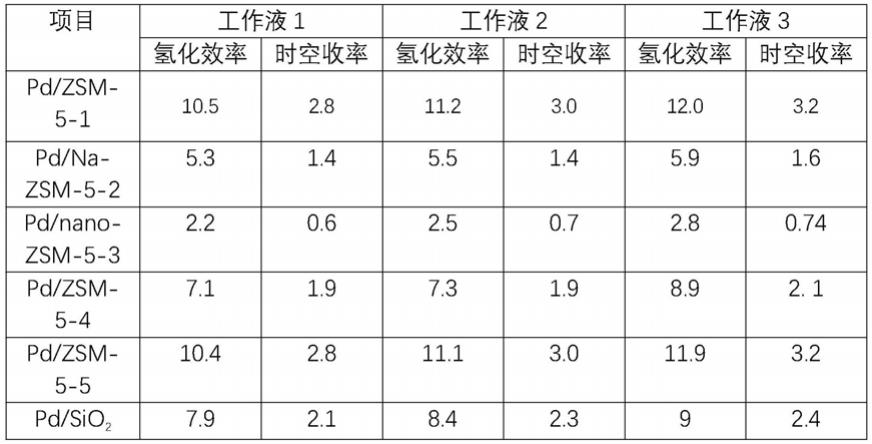
1.本发明属于材料制备技术领域,具体涉及一种介孔沸石分子筛为在的pb、催化剂及其制备方法和在双氧水生产中的应用。
技术背景
2.过氧化氢(h2o2,俗称双氧水),由于其氧化性主要作为漂白剂、消毒剂使用,亦可作为化工原料。广泛应用于造纸、化工、环保、电子、航天等行业。近年来,在新型的绿色化工领域中,如:己内酰胺、苯二酚、环氧丙烷等产品生产过程均可以以双氧水为氧化剂,进一步开拓了双氧水新的应用领域。
3.目前,工业上生产过氧化氢的主要方法是蒽醌法。蒽醌法具有自动化程度高,能耗低,污染少、产品纯度高、原料可循环利用、生产成本低等优点,已成为现阶段工业制备双氧水最为成熟和广泛的方法之一。蒽醌法是目前工业生产双氧水普遍采用的方法,制备工序主要包括工作液配置、蒽醌加氢、氢蒽醌氧化、双氧水萃取、工作液后处理及再生等过程。具体操作可概括为:将蒽醌 (如2-乙基蒽醌、2-戊基蒽醌)溶解在混有有机溶剂中形成蒽醌工作液,然后在催化剂作用下,催化加氢生成氢蒽醌,再将氧气或空气通入氢化后的工作液中,经一段时间后氢蒽醌被氧化生成蒽醌,同时生产双氧水,生的双氧水经萃取、纯化浓缩可得到不同浓度产品,蒽醌工作液经后处理步骤可重复循环使用,这里蒽醌氢化和氢蒽醌氧化是该工艺的关键工段。因此催化剂作为参与蒽醌加氢反应中的重要部分,对加氢反应速率和选择性都有重要影响。
4.目前蒽醌法制备双氧水的工业生产装置主要采用固定床和浆态床反应器。国内大部分的双氧水企业采用的是黎明化工研究院的固定床工艺,使用pd/al2o3为催化剂,但是由于该催化剂的选择性差,有较多的副产物生成,因此降低了氢蒽醌的产率。
5.浆态床反应器由于采用颗粒状的催化剂,反应和传质快,可以提高催化剂的利用率,而且是在双氧水工业生产中发展迅速和应用广泛的一种反应器形式。
6.工业用蒽醌加氢催化剂一般以pd、pt、ru、rh、ni等金属为活性组分负载于无机非金属载体上制备而成。催化剂的活性中心暴露在载体的表面上,在浆态床反应器的反应过程中不可避免会产生反应液的摩擦、催化剂之间的碰撞使得的活性中心出现掉落的现象,因此导致催化剂活性下降,所以活性中心在催化剂上的牢固度很重要。对于蒽醌加氢反应来说,载体的强酸性和微孔有利于氢原子的溢流,加强了h2的解离,有助于提高蒽醌加氢反应的单程活性和产物中双氧水的浓度。硅铝分子筛具有较强的酸性、并且比表面积大,有利于活性中心的分散,可以降低贵金属的用量,降低投资。但蒽醌与反应溶剂均为大分子的物质,其传质受分子筛择形性孔道尺寸影响较大,因此需要解决载体分子筛酸性和孔道尺寸的兼顾问题。
7.介孔沸石材料是指以结晶的微孔沸石为基础,其中含有丰富介孔,有利于大分子的扩散和传质传热还具有良好的酸性和水热稳定性。与传统的介孔材料有着较大的区别,
因此在催化领域是极有应用价值的催化材料。
技术实现要素:8.为了兼顾分子筛酸性和孔道尺寸以得到活性优异的蒽醌加氢催化剂,本发明的目的在于提供一种以介孔zsm-5沸石分子筛为载体的催化剂及其制备方法,它具备反应所需的强酸性,适当的分子筛孔道尺寸,活性中心稳定不流失,催化效率高等优点。
9.为了实现本发明的上述目的,本发明提供了如下技术方案:
10.本发明提供了一种以介孔分子筛为载体的催化剂及其制备方法和在双氧水生产中的应用。
11.所述的一种介孔沸石分子筛为载体的催化剂,其特征在于该催化剂包括活性组分和介孔沸石分子筛。
12.所述的活性组分选自铂族贵金属pd,催化活性以贵金属单质计,占催化剂总重量的0.01-1.00wt%。
13.所述的介孔分子筛壳为硅铝结构的zsm-5硅铝,占催化剂总重的99
‑ꢀ
99.99%。
