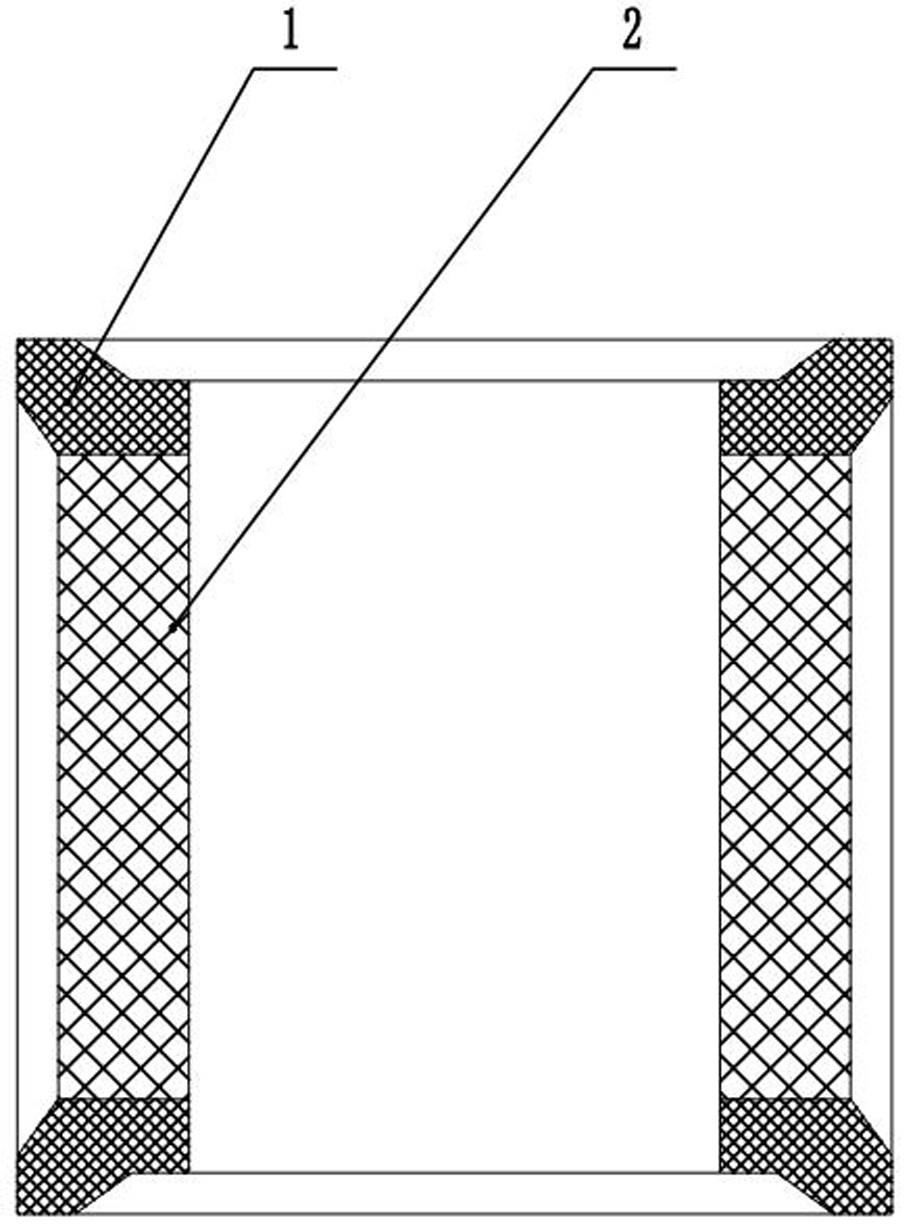
1.本发明属于超硬复合材料合成技术领域,具体涉及一种高性能复合传压部件及其制备方法。
背景技术:2.聚晶金刚石复合片具有金刚石的耐磨性、强度,以及硬质合金基体材料的韧性和可焊性,是一种优良的切削工具与耐磨材料,广泛的应用于机械加工工具、石油与地质钻头、砂轮修整工具等。
3.在超硬材料合成领域,叶腊石是目前为止唯一适用于超硬材料高温高压合成的传压部件,由于叶腊石在高温高压条件下既要做传压介质也要做密封介质,当合成压力达到叶腊石密封边承载压力时,会出现较大的生产损耗,现有的叶腊石传压部件的使用,无法更有效的提高内部压力,一些高端金刚石、立方氮化硼及其复合材料需要极高压技术才能生产制作,否则就达不到效果。
4.目前最好的黄色叶腊石产地为北京门头沟区,但随着叶腊石矿产资源的减少,价格持续走高,作为超硬材料合成的必需品,生产成本显著提高。因此,各企业均开展新的普通叶腊石(红色叶腊石、褐色叶腊石和黑色叶腊石)的尝试,尽量减少黄色叶腊石的使用,以降低成本,或者找到一种替代叶腊石的材料显得尤为重要。
5.为此,申请号为201910227092.x的中国专利公开了一种以黑色叶腊石和黄色叶腊石为原料制备叶腊石的方法,申请号为200310254656.1的中国专利公开了一种叶腊石配方,该专利公开了一种以青灰色叶腊石、红色叶腊石、褐色叶腊石和黄色叶腊石为原料制备叶腊石的方法,这些都是为了减少黄色叶腊石的使用,但是叶蜡石由于其材料本身的局限性,传压过程中压力损失大,导致施加到合成块中心区域的压力与外部施压相比,受到了极大地削弱。
技术实现要素:6.本发明针对现有技术中存在的问题,提供一种高性能复合传压部件与现有叶腊石块相比同时具有优异的密封和传压性能。
7.本发明还提供了上高性能复合传压部件的制备方法。
8.基于上述目的,本发明采取如下技术方案:一种高性能复合传压部件,所述高性能复合传压部件中空,且高性能复合传压部件中间形成合成腔,合成腔上下贯通;所述高性能复合传压部件包括立方体形的传压介质,以及套设在传压介质外的密封方框;密封方框为立方体形框架结构,密封方框的每根框架均与传压介质的侧壁相贴合;所述密封方框的六个侧面的框架均设有向密封方框几何中心处凹陷的缺口,缺口处延伸至传压介质的每个侧面,所述高性能复合传压部件的六个侧面中央均形成正棱锥台状凹槽,凹槽底面与所在平面平行,所述正四棱锥台状凹槽的内轮廓与六面顶压机的合金
顶锤外轮廓相适配。
9.具体的,所述合成腔的横截面为圆形、椭圆形或者方形。
10.具体的,凹槽深度为2~3mm。
11.优选的,所述传压介质由下述重量百分含量的原料组成:石英粉35~49%、滑石粉23~27%、氧化镁粉 12~15%、氧化铝粉 8~10%、氧化钐粉1~3%、云母粉1~2%和硅酸钠6~8%;所述密封方框由下述重量百分含量的原料组成:黄色叶腊石粉91~94%、氧化铁粉1~2%和硅酸钠5~7%。
12.优选的,所述石英粉粒度为80~120目,所述滑石粉、氧化镁粉、氧化铝粉和氧化钐粉粒度为180~200目,所述云母粉为230~250目。
13.优选的,所述黄色叶腊石粉由粗、中、细三种粒度的粉料组成,其中,粗、中、细三种粉料之间的重量比为(3
‑
4):3:3,所述粗粒度粉料为8~18目,中粒度粉料为18~36目,细粒度粉料为36~60目。
