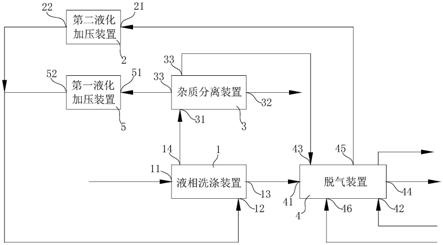
1.本发明属于聚合物制备技术领域,具体涉及一种用于洗涤聚烯烃的系统和方法。
背景技术:2.聚烯烃具有相对密度小、耐化学药品性、耐水性好的优点,同时具有良好的机械强度、电绝缘性等特点,可用于薄膜、管材、板材、各种成型制品、电线电缆等,在农业、包装、电子、电气、汽车、机械、日用杂品等方面有广泛的用途。
3.尽管我国聚烯烃自给率逐年上升,但高端产品基础较弱,仍严重依赖进口,当前国内高端/高性能聚烯烃自给率仅为38%。高性能材料品种包括茂金属系列聚烯烃弹性体、高刚性高抗冲共聚丙烯、多样化的各种改性树脂材料等。这些品种或国内产量较少,或质量未能完全符合用户的要求。目前国内高端专用料仍以进口为主,约80%依赖进口。
4.影响聚烯烃品质主要为等规度和杂质(杂质如残留催化剂、助催化剂、低聚物、盐类、反应生成物等)的影响,其中杂质主要是用灰分指标来表示,大致说明催化剂的活性低,随之而来的是黄指的升高。灰分高在挤出加工,特别是纤维纺丝的加工有比较大的影响。灰分过高原因很多,主要是原料杂质含量高,导致反应变差,主催化剂、teal等残余的金属离子存在于树脂中。灰分过高易产生如下影响:一、聚乙烯制品如超高分子量聚乙烯板等膜料易破膜,产品外观色泽略有影响;二、造粒机组加工时过滤网易堵塞。
5.聚烯烃中氯含量也是非常重要的指标,在催化剂活性不是很高的生产装置中,过高的氯含量会对挤出造粒产生影响,例如文献《本体法聚丙烯的脱氯技术》指出,当氯含量超过50ppm时,会在挤出造粒阶段产生hcl,腐蚀设备。另外在一些高端领域,例如电容膜材料中,聚烯烃中氯含量更加严格。过高的氯含量会严重影响电容膜的介电性能,通常要求氯含量在10ppm以下。
6.由于在聚烯烃生产过程中,催化剂等均被附着在聚烯烃里,通过简单的洗涤,很难将其脱除干净,常见的洗涤方法有间歇法洗涤,需要使用溶剂进行洗涤纯化,此过程是一个大量消耗溶剂且高能耗、高三废的工艺步骤。且目前间歇法洗涤主要应用洗涤釜、抽干釜进行洗涤纯化作业,一般需进行4-6次洗涤,洗涤时间为5-8小时,抽真空干燥需要约20小时。因此,间歇法洗涤存在时间长和洗涤效率低的缺陷。此外,为了提高催化剂的洗涤效果,往往采取延长洗涤时间、增加溶剂用量的措施,但延长洗涤时间会影响生产效率,增加溶剂用量会提高生产成本。
7.也有一些方法采用高效洗涤设备,例如专利号为201610940665.x的发明专利《一种洗涤器和洗涤装置及纯化聚烯烃催化剂的方法》(授权公告号为cn107973868b)、专利号为200810178292.2的发明专利《聚烯烃粗产物催化剂除去和洗涤体系》(授权公告号为cn101412774b)均公开了一种聚烯烃的洗涤设备,有效的提高了洗涤效率。
8.也有方法采用连续操作,例如专利号为200810178290.3的发明专利《洗涤聚烯烃粗产物以从中除去残余催化剂的方法》(授权公告号为cn101412772b)公开了一种洗涤聚烯烃粗产物以从中除去残余催化剂的方法,该方法可以概括为串联三个沉降设备,在沉降设
备中清洗,能洗去部分杂质,尽管该方法采用了多级沉降操作,然而在聚烯烃生产过程中,部分催化剂、助催化剂等杂质与聚烯烃紧密包裹,普通的沉降洗涤效果并不好,该方法也没有提及洗涤液如何处理。
9.也有一些方法使用非极性溶剂去洗涤,由于非极性溶剂和聚烯烃有溶胀效应,因此洗涤效果较好,例如申请号为gb58275的英国专利《process for the purification of olefin polymerizates》(公开号为gb1491371a)、申请号为us89834978的美国专利《purification ofpropylene polymerization product》》(授权公告号为us4167619a)公开了利用液态丙烯去洗涤的方案,然而如同该类方法所描述的,要取得较好洗涤效果,需要在洗涤过程中加入醇类和供氧体(如双氧水等),双氧水脱氧后变成水,水是极性物质对反应系统影响很大,丙烯需要和极性物质严格分离后才能返回反应系统。另外单纯的用液相洗涤,除非采用强烈搅拌,否则洗涤效果也不尽如人意。
技术实现要素:10.本发明所要解决的第一个技术问题是针对现有技术的现状,提供一种用于洗涤聚烯烃的系统,以得到低灰分、低氯含量的聚烯烃洗涤产品,并提高洗涤效率。
11.本发明所要解决的第二个技术问题是提供一种采用上述系统对聚烯烃进行洗涤的方法。
12.本发明解决上述第一个技术问题所采用的技术方案为:一种用于洗涤聚烯烃的系统,其特征在于包括:
13.液相洗涤装置,用于使循环工质以液相状态与聚烯烃进行洗涤,该液相洗涤装置具有供待洗涤的聚烯烃进入的洗涤入口、供循环工质进入的循环工质入口、供洗涤后的聚烯烃输出的洗涤出口以及供洗涤后的循环工质、聚烯烃中的杂质输出的杂质循环工质出口;
14.杂质分离装置,用于将洗涤后的循环工质汽化并分离出杂质以及气相状态的循环工质,其具有与所述杂质循环工质出口相连通的杂质循环工质入口、供分离出的杂质输出的杂质输出口、供分离出的循环工质输出的循环工质出口;
15.脱气装置,用于脱除洗涤后的聚烯烃上残留的循环工质及杂质,该脱气装置具有供洗涤后的聚烯烃输入其中的脱气入口、供惰性气体进入其中的惰性气体入口、供上述杂质分离装置分离出的循环工质的部分输入其中的第三循环工质入口、供脱除循环工质及杂质后的聚烯烃输出的脱气出口、供脱除下来的循环工质输出其中的第三循环工质出口;所述第三循环工质入口与所述杂质分离装置的循环工质出口相连通;
