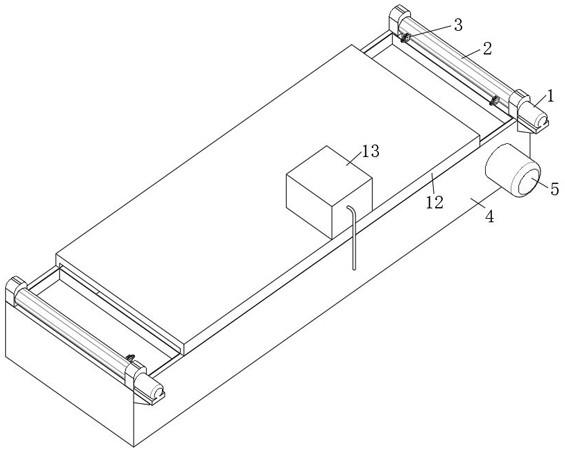
1.本发明涉及超纳滤膜技术领域,尤其涉及一种超纳滤膜智能化输送系统及其使用方法。
背景技术:2.超纳滤膜是一种允许溶剂分子或某些低分子量溶剂或低价离子透过的一种功能性的半透膜,因其能够截留物质的大小为纳米级而得名,常被用于去除地表水中的有机物和色度,去除溶解性盐和分离药品中的物质等。
3.公开号为cn110152499a的一项中国专利公开了一种纳滤膜和纳滤膜的使用方法。该纳滤膜包括聚合物原膜和聚合物原膜表面形成的单宁酸层和聚醚胺层,其使用方法包括以下步骤:制备聚合物原膜;配制磷酸盐缓冲溶液;将单宁酸和聚醚胺分别溶解在磷酸盐缓冲溶液中,配制成单宁酸溶液和聚醚胺溶液;将聚合物原膜浸泡在单宁酸溶液中,然后用去离子水漂洗5min;再将上述浸泡并漂洗后的聚合物原膜浸泡在聚醚胺溶液中,然后用去离子水漂洗5min;重复浸泡单宁酸和聚醚胺溶液0-2次;通过单宁酸和聚醚胺进行反应性层层自组装制备得到所述纳滤膜。制备过程简单,且纳滤膜涂层结构稳定,截留率高,从而解决了现有技术中层层自组装纳滤膜稳定性不足且制备过程繁琐的技术问题。
4.在超纳滤膜生产过程中,使用夹持机构将膜片的边缘夹紧固定,将膜片放入油槽中进行浸油,去除膜片孔隙中的水分,并起到支撑膜的作用,但是膜片被夹持的部位无法与甘油接触,导致该部位浸油效果较差。
技术实现要素:5.本发明要解决的技术问题是:为了克服上述技术中的技术问题之一,本发明提供了一种超纳滤膜智能化输送系统及其使用方法,包括,依次连接的搅拌罐、铸膜机、凝胶清洗一体机、后处理设备、烘干机、平板膜裁剪机和超声波焊接机;所述后处理设备包括浸油槽、转动设置在所述浸油槽上方的若干机械爪、转动设置在所述浸油槽一侧的同步带、设置在所述同步带上的篮筐、设置在所述浸油槽上方的顶板、设置在所述顶板上的喷嘴和驱动所述同步带转动的驱动部,其中,所述喷嘴与所述篮筐的位置相对应。
6.进一步地,所述浸油槽上转动设有支撑梁、设置在所述支撑梁上的若干机械爪和与所述支撑梁传动连接的电机一,其中,所述电机一固定设置在所述浸油槽的上方。
7.进一步地,所述驱动部包括设置在所述浸油槽侧壁上的电机二和与所述电机二传动连接的齿轮,其中,所述齿轮与所述同步带传动连接,且所述齿轮位于所述同步带的两端。
8.进一步地,所述同步带的侧面上固定有若干支撑杆,所述支撑杆上转动连接有所
述篮筐,其中,所述浸油槽的侧壁上开设有滑槽,所述支撑杆滑动设置在所述滑槽内。
9.进一步地,所述篮筐的底部设有橡胶浮块,所述橡胶浮块上设置有网板,其中,所述橡胶浮块上开设有若干气腔。
10.进一步地,所述顶板上还设有设备箱,所述设备箱内安装有油泵,所述顶板下方还设有与所述喷嘴连通的油路,其中,所述油泵的一端与所述浸油槽连通,另一端与所述油路连通。
11.进一步地,所述喷嘴包括喷嘴本体、设置在所述喷嘴本体内的喷油腔、转动设置在所述喷油腔内的连接轴、与所述连接轴一端固定连接的涡轮扇叶、与所述连接轴另一端固定连接的横杆、设置在所述横杆上的凸环和设置在所述凸环外圈的叶片,其中,所述喷油腔与所述油路连通,所述喷油腔远离所述油路的一端设有喷口,所述喷口与所述篮筐位置相对应。
12.进一步地,所述喷油腔的侧壁上开设有两个环槽,所述环槽内均固定安装有轴承,所述轴承的内圈与滑环固定连接,其中,所述滑环通过连接杆与所述连接轴固定连接。
13.进一步地,所述机械爪的内壁设有多个气囊,其中,相邻两个所述气囊相互连通。
