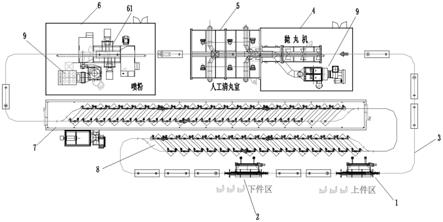
1.本实用新型涉及施工升降机涂装防护技术领域,具体属于一种施工升降机标准节涂装生产线。
背景技术:2.施工升降机标准节作为施工升降机的运行导轨,是施工升降机的重要结构件,由于其运行速度快、运行条件恶劣,因此在施工升降机标准节的生产过程中,为了保证其耐腐蚀性以及美观要求,对施工升降机标准节进行涂装防护是必不可少的工序。现有施工升降机标准节涂装工艺方法为:预处理(人工打磨)——人工喷漆——流平——自然风干,预处理是涂装工艺的首要流程,好的预处理对后续漆膜的附着有着至关重要的作用,而人工打磨是一种比较粗糙的预处理方式。人工喷漆就是通过操作人员,用喷枪对产品的表面直接进行喷油漆。流平指油漆在涂覆后,尚未干燥成膜之前,由于表面张力的作用,逐渐收缩成最小面积的过程。流平后将标准节置于空旷的场地进行自然风干,一般来说,油漆1小时即可达到表干,24小时实干,72小时完全固化。
3.现有技术中的人工打磨效率低、劳动强度大、打磨质量难以保证,人工操作,会有熟练程度,技术水平的问题,难以保证加工工件的一致性且粉尘污染严重。人工喷漆油漆浪费严重,损耗大,增加成本;喷涂质量不稳定;由于人工喷涂的方式不一样,在喷涂过程中很难保证上漆量的均匀和质量的稳定;生产效率低,不适合大批量的生产;污染严重,由于没有对漆雾进行处理,严重影响了操作人员的健康,并对环境造成污染。自然风干时间长,占用场地大。由于投入的人工较多,管理成本较高,工人工资成本较高。现有技术中尚无对施工升降机标准节涂装形成系统的、流水线式的批量涂装生产工艺,无法满足降本增效、提产提质、环保节能的生产目标。
技术实现要素:4.本实用新型的目的在于针对现有涂装技术中效率低、质量参差不齐,污染严重、周期长,人工成本高的问题,在尽量减少传统人工随机性误差影响的前提下,通过半自动的涂装生产线及完善的上件
→
抛丸
→
清丸
→
粉末喷涂
→
粉末固化
→
冷却
→
检查下件的新工艺方法,从而形成施工升降机标准节涂装系统化、流水线式的批量涂装生产工艺,进而实现降本增效、提产提质、环保节能的生产目标。
5.为了实现上述目的,本实用新型采用以下技术方案:
6.一种施工升降机标准节涂装生产线,包括上件区、下件区、输送轨道、抛丸机、清丸室、喷涂房、固化房和冷却工位,所述输送轨道依次穿过上件区、抛丸机、清丸室、喷涂房、固化房、冷却工位、下件区形成一条连续作业的生产线,所述抛丸机中的抛丸室内壁上设有多个开口相对的抛丸器,该抛丸室与清丸室连通,所述清丸室内设有若干个清丸枪,该清丸室的底部设有由清丸室向抛丸机倾斜的回收装置,使清理下落的球体落回至抛丸机中,所述抛丸室和清丸室的顶部均连通滤筒除尘器,所述喷涂房中在输送轨道两侧设有若干个可移
动的喷枪,所述固化房内设有加热系统对经过的标准节加热。
7.进一步地,所述抛丸机为离心抛丸机,该抛丸机的抛丸室底部连通水平设置的第一螺杆挤出机的一端,该第一螺杆挤出机的另一端设有竖直向上的上料管,所述上料管上设有气泵,该上料管的上端连接有水平设置的第二螺杆挤出机的一端,该第二螺杆挤出机的另一端下方设有下料斗,该下料斗的下方设有若干软管连通各个抛丸器。
8.进一步地,所述清丸室中在输送轨道的两侧设有升降机,所述清丸枪为高压气枪,所述回收装置为由清丸室向抛丸机倾斜的滑板。
9.进一步地,所述喷涂房连接有粉末自动回收系统、大旋风装置和过滤装置,所述粉末自动回收系统连通喷涂房中的喷枪将涂料送至喷枪中喷出,所述喷涂房的底部连通大旋风装置的顶部,该大旋风装置的底部连通粉末自动回收系统将涂料重新送回喷涂房,所述过滤装置连通大旋风装置的顶部,该过滤装置中设有滤芯。
10.进一步地,所述固化房的侧边设有加热室,该固化房的顶部和底部均与加热室连通,且固化房的顶部设有气泵提供动力使热气在固化房内循环。
11.进一步地,所述冷却工位为双轨道的输送轨道,将标准节停止在该冷却工位上自然冷却。
