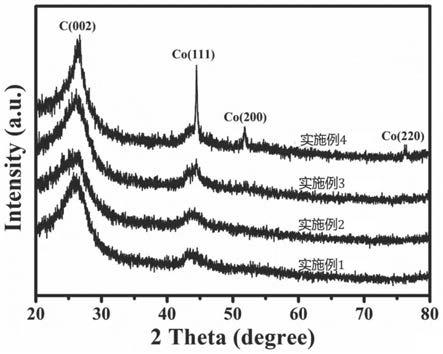
co/3dng催化剂制备及应用于催化氧化木质素及其
β
‑
o
‑
4模型化合物方法
技术领域
1.本发明涉及的是催化剂制备和生物质转化领域的技术,具体是一种利用水热
‑
浸渍
‑
热解法制备三维氮掺杂石墨烯负载钴纳米粒子(co/3dng)催化剂及其在木质素及其β
‑
o
‑
4模型化合物氧化转化中的应用。
背景技术:2.木质素是自然界中储量仅次于纤维素、且含有天然芳香环结构的生物质资源,可以通过氧化解聚得到多官能团的单体化合物,为有机化工和制药工业提供官能化的单体和低聚物原料。多年来人们致力于通过选择合适的催化剂,打断β
‑
o
‑
4连接结构,从而实现木质素的高附加利用。现有的木质素及其β
‑
o
‑
4模型化合物催化氧化解聚中,非金属钴基催化剂具有成本低,资源丰富等优点,以及在碱性条件下相对较好的耐腐蚀性能,有望成为潜在的催化木质素氧化降解的催化剂之一。luo等人(luo h.,wang l.,li g.,et al.nitrogen
‑
doped carbon
‑
modified cobalt
‑
nanoparticle
‑
catalyzed oxidative cleavage of ligninβ
‑
o
‑
4model compounds under mild conditions[j].acs sustainable chem.eng,2018,6:14188
‑
14196.)通过裂解负载于活性炭上的维生素b12制备得到氮掺杂碳材料负载co纳米粒子催化剂,该催化剂在添加无机碱k2co3作为助剂的条件下,对β
‑
o
‑
4模型化合物(2
‑
苯氧基
‑1‑
苯乙醇)的催化氧化表现出良好的催化活性,β
‑
o
‑
4模型化合物转化率和产物苯酚产率为96%。然而,该在不添加k2co3的条件下,β
‑
o
‑
4模型化合物转化率和苯酚产率仅为19%。
技术实现要素:[0003]
本发明针对上述现有技术中存在的不足和缺点,提出一种co/3dng催化剂制备及应用于催化氧化木质素及其β
‑
o
‑
4模型化合物方法,在不添加任何无机碱的条件下进行木质素及其β
‑
o
‑
4模型化合物氧化解聚,表现出了优异的催化活性和选择性。
[0004]
本发明是通过以下技术方案实现的:
[0005]
本发明涉及一种co/3dng催化剂的制备方法,通过将氧化石墨烯(go)分散液与氨水混合并经水热得到三维氮掺杂石墨烯(3dng)后,将3dng浸渍于co盐溶液中,再将浸渍产物冷冻干燥并高温裂解制备得到co/3dng。
[0006]
所述的氧化石墨烯分散液浓度为2
‑
5mg/ml,用量为20ml。
[0007]
所述的氨水浓度为25
‑
28%,氨水用量与氧化石墨烯比例为(0.5
‑
2)ml:(40
‑
100)mg。
[0008]
所述的水热,具体为:将go分散液、氨水依次加热水釜并充分搅拌,再将水热釜转移至烘箱,加热至180℃并保温12h后自然冷却至室温。
[0009]
所述的水热,优选在冷却后将产物体系离心分离,并用去离子水洗涤至ph=7。
[0010]
所述的浸渍,具体为:将去离子水和无水乙醇依次加入钴盐中并充分搅拌,再将
3dng浸入溶液中静置2
‑
24h。
[0011]
所述的浸渍,优选时间12
‑
24h。
[0012]
所述的浸渍,优选在静置后将产物体系离心分离,并用去乙醇和离子水交替洗涤,优选为交替洗涤3次。
[0013]
所述的去离子水和无水乙醇的体积比为1:0
‑
1:7,优选为1:0
‑
1:3。
[0014]
所述的钴盐为co(ch3coo)2·
4h2o、co(no3)2·
6h2o、cocl2·
6h2o或coso4·
7h2o,优选co(ch3coo)2·
4h2o,用量为10
‑
60mg。
[0015]
所述的冷冻干燥是指:将浸渍后的产物降温至
‑
80℃,具体为:将浸渍后的产物冷冻至
‑
25℃后,再通过冷冻干燥机进一步降温至
‑
80℃并干燥12h。
[0016]
所述的高温裂解是指:将冷冻干燥后的产物在n2氛围下加热并保温,具体为:将干燥后的样品置于管式炉石英管加热区,密闭后抽真空、通入n2置换若干次并充入n2,再以5℃/min的升温速率升至600