14.本发明还在于提供一种超纳滤膜的使用方法,包括,s1、预热:二甲基乙酰胺通过搅拌罐自带的输料泵在密闭条件下泵入搅拌罐;搅拌罐自带电加热装置,首先对二甲基乙酰胺进行预热,预热温度为50℃,保温2h;s2、混料搅拌:二甲基乙酰胺完成预热后,利用搅拌罐自带的负压抽料系统将pvdf、致孔剂和改性剂分别抽入搅拌罐并加热至55℃,利用罐内搅拌装置充分搅拌直至pvdf全部溶于二甲基乙酰胺中,得到铸膜液;s3、平板铸膜:铸膜液通过密闭管道均匀地刮涂到铸膜机内的无纺布表面,形成一层厚薄适中,分布均匀的树脂层;s4、凝胶:铸膜后工件迅速被牵引进入凝胶清洗一体机,铸膜液中的pvdf遇水凝固成薄膜,而二甲基乙酰胺则溶于水中;s5、清洗:凝胶后的工件继续被牵引至凝胶清洗一体机中清洗槽,使用自来水对其进行溢流漂洗,去除残留在膜孔内的少量二甲基乙酰胺,使膜具有足够的稳定性和力学性能;工件经凝胶清洗一体机自带风刀进行吹干后进入下一工段;s6、浸油:将清洗后工件浸入后处理设备中浸油槽进行浸油,电机一带动支撑梁转动,然后带动机械爪转动,机械爪将清洗完成后的工件夹持,浸入篮筐中,同时机械爪将工件松开,工件浮出液面,篮筐在同步带的作用下飘向另一端,然后被机械爪夹出;将浸油后的膜片放置到无纺布的框架上,在室温下晾干膜片的表面;s7、烘干:利用烘干机对工件进行烘干,采用加热温控装置对工件进行烘干,能源为电,加热温度为50℃~60℃;取出烘干后的膜,并取样浸泡于去离子水中24小时后,进行性能测试;s8、裁切:测试合格后,采用平板膜裁剪机对平板膜进行裁切成合适尺寸;s9、超声波焊接:采用超声波焊接机热熔接焊接将外购树脂板与膜进行焊接,焊接
完成即为平板膜mbr膜堆。
15.有益效果:1、本发明所述的一种超纳滤膜智能化输送系统及使用方法,通过设置电机一、支撑梁和机械爪;电机一带动支撑梁转动,然后带动机械爪转动,机械爪将清洗完成后的工件夹持,浸入篮筐中,同时机械爪将工件松开,工件浮出液面,篮筐在同步带的作用下飘向另一端,然后被机械爪夹出;降低了工件被机械爪夹持的部位无法浸油的概率,提高了工件的浸油效果。
16.2、本发明通过设置油泵和喷嘴,油泵将浸油槽内的甘油抽出,灌入油路内,再通过喷嘴向下喷出,均匀喷洒到篮筐内漂浮在甘油表面的工件顶面,进一步提高了工件的全面浸油效果,提高了工件的整体质量。
17.3、本发明通过设置涡轮扇叶、横杆、凸环和叶片;甘油经过涡轮扇叶,驱动涡轮扇叶旋转,喷出的甘油被凸环分割,部分甘油分流向凸环的中部,被横杆打碎分散,剩下的甘油分流向凸环的外圈,被叶片打碎扩散,使得喷出的甘油更加分散均匀,提高了甘油喷洒到工件表面的均匀性,进一步提高了工件浸油的效果。
附图说明
18.图1是本发明实施例一的立体图;图2是本发明实施例一的主视图;图3是图2中a处局部放大图;图4是图2中b处局部放大图;图5是图4中c处局部放大图;图6是图5中d处局部放大图;图7是图5中e-e处局部截面图;图8是图3中f处局部放大图;图9是本发明支撑梁内部结构另一示意图;图中:1、电机一;2、支撑梁;3、机械爪;4、浸油槽;5、电机二;6、齿轮;7、同步带;8、支撑杆;9、篮筐;10、网板;11、橡胶浮块;12、顶板;13、设备箱;14、油泵;15、油路;17、喷嘴;18、连接轴;19、涡轮扇叶;20、横杆;21、环槽;22、滑环;23、轴承;24、连接杆;25、凸环;26、叶片;27、气囊;28、液压缸。
具体实施方式
19.为了使本技术领域的人员更好地理解本发明方案,下面将结合本发明实施例中的附图,对本发明实施例中的技术方案进行清楚、完整地描述,显然,所描述的实施例仅仅是本发明一部分的实施例,而不是全部的实施例。基于本发明中的实施例,本领域普通技术人员在没有做出创造性劳动前提下所获得的所有其他实施例,都应当属于本发明保护的范围。
