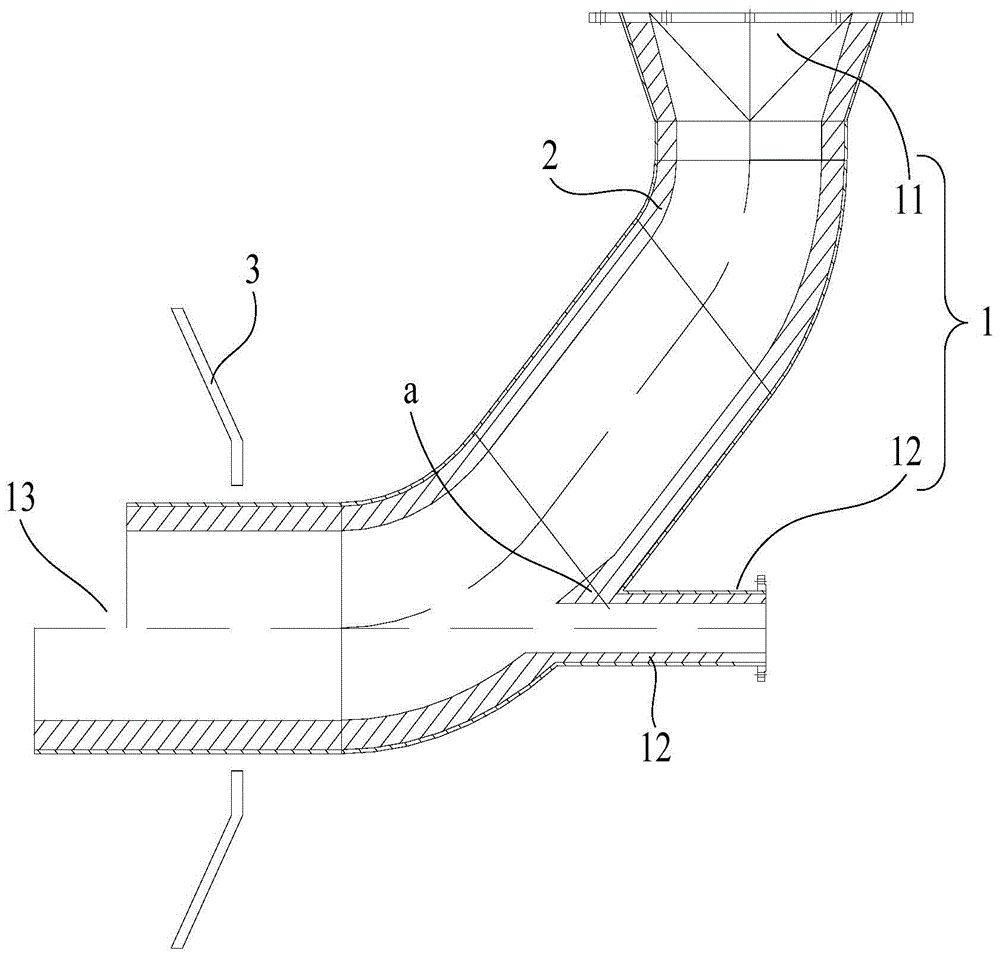
本申请涉及棒磨机配件
技术领域:
,尤其是涉及一种导料入料构件及导料入料构件的生产工艺。
背景技术:
:目前,矿业原料粉碎设备入料口,用于输送铝矿石、水以及氢氧化钠的混合物,即上述的入料口处于湿磨工况,具体地,湿磨工况如下:铝矿石粒度20-40mm,硬度莫氏>6级,相当于hv1050,氢氧化钠按比例加入水中ph值10-12。现有技术中多采用砂型铸造工艺成型制备出合金钢单金属的入料口,容易磨损、腐蚀,使用寿命短,而且用户不得不因此停产、焊补、检修,影响生产。技术实现要素:本申请的目的在于提供一种导料入料构件及导料入料构件的生产工艺,在一定程度上解决了现有技术中存在的合金钢单金属的入料口容易磨损、腐蚀,使用寿命短,影响生产的技术问题。本申请提供了一种导料入料构件,包括外壳,所述外壳的内部中空,且所述外壳形成有与其内部中空处相连通的出料口以及至少两个入料口,所述外壳的内壁设置有用于抗磨损及抗腐蚀的防腐抗磨层。在上述技术方案中,进一步地,多个所述入料口至少包括第一入料口和第二入料口,其中所述第一入料口形成于所述外壳的一端,所述出料口形成于所述外壳的相对的另一端;所述第二入料口形成于所述外壳的一侧,且所述第二入料口朝向远离所述外壳的方向延伸;所述第二入料口的内壁也设置有所述防腐抗磨层。在上述任一技术方案中,进一步地,所述第二入料口的内壁设置的所述防腐抗磨层与所述外壳的内壁设置的所述防腐抗磨层的相交部位朝向所述外壳的内部加长加厚。在上述任一技术方案中,进一步地,所述防腐抗磨层由高铬铸铁形成。在上述任一技术方案中,进一步地,所述防腐抗磨层包括如下质量百分比的组分:c=3%-4%,si=0.8%-1.2%,mn=0.7%-1.0%,cr=22%-26%,mo=0.7%-1.0%,ni=0.6%-1.2%,cu=0.4%-0.6%,v=0.15%-0.2%,p<0.06%,s<0.06%,re=0.05%-0.1%,ti=0.25%-0.35%。在上述任一技术方案中,进一步地,所述外壳由20#钢形成。在上述任一技术方案中,进一步地,所述防腐抗磨层与所述外壳采用消失模负压铸造工艺一体式形成。在上述任一技术方案中,进一步地,所述外壳的厚度为10mm;所述防腐抗磨层的厚度为30mm-50mm。本申请还提供了一种导料入料构件的生产工艺,用于制备上述任一技术方案所述的导料入料构件,因而,具有该导料入料构件的全部有益技术效果,在此,不再赘述。在上述技术方案中,进一步地,所述导料入料构件的生产工艺包括如下步骤:按设计图纸制作所述外壳;依据产品不同部位的磨耗速率,对防腐抗磨层的厚度做相应的差异性设计;依据所述防腐抗磨层的厚度设计,采用消失模铸造工艺在所述外壳的内壁复合形成所述防腐抗磨层;应用余热对铸造完成的所述导料入料构件进行淬火以及回火的热处理。