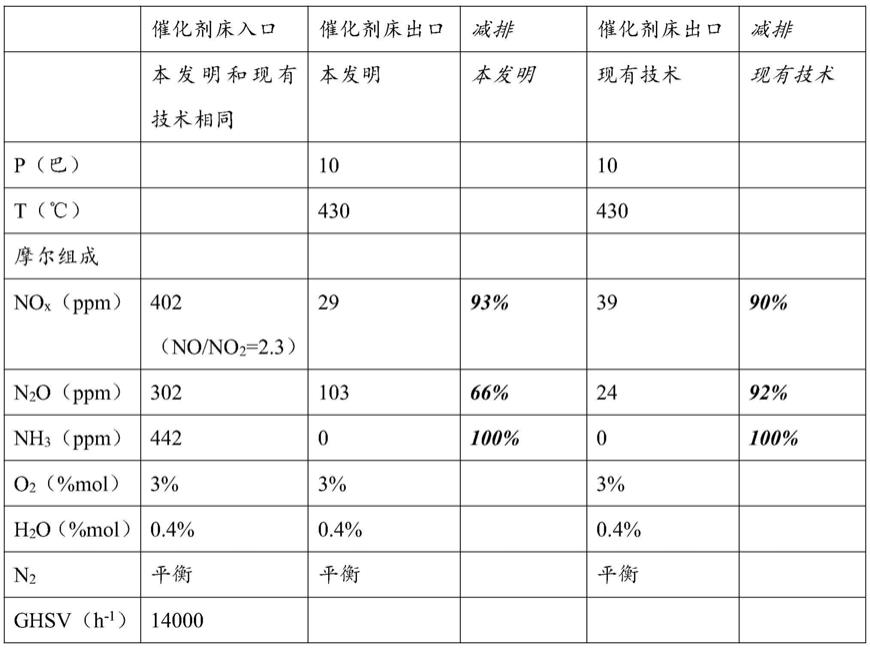
1.本发明涉及通过选择性催化还原从气流中去除氮氧化物(no
x
)。
背景技术:2.出于环境原因,需要减排气流中所含的no
x
。符号no
x
和术语“氮氧化物”通常用于表示单氮的氧化物,即一氧化氮(no)和二氧化氮(no2)。已知上述氮氧化物会危害环境并且是强效温室气体。某些情况下,可能还需要去除一氧化二氮(n2o),可能与去除no
x
结合进行。
3.要去除的含有no
x
和可能含有n2o的气流源自燃烧过程和若干行业的工艺。一个值得注意的例子是硝酸的生产,其中会产生含no
x
的尾气。通常,例如根据适用于气体排放的法律的要求,必须将净化后的气体中氮氧化物和n2o去除到目标水平以下。
4.通过选择性催化还原(scr)去除no
x
是基于在合适的催化剂的存在下以及可能在还原剂的存在下,将氮氧化物还原为环境可接受的化合物。适用于scr的催化剂被称为“脱no
x
催化剂”。常见的还原剂为氨,并且使用氨作为还原剂的选择性催化还原通常被称为“氨scr”。在氨scr过程中涉及的反应被称为“氨scr反应”。
5.通常,scr过程通过将气体通过一个或多个转化器中的一个或多个催化床来进行。可以例如通过将液态或气态氨注入转化器上游的气流中或直接注入转化器中来提供氨。在多床工艺中,氨可以在中间阶段注入,例如在第一个催化床的流出物进入后续催化床之前,将其添加到所述第一个催化床的流出物中。
6.在氨scr中,可能需要过量的氨。术语过量的氨是指相对于在氨scr反应中与no
x
反应的化学计量的量而言氨是过量的。需要供给过量的氨以实现非常低的no
x
残留排放,例如小于40ppm(如20ppm)。在存在过量氨的情况下,一个问题是要避免氨泄漏,即未反应的氨从过程中逃逸并保留在纯化后的气体中。由于在气体冷却时氨可能与残留的no
x
形成硝酸铵,因此氨泄漏会在下游操作中造成爆炸的风险。
7.催化no
x
减排的现有技术主要依赖于以下脱no
x
催化剂的选择:
8.v2o5/tio2‑
wo3钒脱no
x
催化剂;
9.cu
‑
ssz13、cu
‑
zsm
‑
5铜沸石脱no
x
催化剂;
10.fe
‑
fer、fe
‑
zsm5、fe
‑
bea、fe
‑
y载铁沸石脱no
x
催化剂;
11.pt/al2o3铂负载氧化铝脱no
x
催化剂;
12.ce/tio2铈负载二氧化钛脱no
x
催化剂;
13.cu/ceo2铜负载二氧化铈脱no
x
催化剂。
14.在合适的还原剂如氨的存在下,所有上述催化剂均对还原no
x
有效。然而,它们也有缺点。
15.钒和铜沸石脱no
x
催化剂对于n2o减排无效,在典型的氨scr条件下运行时,甚至导致形成大量n2o副产物。因此,它们通常是不期望的,并且在以非常低的no
x
和n2o排放水平为目标时是不适用的。
16.在氨scr中,钒脱no
x
催化剂的另一个缺点是其不催化除scr之外的涉及氨的反应。
因此,它会让任何过量的氨从催化剂床中泄漏。
17.载铁沸石脱no
x
催化剂被认为是目前从硝酸尾气中减排no
x
和n2o最为先进的。例如,沸石可以是镁碱沸石(fer)型或fmi型(例如zsm
‑
5沸石)的沸石。
18.载铁(也称为含铁或铁交换)沸石表示这样的催化剂,其中有目的地将铁(fe)通过离子交换程序负载到沸石载体中。在该步骤中,消耗性元素/离子在沸石载体的位点处被fe离子替代。结果是铁在整个载体中均匀分布。铁交换过程可以在原始沸石粉末上即催化剂成型前进行,或在原始沸石粉末成型后(例如以粒料挤出)进行。
