和风腔室,风腔室设置在净化罐的最下部,风洗室设置在风腔室的上方。风洗室与风腔室之间设有多孔分布板。风洗室的侧壁上部设有活性炭进料口,风洗室的侧壁下部设有活性炭排料口,活性炭进料口位于活性炭排料口的上方。净化罐的顶部设有排烟通道,用于风洗后携带粉尘的气流排出。净化罐的底部中心位置(即风腔室的底部中心位置)设有中心布风器,中心布风器与风机连接,在系统运行时,风机通过中心布风器为系统提供除尘风量。作为优选方案,本实用新型的间歇式活性炭粉尘净化系统还设有温度检测装置和布料装置。系统内各个净化罐的活性炭进料口分别与活性炭输送管道连接,温度检测装置和布料装置设置在活性炭输送管道上,且温度检测装置位于布料装置的上游。同时,所述净化罐包括并联设置的普通净化罐和高温净化罐。解析筛分后的活性炭在进入布料装置之前,先经过温度检测装置进行温度检测,当检测到解析筛分后的活性炭的温度小于等于165℃(超细炭粉的着火点在165℃左右)时,该温度下的活性炭通过布料装置布入普通净化罐;反之,当检测到解析筛分后的活性炭的温度大于165℃时,此时该温度下的活性炭则通过布料装置布入高温净化罐。作为优选,普通净化罐内通过底部风机和中心布风器布入空气来净化粉尘,高温净化罐内则通过底部风机和中心布风器布入氮气来净化粉尘,从而防止进入高温净化罐的活性炭着火燃烧,在净化粉尘的同时保证了生产的安全性。在本实用新型中,所述间歇式活性炭粉尘净化系统还包括设置在各净化罐顶部排烟通道上的粉尘浓度检测装置。所述粉尘浓度检测装置对各净化罐顶部排烟通道排出的气流进行粉尘浓度检测,从而判断相应的净化罐内的活性炭粉尘净化是否满足要求。优选,本实用新型在与各净化罐的活性炭排料口连接的排料通道上还设有星型卸料阀。当某一个或某几个净化罐顶部的粉尘浓度检测装置检测到的粉尘浓度满足净化要求(即粉尘浓度小于等于10mg/s,优选小于等于5mg/s),说明这一个净化罐或这几个净化罐内的活性炭粉尘净化完成,此时打开相应净化罐的排料通道上的星型卸料阀进行活性炭卸料。一般来说,卸料时间为0.5~2min(例如1min),卸料完成后,等待布料装置继续布料,进行进料→风洗→卸料的下一循环。在本实用新型中,为了保证每个净化罐内活性炭的风洗效果,因此设定各个净化罐的进料量为该净化罐罐体体积的0.1~0.5。净化罐的数量为多个,在布料时活性炭通过布料装置依次布入各个净化罐内,即当一个净化罐内的活性炭的进料量达到该净化罐罐体体积的0.1~0.5时,视为该净化罐内布料完成,布料装置再依次布料后续的净化罐。各个净化罐内的进料、风洗或卸料的操作都不是连续进行的,本实用新型通过这样多个间歇式活性炭净化罐组合来实现活性炭中超细粉尘的连续净化。在本实用新型中,净化罐顶部的排烟通道上还设有筛板,筛板用于拦截活性炭流化风洗过程中由于风量控制失常等意外情况带走的大颗粒活性炭。本实用新型的粉尘净化目标在于去除粒径小于等于1.4mm的粉尘,因此,筛板的孔径可设置为1.4~3mm,优选为1.5~2.5mm。进一步优选,在本实用新型中,从高温净化罐顶部排烟通道排出的气流经过烟气除尘后循环至底部中心布风器的进风口,提供部分除尘风量,从而减少氮气的投入成本。在本实用新型中,所述风腔室与风洗室之间设有多孔分布板。为了实现风洗室内气流的均匀分布,所述多孔分布板的开孔率为0.2~1.2%,优选为0.3~1%。结合本实用新型对除尘气流流速的控制,多孔分布板的开孔孔径可设置为小于3mm,优选为小于1.4mm,更优选为小于1mm,在实现除尘气流穿过的同时,又能避免活性炭或者粉尘进入风腔室。