在上述任一技术方案中,进一步地,所述应用余热对铸造完成的所述导料入料构件进行淬火以及回火的热处理包括:在900℃-920℃温度下出砂箱、落砂,同时风冷淬火,而后在500℃-280℃温度下保温3小时。与现有技术相比,本申请的有益效果为:本申请提供的导料入料构件包括外壳以及防腐抗磨层,外壳负责结构强度与相关设备连接,防腐抗磨层则负责抵抗强磨损和腐蚀,做到性能互补,各自发挥优势,协同工作,使得本导料入料构件的使用寿命更长,进而无需经常停产、焊补、检修,从而有助于提高生产效率。本申请提供的导料入料构件的生产工艺中,是将防腐抗磨层与外壳双金属熔铸为一体,不易分离,整体强度高,此外,本导料入料构件的外壳负责结构强度与相关设备连接,本导料入料构件的防腐抗磨层负责抵抗强磨损和腐蚀。附图说明为了更清楚地说明本申请具体实施方式或现有技术中的技术方案,下面将对具体实施方式或现有技术描述中所需要使用的附图作简单地介绍,显而易见地,下面描述中的附图是本申请的一些实施方式,对于本领域普通技术人员来讲,在不付出创造性劳动的前提下,还可以根据这些附图获得其他的附图。图1为本申请实施例一提供的导料入料构件的结构示意图;图2为本申请实施例二提供的导料入料构件的生产工艺的制备方法的流程图。附图标记:1-外壳,11-第一入料口,12-第二入料口,13-出料口,2-防腐抗磨层,3-棒磨机端盖。具体实施方式下面将结合附图对本申请的技术方案进行清楚、完整地描述,显然,所描述的实施例是本申请一部分实施例,而不是全部的实施例。通常在此处附图中描述和显示出的本申请实施例的组件可以以各种不同的配置来布置和设计。因此,以下对在附图中提供的本申请的实施例的详细描述并非旨在限制要求保护的本申请的范围,而是仅仅表示本申请的选定实施例。基于本申请中的实施例,本领域普通技术人员在没有做出创造性劳动前提下所获得的所有其他实施例,都属于本申请保护的范围。在本申请的描述中,需要说明的是,术语“中心”、“上”、“下”、“左”、“右”、“竖直”、“水平”、“内”、“外”等指示的方位或位置关系为基于附图所示的方位或位置关系,仅是为了便于描述本申请和简化描述,而不是指示或暗示所指的装置或元件必须具有特定的方位、以特定的方位构造和操作,因此不能理解为对本申请的限制。此外,术语“第一”、“第二”、“第三”仅用于描述目的,而不能理解为指示或暗示相对重要性。在本申请的描述中,需要说明的是,除非另有明确的规定和限定,术语“安装”、“相连”、“连接”应做广义理解,例如,可以是固定连接,也可以是可拆卸连接,或一体地连接;可以是机械连接,也可以是电连接;可以是直接相连,也可以通过中间媒介间接相连,可以是两个元件内部的连通。对于本领域的普通技术人员而言,可以具体情况理解上述术语在本申请中的具体含义。下面参照图1和图2描述根据本申请一些实施例所述的导料入料构件及导料入料构件的生产工艺。