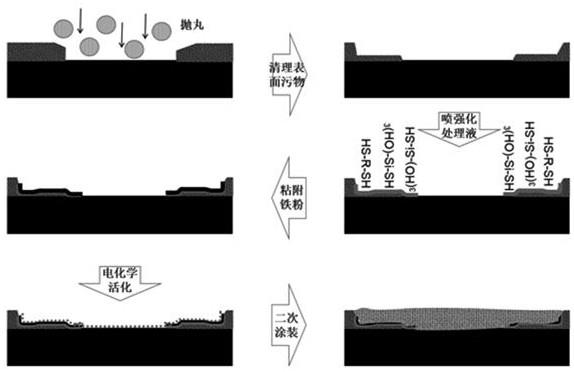
1.本发明涉及一种涂装方法,具体涉及一种针对存在涂装缺陷钢板的二次涂装方法,属于钢结构工程技术领域。
背景技术:2.与其他结构形式相比,钢结构工程具有抗震性能良好、施工周期较短、工业化程度高、污染少、自重轻等方面的优越性,使其在高层、大跨结构等领域中得到了广泛应用。环顾世界,美国、英国以及新加坡等国家的钢结构发展尤为繁荣。近年来,在国家布局新型基础设施的大背景下,我国的钢结构工程也如雨后春笋般出现,诸多代表性钢结构工程象征着我国钢结构理论与设计日趋完善。不仅如此,随着时代的进步和社会的发展,钢结构在现代桥梁建设中也被广泛采用,这极大地促进了我国桥梁设计水平的不断进步。
3.在钢结构工程施工过程中,在钢板表面涂覆多层具有防腐性能的涂料从而形成具有良好保护性能的漆膜是目前钢结构制造领域最为常用的防腐手段。环氧富锌涂料由于对钢铁具有优异的电化学保护作用,往往作为钢结构防腐涂层的底漆。但是涂料成膜后,漆膜夹砂、流挂、针孔、缩孔、起泡、脱皮以及开裂等偶发缺陷会由于操作条件与技术方案等因素不可避免的发生。尤其是由于前处理工艺不当以及环氧富锌底漆与钢板的匹配性不佳等原因,会导致漆膜附着力不良等问题,产生严重的大面积起泡和脱皮现象。此种情况下,往往需要尽快对出现涂装缺陷的部位进行处理,清除缺陷涂层后采用二次涂装的方式及时修复原涂层的缺陷,保证钢结构的整体质量。
4.目前,制造过程中发现涂装缺陷后,一般简单的去除原漆膜后采用和原涂装工艺相同的方式喷涂环氧富锌底漆、中漆以及面漆。然而,去除原漆膜后的钢板一般表面能较低,与二次涂装环氧富锌底漆结合力相比原漆膜往往更差,且新-旧漆膜之间也无法有效结合,所以采用和原涂装工艺相同的方式通常得不到良好的防腐效果。因此,开发出可以有效提高二次涂装后涂层附着力以及耐蚀性的方法对于钢结构制造领域意义重大。
技术实现要素:5.本发明目的是提供了一种针对存在涂装缺陷钢板的二次涂装方法,可以有效提高二次涂装漆膜附着力及耐蚀性。
6.本发明为实现上述目的,通过以下技术方案实现:一种针对存在涂装缺陷钢板的二次涂装方法,包括以下步骤:(1) 原涂层边缘前处理;(2) 配制强化处理液:强化处理液包含以下原料:双巯基化合物、磺基水杨酸、2,2-联吡啶、羧甲基壳聚糖、乙醇、γ―巯丙基三乙氧基硅烷和去离子水;(3) 原涂层边缘强化处理:将通过步骤(2)强化处理液喷在步骤(1)处理之后的原涂层边缘以及衔接处的钢板表面;(4) 电化学活化:以须要进行二次涂装的钢板以及经过步骤(3)处理后的原涂层
边缘为电解池的一极,以惰性电极为另一极,进行电化学活化;(5) 二次涂装:将经过活化的部位重新依次喷涂环氧富锌底漆、中漆以及面漆,完成二次涂装。
7.所述针对存在涂装缺陷钢板的二次涂装方法优选方案,强化处理液配制具体步骤如下:称取2.0~20.0 g双巯基化合物、5.0~20.0 g磺基水杨酸、0.1~3.0 g 2,2-联吡啶、0.5~2.0 g的羧甲基壳聚糖,依次加入到900 ml乙醇中并搅拌均匀,加入70 ml γ―巯丙基三乙氧基硅烷并搅拌均匀,然后在1.0 h内通过滴加的方式加入30 ml去离子水,继续搅拌0.5 h后,完成强化处理液的配制。
8.所述针对存在涂装缺陷钢板的二次涂装方法优选方案,双巯基化合物为双巯基聚乙二醇、双巯基乙酸乙二醇酯、间二苄硫醇、1,2-苯二硫醇、1,3-苯二硫醇、1,4-苯二硫醇中一种或者其中两种的组合。
