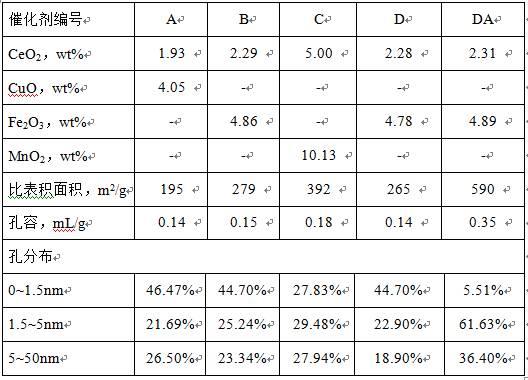
1.本发明属于催化技术领域,特别是涉及一种处理石化及化工污水的催化材料及制备方法。
背景技术:2.石油化工行业生产过程产生的污水中含有大量的有机污染物,对社会和经济的发展造成很大的影响。单纯的通过一次处理和二次生化很难将有机污染物脱除到可排放范围。臭氧催化氧化技术是一种高效的处理污水中有机污染物的方法,通过自由基链式反应同污水中的有机物反应,最后降解为co2、h2o和其他矿物盐,可以有效脱除污水中的有机污染物。
3.催化剂的活性是臭氧催化氧化技术处理有机废水的关键。目前市场上常规的催化剂普遍活性不高,一部分原因是首使用的原材料比表面积和孔容限制导致制备的催化剂孔结构不佳,通过造孔产生孔径大于介孔的孔,不会对有机物产生有效的吸附富集,反应活性很低;一部分是使用活性炭直接负载金属,造成催化剂机械强度和磨损强度偏低,使用过程中损耗较大,活性炭和活性金属的结合作用不强,金属流失情况严重。因此开发有机污染物高效吸附同时具有较强金属结合作用的催化剂对臭氧催化氧化技术是十分必要的。
4.cn106256426a公开了一种用于催化臭氧氧化的催化剂及其制备方法,该发明提供的催化剂为混合载体催化剂,将陶粒、球形al2o3、球形sio2、二氧化硅、分子筛、沸石中的一种或多种浸渍于铜、铁、锰、钴、镍、钼、银、钛、钒中的一种或多种与硝酸盐或乙酸盐形成的水溶液中,浸渍焙烧,再与一定体积的活性炭混合制得,也可将所述载体与活性炭预混合再焙烧制得。
技术实现要素:5.针对现有技术中的不足,本发明目的是提供一种废水处理用臭氧催化氧化催化剂及其制法,所述催化剂具有稳定的多级交联互通微米孔道结构,在催化剂的制备过程中通过化学交联技术将活性金属与无机载体优先结合,大大增强了载体与活性金属之间的结合强度,活性金属不易流失,对有机污染物具有良好的吸附脱除效果。
6.本发明第一方面提供一种废水处理用臭氧催化氧化催化剂的制备方法,所述制备方法包括如下内容:(1)将短切纤维丝与水混合进行打浆处理,得到浆液a;(2)焙烧处理无机硅铝氧化物得到物料b;(3)将步骤(1)得到的浆液a、步骤(2)得到的物料b、粘结组分、活性金属组分前驱体、酸和水混合均匀,然后加入活性炭进一步混合均匀并经成型干燥固化处理后得到催化剂前体c;(4)将步骤(3)得到的催化剂前体c与氢氧化钠溶液接触进行处理,处理完成后进行固液分离,分离得到的固体经干燥焙烧后得到催化剂。
7.上述废水处理用臭氧催化氧化催化剂的制备方法中,步骤(1)中所述短切纤维丝为碱溶性纤维,具体可以选自于聚酯纤维、羧甲基纤维素纤维、羟乙基纤维素纤维中的一种或几种。所述短切纤维丝的长度为2~5mm,单丝直径为10~70nm。
8.上述废水处理用臭氧催化氧化催化剂的制备方法中,步骤(1)中所述短切纤维丝与水的重量比为1:5~20。
9.上述废水处理用臭氧催化氧化催化剂的制备方法中,步骤(2)中所述无机硅铝氧化物为粉末状颗粒物,粒径1~100μm;以无机硅铝氧化物总重量为基准计,其中二氧化硅和氧化铝所占比例大于80wt%,二氧化硅与氧化铝的重量比为1~2:1。更进一步的,所述无机硅铝氧化物的平均孔径为2.0~30.0nm,其中孔径为5.0~15.0nm的孔的孔容占总孔容的80%以上;比表面积5~500m2/g。
10.上述废水处理用臭氧催化氧化催化剂的制备方法中,步骤(2)中所述焙烧处理温度为600~1000℃,优选为650~950℃;焙烧处理时间为3~12h,优选为4~8h。
11.上述废水处理用臭氧催化氧化催化剂的制备方法中,步骤(3)中所述活性炭可以选自磨碎的木质、煤质或果壳质颗粒活性炭。进一步优选的,所述活性炭的比表面积为400~3500m2/g,粒径为1~100微米,平均孔径为0.4~5.0nm,孔径1.2~3.6nm的孔的孔容占总孔容的90%以上。