19.根据目前的技术和文献,沸石的铁负载被认为是确保催化剂适当的减排活性的必要步骤,尤其是对于并行的no
x
和n2o。据称,铁是减排no
x
和n2o的活性材料,并且单体形式的铁在较低温度下具有活性。文献中提出的关于fe
‑
沸石的脱n2o和脱no
x
机制均基于fe
iii
和fe
ii
氧化还原循环,其中吸附氧的解吸作为速率决定步骤。文献数据指出,沸石中的铁为相关反应中的活性物种。
20.载铁沸石催化剂的缺点是成本高。催化剂的成本主要来自于昂贵的铁负载(离子交换)过程。这个过程需要大量的原材料(待交换的铁的前体);该过程产生需要额外费用处理的废水;该过程需要专用的设备项目。此外,该过程对参数非常敏感,必须在严格控制的条件下进行。这增加了催化剂的制造成本。
21.us 2008/0044331公开了一种在载铁沸石催化剂的存在下降低气体中no
x
和n2o含量的方法。
技术实现要素:22.本发明旨在提供一种用于降低气体中no
x
含量的高效且具有成本效益的scr方法。
23.该目标通过降低源气体中氮氧化物(no
x
)含量的方法实现,包括在还原剂的存在下使所述源气体通过适用于no
x
选择性催化还原的催化剂,其中所述催化剂为沸石催化剂,所述催化剂的沸石为未负载有铁且未负载有任何过渡金属的fer沸石。
24.根据权利要求,本发明的另一方面为用于脱no
x
过程的催化剂。
25.所述方法和所述催化剂的优选实施方案在从属权利要求中陈述。
26.本发明的方法使用镁碱沸石(fer)沸石催化剂,其中所述fer沸石未负载铁。
27.所述fer沸石催化剂为可通过这样的方法获得的催化剂,其中不将铁和过渡金属负载到沸石中。特别地,在所述催化剂的制造过程中,不进行将铁或任何过渡金属负载到沸石结构中的离子交换程序。
28.术语过渡金属表示元素周期表第4周期、第5周期、第6周期中的任何元素。在一个优选的实施方案中,所述沸石未负载有周期表第4周期的元素,更优选未负载有fe、cu、v、ni、co和mn中的任一种。
29.所述fer沸石可以负载有至少一种碱金属。为此目的,优选的碱金属为钠和钾。例如,在一个优选的实施方案中,使所述fer沸石与na2o和k2o进行交换过程。因此,用于本发明的fer沸石不含离子交换的铁。尽管未负载有铁,根据本发明的催化剂的fer沸石可含有少量铁,然而其形式与在载铁沸石中存在的离子交换的铁不同。特别地,本发明的催化剂可含有铁的杂质,其通常具有铁的聚集物(agglomerate)的形式;相反,离子交换的铁为与沸石结合的铁原子的形式。
30.与大多数载铁沸石的铁含量相比,根据本发明的催化剂中的铁含量也可以更小。
31.在根据本发明的催化剂中,铁可以例如fe2o3的形式存在。在根据本发明的催化剂中,由于在制造过程中缺少适当的fe
‑
交换步骤,铁(例如fe2o3)可以与在载铁沸石中所见的均匀分散相反地非均匀分散。铁也可以作为沸石结构中的微量杂质被检测到。也可能存在痕量的过渡金属。
32.在一个优选的实施方案中,所述fer
‑
沸石催化剂不含铋。
33.本发明基于如下非常出乎意料的发现,即无铁负载的fer沸石催化剂表现出与更昂贵的载铁沸石催化剂可比较(或甚至更好)的脱no
x
活性。这一发现与当前认为铁负载是沸石催化剂脱no
x
活性的原因的观点相反。申请人已经发现,与载铁沸石催化剂相比,根据本发明的催化剂对于n2o减排的活性往往较低。然而,这种对于n2o减排的活性的降低,被以低得多的成本实现对于no
