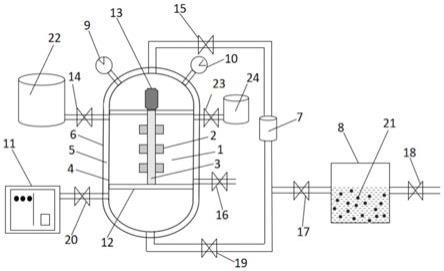
1.本发明涉及一种活性炭再生装置,特别涉及一种高压蒸汽联合酸洗超声与高级氧化活性炭再生方法及装置。
背景技术:2.活性炭是一种化学性质稳定、孔隙结构发达、比表面积巨大的无定型碳质材料。因其具有强大的吸附性能,活性炭在化工、环保、食品与制药、湿法冶金、催化剂载体、电机材料和军事化学防护等领域广泛应用。近年来我国活性炭使用量剧增,废活性炭由于得不到科学有效的回收利用,长期以来被当作危险废弃物进行处理与处置,既造成了炭资源的浪费又污染了环境。因此对废活性炭进行再生利用有利于节约资源、保护环境,极具实际意义和研究价值。再生是通过运用物理或化学等方法对失去活性的活性炭进行再生处理,去除吸附物,释放吸附位点,恢复其吸附性能达到循环利用目的。
3.目前活性炭再生的方法有很多,根据主要再生手段,将再生方法分为3大类:物理再生、化学再生、生物再生。物理再生法是指通过变温、变压或者溶剂萃取等手段打破吸附质与吸附剂之间的平或者分解大分子有机物成为小分子有机物后脱离,实现活性炭的再生。化学再生法是利用再生介质与吸附有机物的化学反应、化学降解等手段进行再生的方法,包括酸碱再生、电化学、氧化再生等。生物再生法是指在sac上进行微生物接种,通过微生物的降解作用再生。从再生时间、效率、再生后效能以及通用性分析,本发明选用高压蒸汽超声波再生法对活性炭进行再生处理。
4.中国专利cn102989435a公布了一种活性炭再生的方法,其特征在于主要包括往失活活性炭中添加酸混合均匀,将活性炭置于真空加热装置中加热再生。该方法采用真空条件会产生大量的能耗,经济效益低。
5.中国专利cn101590398b公开的超声波再生活性炭方法及其装置,采用的是物理再生法,描述的是经过水洗后的活性炭在水中进行超声处理,进行连续再生过程。中国专利cn102974138b公开的超声波在线再生活性炭过滤器及其活性炭再生方法,采用的是物理再生法,描述的是先对活性炭进行正洗和反洗,随后通入蒸汽对过滤器内的水进行加热,随后进行超声再生处理。这些方法不仅会对活性炭清洗不彻底,同时会有大量含有污染物的废水产生。
6.公开号为cn103846080a的中国发明专利公开了一种活性炭再生方法,该方法采用化学溶液再生和超声再生相结合的方法,避免了化学溶液再生不彻底的缺点。其主要步骤为:将需再生废活性炭与特定再生溶剂混合;进行超声处理;超声处理后进行固液分离,再生溶剂回收利用;将分离后的活性炭进行水洗、抽滤;将上述得到的活性炭自然晾干,完成再生过程。但该方法仅仅将污染物从活性炭内转移至溶剂内,并没有达到将污染物完全去除的目的;且再生后产生的溶剂中会含有大量污染物,易造成二次污染。
技术实现要素:7.本发明所要解决的问题是提供一种高效、炭损小、操作简单便捷、具有广泛应用前景的高压蒸汽联合酸洗超声与高级氧化活性炭再生方法及装置。
8.本发明提供的技术方案具体如下。
9.本发明提供一种高压蒸汽联合酸洗超声与高级氧化活性炭再生装置,其包括预处理罐、活性炭再生罐、高压蒸汽发生器、超声波发生器和废液高级氧化处理器;预处理罐经活性炭进口阀门和活性炭再生罐相连,活性炭再生罐上部设置酸洗液进口阀门,酸洗液进口阀门和酸洗液储存罐相连, 酸性清洗液经酸洗液进口阀门进入活性炭再生罐的罐体内,活性炭再生罐中部位置水平设置有两个固定滤板,超声波发生器设置在两个固定滤板之间,经过预处理罐预处理过的需再生的活性炭颗粒进入两个固定滤板之间的罐体内,活性炭再生罐上安装用于检测罐体内部压力的压力表和检测罐体内部温度的温度表,活性炭再生罐下部设置用于排出再生活性炭的活性炭卸口阀门;高压蒸汽发生器用于连续产生高温高压蒸汽,高压蒸汽发生器通过高压蒸汽进口阀门和活性炭再生罐相连,活性炭再生罐的顶部经蒸汽出气口阀门和蒸汽冷凝器相连,蒸汽冷凝器经处理液进口阀门和废液高级氧化处理器相连,活性炭再生罐的底部经废液排口阀门、处理液进口阀门和废液高级氧化处理器相连。
