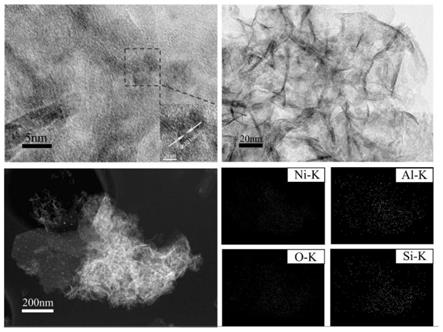
1.本发明属于能源化工领域,尤其涉及一种高活性、高稳定性担载镍催化剂及其制备方法和应用。
背景技术:2.储氢技术是实现氢能使用的关键,有机液体储氢技术相比传统储氢技术有众多优势。液体有机储氢最大的特点就是常温下这些有机液体储氢材料一般为液态,类似于汽油,能够直接使用现有的基础设施,方便运输和储存氢能。然而目前对有机液态储氢材料的加氢一般使用的为ru基催化剂,这类催化剂价格昂贵,提高了有机液体储氢技术的成本,极大限制了有机液体储氢技术的发展。
3.研究开发非贵金属催化剂替代贵金属催化剂应用于有机液态储氢(lohcs)技术中的氢化反应对于降低成本,推广液态有机储氢技术具有重大意义。镍催化剂具有活性高、价格低廉等优点,被广泛应用于加氢反应。但是镍负载氧化物用于有机液态储氢材料的加氢反应很少报道。共沉淀法是将催化剂所需的多种组分同时沉淀的一种方法,常用于制备高含量的多组分催化剂。例如南京大学沈俭一等人在cn 105618058 a专利中报道了共沉淀法制备高含量的ni基催化剂对葡萄糖水溶液加氢制备山梨醇中具有良好的催化活性。如cn 101733106 a、cn 104084209 a专利所报道的催化剂制备方法,一般情况下,共沉淀法制备催化剂时,在得到沉淀前驱体后通常采用直接煅烧还原的方式。但是,沉淀形成的过程中金属与阴离子形成的各类金属盐会直接沉积在催化剂前驱体内部,直接使用干燥后的沉淀会导致金属难以还原,从而降低金属的利用率。同时,直接还原的方法制备的催化剂粒径较大且分布不均会显著影响催化剂的活性。已有文献报道(现代化工,2018年第38卷,87
‑
92页)在催化剂制备过程中经过水热处理后,催化剂的孔容孔径比表面积会显著增大,活性中心的密度增加,催化活性提高。因此,本制备方法将两者结合,在共沉淀的基础上采用水热处理法对沉淀进行6h水热处理,采用较低的氢气压力保证了沉淀不会生成难以还原的镍盐。所制备的催化剂具有较小的粒径分布和粒径大小,金属镍的晶型优异,分散良好。此外,复合氧化物相比于单一氧化物具有独特的物理和化学性质,较大的孔径和比表面积保证了ni能够在载体上均匀分散,同时引入稀土la元素有利于催化剂的稳定性。
技术实现要素:4.为了解决上述技术问题,本发明提供一种高活性、高稳定性担载镍催化剂及其制备方法和应用。
5.为达上述目的,本发明采用如下的技术方案:
6.一种高活性、高稳定性担载镍催化剂,该催化剂以al2o3‑
sio2‑
la2o3或者此三种氧化物中任意两种氧化物形成复合氧化物为载体,以金属镍为活性组分,催化剂的比表面积为100
‑
500m2/g、孔容为0.2
‑
1.4cm3/g、孔径为5
‑
25nm,催化剂中载体中的al
‑
si
‑
la的摩尔比为任意值,镍的总含量为30
‑
90wt%,催化剂ni金属粒径为5
‑
15nm。
7.该催化剂的制备过程如下:
8.(1)称取一定量的a、b、c中的两种以上物质溶解于去离子水中,形成溶液a’,称取一定量的d和/或e,溶解于去离子水中,形成溶液b’,称取f溶解在去离子水中形成溶液c’;
9.(2)在80
‑
90℃水浴条件下将溶液a’和溶液b’同时缓慢滴加到溶液c’中,不断搅拌,形成浅绿色沉淀,过滤沉淀后不断用去离子水和无水乙醇洗涤沉淀,直至洗出液呈中性;
10.(3)将步骤(2)中所得沉淀分散在无水乙醇中,在110
‑
150℃油浴条件下将水和无水乙醇共沸蒸发;
11.(4)将步骤(3)中所得沉淀分散在去离子水中形成悬浊液,在反应釜中通入0.5
‑
1.2mpa氢压,以120
‑
150r/min,温度为130℃
‑
170℃还原5
‑
8h形成催化剂前驱体,然后抽滤,用去离子水和无水乙醇洗涤,放入40
‑
70℃烘箱中干燥4
‑
6h;
12.(5)研磨成粉末后将催化剂在管式炉中通入惰性气体和h2混合气体,升温到420
‑
800℃,混合气气流量为40
‑