20.此处所称的“一个实施例”或“实施例”是指可包含于本发明至少一个实现方式中的特定特征、结构或特性。在本发明的描述中,需要理解的是,术语“上”、“顶”、“底”、等指示的方位或位置关系为基于附图所示的方位或位置关系,仅是为了便于描述本发明和简化描
述,而不是指示或暗示所指的装置或元件必须具有特定的方位、以特定的方位构造和操作,因此不能理解为对本发明的限制。此外,术语“第一”、“第二”仅用于描述目的,而不能理解为指示或暗示相对重要性或者隐含指明所指示的技术特征的数量。由此,限定有“第一”、“第二”的特征可以明示或者隐含的包括一个或者更多个该特征。而且,术语“第一”、“第二”等是用于区别类似的对象,而不必用于描述特定的顺序或先后次序。应该理解这样使用的数据在适当情况下可以互换,以便这里描述的本发明的实施例能够以除了在这里图示或描述的那些以外的顺序实施。
21.实施例一如图1~9所示,一种超纳滤膜智能化输送系统,包括,依次连接的搅拌罐、铸膜机、凝胶清洗一体机、后处理设备、烘干机、平板膜裁剪机和超声波焊接机;所述后处理设备包括浸油槽4、转动设置在所述浸油槽4上方的若干机械爪3、转动设置在所述浸油槽4一侧的同步带7、设置在所述同步带7上的篮筐9、设置在所述浸油槽4上方的顶板12、设置在所述顶板12上的喷嘴17和驱动所述同步带7转动的驱动部,其中,所述喷嘴17与所述篮筐9的位置相对应。
22.所述浸油槽4上转动设有支撑梁2、设置在所述支撑梁2上的若干机械爪3和与所述支撑梁2传动连接的电机一1,其中,所述电机一1固定设置在所述浸油槽4的上方。电机一1驱动支撑梁2转动,然后带动机械爪3转动。机械爪3的驱动方式还可以修改为:所述浸油槽4上方还设有液压缸28,所述液压缸28的活塞杆与所述机械爪3传动连接。液压缸28驱动机械爪3进行移动,提高了机械爪3夹持的范围距离,从而便于工作人员调整夹持工件。
23.所述驱动部包括设置在所述浸油槽4侧壁上的电机二5和与所述电机二5传动连接的齿轮6,其中,所述齿轮6与所述同步带7传动连接,且所述齿轮6位于所述同步带7的两端。同步带7与齿轮6啮合,套设在齿轮6上,齿轮6转动,从而同步带7转动。
24.所述同步带7的侧面上固定有若干支撑杆8,所述支撑杆8上转动连接有所述篮筐9,其中,所述浸油槽4的侧壁上开设有滑槽,所述支撑杆8滑动设置在所述滑槽内。篮筐9设置在同步带7的侧面,滑槽的形状与同步带7的形状适配,以使篮筐9上的支撑杆8可以在滑槽内滑动。
25.所述篮筐9的底部设有橡胶浮块11,所述橡胶浮块11上设置有网板10,其中,所述橡胶浮块11上开设有若干气腔。篮筐9设置在浸油槽4内,通过在篮筐9的底部设置的橡胶浮块11和开设的气腔,使得篮筐9在浸油槽4内的甘油中具有浮力,使得篮筐9始终保持竖直向上的状态,提高了篮筐9运输工件时的稳定性,提高了工件运输时的安全性。
26.所述顶板12上还设有设备箱13,所述设备箱13内安装有油泵14,所述顶板12下方还设有与所述喷嘴17连通的油路15,其中,所述油泵14的一端与所述浸油槽4连通,另一端与所述油路15连通。
27.所述喷嘴17包括喷嘴17本体、设置在所述喷嘴17本体内的喷油腔、转动设置在所述喷油腔内的连接轴18、与所述连接轴18一端固定连接的涡轮扇叶19、与所述连接轴18另一端固定连接的横杆20、设置在所述横杆20上的凸环25和设置在所述凸环25外圈的叶片26,其中,所述喷油腔与所述油路15连通,所述喷油腔远离所述油路15的一端设有喷口,所述喷口与所述篮筐9位置相对应。所述喷嘴17的中部转动安装连接轴18,所述连接轴18的顶端固定连接有涡轮扇叶19,所述连接轴18的底端外圈固接多个横杆20;工件漂浮在篮筐9的