16.第一液化加压装置,用于对气相的循环工质进行液化加压,从而使得气相的循环工质变成液相的循环工质,该第一液化加压装置具有第一液化入口和第一液化出口,所述第一液化入口与所述杂质分离装置的循环工质出口相连通,所述第一液化出口与所述液相洗涤装置的循环工质入口相连通;
17.第二液化加压装置,用于对气相的循环工质进行液化加压,从而使得气相的循环工质变成液相的循环工质,该第二液化加压装置具有第二入口和第二出口,所述第二入口与所述脱气装置的第三循环工质出口相连通,所述第二出口与所述液相洗涤装置的循环工质入口)相连通;
18.同时,所述液相洗涤装置或/和杂质分离装置或/和脱气装置上具有供能与上述杂质发生化学反应的化学试剂进入的化学试剂入口。
19.优选地,还包括有用于输入循环工质的补入管线,该补入管线的输出端与所述系统中的至少一个装置相连通。
20.进一步地,还包括具有膜的膜分离组件,该膜分离组件的入口与所述杂质分离装置的循环工质出口相连通,该膜分离组件之膜的高压侧的出口与所述第一液化加压装置的第一液化入口相连通;该膜分离组件之膜的低压侧的出口与所述脱气装置的第三循环工质入口相连通;且所述膜之供经上述化学反应后的杂质穿过的渗透系数大于供上述循环工质穿过的渗透系数。
21.优选地,所述液相洗涤装置为液相洗涤塔,且液相洗涤塔的顶部具有上述的杂质循环工质出口,上部具有上述的洗涤入口,下部具有上述的循环工质入口,底部具有上述的洗涤出口;
22.所述脱气装置包括脱气罐和杂质脱除罐,所述脱气罐的上部具有上述的脱气入口、第三循环工质入口,下部具有上述的惰性气体入口、化学试剂入口,底部具有上述的脱气出口;所述脱气罐的顶部出口通过循环压缩机与所述杂质脱除罐相连通,且所述杂质脱除罐的上部具有上述第三循环工质出口以及供惰性气体输出的惰性气体出口;
23.所述第一液化加压装置包括有第一换热器和第一增压泵,所述第一换热器具有第一冷介质通道和第一热介质通道,且第一冷介质通道具有第一冷介质入口和第一冷介质出口,第一热介质通道具有第一热介质入口和第一热介质出口;
24.所述第二液化加压装置包括有第二增压泵;
25.还包括有第一加热器、第四加热器;
26.所述液相洗涤塔之杂质循环工质出口与所述第一换热器的第一冷介质入口相连通,所述第一换热器之第一冷介质出口与所述杂质分离装置的杂质循环工质入口相连,所述杂质分离装置之循环工质出口与所述膜分离组件的入口相连通,所述膜分离组件之膜的高压侧的出口与所述第一换热器的第一热介质入口相连通,所述第一换热器的第一热介质出口依次通过上述第一增压泵、第一加热器与所述液相洗涤塔之循环工质入口相连通;所述膜分离组件之膜的低压侧的出口与上述脱气罐上的第三循环工质入口相连通,所述脱气罐之脱气入口与所述液相洗涤塔之洗涤出口之间通过第四加热器相连通;所述杂质脱除罐之第三循环工质出口通过上述第二增压泵与所述第一增压泵的入口相连通;所述杂质脱除罐之惰性气体出口与所述脱气罐之惰性气体入口相连通;所述补入管线的输出端与所述第二增压泵的入口相连通。
27.同样优选地,所述液相洗涤装置为液相洗涤塔,且液相洗涤塔的顶部具有上述的杂质循环工质出口,上部具有上述的洗涤入口,下部具有上述的循环工质入口,底部具有上述的洗涤出口;
28.所述脱气装置包括第一脱气罐、第二脱气罐和杂质脱除罐,所述第一脱气罐的上部具有上述的脱气入口、第三循环工质入口,下部具有上述的化学试剂入口,所述第一脱气罐的顶部出口与所述杂质脱除罐相连通,且所述杂质脱除罐的上部具有上述第三循环工质出口;所述第一脱气罐的底部出口与所述第二脱气罐的上部入口相连通,且第二脱气罐的下部具有上述的惰性气体入口,底部具有上述的脱气出口,同时第二脱气罐的顶部出口通
过循环压缩机与所述惰性气体入口相连通;
29.所述第一液化加压装置包括有第一换热器和第一增压泵,所述第一换热器具有第一冷介质通道和第一热介质通道,且第一冷介质通道具有第一冷介质入口和第一冷介质出口,第一热介质通道具有第一热介质入口和第一热介质出口;
30.所述第二液化加压装置包括有第二增压泵;
31.还包括有第一加热器、第四加热器;
32.所述液相洗涤塔之杂质循环工质出口与所述第一换热器的第一冷介质入口相连通,所述第一换热器之第一冷介质出口与所述杂质分离装置的杂质循环工质入口相连,所述杂质分离装置之循环工质出口与所述膜分离组件的入口相连通,所述膜分离组件之膜的高压侧的出口与所述第一换热器的第一热介质入口相连通,所述第一换热器的第一热介质出口依次通过上述第一增压泵、第一加热器与所述液相洗涤塔之循环工质入口相连通;所述膜分离组件之膜的低压侧的出口与上述第一脱气罐上的第三循环工质入口相连通,所述第一脱气罐之脱气入口与所述液相洗涤塔之洗涤出口之间通过第四加热器相连通;所述杂质脱除罐之第三循环工质出口通过上述第二增压泵与所述第一增压泵的入口相连通;所述补入管线的输出端与所述第二增压泵的入口相连通。
33.优选地,所述液相洗涤装置为液相洗涤塔,且液相洗涤塔的顶部具有上述的杂质循环工质出口,上部具有上述的洗涤入口,下部具有上述的循环工质入口,底部具有上述的洗涤出口;