需要说明的是,在本实用新型中,活性炭(通过布料装置)布入净化罐之前,先进风,再进料,从而防止活性炭摔破,也便于活性炭更好地形成颗粒流化状态,以去除活性炭粘附的超细粉尘。而解析筛分后的活性炭分布如下表所示。粒径分布/mm≥11.25.6-11.21.4-5.6≤1.4振动筛上料/%074.4250.6本实用新型的粉尘净化目标在于去除占比0.6%的1.4mm以下的粉尘,但不能去除占比74.4%的活性炭颗粒。在本实用新型中,控制进入净化罐内风洗室的除尘气流的流速u为:此处需要说明的是,流速u为使得粒径为d的活性炭超细粉尘颗粒处于流化状态的风速。本实用新型的粉尘净化目标在于去除粒径小于等于1.4mm的粉尘,同时保留粒径在5.6~11.2mm的活性炭,因此,式(1)中的d的取值范围可取1.4~5.6mm,即相应的风速使得1.4~5.6mm的活性炭颗粒处于流化状态以更好的实现气固接触除尘,此时,小于等于1.4mm的粉尘则全部被吹走(从顶部排烟通道排出),5.6~11.2mm的活性炭则被保留,从而保证活性炭粉尘的净化效率。一般,净化罐的高度为4~25m,优选为4.5~20m,优选为5~18m,更优选为6~15m,进一步优选为7~12m。净化罐的外直径一般为4~20m,优选为5~18m,更优选为6~15m。与现有技术相比,本实用新型具有以下有益技术效果:1、本实用新型包括多个并联设置的净化罐,利用活性炭颗粒流化,实现活性炭中超细粉尘的去除,同时保留大颗粒活性炭;2、本实用新型采用多个活性炭净化罐,并控制各个净化罐内的进料量,通过多个间歇式净化罐组合来实现活性炭超细粉尘的连续净化;3、本实用新型设有普通净化罐和高温净化罐,可根据温度检测分别处理活性炭和高温活性炭,从而防止高温活性炭燃烧,导致系统停机;4、本实用新型通过对净化罐顶部排烟通道排出的烟气粉尘浓度测量来评价活性炭粉尘净化情况,结合星型卸料阀来控制停留时间,从而保证活性炭的粉尘净化效果。附图说明图1为本实用新型一种间歇式活性炭粉尘净化系统的结构示意图;图2为本实用新型另一种间歇式活性炭粉尘净化系统的结构示意图;图3为本实用新型中净化罐的结构示意图;图4为本实用新型的活性炭粉尘净化系统用于活性炭烟气处理工艺的流程图。图4中:为降低进入烟气净化系统中的粉尘含量,在活性炭烟气净化工艺上增加了本实用新型的活性炭粉尘净化系统。附图标记:1:净化罐;101:普通净化罐;102:高温净化罐;2:风洗室;3:风腔室;4:多孔分布板;5:中心布风器;6:活性炭进料口;7:活性炭排料口;8:温度检测装置;9:粉尘浓度检测装置;10:星型卸料阀;11:筛板;12:烟气除尘装置;13:循环风机;14:布料装置;l1:排烟通道;l2:活性炭输送管道;l3:烟气输送管道。具体实施方式根据本实用新型的第一种实施方案,提供一种间歇式活性炭粉尘净化系统。一种间歇式活性炭粉尘净化系统,该系统包括多个并联设置的净化罐1。净化罐1内的上部设有风洗室2,下部设有风腔室3。风洗室2与风腔室3之间设有多孔分布板4。净化罐1的底部中心位置设有中心布风器5。风洗室2的侧壁上部设有活性炭进料口6,风洗室2的侧壁下部设有活性炭排料口7。净化罐1的顶部设有排烟通道l1。在本实用新型中,各个净化罐1的活性炭进料口6分别与活性炭输送管道l2连接。优选的是,活性炭输送管道l2上设有温度检测装置8。作为优选,所述净化罐1包括并联设置的普通净化罐101和高温净化罐102。优选的是,在各个净化罐1顶部排烟通道l1的烟气出口位置,还设有粉尘浓度检测装置9。优选的是,在各个净化罐1的活性炭排料口7处还设有星型卸料阀10。优选的是,在各个净化罐1顶部的排烟通道l1上,且位于粉尘浓度检测装置9的上游位置还设有筛板11。