9.所述针对存在涂装缺陷钢板的二次涂装方法优选方案,原涂层边缘强化处理具体步骤如下:采用喷枪将通过步骤(2)新配制的强化处理液喷在步骤(1)处理之后的原涂层边缘以及衔接处的钢板表面,5~120 s后将粒径为3000~800目的还原铁粉通过气流喷在涂有强化处理液的部位,使其密集粘附在原涂层边缘,10~600 s后采用去离子水把残余还原铁粉冲洗干净。
10.所述针对存在涂装缺陷钢板的二次涂装方法优选方案,电化学活化具体处理步骤如下:以须要进行二次涂装的钢板以及经过步骤(3)处理后的原涂层边缘为电解池的一极,以面积为1平方分米的惰性电极为另一极进行电化学活化,两电极之间以浸润了15~35 ℃的电化学活化液的海绵隔开,通过电流振幅为5.0~10.0 a、频率为60 hz的正弦波交流电,控制所有需要活化的部位活化时间为0.5~10分钟,完成后采用无水乙醇清洗干净并冷风吹干,完成电化学活化;其中所述的电化学活化液按如下步骤配制:分别称取5.0~30.0 g的柠檬酸、3.0~30.0 g的磺基水杨酸和2.0~6.0 g的羧甲基壳聚糖,依次溶解在1 l去离子水中并搅拌均匀,加热至50~95 ℃后加入1.0~2.0 g的邻二氮菲并搅拌均匀,然后依次加入0.5~2.0 g的盐酸羟胺以及1.0~8.0 g的硫酸亚铁铵并搅拌均匀,调整ph为3.0~5.0。
11.所述针对存在涂装缺陷钢板的二次涂装方法优选方案,当海绵中的电化学活化液通过的电量超过0.3 a
·
h时,需要将海绵中的电化学活化液挤出,并重新浸润新的电化学活化液。
12.所述针对存在涂装缺陷钢板的二次涂装方法优选方案,步骤(4)中惰性电极为不锈钢电极、石墨电极、钛电极中的一种。
13.本发明的优点在于:针对存在涂装缺陷钢板的二次涂装方法通过步骤(1),使原漆膜的环氧富锌底漆暴露,从而通过后续的步骤(3)和步骤(4)可以使原漆膜边缘的环氧富锌底漆与衔接处钢板一体化,提高二次涂装漆膜与钢板及原漆膜的兼容性,不仅可以解决目前钢结构制造领域在发现钢板涂装缺陷进行二次涂装后漆膜的附着力明显退化的问题,而且还能大幅提升耐蚀性能。
附图说明
14.附图用来提供对本发明的进一步理解,并且构成说明书的一部分,与本发明的实
施例一起用于解释本发明,并不构成对本发明的限制。
15.图1为针对存在涂装缺陷钢板的二次涂装过程示意图;图2为试验一经过二次涂装后,所得漆膜在进行完240 h中性盐雾试验之后在3.5% nacl溶液中测得的塔菲尔曲线。
具体实施方式
16.下面将结合本发明实施例中的附图,对本发明实施例中的技术方案进行清楚、完整地描述,显然,所描述的实施例仅仅是本发明一部分实施例,而不是全部的实施例。基于本发明中的实施例,本领域普通技术人员在没有做出创造性劳动前提下所获得的所有其他实施例,都属于本发明保护的范围。
17.一种针对存在涂装缺陷钢板的二次涂装方法,按以下步骤进行:(1) 原涂层边缘前处理:采用抛丸的方式将原漆膜边缘的面漆及中漆打磨掉,暴露出新鲜的原漆膜的环氧富锌底漆,采用吸尘装置将表面残余的颗粒、污浊、灰尘等清除干净;(2) 配制强化处理液:称取2.0~20.0 g双巯基化合物、5.0~20.0 g磺基水杨酸、0.1~3.0 g 2,2-联吡啶、0.5~2.0 g的羧甲基壳聚糖,依次加入到900 ml乙醇中并搅拌均匀,加入70 ml γ―巯丙基三乙氧基硅烷并搅拌均匀,然后在1.0 h内通过滴加的方式加入30 