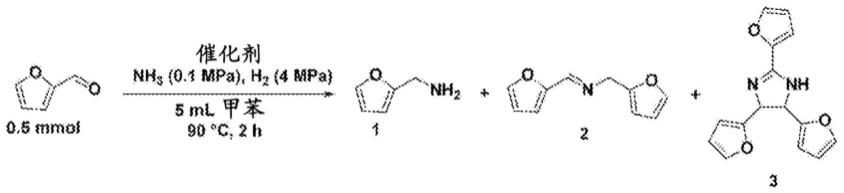
1.本发明涉及一种新型的催化剂。本发明的催化剂可以在低温、低氢气压下有效地促进还原性氨基化反应。
背景技术:2.还原性氨基化(reductive amination)反应通过使羰基化合物与氮源在还原剂存在下发生反应,从而可以进行氮源的烷基化,合成作为合成中间体被在多个领域中通用的胺类。尤其是使用氢分子作为还原剂的还原性氨基化,因其共生物仅有水、环境协调性上优异且反应控制容易,所以被利用于胺合成。
3.作为至今使用氢气作为还原剂的还原性氨基化反应的催化剂,主要使用以钌和铑为代表的贵金属催化剂。从元素战略的观点出发,虽然进行了以非贵金属作为催化剂的研究,但已报导的催化剂需要高温
·
高压。另外,在糠醛和氨的还原性氨基化反应中,现有的非均相系贵金属催化剂rh/al2o3和ru/nb2o5需要80~90℃、氢压为2~4mpa(非专利文献1和2)。
4.最近,作为非贵金属的钴作为还原性氨基化反应的催化剂受到瞩目。例如,专利文献1中公开了使用以金属钴为活性构成要素,以活性炭为载体的催化剂,由异佛尔酮腈合成异佛尔酮二胺的方法。另外,专利文献1中还公开了作为以该活性炭为载体的催化剂的比较例,替代活性炭以cao、al2o3、sio2、tio2等氧化物为载体的催化剂(段落[0056])。以活性炭为载体的催化剂是在氮气氛下烧结制作的(段落[0040]),而相对于此,以氧化物为载体的催化剂是在空气气氛下烧结制作的(段落[0052])。使用任何催化剂的情况下,均是在80℃这样的比较高的温度、8mpa这样的高氢气分压下进行合成反应(段落[0042]和[0047])。
[0005]
现有技术文献
[0006]
专利文献
[0007]
专利文献1:中国专利申请公开第108686660号说明书
[0008]
非专利文献
[0009]
非专利文献1:kawanami et al.green chem.2016,18,487.
[0010]
非专利文献2:hara et al.j.am.chem.soc.2017,139,11493.
技术实现要素:[0011]
发明要解决的课题
[0012]
如以上那样,以往的还原性氨基化反应需要在高温、高氢气压下进行。但是,高温、高氢气压下的反应需要耐热性、耐压性的设备,在经济上和安全面上不理想。本发明是在这样的背景之下完成的,其目的在于提供可在低温、低氢气压(50℃、0.5mpa左右)下进行还原性氨基化反应的方法。
[0013]
用于解决课题的方案
[0014]
本发明人为了解决上述课题,精心研究的结果发现:将钴担载于氧化物上而得的
催化剂在低温、低氢气压下能够有效地促进还原性氨基化反应,以致完成了本发明。
[0015]
即,本发明提供〔1〕~〔15〕。
[0016]
〔1〕一种催化剂,是将钴担载于氧化物上而得的催化剂,其特征在于,通过包含以下的工序(1)~(4)的方法来制造,
[0017]
(1)将含有钴离子的盐和氧化物在水中混合的工序,
[0018]
(2)从由工序(1)得到的混合液中蒸馏除去水,并将得到的固形物干燥的工序,
[0019]
(3)将由工序(2)得到的干燥物在氮气流下进行烧结的工序,
[0020]
(4)将由工序(3)得到的烧结物在氢气流下进行还原的工序。
[0021]
〔2〕根据〔1〕所述的催化剂,其特征在于,被担载于氧化物上的钴的表面中的金属钴的存在率为50%以上。
[0022]
〔3〕根据〔1〕或〔2〕所述的催化剂,其特征在于,催化剂表面中的钴的原子数相对于钴和被氧化元素的原子数的比例为4%以下。
[0023]
〔4〕根据〔1〕~〔3〕中任一项所述的催化剂,其特征在于,被用于还原性氨基化反应。
[0024]
〔5〕根据〔1〕~〔4〕中任一项所述的催化剂,其特征在于,氧化物为sio2、zro2、nb2o5、tio2、al2o3、ceo2、或mgo。
