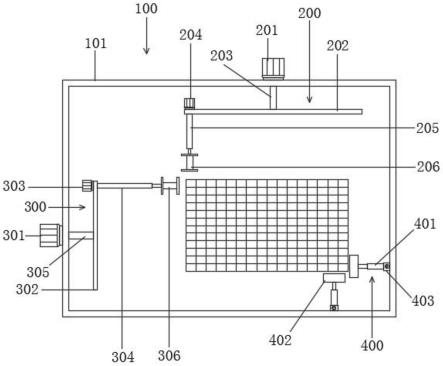
1.本发明涉及新材料制备技术领域,具体为氮磷持留和重金属固定的基生物炭复合材料的制备系统及方法。
背景技术:2.随着社会生产生活节奏的加快,工农业生产及生活中会产生大量的废弃生物质,如不充分加以利用就会腐败变质,不仅浪费了大量资源,还会造成严重的环境污染。目前,以水热法、微波裂解法或高温裂解法制备生物炭材料是利用废弃生物质的有效办法;生物炭具有比表面积高、活性官能团含量丰富等特点,可通过物理吸附和化学吸附等方式有效去除污水中的重金属及染料、农药等难降解有机污染物,是一种成本低廉的吸附剂。但以上述方法制备的生物炭,比表面积和吸附性能比商业活性炭差,如何提高生物炭的使用性能是生物炭的实际应用中所面临的主要问题;微电池法、光催化法和金属氧化物催化法等是目前降解有机污染物的常见方法。微电池法是利用铁-炭填料在电解质溶液中腐蚀形成无数微小的原电池来处理废水的电化学技术,又称内电解法,是利用废水中有些组分易被氧化、有些组分易被还原的特点,当这些不同属性组分相遇,且有导电介质时,电化学反应便会自发进行的方法。微电池法是集电解、混凝、电絮凝、吸附等多种物理化学作用于一体的废水处理方法。
3.现有的生物炭复合材料的制备系统及方法,制备出的生物体复合材料的表面吸附力很弱,对重金属的吸附效果差。
技术实现要素:4.鉴于现有氮磷持留和重金属固定的基生物炭复合材料的制备系统及方法中存在的问题,提出了本发明。
5.因此,本发明的目的是提供氮磷持留和重金属固定的基生物炭复合材料的制备系统及方法,通过设置表面强结合力增强装置,再在制备后的生物炭复合材料表面形成涂层,从而增强表面吸附力,解决了现有的生物炭复合材料的制备系统及方法,制备出的生物体复合材料的表面吸附力很弱,对重金属的吸附效果差的问题。
6.为解决上述技术问题,根据本发明的一个方面,本发明提供了如下技术方案:
7.氮磷持留和重金属固定的基生物炭复合材料的制备系统,包括离心机、烘干机、搅拌机和炭化炉,还包括表面强结合力增强装置;
8.所述表面强结合力增强装置包括支撑架,所述支撑架上安装有第一缠绕组件、第二缠绕组件和夹持组件;
9.所述第一缠绕组件包括第一伺服电机,所述第一伺服电机的输出轴固定连接第一转轴,所述第一转轴远离所述第一伺服电机的输出轴的一端固定连接第一转盘,所述第一转盘上固定安装有第二伺服电机,所述第二伺服电机的输出轴固定连接第一电动伸缩杆,
所述第一电动伸缩杆远离所述第二伺服电机的输出轴的一端固定连接第一卷轮;
10.所述第二缠绕组件包括第二卷轮,所述第二卷轮一端固定连接第二电动伸缩杆,所述第二电动伸缩杆远离所述第二卷轮的一端固定连接第三伺服电机的输出轴,所述第三伺服电机固定安装在第二转盘上,所述第二转盘一端固定连接第二转轴,所述第二转轴远离所述的一端固定连接第四伺服电机的输出轴。
11.作为本发明所述的氮磷持留和重金属固定的基生物炭复合材料的制备系统的一种优选方案,其中:所述第一转轴的外壁通过轴承转动连接所述支撑架,所述第一电动伸缩杆外壁通过轴承转动连接所述第一转盘,所述第一伺服电机固定安装在支撑架上。
12.作为本发明所述的氮磷持留和重金属固定的基生物炭复合材料的制备系统的一种优选方案,其中:所述第二电动伸缩杆外壁通过轴承转动连接所述第二转盘,所述第四伺服电机固定安装在所述支撑架上。
13.作为本发明所述的氮磷持留和重金属固定的基生物炭复合材料的制备系统的一种优选方案,其中:所述夹持组件包括第三电动伸缩杆,所述第三电动伸缩杆一端固定连接u形板,所述u形板内壁可拆卸连接第四电动伸缩杆,所述第四电动伸缩杆一端固定连接夹板。