作为优选,筛板11的孔径为1.4~3mm,优选为1.5~2.5mm。优选的是,所述多孔分布板4的开孔率为0.2~1.2%,更优选为0.3~1%。优选,多孔分布板4的开孔孔径小于3mm,优选为小于1.4mm,更优选为小于1mm。在本实用新型中,该系统包括m个普通净化罐101,其中,1≤m≤10,优选为2≤m≤8,更优选为3≤m≤6。在本实用新型中,该系统包括n个高温净化罐102,其中,1≤n≤10,优选为2≤n≤8,更优选为3≤n≤6。优选的是,各个净化罐1的进料量为该净化罐1罐体体积的0.1~0.6,优选为0.2~0.5。作为优选,高温净化罐102顶部排烟通道l1的烟气出口经由烟气输送管道l3连接至该高温净化罐102底部中心布风器5的进风口。优选的是,烟气输送管道l3上还设有烟气除尘装置12和循环风机13。优选,烟气除尘装置12位于循环风机13的上游。优选的是,该系统还包括设置在活性炭输送管道l2上的布料装置14,且布料装置14位于温度检测装置8的下游。作为优选,所述布料装置14为旋转布料器。在本实用新型中,该系统还包括设置在净化罐1底部的风机。优选的是,所述普通净化罐101通过底部的风机和中心布风器5布入空气。优选的是,所述高温净化罐102通过底部的风机和中心布风器5布入氮气。根据本实用新型的第二种实施方案,提供一种间歇式活性炭粉尘净化方法。一种间歇式活性炭粉尘净化方法或使用第一种实施方案中所述的系统来净化活性炭的方法,该方法包括以下步骤:1)底部风机通过中心布风器5布风进入各个净化罐1的风腔室3,风腔室3的风再通过多孔分布板4自下而上穿过风洗室2,形成除尘气流;2)解析筛分后的活性炭通过布料装置14依次布入各个净化罐1内;3)活性炭进入风洗室2与除尘气流均匀接触;控制除尘气流的流速,形成活性炭颗粒的流化状态,实现活性炭中超细粉尘的去除,超细粉尘随着气流从排烟通道l1排出;4)经过流化风吹后的活性炭从风洗室2的活性炭排料口7排出,排料完成后,重复步骤2)-4)。优选的是,步骤2)中,解析筛分后的活性炭在布料前先经过温度检测;当温度检测装置8检测到的解析筛分后的活性炭温度小于等于165℃,优选小于等于160℃时,该温度下的活性炭通过布料装置14进入普通净化罐101,普通净化罐101内布入空气净化粉尘;反之,相应温度下的活性炭则通过布料装置14进入高温净化罐102,高温净化罐102内布入氮气净化粉尘。优选的是,解析筛分后的活性炭依次布料到各个净化罐1内,且各净化罐1的进料量为该净化罐1罐体体积的0.1~0.6,优选为0.2~0.5。在本实用新型的步骤4)中,粉尘浓度检测装置9对各个净化罐1顶部排烟通道l1排出的气流进行粉尘浓度检测;当检测到的粉尘浓度小于等于10mg/s,优选小于等于5mg/s时,即为满足活性炭净化要求,此时打开星型卸料阀10进行活性炭卸料;优选,卸料时间为0.5~2min。作为优选,所述控制除尘气流的流速,具体为:控制除尘气流进入风洗室2的流速u为:其中:u为除尘气流进入风洗室的流速,d为待去除的活性炭中超细粉尘的粒径,d的取值为1.4~5.6mm,ρ为流体密度,μ为流体黏度,ρp为待去除的活性炭中超细粉尘的密度,g为重力加速度。优选的是,步骤3)中,气流携带超细粉尘经过排烟通道l1的筛板11后,再通过烟气除尘装置12除尘后循环至该高温净化罐102底部中心布风器5的进风口。实施例1如图1和3所示,一种间歇式活性炭粉尘净化系统,该系统包括多个并联设置的净化罐1。净化罐1内的上部设有风洗室2,下部设有风腔室3。风洗室2与风腔室3之间设有多孔分布板4。净化罐1的底部中心位置设有中心布风器5。