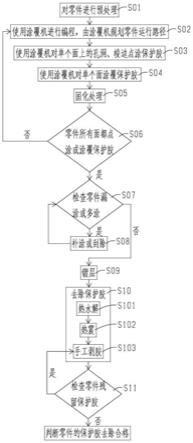
1.本发明涉及表面处理技术领域,具体涉及一种适用于自动涂覆设备的局部镀保护方法。
背景技术:2.局部镀保护为金属表面处理方式之一,常用的方法有包扎法、专用夹具法、绝缘塑料保护法、蜡剂保护法、涂料绝缘法及工序倒置法等,这些方法中用于铝合金微波腔体高精度保护的主要是涂料绝缘法,该方法一般采用手工涂覆溶剂型涂料或阻镀油墨,使用烘箱烘干涂层,电镀完成后再采用稀释剂、脱漆剂等对保护涂层进行退除。
3.涂料绝缘法使用全手工涂覆,耗费大量人工工时,对操作人员的技术及熟练程度依赖较高;在涂覆时需要刷涂多道,每道之间需要待溶剂挥发后,再次涂覆,材料的工艺固化时间较长,约需1h;镀后采用浸泡、人工刷洗等方式去除保护材料,保护及去保护工艺周期约需4~6h,工艺周期长;所用涂覆材料大部分为溶剂型,可挥发性有机物偏高,对操作人员身体有害,可燃液体的危废处置困难。
技术实现要素:4.本发明的目的在于:针对上述存在的问题,提供一种增加预处理方式,并借助涂覆机代替人工涂覆,减少工时,使用安全环保涂覆材料适用于自动涂覆设备的局部镀保护方法。
5.本发明采用的技术方案如下:
6.一种适用于自动涂覆设备的局部镀保护方法包括以下步骤:
7.步骤1,对零件进行化学除油或化学镀镍的预处理;
8.步骤2,使用涂覆机进行编程,由涂覆机自动规划零件的运行路径;
9.步骤3,使用涂覆机对零件单个面上的孔洞、棱边点涂保护胶;
10.步骤4,使用涂覆机对零件单个面进行涂覆保护胶;
11.步骤5,对零件上的保护胶进行固化处理;
12.步骤6,重复步骤1~步骤5,直至零件的所有面的孔洞、棱边及所有面均完成点涂和涂覆保护胶。
13.采用上述技术方案,在涂覆之前使用化学除油或化学镀镍的预处理,使得后续涂覆的保护胶更加牢固,充分发挥保护的作用;先局部点涂,再单面涂覆的方式,保证保护胶能够完全覆盖在零件的各个位置上;每涂覆完一面后,就对保护胶进行固化处理,防止后续涂覆时,损坏已经涂覆的保护胶。
14.优选的,步骤1中的化学除油方式具体为:溶解除油粉,得到除油溶液,将零件置于除油溶液中浸泡6~10min,温度保持在40~60℃。
15.优选的,步骤1中化学镀镍的方式具体为:将零件置于镀镍溶液中浸泡30~45min,温度保持在85~91℃,浸泡后的零件使用流水水洗并烘干;镀镍溶液的ph为4.7~5.2。
16.优选的,步骤3中的保护胶为紫外光固化型丙烯酸树脂可剥胶,涂胶厚度不超过3mm;可剥胶的粘度为500000~800000mpa.s,比重1.05~1.10,硬度65~70,粘接强度大于0.1kg/cm2。
17.采用上述技术方案,点涂孔洞和棱边的保护胶使用安全环保的材料,点涂厚度和该保护胶的参数便于后续保护胶的剥离,减少去除保护胶的工艺耗时,减小操作难度。
18.优选的,步骤4的保护胶为紫外光固化型丙烯酸树脂水解胶,涂胶厚度不超过3mm;水解胶粘度15000~30000mpa.s,比重1.01~1.06,硬度50~55,粘接强度大于0.1kg/cm2。
19.采用上述技术方案,涂覆面的保护胶也使用安全环保的材料,涂覆厚度和该保护胶的参数便于后续保护胶的剥离,缩短去除保护胶的工艺耗时,减小操作难度。
20.优选的,步骤5具体为:采用波长为395nm的led-uv灯,光照强度大于1000mw/cm2,在距离零件30~50mm范围内照射零件10~20s。
21.采用上述技术方案,固化工具使用led-uv灯,该固化工具的固化时间短,进一步缩短整个工艺的耗时。
22.优选的,步骤6后还包括步骤:
23.步骤7,检查零件是否漏涂或多涂保护胶;
24.步骤8,对零件漏涂保护胶的部位进行局部手工补涂,对零件多涂保护胶的部位进行手工刮除。
25.步骤9:对零件进行电镀镀层。
26.采用上述技术方案,人工配合涂覆机对整个零件进行涂覆,涂覆机涂覆结束后,使用人工进行检查并修改,保证零件上涂覆的保护胶均匀、完整。
27.优选的,步骤9后还包括步骤:
28.步骤10,按照热水解、热震、手工剥胶的工序去除零件上的保护胶。
29.优选的,步骤10中热水解工序具体为:将零件放入95~97℃的热水中,浸泡30~40min,取出,并使用压缩空气吹干表面水分。
30.优选的,步骤10中热震工序具体为:使用烘箱将零件加热至150~190℃,保温1h,取出后迅速放入冷水中降温,将零件温度降至室温后,取出零件,使用气压为0.3~0.5mpa的压缩空气吹干零件上的水分,并吹除零件上翘起的胶层。
31.采用上述技术方案,去除保护胶的工序设计,使得保护胶能够快速且大面积剥离零件,并且不对零件造成损坏;缩短去除保护胶的工艺耗时。
32.综上所述,由于采用了上述技术方案,本发明的有益效果是:借助涂覆机对零件进行涂覆,代替全手工涂覆的方式,减少人工工时的耗费;并且对操作人员的技术及熟练程度依赖度不高。使用先局部点涂,后大面积涂覆的方式,不需要涂覆多道,也不需要每道都进行固化,大幅缩短工艺周期。除此之外,使用保护胶代替原来的涂覆材料,安全环保,相对减少涂覆材料对操作人员的身体损害;并且废料不属于可燃液体危废,处置简单。
附图说明
33.图1为本发明的流程图。
具体实施方式
34.下面结合附图,对本发明作详细的说明。
35.为了使本发明的目的、技术方案及优点更加清楚明白,以下结合附图及实施例,对本发明进行进一步详细说明。应当理解,此处所描述的具体实施例仅仅用以解释本发明,并不用于限定本发明。
36.请参看图1,一种适用于自动涂覆设备的局部镀保护方法包括以下步骤:
37.s01:对零件进行化学除油或化学镀镍的预处理,预处理使得后续涂覆的保护胶更加牢固,充分发挥保护的作用;
38.化学除油方式具体为:溶解除油粉,得到20~40g/l的除油溶液,将零件置于除油溶液中浸泡6~10min,温度保持在40~60℃;除油粉采用安美特u-151除油粉;也可采用其他等效的水基除油工艺;
39.化学镀镍的方式具体为:将零件置于镀镍溶液中浸泡30~45min,温度保持在85~91℃,浸泡后的零件使用流水水洗并烘干;镀镍溶液的ph为4.7~5.2,采用美坚375-1型中磷化学镀镍体系:meten375-1a和meten375-1b,其中,meten375-1a为60ml/l,meten375-1b为150ml/l;
40.s02:将零件的图形导入涂覆机中,使用涂覆机进行编程,对零件需要涂覆的面上选择需要涂覆的孔洞、棱边、面,并设置涂覆参数,由涂覆机自动规划零件的运行路径;
41.s03:使用涂覆机对零件单个面上的孔洞、棱边点涂保护胶,涂胶厚度不超过3mm;该保护胶为紫外光固化型丙烯酸树脂可剥胶,粘度为500000~800000mpa.s,比重1.05~1.10,,硬度65~70,粘接强度大于0.1kg/cm2;紫外光固化型丙烯酸树脂可剥胶为安全环保的材料,点涂厚度和该保护胶的参数设计为了便于后续保护胶的剥离,并减少去除保护胶的工艺耗时,减小操作难度。
42.s04:使用涂覆机对零件单个面进行涂覆保护胶,涂胶厚度不超过3mm;该保护胶为紫外光固化型丙烯酸树脂水解胶,耐90℃至少30min,粘度为15000~30000mpa.s,比重1.01~1.06,硬度50~55,粘接强度大于0.1kg/cm2;紫外光固化型丙烯酸树脂水解胶为安全环保的材料,涂覆厚度和该保护胶的参数设计为了便于后续保护胶的剥离,缩短去除保护胶的工艺耗时,减小操作难度;
