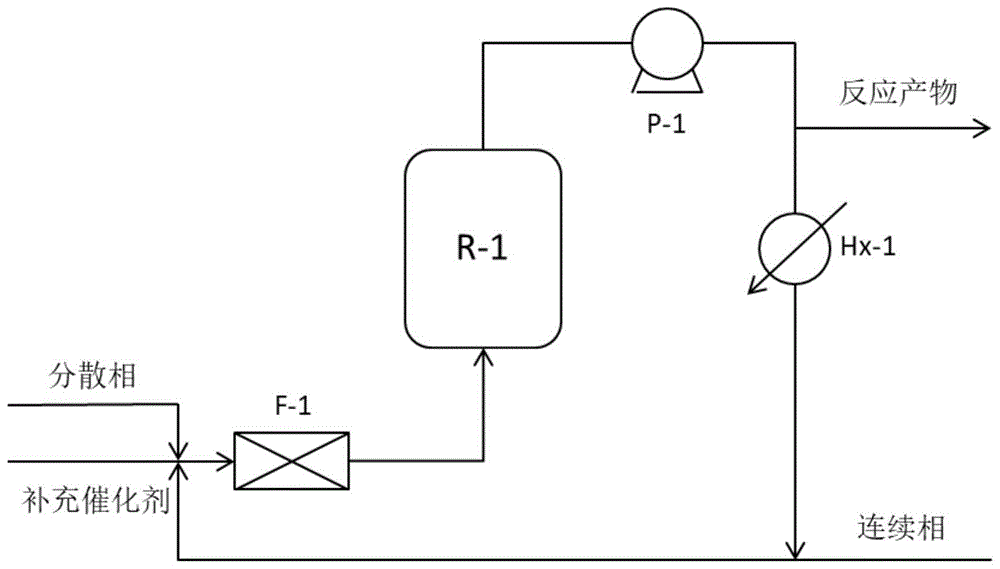
本发明属于有机合成领域,涉及一种醛缩合反应设备及反应方法。
背景技术:
:羟醛缩合是一个众所周知的反应,可以发生在同种类的醛,不同的醛或醛酮之间,反应产物为羟醛,一些不稳定的羟醛产物会进一步脱水生成烯醛。羟醛缩合反应可以采用酸或碱作为催化剂,在工业上一般使用碱金属的氢氧化物(如naoh)为催化剂,该反应的反过程如下:两分子的醛在碱催化剂的作用下,发生二聚生成羟醛,羟醛则有可能进一步脱水生成不饱和烯醛。对于四个碳原子以上的醛,由于醛与水相互之间的溶解度较小,该反应为两相反应。与该反应同时发生的副反应为坎尼扎罗反应(cannizzaroreaction):2rch2cho+naoh→rch2coona+rch2ch2oh在这类反应中,由正丁醛(戊醛)缩合得到的2-乙基-己烯醛(2-丙基庚烯醛及其异构烯醛),再通过加氢得到的2-乙基-己醇(2-丙基庚醇及异构癸醇),是工业上大规模生产的产品。2-乙基-己醇(2-丙基庚醇及异构癸醇)与与邻苯二甲酸反应生成的邻苯二甲酸二酯(dop,dphp),作为通用型增塑剂,主要用于聚氯乙烯的加工,还可用于化纤树脂、醋酸树脂、abs树脂及橡胶等高聚物的加工,或用于造漆、染料、分散剂等。另一个重要的产品是异丁醛与甲醛缩合生成的羟基新戊醛,进一步加氢的得到新戊二醇,也是一种重要的化工原料。新戊二醇主要用于生产饱和聚酯树脂、不饱和聚酯树脂、聚酯多元醇及合成润滑剂所用的酯类、聚合物增塑剂和醇酸树脂等。新戊二醇衍生物广泛用于汽车、纺织、医药、涂料、农药、塑料和石油等领域,目前,美国、日本等国都在致力于新戊二醇的新应用领域开发。目前工业上醛缩合反应器使用较多的为分布器的搅拌釜式反应器,为了加强混合效果,通常需要在反应器内增加挡板。采用上述结构的搅拌釜通常能获得较好的混合效果,但是反应器结构复杂,设备投资较高。同样由于搅拌器的内部构件较多,且反应过程往往涉及压力下的动密封,设备容易发生故障。如果采用多个较小的搅拌器代替单一的大搅拌釜,能部分解决上述问题,但是这会进一步增加设备投资。另一种可能的反应器形式为管式反应器,管式反应器省略了搅拌器,但是单纯地使用管式反应器其反应单程转化率不高。cn1227207公开了一种采用装有填料的管式反应器,由于装有填料后反应器压降显著增大,为确定合适的操作条件,文献中提出了载荷系数b的概念,当载荷系数b≥0.8时,醛缩合反应能获得较好的反应结果。该方法为了实现原料醛的有机相在连续相(催化剂溶液)中的高度分散,进入反应器连续相与有机相的质量比>10:1,甚至高达100:1。cn101838186公开了一种戊醛缩合反应方法,该方法在管式反应器中放置体积占比超过50%的静态混合器,实现了有机相在连续相中平均液滴尺寸0.2~2mm,在连续相与有机相的质量比10~20:1的条件下,获得了较为理想的戊醛转化率。该方法相对于搅拌釜,避免使用了搅拌器,但是将静态混合器置于反应器内部,对于反应器的维护是一个不利因素。技术实现要素:为解决现有技术中存在的技术问题,本发明提供一种醛缩合反应设备及反应方法,所述反应设备无需设置搅拌器以及分布器,简化了反应装置结构,降低了反应器设备及维护成本;所述反应方法可以强化醛缩合反应,提高了醛转化率以及烯醛产品收率。为达到上述技术效果,本发明采用以下技术方案;本发明目的之一在于提供一种醛缩合反应设备,所述缩醛反应设备包括分散相管路、连续相管路、循环管路、反应装置以及分散装置;所述分散装置、反应装置、循环管路以及所述连续相管路依次循环连接;所述分散相管路与所述分散装置进液口相连。