14.优选的,所述氧化铁粉粒度为250~300目。
15.一种制备上述高性能复合传压部件的方法,包括如下步骤:1)磁选:将传压介质原料中的黄色叶腊石粉置于cflj12
‑ⅲ
型选磁机上进行磁选,选出磁性小于3000高斯的原料备用;2)混料:按比例分别称取传压介质和密封方框各原料,在卧式螺带混合机上分别对传压介质和密封方框的原料进行分别混料,采用顺时针逆时针交替运转的方式进行混料,总混料时间为40~50min,分别得到传压介质混合粉料和密封方框混合粉料;将所得的传压介质混合粉料和密封方框混合粉料分别放置于密闭容器内在18~23℃的温度下放置20~30h,备用;3)装料:采用成型装置制作高性能复合传压部件,制作过程采用挤压成型工艺进行,所述成型装置为本发明中突出的发明点,通过成型装置可以实现对密封框架和传压合成块的塑形;所述成型装置,包括四个四瓣模、装料筒、设置于装料筒内的模芯、上压头、下压头和锥套;四个四瓣模的截面均为部分圆环的形状,且四个四瓣模相靠接后形成的截面为整个圆环形,四个四瓣模合为形成用于填料的空腔,装料筒设于空腔内,且装料筒紧贴四个四瓣模的内侧壁,模芯为圆柱形,且模芯的直径小于装料筒的直径,模芯与装料筒之间形成用于充填高性能复合传压部件原料的间隙;锥套套设于四个四瓣模外侧;所述挤压成型工艺,具体步骤如下:先将四个四瓣模组装后,将锥套套设于四个四瓣模外,将下压头从空腔的底端开口处向上伸入空腔内,先铺放下部的密封框架混合粉料,刮平,然后放入装料筒,在装料筒外四角缺口处铺放中部的密封框架混合粉料,刮平;在装料筒内铺放传压合成块混合粉料,刮平,再将模芯放置于传压合成块混合粉料的中心处;再将装料筒从成型装置中抽出;然后铺放上部的密封框架混合粉料,刮平,放入上压头;其中,在放置上压头时可以用定位套来固定上压头和四个四瓣模的相对位置,在放置下压头时可以用u型板来固定下压头和四个四瓣模的相对位置;
4)成型:将完成组装和填料后的成型装置放在100
‑
110t四柱液压机中,抽出u型压板,在15~18mpa压力下压制2~3分钟,再从上压头上取出定位套,在15~18mpa压力下压制2~3分钟,然后再用退料工具将四瓣模从锥套孔中退出,打开四瓣模将成型后的高性能复合传压部件从模芯外取出,得到复合传压部件;5)焙烧:将步骤4)所得复合传压部件放入微波窑炉内,先通入惰性气体排除微波窑炉内的空气,在惰性气体中经过三次升温后,冷却至50
‑
60℃以下出炉,出炉后立即储存。
16.进一步的,步骤2)中顺时针运转时转速为45~50 r/min,顺时针运转时时间为5~7min,逆时针运转时转速为40~45 r/min,逆时针运转时间为3~5min,交替间隔待机时间为1~2 min。
17.进一步的,步骤3)中下压头为t形圆柱状,上压头从空腔的顶端开口处向下伸入空腔内,下压头从空腔的底端开口处向上伸入空腔内;每个四瓣模的内侧面的形状,以及上压头底端的形状、下压头顶端的形状均与高性能复合传压部件外侧面的形状相同,且每个四瓣模的内侧面、上压头下表面和下压头上表面均设有四正棱锥形的凸台,所述凸台外轮廓与所述高性能复合传压部件侧面的正四棱锥台状凹槽内轮廓相适配。
18.进一步的,步骤3)中装料筒侧壁对应四个四瓣模的内侧壁凸台的位置形成相同形状的凸面,所述装料筒壁厚为0.2~1mm。