43.s05:采用波长为395nm的led-uv灯,光照强度大于1000mw/cm2,在距离零件30~50mm范围内,照射零件10~20s;固化工具使用led-uv灯,该固化工具的固化时间短,进一步缩短整个工艺的耗时;
44.s06:重复步骤s02~s05,直至零件的所有面及该面对应的孔洞、棱边均完成点涂和涂覆保护胶;
45.s07:目视或借助10~30倍显微镜检查零件是否漏涂或多涂保护胶;
46.s08:若有漏涂或多涂,则对零件漏涂保护胶的部位进行局部手工补涂,对零件多涂保护胶的部位进行手工刮除,重复步骤s07;人工配合涂覆机对整个零件进行涂覆,涂覆机涂覆结束后,使用人工进行检查并修改,保证零件上涂覆的保护胶均匀、完整;若没有漏涂或多涂,则进行下一步骤;
47.s09:对零件进行电镀金、银,化学镀镍镀层;
48.s10:去除零件上的保护胶:
49.s101:热水解,将零件放入95~97℃的热水中,浸泡30~40min,取出,并使用压缩空气吹干表面水分;
50.s102:热震,使用烘箱将零件加热至150~190℃,保温1h,取出后迅速放入冷水中降温,将零件温度降至室温后,取出零件,使用气压为0.3~0.5mpa的压缩空气吹干零件上的水分,并吹除零件上翘起的胶层;
51.s103:手工剥胶,使用手术刀片的尖端清理孔洞及凹腔内残留的保护胶。
52.s11:目视或借助10~30倍显微镜检查零件表面是否还有残留的保护胶,若是,则重复步骤s103;若否,则判断零件的保护胶去除合格。
53.本方法中,使用紫外光固化型丙烯酸树脂可剥胶和紫外光固化型丙烯酸树脂水解胶组合,材料安全环保,附着牢固并且便于去除;使用先局部点涂,再单面涂覆的方式,保证保护胶能够完全覆盖在零件的各个位置上;每涂覆完一面后,就对保护胶进行固化处理,防止后续涂覆时,损坏已经涂覆的保护胶;去除保护胶的工艺设计,使得保护胶能够快速且大面积剥离零件,并且不对零件造成损坏;缩短去除保护胶的工艺耗时。
54.传统涂料绝缘法的存在不足:第一,单件产品局部保护成本高,全手工涂覆,耗费大量人工工时,对操作人员的技术及熟练程度依赖较高;第二,局部保护及去保护工艺周期长,保护时刷涂多道,每道之间需表干待溶剂挥发后,再次涂覆,且材料的工艺固化时间较长,约需1h;镀后采用浸泡,人工刷洗等方式去除保护材料,保护及去保护工艺周期约需4~6h;第三,工艺能耗较高,固化工艺采用鼓风烘箱烘干,烘干温度一般为60~150℃,设备运行能耗较大;第四,工艺本质不安全、不环保,所用材料大部分为溶剂型,可挥发性有机物偏高,对操作者身体有害,职业防护困难,可燃液体危废处置困难;第五,不适合采用自动化涂覆设备,局部保护零件大部分需要保护六个面,采用自动化涂覆设备,产品装夹困难,总有一个面不能涂覆,运用自动化涂覆设备将使局部涂覆的工艺周期增加一倍。
55.本方法针对涂料绝缘法存在的以上不足进行设计,并解决了上述不足产生的问题。经过计算,本方法能够有效提高局部电镀的生产效率,将局部保护及去保护工艺周期缩短至少60%;并且本方法适合批量生产,能够减少局部电镀过程中保护操作人员约1/3。
56.本文中应用了具体的实施例对本发明的原理及实施方式进行了阐述,以上实施例的说明只是用于帮助理解本发明的方法及其核心思想。应当指出,对于本技术领域的普通技术人员来说,在不脱离本发明原理的前提下,还可以对本发明进行若干改进和修饰,这些改进和修饰也落入本发明权利要求的保护范围内。