34.所述脱气装置包括一次闪蒸罐、二次闪蒸罐和脱气罐,所述一次闪蒸罐的上部具有上述的脱气入口,顶部具有上述的第三循环工质出口,下部具有上述的第三循环工质入口,所述一次闪蒸罐的底部出口与所述二次闪蒸罐相连通,该二次闪蒸罐的顶部具有上述的第三循环工质出口,该二次闪蒸罐的底部出口与所述脱气罐的上部接口相连通,且该脱气罐的下部具有上述的化学试剂入口、惰性气体入口,底部具有上述的脱气出口;
35.所述第一液化加压装置包括有第一换热器和第一增压泵,所述第一换热器具有第一冷介质通道和第一热介质通道,且第一冷介质通道具有第一冷介质入口和第一冷介质出口,第一热介质通道具有第一热介质入口和第一热介质出口;
36.所述第二液化加压装置包括有第二增压泵;
37.还包括有第一加热器、第四加热器、闪蒸冷凝器、减温减压塔;
38.所述液相洗涤塔之杂质循环工质出口与所述第一换热器的第一冷介质入口相连通,所述第一换热器之第一冷介质出口与所述杂质分离装置的杂质循环工质入口相连,所述杂质分离装置之循环工质出口与所述第一换热器的第一热介质入口相连通,所述第一换热器的第一热介质出口依次通过上述第一增压泵、第一加热器与所述液相洗涤塔之循环工质入口相连通;所述杂质分离装置之循环工质出口同时与所述减温减压塔的入口相连通,所述减温减压塔的顶部出口与所述一次闪蒸罐的第三循环工质出口相连通,底部出口与所述闪蒸冷凝器的入口相连通,该闪蒸冷凝器的出口通过上述的第二增压泵与所述第一增压泵的入口相连通;所述一次闪蒸罐之脱气入口与所述液相洗涤塔之洗涤出口之间通过第四加热器相连通;所述补入管线有两条,第一条补入管线的输出端与所述闪蒸冷凝器的入口相连通,第二条补入管线的输出端与所述一次闪蒸罐的第三循环工质入口相连通。
39.在上述各方案中,优选地,所述化学试剂为用于与上述杂质反应的醇类、脂类、含
水环氧类化合物的至少一种,从而将难脱除的杂质经化学反应后变成易脱除的杂质。
40.所述化学试剂优选为异丙醇、正丁醇、乙二醇、碳酸二甲酯、亚磷酸三甲酯、亚硫酸二甲酯、磷酸二甲酯、甲基膦酸二甲酯、磷酸三甲酯、环氧丙烷、水的至少一种。
41.优选地,所述循环工质为烯烃、烷烃中的至少一种,且所述烯烃、烷烃中的碳原子数c为2≤c≤8;所述循环工质为庚烷、己烷、异丁烷、正丁烯、丙烷、丙烯、乙烷、乙烯中的至少一种。
42.本技术中的杂质分离装置可直接为一台设备,如加热罐,循环工质的汽化和分离均在加热罐中进行。杂质分离装置也可为至少两台设备,分别为汽化器和分离罐,循环工质先经过汽化器的汽化,然后再输入分离罐内进行分离。
43.本发明解决上述第二个技术问题所采用的技术方案为一种采用如上所述的系统对聚烯烃进行洗涤的方法,其特征在于步骤如下:
44.a:将循环工质、聚烯烃输入液相洗涤装置内,使循环工质以液相状态与聚烯烃进行洗涤操作,其中,循环工质与所述聚烯烃的质量比为(0.5~3):1【优选为(1~1.5):1】,液相洗涤装置的操作压力为5~40bar,操作温度为40~150℃,洗涤时间为5~60min;
45.b:将步骤a洗涤后的杂质与循环工质输入杂质分离装置,循环工质在杂质分离装置中汽化而呈气相状态并与杂质相分离,气相的循环工质分为两个部分,第一部分经第一液化加压装置冷却成液相状态并加压后作为上述步骤a的循环工质,第二部分输入脱气装置内与经过上述步骤a洗涤后的聚烯烃混合,且将惰性气体输入脱气装置内,以脱除聚烯烃中的液相循环工质、杂质及其他挥发性物质,其中杂质分离装置的操作压力为0.1~0.3mpaa,操作温度≥该循环工质在操作压力下的饱和温度;惰性气体与聚烯烃质量比为0.01~0.1;脱气装置的内部压力为真空~0.3mpaa,温度为100~200℃;
46.c:将步骤b中与聚烯烃接触后的第二部分循环工质经加压液化或者液化加压后变成液体,作为步骤a的循环工质;
47.在上述步骤a或/和步骤b中输入化学试剂,用于将难脱除的杂质经化学反应后变成容易脱除的杂质,其中化学试剂的压力大于步骤a的操作压力或步骤b的杂质分离装置的操作压力,化学试剂与聚烯烃质量比为0.0005~0.001。
48.与现有技术相比,本发明的优点在于:通过设置液相洗涤装置、杂质分离装置、脱气装置、第一液化加压装置,并在液相洗涤装置或/和杂质分离装置或/和脱气装置上设有供能与杂质发生化学反应的化学试剂进入的化学试剂入口,如此,聚烯烃先在液相洗涤装置内与液相的循环工质进行洗涤,从而洗去大部分的杂质,洗涤后的杂质与循环工质通过杂质分离装置后,分离出气相状态的循环工质,气相状态的循环工质一部分可经过液化加压后输入液相洗涤装置,另一部分可输入脱气装置内,与洗涤后的聚烯烃混合,并在惰性气体的作用下进行脱气,以脱去聚烯烃中的液相循环工质、杂质及其他挥发性物质,从脱气装置出来的循环工质经加压后可输入液相洗涤装置。故而,本技术的系统及洗涤方法能有效洗去聚烯烃上的杂质,以得到低灰分、低氯含量的聚烯烃洗涤产品的同时,还能循环利用循环工质,并且能提高洗涤效率。同时,本技术结构简单,便于实施。
附图说明
49.图1为本发明实施例一中系统的部分结构示意图;
50.图2为本发明实施例一中系统的结构示意图;
51.图3为本发明实施例二中系统的结构示意图;
52.图4为本发明实施例三中系统的结构示意图。
具体实施方式
53.以下结合附图实施例对本发明作进一步详细描述。
54.实施例一:
55.如图1~2所示,为本发明的一种用于洗涤聚烯烃的系统和方法的优选实施例一,该系统包括液相洗涤装置1、杂质分离装置3、脱气装置4、第一液化加压装置5、第二液化加压装置2、补入管线100、膜分离组件6、第一加热器71、第四加热器74、。