10.本发明中,预处理罐内,将需再生的活性炭和石墨按照质量比为40:1~20:1混合进行预处理。
11.本发明中,酸性清洗液的ph值在3~5之间。
12.本发明中,活性炭再生罐的罐体为双层结构,其内壁和外壁中间设置吸声保温材料填充物。
13.本发明中,超声波发生器设置在中央旋转轴承上,中央旋转轴承由电机驱动;超声波发生器为4-16个,超声频率可调为25-45khz,单个超声波发生器的功率为25-400w。
14.本发明中,高压蒸汽发生器产生的压力范围为5~13mpa。
15.本发明中,废液高级氧化处理器中设置零价铁/膨胀石墨材料。
16.本发明还提供一种基于上述的装置的高级氧化活性炭再生方法,其按以下步骤进行:(一)、首先将需再生活性炭和石墨在活性炭预处理罐中充分混合进行预处理,再利用活性炭预处理罐内水压和重力作用,使需再生活性炭经由活性炭进口阀门进入活性炭再生罐中;(二)、关闭活性炭进口阀门,打开酸洗液进口阀门,通过酸洗液进口阀门将酸洗液存储罐中的酸性清洗液注入活性炭再生罐,对需再生的活性炭进行酸洗,酸洗完成后打开废液排口阀门和处理液进口阀门将污水排放至废液高级氧化处理;(三)、酸洗结束后,关闭活性炭进口阀门、活性炭卸口阀门、废液排口阀门和酸洗液进口阀门,打开高压蒸汽发生器产生高压蒸汽,打开高压蒸汽进口阀门,使蒸汽进入活性炭再生罐,打开超声波发生器,蒸汽对废活性炭进行加热,同时利用超声高压脱附污染物,污染物在超声波及高温高压的条件下与活性炭上的水蒸汽发生空化作用,石墨的存在加速电子的转移,实现对污染物的降解和脱附;(四)、持续通入蒸汽,当压力表超过一定压力,高压蒸汽发生器自动停止蒸汽供
应,同时蒸汽出气口阀门打开进行泄压,待罐体压力表显示压力低于最小值时,关闭蒸汽出气口阀门同时自动打开高压蒸汽发生器,泄压的蒸汽经过蒸汽冷凝器冷凝,进入废液高级氧化处理器,活性炭再生结束后,打开废液排口阀门和处理液进口阀门,将过程中产生的废液排入废液高级氧化处理器,使得废液中的污染物发生高级氧化反应被去除,从而实现活性炭清洁再生过程,污染物被降解后的废水最终实现达标排放。
17.本发明中,步骤(一)中,预处理罐(22)内,将需再生的活性炭和石墨按照质量比为40:1~20:1混合进行预处理。
18.本发明中,步骤(二)中,酸性清洗液的ph值在3-5之间,废液高级氧化处理器中设置零价铁/膨胀石墨催化剂材料。
19.和现有技术相比,本发明的有益效果在于:(1)本发明通过对活性炭依次进行预处理、酸洗、超声条件下高温高压处理,能够实现活性炭的高效再生,活性炭再生率能够达到90%以上;(2)本发明处理后的废液以及从活性炭中脱除的有机污染物经高级氧化反应被去除,从而实现活性炭清洁再生过程,污染物被降解后的废水最终实现达标排放,绿色环保;(3)本发明通过高压蒸汽联合酸洗超声与高级氧化活性炭再生装置再生活性炭,在活性炭再生过程中,该方法再生能耗低,可节约大量水资源,且降低了污染物产生二次污染的风险,具有很好的经济效益。
附图说明
20.图1是本发明高压蒸汽联合酸洗超声与高级氧化活性炭再生装置的结构示意图。
21.图2是实施例2中再生前后活性炭xrd图谱。
22.图3是实施例2中处理前废活性炭的sem图。