80ml/min,还原5
‑
12h,关闭混合气,放置冷却,即得到担载镍催化剂;
13.所述a为ni(no3)2·
6h2o、nicl2·
6h2o或niso4·
6h2o;
14.所述b为al(no3)3·
9h2o或al2(so4)3;
15.所述c为la(no3)3·
6h2o或lacl3·
7h2o;
16.所述d为na2sio3·
9h2o或k2sio3;
17.所述e为na2co3、nahco3或naoh;
18.所述f为peg2000、peg200、peg600或peg20000。
19.进一步的,所述步骤(3)中油浴为120℃。
20.进一步的,所述步骤(4)中氢压为1mpa。
21.进一步的,所述步骤(4)中还原时间为6h。
22.进一步的,所述步骤(4)中烘箱干燥温度为50℃。
23.进一步的,所述步骤(5)中ar/h2混合气体中氢气的体积分数为10%。
24.进一步的,所述步骤(5)中还原温度为450℃。
25.进一步的,所述步骤(5)中还原时间为6h。
26.本发明提供的ni基催化剂具有活性高、价格低廉等优点。选择过渡金属ni作为活性组分制备非贵金属催化剂替代ru基催化剂能够极大的降低催化剂的成本,同时采用共沉淀的方法一方面可以将ni的载量提高到30wt%以上,另一方面又减少镍的团聚,增加了ni的分散,镍颗粒粒径控制在纳米级别。此工艺简便,设备要求较低,所制得催化剂对有机液体储氢材料的加氢同样具有较高的活性和稳定性。
27.本发明还提供了所述担载镍催化剂在有机液体储氢材料加氢反应中的应用。
28.进一步的,所述应用为反应在高温高压反应釜中进行,实验过程为:通入纯氢气将反应釜内空气排空(避免反应过程发生爆炸),将反应釜加热到130
‑
160℃,通入氢气,开始反应并每隔一段时间取样测试其反应速率,反应温度为130
‑
160℃,氢气压力为5
‑
8mpa,反应转速为400
‑
600r/min。
29.与现有技术相比,本发明具有如下有益效果:
30.(1)本发明制备的担载ni催化剂可应用于有机液体储氢材料的加氢反应,催化活
性高且稳定性良好,能够多次重复使用。
31.(2)本发明制备的催化剂为非贵金属催化剂,不添加贵金属,极大降低了催化剂的成本。
32.(3)本发明高载量的ni在载体上仍具有良好分散性,ni粒径保持在纳米级别。
33.(4)本发明合成工艺简单,设备要求较低,能够大规模生产应用。
附图说明
34.图1为实施例1中催化剂的x射线衍射分析表征图。
35.图2为实施例1中催化剂的透射电镜及元素映射图。
36.图3为对比例3中5种催化剂催化苯加氢活性对比图。
37.图4为对比例4中8种催化剂催化n
‑
正丙基咔唑(npcz)加氢对比图。
38.图5为对比例5中2种催化剂催化乙基咔唑(necz)加氢对比图。
39.图6为对比例6中2种催化剂催化二苄基甲苯(dbt)加氢对比图。
40.图7为实施例5中催化剂的透射电镜图。
41.图8为实施例11中催化剂重复5次催化n
‑
正丙基咔唑吸氢速率图。
具体实施方式
42.以下对比例中所使用的商业0.5wt%ru/al2o3催化剂购自陕西开达化工有限公司,分析纯ar。
43.实施例1
44.称取17.263gni(no3)2·
6h2o和5.068gal(no3)3·
9h2o,溶解于100ml的去离子水中,命名为溶液a’。称取3.837gna2sio3·
9h2o和8.755g的na2co3,溶解于100ml的去离子水中,命名为溶液b’。称取0.5gpeg2000溶解在200ml去离子水命名为溶液c’。在90℃水浴条件下将溶液a’和溶液b’同时缓慢滴加到溶液c’中,不断搅拌,形成浅绿色沉淀,过滤并不断用去离子水洗涤沉淀,直至洗出液呈中性,然后将沉淀分散在150ml无水乙醇中,在120℃油浴条件下将水和乙醇共沸蒸去,然后将沉淀分散在200ml去离子水中形成悬浊液,在高温高压反应釜中通入1mpa氢压,以120r/min,温度为150℃还原6h形成催化剂前驱体,然后抽滤,用去离子水和无水乙醇洗涤,放入50℃烘箱中干燥4h,研磨成粉末后将催化剂在管式炉中ar/h2混合气(h2体积含量10%),以3℃/min的升温速率升到450℃,混合气气流量为60ml/min,还原6h,关闭ar/h2混合气(h2体积含量10%),在管式炉中放置冷却24h,得到ni