12.一种利用施工升降机标准节涂装生产线的涂装工艺,包括以下步骤
13.(1)将标准节在上件区上件后,通过输送轨道将标准节输送至抛丸机中抛丸,完成后进入清丸室中,人工使用清丸枪进行清丸,同时开启滤筒除尘器进行除尘;
14.(2)清丸后的标准节输送至喷涂房中,标准节在缓慢经过喷涂房的过程中两侧的喷枪对标准节喷涂料,喷涂房出口处人工检查喷涂完成后由输送轨道输送出去;
15.(3)喷涂后的标准节输送至固化房中,输送的同时开启固化房中的热风循环加热使涂料固化,然后输送至冷却工位处停留静置一端时间,待标准节完全冷却后输送至下件区中下件完成涂装。
16.进一步地,所述滤筒除尘器中的总除尘风量为28000-31000m3/h。
17.进一步地,所述喷涂房连通有大旋风装置将涂料回收,该大旋风装置的风量为17500立方米/小时。
18.进一步地,所述固化房中的温度为180-220℃,固化时间为40-45min,所述冷却时间为35-40min。
19.本实用新型针对现有涂装技术中效率低、质量参差不齐,污染严重、周期长,人工成本高的问题,采用半自动化的技术及新工艺方法,在尽量减少传统人工随机性误差影响的前提下,通过半自动的涂装生产线及完善的上件
→
抛丸
→
清丸
→
粉末喷涂
→
粉末固化
→
冷却
→
检查下件的新工艺方法,大大的提升标准节预处理能力和涂层耐腐蚀性以及美观性,降低人工成本的同时提高了效率和产能,对环境也更友好,从而形成施工升降机标准节涂装系统化、流水线式的批量涂装生产工艺,进而实现降本增效、提产提质、环保节能的生产目标。
20.本实用新型可最大限度的实现标准节半自动涂装生产线及新工艺方法的最优化组合。该技术采用积放式输送机输送,可实现程序控制下的连续或非连续的工件输送;预处理采用自动抛丸+人工清丸的方式,抛丸清洁达sa2.5 级;粉末喷涂采用往复机喷粉+人工补喷的方式,上粉率高,粉房选用欧州先进技术大旋风二级回收塑料喷房,设计的抽风气流
稳定及合理,保证工件上粉率及涂层质量,回收利用率达98%;粉末固化在烘道内进行高温固化,烘道采用隧道式结构,天然气加热系统,热风循环方式,炉温均匀,保温效果好;侧面炉板采用分层隔离保证能耗降至最低,外侧板采用扣板的形式,美观大方;控制系统采用plc可编程集中控制,整条生产线设计紧凑,维护简单,降低生产成本。
21.本实用新型根据标准节半自动的涂装生产线及完善的上件
→
抛丸
→
清丸
→
粉末喷涂
→
粉末固化
→
冷却
→
检查下件的新工艺方法,通过流水线作业形式,最大化的提升了生产效率,同时通过抛丸、粉末喷涂、粉末固化等先进工艺,使得产品品质有质的提升,采用大旋风二级回收塑料喷房,保证工件上粉率及涂层质量,回收利用率达98%,避免了油漆雾化挥发污染空气的问题,半自动生产线模式所需人工较少,解决了人工成本高的问题。
22.本实用新型的创新思路特点如下:
23.1、满足流水线作业形式要求,实现标准节下件即可发货的新模式;
24.2、预处理采用自动抛丸方式,安全、环保,工件表面质量有保证;
25.3、粉末的回收利用率达98%,可以保证工件上粉率及环保性;
26.4、实现降本增效、提产提质、环保节能三大目标;
27.本实用新型解决的关键问题:(1)人工打磨效率低、劳动强度大、打磨质量难以保证的问题。本实用新型利用抛丸器高速旋转的叶轮将弹丸加速抛打至工件表面,对工件表面进行冲击、刮削,不但可以清理掉工件表面的型砂、锈蚀和污物等,还可以消除工件的表面应力,对工件表面进行抛丸强化,提高工件的抗疲劳强度,增加工件喷涂时的涂膜附着力,并最终达到提高整个工件表面及内在质量的目的。(2)人工喷漆油漆浪费严重,损耗大,增加成本,喷涂质量不稳定且有油漆溶剂挥发污染环境的问题。本实用新型采用往复机喷粉+人工补喷的粉末喷涂方式,上粉率高,粉房选用欧州先进技术大旋风二级回收塑料喷房,设计的抽风气流稳定及合理,保证工件上粉率及涂层质量,回收利用率达98%,避免了油漆溶剂挥发污染环境的问题。(3)没有系统的、流水线式的批量涂装生产工艺的问题。本实用新型采用标准节半自动的涂装生产线及完善的上件