56.其中,液相洗涤装置1用于使循环工质以液相状态与聚烯烃进行洗涤,该液相洗涤装置1为液相洗涤塔,且液相洗涤塔的上部具有供待洗涤的聚烯烃进入的洗涤入口11,下部具有供循环工质进入的循环工质入口12,底部具有供洗涤后的聚烯烃输出的洗涤出口13,顶部具有供洗涤后的循环工质、聚烯烃中的杂质输出的杂质循环工质出口14。
57.杂质分离装置3包括有汽化器3a和分离罐3b,汽化器3a用于将洗涤后的循环工质汽化,该汽化器3a的入口端与杂质循环工质出口14相连通。
58.分离罐3b用于分离出杂质以及气相状态的循环工质,分离罐3b的顶部具有供分离出的循环工质输出的循环工质出口33,侧部具有与汽化器3a的出口端相连通的杂质循环工质入口31,底部具有供分离出的杂质输出的杂质输出口32。
59.脱气装置4用于脱除洗涤后的聚烯烃上残留的循环工质及杂质,脱气装置4包括脱气罐4a和杂质脱除罐4b,脱气罐4a的上部具有供洗涤后的聚烯烃输入其中的脱气入口41、供上述分离罐3b分离出的循环工质的部分输入其中的第三循环工质入口43,下部具有供惰性气体进入其中的惰性气体入口42、供能与杂质发生化学反应的化学试剂进入的化学试剂入口46,底部具有供脱除循环工质及杂质后的聚烯烃输出的脱气出口44;脱气罐4a的顶部出口通过循环压缩机4c与杂质脱除罐4b相连通,且杂质脱除罐4b的上部具有供脱除下来的循环工质输出其中的第三循环工质出口45以及供惰性气体输出的惰性气体出口47;第三循环工质入口43与分离罐3b的循环工质出口33相连通;第三循环工质出口45与液相洗涤装置1的循环工质入口12相连通。
60.上述第一液化加压装置5用于对气相的循环工质进行液化加压,从而使得气相的循环工质变成液相的循环工质,该第一液化加压装置5具有第一液化入口51和第一液化出口52,第一液化入口51与分离罐3b的循环工质出口33相连通,第一液化出口52与液相洗涤装置1的循环工质入口12相连通。本实施例中,第一液化加压装置5包括有第一换热器53和第一增压泵54,第一换热器53具有第一冷介质通道和第一热介质通道,且第一冷介质通道具有第一冷介质入口531和第一冷介质出口532,第一热介质通道具有第一热介质入口533和第一热介质出口534;其中,第一热介质入口533为上述的第一液化入口51,第一增压泵54的输出端为上述的第一液化出口52。
61.第二液化加压装置2包括有第二增压泵23。
62.膜分离组件6内部具有膜,该膜分离组件6的入口与分离罐3b的循环工质出口33相连通,该膜分离组件6之膜的高压侧(即膜分离组件6之入口所在侧)的出口与第一液化加压
装置5的第一液化入口51相连通;该膜分离组件6之膜的低压侧的出口与脱气装置4的第三循环工质入口43相连通;且膜之供经上述化学反应后的杂质穿过的渗透系数大于供上述循环工质穿过的渗透系数。
63.上述各装置的连接方式如下:
64.液相洗涤塔之杂质循环工质出口14与第一换热器53的第一冷介质入口531相连通,第一换热器53之第一冷介质出口532与汽化器3a的入口端相连,汽化器3a的出口端与分离罐3b的杂质循环工质入口31相连通,分离罐3b之循环工质出口33与膜分离组件6的入口相连通,膜分离组件6之膜的高压侧的出口与第一换热器53的第一热介质入口533相连通,第一换热器51的第一热介质出口534依次通过上述第一增压泵54、第一加热器71与液相洗涤塔之循环工质入口12相连通;膜分离组件6之膜的低压侧的出口与上述脱气罐4a上的第三循环工质入口43相连通,脱气罐4a之脱气入口41与液相洗涤塔之洗涤出口13之间通过第四加热器74相连通;杂质脱除罐4b之第三循环工质出口45通过上述第二增压泵23与第一增压泵54的入口相连通;杂质脱除罐4b之惰性气体出口47与脱气罐4a之惰性气体入口42相连通;补入管线100的输出端与第二增压泵23的入口相连通,以补入循环工质。
65.采用本实施例的系统对聚烯烃进行洗涤的方法如下:
66.以洗涤1000kg/h聚丙烯粉料为例,物流号为pp-cru,聚丙烯粉料含杂质106ppm,杂质主要为催化剂、助催化剂残留,成分为ti、mg、al等化合物,循环工质为正己烷,常温常压的新鲜正己烷(温度为40℃,压力为1bar,质量流量为7.32kg/hr),物流号为wash-f,在第二增压泵23之前补入,经过第二增压泵23增压至30bar后与第一换热器53之第一热介质出口534输出的介质汇合,然后经第一增压泵54增压后,进入第一加热器71升温至80℃,与聚丙烯粉料在液相洗涤装置1中逆流接触洗涤,液相洗涤装置1中循环工质与聚丙烯粉料的质量比为1.3:1,循环工质的输入温度为80℃,压力为10bar;聚烯烃的输入温度为40℃,压力为10bar,质量流量为1000.11kg/hr;洗涤时间为30min。