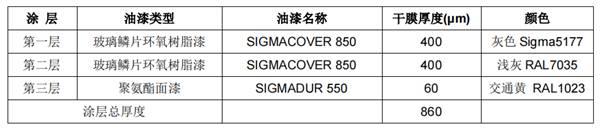
1.本发明属于海上风电机组施工涂装技术领域,特别涉及一种海上风电机组施工主体及附属结构防腐涂装工艺。
背景技术:2.随着社会发展,能源需求越来越大;随着石油、天然气等不可再生能源的消耗及人们环保意识的增强,世界各国的清洁能源发展迅猛,风电作为一种清洁能源也越来越受到人们的重视。海上风力发电机组(简称海上风电机组或海上风机)是一种利用海上风力资源发电的新型发电装备,它通常包括塔头(即风轮与机舱)、塔筒及基础,塔筒的底端固定在基础上,塔头安装在塔筒顶端;基础设置于海底,用于支撑并固定塔筒,基础对海上风电机组的整机安全具有至关重要的作用。
3.目前,海上风电机组在施工过程中,需要对风机机组以及附属结构进行防腐处理,由于在海面上施工,对方面防腐工艺较为复杂,并且根据不同的区域,其防腐方式也不相同,从而导致防腐工艺较为复杂困难,影响风电机组以及附属机构的使用寿命。
4.因此,发明一种海上风电机组施工主体及附属结构防腐涂装工艺来解决上述问题很有必要。
技术实现要素:5.针对上述问题,本发明提供了一种海上风电机组施工主体及附属结构防腐涂装工艺,以解决上述背景技术中提出的问题。
6.为实现上述目的,本发明提供如下技术方案:一种海上风电机组施工主体及附属结构防腐涂装工艺,包括以下内容:(1)基材表面处理:在进行清洗、表面喷砂、涂装作业之前,需检验完成确认,所有不需涂装的位置需要在表面处理和涂装施工前进行临时保护以防止破坏和污染,管线的标示铭牌需保护,以备修补时选用正确的系统,所有管口需密封以避免磨料进入;(2)环境要求:在基材表面温度未超过露点温度3℃,或相对湿度超过80%时,喷砂作业不得进行,8小时内需对空气温度、基材温度、相对湿度进行2次读数,一旦天气出现明显变化,必需对以上参数重新测量;(3)涂装系统:将海上风电机组施工主体及附属结构按照不同的位置进行系统涂装,并且选择不同的喷涂材料进行喷涂,实现海上风电机组施工主体及附属结构每个位置的涂装;(4)喷涂施工:将需要使用的油漆和工具进行准备,按照喷涂技巧对相应的位置进行喷涂,达到全面的喷涂;(5)安全事项:所有的工作都必须严格依照以下的要求执行:施工人员的健康和安全法规、油漆供应商的产品技术手册和承包商的安全政策和方针;(6)涂层修复:所有损伤的涂层,在进一步涂装前应进行修复,涂层修复应按安全
事项相关要求进行操作,涂层修复过程测试应按涂装系统的要求进行:(7)质量控制:涂装作业开始前应进行以下检查或检验:涂料的储存状况、容器和包装完整性、涂料的保质期和有效性和信息数据。
7.进一步的,所述基材表面处理还包括以下处理:
①
喷砂预处理:焊渣飞溅、迭片、潜在的氧化皮需在喷砂前清除掉,对于焊接的结构,锐角和片状结构需有不少于2mm的平滑倒角,焊接裂纹需清除,可见的油、脂、脏污、标记、切割物以及其他的可溶解污染物使用有机溶剂清除;
②
现场口预留处理:不做油漆的焊缝应每边预留不小于50mm的宽度,不做油漆的焊缝区域在油漆前应遮盖;
③
热镀锌表面的表面处理:应清除热镀锌表面的污染,如油脂、油、焊渣、氧化物、盐类或标记材料,镀锌表面应使用石榴非金属磨料扫砂清洁,清理后,镀锌层应连续,表面均匀,无机械损伤;
④