→
抛丸
→
清丸
→
粉末喷涂
→
粉末固化
→
冷却
→
检查下件的新工艺方法,可实现降本增效、提产提质、环保节能的生产目标。
28.综上所述,由于本实用新型采用了上述技术方案,本实用新型具有以下技术效果:
29.1、本实用新型的生产线采用半自动的流水线作业形式,输送方式采用 gwj3积放式输送机输送,配有积放小车,单车吊重800kg挂,该输送方式可实现程序控制下的连续工件输送,工艺节拍为2分钟/节,日产400节以上,效率为人工喷漆的3倍以上,人工成本下降1/3。
30.2、本实用新型预处理采用自动抛丸的模式,利用抛丸器高速旋转的叶轮将弹丸加速抛打至工件表面,对工件表面进行冲击、刮削,不但可以清理掉工件表面的型砂、锈蚀和污物等,还可以消除工件的表面应力,对工件表面进行抛丸强化,提高工件的抗疲劳强度,增加工件喷涂时的涂膜附着力,并最终达到提高整个工件表面及内在质量的目的。
31.3、本实用新型采用采用欧州技术的大旋二级回收塑料喷房,本体采用特种工程塑料,不导电易清理,换色方便快捷;一级大旋风回收,回收效率高,回收利用率达98%;二级过滤器滤芯采用进口滤纸,在过滤标准型粉末涂料时可达到99.9%的效能,可保让尾气排放量<3.0mg/m3,可在室内排放。喷房带有工件识别系统,如没有工件进来,喷枪自动停喷,可减少粉末损耗。
32.4、本实用新型的粉末固化在烘道内进行高温固化,烘道采用隧道式结构,天然气加热系统,热风循环方式,炉温均匀,保温效果好;侧面炉板采用分层隔离保证能耗降至最低,外侧板采用扣板的形式,美观大方,标准节固化冷却下件后即可发货,占用场地小。
附图说明
33.图1是本实用新型的生产线的结构示意图;
34.图2是本实用新型的抛丸机的结构示意图;
35.图3是本实用新型的喷涂房的结构示意图;
36.图4是本实用新型的固化房的结构示意图;
37.图5为本实用新型的工艺流程图;
38.图中:上件区1、下件区2、输送轨道3、抛丸机4、抛丸器41、抛丸室 42、第一螺杆挤出机43、上料管44、第二螺杆挤出机45、下料斗46、清丸室5、喷涂房6、喷枪61、粉末自动回收系统62、大旋风装置63、过滤装置 64、固化房7、冷却工位8、滤筒除尘器9。
具体实施方式
39.为使本实用新型的目的、技术方案及优点更加清楚明白,以下参照附图并举出优选实施例,对本实用新型进一步详细说明。然而,需要说明的是,说明书中列出的许多细节仅仅是为了使读者对本实用新型的一个或多个方面有一个透彻的理解,即便没有这些特定的细节也可以实现本实用新型的这些方面。
40.实施例1
41.如图1所示,一种施工升降机标准节涂装生产线,包括上件区1、下件区 2、输送轨道3、抛丸机4、清丸室5、喷涂房6、固化房7和冷却工位8,所述输送轨道依次穿过上件区1、抛丸机4、清丸室5、喷涂房6、固化房7、冷却工位8、下件区2形成一条连续作业的生产线,所述抛丸机4中的抛丸室 42内壁上设有多个开口相对的抛丸器41,该抛丸室42与清丸室5连通,所述清丸室5内设有若干个清丸枪,该清丸室5的底部设有由清丸室5向抛丸机4倾斜的回收装置,使清理下落的球体落回至抛丸机4中,所述抛丸室42 和清丸室5的顶部均连通滤筒除尘器9,所述喷涂房6中在输送轨道3两侧设有若干个可移动的喷枪61,所述固化房7内设有加热系统对经过的标准节加热。上件区1和下件区2设有液压升降平台,可以实现标准节升降式吊挂上下件。
