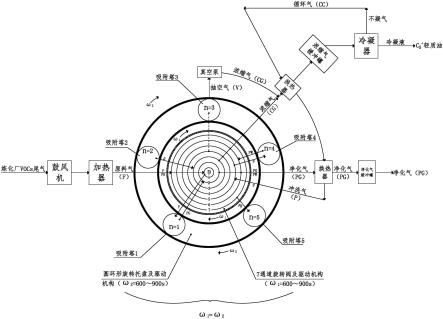
一种vocs尾气的全温程模拟旋转移动床变压吸附净化与回收工艺
技术领域
1.本发明属于工业尾气治理与回收利用领域,涉及尾气的变压吸附净化,更具体的说是涉及一种含vocs尾气的全温程模拟旋转移动床净化与回收工艺。
背景技术:2.在生物制药、煤化工以及炼化厂原油加工及化工产品等生产过程中产生一些含有或具有挥发性很大且浓度较高的轻烃类或苯环烃类或有机物组分组成的尾气或废气,如苯、甲苯、二甲苯、萘、丙酮、己烷、碳二及碳二以上烃类(c
2+
)、苯酚、轻质焦油,以及甲醇/水等混合组分这些易挥发烃类及有机物组分(vocs)复杂,不但造成烃类及有机物损失,而且造成周边环境的恶臭污染。
3.目前,处理含vocs尾气或废气通常使用的方法有吸附法、焚烧法、催化燃烧法、冷凝法及吸收法等。吸附法具有技术成熟、简单易行、治理成本低及适应范围广等优点,在vocs尾气或废气治理技术中占有较大的市场份额,尤其是在生物制药、煤化工及炼化厂与异味治理等领域都得到了广泛应用。
4.现有的吸附法对烃类的净化或回收通常采用常规的轴向流固定床变温吸附(tsa)工艺,其装载吸附塔里的吸附剂多为活性炭或活性碳纤维等,或一塔离线再生或二塔在线再生,比如,已公开的专利cn03254728.5、cn03254729.3、cn200410023944.7、cn02805902.6及cn00118594.2等均提出了由活性炭的固定床变温吸附(tsa)对烃类或易挥发有机物组分进行吸附,然后进行蒸汽解吸冷凝回收或真空解吸溶剂吸收回收的方法。这些方法的主要优点是吸附量较大,吸附效率较高,成本低,排放尾气容易达到环保指标要求。但是,由于固定床吸附剂再生通常需要较高通入较高温度的蒸汽或惰性再生气进行再生,吸附量越大或吸附越容易,吸附剂解吸再生就越困难,尤其是对vocs浓度较高的生物制药与煤化工及炼化厂尾气发生深度吸附或vocs组分在吸附剂上浓缩的程度很高时容易导致燃烧或与含有氧原子的水蒸气发生化学反应而使得吸附剂失火、粉化或飞温等所引起的安全事故就越有可能。另外,变温吸附(tsa)吸附与解吸的循环操作过程中升温与冷却的周期较长,为了能够实现一塔吸附另一塔再生的交替连续净化,吸附周期就可能延长,导致深度吸附或vocs浓缩程度加大,进一步增加了发生安全事故的几率。为此,工业上多采用三个或四个吸附塔并联的tsa工艺来应对解吸再生周期较长的工况。但发生深度吸附或安全事故的风险依然没有完全消除。
5.除了传统的轴向流固定床tsa工艺及系统用于vocs尾气处理及回收外,国内外出现了一种转轮变温吸附(rwtsa)工艺及系统,tsa 转轮吸附器不同于传统的多个固定床吸附器,它由一个吸附转轮旋转而循环通过固定不变的吸附、加热再生、冷却三个不同功能的操作区域,达到连续净化气体的目的,而无须一系列的吸附器和程序控制阀门。由于它大都采用传质快、解吸容易、压力较小的蜂窝状规整吸附剂,可以使循环的周期大为缩短,使得装置更紧凑、运行更可靠,避免了安全隐患,特别适合于处理化工、半导体、汽车、合成皮革
等工业排放的含有vocs 的低压废气。但是,rwtsa工艺及系统比较适用于vocs浓度较低的工况,比如,vocs浓度小于0.1%,其浓缩度达到10~20倍,脱除率也达到97%以上,通常被用作废气焚烧装置的气体预浓缩系统,以降低焚烧成本。rwtsa吸附器及规整型吸附剂大都是由无机材料制成,因此,其本身的不燃性在处理vocs 时比使用活性炭要安全得多,但也发生过因rwtsa吸附转轮表面积累高沸点vocs 过多,而引发吸附剂沸石转轮闷烧的事故,因此,应定期用水冲洗清除沉积在转轮上的高沸点vocs 以恢复其吸附性能。有的用水冲洗清除不掉,只能拆下用高温(300~1000℃)煅烧炭化及水蒸气活化的方法清除,但往往容易造成规整吸附剂部分微孔结构的破坏,导致失去吸附能力而被迫更换转轮,成本大幅度上升。由于生物制药、煤化工及炼化厂vocs尾气中高沸点烃类及诸如酮醚醇酯类的易挥发有机物质较多,必须再增加一个冷凝器,用冷凝的方式脱除或回收这些烃类或易挥发有机物,以免它们堵塞转轮的气流通道和吸附表面,从而可延长转轮吸附器的使用寿命。如果尾气温度过高,还须将尾气冷却至环境温度。其次,转轮吸附器的缺点是其床层高度短,传质效率低于轴向流固定床吸附器,净化度不及后者,并且处理能力有限,当处理规模较大时,需要多个rwtsa吸附器并联运行,投资大幅度增加。另外,rwtsa装置对动态密封的要求很高,必须能承受较大的温度变化所产生的温差应力,并且对含有较为复杂组分的生物制药、煤化工与炼化厂vocs尾气处理工况,对于必须脱除较高毒性或极性的吸附质时,如氨、水、轻质焦油、苯萘及其衍生物等杂质组分,其相对低的脱除率会影响它的应用。
