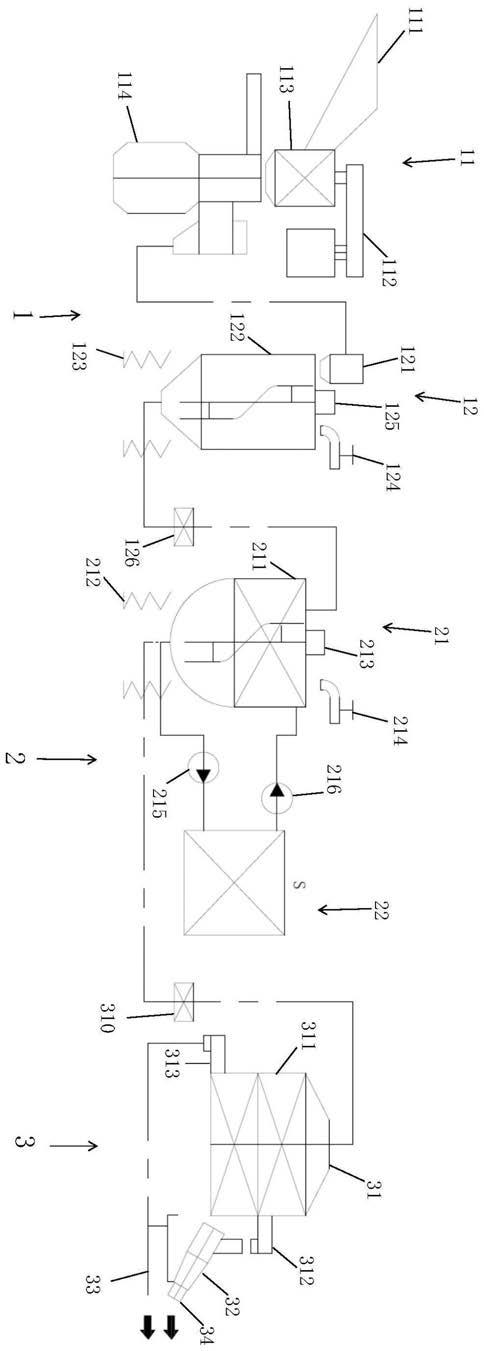
1.本实用新型涉及原料萃取领域,尤其涉及一种高效低温的萃取设备。
背景技术:2.利用超音波将固体颗粒震碎细化,是一项已知的概念,但在早期的超音波粉碎机构中,超声波通过传递装置传递至盛装固体颗粒的容器中,对固体颗粒进行粉碎。传递装置往往是锥状物体,超声波会以锥状物体的顶点为中心向容器四周渐弱。固体颗粒的流动性差,即使搭配搅拌棒也会使远离锥状物体顶点的固体颗粒因接收不到足够强的超声波,而无法被粉碎到所需要的粒径。同时该机构在使用时会持续升温,不得不间歇使用。
3.中国台湾专利“超音波粉碎机构”(公开编号:200600196)公开的超音波粉碎机构是将固体颗粒制成悬浮液,在承载通道中循环流动,在流动过程中利用超音波将固体颗粒多次粉碎,并搭配冷却设备完成萃取。该设备虽然克服了上述问题,但由于该设备要求进料前需将固体原料配置为悬浮液,导致作业成本升高且制程时间长。另一方面该设备在输出产品时经细化后的悬浮液中依然存在细小的固体颗粒,导致产品的纯度不够,还需要进一步加工。
技术实现要素:4.针对现有技术的不足,本实用新型提供了一个可自动化一体化的完成悬浮液配置、萃取及产物的固液分离的萃取设备。
5.上述萃取设备包括:前处理系统,用于粉碎和分散原料,经分散后的原料成为悬浮液;萃取系统,利用超声波进一步粉碎细化所述悬浮液中的固体颗粒;所述萃取系统包括与前处理系统连通的中转区域、与所述中转区域连通的萃取区域;后处理系统,与所述萃取系统的中转区域连通,用于将从所述萃取系统中流出的悬浮液进行固液分离。
6.进一步,所述萃取区域包括萃取本体和可产生超声波的破碎组件;所述萃取本体内设置有中空的承载通道,供所述悬浮液流动,所述破碎组件安装于所述承载通道内并与所述悬浮液接触。
7.进一步,所述承载通道的两端均与所述中转区域连通,所述中转区域可控制所述悬浮液在所述承载通道中以不同的流速循环流动。
8.进一步,所述破碎组件包括超声部、工作部及破碎部;所述工作部的一端与所述超声部连接,所述工作部的另一端朝向所述破碎部,且不与所述破碎部接触。
9.更进一步,所述工作部内部填充了传递介质,且所述工作部的宽度由所述工作部连接所述超声部的一端向远离所述超声部的一端平滑的减小,借此所述工作部可以传递所述超声部发出的超声波,同时提升所述超声波的能量密度,使所述超声波在到达所述破碎部时能量密度最大,利用所述超声波破碎所述悬浮液中的固体颗粒。
10.可选的,所述萃取区域还包括了多个冷却组件,所述冷却组件设置于所述萃取本体上,位于所述承载通道周围,用于冷却所述承载通道内的所述悬浮液。
11.进一步,所述冷却组件设置有冷却水进口、冷却水出口以及连通所述冷却水进口及所述冷却水出口的冷却部,供冷却水在所述冷却组件中循环流动。
12.进一步,所述前处理系统包括挫粉区域和分散区域,所述挫粉区域将原料切碎成较细的粉末后投入到所述分散区域,所述原料在所述分散区域中与纯水混合配制成一定比例的悬浮液。
13.进一步,所述中转区域包括中转桶,以及纯水系统,所述中转桶周围设置了压力传感系统和搅拌系统;经所述前处理系统处理后的所述悬浮液流入到所述中转桶中,再次与纯水混合,进一步配置成所需比例的悬浮液。
14.更进一步,所述后处理系统包括固液分离机和挤渣机,所述挤渣机与所述固液分离机的固体排出口连通;所述固液分离机利用离心的方式将经所述萃取系统处理后的悬浮液进行固液分离,固体通过所述固体排出口进入所述挤渣机,进行再一次机械压榨,挤净残余水分。