最终表面状况:在底漆施工之前,需涂装的表面应清洁、干燥,无油脂或油,达到规定的粗糙度和清洁度,涂装底漆前能够使用压缩空气清除或用吸尘器清洁工件表面。
8.进一步的,所述喷涂施工在以下情况下不得进行:
①
当基材表面温度不能保持超过露点温度3℃以上;
②
当空气的相湿度高于80%或按厂商的要求;
③
环境温度低于5℃,不包括那些适合应用在低温度涂装的油漆;
④
当钢材表面温度高于40℃或按厂商的要求。
9.进一步的,所述喷涂施工中的喷涂技巧具体为:a喷涂施工:喷枪需在整个喷涂过程中保持在适当角度,并与喷涂面保持300-450mm的距离,甚至应当平行走枪,每一次走枪需有50%的搭接,较大的表面应当在两个互成直角的方向交叉进行涂装,每一涂层在整个表面上要均匀一致,流挂和凹陷应立即刷除或移除,再重喷;b辊涂施工:辊涂时,应用质量好的“绒毛”或羊毛的滚筒,当滚筒损坏或磨损而影响涂层的均匀性时应丢弃;c刷涂施工:所用刷子应是高质、高效、好用,首选质量好的猪鬃刷,不得使用尼龙或其他人造猪鬃类刷子。
10.进一步的,所述刷涂施工的应用环境为:喷涂喷不到的区域或小工件;补涂或修复局部损坏的区域;角、边、裂缝、孔洞、焊缝、小弧、螺栓、螺帽、其他不规则表面、喷涂难以达到的区域;表面喷涂每一涂层之前或之后,预涂和喷后的补涂。
11.进一步的,所述涂装系统的多个系统分别为:
①
系统1:以下工件位于大气区的防腐涂层:导管架基础外表面(甲板梁顶面以下)、过渡段和将军柱外表面(甲板以上和以下)、板壳结构(甲板以上)、灌浆管线外表面及支撑外露部分、基础顶法兰外侧;表面处理:喷砂清洁等级sa2.5,表面粗糙度50-80μm;涂层分为三层分别为:玻璃鳞片环氧树脂漆层、玻璃鳞片环氧树脂漆层和聚氨酯面漆层;
②
系统2:以下工件位于浪溅区和水位变动区的防腐涂层:
导管架基础外表面(甲板梁顶面以下)、靠船件中间平台支撑梁、灌浆管线外表面及支撑外露部分、基础顶法兰外侧和靠船防撞系统的防腐涂层;表面处理:喷砂清洁等级sa2.5,表面粗糙度50-80μm;涂层分为三层分别为:玻璃鳞片环氧树脂漆层、玻璃鳞片环氧树脂漆层和聚氨酯面漆层;
③
系统3:以下工件位于水下区的防腐涂层:导管架基础外表面(甲板梁顶面以下)、灌浆管线外表面及支撑外露部分;表面处理:喷砂清洁等级sa2.5,表面粗糙度50-80μm;涂层分为两层分别为:玻璃鳞片环氧树脂漆层和玻璃鳞片环氧树脂漆层;
④
系统4:连接段甲板上表面的防腐涂层;表面处理:喷砂清洁等级sa2.5,表面粗糙度50-80μm;用于甲板非走道部分上表面的涂层分为三层分别为:环氧富锌底漆层、玻璃鳞片环氧树脂漆层和玻璃鳞片环氧树脂漆层;用于甲板上走道表面的涂层分为四层分别为:环氧富锌底漆层、玻璃鳞片环氧树脂漆层或防滑砂层、玻璃鳞片环氧树脂漆层和聚氨酯面漆层;
⑤
系统5:以下工件的防腐涂层:甲板下表面(全部)、甲板支撑梁、加强筋;过渡段(将军柱)内表面(内壁及内部附属构件)以及将军柱内平台、电缆支架、基础顶法兰内侧;表面处理:喷砂清洁等级sa2.5,表面粗糙度50-80μm;涂层分为三层分别为:环氧富锌底漆层、环氧云铁防锈漆层和聚氨酯面漆层;
⑥
系统6:以下工件的防腐涂层:镀锌的爬梯(甲板以上)、镀锌的栏杆(甲板以上)镀锌工件;表面处理:扫砂;涂层分为三层分别为:环氧封闭漆层、环氧云铁防锈漆层和聚氨酯面漆层;