70
/al1si1la0o(表示ni载量为70,al/si/la摩尔比为1/1/0)的担载镍催化剂,该催化剂的x射线衍射分析表征图如图1所示,其透射电镜及元素映射图如图2所示。
45.实施例2
46.称取17.263gni(no3)2·
6h2o和2.435gal(no3)3·
9h2o,溶解于100ml的去离子水中,命名为溶液a。称取5.532gna2sio3·
9h2o和8.735g的na2co3,溶解于100ml的去离子水中,命名为溶液b。称取0.5gpeg2000溶解在200ml去离子水命名为溶液c。在90℃水浴条件下将溶液a和溶液b同时缓慢滴加到溶液c中,不断搅拌,形成浅绿色沉淀,过滤并不断用去离子水洗涤沉淀,直至洗出液呈中性,然后将沉淀分散在150ml无水乙醇中,在120℃油浴条件下将水和乙醇共沸蒸去,然后将沉淀分散在200ml去离子水中形成悬浊液,在高温高压反应釜
中通入1mpa氢压,以120r/min,温度为150℃还原6h形成催化剂前驱体,然后抽滤,用去离子水和无水乙醇洗涤,放入50℃烘箱中干燥4h,研磨成粉末后将催化剂在管式炉中ar/h2混合气(h2体积含量10%),以3℃/min的升温速率升到450℃,混合气气流量为60ml/min,还原6h,关闭ar/h2混合气(h2体积含量10%),在管式炉中放置冷却24h,得到ni
70
/al1si3la0o(表示ni载量为70,al/si/la摩尔比为1/3/0催化剂)的担载镍催化剂。
47.对比例1
48.称取17.263gni(no3)2·
6h2o和11.029gal(no3)3·
9h2o,溶解于100ml的去离子水中,命名为溶液a’。称取16.447g的na2co3,溶解于100ml的去离子水中,命名为溶液b’。称取0.5gpeg2000溶解在200ml去离子水命名为溶液c’。在90℃水浴条件下将溶液a’和溶液b’同时缓慢滴加到溶液c’中,不断搅拌,形成浅绿色沉淀,过滤并不断用去离子水洗涤沉淀,直至洗出液呈中性,然后将沉淀分散在150ml无水乙醇中,在120℃油浴条件下将水和乙醇共沸蒸去,然后将沉淀分散在200ml去离子水中形成悬浊液,在高温高压反应釜中通入1mpa氢压,以120r/min,温度为150℃还原6h形成催化剂前驱体,然后抽滤,用去离子水和无水乙醇洗涤,放入50℃烘箱中干燥4h,研磨成粉末后将催化剂在管式炉中ar/h2混合气(h2体积含量10%),以3℃/min的升温速率升到450℃,混合气气流量为60ml/min,还原6h,关闭ar/h2混合气(h2体积含量10%),在管式炉中放置冷却24h,得到ni
70
/al2o3。
49.对比例2
50.称取17.263gni(no3)2·
6h2o溶解于100ml的去离子水中,命名为溶液a’。称取7.100gna2sio3·
9h2o和5.457g的na2co3,溶解于100ml的去离子水中,命名为溶液b’。称取0.5gpeg2000溶解在200ml去离子水命名为溶液c’。在90℃水浴条件下将溶液a’和溶液b’同时缓慢滴加到溶液c’中,不断搅拌,形成浅绿色沉淀,过滤并不断用去离子水洗涤沉淀,直至洗出液呈中性,然后将沉淀分散在150ml无水乙醇中,在120℃油浴条件下将水和乙醇共沸蒸去,然后将沉淀分散在200ml去离子水中形成悬浊液,在高温高压反应釜中通入1mpa氢压,以120r/min,温度为150℃还原6h形成催化剂前驱体,然后抽滤,用去离子水和无水乙醇洗涤,放入50℃烘箱中干燥4h,研磨成粉末后将催化剂在管式炉中ar/h2混合气(h2体积含量10%),以3℃/min的升温速率升到450℃,混合气气流量为60ml/min,还原6h,关闭ar/h2混合气(h2体积含量10%),在管式炉中放置冷却24h,得到ni