洗涤后的物流(物流号为wash-out,温度为53.38℃,压力为10bar,质量流量为904.64kg/hr),经第一换热器53的第一冷介质通道、汽化器3a汽化,在分离罐3b中分离出杂质,分离出的杂质的物流号为impur-1,从分离罐3b出来的气相物流进入膜分离组件6后,进行化学反应生成的物质的分离操作,高压渗透侧为第一物流,低压渗透侧为第二物流,第一物流进入第一换热器53的第一热介质通道,第二物流温度为240℃左右,进入脱气罐4a,脱气罐4a的内部压力为0.1mpaa,温度为140℃,同时脱气罐4a中加入化学试剂环氧丙烷(物流号为reagents,且环氧丙烷的输入温度为40℃,压力为3bar、质量流量为0.5kg/hr),在脱气罐4a底部引入循环惰性气体(物流号为n2-fresh,且循环惰性气体的输入温度为40℃、压力为3bar、质量流量为50kg/h),循环惰性气体经过冷凝器后进入脱气罐4a内;脱气罐4a顶部物流进循环压缩机4c增压后进入杂质脱除罐4b,该杂质脱除罐4b主要脱除氯丙醇,由于氯丙醇和正己烷共沸,共沸温度为97.4℃,因此杂质脱除罐4b塔底会有部分正己烷损耗。杂质脱除罐4b顶部气相主要为循环惰性气体,返回脱气罐4a;杂质脱除罐4b顶部液相主要为循环工质,去第二增压泵23增压,完成循环工质的循环洗涤。洗涤后的聚丙烯从脱气罐4a的底部排出,排出的聚丙烯的物流号为pp-prod,且排出的聚丙烯的温度为152.4℃,压力为1bar,质量流量为1000.12kg/hr。
67.本实施例采用了正己烷作为循环工质,从下表1中可以看到,聚丙烯粉料含有106ppm左右的催化剂、助催化剂残留,经本工艺洗涤后,催化剂、助催化剂中的大部分的金
属灰分已经被洗出去,残留的金属杂质在20ppm左右。杂质中的氯也以氯丙醇的形式被洗涤脱除,由于氯丙醇和正己烷共沸,因此在脱除氯丙醇的过程中也损耗了些正己烷,另外在脱气过程中也会有部分正己烷损耗,总的新鲜正己烷补充量为7.32kg/h左右。
68.表1物料平衡表
[0069][0070][0071]
实施例二:
[0072]
如图3所示,为本发明的一种用于洗涤聚烯烃的系统和方法的优选实施例二,该系
统包括液相洗涤装置1、杂质分离装置3、脱气装置4、第一液化加压装置5、第二液化加压装置2、补入管线100、膜分离组件6、第一加热器71、第四加热器74。
[0073]
其中,液相洗涤装置1用于使循环工质以液相状态与聚烯烃进行洗涤,该液相洗涤装置1为液相洗涤塔,且液相洗涤塔的上部具有供待洗涤的聚烯烃进入的洗涤入口11,下部具有供循环工质进入的循环工质入口12,底部具有供洗涤后的聚烯烃输出的洗涤出口13,顶部具有供洗涤后的循环工质、聚烯烃中的杂质输出的杂质循环工质出口14。
[0074]
杂质分离装置3包括有汽化器3a和分离罐3b,汽化器3a用于将洗涤后的循环工质汽化,该汽化器3a的入口端与杂质循环工质出口14相连通。
[0075]
分离罐3b用于分离出杂质以及气相状态的循环工质,分离罐3b的顶部具有供分离出的循环工质输出的循环工质出口33,侧部具有与汽化器3a的出口端相连通的杂质循环工质入口31,底部具有供分离出的杂质输出的杂质输出口32。
[0076]
脱气装置4用于脱除洗涤后的聚烯烃上残留的循环工质及杂质,脱气装置4包括第一脱气罐4d、第二脱气罐4e和杂质脱除罐4b,第一脱气罐4d的上部具有供洗涤后的聚烯烃输入其中的脱气入口41、供上述分离罐3b分离出的循环工质的部分输入其中的第三循环工质入口43,下部具有供能与杂质发生化学反应的化学试剂进入的化学试剂入口46,第一脱气罐4d的顶部出口与杂质脱除罐4b相连通,且杂质脱除罐4b的上部具有供脱除下来的循环工质输出其中的第三循环工质出口45;第一脱气罐4d的底部出口与第二脱气罐4e的上部入口相连通,且第二脱气罐4e的下部具有供惰性气体进入其中的惰性气体入口42,底部具有供脱除循环工质及杂质后的聚烯烃输出的脱气出口44,同时第二脱气罐4e的顶部出口通过循环压缩机4c与惰性气体入口42相连通。
[0077]
上述第一液化加压装置5用于对气相的循环工质进行液化加压,从而使得气相的循环工质变成液相的循环工质,该第一液化加压装置5具有第一液化入口51和第一液化出口52,第一液化入口51与分离罐3b的循环工质出口33相连通,第一液化出口52与液相洗涤装置1的循环工质入口12相连通。本实施例中,第一液化加压装置5包括有第一换热器53和第一增压泵54,第一换热器53具有第一冷介质通道和第一热介质通道,且第一冷介质通道具有第一冷介质入口531和第一冷介质出口532,第一热介质通道具有第一热介质入口533和第一热介质出口534;其中,第一热介质入口533为上述的第一液化入口51,第一增压泵54的输出端为上述的第一液化出口52。
[0078]
第二液化加压装置2包括第二增压泵23。
[0079]
膜分离组件6内部具有膜,该膜分离组件6的入口与分离罐3b的循环工质出口33相连通,该膜分离组件6之膜的高压侧(即膜分离组件6之入口所在侧)的出口与第一液化加压装置5的第一液化入口51相连通;该膜分离组件6之膜的低压侧的出口与脱气装置4的第三循环工质入口43相连通;且膜之供经上述化学反应后的杂质穿过的渗透系数大于供上述循环工质穿过的渗透系数。
[0080]
上述各装置的连接方式如下:
[0081]
液相洗涤塔之杂质循环工质出口14与第一换热器53的第一冷介质入口531相连通,第一换热器53之第一冷介质出口532与汽化器3a的入口端相连,汽化器3a的出口端与分离罐3b的杂质循环工质入口31相连通,分离罐3b之循环工质出口33与膜分离组件6的入口相连通,膜分离组件6之膜的高压侧的出口与第一换热器53的第一热介质入口533相连通,
