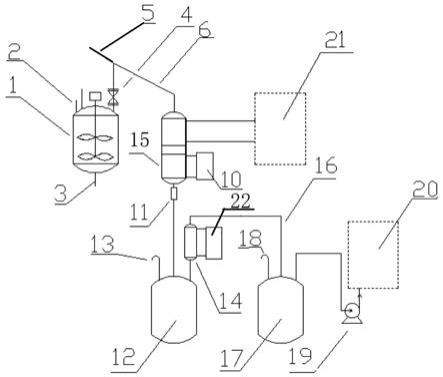
1.本实用新型涉及一种二甲基硅氧烷环体脱低分子防管道结晶系统。
背景技术:2.二甲基硅氧烷环体,是生产硅橡胶、硅油的主要原料,在橡胶填料处理及化妆品上也有广泛应用。用其制备硅橡胶、硅油、及其他聚硅氧烷产品,可以进一步加工成耐高低温、绝缘性能好、耐气候老化、耐臭氧、耐辐射性能更好的多种改良硅橡胶及硅油。
3.二甲基硅氧烷环体在生产、储运过程中不可避免的会引入水分,一般而言,二甲基硅氧烷环体中含有50~200ppm左右的水分,当天气潮湿时,水分含量还会增加,如用此原料直接进行聚合反应,得到的产物会有较多羟基封端聚硅氧烷,影响产品性质,所以聚合前需对其进行加热抽真空脱水处理。
4.二甲基硅氧烷环体d3熔点在75℃,d4熔点在17.5℃,d6熔点在-3℃,而制备硅橡胶、硅油的主要二甲基硅氧烷环体为d4或d4与d3、d5、d6、d7
…
d12的混合物,在冬季气温低于17℃时,按通常脱水系统50~95℃脱出来的低分子可能在冷凝器下部、尾气管道内冷凝并降温至17℃以下结晶,停止脱水后反应釜至冷凝器的水平抽真空管道残留的低分子也会结晶,堵塞真空系统,导致脱水工艺无法正常进行,如果原料脱水、聚合、聚合后物料脱低分子都在同一个釜进行,那么按照脱低环节温度180~190℃,则前部抽真空管道温度会很高,而常用电伴热带耐受温度为105℃以下,不能用来对抽真空管道加热防止结晶,且冷凝器内部管道无法缠绕电伴热带,通常处理办法是使用热水浇淋管道、使用其他釜充氮气升温至一百多摄氏度来暖管,使结晶物料融化,费时费力费能源。另外在通常的脱水系统中,低分子接收罐的抽真空管道无第二冷凝器,会有少量低分子抽到尾气管道结晶,也浪费了原料。再者脱水后若使用釜内氮气吹扫真空管道,釜内蒸汽始终会不断被吹到抽真空管道,无法完全吹扫干净。
技术实现要素:5.为了解决二甲基硅氧烷环体脱低分子系统结晶堵管及尾气中含有原料浪费的问题,主要原理是通过将第一冷凝器的壳程分为三层,上部冷凝层,中部隔热层,下部控温层,可调节温度防低温结晶,冷凝器下部外壳程内通导热油,导热油通过高低温循环一体机打循环;其次在抽真空管道上加入三通,接上氮气,并且将第一冷凝器前水平管道改为坡度管道,靠近冷凝器一侧低,在脱低分子后使用管道内氮气进行吹扫残余低分子,避免使用釜内氮气吹扫带出釜内蒸汽使真空管道内始终有低分子残留结晶;另外低分子接收罐至真空缓冲罐的管道上增加第二冷凝器,使用高低温循环一体机进行控温冷凝,防止有未冷凝的低分子进入尾气处理系统后结晶堵管。
6.二甲基硅氧烷环体脱低分子防管道结晶系统,搅拌釜上接有第一真空管道(带球阀),第一真空管道与坡度管道连接,坡度管道与第一冷凝器连接,第一冷凝器与低分子接收罐连接,低分子接收罐经第二冷凝器与真空缓冲罐连接,真空缓冲罐经真空泵与尾气系
统连接。
7.第一真空管道与坡度管道的连接交汇处设置有三通连接第二氮气管道。
8.所述的第一冷凝器内设置有若干列管,列管间的间隙为第一冷凝器的壳程,所述的壳程自上而下设置有第一列管式冷凝器冷凝层、第一列管式冷凝器隔热层、第一列管式冷凝器控温层,且第一列管式冷凝器冷凝层、第一列管式冷凝器隔热层、第一列管式冷凝器控温层各自隔断不互通。