⑦
系统7:以下工件的防腐涂层:镀锌的爬梯(甲板以下)、镀锌的栏杆(甲板以下)镀锌工件;表面处理:扫砂;涂层分为三层分别为:环氧封闭漆层、玻璃鳞片环氧树脂漆层和聚氨酯面漆层;
⑧
系统8:以下工件的防腐涂层:镀锌的电缆j形管喇叭口段的内表面;镀锌的电缆j形管位于水下区的外表面;表面处理:扫砂;涂层分为两层分别为:环氧封闭漆层和玻璃鳞片环氧树脂漆层;
⑨
系统9:以下工件的防腐涂层:镀锌的电缆j形管位于大气区的外表面;表面处理:扫砂;涂层分为三层分别为:环氧封闭漆层、玻璃鳞片环氧树脂漆层和聚氨酯面漆层;
⑩
系统10:工件的防腐涂层:镀锌的电缆j形管位于浪溅区和水位变动区的外表面;表面处理:扫砂;
涂层分为三层分别为:环氧封闭漆层、玻璃鳞片环氧树脂漆层和聚氨酯面漆层;
⑪
系统11:基础法兰上、下表面及法兰孔的防腐涂层:表面处理:sa2.5,表面粗糙度50-80μm(法兰孔除外);涂层分为一层为:无机硅酸锌底漆层;
⑫
系统12:电缆j形管内外表面、爬梯、栏杆、钢格栅的镀锌要求如下:电缆j形管内表面(喇叭口段除外)和钢格栅只做镀锌处理,不用做油漆,其它镀锌的部件或部位需按相关要求的油漆系统做油漆(见系统6至系统10)表面处理:sa3,表面粗糙度50-100μm;涂层分为一层为:热浸锌层。
12.进一步的,所述安全事项的具体内容为:
①
:所有的工作都必须严格依照以下的要求执行:施工人员的健康和安全法规、油漆供应商的产品技术手册和承包商的安全政策和方针;
②
:在表面预处理,涂装和检查时,工作区域应保持通风良好并达到安全工作所需的可见度;
③
:为安全起见,所有的过程通风设备应具有安全性,磨料灰尘和溶剂蒸汽等不会再重新引入工作区域内;
④
:打砂和喷漆区域须提供照明;
⑤
:所有从事涂装的和/或喷砂处理的人都应该使用个人安全设备,班前会议应每天进行以确保每个人都熟悉安全保护装备(例头盔、手套等),油漆供应商的材料安全数据表,并在会议前通知业主代表,喷砂工人的头部护具应通风良好(不超过20℃),并装备过滤器以防止吸入喷砂残渣、油和湿气;
⑥
:涂装结构与脚手架钢管和垫板之间的距离应在300-500mm之间;
⑦
:脚手架钢管的端面应当封死以防止磨料和其他的物质残留;
⑧
:使用前,脚手架前应得到承包商主管或安全主管的检查和许可,这种检查每周至少一次,检查时应当特别注意连接处和垫板的状况。
13.进一步的,所述涂层修复的具体内容为:
①
厚度不足:涂层厚度不足的区域应彻底清洁,如有必要,可进行打磨,用兼容的涂料补涂,直到满足要求,所补的涂层应与相邻区域的面漆平滑过渡;
②
污染的表面:需覆涂的被污染涂层,用有机溶剂清洁,或用高压水或蒸汽清洗装置去除所有的泥浆、油、油脂、或其他杂质;
③
不露铁的涂层损伤:受损区域的涂层应用砂纸、砂轮片或钢丝刷打磨羽化,确保补涂的连续性;
④
露铁的涂层损伤:受损的区域应按工件原定的要求重新清洁,应用完整的油漆系统进行修复,重新清洁的表面,过渡涂层距受损区周边50毫米的区域,边缘应用砂纸或砂轮片打磨羽化,大的破损应打砂处理,补涂油漆系统的所有油漆,小的破损可用动力工具打磨处理,覆涂底漆和面漆;
⑤