14.作为本发明所述的氮磷持留和重金属固定的基生物炭复合材料的制备系统的一种优选方案,其中:所述u形板内壁固定连接第一固定座,所述第一固定座内壁插接所述第四电动伸缩杆,所述第一固定座和第四电动伸缩杆通过螺栓进行固定;所述第三电动伸缩杆远离所述u形板的一端插接第二固定座,所述第二固定座和第三电动伸缩杆通过螺栓进行固定。
15.作为本发明所述的氮磷持留和重金属固定的基生物炭复合材料的制备系统的一种优选方案,其中:所述第二固定座一端固定连接所述支撑架,所述夹持组件设有两组。
16.氮磷持留和重金属固定的基生物炭复合材料的制备方法,具体包括以下步骤:
17.s1,将有机废弃生物质在活化剂溶液中预处理,然后利用离心机进行离心、再利用烘干机进行烘干;
18.s2,将干燥的生物质粉末与还原性金属粉混合,并使用搅拌机混合均匀,利用炭化炉,在隔绝氧气的条件下炭化制备得到多孔生物炭材料,炭化温度为250-340℃,炭化时间为8-12h;还原性金属包括na和mg、zn、fe中的任意一种或多种,还原性金属粉占生物质粉末的质量比例为3%-5%;
19.s3,取步骤2得到的生物炭粉末加入到钛化合物的溶胶体系中浸泡,溶胶体系中钛化合物包括钛酸四丁酯、钛酸四乙酯、双钛酸二异丙酯、钛酸四丙酯中的任意一种或多种、高温无氧煅烧,然后加入金属盐溶液中负载金属氧化物,将生物炭粉末加入到钛化合物的溶胶体系中浸泡、高温无氧煅烧的步骤和加入金属盐溶液中负载金属氧化物的步骤分别重复至少三次,负载金属氧化物的步骤包括:将生物炭粉末加入到金属盐溶液中浸泡、煅烧和/或加入到金属盐溶液中进行水热反应,从而得到生物炭复合材料;
20.s4,将生物炭复合材料制成板状结构,在板状结构的生物炭复合材料上切割出相距0.1-0.18mm的凹槽,并且生物炭复合材料;将碳纤维缠绕在第一卷轮和第二卷轮上;启动第一伺服电机和第二伺服电机,第二伺服电机驱动第一卷轮旋转,从而对碳纤维进行释放,第一伺服电机带动第一转轴旋转,第一转轴带动第一转盘旋转,第一转盘通过第一电动伸
缩杆带动第一卷轮旋转,从而在板状结构的生物炭复合材料长度反向上缠绕一圈碳纤维;启动第四伺服电机和第三伺服电机,第三伺服电机带动第二卷轮旋转,从而对碳纤维进行释放,第四伺服电机带动第二转轴旋转,第二转轴带动第二转盘旋转,第二转盘带动第二电动伸缩杆旋转,第二电动伸缩杆带动第二卷轮旋转,从而在板状结构的生物炭复合材料宽度反向上缠绕一圈碳纤维;第一电动伸缩杆伸长,再在长度方向上缠绕一圈,第二电动伸缩杆伸长,再在宽度方向上缠绕一圈,循环在长度和宽度方向上进行缠绕;
21.s5将羟基磷灰石纳米带按照浓度为12~18g/l分散在无水乙醇中,优选设置为15g/l,然后将该溶液滴定于s4的碳纤维表面,溶液的滴定量为7~11ml/cm;
22.s6,将酚醛树脂粉末与无水乙醇按照质量百分比为10~18%混合,再按照6~10g/l的比例加入羟基磷灰石纳米带形成混合溶液;
23.s7,将缠绕碳纤维的生物炭复合材料浸泡在s5的混合溶液中。
24.s8,将s6的混合溶液滴定于s7处理后的生物炭复合材料的碳纤维表面;
25.s7,将s8处理后的生物炭复合材料置于硫化机中,在温度为165~175℃、压力为9~10mpa条件下处理30-40分钟,从而在生物炭复合材料表面形成生物涂层。
26.作为本发明所述的氮磷持留和重金属固定的基生物炭复合材料的制备方法的一种优选方案,其中:金属盐溶液包括氯化镁溶液、氯化锌溶液、氯化铝溶液、氯化铁溶液、硫酸铁溶液、硝酸铁溶液、醋酸铁溶液、氯化亚铁溶液、硫酸亚铁溶液、硝酸亚铁溶液和醋酸亚铁溶液中的任意三种或多种。
27.作为本发明所述的氮磷持留和重金属固定的基生物炭复合材料的制备方法的一种优选方案,其中:活化剂包括氢氧化钾、氢氧化钠、氯化锌、硫酸铵、氯化铵、硫酸亚铁、氢氧化铵、碳酸钠、磷酸、硝酸中的任意两种或多种。