70
/sio2。
51.对比例3
52.各称取0.2g实施例1、实施例2、对比例1、对比例2所制备的催化剂和商业0.5wt%ru/al2o3催化剂进行苯的加氢实验。其中,原料苯加入10ml,溶剂正己烷40ml,反应的氢气压为7mpa,反应温度为150℃,转速为600r/min。上述5种催化剂催化苯加氢活性对比结果如图3所示。可知,实施例1制备的ni
70
/al1si1la0o催化剂催化苯加氢在60分钟反应完全,在合适的al/si摩尔比下,复合载体负载镍催化对苯的催化加氢活性都高于al2o3和sio2负载ni催化剂,且催化活性远高于商业0.5wt%ru/al2o3。
53.实施例3
54.称取12.331gni(no3)2·
6h2o和8.446gal(no3)3·
9h2o,溶解于100ml的去离子水中,命名为溶液a。称取6.396gna2sio3·
9h2o和8.528g的na2co3,溶解于100ml的去离子水中,命名为溶液b。称取0.5gpeg2000溶解在200ml去离子水命名为溶液c。在90℃水浴条件下将溶液a和溶液b同时缓慢滴加到溶液c中,不断搅拌,形成浅绿色沉淀,过滤并不断用去离子
水洗涤沉淀,直至洗出液呈中性,然后将沉淀分散在150ml无水乙醇中,在120℃油浴条件下将水和乙醇共沸蒸去,然后将沉淀分散在200ml去离子水中形成悬浊液,在高温高压反应釜中通入1ma氢压,以120r/min,温度为150℃还原6h形成催化剂前驱体,然后抽滤,用去离子水和无水乙醇洗涤,放入50℃烘箱中干燥4h,研磨成粉末后将催化剂在管式炉中ar/h2混合气(h2体积含量10%),以3℃/min的升温速率升到450℃,混合气气流量为60ml/min,还原6h,关闭ar/h2混合气(h2体积含量10%),在管式炉中放置冷却24h,得到ni
50
/al1si1la0o(表示ni载量为50,al/si/la摩尔比为1/1/0催化剂)的担载镍催化剂。
55.实施例4
56.称取22.195gni(no3)2·
6h2o和1.689gal(no3)3·
9h2o,溶解于100ml的去离子水中,命名为溶液a。称取1.279gna2sio3·
9h2o和12.485g的na2co3,溶解于100ml的去离子水中,命名为溶液b。称取0.5gpeg2000溶解在200ml去离子水命名为溶液c。在90℃水浴条件下将溶液a和溶液b同时缓慢滴加到溶液c中,不断搅拌,形成浅绿色沉淀,过滤并不断用去离子水洗涤沉淀,直至洗出液呈中性,然后将沉淀分散在150ml无水乙醇中,在120℃油浴条件下将水和乙醇共沸蒸去,然后将沉淀分散在200ml去离子水中形成悬浊液,在高温高压反应釜中通入1mpa氢压,以120r/min,温度为150℃还原6h形成催化剂前驱体,然后抽滤,用去离子水和无水乙醇洗涤,放入50℃烘箱中干燥4h,研磨成粉末后将催化剂在管式炉中ar/h2混合气(h2体积含量10%),以3℃/min的升温速率升到450℃,混合气气流量为60ml/min,还原6h,关闭ar/h2混合气(h2体积含量10%),在管式炉中放置冷却24h,得到ni
90
/al1si1la0o(表示ni载量为90,al/si/la摩尔比为1/1/0催化剂)的担载镍催化剂。
57.实施例5
58.称取7.433gni(no3)2·
6h2o、22.075gal(no3)3·
9h2o和1.329gla(no3)3·