热镀锌的修复:表面应进行预处理,处理后的表面应无油、油脂、旧油漆和腐蚀产物,用动力工具清洁表面至裸露金属,在环境不允许打砂或电动工具清洁时,用手动工具打磨,表面处理应扩展到未损坏的镀锌涂层,因焊接对节点处的热浸镀锌层造成的损伤,采
用相应厚度的热喷锌替换,并以环氧封闭漆进行封闭,再进行相应中间漆及面漆施工,镀锌层的损伤,也可用相应厚度的富锌底漆修补,再进行中间漆和面漆的施工。
14.本发明的技术效果和优点:1、本发明通过将海上风电机组施工主体及附属结构按照不同的位置进行多个系统涂装,并且选择不同的喷涂材料进行喷涂,实现海上风电机组施工主体及附属结构每个位置的涂装,从而有效的根据不同的工作环境和不同的工件部位,采用不同的涂料和不同的涂装方式进行防腐处理,提高风电机组以及附属结构的防腐效果,提高使用寿命,加快防腐处理,减少对外界污染。
15.本发明的其它特征和优点将在随后的说明书中阐述,并且,部分地从说明书中变得显而易见,或者通过实施本发明而了解。本发明的目的和其他优点可通过在说明书中所指出的结构来实现和获得。
具体实施方式
16.为使本发明实施例的目的、技术方案和优点更加清楚,对本发明实施例中的技术方案进行清楚、完整地说明,显然,所描述的实施例是本发明一部分实施例,而不是全部的实施例。基于本发明中的实施例,本领域普通技术人员在没有做出创造性劳动前提下所获得的所有其他实施例,都属于本发明保护的范围。
17.实施例1:本发明提供了一种海上风电机组施工主体及附属结构防腐涂装工艺,包括以下内容:(1)基材表面处理:在进行清洗、表面喷砂、涂装作业之前,需检验完成确认,所有不需涂装的位置需要在表面处理和涂装施工前进行临时保护以防止破坏和污染,管线的标示铭牌需保护,以备修补时选用正确的系统,所有管口需密封以避免磨料进入;所述基材表面处理还包括以下处理:
①
喷砂预处理:焊渣飞溅、迭片、潜在的氧化皮需在喷砂前清除掉,对于焊接的结构,锐角和片状结构需有不少于2mm的平滑倒角,焊接裂纹需清除,可见的油、脂、脏污、标记、切割物以及其他的可溶解污染物使用有机溶剂清除;
②
现场口预留处理:不做油漆的焊缝应每边预留不小于50mm的宽度,不做油漆的焊缝区域在油漆前应遮盖;
③
热镀锌表面的表面处理:应清除热镀锌表面的污染,如油脂、油、焊渣、氧化物、盐类或标记材料,镀锌表面应使用石榴非金属磨料扫砂清洁,清理后,镀锌层应连续,表面均匀,无机械损伤;
④
最终表面状况:在底漆施工之前,需涂装的表面应清洁、干燥,无油脂或油,达到规定的粗糙度和清洁度,涂装底漆前能够使用压缩空气清除或用吸尘器清洁工件表面。
18.(2)环境要求:在基材表面温度未超过露点温度3℃,或相对湿度超过80%时,喷砂作业不得进行,8小时内需对空气温度、基材温度、相对湿度进行2次读数,一旦天气出现明显变化,必需对以上参数重新测量;所述喷涂施工在以下情况下不得进行:
①
当基材表面温度不能保持超过露点温度3℃以上;
②
当空气的相湿度高于80%或按厂商的要求;
③
环境温度低于5℃,不包括那些适合应用在低温度涂装的油漆;
④
