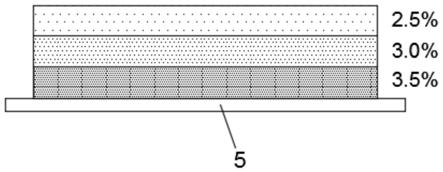
1.本发明涉及锂离子动力电池技术领域,具体涉及一种锂离子电池极片的涂布工艺及涂布装置。
背景技术:2.电池极片的涂布工艺是指将搅拌均匀的浆料均匀地涂覆在集流体上,并将浆料中的有机溶剂进行烘干的一种工艺。如专利cn110379997a公开了一种用于锂离子电池正负极片的涂布工艺,包括以下步骤:s1:称取巩源、锂源和钛源进行混合,在混合过程中,将混合液搅拌3小时形成透明溶胶,并加入稀释剂保持粘度,混合过程中温度为40
‑
130℃,放置3h后再进行二次搅拌;s2:将锂离子电池的正极活性材料或者负极活性材料与导电剂、粘结剂按一定比例混合,经过搅拌后得正极浆料或负极浆料;s3:将s1中的溶胶与s2中的溶胶按照一定比例混合搅拌后,进行烘干涂布。电池极片制造工艺包括浆料制备、浆料涂覆、极片辊压、极片分切、极片干燥等五道程序。
3.锂电池极片剥离强度是指极片活性物质与集流体黏附在一起的牢固程度,是锂电池极片重要指标之一,对电池的内阻和循环性能存在影响。粘结剂在浆料中是否均匀分散对极片的剥离强度起着至关重要的作用。均一的涂布浆料有利于提高极片的剥离强度。
4.在极片烘干过程中,sbr粘结剂及炭黑会随着溶剂蒸发而向表面迁移,使得极片内部产生了浓度梯度,尤其是在高速烘烤过程中。烘干的初始阶段,各成分在电极中均匀分布,而在干燥过程中,随着溶剂蒸发,在气液界面处存在浓度梯度,在固体颗粒层的表面会形成弯月面。溶剂通过毛细管力在石墨颗粒间向表面迁移,并且伴随着颗粒层的膨胀。sbr粘结剂的颗粒尺寸至少比石墨小100倍,石墨颗粒的间距足够让sbr自由移动,溶剂流动会带着聚合物和小颗粒sbr一起迁移上浮,使得粘结剂颗粒在极片的上层富集。而在高速烘烤情况下,从集流体到气液界面的粘结剂浓度梯度分布不断变大,在集流体与涂料区处粘结剂分布很少,影响粘结剂与箔材之间得粘结,这将直接导致极片剥离强度的下降,此外电极得内阻也会相应增大。这将直接影响到电池得电性能和寿命的发挥。因此,电池制作过程中,极片涂布工艺中减少因粘结剂迁移上浮的这种缺陷,提高涂布质量和良品率,降低制作成本,是锂电行业专业人员研发中需要解决的重要任务。
技术实现要素:5.本发明所要解决的技术问题在于解决现有的电池极片涂布过程中粘结剂迁移造成的粘结强度降低和极片内阻增大的问题。
6.本发明通过以下技术手段实现解决上述技术问题的:
7.一种锂离子电池极片的涂布工艺,包括以下步骤:
8.(1)将粘结剂原料分成质量呈梯度递减的若干份粘结剂;
9.(2)将步骤(1)中质量呈梯度递减的若干份粘结剂分别与若干份负极石墨浆料进行混合,即制得若干份含有不同质量浓度粘结剂的负极浆料;
10.(3)涂布时,按照负极浆料中粘结剂的质量浓度由高到底的顺序,先将含有高质量浓度粘结剂的负极浆料喷涂至箔材上,接着喷涂含有中等质量浓度粘结剂的负极浆料,最后喷涂含有最低质量浓度粘结剂的负极浆料;所述若干份含有不同质量浓度粘结剂的负极浆料的涂布厚度保持一致;
11.(4)涂布结束后烘烤至干。
12.本发明采用浓度梯度涂布的方式,按照负极浆料中粘结剂的质量浓度由高到底的顺序,依次将若干份负极浆料喷涂在箔材上,使得靠近箔材的下层粘结剂含量最高,远离箔材的上层粘结剂含量最低,在烘烤过程中,伴随着粘结剂的迁移上浮,靠近箔材的下层粘结剂含量变低,远离箔材的上层粘结剂含量变高,使得多层负极浆料中的粘结剂含量基本一致,粘结剂在极片中的分散变得均匀,改善了涂布过程中粘结剂颗粒随溶剂蒸发迁移上浮现象的方法,解决了锂离子电池因涂布过程中粘结剂迁移造成的粘结强度降低和极片内阻增大的问题。
13.优选地,所述若干份含有不同质量浓度粘结剂的负极浆料的涂布厚度保持一致。
14.优选地,所述箔材为铜箔,所述箔材的厚度为6
‑
8μm。
15.优选地,所述粘结剂包括丁苯橡胶(sbr)或丙烯酸类(paa)粘结剂。
16.优选地,所述负极石墨浆料中的石墨与导电剂的质量浓度比为95%:1%。
17.优选地,所述粘结剂分成三份。
