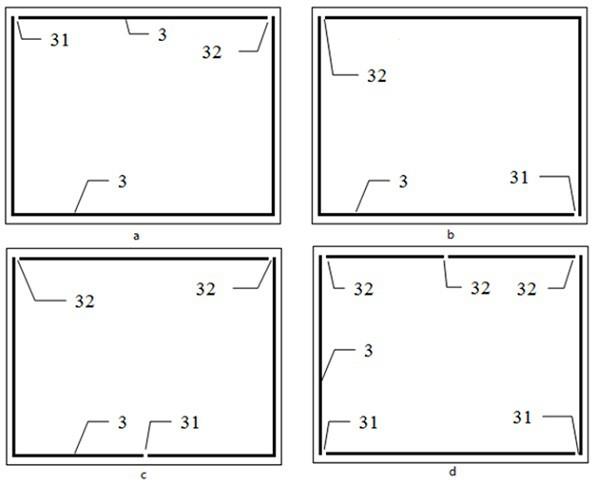
1.本发明涉及显示面板水胶贴合相关技术领域,具体为一种适合水胶灌胶贴合的面板组及其渐次逼近灌胶方法。
背景技术:2.灌胶是一种正在开始应用于显示面板贴合,尤其是大面板贴合的特殊水胶贴合方法,由于设备投入省,溢胶及贴合气泡的可控性高,越来越受欢迎,而现有的灌胶贴合方法,普遍采用在下基板的周边先制作一圈粘合框,然后上下基板对位贴合粘接成待灌胶的面板组,其显著特点是“为适应灌胶过程中进胶并同时排出面板腔体内空气的需要,而待灌胶贴合的面板组的周边粘合框,至少预留了二个缺口,分别对应一个进胶口和一个排气口,从而制作的面板组的待灌胶腔体,是非密闭的”,而现代中的现有技术手段,如图2,仅列举了几组对应进胶口和排气口的缺口示例,其中位置31对应进胶位置,位置32对应排气位置;图2a中,单边二端有二个预留的缺口;图2b中,对边中点各有一个缺口;图2c中,单边二端及对边中点共有三个缺口;图2d中,单边二端和其中点,对边二端共有五个缺口;图2中,这种预留的缺口存在的最大问题是:在灌胶贴口过程中,缺口很容易产生溢胶和贴合气泡;为此,在实际灌胶过程中,采取的典型补救措施是:1.对进胶位置和排气缺口,进行特殊的处理,以便提高缺口和连接管路之间的密封性,但会增加额外工艺或工装夹具设计制作成本;2.后续增加溢胶清洁、除泡等工艺流程,但会直接提高生产成本;专利申请号为“cn201811305561.7”的“一种触摸屏基板和显示屏的水胶贴合工艺”,涉及一种在触摸屏基板和显示屏之间用泡棉胶带粘合形成空腔,然后灌胶进空腔的贴合方法,其明显的缺点是:对进胶口和排气口没有进行特殊的处理,从而不可避免地产生溢胶。为此,工艺结束后,必须对贴合产品进行溢胶清洁,且用泡棉胶带粘合形成空腔,在灌胶过程中很容易在四周形成贴合气泡,所以为提高成品率,还需用专门设备对贴合产品进行除泡;而申请号为“201910075239.8”的“一种显示屏水胶贴合工艺及设备”,也涉及一种灌胶贴合设备和方法,其再明显的缺点是:虽然通过进胶组件和排气组件对进胶口和排气口进行特殊的防溢胶和气泡处理,但面板组贴合完成后,在进胶组件和排气组件位置需进行补胶并固化,在增加工艺流程并延长生产周期的同时,增加了工装辅助夹具的设计、制作、使用成本,此外其设备投入也比较大。
3.而申请号为“cn201811157338.2”的“一种显示面板的集成灌胶贴合装置及贴合方法”及申请号为“cn202011215735.8”的“一种可流水化作业的显示面板水胶灌胶贴合装置和方法”,通过在设计位置预埋透明胶管,作为进胶口和排气口的方法,尽管避免了上述技术中存在的进胶口和排气口的溢胶及漏气等问题,但还存在下述不足:1、由于进胶口和排气口都只有一个,且位置确定,为保证灌胶过程中的腔内空气都能从上述排气口排出,需要在整个面板组的灌胶过程中,配合面板倾角、进胶压力、灌胶速度等的调整,对灌胶进行严格控制,制程复杂;
2、无法实行面板平置进行灌胶,而斜置竖立灌胶,因重力作用,会使下方灌胶腔体外扩,胶水下沉聚集,后续使胶水流平,达到腔体胶层厚度均匀的时间会很长,贴合面板尺寸越大,难度越大,尤其不适合采用双组份热固化水胶来灌胶贴合大尺寸面板组;3、上述技术更是其无法用增加进胶口来提高灌胶贴合产能;4、在设计位置预埋透明胶管,作为进胶口和排气口的方法,也增加了贴合工艺流程和成本。