当钢材表面温度高于40℃或按厂商的要求;(3)涂装系统:将海上风电机组施工主体及附属结构按照不同的位置进行系统涂装,并且选择不同的喷涂材料进行喷涂,实现海上风电机组施工主体及附属结构每个位置的涂装;(4)喷涂施工:将需要使用的油漆和工具进行准备,按照喷涂技巧对相应的位置进行喷涂,达到全面的喷涂,浪溅区所涂玻璃鳞片漆应向大气区和水位变动区各延伸30~50cm,玻璃鳞片漆与环氧树脂漆之间采用“搭接”形式过渡连接,即把过渡区域的涂层轻轻打毛,并打磨成平滑的过渡层,且平滑过渡层的坡口宽度不小于5cm,然后再将玻璃鳞片涂层搭接到环氧树脂漆之上;所述喷涂施工中的喷涂技巧具体为:a喷涂施工:喷枪需在整个喷涂过程中保持在适当角度,并与喷涂面保持300-450mm的距离,甚至应当平行走枪,每一次走枪需有50%的搭接,较大的表面应当在两个互成直角的方向交叉进行涂装,每一涂层在整个表面上要均匀一致,流挂和凹陷应立即刷除或移除,再重喷;b辊涂施工:辊涂时,应用质量好的“绒毛”或羊毛的滚筒,当滚筒损坏或磨损而影响涂层的均匀性时应丢弃;c刷涂施工:所用刷子应是高质、高效、好用,首选质量好的猪鬃刷,不得使用尼龙或其他人造猪鬃类刷子;所述刷涂施工的应用环境为:喷涂喷不到的区域或小工件;补涂或修复局部损坏的区域;角、边、裂缝、孔洞、焊缝、小弧、螺栓、螺帽、其他不规则表面、喷涂难以达到的区域;表面喷涂每一涂层之前或之后,预涂和喷后的补涂;(5)安全事项:所有的工作都必须严格依照以下的要求执行:施工人员的健康和安全法规、油漆供应商的产品技术手册和承包商的安全政策和方针;所述安全事项的具体内容为:
①
:所有的工作都必须严格依照以下的要求执行:施工人员的健康和安全法规、油漆供应商的产品技术手册和承包商的安全政策和方针;
②
:在表面预处理,涂装和检查时,工作区域应保持通风良好并达到安全工作所需的可见度;
③
:为安全起见,所有的过程通风设备应具有安全性,磨料灰尘和溶剂蒸汽等不会再重新引入工作区域内;
④
:打砂和喷漆区域须提供照明;
⑤
:所有从事涂装的和/或喷砂处理的人都应该使用个人安全设备,班前会议应每天进行以确保每个人都熟悉安全保护装备(例头盔、手套等),油漆供应商的材料安全数据表,并在会议前通知业主代表,喷砂工人的头部护具应通风良好(不超过20℃),并装备过滤器以防止吸入喷砂残渣、油和湿气;
⑥
:涂装结构与脚手架钢管和垫板之间的距离应在300-500mm之间;
⑦
:脚手架钢管的端面应当封死以防止磨料和其他的物质残留;
⑧
:使用前,脚手架前应得到承包商主管或安全主管的检查和许可,这种检查每周至少一次,检查时应当特别注意连接处和垫板的状况;(6)涂层修复:所有损伤的涂层,在进一步涂装前应进行修复,涂层修复应按安全事项相关要求进行操作,涂层修复过程测试应按涂装系统的要求进行:所述涂层修复的具体内容为:
①
厚度不足:涂层厚度不足的区域应彻底清洁,如有必要,可进行打磨,用兼容的涂料补涂,直到满足要求,所补的涂层应与相邻区域的面漆平滑过渡;
②
污染的表面:需覆涂的被污染涂层,用有机溶剂清洁,或用高压水或蒸汽清洗装置去除所有的泥浆、油、油脂、或其他杂质;
③
不露铁的涂层损伤:受损区域的涂层应用砂纸、砂轮片或钢丝刷打磨羽化,确保补涂的连续性;
④
露铁的涂层损伤:受损的区域应按工件原定的要求重新清洁,应用完整的油漆系统进行修复,重新清洁的表面,过渡涂层距受损区周边50毫米的区域,边缘应用砂纸或砂轮片打磨羽化,大的破损应打砂处理,补涂油漆系统的所有油漆,小的破损可用动力工具打磨处理,覆涂底漆和面漆;