6h2o溶解于100ml的去离子水中,命名为溶液a。称取18.834g的na2co3,溶解于100ml的去离子水中,命名为溶液b。称取0.5gpeg2000溶解在200ml去离子水命名为溶液c。在90℃水浴条件下将溶液a和溶液b同时缓慢滴加到溶液c中,不断搅拌,形成浅绿色沉淀,过滤并不断用去离子水洗涤沉淀,直至洗出液呈中性,然后将沉淀分散在150ml无水乙醇中,在120℃油浴条件下将水和乙醇共沸蒸去,然后将沉淀分散在200ml去离子水中形成悬浊液,在高温高压反应釜中通入1mpa氢压,以120r/min,温度为150℃还原6h形成催化剂前驱体,然后抽滤,用去离子水和无水乙醇洗涤,放入50℃烘箱中干燥4h,研磨成粉末后将催化剂在管式炉中ar/h2混合气(h2体积含量10%),以3℃/min的升温速率升到750℃,混合气气流量为60ml/min,还原6h,关闭ar/h2混合气(h2体积含量10%),在管式炉中放置冷却24h,得到ni
30
/al6si0la1o(表示ni载量为30,al/si/la摩尔比为6/0/1催化剂)的担载镍催化剂。催化剂的透射电镜如图7所示。
59.实施例6
60.称取7.433gni(no3)2·
6h2o、14.717gal(no3)3·
9h2o和3.988gla(no3)3·
6h2o溶解于100ml的去离子水中,命名为溶液a。称取15.6165g的na2co3,溶解于100ml的去离子水中,命名为溶液b。称取0.5gpeg2000溶解在200ml去离子水命名为溶液c。在90℃水浴条件下将溶液a和溶液b同时缓慢滴加到溶液c中,不断搅拌,形成浅绿色沉淀,过滤并不断用去离子水洗涤沉淀,直至洗出液呈中性,然后将沉淀分散在150ml无水乙醇中,在120℃油浴条件下将水和乙醇共沸蒸去,然后将沉淀分散在200ml去离子水中形成悬浊液,在高温高压反应釜
中通入1mpa氢压,以120r/min,温度为150℃还原6h形成催化剂前驱体,然后抽滤,用去离子水和无水乙醇洗涤,放入50℃烘箱中干燥4h,研磨成粉末后将催化剂在管式炉中ar/h2混合气(h2体积含量10%),以3℃/min的升温速率升到750℃,混合气气流量为60ml/min,还原6h,关闭ar/h2混合气(h2体积含量10%),在管式炉中放置冷却24h,得到ni
30
/al4si0la3o(表示ni载量为30,al/si/la摩尔比为4/0/3催化剂)的担载镍催化剂。
61.实施例7
62.称取7.433gni(no3)2·
6h2o、2.612gal(no3)3·
9h2o和5.320gla(no3)3·
6h2o溶解于100ml的去离子水中,命名为溶液a。称取4.073gna2sio3·
9h2o和7.2564g的na2co3,溶解于100ml的去离子水中,命名为溶液b。称取0.5gpeg2000溶解在200ml去离子水命名为溶液c。在90℃水浴条件下将溶液a和溶液b同时缓慢滴加到溶液c中,不断搅拌,形成浅绿色沉淀,过滤并不断用去离子水洗涤沉淀,直至洗出液呈中性,然后将沉淀分散在150ml无水乙醇中,在120℃油浴条件下将水和乙醇共沸蒸去,然后将沉淀分散在200ml去离子水中形成悬浊液,在高温高压反应釜中通入1mpa氢压,以120r/min,温度为150℃还原6h形成催化剂前驱体,然后抽滤,用去离子水和无水乙醇洗涤,放入50℃烘箱中干燥4h,研磨成粉末后将催化剂在管式炉中ar/h2混合气(h2体积含量10%),以3℃/min的升温速率升到750℃,混合气气流量为60ml/min,还原6h,关闭ar/h2混合气(h2体积含量10%),在管式炉中放置冷却24h,得到ni
30
/al1si1la1o(表示ni载量为30,al/si/la摩尔比为1/1/1催化剂)的担载镍催化剂。
63.实施例8
64.称取7.433gni(no3)2·
6h2o和3.122gla(no3)3·
6h2o溶解于100ml的去离子水中,命名为溶液a。称取5.454gna2sio3·