作为本发明优选的技术方案,所述分散装置出液口与所述反应装置进样口相连;优选地,所述反应装置出样口与所述循环管路的入口相连;优选地,所述循环管路出口与所述连续相管路相连;优选地,所述连续相管路与所述分散装置进液口相连;优选地,所述循环管路上设置有反应产物出口。本发明目的之二在于提供另一种醛缩合反应设备,所述缩醛反应设备包括分散相管路、连续相管路、循环管路、反应装置、第一分散装置以及第二分散装置;所述反应装置、循环管路以及第二分散装置依次循环连接;所述分散相管路以及所述连续相管路分别独立地与所述第一分散装置进液口相连;所述第一分散装置出液口与所述反应装置进样口相连。作为本发明优选的技术方案,所述反应装置出样口与所述循环管路的入口相连;优选地,所述循环管路出口与所述第二分散装置进液口相连;优选地,所述第二分散装置出液口与所述反应装置进样口相连;优选地,所述循环管路上设置有反应产物出口。本发明中,通过循环管路的设置,形成外循环物流,将反应器中的两相混合物抽出反应器,通过分散装置后返回反应器,强化反应分散相在反应器中的高度分散。本发明中,虽然包括两种不同的醛缩合反应设备,但是第一个反应设备中通过同一分散装置实现分散相在流动相中的分散以及循环物料中分散相的分散。而第二个反应设备中通过第一反应装置实现分散相在流动相中的分散,通过第二分散装置实现环物料中分散相的分散。本发明中,反应装置可以采用单一反应器,也可采用多个反应器串联的形式,所述反应器可以是管式反应器或釜式反应器。本发明目的之三在于提供一种醛缩合反应方法,所述醛缩合反应方法包括:分散相经第一分散,分散于流动相,得到反应物流;所述反应物流进入反应装置进行反应后,分为循环物流以及反应产物物流;所述循环物流经第二分散后返回所述反应装置;所述反应物流中的分散相通过所述反应装置横截面的表观液速小于0.1m/s。其中,所述反应物流中的分散相通过所述反应装置横截面的表观液速可以是0.09m/s、0.08m/s、0.07m/s、0.06m/s、0.05m/s、0.04m/s、0.03m/s、0.02m/s或0.01m/s等,但并不仅限于所列举的数值,该数值范围内其他未列举的数值同样适用。本发明中,在反应前对分散相进行分散,使分散相充分分散于流动相中,虽然可以实现反应装置入口段的液液两相高度分散,但是对于较大体积的反应装置,分散相(有机相)液滴的聚并难以避免。为了避免在反应装置内部使用结构复杂的内构件,需要控制反应过程中的一些工艺条件,进入反应器内的分散相流速以及反应器的尺寸都是会影响分散相在液相分散的因素。气体流速过大气泡会在反应器中迅速发生聚并,从而失去分散效果。因此,本发明进一步限定了所述反应物流中的分散相通过所述反应装置横截面的表观液速小于0.1m/s。作为本发明优选的技术方案,所述反应物流中的分散相通过所述反应装置横截面的表观液速小于0.05m/s。作为本发明优选的技术方案,所述分散相与所述流动相的体积比为10~1:1,如9:1、8:1、7:1、6:1、5:1、4:1、3:1或2:1等,但并不仅限于所列举的数值,该数值范围内其他未列举的数值同样适用,优选为3~1:1。优选地,所述分散相分别独立地经所述第一分散以及第二分散后,分散于所述连续相中的液滴直径小于100μm,如10nm、20nm、50nm、100nm、200nm、500nm、1μm、2μm、5μm、10μm、20μm、50μm或80μm等,但并不仅限于所列举的数值,该数值范围内其他未列举的数值同样适用,优选地100nm~10μm。