⑤
热镀锌的修复:表面应进行预处理,处理后的表面应无油、油脂、旧油漆和腐蚀产物,用动力工具清洁表面至裸露金属,在环境不允许打砂或电动工具清洁时,用手动工具打磨,表面处理应扩展到未损坏的镀锌涂层,因焊接对节点处的热浸镀锌层造成的损伤,采用相应厚度的热喷锌替换,并以环氧封闭漆进行封闭,再进行相应中间漆及面漆施工,镀锌层的损伤,也可用相应厚度的富锌底漆修补,再进行中间漆和面漆的施工(7)质量控制:涂装作业开始前应进行以下检查或检验:涂料的储存状况、容器和包装完整性、涂料的保质期和有效性和信息数据。
19.实施例2:所述涂装系统的多个系统分别为:
①
系统1:以下工件位于大气区的防腐涂层:导管架基础外表面(甲板梁顶面以下)、过渡段和将军柱外表面(甲板以上和以下)、板壳结构(甲板以上)、灌浆管线外表面及支撑外露部分、基础顶法兰外侧;表面处理:喷砂清洁等级sa2.5,表面粗糙度50-80μm;涂层分为三层分别为:玻璃鳞片环氧树脂漆层、玻璃鳞片环氧树脂漆层和聚氨酯面漆层,具体参数如下表所示:
②
系统2:以下工件位于浪溅区和水位变动区的防腐涂层:导管架基础外表面(甲板梁顶面以下)、靠船件中间平台支撑梁、灌浆管线外表面及支撑外露部分、基础顶法兰外侧和靠船防撞系统的防腐涂层;表面处理:喷砂清洁等级sa2.5,表面粗糙度50-80μm;
涂层分为三层分别为:玻璃鳞片环氧树脂漆层、玻璃鳞片环氧树脂漆层和聚氨酯面漆层,具体参数如下表所示:
③
系统3:以下工件位于水下区的防腐涂层:导管架基础外表面(甲板梁顶面以下)、灌浆管线外表面及支撑外露部分;表面处理:喷砂清洁等级sa2.5,表面粗糙度50-80μm;涂层分为两层分别为:玻璃鳞片环氧树脂漆层和玻璃鳞片环氧树脂漆层,具体参数如下表所示:
④
系统4:连接段甲板上表面的防腐涂层;表面处理:喷砂清洁等级sa2.5,表面粗糙度50-80μm;用于甲板非走道部分上表面的涂层分为三层分别为:环氧富锌底漆层、玻璃鳞片环氧树脂漆层和玻璃鳞片环氧树脂漆层,具体参数如下表所示:用于甲板上走道表面的涂层分为四层分别为:环氧富锌底漆层、玻璃鳞片环氧树脂漆层或防滑砂层、玻璃鳞片环氧树脂漆层和聚氨酯面漆层,具体参数如下表所示:
⑤
系统5:以下工件的防腐涂层:甲板下表面(全部)、甲板支撑梁、加强筋;过渡段(将军柱)内表面(内壁及内部附属构件)以及将军柱内平台、电缆支架、基础顶法兰内侧;表面处理:喷砂清洁等级sa2.5,表面粗糙度50-80μm;涂层分为三层分别为:环氧富锌底漆层、环氧云铁防锈漆层和聚氨酯面漆层,具体参数如下表所示:
⑥
系统6:以下工件的防腐涂层:镀锌的爬梯(甲板以上)、镀锌的栏杆(甲板以上)镀锌工件;表面处理:扫砂;涂层分为三层分别为:环氧封闭漆层、环氧云铁防锈漆层和聚氨酯面漆层,具体参数如下表所示:
⑦
系统7:以下工件的防腐涂层:镀锌的爬梯(甲板以下)、镀锌的栏杆(甲板以下)镀锌工件;表面处理:扫砂;涂层分为三层分别为:环氧封闭漆层、玻璃鳞片环氧树脂漆层和聚氨酯面漆层,具
体参数如下表所示:
⑧
系统8:以下工件的防腐涂层:镀锌的电缆j形管喇叭口段的内表面;镀锌的电缆j形管位于水下区的外表面;表面处理:扫砂;涂层分为两层分别为:环氧封闭漆层和玻璃鳞片环氧树脂漆层,具体参数如下表所示:
⑨
系统9:以下工件的防腐涂层:镀锌的电缆j形管位于大气区的外表面;表面处理:扫砂;涂层分为三层分别为:环氧封闭漆层、玻璃鳞片环氧树脂漆层和聚氨酯面漆层,具体参数如下表所示:
⑩
系统10:工件的防腐涂层:镀锌的电缆j形管位于浪溅区和水位变动区的外表面;表面处理:扫砂;涂层分为三层分别为:环氧封闭漆层、玻璃鳞片环氧树脂漆层和聚氨酯面漆层,具体参数如下表所示:
⑪
系统11:基础法兰上、下表面及法兰孔的防腐涂层:表面处理:sa2.5,表面粗糙度50-80μm(法兰孔除外);
涂层分为一层为:无机硅酸锌底漆层,具体参数如下表所示:
⑫
系统12:电缆j形管内外表面、爬梯、栏杆、钢格栅的镀锌要求如下:电缆j形管内表面(喇叭口段除外)和钢格栅只做镀锌处理,不用做油漆,其它镀锌的部件或部位需按相关要求的油漆系统做油漆(见系统6至系统10)表面处理:sa3,表面粗糙度50-100μm;涂层分为一层为:热浸锌层,具体参数如下表所示:实施例3:对上述涂装后的产品进行质量控制检测,具体步骤为:s1涂层试板:测试板应用与要进行涂装的工件相同的基材制作,试板的尺寸为300x300x6毫米,试板清洁方法与油漆系统应用与待涂装的工件或区域相同;s2外观检查:防腐涂装完成并达到固化要求出厂前应进行检验,检验项目包括:颜色和光泽、有无气泡、锈蚀、开裂、剥落、粉化、渗色、咬边或皱皮、缩孔或鱼眼、白化、漏涂或擦伤等涂装缺陷,观察检验项目包括目测和10倍放大镜检查,以上任何缺陷被发现后,修补工作需按照涂层修复的方法进行修复;s3膜厚:为了获得规定的干膜厚,操作者应频繁测试湿膜厚,包括校准,应根据标准《漆膜厚度测定法》执行,干膜厚度应大于或等于设计厚度值者应占检测点总数的90%以上,其它测点的干膜厚度也不应低于90%的设计厚度值。每10平方米取5个基准面,每个基准面采用3点测量,3点厚度的平均值为该基准面局部涂层的厚度值,如达不到上述要求,必须进行补涂直到满足厚度要求,每一涂层都要测试,最大厚度应遵循油漆厂商的详细建议;s4漏涂测试:对桩体外表面(一定桩长范围内)100%的涂装范围均应采用高压漏涂点检测仪进行漏点检测;桩体内表面和防撞管、电缆管、爬梯表面的50%涂装范围应进行漏点抽检;其余部位按10%范围进行漏点抽检,抽检位置由现场监理(或监造)工程师指定,漏涂点应按nacesp0188进行检测,干膜厚度在200-300微米时,检漏电压为1500v;300-400微米时,检漏电压为2000v;400~600微米时,检漏电压为2500v;600~1000微米时,检漏电压为3000v,发现任何漏涂点均应进行补涂,且修补处的干膜厚度复测结果应满足设计要求;s5附着力测试:涂层施工完成并按涂料固化性能规定时间后,由发包人或其委托的监理进行涂层附着力的抽检试验,试验结果要满足8mpa以上的设计要求(镀锌件油漆系统和法兰面无机锌油漆系统除外),并按涂层修复要求对试验破损位置进行修补(附着力可在现场挂板检测,不在原结构上试验)。
20.尽管参照前述实施例对本发明进行了详细的说明,本领域的普通技术人员应当理解:其依然可以对前述各实施例所记载的技术方案进行修改,或者对其中部分技术特征进
行等同替换;而这些修改或者替换,并不使相应技术方案的本质脱离本发明各实施例技术方案的精神和范围。