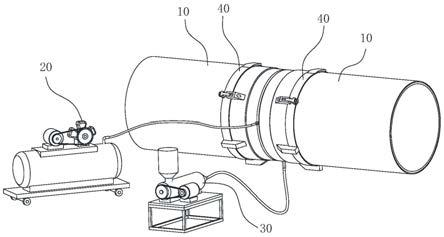
1.本发明属于焊缝防腐蚀技术领域,具体涉及一种管道对接焊缝的抗腐蚀处理系统及方法。
背景技术:2.随着石油、天然气等能源的不断开发,石气管线的迅猛发展,油气管道的铺设面临着高压输送、低温环境、远距离输送、深海高压铺设、酸性土壤环境输送以及高压杂散电流等恶劣服役条件的威胁。钢以相对低廉的价格、可靠的性能在工业生产中被广泛应用于建筑业、制造业,石油天然气管道一般采用焊接方式进行连接,现有技术中管道焊接完成后往往只能对焊缝外表面进行防腐处理,而内表面由于空间狭小很难再进行防腐处理,但实际上管道内输送的石油、天然气等物质会对管道内壁造成剧烈腐蚀,除此,还有电化学腐蚀、微生物腐蚀和应力腐蚀等腐蚀形式,而腐蚀是金属构件与管线的失效的主要形式之一,美国统计数据表明15%~30%的埋地管线腐蚀与微生物有关,腐蚀会导致管道发生油、气、水的泄露,造成严重经济损失甚至造成人员伤亡以及生态环境的破坏,因此亟需一种能够对焊缝内表面、外表面同时进行防腐蚀处理的系统和方法。
技术实现要素:3.本发明的目的是提供一种管道对接焊缝的抗腐蚀处理系统及方法,尤其能够提高焊缝内表面的抗腐蚀性能。
4.本发明采取的技术方案具体如下:
5.一种管道对接焊缝的抗腐蚀处理系统,包括:
6.内衬,
7.高压气源,以及
8.注胶装置;
9.所述内衬位于两管道对接形成的接缝内侧,表面具有耐腐蚀涂层,内衬一端与其中一管道内壁焊接,该端设置在管道内流体上游段,另一端外环面设有环形注胶槽,该端设置在管道内流体下游段,环形注胶槽两侧具有密封圈,密封圈置于内衬外环面上开设的环槽内,内衬外环面与焊缝对齐位置处设有注胶孔、溢胶孔和充气孔,内衬中开设有:
10.第一胶道,用于连通所述环形注胶槽和注胶孔;
11.第二胶道,用于连通所述环形注胶槽和溢胶孔;
12.以及气道,用于连通两密封圈所在的环槽和充气孔;
13.所述两管道的端部与注胶孔、溢胶孔和充气孔对应位置处分别设有半圆形缺口;
14.所述高压气源通过管路与充气孔连通;
15.所述注胶装置通过管路与注胶孔连通。
16.还包括:
17.两管道接缝外侧的
18.过渡层:铜镍合金涂层,铜镍均为微米级粉末,微米级粉的粒径为40微米到90微米,铜粉的质量百分比为50%至70%,垂直喷涂在接缝焊接完成后的焊缝表面;
19.阳极性金属涂层:锌涂层,锌为微米级粉末,微米级粉的粒径为40微米到80微米,喷涂在所述铜镍合金涂层表面;
20.抗菌性疏水层,该层为纳米级别的二氧化硅颗粒,颗粒的最大尺寸在250纳米,并含有质量分数为10%的铬、10%的镍、10%的钼元素,喷涂在锌涂层表面,抗菌性疏水层的厚度为200微米;
21.热缩带,包覆在喷涂完上述各涂层后的焊缝外侧。
22.所述内衬由内圈和外圈相互嵌套而成,其中所述环形注胶槽、环槽、注胶孔、溢胶孔和充气孔开设在外圈上,所述注胶孔和充气孔的孔壁上设有螺纹,所述第一胶道、第二胶道和气道开设在内圈的外环面上;所述环形注胶槽的槽底部开设有贯穿外圈的第一通孔和第二通孔,所述环槽的槽底开设有贯穿外圈的第三通孔,所述第三通孔沿外圈周向间隔设置多个。
23.所述第一胶道和第二胶道是平行于内衬轴线设置的直线槽,其中
24.第一胶道的两端分别与注胶孔和第一通孔对齐,
25.第二胶道的两端分别与溢胶孔和第二通孔对齐;
26.所述气道包括:
27.环形段,与外圈上远离接缝的一环槽对应,并与该环槽底部的第三通孔连通;
28.两对称布置的弧形段,与外圈上靠近接缝的一环槽对应,并与该环槽底部的第三通孔连通;
29.两平直段,用于将两弧形段与环形段连通,其中一平直段延伸至所述充气孔;
30.所述两弧形段的两端彼此断开,所述第一胶道和第二胶道分别从两弧形段之间的两处断开区域穿过。
