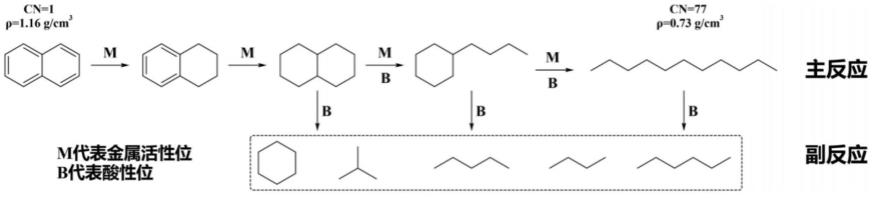
1.本发明属于煤焦油加氢制取柴油技术领域,具体涉及一种煤焦油加氢制柴油用催化剂及其制备与应用。
背景技术:2.随着我国经济高速发展,能源安全供应问题已日益成为我国可持续发展的重大战略问题。在石油对外依赖度居高不下的情况下,拓展能源燃料途径,开发深加工技术和产品具有重要的经济价值和战略意义。煤焦油作为煤炼焦、热解和气化过程中的副产物,其国内产量已超过2000万吨/年。目前,国内煤焦油的加工利用一部分用于提取工业萘和酚等化学品。另一部分经简单处理后直接燃烧,但直接燃烧会生成大量no
x
、so
x
等有毒气体和固体颗粒,对大气环境污染严重。
3.目前国内煤焦油加氢生产柴油技术在迅速发展,通过加氢技术可以使柴油脱硫氮和部分脱芳烃。但该柴油十六烷值仍然较低,其主要原因是柴油中含有大量饱和环烷烃。通过对柴油中饱和环烷烃的加氢开环可以进一步提高柴油十六烷值和降低柴油密度,从而提高柴油品质。
4.煤焦油加氢技术的目标是生产低密度优质柴油并尽可能提高油品收率,其关键在于催化剂。该催化剂需要同时具备高加氢金属活性位和合适的酸性以提供加氢活性和开环活性,同时避免催化剂酸性太高导致油品过度裂解而导致的柴油收率下降。多环芳烃加氢开环路径是加氢生成饱和环烷烃,之后将饱和环烷烃异构化,最后将异构化产物开环生成开环产物,以萘加氢开环为例,其反应路径、十六烷值以及密度变化如下所示:
[0005][0006]
催化剂的组成(金属活性组分、助剂和载体)和制备方法(焙烧温度、预处理试剂和温度)对催化剂的性能有着决定性的影响。在催化剂各种组分相同的条件下,不同的制备方法会导致催化剂的各种性能(活性组分分散度、晶粒大小、催化剂孔径分布以及比表面积)有较大差异,从而导致催化剂反应活性有较大区别。
[0007]
国内外对煤焦油加氢技术已有了较多的研究,但主要集中在贵金属催化剂。us 6241876b1公布了一种以hy分子筛为载体的高加氢活性贵金属催化剂,该催化剂可以在较低温度条件下对煤焦油加氢以提高柴油十六烷值。cn200810104303.2公布了一种用于柴油深度加氢脱芳烃的贵金属催化剂,经该催化剂脱芳烃的柴油十六烷值较高。cn103480408a公布了一种以usy分子筛和氧化铝为载体,负载贵金属和稀土元素的柴油加氢催化剂。但在工业应用过程中,经脱硫脱氮的催化剂仍含有一定的硫和氮,贵金属催化剂容易中毒失活。因此其催化剂寿命较短,不适宜工业应用。近期,国内研究人员开始采用过渡金属催化剂进
行相关研究。cn104646052 a公布了一种过渡金属催化剂并采用氟和磷作为助剂,该催化剂对双环芳烃的开环活性较高。cn109097099 a公布了一种以碘为助剂的过渡金属催化剂,该催化剂可在脱除煤焦油中硫氮的同时,也能使芳烃饱和或异构化。总体来说,上述公开的煤焦油加氢催化剂各具特点,贵金属加氢活性高,但其价格昂贵且容易中毒失活。过渡金属催化剂价格低廉,但过渡金属通常采用硫化处理,其加氢活性较低。
技术实现要素:[0008]
本发明针对煤焦油加氢处理馏分油的组成特点,以高十六烷值、高收率和低密度柴油为目标产物。通过对过渡金属碳化预处理,以制备高加氢活性的过渡金属碳化物为催化剂。
[0009]
为实现上述目的,本发明是通过以下技术方案来实现:
[0010]
本发明第一方面提供了一种煤焦油加氢制柴油用催化剂,包括载体以及位于载体上的金属活性组分和助剂;所述载体为usy分子筛和kit-5分子筛,以调控催化剂载体酸性和孔径;所述金属活性组分为co、mo、ni和w的水溶性盐中的一种或多种,以调控催化剂加氢活性;所述助剂为f、p和k的水溶性盐类中的一种或多种,以改善催化剂酸性和金属活性组分分散度。所述载体占催化剂总质量的30%-85%,金属活性组分占催化剂总质量的10%-40%,助剂占催化剂总质量的0.2%-2.5%。
[0011]
进一步,所述co、mo、ni和w的水溶性盐包括硝酸钴、钼酸铵、硝酸镍和偏钨酸铵;f、p和k的水溶性盐包括氟化钾、磷酸钾和硝酸钾。
[0012]
本发明第二方面提供了上述煤焦油加氢制柴油用催化剂的制备方法,包括如下步骤:
[0013]
步骤1:将原位碳化剂溶于去离子水中搅拌均匀,再加入usy分子筛和kit-5分子筛,剧烈搅拌,烘干得到催化剂载体;
[0014]
步骤2:将金属活性组分和助剂溶于去离子水中搅拌均匀,通过共浸渍法负载于催化剂载体上,烘干得到催化剂前驱体;
[0015]
步骤3:将上述催化剂前驱体在h2/n2混合气气氛下进行碳化还原处理,得到所述催化剂。
[0016]
进一步,所述步骤1中原位碳化剂为羟乙基纤维素、葡萄糖、果糖和麦芽糖中的一种。
[0017]
进一步,所述步骤1中分子筛质量比为:usy/kit-5=0.3-2;原位碳化剂占催化剂质量的1%-15%。
[0018]
进一步,所述步骤1中剧烈搅拌的时间为2-5h,烘干温度为80-100℃,烘干时间为10-20h。
[0019]
进一步,所述步骤2中烘干温度为80-100℃,时间为10-20h;
[0020]
进一步,所述步骤2中金属活性组分为硝酸钴、钼酸铵、硝酸镍、偏钨酸铵的一种或多种;助剂为氟化钾、磷酸钾、硝酸钾的一种或多种。
[0021]
进一步,所述步骤3中h2/n2混合气流速为50-120ml/min;碳化还原过程采用程序升温模式,常温以升温速率5-10℃/min升至500℃,再以升温速率2-3℃/min升至终温700-1000℃,最后在终温下保持3-5h。
[0022]
本发明第三方面提供了上述煤焦油加氢制柴油用催化剂的的应用,具体为:将所述催化剂置于固定床用于煤焦油加氢制柴油时,其反应条件为:氢油体积比为400-1200,反应压力为5-10mpa,反应温度为300-500℃,液体空速为0.1-1.2h-1
。
[0023]
与现有技术相比,本发明的有益效果如下:
[0024]
本发明所述催化剂针对煤焦油芳烃含量高、硫氮含量高以及十六烷值低等特点,开发出高加氢活性、高脱硫氮能力和高开环能力的催化剂。相较于传统碳化法(ch4/h2),上述催化剂采用可溶于水的糖类为原位碳化剂,可缩短碳化用时、减少表面催化剂表面积碳和降低传统碳化方法成本,同时提高催化剂金属活性位和反应活性。经上述催化剂催化反应后,生产的柴油具有密度低、硫氮含量低和十六烷值高等优点。
具体实施方式
[0025]
以下所述实例以本发明技术方案为前提进行实施,给出了详细的实施方式和具体的操作过程,但并不限制本发明专利的保护范围,凡采用等同替换或等效变换的形式所获得的技术方案,均应落在本发明的保护范围之内。
[0026]
实施例1
[0027]
取2g羟乙基纤维素(占催化剂总质量的1%)加入到去离子水中搅拌均匀,在该水溶液中加入usy分子筛和kit-5分子筛,剧烈搅拌3h。将搅拌好的溶液在100℃下烘干10h以确保载体不含水分,得到催化剂载体。控制上述分子筛质量比为usy/kit-5=0.5。
[0028]
催化剂金属活性组分为硝酸钴和钼酸铵,助剂采用磷酸钾。将催化剂活性组分和助剂溶于去离子水中搅拌均匀,采用等体积共浸渍法将溶液均匀负载在催化剂载体上并在80℃下烘干10h得到催化剂前驱体。其中,硝酸钴、钼酸铵和磷酸钾分别占催化剂总质量的5.5%、18%和0.3%。
[0029]
取3g上述催化剂前驱体置于固定床反应管中部,反应管通入h2含量为20%的h2/n2混合气,混合气流速为50ml/min。将反应管温度以5℃/min从常温升温至500℃,之后以2℃/min的升温速率升温至700℃,并保持3h。之后将气体切为氢气并调节工艺调节,具体工艺条件为:氢油体积比500,反应温度350℃,反应压力:5mpa,液体空速为0.2h-1
,催化评价结果见表1。
[0030]
实施例2
[0031]
取10g葡萄糖(占催化剂总质量的5%)加入到去离子水中搅拌均匀,在该水溶液中加入usy分子筛和kit-5分子筛,剧烈搅拌4h。将搅拌好的溶液在80℃下烘干10h以确保载体不含水分,得到催化剂载体。控制上述分子筛质量比为usy/kit-5=0.8。
[0032]
催化剂金属活性组分为硝酸钴和偏钨酸铵,助剂采用氟化钾。将催化剂活性组分和助剂溶于去离子水中搅拌均匀,采用等体积共浸渍法将溶液均匀负载在催化剂载体上并在100℃下烘干10h得到催化剂前驱体。其中,硝酸钴、偏钨酸铵和氟化钾分别占催化剂总质量的7%、21%和0.5%。