6.通常,回收vocs或易挥发有机物溶剂主要是采用活性炭作吸附剂,蒸汽再生的tsa 方法,自从psa 工艺开发成功后,由于操作在常温下进行,对热稳定性差的溶剂诸如氟利昂、甲基乙基酮等分离有利,同时也在很大程度上避免了吸附剂上有机物累积而发生闷烧,对气体中含0.1~0.5%(v/v)以上高浓度的vocs分离能耗较低,有逐步取代tsa工艺的趋势。比如,采用psa 工艺从含0.5%的二氯甲烷的工厂废气中回收二氯甲烷,鼓风机将废气抽送至二塔组成的vsa 系统,塔内装填有高硅铝比、具有疏水性质的zms-5 分子筛,吸附压力约为0.1mpa,塔顶排出的气体中的二氯甲烷浓度约为10~100ppmv,吸附下来的二氯甲烷在再生期间通过真空泵抽出,其二氯甲烷的浓度约为20%,经冷凝后液化回收,未被冷凝的二氯甲烷则返回psa入口进一步回收二氯甲烷。然而,psa方法仍然有诸多的问题,第一,psa方法净化或回收vocs,要求含vocs超过一定的浓度,一般是单组分浓度要大于0.1%,vocs浓度太低而使得其分压过低,导致psa吸附效率低下,吸附与解吸周期过长,成本高,并仍有易燃的高沸点物质累积而发生吸附剂闷烧的危险;第二,净化纯度低。比如,上述回收二氯甲烷的psa工艺中,吸附塔顶排出的非吸附相气体中仍含有10~100ppmv的二氯甲烷,直接排放是不符合更加严格的大气排放要求(小于10ppmv),尤其是生物制药行业中的异味与恶臭组分,若存有1ppmv以上,就使得周边的居民闻得到,会对身心及人体器官伤害;第三,psa方法不适合成分复杂的vocs尾气的处理工况,尤其是生物制药、煤化工及炼化厂生产过程中产生的含vocs尾气,这是由于常规的psa工艺都是采用轴向流固定的吸附床层,虽然可以利用多种吸附剂形成的复合吸附剂床层来应对vocs尾气中的多种复杂组分的吸附工况,但由于这些多种组分在常温或环境温度下的吸附能力相差较大,而且大多数组分均是沸点比较高、极性比较强的,极其容易被深度吸附导致解吸再生困难,因为抽真空的程度有限,工业上的最大真空度为-0.09~0.08mpa,吸附塔底靠近抽真空的吸附剂床层容易被解吸再生,吸附塔上部尤其是靠近塔顶的吸附剂床层因抽真空力度的减弱而难以解吸再生完全,而且上部的
吸附剂往往是孔径较小的分子筛,一旦vocs被深度吸附,是很难通过抽真空方式实现吸附剂的解吸再生完全,这会导致vocs杂质组分在分子筛上累积,极其容易使得非吸附相的气体中vocs含量因穿透而超标,不能满足大气排放的要求;第四,传统的轴向流固定床psa 工艺中所存在的“纯度与收率之间呈现反比关系”的矛盾非常突出,尤其是vocs浓度较低的工况非常明显,psa工艺的净化或回收的效率非常低,投入产出比较低,没有良好的经济性;第五,psa工艺装置需要较多的程序控制阀门及调节阀门来配套实现压力变化的控制,导致装置的动态设备投资高、操作稳定性较差、吸附与解吸再生的循环操作匹配性差,尤其是常压吸附与抽真空解吸的vsa工艺。
技术实现要素:7.本发明的目的在于:为了解决含vocs尾气处理中现有技术存在的包括高浓度、高沸点组分在变温吸附(tsa)与变压吸附(psa)循环操作过程中的累积发生燃烧或化学反应而引起的安全隐患以及“纯度与收率之间呈现反比关系”的矛盾突出、装置稳定性较差在内的诸多问题,提供了一种vocs尾气的全温程模拟旋转移动床变压吸附(full temperature range simulated rotated moving psa——ftrsrmpsa)净化与回收新工艺,该工艺是一种以轴向流固定床全温程变压吸附(ftrpsa)为基础,利用vocs尾气中高沸点的易挥发组分与低沸点的惰性气体组分之间在60~130℃温度范围及常压至1.0mpa压力范围的物理化学性质与相对吸附分离系数的差异性,将置于一多通道旋转阀中央且在其周围安置于一圆环形旋转托盘上装载有一种或多种吸附剂且具有一定高径比的多个轴向流固定床吸附塔且通过管道连接以及调控旋转阀旋转方向与旋转速度(ω1)、圆环形旋转托盘旋转方向与旋转速度(ω2),使得流经多通道旋转阀通道及通道进出口端与圆环形旋转托盘上的吸附塔进出口端连接的管道及吸附塔中旋转移动的吸附床层的气体,在不断地通过进出每个吸附塔进出口的位置及每个吸附床层在旋转同时完成各自的吸附与解吸步骤的传质,进而形成了“模拟旋转移动床”的变压吸附过程,实现了轴向流固定床全温程变压吸附基础上的模拟旋转移动床变压吸附过程,使得含vocs尾气的净化与回收