技术实现要素:4.本发明的目的在于提供一种适合水胶灌胶贴合的面板组及制作和面板贴合方法,以达到避免现有技术中的贴合除泡、溢胶清洁处理、灌胶贴合后补胶再固化等缺陷的同时,使显示面板水胶灌胶贴合的产生流程更简单,效率和产能更高,成本更低,从而降低设备和生产投入,提高经济效益的优点。
5.为实现上述目的,本发明提供如下技术方案:一种适合水胶灌胶贴合的面板组及制作和面板贴合方法,包括上基板、下基板和粘合框,所述上基板通过粘合框与下基板组合为密封状,所述上基板通过粘合框与下基板组合内部形成待灌胶腔体,所述上基板、下基板、粘合框和待灌胶腔体组合为面板组。
6.优选的,所述粘合框采用双面带胶弹性材料,所述双面带胶弹性材料优选高可压缩泡棉材料,所述面板组在四周用双面带胶弹性材料粘贴密封制成。
7.优选的,所述粘合框为可紫外或热固化的液态硅胶,通过图形点胶、上基板和下基板对位贴合和固化制成,并形成待灌胶腔体。
8.优选的,所述粘合框制程步骤包括:(a)先根据待灌胶腔体的高度要求,在上基板或下基板上,也可分别在二个基板上,按设计图形经过点胶、固化成基框;(b)再选其中一个基板或基板的成形基框上,经二次点胶,对位贴合,并使面板组翻转固化,而成形,并制成待灌胶腔体;(c)也可上基板和下基板在二次点胶后,先翻转对位贴合,再固化成形,第二次点胶的基板,先选还没有经点胶的另一基板,所述基框可多次点胶、固化而成。
9.优选的,所述粘合框中的设计进胶和排气位置被针尖状的空心针头插入形成进胶口和排气口,所述空心针头的后端连接有连接管道,所述进胶口向面板组进行灌胶的同时,通过排气口排出面板组密封腔体内的空气,再让面板组水平静置至胶水流平后,拔出进胶口和排气口的空心针头,并经胶水固化,完成面板组的灌胶贴合。
10.优选的,所述面板组的更进一步贴合方法包括以下步骤:第一步,先在上述粘合框的上下边中点位置,分别插入连接管道的空心针头制成第一个进胶口和第一个排气口,并通过上述第一个进胶口进行灌胶;第二步,根据已灌胶腔体内胶水轮廓线及延伸进程,在第一个进胶口二侧粘合框的对称位置,分别通过插入连接管道的空心针头,建立二个对称进胶口,同时进行灌胶;第三步,用第二步的方法,不断向上述第一个排气口,延伸建立新的对称进胶口进行灌胶,直到地胶水快逼近上述排气口;第四步,根据上述排气口周围存留空气的分布,通过插入空心针头,建立第二个排
气口或后续排气口,直到胶满上述待灌胶腔体,排气口内侧无存留气泡,灌胶结束;第五步,基板水平静置,待胶水流平,胶层厚度均匀,拨出所有进胶口和出胶口的空心针头,并对腔体内的胶水进行固化,面板组水胶贴合制程结束。
11.优选的,所述空心针头直接连接的管道是透明的,至少在排气口,紧邻上述空心针头后一段排气管道是透明的。
12.与现有技术相比,本发明的有益效果是:该适合水胶灌胶贴合的面板组及制作和面板贴合方法:1.用空心针头,插入待灌胶面板组周边弹性粘合框相应设计位置,从而直接形成进胶口和排气口的技术方法,方便实用,简单可靠。