作为本发明优选的技术方案,所述循环物流以及反应产物物流的质量流量比大于8:1,如10:1、15:1、20:1、25:1、30:1、35:1、40:1、45:1、50:1、60:1、70:1、80:1或100:1等,但并不仅限于所列举的数值,该数值范围内其他未列举的数值同样适用,优选为10~40:1。作为本发明优选的技术方案,所述分散相为有机相。优选地,所述有机相包括c1~c20的醛或c3~c20的酮中的任意一种或者至少两种的组合。其中,c1~c20的醛可以是甲醛、乙醛、丙醛、丁醛、正戊醛、异戊醛、苯甲醛或苯乙醛等,c3~c20的酮可以是丙酮、丁酮、环丁酮、3-戊酮、环戊酮或环己酮等,以上化合物仅为简单举例,并不仅限于上述化合物。优选地,所述连续相为催化剂溶液。优选地,所述催化剂包括碱金属氢氧化物或胺类有机碱中的任意一种或至少两种的组合。其中,所述碱金属氢氧化物可以是氢氧化钠或氢氧化钾,所述胺类有机碱可以是乙胺、二甲基三胺、三甲胺或三乙胺等,以上化合物仅为简单举例,并不仅限于上述化合物。优选地,所述催化剂溶液的溶剂包括水、醇或酚中的任意一种或至少两种的组合。其中,所述醇可以是甲醇、乙醇、正丙醇、异丙醇、1-丁醇、2-丁醇、环戊醇或环己醇等,酚可以是取代或未取代的苯酚或萘酚等,以上化合物仅为简单举例,并不仅限于上述化合物。作为本发明优选的技术方案,所述醛缩合反应方法包括:分散相经第一分散,分散于流动相,所述分散相分散于所述连续相中的液滴直径小于100μm,得到反应物流;所述分散相为有机相,所述有机相包括c1~c20的醛或c3~c20的酮中的任意一种或者至少两种的组合;所述连续相为催化剂溶液,所述催化剂包括碱金属氢氧化物或胺类有机碱中的任意一种或至少两种的组合,所述催化剂溶液的溶剂包括水、醇或酚中的任意一种或至少两种的组合;所述反应物流进入反应装置进行反应后,分为循环物流以及反应产物物流,述循环物流以及反应产物物流的质量流量比大于8:1;所述循环物流经第二分散后返回所述反应装置;所述反应物流中的分散相通过所述反应装置横截面的表观液速小于0.1m/s。与现有技术相比,本发明至少具有以下有益效果:本发明提供一种醛缩合反应设备及反应方法,所述反应设备无需设置搅拌器以及分布器,简化了反应装置结构,降低了反应器设备及维护成本;所述反应方法可以强化醛缩合反应,提高了醛转化率以及烯醛产品收率。附图说明图1本发明提供的一种醛缩合反应设备的结构示意图;图2本发明提供的另一种醛缩合反应设备的结构示意图;图3本发明实施例1提供的醛缩合反应设备的结构示意图;图4本发明实施例2提供的醛缩合反应设备的结构示意图;图中:分散装置:f-1、f-2以及f-3,反应装置:r-1以及r-2,循环泵:p-1、p-2、p-3、p-4、p-5、p-6、p-7以及p-8,换热器:hx-1、hx-2、hx-3以及hx-4,层析器:d-1以及d-2,管路:101、102、103、104、105、106、107、108、109、110、111、112、201、202、203、204、205、206、207、208、209、210、211、212以及213。下面对本发明进一步详细说明。但下述的实例仅仅是本发明的简易例子,并不代表或限制本发明的权利保护范围,本发明的保护范围以权利要求书为准。具体实施方式下面结合附图并通过具体实施方式来进一步说明本发明的技术方案。为更好地说明本发明,便于理解本发明的技术方案,本发明的典型但非限制性的实施例如下:本发明具体实施方式部分提供一种醛缩合反应设备,其结构如图1所示,所述缩醛反应设备包括分散相管路、连续相管路、循环管路、反应装置r-1以及分散装置f-1;所述分散装置f-1、反应装置r-1、循环管路以及所述连续相管路依次循环连接;所述分散相管路与所述分散装置f-1进液口相连。