15.本实用新型中的萃取设备的优势在于以下几点:
16.(1)本实用新型将固体原料配置成悬浮液的过程,与萃取的过程整合为一连续的生产线,节约了配置悬浮液的人工成本,同时提高了生产效率,缩短了制程时间。
17.(2)本实用新型设计了多个冷却组件,保证了冷却效果,有效的控制了萃取时悬浮液的温度,有利于原料中活性成分保持稳定,同时降低了连续生产的高温风险。
18.(3)本实用新型设计了固液分离装置,可将经超声波震荡过后的萃取液通过离心进行固液分离,固体还会经过二次压榨,从而提高产品的纯度,提高产出率。
附图说明
19.图1为本实用新型的示意图。
20.图2为本实用新型的萃取区域的局部示意图。
具体实施方式
21.以下配合图式及本实用新型的较佳实施例,进一步阐述本实用新型为达成预定实用新型目的所采取的技术手段。
22.如图1所示,本实用新型所述的萃取设备包括前处理系统1、萃取系统2、后处理系统3以及控制系统。前处理系统1用于将原料分散成悬浮液。萃取系统2包括了中转区域21和与中转区域21连通的萃取区域22:中转区域21与前处理系统1连通,将经前处理系统1处理后的悬浮液输送到萃取区域22中;萃取区域22利用超声波对悬浮液中的固体颗粒进一步进行细化,并将细化后的悬浮液再次输送至中转区域21中。后处理系统3与中转区域21连通,经进一步细化后的悬浮液通过中转区域21流入后处理系统3中,在后处理系统3中进行固液分离最终完成萃取。前处理系统1、萃取系统2以及后处理系统3均受控制系统控制,全自动一体化的完成萃取工艺。
23.进一步地,如图1所示,前处理系统1包括挫粉区域11和分散区域12。
24.挫粉区域11包括加料斗111、挫粉机112、料仓113以及粉碎机114。
25.加料斗111设置在料仓113的上方,供加入欲加工的原物料,挫粉机112 的旋转切刀伸入料仓113的内部,料仓113与粉碎机114连通,粉碎机114中设置有刀片,用于将原料进
一步研磨细化成粉末状态。
26.分散区域12包括真空输送系统121、储液桶122、压力传感系统123、纯水系统124、搅拌器125以及固液输送泵126。真空输送系统121的一端连通粉碎机114,另一端连通储液桶122,可将欲加工的原料粉末从粉碎机114中抽吸至储液桶122中。压力传感系统123置于储液桶122的底部,监控储液桶122中固液的重量。纯水系统124设置于储液桶122的上方,可向储液桶122中注入纯水。搅拌器125伸入到储液桶122内部,用以搅拌储液桶122中的悬浮液。固液输送泵126一端连通储液桶122,另一端连通中转区域21,可将悬浮液输送至中转区域21中。
27.如图1所示,中转区域21包括了中转桶211、压力传感系统212、搅拌器 213、纯水系统214、循环输入泵215以及循环输出泵216。中转区域21的中转桶211与通过固液输送泵126与分散区域12的储液桶122连通,中转桶211接收经前处理系统1处理过的悬浮液;压力传感系统212设置于中转桶211的底部,用于监控中转桶211内物料的重量;搅拌器213伸入中转桶211的内部,用于搅拌中转桶211中的物料;纯水系统214设置于中转桶211的上方,用以向中转桶211中注入纯水;循环输入泵215、循环输出泵216将中转桶211与萃取区域22连通,其中循环输入泵215可将中转桶211中的悬浮液输送至萃取区域22中,而循环输出泵216可将萃取区域22中的悬浮液输送回中转桶211中。