‑
1000℃并保温60min。
[0017]
本发明涉及上述方法制备得到的co/3dng催化剂,具有三维网络结构,且co纳米颗粒均匀分布在三维石墨烯表面。
[0018]
本发明涉及上述co/3dng催化剂的应用,将其用于催化氧化木质素及其模型化合物,具体为:将co/3dng催化剂、木质素或木质素模型化合物及甲醇在氧气环境下高压加热反应实现催化氧化,并进行产物分析。
[0019]
所述的氧气环境,具体通过将聚四氟乙烯容器密闭后,通入氧气置换若干次并充入氧气至反应初始压力为0.1
‑
0.3mpa,优选氧气初始压力0.2mpa。
[0020]
所述的高压加热反应,在氧气环境下,搅拌同时加热升温至80
‑
120℃并反应1
‑
12h,优选反应温度120℃。
[0021]
所述的木质素为溶剂型木质素、碱性木质素或木质素磺酸盐,优选溶剂型木质素。
[0022]
所述的木质素β
‑
o
‑
4模型化合物为2
‑
苯氧基
‑1‑
苯乙醇。
[0023]
所述的co/3dng催化剂、木质素或木质素模型化合物与甲醇的比例为(20
‑
50)mg:(50
‑
100)mg:(5
‑
10)ml或(0.5
‑
3)mg:(0.01
‑
0.05)mmol:(2
‑
5)ml。
[0024]
所述的产物分析,待反应结束降至室温,利用磁铁直接回收催化剂co/3dng,并收集液体产物后,用液相色谱
‑
质谱联用仪和液相色谱仪分别对得到的液体产物进行定性和定量检测,具体包括:通过外标法做出各产物的标准曲线,根据标准曲线计算,最终得到各种产物的浓度分布,进而计算转化率及产率。技术效果
[0025]
本发明整体解决了现有催化剂需要在添加无机碱的条件下才能有效地催化氧化木质素及其模型化合物转化的问题以及填补了以三维氮掺杂石墨烯为载体,以co盐前驱体,通过浸渍
‑
裂解的方法得到co/3dng催化剂,用于木质素及其β
‑
o
‑
4模型化合物氧化解聚的技术空白。
[0026]
与现有技术相比,本发明采用水热
‑
浸渍
‑
裂解方法,可以简单、快速制备出co/3dng催化剂。在不添加任何碱的条件下,在0.2mpa o2、120℃、6小时的反应条件下,对木质素β
‑
o
‑
4模型化合物2
‑
苯氧基
‑1‑
苯乙醇的转化率高达97%,主产物苯酚的产率97%,选择性为100%。且本发明制备的co/3dng催化剂具有良好磁性,利用磁铁可直接回收循环利用。
附图说明
[0027]
图1为实施例制备得到的co/3dng x射线衍射(xrd)图;
[0028]
图2为实施例制备得到的co/3dng扫描电子显微镜(sem)图;
[0029]
图2中:abcd依次为各个实施例。
具体实施方式
实施例1
[0030]
本实施例具体包括以下步骤:
[0031]
步骤1、将20ml,2mg/ml go分散液加入40ml水热釜,再量取0.5ml nh3·
h2o加入go分散液中,并充分搅拌混合5min。然后,将反应釜转移至烘箱,加热至180℃,并保温12h。待反应结束,反应釜自然冷却后,将产物体系进行离心分离,并用去离子水洗涤至中性ph=7,保存于去离子水中备用。将得到的产物命名为3dng。
[0032]
步骤2、称取10mg co(ch3coo)2·
4h2o,依次量取7ml去离子水,7ml无水乙醇加入,并充分搅拌10min。再将3dng浸渍于co盐溶液中,并静置24h。然后,将浸渍后的3dng在乙醇和水的混合溶液(1:1)中进行多次洗涤后,将产物放入冰箱(
‑
25℃)冷冻12h,最后将产物置于冷冻干燥机中在
‑
80℃下干燥12h。
[0033]
步骤3、将冷冻干燥后的样品放置于管式炉加热区,密闭后,抽真空通入n2置换3次,然后充入n2,以5℃/min的升温速率升至600℃,并保温60min。待反应结束,系统自然冷却后将样品从管式炉中取出。将得到的产物命名为co/3dng
‑
600。
[0034]
如图1所示,xrd结果表明,co/3dng
‑
600中除了石墨烯宽的(002)衍射峰外,在44.39
°
处出现的宽衍射峰对应金属co(jcpds no.15
‑
0806)的(111)晶面,实验制备得到的石墨烯负载co纳米粒子复合材料。
[0035]