18.本发明还提供一种使用上述锂离子电池极片的涂布工艺的装置,包括狭槽和若干个浆料罐;所述狭槽的进料端通过若干个管道分别与若干个浆料罐的出料端连通;每个管道上连接有真空泵;
19.若干份含有不同质量浓度粘结剂的负极浆料分别设置在若干个所述浆料罐内。
20.进一步地,所述狭槽内设置有若干道槽模,每道所述槽模的进料口分别与若干个管道的出料口连通。
21.进一步地,所述浆料罐设置有三个,所述狭槽的进料端通过三个管道分别与三个浆料罐的出料端连通。
22.进一步地,所述狭槽内设置有三道槽模。
23.本发明具有如下的有益效果:本发明采用浓度梯度涂布的方式,按照负极浆料中粘结剂的质量浓度由高到底的顺序,依次将若干份负极浆料在喷涂在箔材上,使得靠近箔材的下层粘结剂含量最高,远离箔材的上层粘结剂含量最低,在烘烤过程中,伴随着粘结剂的迁移上浮,靠近箔材的下层粘结剂含量变低,远离箔材的上层粘结剂含量变高,使得多层浆料中的粘结剂含量基本一致,粘结剂在极片中的分散变得均匀,改善了涂布过程中粘结剂颗粒随溶剂蒸发迁移上浮现象的方法,解决了锂离子电池因涂布过程中粘结剂迁移造成的粘结强度降低和极片内阻增大的问题。
附图说明
24.图1为本发明实施例的一种锂离子电池极片的涂布工艺使用的装置结构示意图;
25.图2为本发明实施例2的涂布后的电池极片中粘结剂分布示意图;
26.图3为本发明对比例的涂布后的电池极片中粘结剂分布示意图。
27.附图标号说明
28.1、狭槽;11、槽模;2、浆料罐;3、真空泵;4、圆辊;5、箔材。
具体实施方式
29.为使本发明实施例的目的、技术方案和优点更加清楚,下面将结合本发明实施例,对本发明实施例中的技术方案进行清楚、完整地描述,显然,所描述的实施例是本发明一部分实施例,而不是全部的实施例。基于本发明中的实施例,本领域普通技术人员在没有作出创造性劳动前提下所获得的所有其他实施例,都属于本发明保护的范围。
30.下述实施例中所用的试验材料和试剂等,如无特殊说明,均可从商业途径获得。
31.实施例中未注明具体技术或条件者,均可以按照本领域内的文献所描述的技术或条件或者按照产品说明书进行。
32.实施例1
33.如图1所示,本实施例公开了一种锂离子电池极片的涂布工艺使用的装置,包括狭槽1和三个浆料罐2;
34.如图1所示,本实施例的狭槽1内设置有三道槽模11,三道槽模11的进料口分别通过三个管道与三个浆料罐2的出料端连通,管道的一端与槽模11的进料口焊接固定并连通,管道的另一端与浆料罐2的出料口焊接固定并连通;
35.如图1所示,本实施例的每个管道上分别装配有真空泵3。
36.本实施例的三个浆料罐2内分别装有质量浓度呈梯度递减的高质量浓度粘结剂的负极浆料、中等质量浓度粘结剂的负极浆料和最低质量浓度粘结剂的负极浆料。
37.涂布时,需要先将箔材5置于圆辊4上,然后按照三个浆料罐2中的负极浆料中的粘结剂的含量不同,按照负极浆料中粘结剂的质量浓度由高到底的顺序,先后启动三个真空泵3打开,三个浆料罐2内的负极浆料分别通过三个管道进入到狭槽1的三道槽模11,三道槽模11可分别进行负极浆料的喷涂,先将含有高质量浓度粘结剂的负极浆料喷涂至箔材5上,接着喷涂含有中等质量浓度粘结剂的负极浆料,最后喷涂含有最低质量浓度粘结剂的负极浆料,并保证三份负极浆料的涂布厚度相同。
38.实施例2
39.一种锂离子电池极片的涂布工艺,包括以下步骤:
40.(1)将sbr粘结剂分成质量呈梯度递减的三份粘结剂,使得三份粘结剂的质量比为3.5:3:2.5;
41.(2)将步骤(1)中质量比为3.5:3:2.5的三份粘结剂分别与三份负极石墨浆料进行混合,即制得三份含有不同质量浓度粘结剂的负极浆料,其中,第一份负极浆料中各组分的的质量浓度比为石墨:导电剂:粘结剂:cmc=95%:1%:3.5%:0.5%,第二份负极浆料中各组分的的质量浓度比为石墨:导电剂:粘结剂:cmc=95%:1%:3%:1%,第三份95%:1%:3.5=95%:1%:2.5%:1.5%,保持电池极片总的粘结剂使用量不变;
42.(3)将制得三份负极浆料分别装入涂布装置的三个浆料罐2内;