的吸附与解吸快速而多步骤的循环操作,在实现vocs的回收率与净化纯度“双高”及避免/缓解深度吸附、共吸附及竞争性吸附的同时,适用于各种含vocs尾气作为原料气相应的流量、组分浓度、压力或温度的波动工况,充分利用了轴向流固定床全温程变压吸附、旋转轮吸附及模拟移动床的各种优势,克服了现有技术工艺的缺陷,具体方案如下:一种vocs尾气的全温程模拟旋转移动床变压吸附净化与回收方法,所述的全温程模拟旋转移动床变压吸附(ftrsrmpsa)系统是由n(2≤n≤20的自然整数)个装载有多种吸附剂且具有一定高径比的轴向流固定床层吸附塔,且安置在一个以旋转速度(ω2,秒(s)为单位)的圆环形旋转托盘上的吸附塔、有m(4≤m≤36的自然整数)个通道并安置在圆环形旋转托盘中央以旋转速度(ω1,秒(s)为单位)旋转的多通道旋转阀、多通道旋转阀与系统外物料气体进出的物料管道以及连接于经圆环形托盘内置管道至吸附塔上下与多通道旋转阀之间的工艺管道,以及相应的驱动圆环形旋转托盘及多通道旋转阀旋转方向及其调控其旋转速度(ω1与ω2)的驱动机构、缓冲罐、加热器/冷却器/换热器、真空泵/冷凝器/或压缩机所构成而形成一个ftrsrmpsa系统,其特征在于,吸附塔进出口与m通道旋转阀进出口连接的管道是通过预设在圆环形旋转托盘的内置管道相连形成工艺管道且与m通道旋转阀通
道数m相同,进出ftrsrmpsa系统物料气体的位置是由m通道旋转阀旋转的通道加以交替分配来固定,其物料气体包括含vocs尾气为原料气(f)、净化气(pg)为排放气、冲洗气(p)、终充气(fr)、逆放(d)气或/与抽真空气(v)或/与冲洗废气(pw)组成的解吸气(d)为浓缩气(cg)以及不凝气体组成的循环气(cc),并相应的连接包括缓冲罐(器)、加热器/冷却器/换热器/冷凝器/压缩机/抽真空泵/循环泵在内的设备,由m通道旋转阀进出口与吸附塔进出口之间通过圆环形旋转托盘中内置管道连接的工艺管道中工艺气体流动的位置是移动变化的,工艺气体是在ftrsrmpsa系统内流动,包括原料气(f)、净化气(pg)、冲洗气(p)、均压降气(ed)、顺放气(pp)\逆放气(d)气或/与抽真空气(v)或/与冲洗废气(pw)组成的解吸气(d)为浓缩气(cg)、均压升气(er)、终充气(fr)以及循环气(cc),具体的含vocs尾气的吸附与解吸的循环过程为,来自ftrsrmpsa系统外的含vocs尾气为原料气(f),直接或经过加热器/换热器加热至60~130℃、直接或经鼓风机或压缩机增压至0.2~1.0mpa,进入m通道旋转阀中的原料气(f)通道进口,并经m通道旋转阀原料气(f)通道及出口、圆环形旋转托盘内置管道及圆环形旋转托盘上对应的处于吸附状态的一个或多个轴向流固定床吸附塔进口连接的工艺管道,从吸附塔底部进入进行吸附(a)步骤,经过m通道旋转阀旋转方向及旋转速度(ω1)与圆环形旋转托盘旋转方向及旋转速度(ω2)之间的调控匹配连续地步进,从吸附塔顶部流出的非吸附相气体经工艺管道进入m通道旋转阀净化气(pg)通道,并从m通道旋转阀净化气(pg)通道流出并经换热冷却至常温后进入净化气(pg)缓冲罐后,或直接排放,或输出使用,净化气(pg)中的vocs浓度小于等于1ppmv,处于吸附状态的吸附塔在完成吸附(a)步骤后,随着m通道旋转阀与圆环形旋转托盘继续旋转步进,结束吸附(a)步骤的吸附塔进入或顺放(pp)或/与均压降(ed)步骤,顺放(pp)步骤流出的顺放气(pp)作为冲洗气(p)流经圆环形旋转托盘内置管道、m通道旋转阀顺放气(pp)通道、圆环形旋转托盘其它内置管道以及其它处于冲洗(p)步骤的吸附塔进行冲洗(p),结束顺放(pp)步骤的吸附塔,随后对另一个处于均压升(er)状态的吸附塔通过系统内的工艺管道进行均压降(ed),结束均压降(ed)步骤的吸附塔,随着m通道旋转阀与圆环形旋转托盘持续地旋转步进而进入逆放(d)或/与抽真空(v)或/与冲洗(p)步骤,从吸附塔流出的逆放气(d)或/与抽真空气(v)或/与冲洗废气(pw)所形成的解吸气(d)作为浓缩气(cg),流经圆环形旋转托盘内置管道以及m通道旋转阀逆放气(d)/抽真空气(v)/冲洗废气(pw)通道及其出口端流出所形成的解吸气(d)作为浓缩气(cg),或直接进入焚烧系统焚烧处理,或经过换热冷却后进入浓缩气(cg)缓冲罐后再经过冷凝器冷凝,形成的冷凝液为回收的vocs溶剂,形成的不凝气体经过换热加热及/或加压后作为循环气(cc),或经循环泵直接返回原料气(f),或作为冲洗气(p),或作为终充气(fr)使用,由此,vocs的净化脱除率或回收率达到98%以上,结束逆放(d)或/与抽真空(