14.所述介孔沸石分子筛为载体的催化剂制备方法包括下述步骤:
15.一.介孔分子筛载体zsm-5的制备
16.1.第一步制备zsm-5前驱体溶液反应物料的摩尔组成按照 n(sio2):n(al2o3):n(tpaoh):n(h2o)=1.0:0.05-0.067:0.30-0.40:30-35。得到的物料经过除醇处理后装入釜中于80℃下陈化18-24h,得到澄清溶液,即为前驱体的溶液。
17.2.第二步:将前驱体溶液加入到表面活性剂的无水乙醇溶液中,持续搅拌,并用稀盐酸(3m)调节体系的ph值为5-6。所得混合物在室温下持续搅拌 9-24h,经过喷雾干燥成型得到颗粒尺寸约70μm的球形的产品、再经烘干和焙烧得到具有sba-15结构的以zsm-5为孔壁的h型介孔沸石分子筛。
18.进一步的,所述表面活性剂与胶液中sio2干基的摩尔比为0.03-0.05
19.进一步的,所述载体分子筛的硅源为正硅酸四乙酯、正硅酸四丙酯、正硅酸四丁酯中的一种或两种以上的混合;
20.进一步的,所述的载体分子筛的铝源为十八水合硫酸铝,偏铝酸铝中的一种或者两种的混合;
21.进一步的,所述的载体分子筛的模板剂为四丙基氢氧化铵;
22.进一步的,所述的表面活性剂为三嵌段表面活性剂p123(ma=5800);
23.进一步的,所述的zsm-5分子筛的硅铝比为15-20(分子比),选择该硅铝比范围内的分子筛有利于蒽醌加氢反应的选择性。
24.作为优选方案,所述催化剂可以采用下面方法制备:
25.溶胶法:在搅拌条件下,将pd的前驱体、高分子保护剂与去离子水充分混合并加热至70℃,然后将还原剂加入并搅拌均匀,冷却至室温再将载体加入搅拌2-20h,静止过滤,用去离子水洗涤至检测不到氯离子。
26.进一步的,所述pd的前驱体为硝酸钯、氯钯酸、氯化钯中的一种或两种的混合物;
27.进一步的,所述的高分子保护剂为聚乙烯醇、聚乙烯吡咯烷酮、四羟甲基氯化磷、聚二甲基二丙烯氯化铵、硫醇类物质;
28.进一步的,所述的还原剂为柠檬酸钠、四羟甲基氯化磷、草酸和硼氢化钠;
29.进一步的,所述pd元素:还原剂:高分子保护剂:载体:水的质量比为1: (0.1-25):(0.1-25):(50-200):(200-10000)。
30.作为优选方案,将所得物于100℃下干燥;干燥时间为10h;干燥后的产品经450℃焙烧5h,再置于还原炉中,升温速度10-15℃/min,通入氢气还原,氢气流速保持30ml/min,还原0.5-5h后得pd催化剂。
31.本发明的有益效果是:
32.(1)具有sba-15孔道结构的zsm-5介孔沸石分子筛的比表面积大,有利于活性中心的负载和高度分散,而且zsm-5分子筛的微孔孔道有利于减小活性中心金属的颗粒粒径,优选为1-5nm;同时有利于氢溢流,从而提高催化剂的加氢活性,减少贵金属的用量;具有sba-15介孔结构的沸石分子筛载体8-10nm 的孔道尺寸有利于蒽醌加氢反应物和产物的扩散,有利于孔内的传质,有效避免了副产物的大量产生,进而提高催化剂的选择性。
33.(2)采用zsm-5为介孔孔壁大大提高了催化剂本身的强度,使得其在反应中具有更好的耐磨性,可以大大提高催化剂的稳定性、降低磨损率,延长催化剂的使用寿命。
34.(3)采用具有较强酸性的硅铝比为15-20的h型介孔zsm-5沸石分子筛为载体,可以加速h2的解离,加快反应进程,提高反应效率。
35.(4)采用溶胶法可以将活性中心牢固的负载在载体表面,从而减少活性中心的流失,延长催化剂的使用寿命,降低催化剂的使用成本。
附图说明
36.图1为本发明介孔沸石分子筛zsm-5载体的xrd谱图。
37.图2为本发明催化剂的透射电子显微镜照片。
具体实施方式