ml去离子水,继续搅拌0.5 h后,完成强化处理液的配制;其中所述的双巯基化合物为双巯基聚乙二醇、双巯基乙酸乙二醇酯、间二苄硫醇、1,2-苯二硫醇、1,3-苯二硫醇、1,4-苯二硫醇中一种或者其中两种的组合;(3) 原涂层边缘强化处理:采用喷枪将通过步骤(2)新配制的强化处理液喷在步骤(1)处理之后的原涂层边缘以及衔接处的钢板表面,5~120 s后将粒径为3000~800目的还原铁粉通过气流喷在涂有强化处理液的部位,使其密集粘附在原涂层边缘,10~600 s后采用去离子水把残余还原铁粉冲洗干净;(4) 电化学活化:以须要进行二次涂装的钢板以及经过步骤(3)处理后的原涂层边缘为电解池的一极,以面积为1平方分米的惰性电极为另一极进行电化学活化,两电极之间以浸润了15~35 ℃的电化学活化液的海绵隔开,通过电流振幅为5.0~10.0 a、频率为60 hz的正弦波交流电,控制所有需要活化的部位活化时间为0.5~10分钟,完成后采用无水乙醇清洗干净并冷风吹干,完成电化学活化;其中所述的电化学活化液按如下步骤配制:分别称取5.0~30.0 g的柠檬酸、3.0~30.0 g的磺基水杨酸和2.0~6.0 g的羧甲基壳聚糖,依次溶解在1 l去离子水中并搅拌均匀,加热至50~95 ℃后加入1.0~2.0 g的邻二氮菲并搅拌均匀,然后依次加入0.5~2.0 g的盐酸羟胺以及1.0~8.0 g的硫酸亚铁铵并搅拌均匀,调整ph为3.0~5.0;(5) 二次涂装:将经过活化的部位重新依次喷涂环氧富锌底漆、中漆以及面漆,完成二次涂装。
18.本实施例中,步骤(4)中所述的惰性电极为不锈钢电极、石墨电极、钛电极中的一种。
19.本实施例中,步骤(4)中所述的浸润了电化学活化液的海绵,当海绵中的电化学活化液通过的电量超过0.3 a
·
h时,需要将海绵中的电化学活化液挤出,并重新浸润新的电
化学活化液。
20.本实施方式的一种针对存在涂装缺陷钢板的二次涂装方法,步骤(2)配制的强化处理液中的磺基水杨酸可以络合锌离子、亚铁离子和铁离子,2,2-联吡啶可以络合亚铁离子。强化处理液中的羧甲基壳聚糖既是金属离子络合剂,又可以起到增稠的效果,使强化处理液可以很好的覆盖需要处理的部位。强化处理液中的双巯基化合物可以依靠两个巯基偶联两种金属。在步骤(2)强化处理液的配制过程中,γ―巯丙基三乙氧基硅烷在缓慢加入去离子水之后可以解离为γ―巯丙基硅醇,从而利用巯基和三羟基偶联金属/金属或者环氧树脂/金属。
21.通过步骤(1),使原漆膜的环氧富锌底漆暴露,当步骤(3)将新配制的强化处理液喷在步骤(1)处理之后的原涂层边缘及衔接处钢板表面后,强化处理液中的磺基水杨酸、2,2-联吡啶和羧甲基壳聚糖使原漆膜环氧富锌底漆中锌的氧化膜以及衔接处钢板表面的氧化膜活性溶解,暴露出新鲜的金属。锌和铁与强化处理液中的双巯基化合物利用巯基形成高强度的化学键,使双巯基化合物吸附在经过喷涂过强化处理液之后的表面;γ―巯丙基硅醇可以凭借巯基与环氧富锌底漆中的锌、环氧树脂以及衔接处的钢板表面紧密结合,还可以凭借三羟基与环氧富锌底漆中的锌以及衔接处的钢板表面紧密结合。当通过气流将还原铁粉喷在涂有强化处理液的部位时,还原铁粉会与吸附的双巯基化合物以及γ―巯丙基硅醇上的巯基和羟基键合,从而被牢牢固定在原涂层富锌底漆及衔接处钢板表面。