v)或/与冲洗(p)步骤的吸附塔,随着m通道旋转阀与圆环形旋转托盘连续不断地旋转步进而进入均压升(er)及/或等待(-)步骤,从处于均压降(ed)步骤的吸附塔流出并经圆环形旋转托盘内置管道及m通道旋转阀均压降气(ed)通道而进入处于均压升(er)步骤的吸附塔进行均压,使得处于均压升(er)步骤的吸附塔内的压力与处于均压降(ed)步骤的吸附塔内的压力相等为止,结束均压升(er)或/与等待区(-)步骤的吸附塔,随着m通道旋转阀与圆环形旋转托盘进一步连续旋转而进入终充(fr)步骤,来自系统外的终充气(fr)流经m通道旋转阀终充气(fr)通道与圆环形旋转托盘内置管道进入吸附塔进行充压直至吸附塔内的压力达到吸附(a)步骤所需的吸附压力为止,即,吸附塔的操作经历了由吸附(a)-顺放(pp)/均压
降(ed)-逆放(d)/抽真空(v)-冲洗(p)-均压升(er)/等待(-)-终充(fr)步骤构成的吸附与解吸的循环过程,并准备下一轮吸附与解吸的循环操作,其中,每一个吸附塔或进行一个步骤或多个步骤且进行每一步骤,均通过旋转阀旋转方向及旋转速度(ω1)与圆环形旋转托盘旋转方向及旋转速度(ω2)之间的调控匹配,使得旋转中的m通道旋转阀中m个通道与圆环形旋转托盘旋转中的n个吸附塔吸附与解吸的循环操作中的时序表首尾连接成圆,并完整地形成变压吸附(psa)吸附与解吸过程的操作循环性,所有的物料气体及工艺气体被均匀交替地分布在系统中的m通道旋转阀中m个圆通道与圆环形旋转托盘中内置管道及各个吸附塔内,并将一个循环周期的变压吸附(psa)通过旋转的m通道旋转阀(ω1)与接通的相应旋转的圆环形旋转托盘(ω2)上吸附塔分别同时进行吸附与解吸过程中的各个步骤,进出吸附塔的工艺气体位置是通过旋转阀旋转方向及旋转速度(ω1)与圆环形旋转托盘旋转方向及旋转速度(ω2)匹配而不断地变化,使得每个吸附塔重复吸附与解吸步骤,相当于每个固定床吸附塔在m通道旋转阀与圆环形旋转托盘旋转的同时完成各自的吸附与解吸步骤,进而形成了“模拟旋转移动床”的变压吸附过程,由此,从含vocs尾气中获得的净化气(pg),其中的vocs浓度小于等于1ppmv,vocs脱除率或回收率大于等于98%。
8.进一步的,所述的一种vocs尾气的全温程模拟旋转移动床变压吸附净化与回收工艺,其特征在于,所述的m通道旋转阀及圆环形旋转托盘旋转方向及其调控其旋转速度(ω1与ω2)之间的调控匹配,包括,1)同向同步,顺时针或逆时针方向的同向旋转,且,ω1=ω2/≠0,2)同向异步,顺时针或逆时针方向的同向旋转,且,ω1>ω2或ω1<ω2或ω1≠0/ω2=0或ω1=0/ω2≠0,3)异向同步,顺时针/逆时针或逆时针/顺时针的异向旋转,且,ω1=ω2/≠0,4)异向异步,顺时针/逆时针或逆时针/顺时针的异向旋转,且,ω1>ω2或ω1<ω2或ω1≠0/ω2=0或ω1=0/ω2≠0,优选的,同向同步,顺时针或逆时针方向的同向旋转,且,ω1=ω2/≠0,与,同向异步中的顺时针或逆时针方向的同向旋转,且,ω1>0/ω2=0或ω1<ω2。
9.进一步的,所述的一种vocs尾气的全温程模拟旋转移动床变压吸附净化与回收工艺,其特征在于,所述的原料气(f),或为煤化工厂与炼化厂含以烃类为主要的vocs有源尾气包括催化干气、焦化干气、三顶瓦斯气、重整气、加氢尾气、psa解吸气、乙烯裂解尾气、油吸收尾气以及焦炉尾气,或为有机溶剂厂含有机物为主的vocs有源尾气包括苯及其衍生物、氯甲烷、氯乙烯、酮、醚、酯、酚、醇、酊及胺类在内的有机物尾气,或生物制药含vocs有源尾气包括苯及其衍生物、酯、胺、砜、酊及含二噁英、噁磋的臭气,或包括半导体、油漆、制鞋、电镀、印染、纺织行业在内的其它行业所产生的vocs尾气。
10.进一步的,所述的一种vocs尾气的全温程模拟旋转移动床变压吸附净化与回收工艺,其特征在于,所述的全温程模拟旋转移动床变压吸附(ftrsrmpsa)系统的实际操作温度的大小,在60~130℃范围内,取决于原料气中vocs含量的大小,其中,vocs含量大,操作温度就高,反之亦然,且,相应的多通道旋转阀及圆环形旋转托盘的旋转速度(ω1与/或ω2)变小。
11.进一步的,所述的一种vocs尾气的全温程模拟旋转移动床变压吸附净化与回收工艺,其特征在于,所述的ftrsrmpsa系统中的吸附与解吸的循环操作步骤,对于vocs回收工况而言,在吸附步骤完成后增设置换(dp)步骤,采用经增压至吸附压力的浓缩气(cg)作为置换气(dp)进行置换(dp),置换(dp)步骤的操作压力与温度,与吸附(a)步骤的操作压力与温度相同或接近,置换(dp)步骤产生的置换废气(dpw)经一次性吸附精脱后,或作为净化气
