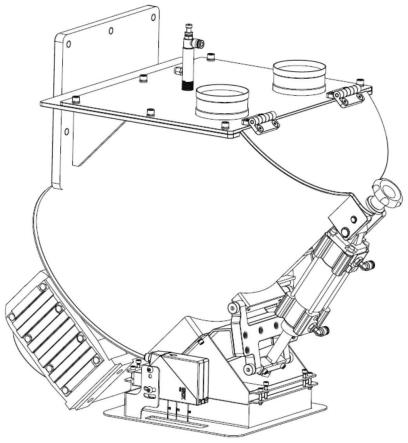
1.本发明涉及b22c,更具体地,本发明涉及一种微滴喷印装备高速高压雾化混料工艺及装置。
背景技术:2.微滴喷印为通过喷射粘结剂和粉料混合在一起后,进行打印的方法,其中为了使粘结剂更好地将粉料粘结在一起,需要在粉料中加入固化剂,其中固化剂一般为浓硫酸或有机酸配成的酸性液体,有水基或油基,比如甲苯或苯等作溶剂的种类,均是利用粉料附着的酸性物质和粘结剂作用起到更好的粘结作用,故粉料和固化剂的混合均匀性对微滴喷印性能具有重要影响。
3.而目前的固化剂往往存在粘度较大的问题,一般25℃时粘度为10mpa
·
s以上,甚至对于高酸固化剂,可能达到60mpa
·
s,高于3d打印粘度的要求,而如果降低酸值,减少粘度,其固化速率难以满足要求,故目前通过研究新的固化剂,如cn108543908b、cn105057566b、cn104447420b等提供的固化剂来改善其粘度。
4.但是这类固化剂也造成了成本提高等问题,且在混料过程中,直接通过管道滴入待混成型粉料时,由于滴入点单一随即带来的是固化剂很难充分打散与成型粉料全方位无死角混合,同样难以保证其可以和粉料均匀分散,故提供一种新的设备,来改善固化剂难以均匀和粉料混合等问题具有重要意义,且因为固化剂为较粘稠的液态,在和粉料混合过程中,也会导致所流经的管路存在挂壁现象,造成在实际混料过程中固化剂与成型粉料的实际配比不确定的问题。
技术实现要素:5.为了解决上述问题,本发明第一个方面提供了一种微滴喷印装备高速高压雾化混料装置,包括:
6.混料桶,包括位于混料桶内部的混料叶轮和位于混料桶侧面底部的放料闸门;
7.雾化注入组件,位于混料桶上方;
8.粉料注入口,位于混料桶上方。
9.作为本发明一种优选的技术方案,所述雾化固化剂注入组件包括:
10.滴管;
11.压缩气体注入口,和滴管连通;
12.固化剂注入口,和滴管连通,用于将固化剂注入滴管。
13.发明人发现,相比于直接注入混料桶中,本发明通过使用滴管提供一个固化剂和压缩气体混合的空间,来用于粘稠液态固化剂依靠压缩气体高压作用,快速流经喷嘴,并在其喷嘴出口形成雾状喷洒到混料桶中,从而增加和粉料的接触面积。本发明不对固化剂做具体限定,可为水基或油基固化剂,其中的酸可来自有机酸,如丙烯酸、脂肪酸等,也可来自无机酸,如硫酸等,不做具体限定,本发明提供的装置可用于25℃时粘度在60mpa
·
s及以下
的固化剂和粉料的分散混合。
14.作为本发明一种优选的技术方案,所述雾化注入组件还包括:压力调节阀,连通压缩气体注入口和滴管,用于调节进入滴管的压缩气体的压力;本发明不对压力调节阀调节压力的大小做具体限定,可根据固化剂本身的粘度进行选择,一般调节压缩气体的压力在0.1~0.6mpa。
15.作为本发明一种优选的技术方案,所述压力调节阀位于固化剂注入口的上方;本发明控制压缩气体在固化剂上方加入滴管,有利于固化剂在压缩气体作用下全部从滴管流出,减少流经的管路存在挂壁现象造成实际混料中固化剂和粉料配比不稳定的问题。
16.作为本发明一种优选的技术方案,所述滴管下方设有喷嘴,和混料桶内部连通。
17.作为本发明一种优选的技术方案,所述粉料注入口个数大于等于1个,当至少一种粉料的酸耗值大于等于3ml时,所述粉料注入口的个数为2个及以上时,所述至少一个粉料注入口用于加入酸耗值小于3ml的粉料或含有固化剂的粉料,使得粉料总的酸耗值小于3ml。为了满足不对3d打印材料的性能要求,粉料的性能也具有大的差距,且也收到产地、制备工艺或者喷印次数的限定,使得不同粉料固有的酸耗值也有所不同,这也会影响固化剂的使用量。酸耗值用于反映粉料中碱性物质的含量,一般用中和50g原粉料的碱性物质达到ph为7时所需消耗的0.1n盐酸的体积来表示。