x
减排可比较的活性这一优势所充分补偿。脱n2o性能可以通过对操作参数进行微调而达到相同的接近完全的减排水平,从而与载铁沸石相匹配。没有检测到氨的泄漏。由于在制造过程中未负载有铁或过渡金属,本发明的催化剂可以以具有竞争力的成本获得。
34.本发明的催化剂优选地包含无机粘合剂材料。优选的无机粘合剂包括al2o3、sio2、zro2、ceo2。优选的粘合剂浓度为10%至30%wt。优选的fer沸石类型的si/al比大于6。所述比率更优选在8至9的范围内,最优选为8.8或约8.8。这些优选实施方案显示了机械稳定性和化学活性之间最佳的折衷方案。
35.根据本发明的实施方案,n2o的去除也可以与no
x
的去除并行进行或单独进行。
36.必须注意,根据本发明的fer
‑
沸石本身即是用于从源气体中去除no
x
和可能的n2o的催化剂,即所述fer
‑
沸石不仅仅是催化剂的载体。优选地,所述fer
‑
沸石在不进行预处理的情况下对于去除no
x
和可能的n2o具有活性。
37.优选地,仅在本发明的fer
‑
沸石的存在下,即在没有任何其他催化剂的情况下,进行去除no
x
的过程(以及可能的并行去除n2o的过程)。
38.本发明适用于去除no
x
的方法以及去除no
x
和n2o的方法(例如并行的no
x
还原和n2o分解)。源气体可以是烟道气,例如燃烧过程产生的气体,或在进一步使用之前或排放到大气中之前需要no
x
和可能的n2o减排的另一种工艺气体。本发明的一个引人注意的应用涉及硝酸生产过程中尾气的处理。
39.根据本发明的方法可以在与使用载铁fer沸石催化剂的方法类似的温度、压力、空速和组成下进行。本发明能够使no
x
和n2o的目标浓度达到低至50ppm。
40.本发明也适用于改造程序,例如硝酸工厂的改造。可能需要改造硝酸工厂以满足排放至大气的尾气中no
x
和n2o的目标浓度。
具体实施方式
41.根据本发明的降低源气体中氮氧化物(no
x
)含量的方法可以在包括一个催化床或多个催化床的脱no
x
阶段中进行。所述一个或多个催化床可含于一个压力容器或多个压力容器中。在多床的实施方案中,根据不同的实施方案,两个或更多个床可含于同一压力容器中或每个催化床可具有单独的容器。本发明中使用的任何催化床可以具有轴流、径向流、轴
‑
径向混合流中的任一种。
42.根据本发明的方法在还原剂的存在下进行。优选地,所述还原剂为含氮的还原剂。特别优选地,所述还原剂是或包括氨。所述还原剂优选为气态。氨可以超过用于还原no
x
的化学计量的量。
43.根据本发明的方法可包括添加含氨还原剂的步骤。优选地,添加的还原剂中所含的氨与源气体中所含的no
x
的摩尔比为0.5至2.5,优选为0.8至2.0,更优选为0.9至1.5。
44.例如,根据一个实施方案的方法可以包括提供与源气体接触的至少一股含氨还原剂的料流的步骤。含氨还原剂可在进入催化床之前与源气体混合。在多床的实施方案中,所述还原剂可以在中间步骤添加,例如在第一个催化床的流出物进入下一个催化床之前添加到该流出物中。
45.根据本发明的方法可以包括在进行该方法的一个或多个催化床中设置适当的空速。基于相关气体流速和催化剂体积,优选地,通过含有根据本发明的催化剂的催化床的空速为5000至50000(5
×
103至50
×
103)h
‑1,优选为7000至25000(7
×
103至25
×
103)h
‑1。
46.所述方法的温度优选高于300℃。压力通常可在1至50巴的范围内。