(pg)直接排放,或冲洗气(p),或终充气(fr)循环使用,置换(dp)步骤完成后,优选的,直接进行逆放(d)或抽真空(v)及/或冲洗(p),所获得的由逆放(d)或抽真空(v)及/或冲洗废气(pw)组成的解吸气(d)作为vocs浓缩气(cg)的浓度大于等于80~90%,回收率大于等于98%。
12.进一步的,所述的一种vocs尾气的全温程模拟旋转移动床变压吸附净化与回收工艺,其特征在于,所述的冲洗气(p),或来自系统内的处于顺放(pp)步骤流出的顺放气(pp),或来自系统外的净化气(pg),或循环气(cc),通过m通道旋转阀通道(槽道)中一个或多个的开孔实现分批次进行冲洗,开孔数至多为3个,对于脱除vocs的净化为主要目的而言,优选的,来自系统外的净化气(pg)作为冲洗气(p),对于vocs的回收为主要目的而言,优选的,来自系统内的顺放气(pp)或系统外的循环气(cc)作为冲洗气(p)。
13.进一步的,所述的一种vocs尾气的全温程模拟旋转移动床变压吸附净化与回收工艺,其特征在于,所述的逆放(d)步骤采用抽真空方式进行解吸,增设的真空泵,或与解吸气(d)流出m通道旋转阀的物流管道相连,或与圆环形旋转托盘上的吸附塔出口端连接的外置管道直接相连且在外置管道上设有控制阀门,优选的与圆环形旋转托盘上的吸附塔出口端连接的外置管道直接相连且在外置管道上设有控制阀门。
14.进一步的,所述的一种vocs尾气的全温程模拟旋转移动床变压吸附净化与回收工艺,其特征在于,所述的终充气(fr),或来自系统外的原料气(f),或净化气(pg),或循环气(cc),优选的采用原料气(f)或/及循环气(cc)作为终充气(fr)。
15.进一步的,所述的一种vocs尾气的全温程模拟旋转移动床变压吸附净化与回收工艺,其特征在于,所述的ftrsrmpsa系统的固定床吸附塔的高径比为2~5,吸附塔中装载有,或活性氧化铝,或活性炭,或分子筛,或碳分子筛,或高分子有机物或碳纤维或以硅酸盐纤维为基材制成的复合颗粒状吸附剂。优选的,含高硅的活性氧化铝、活性炭、硅铝比大于1的硅酸盐分子筛与碳分子筛组合的复合颗粒状吸附剂,或高分子有机物或碳纤维或以硅酸盐纤维(含氟化硅、陶瓷与玻璃纤维)为基材制成的复合吸附剂。
16.本发明的有益效果如下:1、通过本发明可以将传统的固定复合床层tsa、psa/ftrpsa的吸附与解吸循环操作模式模拟变成全温程旋转轮移动床psa工艺,获得比固定床层或典型的扇形吸附室旋转轮tsa、psa效率更高的vocs尾气的净化深度及回收率,突破了常规与固定吸附床层tsa、psa/ftrpsa工艺所具有显著的“纯度与收率呈反比关系”的技术限制,又大幅度降低了旋转轮tsa或psa工艺与装备制造复杂性及成本。
17.2、本发明通过对多通道旋转阀与圆环形旋转托盘的旋转方向与旋转速度(ω1与ω2)之间的调控匹配,能够在传统的固定床psa/ftrpsa工艺上实现多组合多步骤的吸附与解吸的psa循环操作,解决了传统的轴向流与径向流固定床psa/ftrpsa的vocs尾气净化的吸附周期长、仅适合单一或简单组分的净化脱除或回收、气流分布均匀的吸附床和快开闭与长寿命高稳定性阀门等有着严格要求的限制等问题,并能灵活地根据净化气的技术指标要求及应用场景,进行调节且含盖了变压吸附(psa)/全温程变压吸附(ftrpsa)、真空变压吸附(vsa)等典型的轴向流或径向流固定床psa工艺,以及典型的扇形吸附室旋转轮psa或快轮psa的移动床工艺等现有的移动床psa工艺。
18.3、本发明大幅度降低了传统的固定床psa/ftrpsa的vocs尾气的净化或回收装置的程序控制阀门及调节阀门的数量,并能有效地避免高浓度vocs组分在吸附剂上在较高解
吸再生温度下发生燃烧、吸附剂失火或粉化等所引起的安全隐患,进一步提高了操作运行的稳定性与安全性,相应地减少吸附剂装填量,使得轴向流固定床的高径比进一步减小,同时也减少了径向流固定床psa与快轮psa装置制造的复杂性并能替代国外进口,进一步降低了投资与生产成本。
19.4、本发明通过对操作温度/压力、吸附塔的高径比与所装填的吸附剂组合及多通道旋转阀与圆环形旋转托盘的旋转方向与旋转速度(ω1与ω2)之间的调控匹配来适应于含vocs尾气的原料气出现较大的波动工况,包括组分、浓度、压力、温度、流量等的波动,操作弹性较大,尤其是解决了在传统的固定床psa/ftrpsa工艺中突出存在的共吸附、竞争性吸附或深度吸附等技术性难题,并无需旋转轮psa工艺所需的昂贵的规整式吸附剂,使得vocs尾气的净化深度或回收率达到“双高”。
附图说明