9.所述的第一冷凝器为第一列管式冷凝器,其中,第一列管式冷凝器冷凝层壳程接入循环水系统,第一列管式冷凝器隔热层壳程内填充隔热材料,第一列管式冷凝器控温层壳程接入循环导热油的高低温循环一体机,第一列管式冷凝器控温层下方通过管道视镜后进入低分子接收罐,接收罐上有放空阀,接收罐上接有第二冷凝器,所述的第二冷凝器为第二列管式冷凝器,第二列管式冷凝器接入循环导热油的高低温循环一体机,第二列管式冷凝器通过管道接入真空缓冲罐,真空缓冲罐上有放空阀,真空缓冲罐通过管道接入真空泵,真空泵后为尾气管道系统。
10.坡度管道的坡度为20-45
°
,且低端与第一冷凝器15连接。
11.第一冷凝器上部设置有循环水系统,该循环水系统与第一列管式冷凝器冷凝层连接;下部设置有第一高低温循环一体机;第二冷凝器上设置有第二高低温循环一体机。
12.搅拌釜上设置有第一氮气管道,底部设置有排料管道。第一冷凝器与低分子接收罐的连接管道上设置有管道视镜。
13.低分子接收罐上设置有第一放空管道;真空缓冲罐上设置有第二放空管道。
14.进一步的,所需脱低分子的二甲基硅氧烷环体是d3、d4、d6以及包含三者中至少一种的混合物。
15.进一步的,搅拌釜和第一列管式冷凝器冷凝层之间无水平管道,使用坡度管道代替水平管道。
16.进一步的,釜上竖直管道与坡度管道交汇处加入三通,另一端连接氮气管道,氮气管道吹扫方向与坡度管道方向一致。
17.进一步的,冷凝层壳程连接循环水系统,可对冷凝层进行降温冷凝,控温层壳程内接入通过高低温循环一体机打循环的导热油,可对控温层壳程内导热油进行升降温,隔热层壳程内为隔热密封材质,防止冷凝层与控温层壳程内介质互流及热交换,另外,冷凝、隔热、控温每种区域不限于只有一个。
18.进一步的,低分子接收罐上接有第二列管式冷凝器,冷凝器接入通过高低温循环一体机打循环的导热油,可对冷凝器进行控温。
19.本实用新型同现有技术相比其优点在于:
20.1.防止脱水系统内各处会结晶堵管的可能,使二甲基硅氧烷环体脱水工艺能够正常进行,节省了处理结晶堵管的时间、人力、能源消耗。
21.2.低分子接收罐的抽真空管道加装第二冷凝器,可进一步冷凝回收原料,同时防止尾气管道结晶。
附图说明
22.图1为本实用新型一种二甲基硅氧烷环体脱低分子防管道结晶系统整体结构示意
图。
23.图2为本实用新型一种二甲基硅氧烷环体脱低分子防管道结晶系统第一冷凝器内部示意图。
24.图中:1、搅拌釜;2、第一氮气管道;3、排料管道;4、第一真空管道;5、第二氮气管道;6、坡度管道;7、第一列管式冷凝器冷凝层;8、第一列管式冷凝器隔热层;9、第一列管式冷凝器控温层;10、第一高低温循环一体机;11、视镜管道;12、低分子接收罐;13、第一放空管道;14、第二冷凝器;15、第一冷凝器;16、第二真空管道;17、真空缓冲罐;18、第二放空管道;19、真空泵;20、尾气系统,21、循环水系统,22、第二高低温循环一体机。
25.第二冷凝器为列管冷凝器,购买自无锡双盛石化装备有限公司。
具体实施方式
26.实施例1