[0025]
〔6〕根据〔1〕~〔4〕中任一项所述的催化剂,其特征在于,氧化物为sio2。
[0026]
〔7〕根据〔1〕~〔4〕中任一项所述的催化剂,其特征在于,工序(1)中使用的氧化物为sio2,且该sio2的表面硅烷醇基量为4mmol/g以下。
[0027]
〔8〕根据〔1〕~〔4〕中任一项所述的催化剂,其特征在于,工序(1)中使用的氧化物为sio2,且该sio2的表面积为100m2g-1
以上。
[0028]
〔9〕根据〔1〕~〔4〕中任一项所述的催化剂,其特征在于,工序(1)中使用的氧化物为sio2,该sio2的表面硅烷醇基量为4mmol/g以下,且该sio2的表面积为100m2g-1
以上。
[0029]
〔10〕根据〔1〕~〔4〕中任一项所述的催化剂,其特征在于,工序(1)中使用的氧化物为sio2,且该sio2是被加热处理过的sio2。
[0030]
〔11〕根据〔10〕所述的催化剂,其特征在于,加热处理为350~480℃、进行3~8小时的加热处理。
[0031]
〔12〕一种胺的制造方法,其特征在于,包含在〔1〕~〔11〕中任一项所述的催化剂和还原剂的存在下,由通式(i)所示的羰基化合物得到通式(ii)所示的胺的工序。
[0032][0033]
〔式中,r1和r2相同或者不同地表示氢原子、可以具有取代基的芳基、或可以具有取代基的烷基。其中,r1和r2可以相互键合形成环。〕
[0034][0035]
〔式中,r1和r2与上述相同含义。〕
[0036]
〔13〕根据〔12〕所述的胺的制造方法,其特征在于,还原剂为氢分子。
[0037]
〔14〕根据〔13〕所述的胺的制造方法,其特征在于,由通式(i)所示的羰基化合物得到通式(ii)所示的胺的工序在100℃以下的温度下、1.0mpa以下的氢气压下进行。
[0038]
〔15〕根据〔14〕所述的胺的制造方法,其特征在于,通式(i)所示的羰基化合物为糠醛,通式(ii)所示的胺为糠基胺。
[0039]
本说明书包含记载于本技术的优先权的基础即日本国专利申请特愿2020-036868的说明书和/或附图中的内容。
[0040]
发明效果
[0041]
本发明提供新型的催化剂。本发明的催化剂可以在低温、低氢气压下有效地促进还原性氨基化反应。
附图说明
[0042]
图1是co/sio2催化剂的再利用性的研究结果。
[0043]
图2是反应前(左)和4次再利用后(右)的co/sio2催化剂的电子显微镜照片。
[0044]
图3是co/sio2催化剂的xrd图案。改变了还原温度。
[0045]
图4是co/sio2和coo/sio2的xps图谱。
具体实施方式
[0046]
以下对本发明进行详细说明。
[0047]
(a)催化剂
[0048]
本发明的催化剂是将钴担载于氧化物上而得的催化剂,其特征在于,其是通过包含下述的工序(1)~(4)的方法制造的催化剂。
[0049]
工序(1)中,将含有钴离子的盐和氧化物在水中混合。
[0050]
作为含有钴离子的盐没有特别限定,例如可以使用硝酸钴、氯化钴、硫酸钴等。
[0051]
作为氧化物也没有特别地限定,可以是金属氧化物,也可以是非金属氧化物。具体而言,可列举出sio2、zro2、nb2o5、tio2、al2o3、ceo2、mgo等。氧化物优选是难以与钴形成复合氧化物的氧化物,从这样的观点考虑,优选sio2。
[0052]
此处作为原料使用的sio2优选是表面硅烷醇基量少的。这是因为sio2表面的硅烷醇基与钴发生反应并生成氧化钴,如果表面硅烷醇基量多,则担载于sio2上的钴中的金属钴(co0)的比率降低,且催化活性下降。具体而言,优选表面硅烷醇基量为4mmol/g以下,更优选为3.5mmol/g以下,进一步优选为3mmol/g以下。
[0053]