所述分散装置f-1出液口与所述反应装置r-1进样口相连,所述反应装置r-1出样口与所述循环管路的入口相连,所述循环管路出口与所述连续相管路相连,所述连续相管路与所述分散装置f-1进液口相连,所述循环管路上沿循环物流方向依次设置有循环泵p-1以及换热器hx-1,所述循环管路上设置有反应产物出口。本发明具体实施方式部分提供另一种醛缩合反应设备,其结构如图2所示,所述缩醛反应设备包括分散相管路、连续相管路、循环管路、反应装置r-2、第一分散装置f-2以及第二分散装置f-3;所述反应装置r-2、循环管路以及第二分散装置f-3依次循环连接;所述分散相管路以及所述连续相管路分别独立地与所述第一分散装置f-2进液口相连;所述第一分散装置f-2出液口与所述反应装置r-2进样口相连。所述反应装置r-2出样口与所述循环管路的入口相连,所述循环管路出口与所述第二分散装置f-3进液口相连,所述第二分散装置f-3出液口与所述反应装置r-2进样口相连,所述循环管路上沿循环物流方向于所述第二分散装置f-3前依次设置有循环泵p-5以及换热器hx-4,所述循环管路上设置有反应产物出口。本发明中,所述产物经层析装置分离后,水相与循环物流合并后经分散返回反应器,有机相作为产品采出,并经后续提纯处理。本发明中,反应管路上设置有循环泵以及换热器等装置,所述循环泵以及换热器的位置可视生产的具体需要进行调整,其设置方式为本领域公知,在此不再赘述。实施例1本实施例提供一种醛缩合反应设备,其结构如图3所述,所述缩醛反应设备包括分散相管路、连续相管路、循环管路、反应装置r-1以及分散装置f-1;所述分散装置f-1、反应装置r-1、循环管路以及所述连续相管路依次循环连接;所述分散相管路101以及补充催化剂管路102分别独立地与所述分散装置f-1的进液口相连,所述分散装置f-1出液口与所述反应装置r-1进样口通过管路103相连,所述反应装置r-1出样口与所述循环管路上的循环泵p-1的进液口通过管路104相连,所述循环泵p-1的出液口与换热器hx-1的进液口通过管路105以及106相连,所述换热器hx-1的出液口与所述连续相管路通过管路107相连,所述连续相管路与所述分散装置f-1进液口通过管路112相连;所述循环管路上设置有产物出口,所述产物出口位于管路105以及106的连接处,所述产物出口与循环泵p-3的进液口相连,所述循环泵p-3的出液口与换热器hx-2的进液口通过管路108相连,所述换热器hx-2的出液口与层析器d-1通过管路109相连,所述层析器d-1的水相出口与循环泵p-2的进液口通过管路111相连,所述循环泵p-2的出液口连接至管路112,所述层析器d-1的有机相出口与循环泵p-4通过管路110相连。实施例2本发明具体实施方式部分提供一种醛缩合反应设备,其结构如图4所述,所述缩醛反应设备包括分散相管路、连续相管路、循环管路、反应装置r-2、第一分散装置f-2以及第二分散装置f-3;所述反应装置r-2、循环管路以及第二分散装置f-3依次循环连接;所述分散相管路201以及补充催化剂管路202分别独立地与所述第一分散装置f-2的进液口相连,所述第一分散装置f-2出液口与所述反应装置r-2进样口通过管路203相连。