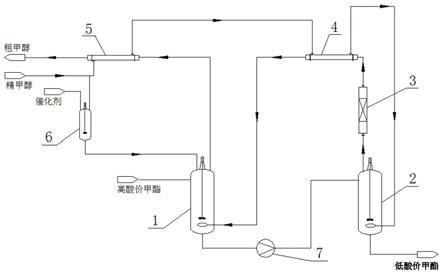
1.本实用新型涉及脂肪酸酯化,如丁酸甘油酯、生物柴油的制备,具体涉及一种有效促进酯化反应的系统。
背景技术:2.脂肪酸与羟基的反应通称为酯化,如脂肪酸与甘油反应生成脂肪酸甘油酯,脂肪酸与醇基反应生成诸如脂肪酸甲酯(俗称生物柴油)、脂肪酸乙酯、丙酯等,在酯化反应过程中同时产生水,当生成的水含量越来越多时,伴随着可逆反应,即反应达到平衡,不仅影响反应效率,而且影响脂肪酯的纯度。为此,如何提高反应效率,提高脂肪酯的纯度是酯化反应关键。
3.目前,普通采用的酯化方法是利用单一的反应釜,在适合的催化剂作用下,脂肪酸中加入过量的羟基物,如甘油、甲醇等以降低水份浓度提高反应效率,这种方法存在加入过量羟基物,需要再精制,造成生产成本上升;同时通过提高温度蒸发去除反应中生成的水份,破坏平衡,促进正向反应,这种方法存在热能消耗大,增加生产成本。而且采用单一釜的生产手段,投资大、操作复杂、热能浪费、生产成本上升。但这两种方法都存在生物柴油是可再生能源,具备良好的环境友好性,可生物降解的特点,与传统的化石柴油相比,由于生物柴油氧含量高而燃烧充分,毒害物排放量低而释放较少颗粒、二氧化碳、硫氧化物、碳氢化合物、烟尘等,因此全世界掀起了研究生物柴油的热潮。
4.如生产三丁酸甘油酯,利用直接酯化法,需要加入2倍的过量丁酸与甘油反应,在高温状态下蒸发水份,促进正向反应,但同时伴随在丁酸一起的水分需要再精馏脱除水份,效率低且热能消耗高。
5.如利用大量的地沟油生产生物柴油普通采用方法有酸碱两步催化法、生物酶催化法、超临界法。其中酸碱两步催化法多采用间歇式生产,投资大,因采用气态甲酯化,热能消耗高。生物酶催化法、超临界法,当粗甲酯酸价很难降低到5mgkoh/g以下。
技术实现要素:6.本实用新型所要解决的技术问题是提供一种有效促进酯化反应的系统,通过该系统能够提高反应效率,降低生产成本。
7.为解决上述技术问题,本实用新型所采取的技术方案是:一种有效促进酯化反应的系统,包括反应釜一、反应釜二、干燥器、换热器一、换热器二、混合罐、输送泵,所述混合罐与反应釜一管道连接,反应釜一通过输送泵与反应釜二管道连接,反应釜二通过干燥器与换热器一管道连接,换热器一还通过另外管道与反应釜二连接;换热器一通过管道与反应釜一连接,换热器一通过管道与换热器二连接,换热器二通过管道与反应釜一连接;催化剂输入管道与混合罐连接,脂肪酸或甘油输入管道与反应釜一连接,丁酸或甲醇输入管道分别与混合罐和换热器二连接,换热器二还与含水丁酸或甲醇输出管道连接,反应釜二与反应釜一通过输送泵进行连接。
8.本实用新型有效促进酯化反应的方法,包括以下步骤:
9.(1).丁酸或甲醇经换热器二、换热器一后进入反应釜二,通过液相丁酸或甲醇与气相丁酸或甲醇换热;
10.(2).向反应釜一中加入甘油或脂肪酸,向混合罐内加入催化剂和丁酸或催化剂和甲醇并进行充分溶解混合;
11.(3).将反应釜一中的甘油或脂肪酸与来源于换热器一的含水丁酸或甲醇,以及来源于混合罐的催化剂混合并反应,进行第一次酯化反应;
12.(4).通过输送泵将反应釜一中的丁酸甘油酯或甲酯泵入反应釜二中,在反应釜二中通过换热器一加入无水丁酸或无水甲醇混合并反应,进行第二次酯化反应;