19.进一步的,步骤5)中的三次升温具体步骤为,利用微波加热快速升温至180~230℃并保温10~15 min,然后升温至250~280℃并保温25~30min,再升温至300~320℃并保温35~40 min,最后再冷却。
20.进一步的,步骤5)所述惰性气体为氮气、氦气、氖气、氩气、氪气、氙气、氡气中的任意一种。
21.与现有技术相比,本发明的有益效果在于:本发明高性复合传压部件立方体的六个侧面采用正四棱锥台状凹槽结构,可有效减少复合传压部件在受压过程中的流动变形,有利于高压腔中的超高压的形成与保持,提高合成腔体的内部压力;复合传压部件的密封方框和传压介质采用分体式设计,在高压情况下可以分别利用密封方框良好的流动性和密封性以及传压介质更高的传压效率的特点,使复合传压部件兼具密封性好,传压效率高的优点。
22.本发明高性能复合传压部件的密封方框采用优质可塑性黄色叶腊石加上高摩擦系数的氧化铁所形成高摩擦系数的可塑性复合材料,密封性能得到大大提高,传压介质采用粘性矿物质和硬质矿物质替代叶腊石的材料,节约了叶腊石矿的实用,提高压力传递效果,所制备的复合传压部件与现有叶腊石传压部件相比同时具有优异的密封和传压性能。
23.本发明成型装置装料中,通过借助薄壁辅助装料筒,实现密封方框混合料和传压介质混合料分次装料,并达到一次复合压制成型的技术效果,解决了封方框和传压介质整体复合一次压制成型的技术难题。由于本成型装置结构简单、使用方便,能够显著提高产品的成型效率,所制压制的复合传压部件具有质量好,次品低的特点,可应用于大规模工业压制复合传压部件。
24.本发明通过复合传压部件微波焙烧工艺的合理选择,以便使复合传压部件的含水量、抗压强度、剪切强度及软硬程度发生改变,从而改变和调整复合传压部件的自身性能以
满足合成聚晶金刚石复合片的要求。
25.将本发明高性能复合传压部件取代专利cn107362750 a一种聚晶金刚石复合片及其合成块中的叶腊石块,制备得到聚晶金刚石复合片,检测结果为,磨耗比由32万提高到38万,提高了19%,抗冲击韧性由85焦耳提高到99焦耳,提高了16%,在750℃条件下烧结2小时后,磨耗比由30万提高到36万,提高了20%,抗冲击韧性由84焦耳提高到97焦耳,提高了15%,说明采用本发明高性能复合传压部件制备的聚晶金刚石复合片不仅具有较高的力学性能,而且还具有良好的热学性能,同时还解决了现有的叶腊石传压部件的使用,无法更有效的提高内部压力的难题。
附图说明
26.图1是本发明所述高性能复合传压部件的纵向截面结构示意图;图2是本发明所述高性能复合传压部件的横向截面结构示意图;图3为正在成型装置中装填密封框架混合粉料以及传压介质混合粉料时的纵向截面结构示意图,图中为正在填充中部的密封框架混合粉料时的截面图;图4为在成型装置中装填密封框架混合粉料以及传压介质混合粉料后用定位套固定上压头时的纵向截面图;图5为正在成型装置中密封框架混合粉料以及传压介质混合粉料装填完成时的横向截面结构示意图;图1和图2中:1、密封框架;2、传压介质;图3中、图4和图5中:100、薄壁辅助装料筒;101、上压头;102、模芯;103、四瓣模;104、定位套;105、锥套;106、下压头;108、u型压板。
具体实施方式