13.2.进胶口和排气口,由于针头和弹性粘合框之间的自然紧密结合,消除了进胶口和排气口的溢胶及贴合气泡隐患,避免了溢胶清洁、设备除泡或后续补胶等不必要的工艺流程和生产工艺及设备投入。
14.3.进胶口和排气口的位置和数量灵活可调,非常方便灌胶工艺控制、贴合气泡消除、灌胶生产效率的提高。
15.4.可通过面板平置状态进行灌胶,减少胶水在腔体内的静置流平时间,也可通过增加进胶口来提高灌胶贴合生产效率。
附图说明
16.图1为本发明面板组正剖视结构示意图;图2为待灌胶腔体非密闭的现有技术制作的面板组粘合框缺口示例图;图3为本发明整体无缺口粘合框俯剖视结构示意图;图4为本发明空心针头扎入粘合框构成进胶口或排气口正剖视结构示意图;图5为待灌胶腔体密闭的面板组中粘合框设计进胶及排气位置示例图1;图6为待灌胶腔体密闭的面板组中粘合框设计进胶及排气位置示例图2;图7为待灌胶腔体密闭的面板组中粘合框设计进胶及排气位置示例图3。
17.图中:1、上基板;2、下基板;3、粘合框;31、进胶位置;32、排气位置;4、待灌胶腔体;5、连接管道;6、空心针头。
具体实施方式
18.下面将结合本发明实施例,对本发明实施例中的技术方案进行清楚、完整地描述,显然,所描述的实施例仅仅是本发明一部分实施例,而不是全部的实施例。基于本发明中的实施例,本领域普通技术人员在没有做出创造性劳动前提下所获得的所有其他实施例,都属于本发明保护的范围。
19.本发明提供一种技术方案:一种适合水胶灌胶贴合的面板组及制作和面板贴合方法,包括上基板1、下基板2和粘合框3,上基板1通过粘合框3与下基板2组合为密封状,上基板1通过粘合框3与下基板2组合内部形成待灌胶腔体4,上基板1、下基板2、粘合框3和待灌胶腔体4组合为面板组。
20.粘合框3采用双面带胶弹性材料,双面带胶弹性材料优选高可压缩泡棉材料,面板组在四周用双面带胶弹性材料粘贴密封制成。
21.粘合框3为可紫外或热固化的液态硅胶,通过图形点胶、上基板1和下基板2对位贴合和固化制成,并形成待灌胶腔体4。
22.粘合框3制程步骤包括:a先根据待灌胶腔体4的高度要求,在上基板1或下基板2上,也可分别在二个基板上,按设计图形经过点胶、固化成基框;b再选其中一个基板或基板的成形基框上,经二次点胶,对位贴合,并使面板组翻转固化,而成形,并制成待灌胶腔体4;c也可上基板1和下基板2在二次点胶后,先翻转对位贴合,再固化成形,第二次点胶的基板,先选还没有经点胶的另一基板,基框可多次点胶、固化而成。
23.粘合框3中的设计进胶和排气位置被针尖状的空心针头6形成进胶口和排气口,空心针头6的后端,进胶口向面板组进行灌胶的同时,通过排气口排出面板组密封腔体内的空气,再让面板组水平静置至胶水流平后,拔出进胶口和排气口的空心针头6,并经胶水固化,完成面板组的灌胶贴合。
