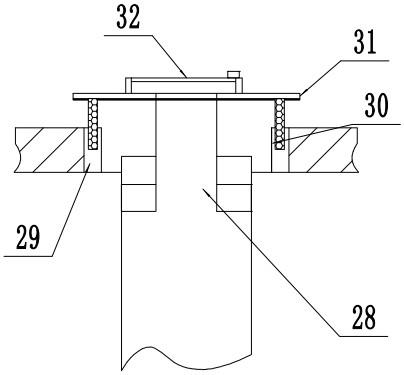
1.本实用新型属于铂金属回收技术领域,尤其涉及含铂废催化剂载体溶解回收设备。
背景技术:2.铂,在现代科技和工业发展进程中也具有及其重要的用途。铂族金属具有优良的催化性能。在化学工业中,尤其在石油化学工业、石油精炼工业、医药及能源工业中,广泛地使用含铂族金属如铂、钯的催化剂,由于铂的稀有以及重要性,一般需要对铂废催化剂中回收提取铂,常见的铂废催化剂回收提取装置,多数都是通过湿法溶解提纯的方式,一般先对铂废催化剂进行酸性溶解,然后进行沉淀析出,但是现有的溶解回收设备铂废催化剂进行处理时,溶解力度有限,沉淀析出速度慢效率低。
技术实现要素:3.本实用新型实施例的目的在于提供含铂废催化剂载体溶解回收设备,旨在解决上述问题。
4.本实用新型是这样实现的,含铂废催化剂载体溶解回收设备包括:壳体,壳体内部环形等间隔设置有多个回收箱,回收箱用于对含铂废催化剂进行溶解沉淀,所述回收箱的内部上侧设置有溶解混合腔,内部下侧设置有沉淀腔,溶解混合腔用于对含铂废催化剂进行溶解,沉淀腔用于对溶解后的含铂废催化剂溶液进行沉淀,壳体中心处设置有一组动力催化箱,动力催化箱底端分别与回收箱内部的溶解混合腔相互连通,用于加快回收箱内部含铂废催化剂溶解的速度以及控制溶解混合腔内部的溶液朝向沉淀腔内部流动,所述溶解混合腔的内顶部设置有搅拌机构,用于进一步提高含铂废催化剂在溶解混合腔内部溶解的速度。
5.有益效果,本实用新型提供的含铂废催化剂载体溶解回收设备,通过在壳体内部设置有多个回收箱,可同时对大量以及不同类型的含铂废催化剂进行回收;通过在回收箱内部设置上侧的溶解混合腔和下侧的沉淀腔,便于对含铂废催化剂进行快速的回收处理;通过向溶解混合腔内部利用压板升降控制酸性溶液进出的方式,便于准确的控制酸性溶液的进出量,以及在设置密封板、升降杆、电动挡板便于控制溶解混合腔内部的溶液转移至沉淀腔内部进行反应,整体提高本设备的回收加工处理的效率。
附图说明
6.图1为含铂废催化剂载体溶解回收设备的结构示意图。
7.图2为含铂废催化剂载体溶解回收设备中自动下料机构的结构示意图。
8.图3为含铂废催化剂载体溶解回收设备中惰性气体箱与动力催化箱的连接结构示意图。
9.附图中:壳体10,回收箱11,动力催化箱12,溶解混合腔13,沉淀腔14,搅拌轴15,搅
拌电机16,隔板17,泵体18,气液混合输送管19,惰性气体箱21,出气口22,封板23,压板25,电动伸缩杆26,自动下料机构27,延伸管28,升降槽29,升降杆30,密封板31,电动挡板32。
具体实施方式
10.为了使本实用新型的目的、技术方案及优点更加清楚明白,以下结合附图及实施例,对本实用新型进行进一步详细说明。应当理解,此处所描述的具体实施例仅仅用以解释本实用新型,并不用于限定本实用新型。
11.以下结合具体实施例对本实用新型的具体实现进行详细描述。
12.如图1所示,为本实用新型实施例提供的含铂废催化剂载体溶解回收设备的结构图,包括:壳体10,壳体10内部环形等间隔设置有多个回收箱11,回收箱11用于对含铂废催化剂进行溶解沉淀,所述回收箱11的内部上侧设置有溶解混合腔13,内部下侧设置有沉淀腔14,溶解混合腔13用于对含铂废催化剂进行溶解,沉淀腔14用于对溶解后的含铂废催化剂溶液进行沉淀,壳体10中心处设置有一组动力催化箱12,动力催化箱12底端分别与回收箱11内部的溶解混合腔13相互连通,用于加快回收箱11内部含铂废催化剂溶解的速度以及控制溶解混合腔13内部的溶液朝向沉淀腔14内部流动,所述溶解混合腔13的内顶部设置有搅拌机构,用于进一步提高含铂废催化剂在溶解混合腔13内部溶解的速度。
13.在本实用新型实施例中,所述回收箱11邻近壳体10内壁的位置通过固定杆固定在壳体10上,同时动力催化箱12的侧壁也通过固定杆安装在回收箱11上,回收箱11内部横向安装有隔板17,用于分隔回收箱11内部,形成上侧的溶解混合腔13和下侧的沉淀腔14,溶解混合腔13与沉淀腔14之间设置有自动下料机构27,利用自动下料机构27实现溶解混合腔13与沉淀腔14之间的连通与闭合,控制溶解混合腔13内部含铂废催化剂溶液朝向沉淀腔14内部流动,所述溶解混合腔13顶部一侧开设有进料口,且沉淀腔14侧壁上设置有泵体18,泵体18用于将沉淀腔14内部铂沉淀析出后的溶液向外排出。