42.输送轨道3为设置在积放式输送链工位,设有双层轨道三维空间闭环连续输送系统,该输送系统包括积放式输送线和积放式输送机。积放式输送线可以高速运行,节省工位之间货物运送的时间,提高了生产率,同时也大大减少了吊具数量,降低了链条牵引力降低了造价。积放式输送机采用gwj3输送,配有积放小车,单车吊重800kg挂,可实现程序控制下的连续或非连续的工件输送。输送系统具有完整的线路自动装置,可以完成输送物品分类、贮存、分支、合流、自动装卸等复杂工艺流程,使工厂的生产按照一定的工艺流程有条不紊地进行。
43.抛丸机4为离心抛丸机,该抛丸机4的抛丸室42底部连通水平设置的第一螺杆挤出机43的一端,该第一螺杆挤出机43的另一端设有竖直向上的上料管44,所述上料管44上设有气泵,该上料管44的上端连接有水平设置的第二螺杆挤出机45的一端,该第二螺杆挤出
机45的另一端下方设有下料斗 46,该下料斗46的下方设有若干软管连通各个抛丸器41。抛丸机4设置在抛丸工位上,其中设有抛丸室和抛丸器,抛丸室的长度为2.4米,抛丸室壳体为钢板与型钢焊接结构,具有足够的强度和刚性;抛丸室的四周共设置8台抛丸器,抛丸器的布置经过计算机三维动态模拟,所有布置的角度、位置均由计算机模拟确定,每组抛丸器都跟工件运行方向成一定角度,保证对被清理工件四周及端面进行全方位的抛丸清理,实现最优化抛射效果,达到行业领先水平。人工清丸工位4设有清理室和清丸系统,清理室的长度为5.0米,清理室采用2.0钢板与方钢管焊接结构,具有足够的强度和刚性;清丸系统配有以压缩空气为动力的吹尘枪2支,配合用户采购的吸丸机可清除工件表面附着的灰尘及弹丸。
44.如图2所示,清丸室5中在输送轨道3的两侧设有升降机,作业人员可站在升降机上进行清丸,清丸枪为高压气枪,所述回收装置(图中未示出) 为由清丸室向抛丸机倾斜的滑板,清丸室5设置在人工清丸工位上,抛丸工位、人工清丸工位构成预处理系统,整个预处理系统主要优点为:
①
抛丸设备呈直线布置(上件区+前辅室+抛丸室+清丸室+下件);双钩起吊;循环清理,整体结构紧凑、实用、美观。
②
抛丸器布置采用三维电脑模拟,采用8 台抛丸器,抛丸器与工件进出方向呈一定夹角,对工件表面进行冲击、刮削,不但可以清理掉工件表面的型砂、锈蚀和污物等,还可以消除工件的表面应力,对工件表面进行抛丸强化,提高工件的抗疲劳强度,增加工件喷漆时的漆膜附着力,大大提高抛丸表面质量。
③
抛丸器壳体与清理室之间采用法兰通孔连接,抛丸器两端部长护板采用耐磨轧制mn13防护板,设备整体坚固耐用且方便设备维修。
④
大门与室体之间通过钢护板、橡胶板、毛刷与室体之间采用迷宫性密封,封闭式作业,无粉尘飞扬;
⑤
按钢材用途可清理规定的除锈级别,并可获得不同的抛丸光洁度和清理质量均匀的完工表面;
⑥
流水线作业,速度快,工作效率高,质量稳定。
45.其中滤筒除尘器9设置在粉尘处理工位,该粉尘处理工位设有除尘系统,除尘系统采用二级除尘,分别是沉降室和qacl48竖装式滤筒除尘器,除尘设备总除尘风量约为28000-31000m3/h,除尘点分别是抛丸室、前后密封室、补喷清理室和分离器。在正常操作下,含尘空气经顶部入口进入除尘器,然后向下经导流板分散后通过滤芯,粉尘即被阻挡在滤芯外表面上,过滤后的清洁空气经滤芯中心进入清洁空气室,通过出口管排出。滤芯可自动地和间断地进行清灰,在滤芯清灰过程中,脉冲控制仪接通一只电磁脉冲阀的电源,使相应的薄膜阀喷出脉冲高压空气,高压空气即从内到外穿过滤芯,将附着在滤芯外表面上的粉尘除去,尘粒落入尘斗,然后进入集灰桶。
46.如图3所示,喷涂房6连接有粉末自动回收系统62、大旋风装置63和过滤装置64,所述粉末自动回收系统62连通喷涂房6中的喷枪将涂料送至喷枪 61中喷出,所述喷涂房6的底部连通大旋风装置63的顶部,该大旋风装置 63的底部连通粉末自动回收系统62将涂料重新送回喷涂房6,所述过滤装置 64连通大旋风装置63的顶部,该过滤装置64中设有滤芯。喷涂房6设置在粉末静电喷涂工位,并设有大旋风二级回收喷涂系统,大旋风二级回收喷涂系统包括喷房、电动升降器、大旋风装置、过滤装置和粉末自动回收系统;cqb高效喷房系统整体采用三明治式塑料结构,设计大方明亮,手补工位开放式外置,人工操作便捷,底部回收采用“均流式”多通道设计,抽风气流均化,从而获得更佳的上粉效率,符合atex防火及防爆安全要求;电动升降器外观气派、制造精密能保证自动喷涂时喷枪的长期稳定性及重复