所述反应装置r-2出样口与所述循环管路上的循环泵p-5的进液口通过管路204相连,所述循环泵p-5的出液口与换热器hx-4的进液口通过管路205以及206相连,所述换热器hx-4的出液口与所述第二分散装置f-3的进液口通过管路208相连,所述第二分散装置f-3的出液口与所述反应装置r-2进样口通过管路209相连;所述循环管路上设置有产物出口,所述产物出口位于管路205以及206的连接处,所述产物出口与循环泵p-6的进液口相连,所述循环泵p-6的出液口与换热器hx-5的进液口通过管路207相连,所述换热器hx-5的出液口与层析器d-2通过管路210相连,所述层析器d-2的水相出口与循环泵p-7通过管路212相连,所述循环泵p-7的出液口与所述第二分散装置f-3的进液口通过管路213相连,所述层析器d-2的有机相出口与循环泵p-8通过管路211相连。实施例3本实施例提供一种醛缩合反应方法,所述反应方法使用实施例1提供的装置,所述方法包括以下步骤:来自管线101的混合戊醛(92%正戊醛,4.8%异戊醛,2.1%丁烯及丁烷,1.0%水,77kg/hr)与来自管线102的补充的naoh水溶液(30wt%naoh,维持反应液中naoh浓度在2%),来自hx-1的反应器循环物流以及来自管线112的循环naoh水溶液(循环水相与戊醛进料体积比约2:1),一同经过sk型的静态混合器,经过该静态混合器f-1后,混合戊醛以1-5μm大小的液滴分散在水相中,并经管线103,从反应器r-1底部进入r-1中。反应器r-1为100l的釜式反应器(液位80%),其内径为0.35m。反应器通过氮气维持0.4-0.6mpa的压力。反应温度为120℃。反应器上部液相通过循环泵p-1从反应器抽出后分为两股,大部分循环液相经过换热器hx-1冷却去除反应热后经管线107,与来自层析器d-1的循的催化剂水溶液混合,一同经过管线112与反应原料混合后通过混合器f-1后进入反应器中。从循环流股中抽出一股物流,作为反应产物流(循环物流与产物流的质量比为15:1)。在此条件下有机相经过反应器横截面的表观液速为0.005m/s。由泵p-3经管线110送入换热器hx-2通过冷却水冷却,后两相流通过层析器d-1进行分离,水相为催化剂溶液,通过泵p-2返回反应器中。有机相为产物癸烯醛及少量未反应戊醛,可送入储罐或进入加氢反应器中进行加氢反应后得到癸醇。对该装置一定时间内进出物流流量计量,结合各物流组成色谱分析结果,可以得到使用该装置进行反应后戊醛的转化率、癸烯醛(pba)产物的收率,具体结果可见表1。实施例4本实施例提供一种醛缩合反应方法,所述反应方法使用实施例2提供的装置,所述方法包括以下步骤:来自管线201的正丁醛(99.8%,120kg/hr)与来自管线202的补充的naoh水溶液(30wt%naoh,维持反应液中naoh浓度在2%),混合后一同经过气液分散器f-2。气液分散器f-2是由内外套管组成,内管为表面分布有微孔的陶瓷材料,外管为不锈钢,正丁醛经过内管壁以微液滴形式进入外管水相中。经过分散器f-2之后,正丁醛以100nm-1μm大小的液滴分散在水相中,并经管线203与来自管线209的反应器循环物流及来自层析器d-2的循环naoh水溶液的混合物流汇合后从反应器r-2底部进入。反应器r-2为100l的管式反应器,其内径为0.2m。反应器压力为自升压,温度为120℃。反应器两相混合物通过循环泵p-5抽出后分为两股(循环物流与产物流的质量比为20:1),在此条件下有机相经过反应器横截面的表观液速为0.032m/s。大部分循环液相经过换热器hx-4冷却水冷却去除反应热后,经管线208与来自层析器d-2底部的催化剂溶液混合后,经过气液分散器f-3(与f-2同类型),将水相中聚并的有机相液滴再次分散成100nm-1μm大小的微小液滴后,经管线209与来自203的反应原料混合后从底部进入反应器r-2中。