20.图1为实施例1流程示意图。
21.图2为实施例3流程示意图。
具体实施方式
22.为了使本领域的技术人员更好地理解本发明,下面将结合本发明实施例中的附图对本发明实施例中的技术方案进行清楚、完整的描述。
23.实施例1如图1所示,本实施例提供一种vocs尾气的全温程模拟旋转移动床变压吸附净化与回收工艺及系统,其中,全温程模拟旋转移动床变压吸附(ftrsrmpsa)系统是由5(n=5)个高径比为2~3且装载有含5~7%氧化硅的活性氧化铝、大小孔混掺的活性炭、硅铝比大于1的沸石分子筛与碳分子筛的多种吸附剂组成的轴向流固定复合床层吸附塔,并安置在一个以旋转速度(ω2=600~900s)的圆环形旋转托盘上的吸附塔、有7(m=7)个通道并安置在圆环形旋转托盘中央的以旋转速度(ω1=600~900s)旋转的7通道旋转阀、7通道旋转阀与系统外物料气体进出的物料管道以及连接于经圆环形旋转托盘内置管道至吸附塔上下与7通道旋转阀进出口连接的工艺管道,以及相应的驱动圆环形旋转托盘及7通道旋转阀旋转方向及其调控其旋转速度(ω1与ω2)的驱动机构、加热器、冷却器、换热器、冷凝器、缓冲罐、真空泵、循环泵与鼓风机所构成而形成一个ftrsrmpsa系统,吸附塔进出口与旋转阀进出口连接的管道是通过预设在圆环形旋转托盘的内置管道相连形成工艺管道且与7通道旋转阀通道数相同,进出ftrsrmpsa系统物料气体的位置是7通道旋转阀旋转的通道加以分配来固定,其物料气体包括商用天然气为原料气(f)、净化气(pg)、以原料气(f)为终充气(fr)以及逆放气(d)、抽真空气(v)和冲洗废气(pw)组成的解吸气(d)作为浓缩气(cg)以及不凝气所形成的循环气(cc)为冲洗气(p),并相应的连接包括加热器、冷却器、换热器、缓冲罐(器)、冷凝器、真空泵、循环泵与鼓风机在内的设备,由7通道旋转阀进出口与5个吸附塔进出口之间通过圆环形旋转托盘中内置管道连接的工艺管道中工艺气体流动的位置是移动变化的,工艺气体是在ftrsrmpsa系统内流动,包括原料气(f)、来自系统外的循环气(cc)作为冲洗气(p)、逆放气(d)/抽真空气(v)与冲洗废气(pw)组成的解吸气(d)作为浓缩气(cg)、以原料气(f)为终充气(fr)以及净化气(pg)。
24.具体吸附与解吸的循环过程为,来自ftrsrmpsa系统外的炼化厂vocs尾气作为原
料气(f),其来自炼化厂催化裂解、焦化延迟、加氢等工艺过程中产生的含vocs饱和干气,其中,vocs主要成分为c5及c5以上的高烷烃类、苯、甲苯、二甲苯等以及少量的丁二烯、异丁烯、戊烯等烯烃,vocs总浓度为3%,温度为30~40℃,压力为0.1mpa,经鼓风机与加热器升温至60~90℃,直接从7通道旋转阀的原料气(f)通道进口进入并经7通道旋转阀中的原料气(f)通道(如m=1)及出口、圆环形旋转托盘内置管道及圆环形旋转托盘上对应的处于吸附状态的1个轴向流固定床吸附塔(如图1所示的吸附塔1,n=1)进口连接的工艺管道,从吸附塔底部进入进行吸附(a),吸附(a)步骤中的吸附压力为0.1~0.2mpa,吸附温度为60~90℃,经过7通道旋转阀旋转方向及旋转速度(ω1)与圆环形旋转托盘旋转方向及旋转速度(ω2)之间的调控匹配为,顺时针同向且ω1=ω2=600~900s的同向同步,并连续地步进,从处于吸附(a)步骤的吸附塔(n=1)顶部流出的非吸附相气体正好经工艺管道进入7通道旋转阀的净化气(pg)通道(如m=2),并从7通道旋转阀的净化气(pg)通道流出形成净化气(pg),其中的水、c
5+
的含量(露点降)为-65~-55℃,vocs组分的含量小于等于0.1~0.2ppmv,经与循环气(cc)热交换降温后进入净化气(pg)缓冲罐后,作为燃料气输出使用,随着7通道旋转阀与圆环形旋转托盘继续地同向同步的旋转步进,全部完成吸附(a)步骤后的吸附塔1同时也旋转至如图1所示的吸附塔2(n=2)的原先位置,进入逆放(d)步骤,吸附塔2也由如图1所示的初始位置旋转步进至图1所示的吸附塔3的初始位置上,而吸附塔3同时从其初始位置旋转步进至吸附塔4的初始位置上,吸附塔4步进移动至吸附塔5的初始位置,而吸附塔5步进移动至吸附塔1的初始位置,5个吸附塔在连续地旋转步进中进行各自相应的吸附与解吸的步骤,与此同时,吸附塔1进行逆放(d)步骤产生的逆放气(d)作为解吸气(d)流经圆环形旋转托盘内置管道及7通道旋转阀逆放气(d)通道(如m=3)及通道出口端与换热器进出口端换热降温后作为浓缩气(cg)进入浓缩气(cg)缓冲罐,并经过冷凝器冷凝,产生的冷凝液为c5及c5以上烃类(c
5+
)液体,作为轻质油或石化原料输出,其c