18.故在使用高酸耗值的粉料时,为了获得优良的成型效果,可将相差极大的两种粉料按比例混合降低粉材的耗酸量(即耗费固化剂的量)达到成型粉料与固化剂的最优配比,或者采用含有固化剂的粉料(一般为之前粉料和固化剂混合后的残留料),来控制粉料总的酸耗值小于3ml,优选为0~2ml。
19.作为本发明一种优选的技术方案,所述混料叶轮通过叶轮轴设置在混料桶底部,所述混料叶轮包括叶片底部和叶片末端,所述叶片底部的上方和叶片末端下方连接,所述叶片底部的下方和叶轮轴上方连接。此外,发明人发现,当雾化后的固化剂和粉料注入到混料桶后,需要通过混料叶轮进行混料,其中在混料过程中,当使用由叶片底部和叶片末端呈折线形的混料叶轮时具有更好的混料状态。
20.作为本发明一种优选的技术方案,所述叶片底部和叶轮轴的旋转方向的角度为50~65
°
,可列举的有,50
°
、55
°
、60
°
、65
°
,所述叶片末端和叶轮轴的旋转方向的角度为80~100
°
,可列举的有,80
°
、85
°
、90
°
、95
°
、100
°
。且发明人发现,当控制叶片底部和叶片末端相对于旋转方向的角度时,发明人发现,可使得粉料呈四散方向向周围分散的同时,叶片底部的粉料更易向上爬升的同时,叶片末端的粉料也更容易打散。从而进一步增加雾化固化剂接触的同时,也有利于本发明提供粉料之间的碰撞从而促进固化剂进一步分散,进一步增加粉料之间分布的酸性物质的均匀性。
21.作为本发明一种优选的技术方案,所述混料桶为倾斜设置,所述倾斜角度为30~60
°
,可列举的有,30
°
、35
°
、40
°
、45
°
、50
°
、55
°
、60
°
。本发明所述倾斜角度为混料桶中心轴和水平面的夹角。发明人发现,相当于混料桶竖直放置,当倾斜放置时,更有利于混料过程中粉料和固化剂的接触和混后放料。
22.本发明不对混料叶轮的个数做具体限定,可为1个,也可为2个及以上,如1~4个,具体可根据混料桶的尺寸进行选择,其中当为2个及以上混料叶轮时,相邻混料叶轮间角度相同。
23.作为本发明一种优选的技术方案,当混料叶轮旋转到最高处时,所述混料叶轮的最高点的高度位于粉料注入口注入的粉料体积的1/2~2/3处,更优选地,所述叶轮轴的倾斜角度为30~60
°
,可列举的有,30
°
、35
°
、40
°
、45
°
、50
°
、55
°
、60
°
,所述叶轮轴的倾斜角度为叶轮轴的中心轴和水平面的夹角。发明人发现,因为本发明混料桶倾斜放置,也使得混料叶轮的最高点不断变化,而发明人也发现,当使得最高点为注入的粉料体积的1/2~2/3(根据混料桶的容积来计算)时,淹没在粉料中的混料叶轮也会促进混合效果,提高混合效率。
24.作为本发明一种优选的技术方案,所述混料装置还包括驱动马达,和混料叶轮连接;优选地,所述驱动马达和叶轮轴连接。
25.作为本发明一种优选的技术方案,所述混料装置还包括:
26.闸门动力组件,和放料闸门连接;用于控制闸门的开闭,可为气缸或其它动力源;
27.料位传感器,用于监测混料桶中料位;
28.密封调节罩,设置与放料闸门外部,减少粉料的分散,并起到粉料收集等作用。
29.本发明第二个方面提供了一种使用如上所述的微滴喷印装备高速高压雾化混料装置的混料方法,包括:
30.将固化剂和粉料分别通过雾化注入组件和粉料注入口注入混料桶内,在混合叶轮旋转下混料,混料完成后开启放料闸门放料。
31.本发明与现有技术相比具有以下有益效果:
32.(1)本发明通过设置雾化注入组件来将粘稠液态固化剂雾化后,有利于和粉料均匀融合,且在混合过程中,通过高速旋转的混料叶轮高高抛起粉料,使得粉料间产生物理热量进一步促进固化剂和粉料完全融合,为下一步高精度成型提供保障。
33.(2)此外,发明人也发现通过本发明混料装置,有利于促进雾状固化剂液滴的打散,减少较高粘度固化剂带来的粘接等问题,解决粉料和固化剂混合后松散度差的问题。