24.面板组的更进一步贴合方法包括以下步骤:第一步,先在上述粘合框3的上下边中点位置,分别插入连接管道5的空心针头6制成第一个进胶口和第一个排气口,并通过上述第一个进胶口进行灌胶;第二步,根据已灌胶腔体内胶水轮廓线及延伸进程,在第一个进胶口二侧粘合框3的对称位置,分别通过插入连接管道5的空心针头6,建立二个对称进胶口,同时进行灌胶;第三步,用第二步的方法,不断向上述第一个排气口,延伸建立新的对称进胶口进行灌胶,直到地胶水快逼近上述排气口;第四步,根据上述排气口周围存留空气的分布,通过插入空心针头6,建立第二个排气口或后续排气口,直到胶满上述待灌胶腔体4,排气口内侧无存留气泡,灌胶结束;第五步,基板水平静置,待胶水流平,胶层厚度均匀,拨出所有进胶口和出胶口的空心针头,并对腔体内的胶水进行固化,面板组水胶贴合制程结束。
25.空心针头6直接连接的管道是透明的,至少在排气口,紧邻上述空心针头6后一段排气管道是透明的。
26.对照图1,上基板1、下基板2,通过周边一圈粘合框3组成的待灌胶贴合的面板组,包括了待灌胶腔体4。
27.对照图2,现有技术制作的包括非密闭的待灌胶腔体4的面板组粘合框缺口示例对应进胶位置31和排气位置32,图2a中,单边二端有二个预留的缺口;图2b中,待灌胶腔体4的对角位置各有一个缺口;图2c中,单边二端及对边中点共有三个缺口;图2d中,单边二端拐角和其中点,及对边二端拐角共有五个缺口。
28.对照图3,待灌胶腔体密闭的面板组中的粘合框3无缺口,在灌胶前的待灌胶腔体4处于密闭状态。
29.对照图4,连接管道5在前端成针尖状的空心针头6,直接插入粘合框3中的设计位置,从而可形成一个进胶口或排气口,其中连接管道5对应进胶管道或排气管道。
30.对照图5,面板组粘合框3中,可形成一个进胶口和一个排气口的设计进胶位置31及排气缺口32示例。
31.对照图6,面板组粘合框3中,可形成一个进胶口和二个排气口的设计进胶位置31
及排气缺口32示例,一个设计进胶位置31,在底边的中点,二个排气口的排气缺口32,在对边二端角点。
32.对照图7,面板组粘合框3中,可形成二个进胶口和三个排气口的设计进胶位置31及排气缺口32示例,二个设计进胶位置31,在一边二端拐角点,三个排气口的设计排气缺口32,在对边中点及其二端拐角点。
33.实施例一:一种适合水胶灌胶贴合的面板组,如图1,面板组包括上基板1、下基板2、粘合上下基板的一圈周边粘合框3,如图3所示,用一圈周边粘合框3粘合组成的面板组的待灌胶腔体4是密封的,如图2所示,周边粘合框3中没有特别制作的进胶及排气用缺口。
34.面板组周边一圈密封的粘合框3,可用双面带胶泡棉,也可用其它双面粘性的弹性材料,粘接上基板1、下基板2而成。
35.如图4,用一种连接管道5,并在前端成针尖状的空心针头6,直接插入粘合框3中设计的进胶位置31,从而形成一个进胶口,如图5;用后端连接排气管道5的空心针头6,直接插入设计的粘合框3中排气位置32,形成一个排气口,通过进胶口向面板组进行灌胶,同时通过排气口完全排出面板组腔内空气,再经面板组水平静置至胶水流平,从粘合框3的进胶位置31和排气位置32拔出空心针头6,然后经胶水固化,完成面板组的灌胶贴合。
36.插入面板组粘合框3的空心针头6直接连接的连接管道5是透明的,至少紧邻管道与空心针头6连接部的后一段连接管道5是透明的,更进一步,至少在排气口,紧邻连接部的后一段连接管道5是透明的,通过透明连接管道5,可监控溢胶,从而控制进胶,当透明连接管道5中出现胶水时,可立刻停止进胶口的灌胶。
