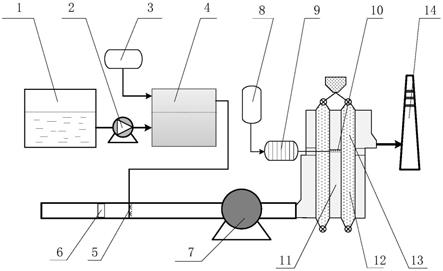
[0001]
本实用新型涉及燃煤电厂、钢厂烧结机、工业锅炉、生物质电厂、垃圾焚烧厂等行业废气进行综合治理的烟气净化领域,具体为一种基于前置氧化的活性焦联合脱硫脱硝系统。
背景技术:[0002]
我国95%以上大型燃煤机组实现超低排放,但治理工艺路线单一,运行成本高,面临迫切的转型需求,一体化脱除和资源化利用是未来发展的方向。与电力行业污染物治理相比,非电行业污染物排放分布广、烟气量小、烟气工况复杂、治理难度大,一体化脱除和低温脱硝技术具有迫切的市场需求。
[0003]
活性焦烟气联合脱硫脱硝技术,可实现多种污染物一体化脱除和硫资源化,并可以在80~150℃范围实现低温脱硝,是我国最具前景的烟气治理技术。活性焦联合脱硫脱硝技术在我国钢铁、冶金等行业有60余套业绩,普遍存在脱硝效率低、运行不稳定等问题。实践表明,活性焦虽可以实现低温脱硝,但反应速度慢、活性焦装填量、脱硝效率低、运行不稳定、催化剂用量大,且受so2、h2o等浓度影响较大。
[0004]
no2反应活性高,通过喷射氧化剂,将no氧化为no2是提升活性焦脱硝效率的重要手段。o3是工程中最常用的no氧化剂,但是o3发生成本高(每产生1kgo3,电耗7~8kwh,o2耗量约10kg,按照商业用电0.7元/kwh计算,单位o3成本约为10500元/吨)、耗量大,工艺中存在o3逃逸,氧化剂利用率低,氧化成本同样较高。h2o2是一种廉价清洁的氧化剂,单位质量成本仅为o3的1/10,且h2o2分子量小,同等摩尔比条件下,质量仅为o3的2/3。在同等摩尔比条件下氧化no,h2o2成本仅为o3的1/15。且h2o2氧化过程只产生o2,不产生二次污染。因此,在no氧化工艺中采用h2o2取代o3,对于降低工艺成本具有重要意义。但在h2o2氧化no工艺中,多采用压缩雾化方式将喷入烟道氧化no,这种工艺氧化效率低,一般小于60%。受限于氧化效率和h2o2喷射量,导致现有技术no
x
脱除效率低,不能满足排放需求。
技术实现要素:[0005]
针对现有技术中存在的问题,本实用新型提供一种基于前置氧化的活性焦联合脱硫脱硝系统,能使活性焦表面低温标准scr反应过程改变为快速scr反应过程,从而降低活性焦用量,提升脱硝效率和运行稳定性。
[0006]
本实用新型是通过以下技术方案来实现:
[0007]
一种基于前置氧化的活性焦联合脱硫脱硝系统,包括设置在烟道上的前置氧化系统、依次设置在烟道出口的吸收系统和烟囱;
[0008]
前置氧化系统包括依次连接的h2o2储罐和超声雾化器,与超声雾化器入口连接的压缩气体罐;超声雾化器的出口接入烟道;
[0009]
吸收系统包括吸收塔;所述的吸收塔采用分段式错流烟气净化吸附塔,包括上下隔离的出气室和进气室,从中间连通出气室和进气室的中间气室;形成中间气室的吸附剂
层内设置活性焦,与进气室对应下段为脱硫段,与出气室对应上段为脱硝段,中间气室内设置喷氨装置;吸收塔的进气室连接烟道出口,出气室连接烟囱。
[0010]
优选的,前置氧化系统还包括依次设置在烟道内的断面混合器和喷射格栅;喷射格栅与超声雾化器出口连接;断面混合器设置在喷射格栅的上游侧。
[0011]
优选的,h2o2储罐和超声雾化器之间设置有输送泵。
[0012]
优选的,吸收塔的烟气入口通过引风机连接烟道出口。
[0013]
优选的,吸收塔内盛装粒径为5~15mm的煤基不定型活性焦。
[0014]
优选的,喷氨装置包括设置在中间气室内的喷氨格栅,以及与喷氨格栅依次连接的氨蒸发器和氨储罐。
[0015]
与现有技术相比,本实用新型具有以下有益的技术效果:
[0016]
本实用新型通过设置前置氧化系统,并采用h2o2为氧化剂替代o3,通过超声雾化和压缩空气携带的雾化方式输送至烟道,相比于压缩空气直接雾化,h2o2分子雾化粒径更小,避免了h2o2蒸发过程中的无效分解,从而降低h2o2氧量,同时将h2o2氧化no效率提升至98%以上,且同等条件下,h2o2氧化成本仅为o3氧化成本的1/15,整个设备简单,投资和运行成本低;同时,吸收系统采用分段式错流烟气净化吸附塔,并采用活性焦为催化剂,通过改变scr反应路径,提升脱硝效率,保证活性焦联合脱硫脱硝系统连续稳定运行,既适用于新建活性焦联合脱硫脱硝工程,又适用于现有活性焦联合脱硫脱硝项目改造,具有重要的应用前景。
[0017]
进一步,本实用新型还通过采用在喷射格栅上游侧设置断面混合器的方式,使h2o2和烟气能充分混合,提高处理效果。
[0018]
进一步,本实用新型采用设置输送泵的方式,将过氧化氢送入超声雾化器,提高了处理效率。