31.还包括:
32.热缩带支撑机构,用于在包覆热缩带的初期将热缩带的两端沿管道周向均匀张紧,其包括:
33.绑带,以及
34.垫块;
35.所述绑带沿管道周向绑扎在焊缝两侧的管道上;
36.所述垫块固定在绑带上,垫块朝向焊缝的一端设有坡面,垫块设有多个并沿绑带的长度方向等距间隔设置。
37.至少其中一个所述垫块为如下结构,包括:
38.固定部,以及
39.活动部;
40.所述固定部与绑带固接;
41.所述活动部沿平行于管道轴线的方向与固定部活动连接,活动部上转动设置有一螺杆,螺杆转过固定部上开设的螺孔,螺杆的端部设有旋钮。
42.所述高压气源为移动式空压机。
43.所述注胶装置为螺旋式挤出机,螺旋式挤出机的外壁上设有加热装置。
44.一种应用所述抗腐蚀处理系统处理管道焊缝的方法,包括如下步骤:
45.步骤1:在两根管道需要对接的一端加工出坡口,并在坡口上加工出与所述注胶孔、溢胶孔和充气孔对应的半圆形缺口;
46.步骤2:在两根管道对接之前将内衬的一端焊接在其中一根管道的内壁上,并对焊接区域进行防腐处理,焊接后的内衬的另一端凸出于该管道的端部;
47.步骤3:将焊接有内衬的管道与另一根管道对接,对接时确保两管道端部的半圆形缺口相互对齐,并使内衬的凸出部分插入上述另一根管道内;
48.步骤4:将高压气源的出气口通过管路连接在充气孔上,将注胶装置的出料口通过管路连接在注胶孔上,利用火焰喷枪对管道接缝两侧10cm范围内的区域进行预热,预热温度为80℃
‑
120℃;
49.步骤5:启动高压气源,向环槽充气,此时密封圈在高压气体作用下向外膨胀并抵紧管道内壁;
50.步骤6:将热熔性防腐胶注入注胶装置内,注胶装置对热熔胶进行加热以提高其流动性,注胶装置将加热后的热熔性防腐胶注入环形注胶槽内,当热熔性防腐胶从溢出孔溢出时,停止注胶;
51.步骤7:待热熔性防腐胶冷却至常温后,将充气管路和注胶管路从内衬上拆除,再采用堆焊工艺将注胶孔、溢胶孔和充气孔封堵,然后对两管道坡口之间形成的v形槽实施堆焊焊接;
52.步骤8:焊缝冷却后,利用喷砂抛光机对焊缝表面两侧5厘米内进行抛光除锈,对管道外部存在的焊接飞溅物、油污、焊渣等杂质处理干净;
53.步骤9:利用手持喷枪,依次将铜镍冷喷涂料、镀锌冷喷涂料和疏水涂料喷涂在焊缝表面,其中,铜镍冷喷涂料送粉速率为100g/min至500g/min,送粉距离为30mm至100mm;镀锌冷喷涂料送粉速率为100g/min至500g/min,送粉距离为30mm至100mm;疏水涂料送粉速率为30g/min30g/min至50g/min,送粉距离为30mm至60mm;每种涂料喷涂0.5毫米后对外表面均进行打磨处理,打磨掉0.1毫米至0.3毫米的厚度使得该层表面无明显缺陷,最终得到致密结构的保护层,并将涂层与管道外部过渡处打磨圆滑平整后进行下一层的喷涂,铜镍冷喷涂料和镀锌冷喷涂料喷涂完毕后,需要利用火焰喷枪对涂层进行烘烤,使其充分固化后再进行抗菌性疏水层的喷涂;
54.步骤10:将所述热缩带支撑机构分别绑扎在焊缝两侧的管道上,然后开始贴敷热缩带,具体方法如下:
55.步骤a:利用火焰喷枪对热缩带的一端进行预热,使其表面成熔融状态,然后将该端贴敷在焊缝及焊缝两侧指定宽度的区域内;
56.步骤b:利用火焰喷枪对热缩带另一端进行预热,使其表面成熔融状态,然后将该端绕管道一圈,并将其贴敷在步骤a中已经贴敷好的热缩带外表面上;热缩带自然长度大于管道外径,缠绕热缩带时应确保热缩带两侧分别被两热缩带支撑机构的垫块张紧;
57.步骤c:利用火焰喷枪,沿着焊缝周向对热缩带的中间区域进行加热,使该中间区域收缩并包裹在焊缝上;
58.步骤d:将包含有固定部和活动部的垫块从热缩带内侧抽离,具体方法为:转动旋钮,使活动部在螺纹杆和螺纹孔的作用下向固定部收拢;