在步骤(4)中,当钢板以及粘附的还原铁粉表面通过阳极电流时,电化学活化液中的柠檬酸、磺基水杨酸以及邻二氮菲作为亚铁离子和铁离子的强络合剂可以将钢铁氧化膜去除,铁在亚铁离子强络合剂的作用下,加速阳极氧化并使新鲜的铁裸露,有利于与底漆形成环氧树脂-铁的化学键从而提升漆膜附着力,且晶界处会先发生刻蚀,从而使钢铁表面粗糙度增加,能够增加后续漆膜的机械附着力;当裸露的钢板以及粘附的还原铁粉表面通过阴极电流时,电化学活化液中的亚铁离子会发生还原形成金属铁,弥补氧化过程中钢铁的过腐蚀。总体来讲,在交流电的作用下会不断的发生铁的刻蚀和沉积,使钢铁表面维持活性状态;阳极刻蚀的电流效率高于阴极沉积的电流效率,因此可以增加表面粗糙度,从而通过高强度化学键合以及机械铆合提升后续环氧富锌底漆的附着力。
22.用以下试验验证本发明的有益效果:试验一:将缺陷处原缺陷漆膜去除后,本试验的一种针对存在涂装缺陷钢板的二次涂装方法按以下步骤进行:(1) 原涂层边缘前处理:采用抛丸的方式将原漆膜边缘的面漆及中漆打磨掉,暴露出新鲜的原漆膜的环氧富锌底漆,采用吸尘装置将表面残余的颗粒、污浊、灰尘等清除干净;(2) 配制强化处理液:称取2.0 g双巯基聚乙二醇、20.0 g磺基水杨酸、0.1 g 2,2-联吡啶、0.5 g的羧甲基壳聚糖,依次加入到900 ml乙醇中并搅拌均匀,加入70 ml γ―巯丙基三乙氧基硅烷并搅拌均匀,然后在1.0 h内通过滴加的方式加入30 ml去离子水,继续搅拌0.5 h后,完成强化处理液的配制;(3) 原涂层边缘强化处理:采用喷枪将通过步骤(2)新配制的强化处理液喷在步骤(1)处理之后的原涂层边缘以及衔接处的钢板表面,120 s后将粒径为3000目的还原铁粉通过气流喷在涂有强化处理液的部位,使其密集粘附在原涂层边缘,10 s后采用去离子水
把残余还原铁粉冲洗干净;(4) 电化学活化:以须要进行二次涂装的钢板以及经过步骤(3)处理后的原涂层边缘为电解池的一极,以面积为1平方分米的不锈钢电极为另一极进行电化学活化,两电极之间以浸润了15 ℃的电化学活化液的海绵隔开,通过电流振幅为5.0 a、频率为60 hz的正弦波交流电,当海绵中的电化学活化液通过的电量超过0.3 a
·
h时,需要将海绵中的电化学活化液挤出,并重新浸润新的电化学活化液;控制所有需要活化的部位活化时间为10分钟,完成后采用无水乙醇清洗干净并冷风吹干,完成电化学活化;其中所述的电化学活化液按如下步骤配制:分别称取30.0 g的柠檬酸、3.0 g的磺基水杨酸和6.0 g的羧甲基壳聚糖,依次溶解在1 l去离子水中并搅拌均匀,加热至50 ℃后加入1.0 g的邻二氮菲并搅拌均匀,然后依次加入0.5 g的盐酸羟胺以及1.0 g的硫酸亚铁铵并搅拌均匀,调整ph为5.0;(5) 二次涂装:将经过活化的部位重新依次喷涂环氧富锌底漆、中漆以及面漆,完成二次涂装。
23.试验二:将缺陷处原缺陷漆膜去除后,本试验的一种针对存在涂装缺陷钢板的二次涂装方法按以下步骤进行:(1) 原涂层边缘前处理:采用抛丸的方式将原漆膜边缘的面漆及中漆打磨掉,暴露出新鲜的原漆膜的环氧富锌底漆,采用吸尘装置将表面残余的颗粒、污浊、灰尘等清除干净;(2) 配制强化处理液:称取5.0 g双巯基乙酸乙二醇酯、5.0 g 1,2-苯二硫醇、10.0 g磺基水杨酸、1.5 g 2,2-联吡啶、1.5 g的羧甲基壳聚糖,依次加入到900 ml乙醇中并搅拌均匀,加入70 ml γ―巯丙基三乙氧基硅烷并搅拌均匀,然后在1.0 h内通过滴加的方式加入30 ml去离子水,继续搅拌0.5 h后,完成强化处理液的配制;(3) 