第一换热器51的第一热介质出口534依次通过上述第一增压泵54、第一加热器71与液相洗涤塔之循环工质入口12相连通;膜分离组件6之膜的低压侧的出口与上述第一脱气罐4d上的第三循环工质入口43相连通,第一脱气罐4d之脱气入口41与液相洗涤塔之洗涤出口13之间通过第四加热器74相连通;杂质脱除罐4b之第三循环工质出口45通过上述第二增压泵23与第一增压泵54的入口相连通;补入管线100的输出端与第二增压泵23的入口相连通,以补入循环工质。
[0082]
采用本实施例的系统对聚烯烃进行洗涤的方法如下:
[0083]
以洗涤1000kg/h聚丙烯粉料为例,物流号为pp-cru,聚丙烯粉料含杂质106ppm,杂质主要为催化剂、助催化剂残留,成分为ti、mg、al等化合物,循环工质为正己烷,常温常压的新鲜正己烷(温度为40℃,压力为1bar,质量流量为7.32kg/hr),物流号为wash-f,在第二增压泵23之前补入,经过第二增压泵23增压至30bar后与第一换热器53之第一热介质出口534输出的介质汇合,然后经第一增压泵54增压后,进入第一加热器71升温至80℃,与聚丙烯粉料在液相洗涤装置1中逆流接触洗涤,液相洗涤装置1中循环工质与聚丙烯粉料的质量比为3:1,循环工质的输入温度为80℃,压力为5bar;聚烯烃的输入温度为40℃,压力为10bar,质量流量为1000.11kg/hr;洗涤时间为5min。洗涤后的物流(物流号为wash-out,温度为53.38℃,压力为10bar,质量流量为904.64kg/hr),经第一换热器53的第一冷介质通道、汽化器3a汽化,在分离罐3b中分离出杂质,分离出的杂质的物流号为impur-1,从分离罐3b出来的气相物流进入膜分离组件6后,进行化学反应生成的物质的分离操作,高压渗透侧为第一物流,低压渗透侧为第二物流,第一物流进入第一换热器53的第一热介质通道,第二物流温度为240℃左右,进入第一脱气罐4d,同时第一脱气罐4d中加入化学试剂环氧丙烷(物流号为reagents,且环氧丙烷的输入温度为40℃,压力为3bar、质量流量为0.5kg/h),第一脱气罐4d顶部物流进入杂质脱除罐4b,杂质脱除罐4b顶部液相主要为循环工质,去第二增压泵23增压,完成循环工质的循环洗涤。第一脱气罐4d底部物流进入第二脱气罐4e,同时,第二脱气罐4e下部引入循环惰性气体(物流号为n2-fresh,且循环惰性气体的输入温度为40℃、压力为3bar、质量流量为50kg/h),循环惰性气体经过冷凝器后进入第二脱气罐4e内,第二脱气罐4e顶部物流经循环压缩机4c增压以及冷凝器后再返回至第二脱气罐4e内。上述第一脱气罐4d的内部压力为0.3mpaa,温度为100℃;第二脱气罐4e的内部压力为0.3mpa,温度为200℃。
[0084]
实施例三:
[0085]
如图4所示,为本发明的一种用于洗涤聚烯烃的系统和方法的优选实施例三,该系统包括液相洗涤装置1、杂质分离装置3、脱气装置4、第一液化加压装置5、第二液压加压装置2、补入管线100、第一加热器71、第四加热器74、闪蒸冷凝器8、减温减压塔9。
[0086]
其中,液相洗涤装置1用于使循环工质以液相状态与聚烯烃进行洗涤,该液相洗涤装置1为液相洗涤塔,且液相洗涤塔的上部具有供待洗涤的聚烯烃进入的洗涤入口11,下部具有供循环工质进入的循环工质入口12,底部具有供洗涤后的聚烯烃输出的洗涤出口13,顶部具有供洗涤后的循环工质、聚烯烃中的杂质输出的杂质循环工质出口14。
[0087]
杂质分离装置3包括有汽化器3a和分离罐3b,汽化器3a用于将洗涤后的循环工质汽化,该汽化器3a的入口端与杂质循环工质出口14相连通。
[0088]
分离罐3b用于分离出杂质以及气相状态的循环工质,分离罐3b的顶部具有供分离
出的循环工质输出的循环工质出口33,侧部具有与汽化器3a的出口端相连通的杂质循环工质入口31,底部具有供分离出的杂质输出的杂质输出口32。
[0089]
脱气装置4用于脱除洗涤后的聚烯烃上残留的循环工质及杂质,脱气装置4包括一次闪蒸罐4j、二次闪蒸罐4k和脱气罐4a,一次闪蒸罐4j的上部具有供洗涤后的聚烯烃输入其中的脱气入口41,顶部具有供脱除下来的循环工质输出其中的第三循环工质出口45,下部具有供上述分离罐3b分离出的循环工质的部分输入其中的第三循环工质入口43,一次闪蒸罐4j的底部出口与二次闪蒸罐4k相连通,该二次闪蒸罐4k的顶部具有供脱除下来的循环工质输出其中的第三循环工质出口45,该二次闪蒸罐4k的底部出口与脱气罐4a的上部接口相连通,且该脱气罐4a的下部具有供能与杂质发生化学反应的化学试剂进入的化学试剂入口46、供惰性气体进入其中的惰性气体入口42,底部具有供脱除循环工质及杂质后的聚烯烃输出的脱气出口44;
[0090]
上述第一液化加压装置5用于对气相的循环工质进行液化加压,从而使得气相的循环工质变成液相的循环工质,该第一液化加压装置5具有第一液化入口51和第一液化出口52,第一液化入口51与分离罐3b的循环工质出口33相连通,第一液化出口52与液相洗涤装置1的循环工质入口12相连通。本实施例中,第一液化加压装置5包括有第一换热器53和第一增压泵54,第一换热器53具有第一冷介质通道和第一热介质通道,且第一冷介质通道具有第一冷介质入口531和第一冷介质出口532,第一热介质通道具有第一热介质入口533和第一热介质出口534;其中,第一热介质入口533为上述的第一液化入口51,第一增压泵54的输出端为上述的第一液化出口52。
[0091]
第二液化加压装置2包括第二增压泵23。
[0092]
上述各装置的连接方式如下:
[0093]
液相洗涤塔之杂质循环工质出口14与第一换热器53的第一冷介质入口531相连通,第一换热器53之第一冷介质出口532与汽化器3a的入口端相连,汽化器3a的出口端与分离罐的杂质循环工质入口31相连通,分离罐之循环工质出口33与第一换热器53的第一热介质入口533相连通,第一换热器53的第一热介质出口534依次通过上述第一增压泵54、第一加热器71与液相洗涤塔之循环工质入口12相连通;分离罐之循环工质出口33同时与减温减压塔9的入口相连通,减温减压塔9的顶部出口与一次闪蒸罐4j的第三循环工质出口45相连通,底部出口与闪蒸冷凝器8的入口相连通,该闪蒸冷凝器8的出口通过第二增压泵23与第一增压泵54的入口相连通;一次闪蒸罐4j之脱气入口41与液相洗涤塔之洗涤出口13之间通过第四加热器74相连通;补入管线100有两条,第一条补入管线110的输出端与闪蒸冷凝器8的入口相连通,第二条补入管线120的输出端与一次闪蒸罐4j的第三循环工质入口43相连通,以补入循环工质。
[0094]
采用本实施例的系统对聚烯烃进行洗涤的方法如下:
[0095]
以洗涤1000kg/h聚丙烯粉料为例,物流号为pp-cru,聚丙烯粉料含杂质92ppm,杂质主要为催化剂、助催化剂残留,成分为ti、mg、al等化合物,循环工质为丙烯、正丁烯,常温常压的新鲜液体正丁烯(物流号为wash-f-h,温度为40℃,压力为8bar,质量流量为8.03kg/hr),在闪蒸冷凝器8之前补入,在此处补入正丁烯的作用除了补充损耗,更主要是为了增加闪蒸汽体中重组分的含量,使得闪蒸汽体能够使用循环水就可以冷凝成液体,经过闪蒸冷凝器8冷凝后,进入第二增压泵23增压至40bar,然后与第一换热器53之第一热介质出口534
输出的介质汇合,然后经第一增压泵54增压后,进入第一加热器71升温至80℃,与聚丙烯粉料在液相洗涤装置1中逆流接触洗涤,液相洗涤装置1中循环工质与聚丙烯粉料的质量比为1.4:1,聚烯烃的质量流量为1000.09kg/hr;洗涤温度为80℃,洗涤压力为40bar,洗涤时间为40min。洗涤后的物流,物流号为wash-out,经第一换热器53的第一冷介质通道、汽化器3a汽化,在分离罐3b中分离出杂质,分离出的杂质的物流号为impur-1,从分离罐3b出来的气相物流分成两股物流,第一物流进入第一换热器53的第一热介质通道冷凝成液相,第二物流温度此时为高温高压状态,第二物流先进入减温减压塔9降温降压至50℃、9bar左右,减温减压塔9顶部底部物流进入闪蒸冷凝器8,减温减压塔9顶部出来的气相作为载气经载气加热器h6加热后去一次闪蒸塔4j进行闪蒸处理,wash-f-l物流为常温的新鲜气体丙烯(温度为40℃,压力为9bar,质量流量为4.83kg/hr),在这里补入丙烯,除了补充损耗,更主要是为了增加一次闪蒸罐4j中易挥发组份的浓度,使聚丙烯产品中残留的循环工质更少,一次闪蒸罐4j的操作压力约8bar,温度为180℃,经一次闪蒸罐4j的闪蒸操作后,一次闪蒸罐4j顶部物流进入闪蒸冷凝器8,一次闪蒸罐4j底部还含有少量循环工质,少量循环工质进入二次闪蒸罐4k进行低压闪蒸操作,二次闪蒸罐4k的内部压力为0.1mpaa,温度为150℃,绝大部分循环工质从二次闪蒸罐4k顶部离开,离开的循环工质的物流号为vent-c,其质量流量为10.83kg/hr,温度为150℃,压力为1bar,离开的循环工质为气相,这部分气体无法使用循环水或低温水液化,因此排入火炬,当然也可以使用一台小型压缩机,进行压缩后再进入循环,这台小压缩机能耗非常小。二次闪蒸罐4k底部的聚丙烯进入脱气罐4a,脱气罐4a的内部压力为0.1mpaa,温度为150℃,同时脱气罐4a中加入化学药剂环氧丙烷,环氧丙烷的物流号为reagents,温度为40℃,压力为3bar,质量流量为3kg/hr,在脱气罐4a下部引入循环惰性气体,循环惰性气体的物流号为n2-fresh,质量流量为20kg/h,循环惰性气体经过冷凝器后进入脱气罐4a内。本实施例因采用二次闪蒸技术,因此这里脱气仅使用新鲜氮气作为循环惰性气体进行脱气即可。洗涤后的聚丙烯从脱气罐4a的底部排出,排出的聚丙烯的物流号为pp-prod,且排出的聚丙烯的温度为148.77℃,压力为1bar,质量流量为1000.05kg/hr。
[0096]
本实施例采用了丙烯和正丁烯作为循环工质,从下表2、3可以看到,聚丙烯粉料含有92ppm左右的催化剂、助催化剂残留,经本工艺洗涤后,催化剂、助催化剂中的大部分的金属灰分已经被出去,剩余的金属杂质已小于15ppm。杂质中的氯也以氯丙醇的形式被洗涤脱除。本实施例中wash-f-h为正丁烯补充量,补入闪蒸冷凝器8前,增加了闪蒸汽体中正丁烯的含量,使得本实施例能够使用循环水进行冷却,如下表2所示闪蒸冷凝器8中71kw可采用循环水进行冷凝,能耗非常低;另外采用循环工质后,汽化器3a所需能耗仅为18kw,第一换热器节省了134kw的热量,热量回收率达88%,物料平衡表中vent-c物流为微正压的二次闪蒸气,无法简单冷凝液化,作为废气排放,当然也可以增加一台小型压缩机增压后液化,进行循环洗涤。
[0097]
表2主要换热器换热量一览表
[0098]
换热器名称第一加热器第一换热器汽化器第四加热器闪蒸冷凝器换热量/kw25.51341812271
[0099]
表3物料平衡表
[0100][0101][0102]