如图2所示,sem结果表明,复合材料具有三维网络结构,而且co纳米颗粒均匀分布在三维石墨烯材料的表面,实验制备得到co/3dng。实施例2
[0036]
本实施例具体包括以下步骤:
[0037]
第一步,将20ml,3mg/ml go分散液加入40ml水热釜,再量取1.0ml nh3·
h2o加入go分散液中,并充分搅拌混合5min。然后,将反应釜转移至烘箱,加热至180℃,并在此温度下保温12h。待反应结束,反应釜自然冷却后,将产物转移至去离子水中进行透析直至去离子水ph=7,并将得到的产物命名为3dng。
[0038]
第二步、称取20mg co(ch3coo)2·
4h2o,依次量取7ml去离子水,7ml无水乙醇加入,并充分搅拌10min。再将3dng浸渍于co盐溶液中,并静置24h。然后,将浸渍后的3dng在乙醇和水的混合溶液(1:1)中进行多次洗涤后,将产物放入冰箱(
‑
25℃)冷冻12h,最后将产物置于冷冻干燥机中在
‑
80℃下干燥12h。
[0039]
第三步、将冷冻干燥后的样品放置于管式炉加热区,密闭后,抽真空通入n2置换3次,然后充入n2,以5℃/min的升温速率升至700℃,并保温60min。待反应结束,系统自然冷却后将样品从管式炉中取出。将得到的产物命名为co/3dng
‑
700。
[0040]
如图1和图2所示,本实施例的xrd和sem结果与实施例1相似,表明实验制备得到co/3dng。
[0041]
本实施例与实施例1的区别在于:go分散液浓度从2mg/ml增加至3mg/ml,氨水用量从0.5mg/ml增加至1mg/ml,co(ch3coo)2·
4h2o用量从增加10mg增加至20mg,裂解温度从600℃增加至700℃。实施例3
[0042]
本实施例具体包括以下步骤:
[0043]
步骤1、将20ml,4mg/ml go分散液加入40ml水热釜,再量取1.5ml nh3·
h2o加入go分散液中,并充分搅拌混合5min。然后,将反应釜转移至烘箱,加热至180℃,并在此温度下保温12h。待反应结束,反应釜自然冷却后,将产物转移至去离子水中进行透析直至去离子水ph=7,并将得到的产物命名为3dng。
[0044]
步骤2、称取30mg co(ch3coo)2·
4h2o,依次量取7ml去离子水,7ml无水乙醇加入,并充分搅拌10min。再将3dng浸渍于co盐溶液中,并静置24h。然后,将浸渍后的3dng在乙醇和水的混合溶液(1:1)中进行多次洗涤后,将产物放入冰箱(
‑
25℃)冷冻12h,最后将产物置于冷冻干燥机中在
‑
80℃下干燥12h。
[0045]
步骤3、将冷冻干燥后的样品放置于管式炉加热区,密闭后,抽真空通入n2置换3次,然后充n2,以5℃/min的升温速率升至800℃,并保温60min。待反应结束,系统自然冷却后将样品从管式炉中取出。将得到的产物命名为co/3dng
‑
800。
[0046]
xrd结果表明,与co/3dng
‑
600和co/3dng
‑
700相比,co/3dng
‑
800在44.39
°
处(111)衍射峰强度增加。sem结果表明,与实施例1和实施例2相似,co/3dng
‑
800具有三维网络结构,且co纳米颗粒均匀分布在三维石墨烯表面,实验制备得到co/3dng。
[0047]
本实施例与实施例1的区别在于:go分散液浓度从2mg/ml增加至4mg/ml,氨水用量从0.5mg/ml增加至1.5mg/ml,co(ch3coo)2·
4h2o用量从增加10mg增加至30mg,裂解温度从600℃增加至800℃。实施例4
[0048]
本实施例具体包括以下步骤:
[0049]
第一步、将20ml,5mg/ml go分散液加入40ml水热釜,再量取2ml nh3·
h2o加入go分散液中,并充分搅拌混合5min。然后,将反应釜转移至烘箱,加热至180℃,并在此温度下保持12h。待反应结束,反应釜自然冷却后,将产物转移至去离子水中进行透析直至去离子水ph=7,并将得到的产物命名为3dng。
[0050]
第二步、称取40mg co(ch3coo)2·
4h2o,依次量取7ml去离子水,7ml无水乙醇加入,并充分搅拌10min。再将3dng浸渍于co盐溶液中,并静置24h。然后,将浸渍后的3dng在乙醇和水的混合溶液(1:1)中进行多次洗涤后,将产物放入冰箱(