13.(5).反应釜二反应过程中产生的少量水份随丁酸气体或甲醇气体一起蒸发,通过干燥器中的干燥剂吸收丁酸和水分混合气相中水分或甲醇和水分混合气相中水分,提高丁酸或甲醇的纯度,然后经过换热器一与经过换热器一的无水丁酸或无水甲醇进行换热,然后进入反应釜一;
14.(6).反应釜一反应过程中产生的少量水份随丁酸或甲醇气体一起蒸发,与经过换热器二的无水丁酸或无水甲醇进行换热,冷凝后丁酸或甲醇作为含水丁酸或含水甲醇输出存放备用或再精馏脱水回用;
15.(7). 停止反应,从反应釜二中排出高线纯度的三丁酸甘油酯或生物柴油。
16.所述步骤(2)中,生产三丁酸甘油酯时则催化剂为酸性催化剂,催化剂的加入量为甘油重量的0.1
‑
0.5%,丁酸的加入量与甘油的摩尔比为1.5
‑
2:1;所述步骤(2)和步骤(3)中反应釜一和反应釜二的反应温度均为150
‑
180℃。
17.所述步骤(2)中,生产生物柴油时则催化剂为酸性催化剂,催化剂的加入量为脂肪重量的0.1
‑
0.3%,甲醇的加入量为脂肪酸的15
‑
20%;所述步骤(2)和步骤(3)中反应釜一和反应釜二的反应温度均为80
‑
95℃。
18.本实用新型采用上述技术方案所设计的一种有效促进酯化反应的系统,可通过两级或多级反应釜进行多级反应,丁酸或甲醇与水分混合气体经过干燥剂吸收其中的水分,提高了纯度,有利于下一步提高反应效率;低温液相丁酸或甲醇与高温丁酸或甲醇气相换热节省热能;本实用新型可实现连续化生产,从而实现连续进料、连续反应、连续出料的功能,丁酸甘油酯、生物柴油的制备效果好,成本低,效率高,有效地促进了酯化反应。
附图说明
19.图1表示本实用新型一种有效促进酯化反应的系统结构示意图。
具体实施方式
20.下面结合附图对本实用新型一种有效促进酯化反应的系统作具体说明。
21.本实用新型一种有效促进酯化反应的系统,参见图1(以制备生物柴油为例),包括反应釜一1、反应釜二2、干燥器3、换热器一4、换热器二5、混合罐6、输送泵7,其中,混合罐6与反应釜一1通过相应的管道连接,反应釜一1经过输送泵7与反应釜二2通过相应的管道连接,反应釜二2经过干燥器3与换热器一4通过相应的管道连接,换热器一4还通过另外的管道与反应釜二2连接。换热器一4通过相应的管道与反应釜一1连接,换热器一4通过相应的
管道与换热器二5连接,换热器二5通过相应的管道反应釜一1连接。催化剂输入管道与混合罐6连接,甘油(或脂肪酸)输入管道与反应釜一1连接,丁酸(或甲醇)的输入管道分别与混合罐6和换热器二5连接,换热器二5还与含水丁酸(含水甲醇)输出管道连接。
22.本实用新型有效促进酯化反应的方法实施例1,包括以下步骤:
23.(1).将丁酸经换热器二、换热器一后进入反应釜二,通过液相丁酸与气相丁酸换热;
24.(2).向反应釜一中加入甘油,向混合罐内加入酸性催化剂和丁酸并进行充分溶解混合,酸性催化剂的加入量为甘油重量的0.1%,丁酸的加入量与甘油的摩尔比为1.5:1;
25.(3).将反应釜一中的甘油与来源于换热器一的含水丁酸,以及来源于混合罐的催化剂混合并反应,进行第一次酯化反应;反应釜一的反应温度均为150℃;
26.(4).通过输送泵将反应釜一中的丁酸甘油酯泵入反应釜二中,在反应釜二中通过换热器一加入无水丁酸混合并反应,进行第二次酯化反应,反应釜二的反应温度均为150℃;
27.(5).反应釜二反应过程中产生的少量水份随丁酸气体一起蒸发,通过干燥器中的干燥剂吸收丁酸和水分混合气相中水分,提高丁酸的纯度,然后经过换热器一与经过换热器一的无水丁酸进行换热,然后进入反应釜一;