表面上,工作时,甘油从喷嘴17中喷出,喷嘴17喷出的力较大,经过涡轮扇叶19,使得涡轮扇叶19旋转,带动连接轴18转动,带动横杆20转动,将喷出的甘油打散,使得喷出的甘油更加分散均匀,从而提高了甘油喷洒到工件表面的均匀性,继而进一步提高了工件浸油的效果。
28.所述喷油腔的侧壁上开设有两个环槽21,所述环槽21内均固定安装有轴承23,所述轴承23的内圈与滑环22固定连接,其中,所述滑环22通过连接杆24与所述连接轴18固定连接。工作时,连接轴18转动,带动滑环22沿着环槽21旋转,通过轴承23降低了滑环22转动时的摩擦力,同时限定了滑环22的位置,降低了滑环22从环槽21内脱离的概率,提高了连接轴18转动的稳定性。
29.所述机械爪的内壁设有多个气囊27,其中,相邻两个所述气囊27相互连通;工作时,机械爪3夹持工件上,使得气囊27接触工件,气囊27内的气体向周边的减压气囊27扩散,将工件夹持部位包裹,降低了对工件的挤压力,降低了工件的损坏概率。
30.实施例二本实施例二在实施例一的基础上,还提供了一种超纳滤膜智能化输送系统及使用方法,其中的一种超纳滤膜智能化输送系统与实施例一相同,此处不在赘述。具体的一种超纳滤膜智能化输送系统的使用方法如下:s1、预热:二甲基乙酰胺通过搅拌罐自带的输料泵在密闭条件下泵入搅拌罐;搅拌罐自带电加热装置,首先对二甲基乙酰胺进行预热,预热温度为50℃,保温2h;s2、混料搅拌:二甲基乙酰胺完成预热后,利用搅拌罐自带的负压抽料系统将pvdf、致孔剂和改性剂分别抽入搅拌罐并加热至55℃,利用罐内搅拌装置充分搅拌直至pvdf全部溶于二甲基乙酰胺中,得到铸膜液;s3、平板铸膜:铸膜液通过密闭管道均匀地刮涂到铸膜机内的无纺布表面,形成一层厚薄适中,分布均匀的树脂层;s4、凝胶:铸膜后工件迅速被牵引进入凝胶清洗一体机,铸膜液中的pvdf遇水凝固成薄膜,而二甲基乙酰胺则溶于水中;s5、清洗:凝胶后的工件继续被牵引至凝胶清洗一体机中清洗槽,使用自来水对其进行溢流漂洗,去除残留在膜孔内的少量二甲基乙酰胺,使膜具有足够的稳定性和力学性能;工件经凝胶清洗一体机自带风刀进行吹干后进入下一工段;s6、浸油:将清洗后工件浸入后处理设备中浸油槽4进行浸油,电机一1带动支撑梁2转动,然后带动机械爪3转动,机械爪3将清洗完成后的工件夹持,浸入篮筐9中,同时机械爪3将工件松开,工件浮出液面,篮筐9在同步带7的作用下飘向另一端,然后被机械爪3夹出;将浸油后的膜片放置到无纺布的框架上,在室温下晾干膜片的表面;s7、烘干:利用烘干机对工件进行烘干,采用加热温控装置对工件进行烘干,能源为电,加热温度为50℃~60℃;取出烘干后的膜,并取样浸泡于去离子水中24小时后,进行性能测试;s8、裁切:测试合格后,采用平板膜裁剪机对平板膜进行裁切成合适尺寸;s9、超声波焊接:采用超声波焊接机热熔接焊接将外购树脂板与膜进行焊接,焊接完成即为平板膜mbr膜堆;s10:裁切:对外购不锈钢进行裁切,裁切过程产生少量边角料;s11:焊接:加工好的不锈钢进行简单焊接,制成所需的结构件;焊接采用气保焊及
氩弧焊,焊接过程产生焊接烟尘及废焊渣;s12:整体组装:外购外框架、五金件、标准配件和上述加工完成的膜组件及结构件进行整体组装。
31.以上所述仅为本发明的较佳实施例,并不用以限制本发明,凡在本发明的精神和原则之内,所作的任何修改、等同替换、改进等,均应包含在本发明的保护范围之内。