实施例一参见图1所示,本申请的实施例提供了一种导料入料构件,尤其可作为棒磨机的入料口使用,但不仅限于此,还可应用在其他设备中;具体地,本导料入料构件包括外壳1,外壳1的内部中空,且外壳1形成有与其内部中空处相连通的出料口13以及两个入料口,当然,入料口的数量不仅限于两个,还可根据实际需要设置;外壳1的内壁设置有用于抗磨损及抗腐蚀的防腐抗磨层2。基于以上描述的结构可知,外壳1负责结构强度与相关设备连接,防腐抗磨层2则负责抵抗强磨损和腐蚀,做到性能互补,各自发挥优势,协同工作,使得本导料入料构件的使用寿命更长,进而无需经常停产、焊补、检修,从而有助于提高生产效率。在该实施例中,优选地,如图1所示,两个入料口分别为第一入料口11和第二入料口12,其中第一入料口11形成于外壳1的一端,第一入料口11主要用于输入矿石等,进一步,优选地,第一入料口11呈锥形结构,起到导料的作用;出料口13形成于外壳1的相对的另一端,且出料口13延伸至棒磨机端盖3的内部,出料口13用于将上述的矿石以及下述的氢氧化钠液体所形成的混合物料输入至棒磨机内;第二入料口12形成于外壳1的一侧,且第二入料口12朝向远离外壳1的方向延伸,第二入料口12主要用于输入碱性溶液例如氢氧化钠溶液;第二入料口12的内壁也设置有防腐抗磨层2,起到防腐蚀的作用,进一步,优选地,第二入料口12呈直管状。在该实施例中,优选地,如图1所示,第二入料口12的内壁设置的防腐抗磨层2与外壳1的内壁设置的防腐抗磨层2的相交部位朝向外壳1的内部加长加厚。根据以上描述的结构可知,在强磨损区域加厚并且向前延伸防腐耐磨层,解决局部过早磨穿问题,进一步延长产品的使用寿命。在该实施例中,优选地,外壳1由20#钢形成,保证一定的结构强度,能够与相关设备连接。防腐抗磨层2由高铬铸铁形成,起到抗磨、防止化学腐蚀以及电腐蚀的作用,具体地,高铬铸铁包括如下质量百分比的组分:c=3%-4%,si=0.8%-1.2%,mn=0.7%-1.0%,cr=22%-26%,mo=0.7%-1.0%,ni=0.6%-1.2%,cu=0.4%-0.6%,v=0.15%-0.2%,p<0.06%,s<0.06%,re=0.05%-0.1%,ti=0.25%-0.35%。基于上述组分可知,化学元素中适量加入cu,结晶时绝大部分存留在晶间,可减少微电池生成,降低晶间腐蚀。化学元素中适量加入mo、ni,可防止氢氧化钠腐蚀。化学元素中适量加入v,生成金相组织vc,硬度为hv=2800的质点。化学元素中适量加入ti生成金相组织tic,硬度为hv=3200的质点。以上这些极硬质点占产品总体积的28%以上,均匀分散于产品基体中,被高强度金相组织回火马氏体紧紧包裹,这样产品的平均硬度约为hv1600,铝矿石硬度hv1050,该硬度比1600:1050=1.5:1,完全满足了耐磨件与磨粒的硬度比(1.4-1.6):1的理想数据。注意,上述的高铬铸铁的化学组成是一个范围,具体多少要根据矿石的粒度大小调整产品的冲击韧性,根据矿石的硬度调整产品的相对硬度。