14.在本实用新型的一个实例中,所述搅拌机构包括固定在溶解混合腔13内顶部的搅拌轴15,搅拌轴15的周向侧壁上均匀安装有多个搅拌叶片,搅拌轴15顶端转动连接有固定在回收箱11外顶部的搅拌电机16,启动搅拌电机16驱动搅拌轴15旋转,然后带动搅拌叶片转动对溶解混合腔13内部的含铂废催化剂进行混合溶解。
15.作为本实用新型的一种优选实施例,所述动力催化箱12内部装填有酸性溶液,动力催化箱12底部朝向回收箱11底部分别连通有气液混合输送管19,气液混合输送管19末端穿过回收箱11内部的沉淀腔14向上延伸至自动下料机构27内部,所述动力催化箱12内部升降式连接有压板25,压板25顶端连接有固定在动力催化箱12外顶部的电动伸缩杆26,启动电动伸缩杆26带动压板25向下移动,然后通过压板25对动力催化箱12内部的溶液进行挤压,而后将溶液沿着气液混合输送管19,在气液混合输送管19的顶端涌出,对自动下料机构27施加向上的冲击推力,此时驱动自动下料机构27开启;
16.参阅图2,所述自动下料机构27包括有开设在隔板17中心处的通孔,通孔的顶部升降式连接有密封板31,密封板31底部一圈等间隔连接有多个升降杆30,升降杆30滑动连接在开设在隔板17上的升降槽29中,同时气液混合输送管19的一端内部滑动连接有延伸管28,延伸管28顶部与密封板31底部相互连通,且密封板31顶部设置有用于开合密封板31内部的电动挡板32,通过开启电动挡板32将气液混合输送管19内部的酸性容易沿着延伸管28
通过密封板31中部朝向溶解混合腔13内部输送,然后与溶解混合腔13内部的含铂废催化剂进行混合溶解反应;所述升降杆30底端连接有限位板,防止升降杆30从升降槽29中脱落。在反应一段时间后,需要将溶解混合腔13内部的溶液转移至沉淀腔14内部时,此时关闭电动挡板32,继续控制电动伸缩杆26带动压板25向下对气液混合输送管19内部的溶液进行施压,此时由于电动挡板32的闭合,延伸管28内部的溶液会对密封板31施加直接向上的推力,此时升降杆30在升降槽29内部向上移动,然后溶解混合腔13内部的溶液沿着密封板31底部的通孔流向沉淀腔14内部进行沉淀,此时通过设置升降杆30、密封板31、电动挡板32等结构,在保持向溶解混合腔13内部稳定输入酸性溶液的同时,又可准确的将溶解混合腔13内部溶解后的溶液转移至沉淀腔14中进行反应。
17.参阅图3,作为本实用新型的一种优选实施例,所述动力催化箱12的一侧壁上设置有惰性气体箱21,惰性气体箱21的一端连通有设置在动力催化箱12箱壁中的出气口22,通过出气口22将惰性气体箱21与动力催化箱12相互连通,为了进一步提高溶解混合腔13内部含铂废催化剂的溶解搅拌速度,通过在出气口22的端口出摆动连接有一组封板23,封板23用于控制出气口22内部气体的流出,在压板25向上移动时,会带动动力催化箱12内底部产生向上的吸力,此时封板23会向外摆动,然后惰性气体箱21内部的惰性气体流入到动力催化箱12内部,然后压板25向下移动时封板23受到压力闭合,此时已经输入到动力催化箱12内部的惰性气体会跟随动力催化箱12内部的酸性溶液一同沿着气液混合输送管19输入到溶解混合腔13内部,利用惰性气体的特性提高含铂废催化剂与酸性溶液的混合力度,从而提高溶解速度。
18.本实用新型上述实施例中提供了含铂废催化剂载体溶解回收设备,使用时,首先将待回收的含铂废催化剂置于溶解混合腔13中,然后启动电动伸缩杆26运行带动压板25向下移动,此时动力催化箱12内部在压板25上移时,流入有一部分惰性气体,然后跟随动力催化箱12内部的酸性溶液一同经过气液混合输送管19的输送,进过开启下的电动挡板32输入到溶解混合腔13内部,与含铂废催化剂混合,同时开启搅拌轴15对其进行混合搅拌溶解,在溶解到相应的状态时,通过关闭电动挡板32,此时继续启动电动伸缩杆26带动压板25向下移动,利用气液混合输送管19内部的气液对密封板31产生向上的推力,此时密封板31与隔板17相互分离,然后将溶解混合腔13内部溶解后的溶液输入到沉淀腔14内部进行沉淀析出。
19.以上所述仅为本实用新型的较佳实施例而已,并不用以限制本实用新型,凡在本实用新型的精神和原则之内所作的任何修改、等同替换和改进等,均应包含在本实用新型的保护范围之内。