另外,作为原料使用的sio2优选表面积大的。这是因为若表面积小,则催化活性下降。具体而言,优选表面积为100m2g-1
以上,更优选为110m2g-1
以上,进一步优选为120m2g-1
以上。
[0054]
表面硅烷醇基量少且表面积大的sio2可以通过加热处理sio2来获得。该加热处理中的温度优选为400℃左右。更具体地说,优选为300~480℃,更优选为350~450℃。加热处理中的加热时间优选为5小时左右。更具体地说,优选为3~8小时,更优选为4~6小时。
[0055]
作为含有钴离子的盐和氧化物的混合比,没有特别限定,钴相对于氧化物的比率优选为20wt%左右,可以设为例如5~50wt%、10~30wt%、或15~25wt%。
56.工序(2)中,从由工序(1)得到的混合液中蒸馏除去水,并将得到的固形物干燥。
[0057]
水的蒸馏除去可以按照常规方法进行,可以使用例如旋转蒸发器进行。干燥也可以按照常规方法进行,例如可以通过在减压下加热进行。
[0058]
工序(3)中,将由工序(2)得到的干燥物在氮气流下进行烧结。
[0059]
作为烧结时的温度没有特别限定,可以设为例如200~600℃、300~500℃、或350~450℃。烧结时间也没有特别限定,可以设为例如0.5~4小时、1~3小时、或1.5~2.5小时。
[0060]
工序(4)中,将由工序(3)得到的烧结物在氢气流下进行还原。
[0061]
氢气流下的还原在高温条件下进行。高温条件只要是能够还原氧化钴,而将其变为金属钴的温度即可,可以设为例如400~800℃、500~700℃、或550~650℃。进行还原的时间也没有特别限定,可以设为例如0.5~4小时、1~3小时、或1.5~2.5小时。
[0062]
予以说明,如上所述,在本说明书中,对于称为“催化剂”的“物质”通过制造方法特定而不是通过结构和特性,这是因为担载于氧化物上的钴的结构和特性极其复杂,实施特定这些的操作需要付出明显过大的经济支出和时间。
[0063]
在本发明的催化剂中,担载于氧化物上的钴含有大量金属钴(co0)。本发明的催化剂即便在低温、低氢气压下也显示高活性,认为大量含有金属钴是该理由之一。“大量含有金属钴的钴”是指例如担载于氧化物上的钴的表面中的金属钴的存在率为50%以上、优选为60%以上的钴。此处,金属钴的存在率由x射线光电子能谱(xps)估算。催化剂中的钴,除了金属钴(co0)之外还包含氧化钴(co
2+
)。由于金属钴与氧化钴在xps光谱仪和x射线衍射(xrd)图案中被检测出不同的峰,所以也可以通过这些峰定义“大量含有金属钴的钴”。例如如图4所示,在xps光谱中,金属钴在60ev(或59ev)附近被检测出峰,氧化钴(ii)在62ev附近被检测出峰,因此,可以将在60ev(或59ev)附近被检测出峰而在62ev附近没有被检测出峰的钴定义为“含有大量金属钴的钴”。另外,如图3所示,在金属钴的标准xrd图案即00-015-0806中,在45
°
附近、53
°
附近、76
°
附近被检测出峰,在氧化钴(ii)的标准xrd图案即00-048-1719中,在36
°
附近、43
°
附近、62
°
附近被检测出峰。因此,也可以将在xrd图案中在45
°
附近、53
°
附近、76
°
附近被检测出峰的钴或在45
°
附近、53
°
附近、76
°
附近被检测出峰而在36
°
附近、43
°
附近、62
°
附近没有被检测出峰的钴定义为“大量含有金属钴的钴”。
[0064]
催化剂表面上的钴的原子数少也被认为是本发明的催化剂在低温、低氢气压下显示高活性的一个理由。在此,“催化剂表面上的钴的原子数少”是指例如催化剂表面上的钴的原子数相对于钴和被氧化元素的原子数的比例为4%以下、3%以下、或2%以下。予以说明,所谓“被氧化元素”是指氧化物中被氧化了的元素(例如二氧化硅中的硅)。
[0065]
本发明的催化剂主要用于还原性氨基化反应,但也可以用于其他的反应。