59.步骤e:将绑带断开,从步骤d所述垫块处依次将各垫块从热缩带内侧抽离;
60.步骤f:利用火焰喷枪,对热缩带两侧区域进行加热,使其两侧包裹在管道外壁上,加热的同时手持压辊挤压热缩带,排出热缩带下方空气。
61.所述步骤6中,注胶时所述注胶孔位于管道接缝的正下方,所述溢胶孔位于管道接缝的正上方。
62.本发明取得的技术效果为:本发明在焊缝内侧设置内衬,内衬与管道内壁之间形成注胶区域,为了使内衬能够轻松插进管道内,内衬的外径小于管道内径,管道插接到位后密封圈处于松弛的状态,本发明在焊缝上预留充气孔和注胶孔,通过高压气体使密封圈膨胀,进而防止后续注胶过程中胶液向两侧扩散,确保胶液充满环形注胶槽,注胶完成后能够使焊缝内壁与管道内腔完全隔离,进而提高焊缝内侧的抗腐蚀性能。与现有技术相比,本发明具有耐腐蚀、延长油气管道使用寿命的优点,可显著降低发生油气管道泄漏的风险、减少腐蚀维护工作和费用。
附图说明
63.图1是本发明的实施例所提供的抗腐蚀处理系统的立体图;
64.图2是本发明的实施例所提供的抗腐蚀处理系统的主视图;
65.图3是图2的a
‑
a剖视图;
66.图4是图3的b
‑
b剖视图;
67.图5是本发明的实施例所提供的内衬的爆炸图;
68.图6是本发明的实施例所提供的内衬另一视角的爆炸图;
69.图7是本发明的实施例所提供的热缩带支撑机构的立体图;
70.图8是本发明的实施例所提供的经过抗腐蚀处理后的管道焊缝剖视图。
具体实施方式
71.为了使本发明的目的及优点更加清楚明白,以下结合实施例对本发明进行具体说明。应当理解,以下文字仅仅用以描述本发明的一种或几种具体的实施方式,并不对本发明具体请求的保护范围进行严格限定。
72.实施例1
73.如图1
‑
6所示,一种管道对接焊缝的抗腐蚀处理系统,包括:内衬50,高压气源20,以及注胶装置30;所述内衬50位于两管道10对接形成的接缝内侧,表面具有耐腐蚀涂层,内衬50一端与其中一管道10内壁焊接,该端设置在管道内流体上游段,另一端外环面设有环形注胶槽53,该端设置在管道内流体下游段,环形注胶槽53两侧具有密封圈54,密封圈54置于内衬50外环面上开设的环槽541内,内衬50外环面与焊缝对齐位置处设有注胶孔55、溢胶孔56和充气孔57,内衬50中开设有:第一胶道511,用于连通所述环形注胶槽53和注胶孔55;第二胶道512,用于连通所述环形注胶槽53和溢胶孔56;以及气道513,用于连通两密封圈54所在的环槽541和充气孔57;所述两管道10的端部与注胶孔55、溢胶孔56和充气孔57对应位置处分别设有半圆形缺口;所述高压气源20通过管路与充气孔57连通;所述注胶装置30通过管路与注胶孔55连通。本发明在焊缝内侧设置内衬50,内衬50与管道10内壁之间形成注胶区域,为了使内衬50能够轻松插进管道10内,内衬50的外径小于管道10内径,管道10插接
到位后密封圈54处于松弛的状态,本发明在焊缝上预留充气孔57和注胶孔55,通过高压气体使密封圈54膨胀,进而防止后续注胶过程中胶液向两侧扩散,确保胶液充满环形注胶槽53,注胶完成后能够使焊缝内壁与管道10内腔完全隔离,进而提高焊缝内侧的抗腐蚀性能。进一步的,如图8所示,本发明还包括两管道10接缝外侧的:过渡层:铜镍合金涂层101,铜镍均为微米级粉末,微米级粉的粒径为40微米到90微米,铜粉的质量百分比为50%至70%,垂直喷涂在接缝焊接完成后的焊缝表面,铜镍之间彼此可无限固溶,从而形成连续固溶体,铜质地较软,因而能够较好的连接焊缝与阳极性金属涂层,同时将焊缝表面不光滑处进行填充;阳极性金属涂层:锌涂层102,锌为微米级粉末,微米级粉的粒径为40微米到80微米,喷涂在所述铜镍合金涂层101表面;抗菌性疏水层103,该层为纳米级别的二氧化硅颗粒,颗粒的最大尺寸在250纳米,并含有质量分数为10%的铬、10%的镍、10%的钼元素,该层喷涂在锌涂层102表面;抗菌性疏水层103的厚度为200微米;热缩带104,包覆在喷涂完上述各涂层后的焊缝外侧。