28.作为本发明所述的氮磷持留和重金属固定的基生物炭复合材料的制备方法的一种优选方案,其中:浸泡在s7的混合溶液中的时间为8-12小时。
29.与现有技术相比:
30.1、通过设置表面强结合力增强装置,在生物炭复合材料表面缠绕碳纤维,并且宽度方向上和长度方向上的碳纤维是交错分布的,从而碳纤维不易脱落,能够长期维持生物炭复合材料表面的吸附力;
31.2、本发明提供的生物炭复合材料的制备方式简单,能耗低,便于批量生产,并且制备的生物炭材料本身具有很好的吸附力,且表面具有很多小孔,能够吸附更多的重金属。
附图说明
32.图1为本发明提供的表面强结合力增强装置的结构示意图;
33.图2为本发明提供的夹持组件的示意图;
34.图3为生物炭复合材料的sem图。
35.图中:表面强结合力增强装置100、支撑架101、第一缠绕组件200、第一伺服电机201、第一转盘202、第一转轴203、第二伺服电机204、第一电动伸缩杆205、第一卷轮206、第二缠绕组件300、第四伺服电机301、第二转盘302、第三伺服电机303、第二电动伸缩杆304、第二转轴305、第二卷轮306、夹持组件400、第三电动伸缩杆401、u形板402、第二固定座403、第一固定座404、第四电动伸缩杆405、夹板406。
具体实施方式
36.为使本发明的目的、技术方案和优点更加清楚,下面将结合附图对本发明的实施方式做进一步的详细描述。
37.本发明提供氮磷持留和重金属固定的基生物炭复合材料的制备系统,请参阅图1-3,包括离心机、烘干机、搅拌机和炭化炉,还包括表面强结合力增强装置100;
38.所述表面强结合力增强装置100包括支撑架101,支撑架101上安装有第一缠绕组件200、第二缠绕组件300和夹持组件400;
39.第一缠绕组件200包括第一伺服电机201,第一伺服电机201的输出轴固定连接第一转轴203,第一转轴203远离第一伺服电机201的输出轴的一端固定连接第一转盘202,第一转盘202上固定安装有第二伺服电机204,第二伺服电机204的输出轴固定连接第一电动伸缩杆205,第一电动伸缩杆205远离第二伺服电机204的输出轴的一端固定连接第一卷轮206,第一转轴203的外壁通过轴承转动连接支撑架101,第一电动伸缩杆205外壁通过轴承转动连接第一转盘202,第一伺服电机201固定安装在支撑架101上;
40.第二缠绕组件300包括第二卷轮306,第二卷轮306一端固定连接第二电动伸缩杆304,第二电动伸缩杆304远离第二卷轮306的一端固定连接第三伺服电机303的输出轴,第三伺服电机303固定安装在第二转盘302上,第二转盘302一端固定连接第二转轴305,第二转轴305远离的一端固定连接第四伺服电机301的输出轴,第二电动伸缩杆304外壁通过轴承转动连接第二转盘302,第四伺服电机301固定安装在支撑架101上。
41.夹持组件400包括第三电动伸缩杆401,第三电动伸缩杆401一端固定连接u形板402,u形板402内壁可拆卸连接第四电动伸缩杆405,第四电动伸缩杆405一端固定连接夹板406,u形板402内壁固定连接第一固定座404,第一固定座404内壁插接第四电动伸缩杆405,第一固定座404和第四电动伸缩杆405通过螺栓进行固定;第三电动伸缩杆401远离u形板402的一端插接第二固定座403,第二固定座403和第三电动伸缩杆401通过螺栓进行固定,第二固定座403一端固定连接支撑架101,夹持组件400设有两组。
42.氮磷持留和重金属固定的基生物炭复合材料的制备方法,具体包括以下步骤:
43.s1,将有机废弃生物质在活化剂溶液中预处理活化剂包括氢氧化钾、氢氧化钠、氯化锌、硫酸铵、氯化铵、硫酸亚铁、氢氧化铵、碳酸钠、磷酸、硝酸中的任意两种或多种,然后利用离心机进行离心、再利用烘干机进行烘干;