[0066]
(b)胺的制造方法
[0067]
本发明的胺的制造方法是使用上述的本发明的催化剂,并通过还原性氨基化反应来制造胺的方法。更具体地说是一种胺的制造方法,其特征在于,包含在本发明的催化剂和还原剂的存在下,由通式(i)所示的羰基化合物得到通式(ii)所示的胺的工序。
[0068][0069]
〔式中,r1和r2相同或不同,表示氢原子、可以具有取代基的芳基、或可以具有取代基的烷基。其中,r1和r2可以相互键合形成环。〕
[0070]
[0071]
〔式中,r1和r2与上述含义相同。〕
[0072]
本发明中“芳基”是例如苯基、萘-1-基、萘-2-基、吡啶基(吡啶-2-基、吡啶-3-基、吡啶-4-基)、嘧啶基(嘧啶-2-基、嘧啶-4-基、嘧啶-5-基)、呋喃基(呋喃-2-基、呋喃-3-基)、噻吩基(噻吩-2-基、噻吩-3-基)、吡咯基(吡咯-2-基、吡咯-3-基)等。
[0073]
本发明中“烷基”是例如甲基、乙基、正丙基、异丙基、正丁基、异丁基、仲丁基、叔丁基、正戊基等。
[0074]
本发明中“可以具有取代基的芳基”和“可以具有取代基的烷基”中的“取代基”是例如甲基、乙基、甲氧基、乙氧基、氟原子、氯原子、溴原子、碘原子、三氟甲基、羟甲基等。
[0075]
通式(i)和通式(ii)中的r1和r2只要是氢原子、可以具有取代基的芳基、或可以具有取代基的烷基即可,优选一者是氢原子另一者是可以具有取代基的芳基,更优选一者是氢原子,另一者是可以具有取代基的苯基或可以具有取代基的呋喃基,进一步优选一者是氢原子另一者是呋喃基。
[0076]
通式(i)和通式(ii)中r1和r2可以相互键合,形成环己烷等环。
[0077]
作为优选的通式(i)所示的羰基化合物,可列举出糠醛,作为优选的通式(ii)所示的胺,可列举出糠基胺。
[0078]
作为还原剂,可以是在还原性氨基化反应通常使用的还原剂,优选使用氢分子的还原剂。
[0079]
使用的催化剂的量没有特别限定。相对于通式(i)所示的羰基化合物1mmol,可使用例如20~60mg、或30~50mg。
[0080]
由通式(i)所示的羰基化合物得到通式(ii)所示的胺的工序优选在低温、低氢气压下进行。例如温度可以设为100℃以下、90℃以下、80℃以下、70℃以下、或60℃以下。氢气压可以设为1.0mpa以下、0.9mpa以下、0.8mpa以下、0.7mpa以下、或0.6mpa以下。
[0081]
实施例
[0082]
以下通过实施例对本发明进行更详细说明,本发明并不限定于该实施例。
[0083]
〔实施例1〕
[0084]
(a)材料和方法
[0085]
(1)试剂
[0086]
硝酸钴六水合物购自关东化学。sio2(cariact q-10)由富士
シリシア
提供,mgo由宇部兴产提供,tio2(st-01)由石原产业提供。zro2(jrc-zro-6)、al2o3(jrc-alo-9)、ceo2(jrc-ceo-5)使用催化学会的参考催化剂。nb2o5通过将含水铌酸(由companhia brasileira de metalurgia e mineracao提供)在空气下于400℃烧结而制备。予以说明,测定sio2(cariact q-10)的表面硅烷醇基量,结果为3mmol/g。
[0087]
(2)20wt%担载钴催化剂的制备法
[0088]
将硝酸钴六水合物(1.23g)和载体(1g)分散于50ml的蒸馏水中,在室温下搅拌1小时。利用旋转蒸发器将水蒸馏除去之后,在减压下(~0.25kpa)进行加热干燥(100℃)。将干燥粉末在氮气流中下于400℃烧结2小时,得到前驱物。将前驱物在600℃下进行2小时的氢气还原(30ml/min),从而制备担载钴催化剂。氢气还原后,在不爆露于空气中的情况下转移到手套箱中,用于催化反应。
[0089]
(3)还原性氨基化反应