根据生产中加入氢氧化钠数量调整产品的抗腐蚀性能,根据液态情况的流量调整产品抗微电池生成。以下以实际生产中经常遇到的工况为例加以说明:铝矿石粒度30mm,莫氏硬度6.5级,ph值=10,在此种工况下,优选地:高铬铸铁的化学组成如下:c=3.8%,si=1.1%,mn=0.9%,cr=24%,mo=0.9%,ni=0.8%,cu=0.5%,v=0.16%,p<0.06%,s<0.06%,re=0.07%,ti=0.3%。在保证抗磨、抗腐蚀的前提下,钼、钒、钛、铜等贵重元素取小值,成本较低,而碳含量取大值,保证其硬度足够,且不会增加成本,此外,针对碳含量取大值,则不需加热炉加热采用高温出箱利用余热进行风冷淬火,可获得理想硬度,这样每吨产品成本可降1000元,在实际生产中具有重要意义。在该实施例中,优选地,防腐抗磨层2与外壳1采用消失模负压铸造工艺一体式形成,两者熔铸为一体,不会出现分离的问题,而且整体结构强度高,不易损坏。在该实施例中,优选地,外壳1的厚度为10mm,满足结构强度的需求;防腐抗磨层2的厚度为30mm-50mm,满足防腐抗磨的需求。综上,采用20#的外壳1与高铬铸铁的防腐抗磨层2复合新工艺,其中,20#钢的外壳1负责结构强度与相关设备的连接,而高铬铸铁的防腐抗磨层2则负责抵抗强磨损和腐蚀,做到性能互补,各自发挥优势。实施例二本申请的实施例还提供一种导料入料构件的生产工艺,用于制备上述任一实施例所述的导料入料构件,因而,具有该导料入料构件的全部有益技术效果,在此,不再赘述。在该实施例中,优选地,如图2所示,导料入料构件的生产工艺包括如下步骤:按设计图纸制作20#钢的外壳1;依据产品不同部位的磨耗速率,对高铬铸铁的防腐抗磨层2的厚度做相应的差异性设计(优选地,外壳1的厚度为10mm,防腐抗磨层2的厚度为30mm-50mm);依据防腐抗磨层2的厚度设计,采用消失模铸造工艺在外壳1的内壁复合形成高铬铸铁的防腐抗磨层2,且熔铸完成后所形成的金相组织为甲+乙+巳+丙(优选地,浇注温度1340℃-1380℃);应用余热对铸造完成的导料入料构件进行淬火以及回火的热处理,获得最终的金相组织为甲+乙+巳+丁(上述回火步骤中,金相组织丙转变为金相组织丁,获得理想的金相组织,同时消除产品的内应力)。可见,充分利用余热,节约能源。进一步,优选地,应用余热对铸造完成的导料入料构件进行淬火以及回火的热处理包括:在900℃-920℃温度下出砂箱、落砂,同时风冷淬火,而后在500℃-280℃温度下保温3小时,回火的目的在于使金相组织丙转变为金相组织丁,获得理想的金相组织,同时消除产品的内应力。为了更清楚地了解本工艺所制备的导料入料构件的优越性能,现将现有技术中利用单金属砂型铸造工艺所生产的合金钢单金属的入料口的性能与利用本生产工艺所获得的导料入料构件的性能做对比,具体参见表一、表二、表三以及表四所示:表一两种产品化学成分的对照表注意:化学元素组成均以质量百分比表示。