本技术以一种烃类为循环工质,使用液相循环工质对聚烯烃进行洗涤,通常情况下液相循环工质与聚烯烃进行逆流接触,以洗涤内部杂质,另外也可以采用其他方式加强液固接触,例如采用旋流设备或者搅拌。液相洗涤一般能洗去能溶解于循环工质的物质,例如部分低聚物,主要还是物理洗涤,例如洗涤靠范德华力附着于表面的金属成分,如ti等活性中心成分、催化剂载体部分,小部分未能洗涤的部分残留在洗涤后的聚烯烃产品里,可在
液相洗涤工序中加入化学试剂进行化学洗涤(也就是液相洗涤装置1上具有供化学试剂进入的接口),边反应边洗涤,反应原理如下所示:
[0103]
醇法:mcln+2nroh
→
m(oh)n+hcl+nror
[0104]
酯法:
[0105]
环氧法:mcln+nh2o+nro
→
m(oh)n+nr(oh)cl
[0106]
m=金属,r=烃基,x/z=ro或r’[0107]
由于醇法和环氧法能产生氯化氢气体,使得催化剂残渣更加稀松,促进洗涤效果,因此优选采用醇法或环氧法(环氧法中间产物为氯化氢)。液相洗涤温度越高则洗涤效果越好,温度越高,液体分子热运动越剧烈。
[0108]
洗涤后的洗涤液中混杂了一些高沸点杂质,因此只需要将洗涤液蒸发后即能将高沸点杂质除去,由于将全部洗涤液蒸发耗能非常大,因此有必要在蒸发前设置节能换热器(如各实施例中的第一换热器53)来回收热量,然后再进行蒸发分离操作。蒸发后的气相分为两个部分,第一部分气相经第一换热器53冷凝回收热量后,加压返回液相洗涤塔,完成一次循环;第二部分气相作为载气,去脱气装置4脱除聚烯烃中溶剂及其余杂质。尽管在分离罐中,盐类等高沸点物质几乎被脱除干净,但仍有少量的其余高沸点物质会被带入气相中去,另外由于循环工质一直处于循环洗涤中,因此也会残留少量化学反应产物,因此优选增加膜分离组件(如实施例一、二中的膜分离组件6),该膜为重组分或化学反应产物渗透因子大于循环工质渗透因子的一种烃膜,可选用橡胶态高分子膜,如有机硅氧烷类高分子膜等,该膜的高压侧为高压清洁气体,返回第一换热器53,低压侧为低压气体,里面含有大部分的重组分和化学反应产物。
[0109]
上述的第二部分气相为高温状态,进入脱气装置4作为载气进行一次脱气,去脱除聚烯烃中的循环工质和其余杂质,同时在脱气装置4中加入化学试剂,用于和其余难洗涤的杂质进行反应,进而脱除杂质,化学试剂的反应原理和前述液相洗涤加入的化学试剂的反应原理相同。脱气装置的压力优选为0.1~0.3mpaa,温度优选为100~200℃,在高温下化学反应产物也以气态的形式被载气带出,去进一步分离,分离设备即本技术中的杂质脱除塔优选为精馏塔,据所选择循环工质以及化学反应产物的沸点关系来确定精馏塔塔顶和塔底馏出物的组成,具体地,当循环工质沸点大于化学反应产物的沸点时,循环工质以液态的形式从精馏塔底部离开,当循环工质沸点小于化学反应产物的沸点时,循环工质以液态的形式从精馏塔顶部离开,液态的循环工质经增压后与前述第一换热器53冷凝下来的液态循环工质混合后,经第一增压泵54加压后去液相洗涤塔,完成总的工质循环。
[0110]
由于载气为循环工质,尽管节省了大量的惰性气体,但由于脱气平衡的限制,脱气后的聚烯烃仍有微量的循环工质,因此该聚烯烃需要使用惰性气体进行二次脱气,在二次脱气罐中,惰性气体从罐底部进入,聚烯烃从顶部加入,逆流接触,顶部的气体,如有需要则设置固体分离装置,例如旋风分离器、布袋除尘器、过滤器等,进入循环压缩机增压,为防止惰性气体中过高的循环工质浓度,需要设置一股小流量排放气。二次脱气塔塔底为聚烯烃产品。当然一次脱气操作和二次脱气操作可以在同一设备内进行,具体为循环工质载气从脱气罐中上部加入,化学试剂从脱气罐中部加入,惰性气体从脱气罐底部加入,脱气罐中设置防止气体返混的结构内件,循环工质载气和惰性气体从脱气罐顶部一起进入上述的精馏塔,精馏塔塔顶设置分凝器,精馏塔顶部液相和底部液相的组成与前述物质相同,顶部气相
为惰性气体,并返回循环压缩机增压,精馏塔塔顶分凝器的温度设置原则为:使得分凝后的气相中循环工质含量小于聚烯烃产品中循环工质含量所对应的气相平衡含量。
[0111]
上述循环工质在循环洗涤过程中,主要能耗为蒸发循环工质,以及压缩循环工质所消耗的能量,液相洗涤塔顶部的洗涤液需要全部汽化,这里能耗非常大,尽管设置了第一换热器,但由于纯物质其沸点和泡点一致,因此只能加热显热段,只能回收约30%左右的热量;另外在液相洗涤塔底部的聚烯烃中也含有大量的循环工质,这部分循环工质需要先减压加热闪蒸,除去大部分的循环工质,以节省能量,这就要求循环工质为易挥发性物质,即碳数较少的烃类,该部分循环工质减压后,以气相形式离开聚烯烃产品,由于冷凝温度低,无法冷凝成液相,因此需要设置压缩机进行增压后再冷凝,成为液相后再进入洗涤循环,这部分气体循环量很大,压缩机能耗也非常大,压缩机为动设备,整个洗涤装置安全性能也会下降,因此这里期望所述汽相为高沸点物质,即在低压情况下,仅使用循环水或者低温水就能使汽相能够冷凝成液相的物质,可以是碳数较多的烃类。为了使第一换热器最大限度回收热量、增加闪蒸气体量及减小压缩机能耗甚至取消压缩机,循环工质可以采用混合工质,这样可以使第一换热器回收90%左右的洗涤塔顶部的洗涤液蒸发热量,另外由于低沸点物质的存在,在闪蒸工段也能去除大部分的循环工质,而由于高沸点物质的存在,闪蒸汽体只需循环水或低温水既可以冷凝成液体,利用泵加压后循环洗涤。