9h2o和11.005g的na2co3,溶解于100ml的去离子水中,命名为溶液b。称取0.5gpeg2000溶解在200ml去离子水命名为溶液c。在90℃水浴条件下将溶液a和溶液b同时缓慢滴加到溶液c中,不断搅拌,形成浅绿色沉淀,过滤并不断用去离子水洗涤沉淀,直至洗出液呈中性,然后将沉淀分散在150ml无水乙醇中,在120℃油浴条件下将水和乙醇共沸蒸去,然后将沉淀分散在200ml去离子水中形成悬浊液,在高温高压反应釜中通入1mpa氢压,以120r/min,温度为150℃还原6h形成催化剂前驱体,然后抽滤,用去离子水和无水乙醇洗涤,放入50℃烘箱中干燥4h,研磨成粉末后将催化剂在管式炉中ar/h2混合气(h2体积含量10%),以3℃/min的升温速率升到750℃,混合气气流量为60ml/min,还原6h,关闭ar/h2混合气(h2体积含量10%),在管式炉中放置冷却24h,得到ni
30
/al0si4la3o(表示ni载量为30,al/si/la摩尔比为0/4/3催化剂)的担载镍催化剂。
65.实施例9
66.称取6.058gnicl2·
6h2o、2.184gal2(so4)3和4.515glacl3·
7h2o溶解于100ml的去离子水中,命名为溶液a。称取1.967gk2sio3和13.928g的nahco3,溶解于100ml的去离子水中,命名为溶液b。称取0.5gpeg200溶解在200ml去离子水命名为溶液c。在90℃水浴条件下将溶液a和溶液b同时缓慢滴加到溶液c中,不断搅拌,形成浅绿色沉淀,过滤并不断用去离子水洗涤沉淀,直至洗出液呈中性,然后将沉淀分散在150ml无水乙醇中,在120℃油浴条件下将水和乙醇共沸蒸去,然后将沉淀分散在200ml去离子水中形成悬浊液,在高温高压反应釜中通入1mpa氢压,以120r/min,温度为150℃还原6h形成催化剂前驱体,然后抽滤,用去离子水和无水乙醇洗涤,放入50℃烘箱中干燥4h,研磨成粉末后将催化剂在管式炉中ar/h2混合气(h2体积含量10%),以3℃/min的升温速率升到750℃,混合气气流量为60ml/min,还原
6h,关闭ar/h2混合气(h2体积含量10%),在管式炉中放置冷却24h,得到ni
30
/al1si1la1o(表示ni载量为30,al/si/la摩尔比为1/1/1催化剂)的担载镍催化剂。
67.实施例10
68.称取6.686gniso4·
6h2o、2.184gal2(so4)3和4.515glacl3·
7h2o溶解于100ml的去离子水中,命名为溶液a。称取4.073gk2sio3和6.63g的naoh,溶解于100ml的去离子水中,命名为溶液b。称取0.5gpeg20000溶解在200ml去离子水命名为溶液c。在90℃水浴条件下将溶液a和溶液b同时缓慢滴加到溶液c中,不断搅拌,形成浅绿色沉淀,过滤并不断用去离子水洗涤沉淀,直至洗出液呈中性,然后将沉淀分散在150ml无水乙醇中,在120℃油浴条件下将水和乙醇共沸蒸去,然后将沉淀分散在200ml去离子水中形成悬浊液,在高温高压反应釜中通入1mpa氢压,以120r/min,温度为150℃还原6h形成催化剂前驱体,然后抽滤,用去离子水和无水乙醇洗涤,放入50℃烘箱中干燥4h,研磨成粉末后将催化剂在管式炉中ar/h2混合气(h2体积含量10%),以3℃/min的升温速率升到750℃,混合气气流量为60ml/min,还原6h,关闭ar/h2混合气(h2体积含量10%),在管式炉中放置冷却24h,得到ni
30
/al1si1la1o(表示ni载量为30,al/si/la摩尔比为1/1/1催化剂)的担载镍催化剂。
69.对比例4
70.分别称取0.2g实施例1、3、4、6、7、8、9、商业0.5wt%ru/al2o3催化剂进行n
‑
正丙基咔唑(npcz)的加氢实验。其中,原料npcz加入2g,溶剂环己烷加入40ml,反应的氢气压为7mpa,反应温度为150℃,转速为600r/min。上述催化剂催化npcz的吸收氢气的量随时间变化如图4所示,可知实施例1、3、4、6、7、8、9制备的催化剂对npcz的加氢活性均高于商业0.5wt%ru/al2o3催化剂,尤其是实施例7所制备的ni
30