28.(6).反应釜一反应过程中产生的少量水份随丁酸气体一起蒸发,与经过换热器二的无水丁酸进行换热,冷凝后丁酸作为含水丁酸输出存放备用或再精馏脱水回用;
29.(7). 停止反应,从反应釜二中排出高线纯度的三丁酸甘油酯。
30.本实用新型有效促进酯化反应的方法实施例2,包括以下步骤:
31.(1).将丁酸经换热器二、换热器一后进入反应釜二,通过液相丁酸与气相丁酸换热;
32.(2).向反应釜一中加入甘油,向混合罐内加入酸性催化剂和丁酸并进行充分溶解混合,酸性催化剂的加入量为甘油重量的0.3%,丁酸的加入量与甘油的摩尔比为1.7:1;
33.(3).将反应釜一中的甘油与来源于换热器一的含水丁酸,以及来源于混合罐的催化剂混合并反应,进行第一次酯化反应;反应釜一的反应温度均为165℃;
34.(4).通过输送泵将反应釜一中的丁酸甘油酯泵入反应釜二中,在反应釜二中通过换热器一加入无水丁酸混合并反应,进行第二次酯化反应,反应釜二的反应温度均为165℃;
35.(5).反应釜二反应过程中产生的少量水份随丁酸气体一起蒸发,通过干燥器中的干燥剂吸收丁酸和水分混合气相中水分,提高丁酸的纯度,然后经过换热器一与经过换热器一的无水丁酸进行换热,然后进入反应釜一;
36.(6).反应釜一反应过程中产生的少量水份随丁酸气体一起蒸发,与经过换热器二的无水丁酸进行换热,冷凝后丁酸作为含水丁酸输出存放备用或再精馏脱水回用;
37.(7). 停止反应,从反应釜二中排出高线纯度的三丁酸甘油酯。
38.本实用新型有效促进酯化反应的方法实施例3,包括以下步骤:
39.(1).将丁酸经换热器二、换热器一后进入反应釜二,通过液相丁酸与气相丁酸换热;
40.(2).向反应釜一中加入甘油,向混合罐内加入酸性催化剂和丁酸并进行充分溶解
混合,酸性催化剂的加入量为甘油重量的0.5%,丁酸的加入量与甘油的摩尔比为2:1;
41.(3).将反应釜一中的甘油与来源于换热器一的含水丁酸,以及来源于混合罐的催化剂混合并反应,进行第一次酯化反应;反应釜一的反应温度均为180℃;
42.(4).通过输送泵将反应釜一中的丁酸甘油酯泵入反应釜二中,在反应釜二中通过换热器一加入无水丁酸混合并反应,进行第二次酯化反应,反应釜二的反应温度均为180℃;
43.(5).反应釜二反应过程中产生的少量水份随丁酸气体一起蒸发,通过干燥器中的干燥剂吸收丁酸和水分混合气相中水分,提高丁酸的纯度,然后经过换热器一与经过换热器一的无水丁酸进行换热,然后进入反应釜一;
44.(6).反应釜一反应过程中产生的少量水份随丁酸气体一起蒸发,与经过换热器二的无水丁酸进行换热,冷凝后丁酸作为含水丁酸输出存放备用或再精馏脱水回用;
45.(7). 停止反应,从反应釜二中排出高线纯度的三丁酸甘油酯。
46.本实用新型有效促进酯化反应的方法实施例4,包括以下步骤:
47.(1).将甲醇经换热器二、换热器一后进入反应釜二,通过液相甲醇与气相甲醇换热;
48.(2).向反应釜一中加入脂肪酸,向混合罐内加入酸性催化剂和甲醇并进行充分溶解混合;催化剂的加入量为脂肪重量的0.1%,甲醇的加入量为脂肪酸的15%;
49.(3).将反应釜一中的脂肪酸与来源于换热器一的含水甲醇,以及来源于混合罐的催化剂混合并反应,进行第一次酯化反应,反应釜一的反应温度均为80℃;