27.二甲基硅氧烷环体脱低分子防管道结晶系统,搅拌釜1上接有第一真空管道4,第一真空管道4与坡度管道6连接,坡度管道6与第一冷凝器15连接,第一冷凝器15与低分子接收罐12连接,低分子接收罐12经第二冷凝器14与真空缓冲罐17连接,真空缓冲罐17经真空泵19与尾气系统20连接。
28.第一真空管道4与坡度管道6的连接交汇处设置有三通连接第二氮气管道5。
29.所述的第一冷凝器15内设置有若干列管,列管间的间隙为第一冷凝器15的壳程,所述的壳程自上而下设置有第一列管式冷凝器冷凝层7、第一列管式冷凝器隔热层8、第一列管式冷凝器控温层9,且第一列管式冷凝器冷凝层7、第一列管式冷凝器隔热层8、第一列管式冷凝器控温层9各自隔断不互通。
30.坡度管道6的坡度为30
°
,且低端与第一冷凝器15连接。
31.第一冷凝器15上部设置有循环水系统21,该循环水系统21与第一列管式冷凝器冷凝层7连接;下部设置有第一高低温循环一体机10;第二冷凝器14上设置有第二高低温循环一体机22。
32.所述的第一冷凝器15为一个圆柱形金属外壁,内部有若干列管从上至下,上下连接有封头,气态脱低分子从上部进入封头,只能通过若干列管到达下部封头,在经过列管时,物料与列管外部和圆筒内部之间的填充介质发生热交换,冷凝流入低分子接收罐。另外,列管外部和圆筒内部之间的空间称为壳程,第一冷凝器壳程总共分上中下三层,三层各自隔断不互通,第一列管式冷凝器冷凝层7为冷凝层,内部填充介质为循环水,并与冷凝器外界循环水系统21连接进行循环;第一列管式冷凝器隔热层8为隔热层,内部填充介质为隔热材质,起到隔绝第一层与第三层温度的作用;第一列管式冷凝器控温层9为控温层,内部填充介质为导热油,与冷凝器外界的第一高低温循环一体机10连接进行循环。
33.搅拌釜1上设置有第一氮气管道2,底部设置有排料管道3。
34.低分子接收罐12上设置有第一放空管道13;真空缓冲罐17上设置有第二放空管道18。
35.实施例2
36.下面结合附图并用最佳的实施例对本实用新型作详细的说明。
37.气温4℃下,将d4原料打入搅拌釜1内,搅拌升温至80℃后,开启真空泵20,打开抽
真空管线所有阀门,开始对物料脱水,启动第一冷凝器15、第二冷凝器14的高低温循环一体机导热油循环,并设定高低温循环一体机导热油温度为25℃,搅拌釜内脱出的低分子经过第一真空管道4、坡度管道6后部分冷凝,及时顺着坡度管道流入冷凝器内,未冷凝的蒸汽经过第一列管式冷凝器冷凝层7,在上部壳程内循环水的作用下大部分冷凝为液体,进一步的通过第一列管式冷凝器隔热层8达到冷凝器的第一列管式冷凝器控温层9,第一列管式冷凝器控温层9壳程内25℃导热油对冷凝后的液体及时控温防止物料温度低于17℃结晶,进一步通过视镜管道11后储存在低分子接收罐12,还剩余少量未冷凝的蒸汽在第二冷凝器14处,壳程内25℃导热油对其进行控温冷凝,回到低分子接收罐12内。待脱低分子完毕后,停止真空泵20,关闭搅拌釜抽第一真空管道4的阀门,打开第二氮气管道5及真空缓冲罐17放空阀,使用氮气对抽真空管道进行吹扫,管道内残留的低分子全部流入低分子接收罐和真空缓冲罐内,关闭第二氮气管道5,整个脱低分子工艺完毕,系统无一处结晶堵管。