37.用一种后端连接管道5并前端成针尖状的空心针头6,直接插入粘合框3相应位置,从而形成的进胶口和排气口,可以各有几个,但至少进胶口和排气口各有一个。
38.具有一个进胶口和一个排气口的设计,及一个进胶口和一个排气口生成方法,包括相应的灌胶贴合方法,构成本发明的实施例一。
39.实施例二:在实施例一中,粘合框3,优选采用可固化液态硅胶,按设计图形,采用点胶、上下基板对位贴合、再固化的流程制成,如图2所示,粘合框3中四周没有特别制作的进胶及排气用缺口,从而造成的待灌胶腔体4是密封的,但设计的进胶位置31和排气位置32,共有3个,如图6所示。
40.按图6的一个设计进胶位置31在底边的中点,用后端连接进胶管道5的空心针头6,直接插入设计的粘合框3中进胶位置31,形成一个进胶口,排气位置32,在进胶位置31的对边二端拐角,采用空心针头6,直接插入粘合框3的二端角点设计位置32,形成二个排气口,构成本发明的实施例二。
41.实施例三:在实施例二中,一圈周边硅胶框3,是先经过在第2基板上点胶固化成框,再在已固化的框体上实施二次点胶,然后上下基板对位贴合,并使面板组翻转固化,制成灌胶腔体4密封的面板组,也可上下基板先翻转贴合,再固化,制成待灌胶腔体4密封的面板组,第二次点胶的基板,先选还没有经点胶的另一基板。
42.工艺制作的硅胶粘合框3中,如图7所示,在设计进胶位置31和排气位置32,采用空
心针头6,直接插入粘合框3,从而在一边二端角点设计位置31形成二个进胶口,在对边中点及二端角点设计位置32,形成三个排气口,构成本发明的实施例三。
43.实施例四在实施例二中,一圈周边硅胶框3,事先在上基板1和下基板2上,按设计图形经过点胶、固化成基框;然后再选其中一个基板或基板的成形基框上,经二次点胶,对位贴合,并使面板组翻转固化,而成形,并制成待灌胶腔体。所述基框可多次点胶、固化而成。
44.上述面板组贴合方法,包括:第一步,先在上述粘合框3的上下边中点位置,分别插入连接管道5的空心针头6制成第一个进胶口和第一个排气口,并通过上述第一个进胶口进行灌胶;第二步,根据上述已灌胶腔体内胶水轮廓线及延伸进程,在第一个进胶口二侧粘合框3的对称位置,分别通过插入连接管道5的空心针头6,建立二个对称进胶口,交同时进行灌胶;第三步,用第二步的方法,不断向上述第一个排气口,延伸建立新的对称进胶口进行灌胶,直到地胶水快逼近上述排气口;第四步,根据上述排气口周围存留空气的分布,通过插入空心针头6,建立第二个排气口或后续排气口,直到胶满上述待灌胶腔体4,排气口内侧无存留气泡,灌胶结束;最后,基板水平静置,待胶水流平,胶层厚度均匀,拨出所有进胶口和出胶口的空心针头,并对腔体内的胶水进行固化,面板组水胶贴合制程结束,构成本发明的实施例四,本实施例尤其适合大尺寸、甚至超大尺寸面板组的水胶灌胶贴合。
45.以上所述仅是本发明的优选实施方式,应当指出:对于本技术领域的普通技术人员来说,在不脱离本发明原理的前提下,还可以做出若干改进和润饰,这些改进和润饰也应视为本发明的保护范围。
46.尽管已经示出和描述了本发明的实施例,对于本领域的普通技术人员而言,可以理解在不脱离本发明的原理和精神的情况下可以对这些实施例进行多种变化、修改、替换和变型,本发明的范围由所附权利要求及其等同物限定。