[0019]
进一步,本实用新型通过设置引风机将烟道内的烟气送入吸收塔内,确保吸收塔内的吸收效率。
附图说明
[0020]
图1为本实用新型的结构示意图。
[0021]
图2为h2o2压缩雾化氧化no特性示意图。
[0022]
图3为h2o2超声雾化氧化no特性示意图。
[0023]
图4为基于快速scr反应的活性焦脱硝性能验证示意图。
[0024]
图中:1为h2o2储罐、2为输送泵、3为压缩气体罐、4为超声雾化器、5为喷射格栅、6为断面混合器、7为引风机、8为氨储罐、9为氨蒸发器、10为喷氨格栅、11为吸附塔、12为脱硫段、13为脱硝段、14为烟囱。
具体实施方式
[0025]
下面结合具体的实施例对本实用新型做进一步的详细说明,所述是对本实用新型的解释而不是限定。
[0026]
本实用新型一种基于前置氧化的活性焦联合脱硫脱硝系统,如图1所示,包括前置氧化系统、吸收系统和烟囱三部分。前置氧化系统包括依次连接的h2o2储罐1、输送泵2、超声雾化器4;吸收系统包括吸收塔11、设置在吸收塔11内部下段的脱硫段12、设置在吸收塔11
内部上段的脱硝段13、以及设置在吸收塔11内部中间气室的喷氨格栅10和依次与喷氨格栅10连接的氨蒸发器9和氨储罐10连接。
[0027]
雾化后的h2o2采用压缩气体携带,超声雾化器4入口与压缩气体罐3连接,出口与喷射格栅5连接,喷射格栅5前面设置断面混合器6,用于h2o2与烟气的充分混合。h2o2喷入烟道将no氧化为no2,含有so2和no2气体的烟气经引风机7进入吸附塔11,吸附剂为活性焦,吸收塔11采用分段式错流烟气净化吸附塔,包括上下隔离的出气室和进气室,从中间连通出气室和进气室的中间气室;形成中间气室的吸附剂层内设置活性焦,与进气室对应下段为脱硫段12,与出气室对应上段为脱硝段13,中间气室内设置喷氨装置;其中,下段为脱硫段12,上段为脱硝段13,中间气室内设置喷氨格栅10,喷氨格栅10依次与氨蒸发器9和氨储罐8连接。吸收塔出口与烟囱14连接,净化后的烟气经烟囱14排放。
[0028]
作为本实用新型优选的实施方式,所述的喷射格栅5前设置断面混合器6,用于h2o2和烟气的充分混合;
[0029]
作为本实用新型优选的实施方式,所述的h2o2储罐1和超声雾化器4之间设置有输送泵2;
[0030]
作为本实用新型优选的实施方式,所述的吸收塔11的烟气入口通过引风机7连接烟道出口。
[0031]
在实际应用过程中,通过控制超声雾化器4的功率和压缩气体的流量,控制氧化剂h2o2喷入量,h2o2储罐1和输送泵2用于补充超声雾化器4内h2o2量,在250~500℃条件下,雾化后的h2o2通过喷射格栅5均匀喷入烟道,将no氧化为no2,保证氧化效率>98%;然后含有so2、no2的气体进入吸收塔11,含有so2、no2的气体进入吸收塔11,首先通过脱硫段12脱除大部分so2,脱硫后的烟气与喷氨格栅10喷出的nh3混合,进入脱硝段13通过快速scr反提高脱硝效率,实现so2脱除效率>98%,no2脱除效率>80%。
[0032]
其中,所述喷射格栅5所处位置对应烟气温度为250~500℃;
[0033]
其中,所述h2o2储罐1内h2o2质量浓度为20~50%,h2o2与no摩尔比为1~5;
[0034]
其中,所述h2o2喷射量可以通过所述的超声雾化器4的功率和压缩气体量调节,使脱硝段no和no2比例接近1:1,保证快速scr反应发生。
[0035]
在目前的h2o2氧化no工艺中,采用压缩雾化方式将h2o2喷入烟道氧化no进行脱硫脱硝处理的研究结果,如图2所示,工艺氧化效率低,一般小于60%;而采用本实用新型进行脱硫脱硝处理的研究结果,如图3所示,使h2o2氧化no效率提升至98%以上;
[0036]
同时,在nh
3-scr反应过程中,存在两种反应过程,即标准scr反应过程和快速scr反应过程,反应方程分别如(1)、(2)所示。研究表明,快速scr反应速率在低温段比标准scr至少快10倍,可以显著提升脱硝效率,降低催化剂用量。实用新型人针对活性焦脱硝过程验证了快速scr反应过程,发现当no2占比约为0.5,即no2/no摩尔比为1.0时,脱硝效率达到最大,即快速scr反应效果优于标准scr反应,结果如图4所示。
[0037]
4no+4nh3+o2=4n2+6h2o (1)
[0038]
no+no2+2nh3=2n2+3h2o (2)
[0039]
基于以上研究结果,本实用新型提出一种基于前置氧化的活性焦联合脱硫脱硝系统,即采用h2o2为氧化,提升一定比例的no氧化为no2,通过改变活性焦表面标准scr反应过程为快速scr反应过程,提升脱硝效率。