12.上述废水处理用臭氧催化氧化催化剂的制备方法中,步骤(3)中所述粘结组分为无机粘结剂,优选为硅酸盐类无机粘结剂、磷酸盐类无机粘结剂中的一种或多种;所述硅酸盐类无机粘结剂具体可以是硅酸铝、硅酸钠、硅酸钙、硅酸二钙和硅酸三钙中的一种或几种,优选为硅酸钠和/或硅酸铝;所述磷酸盐类无机粘结剂具体可以是磷酸铝、磷酸二氢铝、磷酸二氢钠、焦磷酸钠、三聚磷酸钠、六偏磷酸钠中的一种或几种,优选为磷酸二氢铝和/或三聚磷酸钠。
13.上述废水处理用臭氧催化氧化催化剂的制备方法中,步骤(3)中所述活性金属组分前驱体为活性金属的氧化物,或者是活性金属的可溶性盐,所述可溶性盐具体可以是含活性金属的硝酸盐、乙酸盐、碳酸盐中的一种或几种。所述活性金属组分包括过渡金属和稀土金属,其中,所述过渡金属选自于钒、铬、锰、铁、钴、铜和钛中的一种或多种;所述稀土金属选自镧和/或铈。
14.上述废水处理用臭氧催化氧化催化剂的制备方法中,所述活性炭、无机硅铝氧化物、短切纤维丝、粘结组分和活性金属前驱物的质量比为15~50:50~80:5~15:2~5:5~15。
15.上述废水处理用臭氧催化氧化催化剂的制备方法中,步骤(3)中所述酸可以为无机酸和/或有机酸,所述无机酸具体可以选择硝酸、盐酸、硫酸、磷酸中的一种或几种;所述有机酸可以是乙酸、丙酸、甲酸中的一种或多种,进一步优选所述酸为硝酸和/或乙酸。
16.上述具有多级孔道结构的活性炭复合载体催化剂制备方法中,步骤(3)中所述干燥温度为60~150℃,优选90~120℃,干燥处理时间3~12h,优选3~9h。
17.上述具有多级孔道结构的活性炭复合载体催化剂制备方法中,步骤(3)中所述固化在氮气或多惰性气体保护下进行,进一步的,固化温度为150~450℃,优选为200~350℃;固化处理时间3~12h,优选3.5~8.5h。
18.上述具有多级孔道结构的活性炭复合载体催化剂制备方法中,步骤(3)中所述酸
的添加量占催化剂干基质量的1wt%~10wt%,优选3wt%~6wt%。
19.上述废水处理用臭氧催化氧化催化剂的制备方法中,步骤(3)中所述将步骤(1)得到的浆液a、步骤(2)得到的物料b、粘结组分、活性金属组分前驱体、酸和水混合均匀时,对各物料的加入次序没有特殊限制,优选的可以先将活性金属组分前驱体与酸和水形成溶液后,然后与其他物料进一步混合均匀;或者也可以先将物料b与酸和水混合得到浆液,然后在与其它物料进一步混合均匀。
20.上述废水处理用臭氧催化氧化催化剂的制备方法中,步骤(4)中所述氢氧化钠溶液的投加量按照二氧化硅和氢氧化钠的摩尔比为1:3~4,氢氧化钠溶液浓度为7wt%~10wt%。
21.上述废水处理用臭氧催化氧化催化剂的制备方法中,步骤(4)中所述干燥温度为50~150℃,优选为60~120℃,干燥时间为2~12h。
22.上述废水处理用臭氧催化氧化催化剂的制备方法中,步骤(4)中所述焙烧在惰性气氛下件,所述惰性气氛可以是氮气、氦气、氖气、氩气、氪气、氙气中的一种或几种,焙烧温度为300~1000℃,优选为400~800℃。
23.上述废水处理用臭氧催化氧化催化剂的制备方法中,所述成型技术可以采用本领域现有成型方法中的任一种,本领域技术人员可以根据实际需要进行自由选择,而这种选择属于本领域技术人员的普通知识,如可以为条形、球形、三叶草形和四叶草形中的任一种。
24.本发明第二方面提供一种采用上述方法制备得到的废水处理用臭氧催化氧化催化剂,所述催化剂包括载体和活性金属组分,其中活性金属组分包括过渡金属和稀土金属,其中,所述过渡金属选自于钒、铬、锰、铁、钴、铜和钛中的一种或多种;所述稀土金属选自镧和/或铈;所述载体包括4a分子筛、无机硅铝氧化物、活性炭和粘结剂。