38.下面结合具体实施方式对本发明作进一步详细的说明,以帮助本领域的技术人员对本发明的发明构思、技术方案有更完整、准确和深入的理解,本发明的保护范围包括但不限于以下实施例,在不偏离本技术的精神和范围的前提下任何对本发明的技术方案的细节和形式所做出的修改均落入本发明的保护范围内。
39.实施例1
40.第一步:制备zsm-5前驱体溶液。将100.8正硅酸四乙酯、115.0g四丙基氢氧化铵水溶液(25wt%)以及35.57g去离子水混合,室温下搅拌1.5h至水解完全得到硅溶液。同时取41.8g十八水合硫酸铝与80.0g去离子水混合搅拌2h 得到铝溶液,将硅溶液匀速加入到铝溶液中,升温除醇并补水后,再持续搅拌 4h后得到均匀的硅铝凝胶然后装入晶化釜中,于80℃下陈化18h,得到澄清溶液,即为zsm-5前驱体溶液。
41.第二步:前驱体溶液与表面活性剂自组装。在35-40℃的条件下,取120g 三嵌段表面活性剂p123溶于152g乙醇当中,待完全溶解后,搅拌状态下加入到第一步中制备的zsm-5前驱体溶液,用稀盐酸(hcl 3m)调节体系的ph值为5-6,持续剧烈搅拌24h,之后将得到的胶液装入釜中晶化24h,再经过喷雾干燥得到颗粒尺寸约70μm的球形产品,最后在空气中550℃下焙烧6h即得到具有介孔sab-15结构的h型的zsm-5沸石分子筛,该分子筛的硅铝分子比
为 15。
42.第三步:溶胶法担载活性金属中心制备加氢催化剂。将0.52g pdcl2和0.7g 柠檬酸钠(还原剂)溶于50g水中,在50-80℃下搅拌1h溶解得稳定的活性胶液,之后加入0.75g聚乙烯吡咯烷酮(pvp)(保护剂)搅拌1h,将62.5g分子筛载体浸渍于活性液中持续3h后,静置后倾倒出上层液体,去离子水洗涤下层沉淀物直至滤液中检测不到氯离子,将所得物于100℃下干燥;干燥后的产品经450℃焙烧5h,再置于还原炉中,升温速度10-15℃/min,通入氢气还原,氢气流速保持30ml/min,还原1h后得催化剂pd/zsm-5-1,其中pd的负载量为0.5%wt。按照美国astm d5757-00标准测得的催化剂的磨损率为0.5%。
43.对比例1
44.催化剂的制备方法同实施例1,只是将在第二步得到的h型的zsm-5进行钠交换后再用于第三步的活性中心负载,得到的催化剂为pd/na-zsm-5-2。
45.对比例2
46.催化剂的制备方法同实施例1中第三步,只是将载体替换为同样颗粒大小的常规氢型硅铝分子比为15的纳米zsm-5分子筛,得到催化剂pd/nano
‑ꢀ
zsm-5-3,其中pd的负载量为0.5%wt。按照美国astm d5757-00标准测得的催化剂的磨损率为0.7%。
47.对比例3
48.催化剂的制备方法同实施例1,只是将载体的硅铝比控制为40,得到催化剂pd/zsm-5-4,其中pd的负载量为0.5%wt。按照美国astm d5757-00标准测得的催化剂的磨损率为0.7%。
49.对比例4
50.催化剂的制备方法同实施例1中的第一、二步,只是将第三步的活性中心的负载方法替换为常规的等体积浸渍法,将0.52g pdcl2溶于22.5g水中,然后取62.5g的介孔zms-5分子筛进行等体积浸渍,去离子水洗涤直至滤液中检测不到氯离子,将所得物于100℃下干燥;干燥后的产品经450℃焙烧5h,再置于还原炉中,升温速度10-15℃/min,通入氢气还原,氢气流速保持30ml/min,还原1h后得催化剂pd/zsm-5-5,其中pd的负载量为0.5%wt。
51.对比例5
52.催化剂的制备方法同实施例1中的第三步,只是将载体替换为同质量、同样颗粒大小的二氧化硅,得到催化剂pd/sio2,其中pd的负载量为0.5%wt。按照美国astm d5757-00标准测得的催化剂的磨损率为0.6%。