34.(3)且本发明提供的装置拆卸方便、结构紧促,加工方便,能有效避免固化剂注入管道挂壁现象,降低了成型粉料受固化剂挂壁带来配比不确定的影响,保证成型粉料与固化剂配比的精确性,且工作可靠性高。
35.(4)此外,通过本发明提供的的高压雾化工艺及高速搅拌混合装置,可使用更高转速进行混合,有利于提高混合效率,减少固化剂雾滴成团析出并促进粉料的快速分散和碰撞,提高混料均匀性。
附图说明
36.图1为本发明混料装置的结构示意图。
37.图2为本发明混料装置的内部结构示意图。
38.图3为混料叶轮的结构示意图。
39.图4为雾化注入组件的结构示意图。
40.其中,1混料桶、1-2混料叶轮、1-3放料闸门、1-4粉料注入口、2驱动马达、3闸门动力组件、4雾化注入组件、4-1滴管、4-2压力调节阀、4-3固化剂注入口、4-4喷嘴、5料位传感器、6密封调节罩。
具体实施方式
41.实施例
42.对照例
43.本例提供一种微滴喷印装备高速高压雾化混料装置,包括:混料桶,包括位于混料桶内部的混料叶轮和位于混料桶侧面底部的放料闸门;固化剂注入口,和混料桶内部连通;所述粉料注入口的个数为2个,一个注入酸耗值大于等于3ml的粉料,一个注入酸耗值小于3ml的粉料/含有固化剂的粉料,使得总的粉料的酸耗值在0.2ml左右;所述混料叶轮通过叶轮轴设置在混料桶底部,所述混料叶轮有两个,所述混料叶轮包括叶片底部和叶片末端,所述叶片底部的上方和叶片末端下方连接,所述叶片底部的内侧面和叶轮轴固定连接;所述叶片底部和叶轮轴的旋转方向的角度为85
°
,所述叶片末端和叶轮轴的旋转方向的角度为50
°
;所述混料桶为倾斜设置,所述倾斜角度为45
°
,当混料叶轮旋转到最高处时,所述混料叶轮的最高点的高度位于粉料注入口注入的粉料体积的2/3处,所述叶轮轴的倾斜角度为45
°
;所述混料装置还包括驱动马达,和混料叶轮连接;所述驱动马达和叶轮轴连接;所述混料装置还包括:闸门动力组件,和放料闸门连接;用于控制闸门的开闭,可为气缸或其它动力源;料位传感器,用于监测混料桶中料位;密封调节罩,设置与放料闸门外部,减少粉料的分散,并起到粉料收集等作用。
44.本例还包括使用如上所述的微滴喷印装备高速高压雾化混料装置的混料方法,包括:
45.将固化剂和粉料分别通过固化剂注入口和粉料注入口注入混料桶内,在混合叶轮的转速为2转/s下混料,混料完成后开启放料闸门放料。
46.测试结果:固化剂在固化剂注入口管道中存在挂壁现象,流经管道的固化剂不能完全注入即产生粉料与固化剂配比偏差;固化剂直接滴入后,与粉料形成团状,由于混料叶轮转速偏低及混料叶轮角度不合理,在混料过程中混料叶轮不能充分打散团状固化剂造成混合不均匀。
47.实施例1
48.如图1~4所示,本例提供一种微滴喷印装备高速高压雾化混料装置,包括:混料桶1,包括位于混料桶1内部的混料叶轮1-2和位于混料桶1侧面底部的放料闸门1-3;雾化注入组件4,位于混料桶1上方;粉料注入口1-4,位于混料桶1上方,所述雾化固化剂注入组件4包括:滴管4-1;压缩气体注入口,和滴管4-1连通;固化剂注入口4-3,和滴管4-4连通,用于将固化剂注入滴管4-1,所述雾化注入组件4还包括:压力调节阀4-2,连通压缩气体注入口和滴管4-1,用于调节进入滴管4-1的压缩气体的压力,所述压力调节阀4-2位于固化剂注入口4-3的上方,所述滴管4-1下方设有喷嘴4-4,和混料桶1内部连通;所述粉料注入口1-4的个数为2个,一个注入酸耗值大于等于3ml的粉料,一个注入酸耗值小于3ml的粉料/含有固化剂的粉料,使得总的粉料的酸耗值在0.2ml左右;所述混料叶轮1-2通过叶轮轴设置在混料桶底部,所述混料叶轮1-2有两个,所述混料叶轮1-2包括叶片底部和叶片末端,所述叶片底部的上方和叶片末端下方连接,所述叶片底部的内侧面和叶轮轴固定连接;所述叶片底部和叶轮轴的旋转方向的角度为50