47.优选地,所述源气体的温度不高于500℃,更优选地在200℃至500℃的范围内,或者甚至更优选地在300℃至500℃的范围内。因此,去除no
x
的过程在500℃或更低,优选在200℃至500℃或300℃至500℃下进行。特别优选的范围为380℃至450℃。
48.因此,根据本发明的fer
‑
沸石催化剂在上述温度范围内对于去除no
x
可具有活性。根据本发明的方法还可包括降低源气体中n2o含量的步骤。可以在去除no
x
之前或之后进行去除n2o的步骤。在同一催化床中,n2o的去除也可以与no
x
的去除并行进行。特别地,一个实施方案包括通过使含no
x
和含n2o的气体通过未负载有铁和过渡金属的催化剂来并行去除no
x
和n2o。这可以在一个或多个含有所述催化剂的催化剂床中完成。
49.因此,根据本发明的fer
‑
沸石催化剂对于no
x
和n2o的并行去除可具有活性。特别优选地,所述fer
‑
沸石催化剂在不高于500℃、优选200℃至500℃、更优选300℃至500℃、甚至更优选380℃至450℃的温度下对于no
x
和n2o的并行去除可具有活性。
50.在本发明的各种实施方案中,去除no
x
和可能的n2o的过程可以在一个或多个仅含有本发明催化剂的催化剂床中进行,其中所述fer沸石催化剂是在没有铁负载和过渡金属负载的情况下获得的。
51.n2o的去除也可在n2o分解催化剂的存在下进行。所述n2o分解催化剂可以是与脱no
x
过程所用相同或不同的催化剂。所述n2o分解催化剂可以是常规的载铁沸石催化剂或未负载有铁和过渡金属的根据本发明的fer沸石催化剂。已知n2o的分解在铁沸石催化剂存在下发生。在上述现有技术us 2008/0044331中从[0030]开始给出了n2o分解的可能解释。如上所述,申请人已经注意到,根据本发明的催化剂也具有显著的脱n2o活性。
[0052]
当对n2o也进行去除时,优选去除所述源气体中初始含有的n2o的至少10%,更优选至少30%,甚至更优选至少50%。
[0053]
用于去除no
x
和n2o的方法的又一个实施方案包括脱n2o阶段及其后的脱no
x
阶段,中间添加含氨还原剂。为此,将一个或多个脱n2o催化床(脱n2o阶段)布置在一个或多个脱no
x
催化床(脱no
x
阶段)的上游。该实施方案(先脱n2o的设置)的优点是节省了n2o分解催化剂,因为在脱no
x
阶段还发生进一步的n2o减排,直至目标n2o减排水平。
[0054]
在先脱n2o的设置中,优选的特征是在脱n2o阶段中去除n2o不超过90%,优选不超
过80%。这样的优点是n2o的残留含量有助于在随后的脱no
x
阶段中破坏no
x
。
[0055]
另一实施方案包括脱n2o阶段在脱no
x
阶段下游(先脱no
x
的设置)。特别是当脱no
x
催化床和脱n2o催化床含于同一压力容器(双床反应器)中时,脱no
x
床处于在先位置是有利的。在这种情况下,还原剂和工艺气体的混合可以在压力容器外进行;所述双床反应器的体积较小,且该反应器的构造较为简单。
[0056]
包括去除n2o的方法也可包括添加n2o还原剂。所述n2o还原剂可包括碳氢化合物、一氧化碳(co)、氢(h2)或其混合物。
[0057]
本发明的一个特别优选的应用涉及硝酸生产过程中尾气的处理。
[0058]
合成硝酸的工业过程涉及氨的催化氧化以产生含有n2o和氮氧化物的气体。氨的所述氧化通常在铂
‑
铑(pt
‑