27.为了使本发明的技术目的、技术方案和有益效果更加清楚、明确,以下对本发明进一步详细说明。应当理解,此处所描述的具体实施例仅用以解释本发明,并不用于限定本发明。
28.实施例1如图1至图2所示,一种高性能复合传压部件,所述高性能复合传压部件中空,且高性能复合传压部件中间形成合成腔,合成腔上下贯通;所述合成腔的横截面为圆形;所述高性能复合传压部件包括立方体形的传压介质2,以及套设在传压介质2外的密封方框1;密封方框1为立方体形框架结构,密封方框1的每根框架均与传压介质2的侧壁相贴合;所述密封方框1的六个侧面的框架均设有向密封方框1几何中心处凹陷的缺口,缺口处延伸至传压介质2的每个侧面,即,所述高性能复合传压部件的六个侧面中央均形成正棱锥台状凹槽,凹槽底面与所在平面平行,凹槽深度为2mm,所述正四棱锥台状凹槽的内轮廓与六面顶压机的合金顶锤外轮廓相适配;所述传压介质2由下述重量百分含量的原料组成:石英粉35%、滑石粉27%、氧化镁粉 15%、氧化铝粉 10%、氧化钐粉3%、云母粉2%和硅酸钠8%;
所述密封方框1由下述重量百分含量的原料组成:黄色叶腊石粉91%、氧化铁粉2%和硅酸钠7%。
29.所述石英粉粒度为80目,所述滑石粉、氧化镁粉、氧化铝粉和氧化钐粉粒度为180目,所述云母粉为230目。
30.所述黄色叶腊石粉由粗、中、细三种粒度的粉料组成,其中,粗、中、细三种粉料之间的重量比为4:3:3,所述粗粒度粉料为8目,中粒度粉料为18目,细粒度粉料为36目,所述氧化铁粉粒度为250目。
31.实施例2一种制备实施例1所述高性能复合传压部件的方法,具体步骤如下:1)磁选:将传压介质2原料中用到的黄色叶腊石粉置于cflj12
‑ⅲ
型选磁机上进行磁选,选出磁性小于3000高斯的原料备用;2)混料:按比例分别称取传压介质2和密封方框1各原料,在卧式螺带混合机上分别对传压介质2和密封方框1的原料进行分别混料,采用顺时针逆时针交替运转的方式,顺时针运转时转速为45r/min,顺时针运转时时间为5min,逆时针运转时转速为40r/min,,逆时针运转时间为3min,交替间隔待机时间为1min,总混料时间为40min,分别得到传压介质2混合粉料和密封方框1混合粉料;将所得的传压介质2混合粉料和密封方框1混合粉料分别放置于密闭容器内在18℃的温度下放置20h,备用;3)装料:采用成型装置制作高性能复合传压部件,制作过程采用挤压成型工艺进行;如图3、图4、图5所示,所述成型装置,包括四个四瓣模103、薄壁辅助装料筒100、设置于薄壁辅助装料筒100内的模芯102、上压头101、下压头106和锥套105;四个四瓣模103的截面均为部分圆环的形状,且四个四瓣模103相靠接后形成的截面为整个圆环形,四个四瓣模103合为形成用于填料的空腔,薄壁辅助装料筒100设于空腔内,且薄壁辅助装料筒100紧贴四个四瓣模103的内侧壁,模芯102为圆柱形,且模芯102的直径小于薄壁辅助装料筒100的直径,模芯102与薄壁辅助装料筒100之间形成用于充填高性能复合传压部件原料的间隙;下压头106为t形圆柱状,上压头101从空腔的顶端开口处向下伸入空腔内,下压头106从空腔的底端开口处向上伸入空腔内;每个四瓣模103的内侧面的形状,以及上压头101底端的形状、下压头106顶端的形状均与高性能复合传压部件外侧面的形状相同,且每个四瓣模103的内侧面、上压头101下表面和下压头106上表面均设有四正棱锥形的凸台,所述凸台外轮廓与所述高性能复合传压部件侧面的正四棱锥台状凹槽内轮廓相适配;薄壁辅助装料筒100侧壁对应四个四瓣模103的内侧壁凸台的位置形成相同形状的凸面,所述薄壁辅助料筒壁厚为0.5mm。