°
,所述叶片末端和叶轮轴的旋转方向的角度为85
°
;所述混料桶1为倾斜设置,所述倾斜角度为45
°
,当混料叶轮旋转到最高处时,所述混料叶轮的最高点的高度位于粉料注入口1-4注入的粉料体积的1/2处,所述叶轮轴的倾斜角度为45
°
;所
述混料装置还包括驱动马达2,和混料叶轮1-2连接;所述驱动马达2和叶轮轴连接;所述混料装置还包括:闸门动力组件3,和放料闸门1-3连接;用于控制闸门的开闭;料位传感器5,用于监测混料桶1中料位;密封调节罩6,设置与放料闸门1-3外部,减少粉料的分散,并起到粉料收集等作用。
49.本例还包括使用如上所述的微滴喷印装备高速高压雾化混料装置的混料方法,包括:
50.将固化剂和粉料分别通过雾化注入组件4和粉料注入口1-4注入混料桶1内,在混合叶轮1-2的转速为6转/s下混料,混料完成后开启放料闸门1-3放料。
51.测试结果:流经管道的固化剂在喷嘴出口形成雾化状态均匀地喷射到搅动中的粉料表面,在喷射与搅拌过程中,粉料与固化剂能够充分打散并融合,粉料与固化剂配比精确;由于混料叶轮转速的提高及混料叶轮角度优化,在混料过程中混料叶轮高速转动,粉料借由离心力的作用,被混料叶轮高高抛起并离散下落,过程中与雾化喷射出的固化剂充分且均匀的融合在一起,无成团,获得优质混合成型粉料。
52.实施例2
53.如图1~3所示,本例提供一种微滴喷印装备高速高压雾化混料装置,包括:混料桶1,包括位于混料桶1内部的混料叶轮1-2和位于混料桶1侧面底部的放料闸门1-3;雾化注入组件4,位于混料桶1上方;粉料注入口1-4,位于混料桶1上方,所述雾化固化剂注入组件4包括:滴管4-1;压缩气体注入口,和滴管4-1连通;固化剂注入口4-3,和滴管4-4连通,用于将固化剂注入滴管4-1,所述雾化注入组件4还包括:压力调节阀4-2,连通压缩气体注入口和滴管4-1,用于调节进入滴管4-1的压缩气体的压力,所述压力调节阀4-2位于固化剂注入口4-3的上方,所述滴管4-1下方设有喷嘴4-4,和混料桶1内部连通;所述粉料注入口1-4的个数为2个,一个注入酸耗值大于等于3ml的粉料,一个注入酸耗值小于3ml的粉料/含有固化剂的粉料,使得总的粉料的酸耗值在0.2ml左右;所述混料叶轮1-2通过叶轮轴设置在混料桶底部,所述混料叶轮1-2有两个,所述混料叶轮1-2包括叶片底部和叶片末端,所述叶片底部的上方和叶片末端下方连接,所述叶片底部的内侧面和叶轮轴固定连接;所述叶片底部和叶轮轴的旋转方向的角度为65
°
,所述叶片末端和叶轮轴的旋转方向的角度为100
°
;所述混料桶1为倾斜设置,所述倾斜角度为30
°
,当混料叶轮旋转到最高处时,所述混料叶轮的最高点的高度位于粉料注入口1-4注入的粉料体积的2/3处,所述叶轮轴的倾斜角度为30
°
;所述混料装置还包括驱动马达2,和混料叶轮1-2连接;所述驱动马达2和叶轮轴连接;所述混料装置还包括:闸门动力组件3,和放料闸门1-3连接;用于控制闸门的开闭;料位传感器5,用于监测混料桶1中料位;密封调节罩6,设置与放料闸门1-3外部,减少粉料的分散,并起到粉料收集等作用。
54.本例还包括使用如上所述的微滴喷印装备高速高压雾化混料装置的混料方法,包括:
55.将固化剂和粉料分别通过雾化注入组件4和粉料注入口1-4注入混料桶1内,在混合叶轮1-2的转速为6转/s下混料,混料完成后开启放料闸门1-3放料。
56.测试结果:流经管道的固化剂在喷嘴出口形成雾化状态均匀地喷射到搅动中的粉料表面,在喷射与搅拌过程中,粉料与固化剂能够充分打散并融合,粉料与固化剂配比精确;由于混料叶轮转速的提高及混料叶轮角度优化,在混料过程中混料叶轮高速转动,粉料
借由离心力的作用,被混料叶轮高高抛起并离散下落,过程中与雾化喷射出的固化剂充分且均匀的融合在一起,无成团,获得优质混合成型粉料。