28.结合图2所示,萃取区域22包括了萃取本体220、可产生超声波的破碎组件,以及中空的承载通道221。承载通道221设置于所述萃取本体220内部,供悬浮液流动,承载通道221的一端连通循环输入泵215,另一端连通循环输出泵 216,可使悬浮液在中转桶211与承载通道221内循环流动;承载通道221设置有两个相对应的开口2210用以安装破碎组件,破碎组件可将开口2210完全密封。
29.如图2所示,破碎组件包括可以发出超声波的超声部222、可传递并集中超声波能量的工作部223、以及破碎部224。超声部222安装于萃取本体220上,通过连接机构231固定在萃取本体220上,工作部223的一端连接于超声部222,另一端通过其中一个开口2210延伸至承载通道221内并与悬浮液接触;破碎部 224安装于另一个开口2210处,并通过连接机构231固定于萃取本体220上,破碎部224的顶端伸入承载通道221内并与悬浮液接触,但不与工作部223接触。在本实施例中连接机构231为螺钉连接,但不以此为限。破碎组件与萃取本体220之间的空隙通过密封圈232加以密封,以达到密封承载通道221的开口2210的目的。
30.工作部223内部填充有超声波传递介质,用以传递超声波,在本实施例中该传递介质为纯水,但并不以此为限。工作部223的宽度由接近超声部222的一端向远离超声部223的一端平滑减小,并在远离超声部223的一端形成某一特定形状的凸起,借此可以使工作部223在传递超声波的同时,逐渐提高超声波的能量密度,进而在超声波到达破碎部224顶端时,超声波的能量密度最大,借此利用超声波在破碎部224处粉碎细化固体颗粒。需特别说明的是,工作部 223的形状需要跟材质相配合,在本实施例中工作部223的材质为不锈钢,其形状可以设计成平滑的喇叭锥状。若选用压电材料作为工作部223的材料时,工作部223必须相对应的设置成一圆球状。
31.此外,在本实施例的萃取本体220上,还设置有多个冷却组件,冷却组件设置于承载通道周围。冷却组件包括冷却水进口225、冷却水出口226以及连通冷却水进口225和冷却水出口226的冷却部。如图2所示,冷却部被设计为萃取本体220内的通过机加工开出的冷却
水管道227。在此基础上,冷却部的另一种设计形式为冷却水套228;如图2所示,冷却水套228可套设于承载通道221 的外壁,冷却水套228可根据需要选配。冷却水会不断的从冷却水进口225进入冷却部中并对承载通道221中的悬浮液进行冷却,再通过冷却水出口226排出。借此可保证固体颗粒在受到到超声波震荡作用时,承载通道221内的温度也不会升高,保证了原料的化学性质稳定。
32.如图1所示,后处理系统3包括固液分离机31、挤渣机32、液体管道33 及固体管道34。固液分离机31设置有离心桶311,离心桶311通过固液输送泵 310与中转桶211连通。离心桶311上设置有固体出口312以及液体出口313,并在液体出口313处设置有细网(图中未示出),用于过滤悬浮液中的固体颗粒。挤渣机32的一端与固体排出口312连通,由固体排出口312排出的固体颗粒会进入挤渣机32进一步榨干残余水分。液体管道33与液体出口313及挤渣机32 连通,固体管道34与挤渣机32连通。