rh)催化网上进行。将如此获得的气体进行随后的吸收步骤,其中使所述气体与水接触以在水中吸收no2并产生硝酸,而n2o不被吸收。所述吸收步骤在吸收器(通常为吸收塔)中进行。所述吸收步骤输送含硝酸的液体产品料流以及含n2o和残留no
x
的气体,该气体被称为尾气。所述尾气处于高于大气压的压力下,并且可以在排放到大气中之前在合适的膨胀器中做膨胀功以用于能量回收。可能需要从尾气中减排no
x
和n2o,以满足适用的环境要求。
[0059]
在尾气膨胀器上游的n2o和no
x
减排被称为三级减排。n2o在硝酸的形成中没有作用,因此也可以在前面的工艺步骤中去除。在氨氧化之后和吸收阶段之前从气体中去除n2o被称为二级减排,而旨在避免氨氧化过程中形成n2o的措施被称为一级减排。在膨胀之后(即膨胀器的下游)进行的n2o和/或no
x
减排被称为四级减排。
[0060]
根据本发明的去除no
x
的方法可以在吸收器下游的三级或四级位置,即分别在尾气膨胀器的上游或下游进行。三级减排是优选的,因为其能够使用粒料催化剂而非整料。
[0061]
本发明的脱no
x
催化剂可以通过例如以下中的任何一种来生产:与添加剂和/或粘合剂共挤出,或者原材料的3d打印,或者粘合剂和沸石的共沉淀。
[0062]
所述催化剂可以成型为不同的形式,其取决于应用(例如硝酸工艺中的三级与四级减排),这也可能影响催化性能(活性)。
[0063]
所述催化剂可以为粒料形式或者整料或泡沫。所述催化剂的形状优选为圆柱形或多叶形挤出物;特别优选的形状为三叶形。优选三叶形的原因是其比单叶形的扩散限制更低,因此具有更高的活性。并且,申请人已经发现,三叶形是活性和机械阻力之间特别优选的折衷方案。所述挤出物的尺寸优选为约2mm外径
×
10mm长度。
[0064]
制备本发明的催化剂的方法可包括以下步骤:i)提供原料,例如al、si和na的前体;ii)混合和水热处理得到粉末;iii)与粘合剂和添加剂混合;iv)挤压成最终形状,例如粒料。所述方法不包括用铁负载沸石的任何步骤,例如离子交换。
[0065]
将根据优选实施方案的fer沸石与0.1%wt的na2o和0.6%wt的k2o进行交换。在离子交换过程之后,在该沸石中观察到最终含量为约0.1%wt的na和约0.5%wt的k。
[0066]
以下为根据本发明的未负载铁的fer沸石催化剂的示例性组成。
[0067][0068]
实施例
[0069]
下表1对使用根据本发明具有上述示例性组成的催化剂并行减排no
x
和n2o的方法和使用常规载铁fer沸石催化剂(铁镁碱沸石催化剂)并行减排no
x
和n2o的现有技术方法进行了比较。所述常规催化剂为含有如下的fe
‑
fer催化剂:fe 0.54%;k 0.13%;na 0.26%;mg<0.05%;si 22.7%;al 3.8%(%wt)。
[0070]
在具有单个催化床的实验室规模的试验车间中进行测试。氨作为还原剂进料,nh3/no
x
比约为1.1(即氨过量10%)。进料条件为具有上游n2o减排的硝酸工厂的典型条件,例如三级n2o减排步骤或二级n2o减排步骤。针对no
x
还原和并行的n2o减排对工艺条件进行了优化。在下表中,符号ppm表示以体积计的百万分之几;符号ghsv表示测试催化剂床中的气时空速。
[0071][0072]
表1
[0073]
该实施例表明:本发明的no
x
减排比现有技术的更高,为93%比90%。本发明方法的n2o减排低于现有技术,为66%比92%。尽管如现有技术中进料过量10%,本发明方法没有氨泄漏。