53.对比例6
54.催化剂的制备方法同实施例1中的第三步,只是将载体替换为同质量、同样颗粒大小的三氧化二铝,得到催化剂pd/al2o3,其中pd的负载量为0.5%wt。按照美国astm d5757-00标准测得的催化剂的磨损率为0.6%。
55.实施例2
56.催化剂的制备方法同实施例1,只是将分子筛的硅铝比调变为20,得到 pd/zsm-5-6,其中pd的负载量为0.5%wt。按照美国astm d5757-00标准测得的催化剂的磨损率为0.6%。
57.实施例3
58.催化剂的制备方法同实施例1,只是将pd的前驱体替换为硝酸钯,同时保持pd的质
量分数不变,得到催化剂pd/zsm-5-7,其中pd的负载量为0.5%wt。按照美国astm d5757-00标准测得的催化剂的磨损率为0.6%。
59.实施例4
60.催化剂的制备方法同实施例1,只是将活性中心负载步骤中的还原剂替换为等摩尔量的四羟甲基氯化磷和草酸和硼氢化钠,得催化剂pd/zsm-5-8和 pd/zsm-5-9,其中pd的负载量均为5%wt。按照美国astm d5757-00标准测得的催化剂的磨损率分别为0.6%和0.58%。
61.实施例5
62.催化剂的制备方法同实施例1,只是将活性中心负载步骤中的保护剂换为等摩尔量的聚乙烯醇、四羟甲基氯化磷和聚二甲基二丙烯氯化铵,得催化剂 pd/zsm-5-10、pd/zsm-5-11和pd/zsm-5-12,其中pd的负载量均为5%wt。按照美国astm d5757-00标准测得的催化剂的磨损率分别为0.6%、0.58%和 0.6%。
63.实施例6
64.实施例中催化剂的性能评价均采用小型的容量为1.2l的浆态床反应器进行。实验中评价采用的工作液为戊基蒽醌与乙基蒽醌的混合物,溶剂采用重芳烃和二异丁基甲醇的混合物。在反应器内加入800ml工作液与溶剂的混合物,然后 20g加氢催化剂,调节搅拌速度为500r/min,从反应器底部通入氢气并控制氢气流速为0.3l/min,采用液体恒流泵引入工作液并控制流速为10ml/min,系统的操作压力控制为0.05mpa(表压),加氢反应的温度控制在40℃。实验评价中采用了三种工作液,工作液溶剂和工作载体如表1所示。其中2-乙基蒽醌的浓度为125g/l,溶剂采用三甲苯和磷酸三辛酯体积为3:1的混合溶剂。催化剂的性能评价结果取自反应进行100h时,见表2。
65.表1工作液溶剂和工作载体配比
66.编号工作液溶剂溶剂体积比工作载体浓度(g/l)1三甲苯+磷酸三辛酯3:12-乙基蒽醌1252三甲苯+磷酸三辛酯3:12-戊基蒽醌1753三甲苯+二异丁基甲醇3:22-戊基蒽醌250
67.表2催化剂的性能评价结果
68.[0069][0070]
由表中结果可见,实施例1-5中的催化剂均表现出优异的催化剂活性,可见本发明中的载体以及采用的制备方法十分有效。
[0071]
贵金属催化剂在反应过程中负载的牢固度十分重要,也就是活性中心的流失速度,与催化剂的使用寿命息息相关。为此,将得到的催化剂采用编号3中的工作液溶剂,在实施例6的反应条件下评价1000h,催化剂的性能评价结果以及将此时的催化剂取出采用icp(电感耦合等离子体发射光谱仪)分析活性中心pd在催化剂上的含量,结果见表3。
[0072]
表3催化剂的性能结果以及icp测试结果
[0073][0074]
由表中结果可见,反应运转1000h后,实施例1的催化剂上活性中负载量变化较小,而对比例4的催化剂上活性中心出现明显的流失,表明本发明中采用的制备方法可以将活性中心牢固的负载在载体上,延长了催化剂的使用寿命,提高了催化剂的稳定性。