32.锥套105套设于四个四瓣模103外侧;采用成型装置制作高性能复合传压部件的挤压成型工艺,具体步骤如下:先将四个四瓣模103组装后,将锥套105套设于四个四瓣模103外,将下压头106从空腔的底端开口处向上伸入空腔内,先铺放下部的密封框架201混合粉料,刮平,然后放入
薄壁辅助装料筒100,在薄壁辅助装料筒100外四角缺口处铺放中部的密封框架201混合粉料,刮平;在薄壁辅助装料筒100内铺放传压合成块202混合粉料,刮平,再将模芯102放置于传压合成块202混合粉料的中心处;再将薄壁辅助装料筒100从成型装置中抽出;然后铺放上部的密封框架201混合粉料,刮平,放入上压头101;其中,在放置上压头101时可以用定位套104来固定上压头101和四个四瓣模103的相对位置,在放置下压头106时可以用u型板108来固定下压头106和四个四瓣模103的相对位置;4)成型:将完成组装和填料后的成型装置放在100t四柱液压机中,抽出u型压板108,在15mpa压力下压制2分钟,再从上压头上取出定位套104,在15mpa压力下压制2分钟,然后再用退料工具将四瓣模103从锥套105孔中退出,打开四瓣模103将成型后的高性能复合传压部件从模芯102外取出,得到复合传压部件;5)焙烧:将步骤4)所得复合传压部件放入微波窑炉内,先通入惰性气体排除微波窑炉内的空气,在惰性气体中利用微波加热快速升温至180℃并保温10min,然后升温至250℃并保温25min,再升温至300℃并保温35min,最后冷却至60℃以下出炉,出炉后立即储存。
33.步骤5)所述惰性气体为氮气。
34.实施例3一种高性能复合传压部件,实施例3中的高性能复合传压部件结构与实施例1相同,不同之处在于各个部件的成分及用量不同,具体为:凹槽深度为3mm;所述传压介质2由下述重量百分含量的原料组成:石英粉49%、滑石粉23%、氧化镁粉 12%、氧化铝粉 8%、氧化钐粉1%、云母粉1%和硅酸钠为6%;所述密封方框1由下述重量百分含量的原料组成:黄色叶腊石粉94%、氧化铁粉1%和硅酸钠5%。
35.所述石英粉粒度为120目,所述滑石粉、氧化镁粉、氧化铝粉和氧化钐粉粒度为200目,所述云母粉为250目。
36.所述黄色叶腊石粉由粗、中、细三种粒度的粉料组成,其中,粗、中、细三种粉料之间的重量比为4:3:3,所述粗粒度粉料为18目,中粒度粉料为36目,细粒度粉料为60目,所述氧化铁粉粒度为300目。
37.实施例4一种制备实施例3所述高性能复合传压部件的方法,所述方法与实施例2中的方法总体步骤相同,使用的成型装置相同,不同之处在于具体的工艺参数。
38.步骤2)中混料的制备工艺与实施例2不同,具体为:按比例分别称取传压介质2和密封方框1各原料,在卧式螺带混合机上分别对传压介质2和密封方框1的原料进行分别混料,采用顺时针逆时针交替运转的方式,顺时针运转时转速为50 r/min,顺时针运转时时间为7min,逆时针运转时转速为45 r/min,逆时针运转时间为5min,交替间隔待机时间为2 min,总混料时间为50min,分别得到传压介质2混合粉料和密封方框1混合粉料;将所得的传压介质2混合粉料和密封方框1混合粉料分别放置于密闭容器内在23℃的温度下放置30h,备用;步骤4)的成型工艺,具体步骤与实施例2的不同之处在于:
将完成组装和填料后的成型装置放在110t四柱液压机中,抽出u型压板108,在18mpa压力下压制3分钟,再从上压头上取出定位套104,在18mpa压力下压制3分钟,然后再用退料工具将四瓣模103从锥套105孔中退出,打开四瓣模103将成型后的高性能复合传压部件从模芯102外取出,得到复合传压部件;步骤5)的焙烧工艺,具体步骤与实施例2的不同之处在于:将步骤4)所得复合传压部件放入微波窑炉内,先通入惰性气体排除微波窑炉内的空气,在惰性气体中利用微波加热快速升温至230℃并保温15 min,然后升温至280℃并保温30min,再升温至320℃并保温40 min,最后冷却至60℃以下出炉,出炉后立即储存。
39.步骤5)所述惰性气体为氩气。
40.对比试验对比例1对比例1提供一种聚晶金刚石复合片,所述聚晶金刚石复合片采用与专利文献(cn107362750 a一种聚晶金刚石复合片及其合成块)中实施例1的结构和实施例2的制备方法获得,不同之处在于:对比例1的聚晶金刚石复合片中,将本发明实施例2所制备的高性能复合传压部件替代专利文献(cn107362750 a一种聚晶金刚石复合片及其合成块)中的叶腊石块,并制备得到聚晶金刚石复合片。
41.试验例将专利文献(cn107362750 a一种聚晶金刚石复合片及其合成块)实施例2中制备得到的聚晶金刚石复合片,以及本发明对比例1的聚晶金刚石复合片在同等测试条件下进行耐磨性、抗冲击韧性、热稳定性测试。
42.采用jb/t3235
‑
2013《人造金刚石烧结体磨耗比测定方法》进行耐磨性测试,采用落锤冲击的方法进行抗冲击韧性测试(即:2kg的冲锤在10cm高度自由落下,利用该能量冲击试样的棱边进行测试,以试样表面出现微观裂纹时,得到抗冲击韧性值。
43.经测试,本发明对比例1与专利cn107362750 a一种聚晶金刚石复合片及其合成块实施例2所制备得到的聚晶金刚石复合片相比,磨耗比由32万提高到38万,提高了19%,抗冲击韧性由85焦耳提高到99焦耳,提高了16%,在750℃条件下烧结2小时后,磨耗比由30万提高到36万,提高了20%,抗冲击韧性由84焦耳提高到97焦耳,提高了15%。
44.说明对比例1采用高性能复合传压部件代替叶腊石块,能够更有效的提高内部压力,所制备的聚晶金刚石复合片不仅具有较高的力学性能,而且还具有良好的热学性能;而专利cn107362750 a一种聚晶金刚石复合片及其合成块中采用的是叶腊石块,由于叶蜡石由于其材料本身的局限性,传压过程中压力损失大,导致施加到合成块中心区域的压力与外部施压相比,受到了极大地削弱,造成所制备的聚晶金刚石复合片力学性能和热学性能不是很高。
45.进一步的,将实施例4所制备的高性能复合传压部件采用对比例1中相同的方法得到的聚晶金刚石复合片在磨耗比、抗冲击韧性、耐热温度等性能方面具有与实施例2相同的性能。
46.最后所应说明的是:上述实施例仅用于说明而非限制本发明的技术方案,任何对本发明进行的等同替换及不脱离本发明精神和范围的修改或局部替换,其均应涵盖在本发明权利要求保护的范围之内。