25.上述废水处理用臭氧催化氧化催化剂中,所述4a分子筛相对结晶度为30~60。
26.上述废水处理用臭氧催化氧化催化剂中,所述催化剂的孔分布具有如下特征:其中孔直径0.1~1.5nm的孔的孔容占总孔容的比例不小于20%,优选为20~50%,孔直径1.5~5nm的孔的孔容占总孔容的比例不小于20%,优选为20~40%,孔直径5~50nm的孔的孔容占总孔容的比例不大于60%,优选为15~40%。
27.上述废水处理用臭氧催化氧化催化剂中,以催化剂总重量为基准,活性炭含量为5~65wt%,优选为10~50wt%;4a分子筛含量为10~65wt%,优选为20~55wt%;无机硅铝氧化物含量为10~55wt%,优选为10~40wt%;粘结剂含量为1~15wt%,优选为2~5wt%;活性金属含量为2~20wt%,优选为5~15wt%。
28.上述废水处理用臭氧催化氧化催化剂中,所述4a分子筛集中分布于催化剂的外表面。
29.本发明第三方面提供一种上述废水臭氧湿式氧化处理方法,在接触条件下将废水和臭氧通过装有上述催化剂的反应器。
30.上述废水处理方法中,所述废水可以来自石油生产、储运或石化产品加工过程中产生的含油污水、石化场地渗漏形成的污染地下水。
31.上述废水处理方法中,所述反应条件为室温常压、体积空速0.1~3 h-1
、氧化剂用量为按原料有机废水cod值计算所需氧化剂用量的0.5~5.0倍。
32.与现有技术相比,本发明提供的废水处理用臭氧催化氧化催化剂及其制备方法具有如下优点:1、本发明所述废水处理用臭氧催化氧化催化剂制备方法中,使用碱溶性纤维对催化剂进行改性,碱溶性纤维均匀混合在催化剂的载体中,再中性水相中不会溶解;在催化剂进行干燥及固化后使用氢氧化钠溶液处理,碱溶性纤维会溶解,溶解后形成三维互通的微米级孔道,同载体自身的微孔、中孔结合形成贯通的多级孔道,强化了污水中有机物在催化剂内部的扩散效应,有利于提高催化剂内部的传质速率。
33.2、本发明所述废水处理用臭氧催化氧化催化剂制备方法中,热处理过的无机硅铝氧化物在成型固化后保证催化剂前体已经具有初步的机械强度,再使用氢氧化钠溶液进行处理,可以在碱溶液的作用下转晶为4a分子筛,形成丰富的微孔结构,大大提高了催化剂的吸附性能,使污水中的有机物可以通过多级孔道的传质效应有效富集在催化剂的内部孔道中,加快催化氧化反应的进行,从而提高处理速率。
34.3、本发明所述废水处理用臭氧催化氧化催化剂制备方法中,活性金属同无机原料预先进行混合,在酸的作用下,无机原料形成部分胶溶性混合物,使活性金属前驱体优先同无机原料形成的胶溶性混合物接触及结合,而后混合物再与活性炭混合,这样可以使活性金属的优先负载在无机氧化物载体成分上,从而避免了在附着力不强的活性炭上的负载。从效果来看,整体提高了催化剂对活性金属的附着力,减少了在水相体系中的金属流失,从而提高了催化剂的使用寿命。
具体实施方式
35.下面结合具体的实施例来进一步说明本发明的制备方法,但是本发明的范围不只限于这些实施例的范围。
36.本发明实施例和比较例中,所述孔容、比表面积、孔分布采用低温液氮物理吸附法测定。本发明中,wt%为质量分数。本发明实施例和比较例中,相对结晶度采用x射线衍射法(徐如人,庞文琴等.分子筛与多孔材料化学.北京:科学出版社. 2014)得出。
37.本发明中所用的市售活性炭比表面积985m2/g、孔容0.45cm3/g,平均孔半径1.1nm、碘吸附值700mg/g、颗粒直径45μm。本发明中所用的无机硅铝氧化物比表面积105m2/g、二氧化硅和氧化铝的质量比为3:2、颗粒直径45μm。