原涂层边缘强化处理:采用喷枪将通过步骤(2)新配制的强化处理液喷在步骤(1)处理之后的原涂层边缘以及衔接处的钢板表面,60 s后将粒径为1600目的还原铁粉通过气流喷在涂有强化处理液的部位,使其密集粘附在原涂层边缘,120 s后采用去离子水把残余还原铁粉冲洗干净;(4) 电化学活化:以须要进行二次涂装的钢板以及经过步骤(3)处理后的原涂层边缘为电解池的一极,以面积为1平方分米的不锈钢电极为另一极进行电化学活化,两电极之间以浸润了25 ℃的电化学活化液的海绵隔开,通过电流振幅为7.0 a、频率为60 hz的正弦波交流电,当海绵中的电化学活化液通过的电量超过0.3 a
·
h时,需要将海绵中的电化学活化液挤出,并重新浸润新的电化学活化液;控制所有需要活化的部位活化时间为5分钟,完成后采用无水乙醇清洗干净并冷风吹干,完成电化学活化;其中所述的电化学活化液按如下步骤配制:分别称取16.0 g的柠檬酸、21.0 g的磺基水杨酸和3.0 g的羧甲基壳聚糖,依次溶解在1 l去离子水中并搅拌均匀,加热至80 ℃后加入1.3 g的邻二氮菲并搅拌均匀,然后依次加入1.0 g的盐酸羟胺以及6.0 g的硫酸亚铁铵并搅拌均匀,调整ph为3.5;(5) 二次涂装:将经过活化的部位重新依次喷涂环氧富锌底漆、中漆以及面漆,完成二次涂装。
24.试验三:将缺陷处原缺陷漆膜去除后,本试验的一种针对存在涂装缺陷钢板的二次涂装方法按以下步骤进行:(1) 原涂层边缘前处理:采用抛丸的方式将原漆膜边缘的面漆及中漆打磨掉,暴
露出新鲜的原漆膜的环氧富锌底漆,采用吸尘装置将表面残余的颗粒、污浊、灰尘等清除干净;(2) 配制强化处理液:称取10.0 g双巯基乙酸乙二醇酯、10.0 g间二苄硫醇、5.0 g磺基水杨酸、3.0 g 2,2-联吡啶、2.0 g的羧甲基壳聚糖,依次加入到900 ml乙醇中并搅拌均匀,加入70 ml γ―巯丙基三乙氧基硅烷并搅拌均匀,然后在1.0 h内通过滴加的方式加入30 ml去离子水,继续搅拌0.5 h后,完成强化处理液的配制;(3) 原涂层边缘强化处理:采用喷枪将通过步骤(2)新配制的强化处理液喷在步骤(1)处理之后的原涂层边缘以及衔接处的钢板表面,5 s后将粒径为800目的还原铁粉通过气流喷在涂有强化处理液的部位,使其密集粘附在原涂层边缘,600 s后采用去离子水把残余还原铁粉冲洗干净;(4) 电化学活化:以须要进行二次涂装的钢板以及经过步骤(3)处理后的原涂层边缘为电解池的一极,以面积为1平方分米的不锈钢电极为另一极进行电化学活化,两电极之间以浸润了35 ℃的电化学活化液的海绵隔开,通过电流振幅为10.0 a、频率为60 hz的正弦波交流电,当海绵中的电化学活化液通过的电量超过0.3 a
·
h时,需要将海绵中的电化学活化液挤出,并重新浸润新的电化学活化液;控制所有需要活化的部位活化时间为0.5分钟,完成后采用无水乙醇清洗干净并冷风吹干,完成电化学活化;其中所述的电化学活化液按如下步骤配制:分别称取5.0 g的柠檬酸、30.0 g的磺基水杨酸和2.0 g的羧甲基壳聚糖,依次溶解在1 l去离子水中并搅拌均匀,加热至95 ℃后加入2.0 g的邻二氮菲并搅拌均匀,然后依次加入2.0 g的盐酸羟胺以及8.0 g的硫酸亚铁铵并搅拌均匀,调整ph为3.0;(5) 二次涂装:将经过活化的部位重新依次喷涂环氧富锌底漆、中漆以及面漆,完成二次涂装。