[0090]
在手套箱内,向特氟隆制内筒中量取担载钴催化剂20mg,加入糠醛0.5mmol、甲苯5ml。将装有反应溶液的内筒放置到不锈钢制高压釜中。将高压釜从手套箱中取出,用氨置换3次后加压0.1mpa。从其上方以全压达0.5mpa的方式导入氢气。将高压釜在50℃加热搅拌。反应后,放冷至室温之后除去压力。然后,向反应溶液中加入作为内标的单氯苯,利用气相色谱确定转化率和收率。
[0091]
(4)再利用实验
[0092]
还原性氨基化反应用上述的方法进行。反应后,将高压釜放入手套箱并解除压力。利用磁铁回收催化剂,用甲苯洗涤。向反应溶液中加入作为内标的单氯苯,利用气相色谱确定转化率和收率。回收得到的钴催化剂同样地进行了还原性氨基化反应。
[0093]
(b)结果
[0094]
(1)载体效应
[0095]
制备载体不同的担载钴催化剂,进行糠醛的还原性氨基化反应,对载体对催化活性的影响进行研究(表1)。以sio2作为载体的催化剂,以收率74%得到作为目标的糠基胺(1)(方案1)。另一方面,其他的载体,没有得到目标产物,而是仅得到中间体亚糠基糠基胺(2)、或者副产物3倍体(3)(方案2-7)。
[0096]
表1
[0097]
载体效应
[0098][0099][0100]
(2)钴担载量的影响
[0101]
固定sio2作为载体,制备钴担载量不同的催化剂。以钴量相同的方式调整催化剂
量,在比载体效应的研究更温和的条件下进行了还原性氨基化反应(表2)。80wt%的催化剂时,催化剂量过少量取困难,因此固定于20mg进行研究。根据钴担载量不同而催化活性大大不同,担载5wt%的催化剂时,没发现目标生成物,相对于此,通过增加担载量而发现催化活性提高,在担载20wt%的催化剂时,大致定量地进行了反应。如果使担载量提升至80wt%,则观察到催化活性的降低。
[0102]
表2
[0103]
担载量效应
[0104][0105][0106]
(3)溶剂效应
[0107]
使用20wt%的担载钴催化剂作为催化剂进行溶剂研究(表3)。使用甲醇的情况下,以比甲苯更高的收率得到糠基胺(方案3)。然而,反应溶液的颜色成为粉色,因此有钴类浸出的风险。因此进行反应后溶液的icp-aes测定,结果可知担载量为1.2%的钴类溶于反应溶液。另外以环己烷作为溶剂进行研究,结果作为副产物生成二糠基胺(方案6)。由以上的结果,考虑收率和选择性,确定甲苯为最佳溶剂。可知以甲苯为溶剂的反应,反应速度虽然降低,但通过延长反应时间而以高收率获取糠基胺(方案2)。
[0108]
表3
[0109]
溶剂效应
[0110]
[0111][0112]a反应时间10h
[0113]
(4)再利用研究
[0114]
最佳化的条件中,进行了co/sio2催化剂的再利用性的研究。在第4次再利用时能看到若干的收率降低(图1)。用电子显微镜观察反应前后的催化剂,结果没看出在反应前后钴粒径上有较大的差别(图2)。因此,认为并不是碳质吸附的原因。
[0115]
(5)基质一般性的研究
[0116]
在最佳化的条件(50℃,氢气压0.5mpa、氨压0.1mpa、反应时间15h、甲苯5ml、20wt%co/sio
2 20mg、基质0.5mmol)下尝试各种羰基化合物的还原性氨基化反应(表4)。可知苯甲醛衍生物几乎不受甲酰基周围的立体的影响。在供电子基时有效地进行反应,相对于此,在吸电子基时需要长时间的反应。即便是具有溴基或吡咯等杂芳香环的基质也没有问题地进行。本催化剂系也可以应用于脂肪族酮或来自生物质的化合物。
[0117]
表4
[0118]
羰基化合物的还原性氨基化反应
[0119][0120]a反应时间25小时,b氢气压0.2mpac以环己烷使用于反应溶剂
[0121]
(5)与贵金属催化剂的比较
[0122]