33.本实施例中的萃取设备在工作时,操作人员通过前处理系统1中的加料斗 111将固体原物料投入到料仓113中,操作人员通过控制系统运行萃取设备。控制系统控制挫粉机112工作,将固体原料打碎,被打碎的固体原料被输送至粉碎机114中进一步细化。经过细化后的原料被真空输送系统121抽吸到储液桶 122中,当压力传感器123测得的固体原料的质量到达一预定范围内时,控制系统发出停止抽吸的命令,并控制纯水系统124向储液桶122中注入纯水,同时控制系统开启搅拌装器125进行搅拌制成悬浮液。当压力传感器123测得悬浮液的质量到达另一预定范围内时,控制系统发出停止注水的指令。接着,控制系统控制固液输送泵126,将制成的悬浮液输送至萃取系统2中的中转桶211中。
34.在悬浮液进入中转桶211之后,控制系统控制中转区域21中的纯水系统 214、压力传感器212以及搅拌器213,将悬浮液再次配置成预萃取液。配置完成后,控制系统控制循环输入泵215和循环输出泵216将预萃取液输送至萃取区域22,并在萃取区域22和中转区域21中持续循环。在循环过程中,控制系统开启萃取区域22中的超声部222,另其发出超声波,再由工作部223将超声波的能量集中传递至破碎部224,使得超声波在到达破碎部224时能量密度最大,预萃取液在承载通道221中流动,并多次通过破碎部224,从而多次受到超声波的作用被震荡细化。另一方面,在循环过程中,控制系统会同时开启冷却水进口225及冷却水出口226,另冷却水持续流动为承载通道221降温。当到达预定的时间后,控制系统会关闭循环输入泵215,利用循环输出泵216将萃取区域 22中的经过细化的细化萃取液全部输送至中转桶211中。
35.输送完成后,控制系统会控制固液输送泵310将中转桶211中的细化萃取液输送至后处理系统3中的离心桶311中进行后处理。离心桶311通过高速离心,将细化萃取液中的液体通过液体出口313输出至液体管道33中,将细化萃取液中的固体通过固体出口312排入挤渣机32中。挤渣机32将细化萃取液中的固体再次压榨,其中的残余水分排入液体管道33中与萃取液中的液体混形成萃取液体,共同通过液体管道33流出。挤渣机中的固体成为萃取固体通过固体管道34流出。
36.利用本实施例中的萃取设备,可以将平均粒径为3至5μm的蚌壳珍珠屑颗粒在2至3小时内,粉碎为平均粒径为0.1至0.5μm的粉体。
37.本实用新型中的萃取设备的优势在于以下几点:
38.(1)本实用新型将固体原料配置成悬浮液的过程,与萃取的过程整合为一连续的
生产线,节约了配置悬浮液的人工成本,同时提高了生产效率,缩短了制程时间。
39.(2)本实用新型设计了多个冷却组件,保证了冷却效果,有效的控制了萃取时悬浮液的温度,有利于原料中活性成分保持稳定,同时降低了连续生产的高温风险。
40.(3)本实用新型设计了固液分离装置,可将经超声波震荡过后的萃取液通过离心进行固液分离,固体还会经过二次压榨,以提高产品的纯度,提高产出率。
41.以上所述仅是本实用新型的优选实施例而已,并非对本实用新型做任何形式上的限制,虽然本实用新型已以优选实施例揭露如上,然而并非用以限定本实用新型,任何熟悉本专业的技术人员,在不脱离本实用新型技术方案的范围内,当可利用上述揭示的技术内容作出些许更动或修饰为等同变化的等效实施例,但凡是未脱离本实用新型技术方案的内容,依据本实用新型的技术实质对以上实施例所作的任何简单修改、等同变化与修饰,均仍属于本实用新型技术方案的范围内。