从循环流股中抽出一股物流,作为反应产物流,由泵p-6经管线207送入换热器hx-5冷却后两相流通过层析器d-2层析分离,水相通过泵p-7后与循环物流混合后返回反应器中。有机相为产物辛烯醛及少量未反应丁醛,由泵p-8送入储罐或送入加氢反应器中进行加氢反应。对该装置一定时间内进出物流流量计量,结合各物流组成色谱分析结果,可以得到使用该装置进行反应后丁醛的转化率、辛烯醛产物的收率,具体结果可见表1。实施例5本实施例的工艺流程及使用的装置与实施例3相同。不同在于所使用的反应器为体积增大为15m3(液位80%),反应器内径2.0m。反应器循环物流(管线109物流)与产物流(管线110物流)的质量比为40:1。在此条件下有机相经过反应器横截面的表观液速为0.047m/s。反应进料混合戊醛流量调整为12000kg/hr。对该装置一定时间内进出物流流量计量,结合各物流组成色谱分析结果,可以得到使用该装置进行反应后戊醛的转化率、癸烯醛产物的收率,具体结果可见表1。对比例1本对比例采用与实施例1相同的实验条件,不同之处在于流程中取消液液分散设备,反应器更换为带气体分布器的搅拌釜。对比例2本对比例采用与实施例2相同的实验条件,不同之处在于,反应器改为多段串联直管,直径缩小为0.08m,在此条件下有机相经过反应器横截面的表观液速为0.2m/s。对比例3本对比例采用与实施例3相同的实验条件,不同之处在于,反应器循环物流(管线206物流)与产物流(管线207物流)的质量比为5:1。对比例1-3反应结果可见表1。表1原料烯烃醛转化率%烯醛产品收率%实施例3混合戊醛78.9%77.6%实施例4正丁醛84.7%84.1%实施例5混合戊醛76.5%75.6%对比例1混合戊醛75.2%74.4%对比例2正丁醛80.2%78.8%对比例3混合戊醛72.2%71.3%由实施例与对比例的实验结果比较可知,采用液液两相分散设备及强制大流量外循环的方式,实现了有机相在催化剂溶液中的高度分散,其醛转化率及产物的选择性均略高于传统的搅拌釜(对比例1)及管式反应器(对比例2)。当有机相经过反应器横截面的表观气速超过0.1m/s(对比例2)时,会影响合成气在反应液相中的分散效果,导致醛转化率及产物收率下降。反应器循环物流流量较低时(对比例3),同样会影响合成气在反应液相中的分散效果,导致醛转化率及产物选择性下降。这说明本发明对有机相经过反应器横截面的表观液速数值以及反应器循环物流与产物流的比值做出限定是非常必要的。本发明简化了反应器结构,降低了设备制造及维护成本,对于醛缩合反应具有重要突破。申请人声明,本发明通过上述实施例来说明本发明的详细结构特征,但本发明并不局限于上述详细结构特征,即不意味着本发明必须依赖上述详细结构特征才能实施。所属
技术领域:
的技术人员应该明了,对本发明的任何改进,对本发明所选用部件的等效替换以及辅助部件的增加、具体方式的选择等,均落在本发明的保护范围和公开范围之内。以上详细描述了本发明的优选实施方式,但是,本发明并不限于上述实施方式中的具体细节,在本发明的技术构思范围内,可以对本发明的技术方案进行多种简单变型,这些简单变型均属于本发明的保护范围。另外需要说明的是,在上述具体实施方式中所描述的各个具体技术特征,在不矛盾的情况下,可以通过任何合适的方式进行组合,为了避免不必要的重复,本发明对各种可能的组合方式不再另行说明。此外,本发明的各种不同的实施方式之间也可以进行任意组合,只要其不违背本发明的思想,其同样应当视为本发明所公开的内容。当前第1页12