准确性,用户可按每种工件所需要的升降高位及低位、行径距离、升降速度等数据预设好,并输入控制系统内留待以后重复使用;喷房含8套瑞士金马自动静电粉末喷枪设备ga03和2套手动喷粉系统2w,静电粉末喷涂系统,采用电子控制的方式调整空气的设定,并持续监测生产参数,可获得高质量的喷涂效果。klc1400型高效率大旋风装置,风量17500立方米/小时,回收利用率高达98%;过滤装置为kfd13-26型高效率过滤器,抽风量17500 立方米/小时,13套dsw型转翼式滤芯清理装置,26个afm-3.5型滤芯,过滤效率达99.9%;粉末自动回收系统实现了由旋风分离装置收回的粉末输送至振动式粉筛,通过筛选后粉末分选至粉桶内,并与粉桶内的新粉混合。粉末被混合后在粉桶内通过流化并输送回喷枪系统上使用
47.如图4所示,固化房7的侧边设有加热室,该固化房7的顶部和底部均与加热室连通,且固化房7的顶部设有气泵提供动力使热气在固化房内循环。固化房7设置在粉末固化工位,粉末固化工位上设有烘道系统,烘道系统由烘道炉体、炉架、炉口装置、炉子密封装置、天然气加热系统、废气排放系统、自动温控系统、热风循环管路等组成。粉末固化炉燃烧机燃烧功率100 万kcal/h,热风循环风机功率p=18.5kw,风量32000m3/hr,烘道烘烤长度36.5 米,采用天然气加热,热风循环方式,炉内温度从室温~220℃(可调),干燥时间40min;烘道炉体采用内外板分层错层隔离专利技术,烘道选用隧道式烘道,采用底部送风底部回风方式,保证炉内温度均匀,送风经济性好,气流组织合理,工件加热较均匀,可保障涂层质量。工件在粉末固化工位6进行粉末固化后转入冷却工位7,冷却工位长25m,可容下15节标准节进行冷却,冷却时间38min,冷却完成后即转入下件工位8,工件下件检验完成后即可进行装配发货,占用场地小。
48.冷却工位8为双轨道的输送轨道,将标准节停止在该冷却工位上自然冷却。
49.本实用新型中还设有电器控制系统工位,电气控制系统工位设有可操作电气控制系统,采用plc集中控制,触摸屏集中显示,设总控制电源开关、温度控制及显示仪表、电压表、三相运行电流指示表和送、排风机电流表;可通过触摸屏设定和修改烘干的参数,操作人员可根据工艺需要选择操作方法,并很容易的了解到设备运行的情况。各加热工位的温度控制均采用数显式自动控制仪,工作时显示各加热点温度的同时进行精确控制。在生产线的各主要工位设置有急停开关,以便于工作过程中进行操作。
50.如图5所示,一种利用上述施工升降机标准节涂装生产线的涂装工艺,包括以下步骤
51.(1)将标准节在上件区上件后,通过输送轨道将标准节输送至抛丸机中抛丸,完成后进入清丸室中,人工使用清丸枪进行清丸,同时开启滤筒除尘器进行除尘,滤筒除尘器中的总除尘风量为28000-31000m3/h;
52.(2)清丸后的标准节输送至喷涂房中,标准节在缓慢经过喷涂房的过程中两侧的喷枪对标准节喷涂料,喷涂房出口处人工检查喷涂完成后由输送轨道输送出去,喷涂房连通有大旋风装置将涂料回收,该大旋风装置的风量为 17500立方米/小时;
53.(3)喷涂后的标准节输送至固化房中,输送的同时开启固化房中的热风循环加热使涂料固化,然后输送至冷却工位处停留静置一端时间,待标准节完全冷却后输送至下件区中下件完成涂装,固化房中的温度为180-220℃,固化时间为40-45min,所述冷却时间为35-40min。
54.以上所述仅是本实用新型的优选实施方式,应当指出,对于本技术领域的普通技术人员来说,在不脱离本实用新型原理的前提下,还可以作出若干改进和润饰,这些改进和润饰也应视为本实用新型的保护范围。