38.实施例1将无机硅铝氧化物800℃焙烧处理6h,然后加入配制好的硝酸铜与硝酸铈和冰乙酸的混合溶液、碱溶性羧甲基纤维素纤维短切丝浆液并混合均匀后,再加入质量含量30%的硅酸钠粘结剂充分混合均匀,再加入活性炭粉末以及水充分混合,使混合物料形成可挤块状物进行挤条,90℃干燥8h后,在氮气保护条件下280℃热处理5h,然后使用循环的质量浓度8%的氢氧化钠溶液进行处理3h,使用蒸馏水洗涤后进行固液分离,将分离得到的固状颗粒在90℃下干燥8h,在氮气保护条件下750℃焙烧3h,得到催化剂a,所用试剂列于表1,所制备催化剂性质列于表2。
39.实施例2无机硅铝氧化物700℃焙烧处理7h,加入配制好的硝酸铁与硝酸铈和硝酸的混合溶液、碱溶性聚酯纤维素纤维短切丝浆液混合均匀后,再加入质量含量25%的硅酸钠粘结剂
充分混合均匀,再加入活性炭粉末以及适量水充分混合,使混合物料形成可挤块状物进行挤条,100℃干燥6h后,在氮气保护条件下270℃热处理5h,待充分冷却后,使用循环的质量浓度7%的氢氧化钠溶液进行处理3h,使用蒸馏水洗涤后进行固液分离,将固状颗粒在100℃下干燥6h,在氮气保护条件下650℃焙烧5h,得到催化剂b,所用试剂列于表1,所制备催化剂性质列于表2。
40.实施例3无机硅铝氧化物900℃焙烧处理5h,加入配制好的硝酸锰与硝酸铈和乙酸的混合溶液、碱溶性羟乙基纤维素纤维短切丝浆液混合均匀后,再加入质量含量30%的硅酸钠粘结剂充分混合均匀,再加入活性炭粉末以及水充分混合,使混合物料形成可挤块状物进行挤条,110℃干燥4h后,在氮气保护条件下300℃热处理3h,待充分冷却后,使用循环的质量浓度8%的氢氧化钠溶液进行处理4h,使用蒸馏水洗涤后进行固液分离,将固状颗粒在110℃下干燥4h,在氮气保护条件下700℃焙烧3h,得到催化剂c,所用试剂列于表1,所制备催化剂性质列于表2。
41.实施例4按照实施例2的比例,在催化剂的制备过程中,焙烧处理后的无机硅铝氧化物、活性炭先混合均匀再加入混合金属溶液及短切丝浆液混合均匀,再加入硅酸钠粘结剂混合均匀,其后催化剂成型剂干燥及焙烧步骤同实施例2,得到催化剂d,所用试剂列于表1,所制备催化剂性质列于表2。
42.对比例1使用颗粒活性炭直接负载fe-ce活性金属后,氮气保护焙烧得到催化剂da,所用试剂列于表1,所制备催化剂性质列于表2。
43.表1 制备催化剂试剂用量催化剂编号abcdda无机硅铝氧化物,g940810485810-短切纤维,g88152680-活性炭,g249868848868352氢氧化钠,g137415798271579-硝酸铈,g8117023817023硝酸铜,g195
‑‑‑‑
硝酸铁,g-689-68993硝酸锰,g
‑‑
642
‑‑
酸,g79212136
‑‑
表2 催化剂性质
硝酸铈和冰乙酸的混合溶液、由表2中催化剂性质可以看出,采用加入短切纤维处理后得到的催化剂与不添加得到的催化剂相比,整体性质得到了改善。
44.评价试验:通过处理模拟化工废水来考察上述方法制备的催化剂的反应性能。
45.金属流失试验:测量出水中金属离子含量,来对比不同方法制备催化剂的金属流失性。固定床反应器中装填上述催化剂,使用酸性大红模拟废水进行连续臭氧催化氧化反应,处理条件为常温常压,原水进水cod为600 mg/l,空速为0.5h-1
,以臭氧为氧化剂。
46.处理200h和1000h后的处理结果见表3和表4。
47.表3 处理200h后臭氧催化氧化试验结果催化剂编号bdda出水cod,mg/l8281126出水金属离子,ppb3936371334表4 处理1000h后臭氧催化氧化试验结果催化剂编号bdda出水cod,mg/l76100126出水金属离子,ppb3808131520由表3和表4的处理结果可以看出,使用本方法制备的催化剂具有良好的活性,同时使用本发明制备方法制备催化剂能够很好的控制金属流失量,使催化剂具有良好的活性稳定性。