23.图4是实施例2中再生处理后活性炭的sem图。
24.图5是实施例2中再生处理后活性炭对亚甲基蓝的吸附值。
25.图6是实施例2中再生处理后活性炭对甲苯气体的穿透吸附曲线。
26.图中标号:1-活性炭再生罐、2-超声波发生器、3-中央旋转轴承、4-再生罐体内壁、5-吸声保温材料填充物、6-再生罐体外壁、7-蒸汽冷凝器、8-废液高级氧化处理器、9-压力表、10-温度表、11-高压蒸汽发生器、12-固定滤板、13-电机、14-活性炭进口阀门、15-蒸汽出气口阀门、16-活性炭卸口阀门、17-处理液进口阀门、18-处理液排口阀门、19-废液排口阀门、20-高压蒸汽进口阀门、21-零价铁/膨胀石墨催化剂材料、22-预处理罐、23-酸洗液进口阀门、24-酸洗液储存罐。
具体实施方式
27.下面通过具体实施方式的详细描述来进一步阐明本发明,但并不是对本发明的限制,仅仅作示例说明。
28.实施例1本发明高压蒸汽联合酸洗超声与高级氧化活性炭再生装置主要由三个部分组成,即由高压蒸汽发生器11、活性炭再生罐1、废液高级氧化处理器装置组成。
29.第一部分是高压蒸汽发生器11,该发生器可以根据活性炭再生罐1内的压力智能
控制设备停起。
30.第二部分为活性炭再生罐1,该活性炭再生罐1的罐体内层材料由玻璃钢制作而成,具有防腐蚀、耐酸碱等功能。该活性炭再生罐体外层材料由高强度不锈钢板制作,内层与外层之间的距离为8-12cm,中间为吸声保温材料填充物,一般为聚氨酯泡沫类物质,消除设备产生的声污染,同时减少热量损失,减少蒸汽冷凝。
31.第三部分为废液高级氧化处理器8,该处理器采用自制零价铁/膨胀石墨作为催化剂,具有高效降解水中有机污染物的性能。
32.具体的,高压蒸汽联合酸洗超声与高级氧化活性炭再生装置,其包括预处理罐22、高压蒸汽发生器11、超声波发生器2、活性炭再生罐1、废液高级氧化处理器8;预处理罐22的预处理过程为采用质量比为40:1~20:1的活性炭与石墨混合,高压蒸汽发生器11可连续产生高温高压蒸汽,高压蒸汽发生器11产生的压力范围为5~13mpa,活性炭再生罐11分为再生罐体内壁4、再生罐体外壁6,中间为吸声保温材料填充物5,活性炭再生罐内壁4的材料由玻璃钢(6~8mm厚度)制作而成,具有防腐蚀、耐酸碱等功能,再生罐体外壁6由高强度不锈钢板制作,活性炭再生罐1中间为中央旋转轴承3和电机13,中央旋转轴承3上固定若干对应排列的超声频率可调的超声波发生器2,超声波发生器2为4-16个,超声频率可调为25-45khz,单个超声波发生器的功率为25-400w,活性炭再生罐1中部设置有固定滤板12,固定滤板12之间的罐体内可放置需再生的活性炭颗粒。活性炭再生罐1下段设置有罐体冷凝液回收口阀门19。活性炭再生罐体11上段罐体设置有压力表9、温度表10、蒸汽出气口阀门15、酸洗液进口阀门23与酸洗液存储罐24相连,压力表和温度表的检测端传感器位于活性炭再生罐1中部位置,酸洗液存储罐24用于存储酸性清洗液,且酸性清洗液ph=3~5。高压蒸汽发生器11在压力表9达到临界压力时自动关闭。同时打开蒸汽出气口阀门15进行泄压。待罐体压力表9显示压力低于最小值时,关闭蒸汽出气口阀门15同时自动打开高压蒸汽发生器11。活性炭再生罐1中段设置有活性炭进口阀门14、活性炭卸口阀门16。废液高级氧化处理器8内有自制零价铁/膨胀石墨催化剂材料21、连接有处理液进口阀门17、处理液排口阀门18。自制零价铁/膨胀石墨催化剂材料的制备方法参考:comparison of the behavior of zvi/carbon composites from both commercial origin and from spent li-ion batteries and mill scale for the removal of ibuprofen in water, journal of environmental management, shuaichen,zixiangli,etc.vol. 264, 15 june 2020, 110480。