使用已经报导的贵金属催化剂ru/nb2o5(hara et al.j.am.chem.soc.2017,139,11493.)和rh/al2o3(kawanami et al.green chem.2016,18,487.),在co/sio2催化剂的最佳条件下尝试还原性氨基化反应。对于金属担载量,调制文献中最佳担载量的催化剂进行了研究(表5)。其结果可知:任一催化剂与co/sio2催化剂相比,都是低活性。
[0123]
表5
[0124]
与贵金属催化剂的比较
[0125][0126][0127]
(6)表征
[0128]
使催化剂制备中的还原温度发生变化并测定了xrd(图3)。可知还原前为co3o4的状态,但通过200℃还原而被还原为coo。随着还原温度上升,来自金属钴的峰变大,自500℃起来自coo的峰几乎变得看不到。
[0129]
(7)co和si的表面原子浓度
[0130]
专利文献1所述的co/sio2催化剂,通过在空气气氛下烧结而制作(段落[0052])。相对于此,本发明的co/sio2催化剂通过在氮气流下烧结而制作。
[0131]
认为活性的不同体现在表面的co与si的比。因此,利用x射线光电子能谱法(xps)求出专利文献1记载的co/sio2催化剂(在空气气氛下烧结)与本发明的co/sio2催化剂(在氮气流下烧结)的co和si的表面原子数(表6)。其结果是本发明的co/sio2催化剂的表面co的比例低于2%。另一方面,专利文献1记载的co/sio2催化剂的表面co的比例达5%左右。认为作为该co表面原子数小是本发明的co/sio2催化剂高活性的一个原因。推测出作为表面co原子数变小的要因,是因为使co粒子成为覆盖sio2粒子的方式的结构,具有防止co粒子的凝集等的可能性。
[0132]
表6
[0133]
利用xps测定得到的co及si的表面原子数
[0134][0135]
(8)钴的电子状态的评价
[0136]
对担载于sio2上的钴的电子状态通过xps进行评价(图4的co/sio2)。其结果是在60.0ev附近检测到峰。另一方面,将氢气还原时的温度不是600℃而是设为200℃的钴的电子状态也同样进行评价(图4的coo/sio2),结果在61.6ev附近检测到峰。co在60ev附近检测
到峰,coo在62ev附近检测到峰(b.schmidt,k.wetzig,ion beams in materials processing and analysis(springer,2013)),因此认为担载于sio2上的钴不是氧化钴,而是金属钴。
[0137]
〔实施例2〕
[0138]
(1)原料sio2硅烷醇基量与催化活性的关系
[0139]
(1-1)硅烷醇基量不同的sio2的制作
[0140]
将sigma-aldrich制的sio2(纯度》99%)10g投入到1m硝酸水溶液500ml中,在室温下搅拌1小时。将其过滤物用500ml的蒸馏水洗涤3次,在90℃使其干燥12小时。将这样操作制备的sio2在以下4种条件下进行处理之后,测定sio2的表面硅烷醇基量。
[0141]
1)不加热、2)在400℃加热1小时、3)在400℃加热2小时、4)在400℃加热5小时。
[0142]
硅烷醇基量的测定按照以下进行。
[0143]
在重量测定装置中,将试样(sio2)在250℃加热5小时,确认了重量达到恒定。然后,将试样以1℃/min加热至1000℃,并测定250℃和1000℃时的试样的重量。予以说明,600℃以上的温度时试样的重量没有变化。250℃与1000℃的试样的重量差相当于从sio2中脱除的水分子的量,其与sio2的表面硅烷醇基量成比例,因此根据该重量差算出试样的硅烷醇基量。予以说明,通过上述加热从2mol的表面硅烷醇基中脱除1mol的水分子。(1-2)催化剂的制作与催化活性的测定
[0144]
以上述4种sio2作为载体,根据实施例1的“(2)20wt%担载钴催化剂的制备法”制作催化剂。具体如以下所述。