5+
浓度99%,收率99%,冷凝产生的不凝气体,作为循环气(cc),经循环泵输送并经与净化气(ng)及解吸气(d)热交换后,作为ftrsrmpsa系统的冲洗气(p)使用,结束逆放(d)步骤的吸附塔1随着7通道旋转阀与圆环形旋转托盘的同向同步地连续旋转步进至至如图1所示的吸附塔3(n=3)的原先位置进入抽真空(v)的解吸步骤,对应的其余4个吸附塔也依次旋转步进至各自新的位置进行各自相应的吸附与解吸步骤,抽真空(v)形成的解吸气(d)从吸附塔的出口端流出并流经与圆环形旋转托盘上的吸附塔出口连接的外置管道且在外置管道上设有真空泵及控制阀门控制流量后,经换热降温后作为浓缩气(cg)进入浓缩气(cg)缓冲罐,并经过冷凝器冷凝,产生的冷凝液为c5及c5以上烃类(c
5+
)液体,作为轻质油或石化原料输出,其c
5+
浓度为99%,收率为99%,冷凝产生的不凝气体,作为循环气(cc),经循环泵输送并经与净化气(ng)及解吸气(d)热交换后,作为ftrsrmpsa系统的冲洗气(p)使用,在抽真空(v)步骤中,最大真空度为-0.08mpa,相应的7通道旋转阀中的一个通道(如m=4)变为空道,结束逆放(d)步骤的吸附塔1随着7通道旋转阀与圆环形旋转托盘的同向同步地连续旋转步进,完成抽真空(v)步骤后的吸附塔1同时也旋转至如图1所示的吸附塔4(n=4)的原先位置进入冲洗(p)步骤,对应的其余4个吸附塔也依次旋转步进至各自新的位置进行各自相应的吸附与解吸步骤,采用经换热后的循环气(cc)作为冲洗气(p),流经7通道旋转阀中的冲洗气(p)通道(如m=5)及相应的圆环形旋转托盘内置管道与工艺管道进入吸附塔1进行冲洗(p),除了冲洗(p)还填充了吸附塔的真空状态,使得吸附塔回到常压或微正压状态,并且冲洗(p)步骤产生的冲洗废气(pw),从吸附塔1出口端
流出并流经相应的工艺管道及圆环形旋转托盘内置管道与7通道旋转阀的冲洗废气(pw)通道(如m=6)流出,一部分(冲洗前期)经换热冷却后作为浓缩气(cg)进入浓缩气(cg)缓冲罐,并经过冷凝器冷凝,进一步回收冲洗废气(pw)中的有效组分c
5+
,一部分(冲洗后期)经换热冷却后作为净化气(pg)而进入净化气(pg)缓冲罐使用,结束冲洗(p)步骤的吸附塔1,随着7通道旋转阀与圆环形旋转托盘继续同向同步地旋转步进至如图1所示的吸附塔5的初始位置而进入终充(fr)步骤,吸附塔2、3、4与5也依次旋转步进移动至相应的新位置进行各自的吸附与解吸步骤,原料气(f)作为终充气(fr)流经7通道旋转阀终充气(fr)通道(如m=7)与圆环形旋转托盘内置管道进入吸附塔1进行充压直至吸附塔内的压力达到吸附(a)步骤所需的吸附压力0.1~0.2mpa为止,并准备下一轮吸附与解吸的循环操作,其中,每一个吸附塔进行每一步骤或多个步骤,均通过7通道旋转阀旋转方向(顺时针)及旋转速度(ω1=600~900s)与圆环形旋转托盘旋转方向(顺时针)及旋转速度(ω2=600~900s)之间的同向同步的调控匹配,使得旋转中的7通道旋转阀中7个通道与圆环形旋转托盘旋转中的5个吸附塔吸附与解吸的循环操作中的时序表首尾连接成圆,并完整地形成变压吸附(psa)吸附与解吸过程的操作循环性,即,吸附(a)-逆放(d)-抽真空(v)-冲洗(p)-终充(fr),所有的物料气体及工艺气体被均匀交替地分布在系统中的7通道旋转阀中7个圆(槽)通道与相应的圆环形旋转托盘中内置管道及5个吸附塔内,并将一个循环周期的变压吸附(psa)通过旋转的7通道旋转阀(ω1)与接通的相应旋转的圆环形旋转托盘(ω2)上吸附塔分别同时进行吸附与解吸过程中的各个步骤,进出各个吸附塔的工艺气体位置是通过7通道旋转阀旋转方向及旋转速度(ω1)与圆环形旋转托盘旋转方向及旋转速度(ω2)同向同步的匹配而不断地变化,使得每个吸附塔均可重复吸附与解吸步骤,相当于每个固定床吸附塔在7通道旋转阀与圆环形旋转托盘同向同步旋转步进的同时完成各自的吸附与解吸步骤,进而形成了“模拟旋转移动床”的真空变压吸附(vsa5-1vd/p,即,5塔-1塔吸附-逆放、抽真空与冲洗解吸)过程,由此,从来自炼化厂含高浓度(3%)vocs(c
5+
为主)尾气中获得浓度为99%、收率为99%的c
5+
轻质油溶剂,并得到vocs含量小于等于0.1~0.2ppmv的净化气(pg)作为燃料气使用,vocs脱除率大于等于99%。