33.本发明基于上述装置进行活性炭再生方法的具体过程是:首先将需要再生处理的吸附饱和的活性炭至于预处理罐中,按照活性炭与石墨比例(40:1~20:1)进行充分混合,石墨的存在可加速物质之间电子的转移,在污染物的降解过程中可起到一定的促进作用。进行预处理操作后,利用活性炭预处理罐22内水压和重力作用,使需再生活性炭经由活性炭进口阀门14进入活性炭再生罐1,打开酸洗液进口阀门23,向活性炭再生罐1中注入酸性清洗液,酸洗主要是为了去除活性炭中重金属等杂质,同时为后续污染物降解过程提供相应的酸性条件。酸洗完成后,打开废液排口阀门19将污水排至废液高级氧化处理器8,开启高压蒸汽发生器11,使高温高压蒸汽(温度在100℃-150℃的饱和蒸汽)进入活性炭再生罐1,同时打开超声波发生器2,饱和吸附的活性炭在超声波和高温高压蒸汽的作用下,开始发生脱附和分解。高温高压蒸汽可以使活性炭吸附的污染物由于
压强的作用破坏了活性炭对污染物的吸附平衡,此时发生脱附解析作用,同时利用超声波的空化作用加速污染物分解脱附的过程,石墨的存在加速电子的转移,可以实现一定程度的污染物的降解作用。活性炭再生罐1需维持一定的压力,当罐内蒸汽压超过一定压力时,自动关闭高压蒸汽发生器11,同时打开蒸汽出气口阀门15,进行泄压操作,多余的蒸汽进入蒸汽冷凝器7进行冷凝。经过1~2h活性炭再生完成,将活性炭再生罐1内冷凝液和蒸汽冷凝器7中冷凝液通入废液高级氧化处理器8中与酸洗液混合,与自制的零价铁/膨胀石墨材料21发生高级氧化反应,在酸性条件下会与有机物污染物发生高级氧化反应,从而实现对有机污染物的降解。最终活性炭再生过程中产生的废液经过处理后达标排放。
34.实施例2在实际工业有机废气处理过程中,通常采用吸附法进行处理,过程中会产生大量的吸附饱和的活性炭。为便于研究,在实验室条件下,利用甲苯废气代替挥发性有机物废气进行实验,获得吸附饱和的活性炭。根据实施例1将吸附饱和的活性炭至于活性炭再生罐中,进行活性炭再生实验。对再生后的活性炭进行再生能效分析,同时吸附甲苯和亚甲基蓝实验。实验结果如下:通过再生前后活性炭xrd图谱(图2)对比分析,发现废活性炭吸附的污染物经过再生过程可实现一定程度的脱附。通过sem图像分析,由废活性炭(图3)表面存在大量杂质,活性炭孔隙被堵塞,再生后的活性炭(图4),表面粗糙且疏松,出现明显孔隙结构,孔的大小和数量明显大且多于废活性炭的数量,经过再生废活性炭微孔结构有明显的提高。
35.对再生后的活性炭进行再生能效分析,同时进行吸附亚甲基蓝废水的实验。由活性炭对亚甲基蓝的吸附值(图5)可知,经过高压蒸汽超声再生后的活性炭,与废活性炭相比,再生后的活性炭对亚甲基蓝吸附效率明显提升,再生率可达90.3%。由再生前后活性炭对甲苯气体的穿透吸附曲线(图6)可知,废活性炭对污染物甲苯气体几乎无吸附去除能力,经过再生后的活性炭对污染物甲苯的穿透时间比废活性炭明显增加,再生后的活性炭对污染物甲苯气体的吸附能力得到极大的恢复。经过实验表明再生后的活性炭对废气和废水中污染物都具有很好的去除性能。