[0145]
将硝酸钴六水合物(1.23g)和sio2(1g)分散于50ml的蒸馏水中,在室温搅拌1小时。利用旋转蒸发器蒸馏除去水之后,在减压下(~0.25kpa)进行加热干燥(100℃)。将干燥粉末在氮气流中、于400℃烧结2小时,得到前驱物。通过将前驱物在600℃进行2小时的氢气还原(30ml/min),制作担载钴催化剂。氢气还原后,在不曝露于空气的情况下转移到手套箱中,用于催化剂反应。
[0146]
使用制作的担载钴催化剂,进行了由糠醛到糠基胺的还原性氨基化反应。反应条件是与实施例1的“(3)还原性氨基化反应”同样地条件。即,糠醛:0.5mmol、0.1mpa nh3、0.5mpa h2、50℃、4h。糠基胺的分离收率如下表所示。
[0147]
表7
[0148]
加热条件原料sio2载体表面的硅烷醇基量(mmol/g)分离收率(%)在400℃加热5小时353在400℃加热2小时53在400℃加热1小时6-没有加热7-[0149]
如表所示,虽然以硅烷醇基量为3mmol/g的sio2作为原料的催化剂显示高活性,但硅烷醇基量为5mmol/g以上的sio2作为原料的催化剂几乎没有显示活性。
[0150]
(2)原料sio2表面积与催化活性的关系
[0151]
将用与〔实施例2〕的“(1)原料sio2硅烷醇基量与催化活性的关系”记载的方法同样的方法制备的sio2以下述4种条件下进行加热处理,之后利用bet法测定sio2的表面积。
[0152]
1)在400℃加热5小时、2)在400℃加热10小时、3)在500℃加热5小时、4)在600℃加
热5小时。
[0153]
另外,对sio2的表面硅烷醇基量也进行测定。
[0154]
以上述4种sio2为载体,根据实施例1的“(2)20wt%担载钴催化剂的制备法”制作了催化剂。使用制作的担载钴催化剂,进行从糠醛到糠基胺的还原性氨基化反应。反应条件为与实施例1的“(3)还原性氨基化反应”同样的条件。即糠醛:0.5mmol、0.1mpa nh3、0.5mpah2、50℃、4h。糠基胺的分离收率如下表所示。
[0155]
表8
[0156][0157]
如表所示,虽然以表面积为120m2g-1
的sio2作为原料的催化剂显示高活性,但以表面积为80m2g-1
以下的sio2作为原料的催化剂几乎没有显示活性。
[0158]
(3)原料sio2硅烷醇基量、以及co0和co
2+
的表面存在比与催化活性的关系
[0159]
制作硅烷醇基量为3mmol/g、5mmol/g、或7mmol/g,表面积为120m2g-1
的sio2,以其作为载体,根据实施例1的“(2)20wt%担载钴催化剂的制备法”制作了催化剂。求出该催化剂的钴中的co0和co
2+
的表面存在比。利用co 3p的xps测定co0和co
2+
的表面存在比,分割在co(0)(59ev)、co(2+)(62ev)这2处所得到的峰,由各自的峰面积估算出。予以说明,分割时使用高斯函数和洛仑兹函数这两者。另外,使用制作的担载钴催化剂,进行了由糠醛到糠基胺的还原性氨基化反应。反应条件是与实施例1的“(3)还原性氨基化反应”同样的条件。即糠醛:0.5mmol、0.1mpa nh3、0.5mpa h2、50℃、4h。糠基胺的分离收率如下表所示。
[0160]
表9
[0161][0162]
如表所示,以硅烷醇基量为3mmol/g的sio2作为原料的催化剂虽然显示高活性,但以硅烷醇基量为5mmol/g或7mmol/g的sio2作为原料的催化剂几乎不显示活性。另外,硅烷醇基量越低,co0的存在比越高,co
2+
的存在比越低。
[0163]
将本说明书引用的全部发行刊物、专利以及专利申请直接作为参考纳入本说明书中。
[0164]
产业上的可利用性
[0165]
本发明的催化剂由于能够促进还原性氨基化反应,所以可用于工业的胺合成中。