25.实施例2如图1所示,在实施例1的基础上,原料气进入ftrsrmpsa系统,其中,将系统中的圆环形旋转托盘的旋转速度ω2调整为0,即不转动,而7通道旋转阀旋转方向仍然维持在顺时针方向,其旋转速度ω1调整为ω1=300~600s的水平,5个吸附塔的位置固定,而通过7通道旋转阀定期顺时针旋转步进使得每个吸附塔均经历吸附(a)-逆放(d)-抽真空(v)-冲洗(p)-终充(fr)的吸附与解吸的循环操作步骤,其中,冲洗(p)步骤产生的冲洗废气(pw),小部分(约30~40%)作为浓缩气(cg)经换热降温进入浓缩气(cg)缓冲罐使用,大部分(约60~70%)直接返回到原料气(f)循环使用,所有的物料气体及工艺气体被均匀交替地分布在系统中的7通道旋转阀中7个圆(槽)通道与圆环形旋转托盘中内置管道及各个吸附塔内,并将一个循环周期的变压吸附(psa)通过旋转的7通道旋转阀(ω1)与接通的相应静止的圆环形旋转托盘(ω2=0)上吸附塔分别同时进行吸附与解吸过程中的各个步骤,进出吸附塔的工艺气体位置是通过7通道旋转阀旋转方向及旋转速度(ω1)而不断地变化,使得每个吸附塔重复吸附与解吸步骤,相当于每个固定床吸附塔在不旋转下随着7通道旋转阀旋转过程中完成各自的吸附与解吸步骤,进而形成了“模拟旋转移动床”的真空变压吸附(vsa)过程,由此,从来自炼化厂含高浓度(3%)vocs(c
5+
为主)尾气中获得浓度为98%、收率为
98%的c
5+
轻质油溶剂,并得到vocs含量小于等于1ppmv的净化气(pg)作为燃料气使用,vocs脱除率大于等于98%,相较于实施例1,由于圆环形旋转托盘静止不移动,即,吸附塔不转动,而7通道旋转阀旋转速度加快,以此来弥补圆环形旋转托盘上吸附塔不转动,但得到的净化气(pg)及回收的c
5+
轻质油溶剂的浓度与脱除率/(回)收率低于实施例1。
26.实施例3如图2所示,在实施例1与2基础上,原料气(f)是来自生物制药产生的含vocs有源尾气包括苯及其衍生物、酯醚醇胺等有机物以及含二噁英、噁磋的臭气组分,vocs浓度为0.1%,常压,温度为100~120℃,流量为5万方/小时,经输送泵输送进入全温程模拟旋转移动床变压吸附(ftrsrmpsa)系统,ftrsrmpsa系统是由3(n=3)个高径比为2~3且装载有含5~7%氧化硅的活性氧化铝、大小孔混掺的活性炭、硅铝比大于1的沸石分子筛与碳分子筛的多种吸附剂组成的轴向流固定复合床层吸附塔,直接安置在有4(m=4)个通道以旋转速度(ω1=1000~1400s)旋转的4通道旋转阀周围,并通过4通道旋转阀与系统外物料气体进出的物料管道以及连接于3个吸附塔上下与4通道旋转阀之间的工艺管道以及连接相应的驱动4通道旋转阀旋转方向及其调控其旋转速度(ω1)的驱动机构、输送泵、真空泵与焚烧炉工艺管道所构成而形成一个ftrsrmpsa系统,其中,取消了圆环形旋转托盘,即,ftrsrmpsa系统中的圆环形旋转托盘及其相应的驱动机构所调控的旋转速度(ω2)为零,4通道旋转阀旋转方向为顺时针,其旋转速度ω1调整为ω1=1000~1400s的水平,3吸附塔的位置固定的,而通过4通道旋转阀定期顺时针旋转步进使得每个吸附塔均经历吸附(a)-抽真空(v)-终充(fr)的吸附与解吸的循环操作步骤,所有的物料气体及工艺气体被均匀交替地分布在系统中的4通道旋转阀中4个圆(槽)通道与圆环形旋转托盘中内置管道及各个吸附塔内,并将一个循环周期的变压吸附(psa)通过旋转的4通道旋转阀(ω1)与接通的相应静止的吸附塔(ω2=0)分别同时进行吸附与解吸过程中的各个步骤,进出吸附塔的工艺气体位置是通过4通道旋转阀旋转方向及旋转速度(ω1)而不断地变化,使得每个吸附塔重复吸附与解吸步骤,相当于每个固定床吸附塔在不旋转下随着4通道旋转阀旋转过程中完成各自的吸附与解吸步骤,进而形成了“模拟旋转移动床”的真空变压吸附(vsa)过程,其中,4通道旋转阀中的4个圆(槽)通道的作用分别是,1个供原料气(f)、1个供净化气(pg)、1个供抽真空(v)步骤对应的空道与1个供原料气(f)为终充气(fr)使用,而终充(fr)步骤实际是预吸附,由此,从含稀浓度vocs的生物制药尾气脱除净化得到的净化气(pg)经过降温与过滤后直接作为排放气排放,其中的vocs含量小于0.1ppmv,满足大气排放标准,而从ftrsrmpsa系统中得到的抽真空(v)解吸气作为浓缩气(cg),vocs的浓度大于等于20~30%,经输送直接进入焚烧炉焚烧处理,产生的焚烧气经喷淋洗涤后直接排放,洗涤液进入生化污水处理站进行处理。
27.显而易见的,上面所述的实施例仅仅是本发明实施例中的一部分,而不是全部。基于本发明记载的实施例,本领域技术人员在不付出创造性劳动的情况下得到的其它所有实施例,或在本发明的启示下做出的结构变化,凡是与本发明具有相同或相近的技术方案,均落入本发明的保护范围之内。