风洗室2的侧壁上部设有活性炭进料口6,风洗室2的侧壁下部设有活性炭排料口7。净化罐1的顶部设有排烟通道l1。实施例2重复实施例1,只是各个净化罐1的活性炭进料口6分别与活性炭输送管道l2连接。活性炭输送管道l2上设有温度检测装置8。所述净化罐1包括并联设置的3个普通净化罐101和2个高温净化罐102。各个净化罐1的进料量为该净化罐1罐体体积的0.3。实施例3重复实施例2,只是在各个净化罐1顶部排烟通道l1的烟气出口位置,还设有粉尘浓度检测装置9。实施例4重复实施例3,只是在各个净化罐1的活性炭排料口7处还设有星型卸料阀10。实施例5重复实施例4,只是在各个净化罐1顶部的排烟通道l1上,且位于粉尘浓度检测装置9的上游位置还设有筛板11。筛板11的孔径为1.5mm。实施例6重复实施例5,只是所述多孔分布板4的开孔率为0.5%。多孔分布板4的开孔孔径小于1mm。实施例7如图2所示,重复实施例6,只是高温净化罐102顶部排烟通道l1的烟气出口经由烟气输送管道l3连接至该高温净化罐102底部中心布风器5的进风口。烟气输送管道l3上还设有烟气除尘装置12和循环风机13。烟气除尘装置12位于循环风机13的上游。实施例8重复实施例7,只是该系统还包括设置在活性炭输送管道l2上的布料装置14,且布料装置14位于温度检测装置8的下游。所述布料装置14为旋转布料器。实施例9重复实施例8,只是该系统还包括设置在净化罐1底部的风机。所述普通净化罐101通过底部的风机和中心布风器5布入空气。所述高温净化罐102通过底部的风机和中心布风器5布入氮气。实施例10一种间歇式活性炭粉尘净化方法,使用实施例9中的净化系统,该方法包括以下步骤:1)底部风机通过中心布风器5布风进入各个净化罐1的风腔室3,风腔室3的风再通过多孔分布板4自下而上穿过风洗室2,形成除尘气流;2)解析筛分后的活性炭通过布料装置14依次布入各个净化罐1内;各净化罐1的进料量为该净化罐1罐体体积的0.3;3)活性炭进入风洗室2与除尘气流均匀接触;控制除尘气流的流速,形成活性炭颗粒的流化状态,实现活性炭中超细粉尘的去除,超细粉尘随着气流从排烟通道l1排出;4)经过流化风吹后的活性炭从风洗室2的活性炭排料口7排出,排料完成后,重复步骤2)-4)。实施例11重复实施例10,只是步骤2)中,解析筛分后的活性炭在布料前先经过温度检测;当温度检测装置8检测到的解析筛分后的活性炭温度小于等于165℃时,该温度下的活性炭通过布料装置14进入普通净化罐101,普通净化罐101内布入空气净化粉尘;反之,相应温度下的活性炭则通过布料装置14进入高温净化罐102,高温净化罐102内布入氮气净化粉尘。实施例12重复实施例11,只是步骤4)中,粉尘浓度检测装置9对各个净化罐1顶部排烟通道l1排出的气流进行粉尘浓度检测;当检测到的粉尘浓度小于等于10mg/s时,即为满足活性炭净化要求,此时打开星型卸料阀10进行活性炭卸料。卸料时间为1min。实施例13重复实施例12,只是步骤3)中所述控制除尘气流的流速,具体为:控制除尘气流进入风洗室2的流速u为:其中:待去除的活性炭中超细粉尘的粒径d=2mm=0.002m,空气密度ρ=1.205kg/m3,空气黏度μ=0.00001809pa·s,待去除的活性炭中超细粉尘的密度ρp=1074kg/h,重力加速度g=9.8m/s2;即控制除尘气流进入风洗室2的流速为1.4m/s。实施例14重复实施例13,只是步骤3)中,气流携带超细粉尘经过排烟通道l1的筛板11后,再通过烟气除尘装置12除尘后循环至该高温净化罐102底部中心布风器5的进风口。当前第1页12