本发明同时对焊缝外侧的抗腐蚀工艺进行了改进,其中铜镍合金涂层101能够增加锌涂层102与焊料之间的结合强度,并且能够将焊接完毕后的焊缝表面缺陷处进行修复,在其他涂层遭破坏后,能够作为保护层,锌涂层102主要作为牺牲层对管道10进行阳极保护,而抗菌性疏水层103能够使焊缝与外部水汽隔离,进一步提高抗腐蚀性能,热缩带104对焊缝进行进一步密封和机械防护。铬元素能够在金属表面形成强力的钝化膜以保护基质,镍元素释放可以穿透细胞膜的重金属离子干扰细胞代谢过程或通过干扰各种酶的效力,从而达到抑制细菌的繁殖的效果,钼元素具有硫酸盐还原菌的耐受性,可以抑制生物膜的生长、可以富集到钝化膜中,以化合物的形式附着到细胞壁上,使细菌破裂死亡。
74.优选的,如图5、6所示,所述内衬50由内圈51和外圈52相互嵌套而成,其中所述环形注胶槽53、环槽541、注胶孔55、溢胶孔56和充气孔57开设在外圈52上,所述注胶孔55和充气孔57的孔壁上设有螺纹,所述第一胶道511、第二胶道512和气道513开设在内圈51的外环面上;所述环形注胶槽53的槽底部开设有贯穿外圈52的第一通孔521和第二通孔522,所述环槽541的槽底开设有贯穿外圈52的第三通孔523,所述第三通孔523沿外圈52周向间隔设置多个。
75.具体的,所述第一胶道511和第二胶道512是平行于内衬50轴线设置的直线槽,其中第一胶道511的两端分别与注胶孔55和第一通孔521对齐,第二胶道512的两端分别与溢胶孔56和第二通孔522对齐;所述气道513包括:环形段5131,与外圈52上远离接缝的一环槽541对应,并与该环槽541底部的第三通孔523连通;两对称布置的弧形段5132,与外圈52上靠近接缝的一环槽541对应,并与该环槽541底部的第三通孔523连通;两平直段5133,用于将两弧形段5132与环形段5131连通,其中一平直段5133延伸至所述充气孔57;所述两弧形段5132的两端彼此断开,所述第一胶道511和第二胶道512分别从两弧形段5132之间的两处断开区域穿过。
76.如图1、7所示,还包括:热缩带支撑机构40,用于在包覆热缩带104的初期将热缩带104的两端沿管道10周向均匀张紧,其包括:绑带41,以及垫块42;所述绑带41沿管道10周向绑扎在焊缝两侧的管道10上;所述垫块42固定在绑带41上,垫块42朝向焊缝的一端设有坡面,垫块42设有多个并沿绑带41的长度方向等距间隔设置。热缩带104在收缩以前,其长度大于管道10外径,因此会向下垂落,若不对其进行支撑则会导致热缩以后各部位厚度不均
匀。
77.进一步的,为方便热缩带支撑机构40进行拆卸,至少其中一个所述垫块42为如下结构,包括:固定部421,以及活动部422;所述固定部421与绑带41固接;所述活动部422沿平行于管道10轴线的方向与固定部421活动连接,活动部422上转动设置有一螺杆423,螺杆423转过固定部421上开设的螺孔,螺杆423的端部设有旋钮424。
78.优选的,所述高压气源20为移动式空压机。所述注胶装置30为螺旋式挤出机,螺旋式挤出机的外壁上设有加热装置。
79.实施例2
80.一种应用实施例1所述抗腐蚀处理系统处理管道10焊缝的方法,包括如下步骤:
81.步骤1:在两根管道10需要对接的一端加工出坡口,并在坡口上加工出与所述注胶孔55、溢胶孔56和充气孔57对应的半圆形缺口;