44.s2,将干燥的生物质粉末与还原性金属粉混合,并使用搅拌机混合均匀,利用炭化炉,在隔绝氧气的条件下炭化制备得到多孔生物炭材料,炭化温度为250-340℃,优选设置为295℃,炭化时间为8-12h,优选设置为10h;还原性金属包括na和mg、zn、fe中的任意一种或多种,还原性金属粉占生物质粉末的质量比例为3%-5%,优选设置为4%;
45.s3,取步骤2得到的生物炭粉末加入到钛化合物的溶胶体系中浸泡,溶胶体系中钛化合物包括钛酸四丁酯、钛酸四乙酯、双钛酸二异丙酯、钛酸四丙酯中的任意一种或多种、高温无氧煅烧,然后加入金属盐溶液中负载金属氧化物,金属盐溶液包括氯化镁溶液、氯化锌溶液、氯化铝溶液、氯化铁溶液、硫酸铁溶液、硝酸铁溶液、醋酸铁溶液、氯化亚铁溶液、硫酸亚铁溶液、硝酸亚铁溶液和醋酸亚铁溶液中的任意三种或多种,将生物炭粉末加入到钛化合物的溶胶体系中浸泡、高温无氧煅烧的步骤和加入金属盐溶液中负载金属氧化物的步骤分别重复至少三次,负载金属氧化物的步骤包括:将生物炭粉末加入到金属盐溶液中浸
泡、煅烧和/或加入到金属盐溶液中进行水热反应,从而得到生物炭复合材料;
46.s4,将生物炭复合材料制成板状结构,在板状结构的生物炭复合材料上切割出相距0.1-0.18mm的凹槽,优选设置为0.14mm,并且生物炭复合材料;将碳纤维缠绕在第一卷轮206和第二卷轮306上;启动第一伺服电机201和第二伺服电机204,第二伺服电机204驱动第一卷轮206旋转,从而对碳纤维进行释放,第一伺服电机201带动第一转轴203旋转,第一转轴203带动第一转盘202旋转,第一转盘202通过第一电动伸缩杆205带动第一卷轮206旋转,从而在板状结构的生物炭复合材料长度反向上缠绕一圈碳纤维;启动第四伺服电机301和第三伺服电机303,第三伺服电机303带动第二卷轮306旋转,从而对碳纤维进行释放,第四伺服电机301带动第二转轴305旋转,第二转轴305带动第二转盘302旋转,第二转盘302带动第二电动伸缩杆304旋转,第二电动伸缩杆304带动第二卷轮306旋转,从而在板状结构的生物炭复合材料宽度反向上缠绕一圈碳纤维;第一电动伸缩杆205伸长,再在长度方向上缠绕一圈,第二电动伸缩杆304伸长,再在宽度方向上缠绕一圈,循环在长度和宽度方向上进行缠绕;
47.s5将羟基磷灰石纳米带按照浓度为12~18g/l分散在无水乙醇中,然后将该溶液滴定于s4的碳纤维表面,溶液的滴定量为7~11ml/cm,优选设置为9ml/cm;
48.s6,将酚醛树脂粉末与无水乙醇按照质量百分比为10~18%混合,优选设置为14%,再按照6~10g/l(优选设置为8g/l)的比例加入羟基磷灰石纳米带形成混合溶液;
49.s7,将缠绕碳纤维的生物炭复合材料浸泡在s5的混合溶液中8-12小时,优选设置为10h。
50.s8,将s6的混合溶液滴定于s7处理后的生物炭复合材料的碳纤维表面;
51.s7,将s8处理后的生物炭复合材料置于硫化机中,在温度为165~175℃,优选设置为170℃、压力为9~10mpa(优选设置为9.5mpa)条件下处理30-40分钟,优选设置为35分钟,从而在生物炭复合材料表面形成生物涂层。
52.虽然在上文中已经参考实施方式对本发明进行了描述,然而在不脱离本发明的范围的情况下,可以对其进行各种改进并且可以用等效物替换其中的部件。尤其是,只要不存在结构冲突,本发明所披露的实施方式中的各项特征均可通过任意方式相互结合起来使用,在本说明书中未对这些组合的情况进行穷举性的描述仅仅是出于省略篇幅和节约资源的考虑。因此,本发明并不局限于文中公开的特定实施方式,而是包括落入权利要求的范围内的所有技术方案。