[0033]
取3g上述催化剂前驱体置于固定床反应管中部,反应管通入h2含量为20%的h2/n2混合气,混合气流速为70ml/min。将反应管温度以3℃/min从常温升温至500℃,之后以2.5℃/min的升温速率升温至800℃,并保持5h。之后将气体切为氢气并调节工艺调节,具体工艺条件为:氢油体积比800,反应温度380℃,反应压力:6mpa,液体空速为0.5h-1
,催化评价结
果见表1。
[0034]
实施例3
[0035]
取20g果糖(占催化剂总质量的10%)加入到去离子水中搅拌均匀,在该水溶液中加入usy分子筛和kit-5分子筛,剧烈搅拌4h。将搅拌好的溶液在80℃下烘干10h以确保载体不含水分,得到催化剂载体。控制上述分子筛质量比为usy/kit-5=1.5。
[0036]
催化剂金属活性组分为硝酸镍和偏钨酸铵,助剂采用硝酸钾。将催化剂活性组分和助剂溶于去离子水中搅拌均匀,采用等体积共浸渍法将溶液均匀负载在催化剂载体上并在100℃下烘干10h得到催化剂前驱体。其中,硝酸镍、偏钨酸铵和硝酸钾分别占催化剂总质量的5.5%、18%和1.5%。
[0037]
取3g上述催化剂前驱体置于固定床反应管中部,反应管通入h2含量为20%的h2/n2混合气,混合气流速为90ml/min。将反应管温度以5℃/min从常温升温至500℃,之后以2.5℃/min的升温速率升温至800℃,并保持5h。之后将气体切为氢气并调节工艺调节,具体工艺条件为:氢油体积比1000,反应温度400℃,反应压力:6mpa,液体空速为0.8h-1
,催化评价结果见表1。
[0038]
实施例4
[0039]
取30g麦芽糖(占催化剂总质量的15%)加入到去离子水中搅拌均匀,在该水溶液中加入usy分子筛和kit-5分子筛,剧烈搅拌4h。将搅拌好的溶液在90℃下烘干10h以确保载体不含水分,得到催化剂载体。控制上述分子筛质量比为usy/kit-5=2。
[0040]
催化剂金属活性组分为硝酸镍和钼酸铵,助剂采用氟化钾。将催化剂活性组分和助剂溶于去离子水中搅拌均匀,采用等体积共浸渍法将溶液均匀负载在催化剂载体上并在100℃下烘干10h得到催化剂前驱体。其中,硝酸镍、钼酸铵和氟化钾分别占催化剂总质量的4%、22%和2%。
[0041]
取3g上述催化剂前驱体置于固定床反应管中部,反应管通入h2含量为20%的h2/n2混合气,混合气流速为100ml/min。将反应管温度以3℃/min从常温升温至500℃,之后以3℃/min的升温速率升温至800℃,并保持5h。之后将气体切为氢气并调节工艺调节,具体工艺条件为:氢油体积比400,反应温度450℃,反应压力:8mpa,液体空速为1h-1
,催化评价结果见表1。
[0042]
对比例1
[0043]
在去离子水中加入usy分子筛和kit-5分子筛,剧烈搅拌3h。将搅拌好的溶液在100℃下烘干10h以确保载体不含水分,得到催化剂载体。控制上述分子筛质量比为usy/kit-5=0.5。
[0044]
催化剂金属活性组分为硝酸钴和钼酸铵,助剂采用磷酸钾。将催化剂活性组分和助剂溶于去离子水中搅拌均匀,采用等体积共浸渍法将溶液均匀负载在催化剂载体上并在80℃下烘干10h得到催化剂前驱体。其中硝酸钴、钼酸铵和磷酸钾分别占催化剂总质量的5.5%、18%和0.3%。
[0045]
取3g上述催化剂前驱体置于固定床反应管中部,反应管通入ch4含量为20%的ch4/h2混合气,混合气流速为50ml/min。将反应管温度以5℃/min从常温升温至500℃,之后以2℃/min的升温速率升温至700℃,并保持3h。之后将气体切为氢气并调节工艺调节,具体工艺条件为:氢油体积比500,反应温度350℃,反应压力:5mpa,液体空速为0.2h-1
。与实施例1
相比,该对比例采用传统的ch4/h2混合气为碳化还原剂,催化评价结果见表1。
[0046]
表1本发明实施例和对比例所得煤焦油加氢制柴油用催化剂的评价结果
[0047][0048]
*金属活性位占比指经co滴定测得的碳化态金属活性位占催化剂的摩尔比。