25.试验四:将缺陷处原缺陷漆膜去除后,本试验的一种针对存在涂装缺陷钢板的二次涂装方法按以下步骤进行:(1) 原涂层边缘前处理:采用抛丸的方式将原漆膜边缘的面漆及中漆打磨掉,暴露出新鲜的原漆膜的环氧富锌底漆,采用吸尘装置将表面残余的颗粒、污浊、灰尘等清除干净;(2) 配制强化处理液:称取3.0 g双巯基乙酸乙二醇酯、3.0 g间二苄硫醇、8.0 g磺基水杨酸、2.0 g 2,2-联吡啶、0.8 g的羧甲基壳聚糖,依次加入到900 ml乙醇中并搅拌均匀,加入70 ml γ―巯丙基三乙氧基硅烷并搅拌均匀,然后在1.0 h内通过滴加的方式加入30 ml去离子水,继续搅拌0.5 h后,完成强化处理液的配制;(3) 原涂层边缘强化处理:采用喷枪将通过步骤(2)新配制的强化处理液喷在步骤(1)处理之后的原涂层边缘以及衔接处的钢板表面,90 s后将粒径为3000目的还原铁粉通过气流喷在涂有强化处理液的部位,使其密集粘附在原涂层边缘,300 s后采用去离子水把残余还原铁粉冲洗干净;(4) 电化学活化:以须要进行二次涂装的钢板以及经过步骤(3)处理后的原涂层边缘为电解池的一极,以面积为1平方分米的不锈钢电极为另一极进行电化学活化,两电极之间以浸润了30 ℃的电化学活化液的海绵隔开,通过电流振幅为7.5 a、频率为60 hz的正弦波交流电,当海绵中的电化学活化液通过的电量超过0.3 a
·
h时,需要将海绵中的电化学活化液挤出,并重新浸润新的电化学活化液;控制所有需要活化的部位活化时间为6分
钟,完成后采用无水乙醇清洗干净并冷风吹干,完成电化学活化;其中所述的电化学活化液按如下步骤配制:分别称取12.0 g的柠檬酸、16.0 g的磺基水杨酸和3.5 g的羧甲基壳聚糖,依次溶解在1 l去离子水中并搅拌均匀,加热至75 ℃后加入1.6 g的邻二氮菲并搅拌均匀,然后依次加入1.6 g的盐酸羟胺以及5.0 g的硫酸亚铁铵并搅拌均匀,调整ph为4.5;(5) 二次涂装:将经过活化的部位重新依次喷涂环氧富锌底漆、中漆以及面漆,完成二次涂装。
26.试验一至试验四针对存在涂装缺陷钢板的二次涂装过程示意图如图1所示。对试验一至试验四得到的二次涂装涂层进行划格法测定涂层附着力,切刀间隙3 mm,采用3m胶带粘贴划出的百格区域,迅速拉开后观察涂层脱落情况,未按照本试验进行处理的再生涂层(对照试验)同样采用划格法测定涂层附着力,涂层附着力结果见表1。
27.表1 涂层附着力测试结果 试验一试验二试验三试验四对照漆膜表面状态切割边缘完全平滑,无一格脱落切割边缘完全平滑,无一格脱落切割边缘完全平滑,无一格脱落切割边缘完全平滑,无一格脱落划线边缘涂层脱落比较严重,且有13格出现涂层脱落。iso等级0级0级0级0级2级
按照试验一得到的二次涂装涂层,在进行完240 h中性盐雾试验之后在3.5% nacl溶液中测得的塔菲尔曲线如图2所示,腐蚀电流仅为5.22
×
10-11 a
·
cm-2
,表明涂层耐蚀性依然非常好,可以继续对钢板形成保护。对盐雾试验后的涂层进行划格法测定涂层附着力,结果为iso等级1级,说明即使涂层经过盐雾腐蚀后,依然具有较好附着力。
28.最后应说明的是:以上所述仅为本发明的优选实施例而已,并不用于限制本发明,尽管参照前述实施例对本发明进行了详细的说明,对于本领域的技术人员来说,其依然可以对前述各实施例所记载的技术方案进行修改,或者对其中部分技术特征进行等同替换。凡在本发明的精神和原则之内,所作的任何修改、等同替换、改进等,均应包含在本发明的保护范围之内。