43.(4)涂布时,按照负极浆料中粘结剂的质量浓度由高到底的顺序,先将第一份负极浆料喷涂至箔材5上,本实施例的箔材5的厚度为6μm,接着喷涂第二份负极浆料,最后喷涂第三份负极浆料,使得未烘烤前实验组极片中粘结剂含量为浓度梯度分布,靠近箔材的下层粘结剂含量为3.5%,中间浓度为3%,远离箔材的上层粘结剂含量为2.5%;保证这三份
负极浆料的涂布厚度相同,涂布后的电池极片中粘结剂分布如图2所示。
44.实施例3
45.一种锂离子电池极片的涂布工艺,包括以下步骤:
46.(1)将paa粘结剂分成质量呈梯度递减的三份粘结剂,使得三份粘结剂的质量比为3.5:3:2.5;
47.(2)将步骤(1)中质量比为3.5:3:2.5的三份粘结剂分别与三份负极石墨浆料进行混合,即制得三份含有不同质量浓度粘结剂的负极浆料,其中,第一份负极浆料中各组分的的质量浓度比为石墨:导电剂:粘结剂:cmc=95%:1%:3.5%:0.5%,第二份负极浆料中各组分的的质量浓度比为石墨:导电剂:粘结剂:cmc=95%:1%:3%:1%,第三份95%:1%:3.5=95%:1%:2.5%:1.5%,保持电池极片总的粘结剂使用量不变;
48.(3)将制得三份负极浆料分别装入涂布装置的三个浆料罐2内;
49.(4)涂布时,按照负极浆料中粘结剂的质量浓度由高到底的顺序,先将第一份负极浆料喷涂至箔材5上,本实施例的箔材5的厚度为7μm,接着喷涂第二份负极浆料,最后喷涂第三份负极浆料,使得未烘烤前实验组极片中粘结剂含量为浓度梯度分布,靠近箔材的下层粘结剂含量为3.5%,中间浓度为3%,远离箔材的上层粘结剂含量为2.5%;保证这三份负极浆料的涂布厚度相同。
50.对比例
51.本对比例使用6um的铜箔,使用粘结剂为丁苯橡胶(sbr),使用的负极浆料中各成分的质量浓度之比为石墨:导电剂:粘结剂:cmc=95%:1%:3%:1%,制备得到的未烘烤前极片中粘结剂含量为3%,涂布后的电池极片中粘结剂分布如图3所示。
52.实施例4
53.将实施例2(实验组)和对比例(对比组)涂布后的电池极片置于相同的烘烤速率、烘烤温度、烘烤时间、风量等条件下烘干,烘烤速率为8m/min、烘烤温度为75℃/85℃梯度烘烤、烘烤时间为4min、风量为25
±
10hz,相同的条件下检测对比组和实验组极片辊压前后的剥离强度和电阻率,并对烘烤后的对比组和实验组的新鲜极片做oso4染色成像测试,观察粘结剂在极片中的分布,以及制备成相同规格的电池后检测对比组和实验组电池的交流内阻大小。
54.进一步分析,实验结果如下表1所示,对比组极片其辊压前后的剥离均低于实验组,实验组电阻率低于对比组,实验组电池的交流内阻也明显低于对比组,说明采用粘结剂含量梯度涂布的方法有效改善了极片的剥离强度和内阻;进一步地,烘烤后的对比组和实验组的新鲜极片oso4染色成像图像表明,对比组粘结剂在烘烤过程中发生了迁移上浮,上层粘结剂成像红色明显较深,下层粘结剂成像颜色较淡,而实验组极片成像上中下层颜色基本一致,粘结剂分散较为均匀,与实验结果相符合。
55.表1为对比组和实验组极片辊压后剥离强度和电阻率对比结果
[0056][0057][0058]
综上,本发明采用浓度梯度涂布的方式,按照负极浆料中粘结剂的质量浓度由高到底的顺序,依次将若干份负极浆料喷涂在箔材5上,使得靠近箔材5的下层粘结剂含量最高,远离箔材5的上层粘结剂含量最低,在烘烤过程中,伴随着粘结剂的迁移上浮,靠近箔材5的下层粘结剂含量变低,远离箔材5的上层粘结剂含量变高,使得多层浆料中的粘结剂含量基本一致,粘结剂在极片中的分散变得均匀,改善了涂布过程中粘结剂颗粒随溶剂蒸发迁移上浮现象的方法,解决了锂离子电池因涂布过程中粘结剂迁移造成的粘结强度降低和极片内阻增大的问题。
[0059]
以上实施例仅用以说明本发明的技术方案,而非对其限制;尽管参照前述实施例对本发明进行了详细的说明,本领域的普通技术人员应当理解:其依然可以对前述各实施例所记载的技术方案进行修改,或者对其中部分技术特征进行等同替换;而这些修改或者替换,并不使相应技术方案的本质脱离本发明各实施例技术方案的精神和范围。