表二两种产品金相组织的对照表表三金相代号结合上述表格所公开的内容可知,本工艺所制备的导料入料构件具有如下特点:导料入料构件的硬度hrc≥60,抗拉强度≥410n/mm2,冲击韧度ak/j·cm2≥20,磨耗速率0.01-0.02g/12hcm2。导料入料构件的金相组织甲的硬度hv=1200-1800(硬度相当于hrc75以上)。导料入料构件的金相组织乙的硬度hv=1200-1600(硬度相当于hrc70以上)。化学元素中适量加入cu,结晶时绝大部分存留在晶间,可减少微电池生成,降低晶间腐蚀。化学元素中适量加入mo、ni,可防止氢氧化钠腐蚀。化学元素中适量加入v,生成金相组织辛,硬度为hv=2800的质点。化学元素中适量加入ti生成金相组织壬,硬度为hv=3200的质点。以上这些极硬质点占产品总体积的28%以上,均匀分散于产品基体中,被高强度金相组织丁紧紧包裹,这样产品的平均硬度约为hv1600,铝矿石硬度hv1050,该硬度比1600:1050=1.5:1,完全满足了耐磨件与磨粒的硬度比(1.4-1.6):1的理想数据。下面将对现有技术中的入料口的耐磨性与本生产工艺所制备的导料入料构件的高铬铸铁的防腐耐磨层的耐磨性能进行比较,具体详见表五:表五计算使用寿命产品名称3cm3重磨耗速率12h/cm2天年(使用寿命)合金钢22.5g÷0.03g=750750÷2=375÷360天=1.04年合金钢22.5g÷0.07g=321.4321.428÷2=160.7÷360天=0.44年高铬铸铁22.5g÷0.01g=22502250÷2=1125÷360天=3.125年高铬铸铁22.5g÷0.02g=11251125÷2=562.5÷360天=1.56年注:设产品安全运行磨耗厚度30mm,重量22.5g/3cm3。磨耗速率的试验方法:磨料为80目金刚砂,冲击角度20°,冲击速度20m/秒,每12小时每cm2的失重量。可见,经过本生产工艺所形成的高铬铸铁的防腐抗磨层2的抗磨损能力更强,使用寿命更长,明显高于现有技术中的入料口。综上,采用20#钢的外壳1与高铬铸铁的防腐抗磨层2复合新工艺所制备的导料入料构件,能够应对强磨损、化学腐蚀、电腐蚀三者共存的液态输送工况,使用寿命更长,无需停产检修、更换等,进而提高了生产效率。注意,本工艺不仅限于针对高铬铸铁与20#钢的双金属熔铸,还可对其他材质的金属进行熔铸,以生产具有不同抗磨性能的以及耐不同化学介质腐蚀的产品。最后应说明的是:以上各实施例仅用以说明本申请的技术方案,而非对其限制;尽管参照前述各实施例对本申请进行了详细的说明,本领域的普通技术人员应当理解:其依然可以对前述各实施例所记载的技术方案进行修改,或者对其中部分或者全部技术特征进行等同替换;而这些修改或者替换,并不使相应技术方案的本质脱离本申请各实施例技术方案的范围。当前第1页12