‑
25℃)冷冻12h,最后将产物置于冷冻干燥机中在
‑
80℃下干燥12h。
[0051]
第三步、将冷冻干燥后的样品放置于管式炉,密闭后,抽真空通入n2置换3次,然后充n2,以5℃/min的升温速率升至900℃,并保温60min。待反应结束,系统自然冷却后将样品从管式炉中取出。将得到的产物命名为co/3dng
‑
900。
[0052]
xrd结果表明,与co/3dng
‑
600、co/3dng
‑
700和co/3dng
‑
800相比,co/3dng
‑
900在44.4
°
处(111)衍射峰强度显著增加,且在51.8
°
和76.2
°
处出现衍射峰,分别对应金属co的(200)和(220)晶面,表明co/3dng
‑
900具有更好的结晶性能。sem结果表明,与co/3dng
‑
600、co/3dng
‑
700和co/3dng
‑
800相比,co/3dng
‑
900上的co纳米颗粒尺寸更大,实验制备得到
co/3dng。
[0053]
本实施例与实施例1的区别在于:go分散液浓度从2mg/ml增加至5mg/ml,氨水用量从0.5mg/ml增加至2mg/ml,co(ch3coo)2·
4h2o用量从增加10mg增加至40mg,裂解温度从600℃增加至900℃。实施例5
[0054]
本实施例涉及上述四种co/3dng催化剂催化木质素模型化合物2
‑
苯氧基
‑1‑
苯乙醇氧化活性测试,具体包括以下步骤:
[0055]
在10ml聚四氟乙烯容器中,加入2mg co/3dng、0.01mm 2
‑
苯氧基
‑1‑
苯乙醇及3.0ml甲醇。再将反应体系置于微型高压反应中,密闭后,通入氧气置换3次,充入氧气至初始反应压力为0.2mpa,以400rpm的速度进行搅拌,同时加热升温至120℃,反应6h,待反应结束降至室温,利用磁铁直接回收催化剂co/3dng,并收集液体产物。用液相色谱
‑
质谱联用仪和液相色谱仪采用外标法计算2
‑
苯氧基
‑1‑
苯乙醇的转化率和各个产物的产率。四种co/3dng催化2
‑
苯氧基
‑1‑
苯乙醇氧化结果见表1。
[0056]
表1不同催化剂对比催化剂2
‑
苯氧基
‑1‑
苯乙醇转化率(%)苯酚产率(%)实施例147.046.3实施例260.460.4实施例381.681.6实施例497.097.0
[0057]
表1可以看出,本方法制备的co/3dng催化剂的催化氧化性能高于现有催化剂(未添加k2co3条件下,2
‑
苯氧基
‑1‑
苯乙醇转化率19%,苯酚产率19%),表明本方法制备的催化剂具有高活性。实施例4催化2
‑
苯氧基
‑1‑
苯乙醇转化率高达97.0%,苯酚产率为97.0%,表明该催化剂不仅具有最高的活性,同时也具有优异的选择性。实施例6
[0058]
本实施例涉及上述co/3dng
‑
900催化剂(实施例4)催化溶剂型木质素氧化解聚活性测试,以桦木木屑为原生木质素,参考文献制备得到溶剂型木质素,其活性测试具体包括以下步骤:
[0059]
在20ml聚四氟乙烯容器中,加入40mg co/3dng、50mg溶剂型木质素及10ml甲醇。再将反应体系置于微型高压反应中,密闭后,通入氧气置换3次,充入氧气至初始反应压力为0.2mpa,以400rpm的速度进行搅拌,同时加热升温至120℃,反应12h,待反应结束降至室温,利用磁铁直接回收催化剂co/3dng,然后通过离心分离固体沉淀,并收集液体产物。用液相色谱
‑
质谱联用仪和液相色谱仪分析各个产物。
[0060]
产物中芳香化合物单体,包括2,6
‑
二甲氧基
‑
1,4
‑
苯醌、苯酚、4
‑
羟基苯甲酸甲酯、香草酸甲酯。由此可知,实施例4催化剂可有效催化溶剂型木质素氧化解聚制备芳香类单体化合物。
[0061]
与现有技术相比,采用水热
‑
浸渍
‑
裂解方法,简单、快速制备出co/3dng催化剂,并在不添加任何碱的条件下,该催化剂可以高效催化氧化木质素及其模型化合物,且co/3dng催化剂具有高选择性和可重复利用稳定性等特点。
[0062]
上述具体实施可由本领域技术人员在不背离本发明原理和宗旨的前提下以不同
的方式对其进行局部调整,本发明的保护范围以权利要求书为准且不由上述具体实施所限,在其范围内的各个实现方案均受本发明之约束。