50.(4).通过输送泵将反应釜一中的甲酯泵入反应釜二中,在反应釜二中通过换热器一加入无水甲醇混合并反应,进行第二次酯化反应,反应釜一的反应温度均为80℃;
51.(5).反应釜二反应过程中产生的少量水份随甲醇气体一起蒸发,通过干燥器中的干燥剂吸收甲醇和水分混合气相中水分,提高甲醇的纯度,然后经过换热器一与经过换热器一的无水甲醇进行换热,然后进入反应釜一;
52.(6).反应釜一反应过程中产生的少量水份随甲醇气体一起蒸发,与经过换热器二的无水甲醇进行换热,冷凝后甲醇作为含水甲醇输出存放备用或再精馏脱水回用;
53.(7). 停止反应,从反应釜二中排出高线纯度的生物柴油。
54.本实用新型有效促进酯化反应的方法实施例5,包括以下步骤:
55.(1).将甲醇经换热器二、换热器一后进入反应釜二,通过液相甲醇与气相甲醇换热;
56.(2).向反应釜一中加入脂肪酸,向混合罐内加入酸性催化剂和甲醇并进行充分溶解混合;催化剂的加入量为脂肪重量的0.2%,甲醇的加入量为脂肪酸的18%;
57.(3).将反应釜一中的脂肪酸与来源于换热器一的含水甲醇,以及来源于混合罐的催化剂混合并反应,进行第一次酯化反应,反应釜一的反应温度均为87℃;
58.(4).通过输送泵将反应釜一中的甲酯泵入反应釜二中,在反应釜二中通过换热器一加入无水甲醇混合并反应,进行第二次酯化反应,反应釜一的反应温度均为87℃;
59.(5).反应釜二反应过程中产生的少量水份随甲醇气体一起蒸发,通过干燥器中的干燥剂吸收甲醇和水分混合气相中水分,提高甲醇的纯度,然后经过换热器一与经过换热器一的无水甲醇进行换热,然后进入反应釜一;
60.(6).反应釜一反应过程中产生的少量水份随甲醇气体一起蒸发,与经过换热器二的无水甲醇进行换热,冷凝后甲醇作为含水甲醇输出存放备用或再精馏脱水回用;
61.(7). 停止反应,从反应釜二中排出高线纯度的生物柴油。
62.本实用新型有效促进酯化反应的方法实施例6,包括以下步骤:
63.(1).将甲醇经换热器二、换热器一后进入反应釜二,通过液相甲醇与气相甲醇换热;
64.(2).向反应釜一中加入脂肪酸,向混合罐内加入酸性催化剂和甲醇并进行充分溶解混合;催化剂的加入量为脂肪重量的0.3%,甲醇的加入量为脂肪酸的20%;
65.(3).将反应釜一中的脂肪酸与来源于换热器一的含水甲醇,以及来源于混合罐的催化剂混合并反应,进行第一次酯化反应,反应釜一的反应温度均为95℃;
66.(4).通过输送泵将反应釜一中的甲酯泵入反应釜二中,在反应釜二中通过换热器一加入无水甲醇混合并反应,进行第二次酯化反应,反应釜一的反应温度均为95℃;
67.(5).反应釜二反应过程中产生的少量水份随甲醇气体一起蒸发,通过干燥器中的干燥剂吸收甲醇和水分混合气相中水分,提高甲醇的纯度,然后经过换热器一与经过换热器一的无水甲醇进行换热,然后进入反应釜一;
68.(6).反应釜一反应过程中产生的少量水份随甲醇气体一起蒸发,与经过换热器二的无水甲醇进行换热,冷凝后甲醇作为含水甲醇输出存放备用或再精馏脱水回用;
69.(7). 停止反应,从反应釜二中排出高线纯度的生物柴油。
70.本实用新型实施例采用两级反应釜进行反应,当然还可采用更多级反应釜进行多级反应,以进一步有效促进酯化反应,整个过程连续进料、连续反应、连续出料,丁酸甘油酯、生物柴油的制备效果好。