82.步骤2:在两根管道10对接之前将内衬50的一端焊接在其中一根管道10的内壁上,并对焊接区域进行防腐处理,焊接后的内衬50的另一端凸出于该管道10的端部;
83.步骤3:将焊接有内衬50的管道10与另一根管道10对接,对接时确保两管道10端部的半圆形缺口相互对齐,并使内衬50的凸出部分插入上述另一根管道10内;
84.步骤4:将高压气源20的出气口通过管路连接在充气孔57上,将注胶装置30的出料口通过管路连接在注胶孔55上,利用火焰喷枪对管道10接缝两侧10cm范围内的区域进行预热,预热温度为80℃
‑
120℃;
85.步骤5:启动高压气源20,向环槽541充气,此时密封圈54在高压气体作用下向外膨胀并抵紧管道10内壁;
86.步骤6:将热熔性防腐胶注入注胶装置30内,注胶装置30对热熔胶进行加热以提高其流动性,注胶装置30将加热后的热熔性防腐胶注入环形注胶槽53内,当热熔性防腐胶从溢出孔溢出时,停止注胶;
87.步骤7:待热熔性防腐胶冷却至常温后,将充气管路和注胶管路从内衬50上拆除,再采用堆焊工艺将注胶孔55、溢胶孔56和充气孔57封堵,然后对两管道10坡口之间形成的v形槽实施堆焊焊接;
88.步骤8:焊缝冷却后,利用喷砂抛光机对焊缝表面两侧5厘米内进行抛光除锈,对管道外部存在的焊接飞溅物、油污、焊渣等杂质处理干净;
89.步骤9:利用手持喷枪,依次将铜镍冷喷涂料、镀锌冷喷涂料和疏水涂料喷涂在焊缝表面,其中,铜镍冷喷涂料送粉速率为100g/min至500g/min,送粉距离为30mm至100mm;镀锌冷喷涂料送粉速率为100g/min至500g/min,送粉距离为30mm至100mm;疏水涂料送粉速率为30g/min30g/min至50g/min,送粉距离为30mm至60mm;每种涂料喷涂0.5毫米后对外表面均进行打磨处理,打磨掉0.1毫米至0.3毫米的厚度使得该层表面无明显缺陷,最终得到致密结构的保护层,并将涂层与管道外部过渡处打磨圆滑平整后进行下一层的喷涂,铜镍冷喷涂料和镀锌冷喷涂料喷涂完毕后,需要利用火焰喷枪对涂层进行烘烤,使其充分固化后再进行抗菌性疏水层的喷涂;
90.步骤10:将所述热缩带支撑机构40分别绑扎在焊缝两侧的管道10上,然后开始贴敷热缩带104,具体方法如下:
91.步骤a:利用火焰喷枪对热缩带104的一端进行预热,使其表面成熔融状态,然后将
该端贴敷在焊缝及焊缝两侧指定宽度的区域内;
92.步骤b:利用火焰喷枪对热缩带104另一端进行预热,使其表面成熔融状态,然后将该端绕管道10一圈,并将其贴敷在步骤a中已经贴敷好的热缩带104外表面上;热缩带104自然长度大于管道10外径,缠绕热缩带104时应确保热缩带104两侧分别被两热缩带支撑机构40的垫块42张紧;
93.步骤c:利用火焰喷枪,沿着焊缝周向对热缩带104的中间区域进行加热,使该中间区域收缩并包裹在焊缝上;
94.步骤d:将包含有固定部421和活动部422的垫块42从热缩带104内侧抽离,具体方法为:转动旋钮424,使活动部422在螺纹杆和螺纹孔的作用下向固定部421收拢;
95.步骤e:将绑带41断开,从步骤d所述垫块42处依次将各垫块42从热缩带104内侧抽离;
96.步骤f:利用火焰喷枪,对热缩带104两侧区域进行加热,使其两侧包裹在管道10外壁上,加热的同时手持压辊挤压热缩带104,排出热缩带104下方空气。
97.所述步骤6中,注胶时所述注胶孔55位于管道10接缝的正下方,所述溢胶孔56位于管道10接缝的正上方。
98.以上所述仅是本发明的优选实施方式,应当指出,对于本技术领域的普通技术人员来说,在不脱离本发明原理的前提下,还可以作出若干改进和润饰,这些改进和润饰也应视为本发明的保护范围。本发明中未具体描述和解释说明的结构、装置以及操作方法,如无特别说明和限定,均按照本领域的常规手段进行实施。