/al1si1la1o在相同的反应条件下,使用较低的载量获得了高的催化活性,npcz在60分钟反应完全,而商业0.5wt%ru/al2o3催化剂则需要240分钟反应完全。
71.对比例5
72.分别称取0.2g实施例1、商业0.5wt%ru/al2o3催化剂进行乙基咔唑(necz)的加氢实验。其中,原料necz加入2g,溶剂环己烷加入40ml,反应的氢气压为7mpa,反应温度为150℃,转速为600r/min。上述催化剂催化necz的吸收氢气的量随时间变化如图5所示,可知实施例1所制备的催化剂在150℃和7mpa压力下对necz加氢仅需要90分钟左右,以商业0.5wt%ru/al2o3作为对比,在相同的实验条件下,240分钟未能反应完全。
73.对比例6
74.分别称取0.2g实施例1、商业0.5wt%ru/al2o3催化剂进行二苄基甲苯(dbt)的加氢实验。其中,原料dbt加入2g,溶剂环己烷加入40ml,反应的氢气压为7mpa,反应温度为150℃,转速为600r/min。上述催化剂催化dbt的吸收氢气的量随时间变化如图6所示,可知实施例1制备的催化剂在150℃和7mpa压力下对dbt加氢仅需要90分钟左右,以商业0.5wt%ru/al2o3作为对比,在相同的实验条件下,240分钟未能反应完全。
75.综上表明,本发明制备的催化剂对苯、n
‑
正丙基咔唑、乙基咔唑、二苄基甲苯均具有良好的催化活性,在一定程度上可作为有机液态储氢分子加氢的通用催化剂。
76.实施例11
77.使用实施例1中制备的0.2g催化剂进行npcz的循环重复加氢实验。其中,原料npcz加入2g,溶剂环己烷加入40ml,反应的氢气压为7mpa,反应温度为150℃,转速为600r/min,
反应结束后进行下次循环反应。所得五次n
‑
正丙基咔唑的吸氢速率如图8所示,可知第五次循环,npcz在90分钟仍可以反应完全,催化剂活性并没有明显衰减,显示出良好的稳定性。
78.对比例7
79.浙江大学叶旭峰等人使用镍基催化剂中高活性的雷尼镍进行了乙基咔唑的加氢测试,将乙基咔唑和活化雷尼镍(raney
‑
ni)催化剂放入不锈钢高压釜中,搅拌速度、温度、压力连续监测。然后将反应器密封,排空约15分钟,然后加热至所需温度。随后,在所需温度和氢气压力下开始反应,同时以1000转/秒的速度搅拌。随着反应的进行,反应器中的压力在整个实验过程中保持不变,从储氢罐中不断添加氢气。用压力计记录氢的消耗量和反应时间。使用气相色谱
‑
质谱仪(hp6890/5973gc
‑
ms)分析液体反应产物。(journalofalloysandcompounds2011年第509卷第152
‑
156页)。北京大学吴勇等人将ni/al2o3和yh3粉末按4:1质量比混合制备了1wt%ni/al2o3‑
yh3催化剂用于乙基咔唑加氢测试(journalofmaterialschemistrya2019年第7卷第16677
–
16684页)。反应条件及所得结果与实施例1催化剂对比如表1所示:
80.表1
81.样品储氢分子反应条件时间产率raney
‑
ninecz10wt%
a
,433k,5mpa h22.586.21wt% ni/al2o3‑
yh3necz12.5wt%,453k,10mpa h21.5100ni
70
/al1si1la0onecz10wt%,423k,7mpa h21.5100
82.a
催化剂与反应物的质量比。
83.由表1可知,在相似的反应条件下,雷尼镍(raney
‑
ni)对necz的加氢在2.5h内并没有完全反应,同样在相同的时间内完成反应的1wt%ni/al2o3‑
yh3所需要的反应条件更高,这表明实施例1所制备的催化剂具有高的催化活性,比雷尼镍催化剂和之前报道的镍基催化剂性能更加优越。
84.以上所述的实施例仅是对本发明的优选方式进行描述,并非对本发明的范围进行限定,在不脱离本发明设计精神的前提下,本领域普通技术人员对本发明的技术方案做出的各种变形和改进,均应落入本发明权利要求书确定的保护范围内。