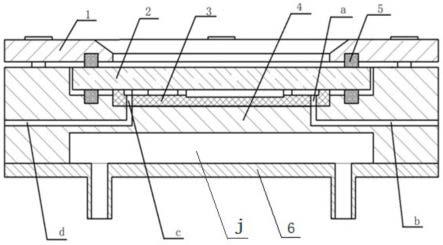
1.本发明属于化学反应设备技术领域,具体涉及到一种气固相连续光催化甲烷直接氧化制甲醇的反应器及方法。
背景技术:2.甲烷是天然气、页岩气、煤层气、可燃冰等含碳资源的主要成分,在世界范围内储量可观,除了被直接用作燃料之外,还可以作为原料来合成高附加值产品。甲醇是重要的基础化工原料,又可以作为清洁燃料,是甲烷转化的最理想产品,保留了甲烷的绝大部分能量。将甲烷转化合成甲醇,有利于实现甲烷资源的高效利用,同时解决了气态甲烷储存和输送成本高的问题,是天然气优化利用中极具吸引力的途径之一。
3.目前工业上通常采用甲烷间接合成甲醇法,即先由甲烷和水蒸气反应生成合成气,再由合成气生产甲醇,存在反应温度高,工艺流程长,能耗和设备投资均较大等缺点。甲烷直接氧化制甲醇可大幅缩短工艺流程,降低能耗。该技术主要面临两大难题:一是甲烷分子的碳氢键解离能很大(439.3kj/mol),活化困难;二是甲醇分子较活泼,容易被过度氧化为二氧化碳。因此高效活化甲烷并控制其氧化程度,抑制甲醇的过度氧化显得尤为重要。
4.光催化甲烷直接氧化为甲醇是理想的反应途径。与传统热催化反应相比,光催化反应从高能量的甲烷激发态出发,能够实现很多传统基态条件下无法自发进行的转化过程或降低催化反应所需要的温度,实现在温和条件下甲烷的转化,并减少副反应的发生。随着光催化甲烷制甲醇技术的发展,可分为气液固多相和气固相反应,多为间歇过程。迄今为止,鲜见关于气固相光催化甲烷直接氧化制甲醇反应的研究报道。
5.光反应器是光催化反应过程的核心设备,然而有关气固相光催化甲烷直接氧化制甲醇的反应器的开发严重滞后于光催化剂的研究和发展。目前,用于气固相光催化甲烷直接氧化制甲醇的反应器主要有流化床光反应器和固定床光反应器,存在以下问题:(1)流化床光反应器通过催化剂的悬浮分散提高了催化剂的有效利用面积,但催化剂回收和后处理较困难,重复使用性差,反应器内光分布不均匀。(2)固定床光反应器虽然解决了催化剂回收和重复使用的问题,但存在有效催化面积小、传质传热效率不高、床层温度不容易控制等缺点。(3)目前光反应器内的流体通道都处于常规尺度,不可避免地存在热质传递受限、光子传输受限、反应器体积大、处理量小等缺点。
技术实现要素:6.本发明所要解决的技术在于克服现有技术的缺点,提供一种设计合理、操作方便、催化剂容易卸载和回收、催化效率高的气固相连续光催化甲烷直接氧化制甲醇的反应器及方法。
7.解决上述技术问题所采用的技术方案是:一种气固相连续光催化甲烷直接氧化制甲醇的反应器,底板上设置有圆柱形的反应器主体,反应器主体底部设置有换热槽,底板上设置有与换热槽相连通的入口和出口,反应器主体中部设置有反应板,位于反应板上方反
应器主体上设置有透光片,反应板与透光片之间形成反应腔体,反应器主体上加工有与反应腔体相连通的进气通道和出气通道,位于透光片上方反应器主体上可拆卸连接有环形的盖板;所述反应板为反应板本体上表面上从一端到另一端依次加工有相连通的原料气混合槽、气体分布槽、反应通道区、气体收集槽,原料气混合槽底部加工有与进气通道相连通的第一通气孔,气体收集槽底部加工有与出气通道相连通的第二通气孔,原料气混合槽和气体分布槽及气体收集槽的深度相同,反应通道区由至少条反应通道组成,反应通道的底低于原料气混合槽的底形成催化剂装填区。
8.作为一种优选的技术方案,所述反应板的原料气混合槽是一长边为圆弧的长方形槽,所述气体分布槽是等腰梯形槽,所述气体收集槽是等腰三角形槽。
9.作为一种优选的技术方案,所述反应通道的宽度为0.5~3mm、深度为0.5~3mm。
10.作为一种优选的技术方案,所述反应通道的底比原料气混合槽e的底低0.1~1mm。
11.作为一种优选的技术方案,所述相邻两条反应通道之间的距离为1~3mm。
12.作为一种优选的技术方案,所述透光片分别与反应器主体和盖板之间均设置有密封圈。
13.作为一种优选的技术方案,所述的反应板用3d打印方法加工制成,材料为树脂或不锈钢或合金或聚合物材料。
14.一种用于气固相连续光催化甲烷直接氧化制甲醇的方法,包括以下步骤组成:
15.s1.将一定量催化剂粉末均匀地平铺于反应板上的催化剂装填区,用原位压制模具对催化剂粉末进行压制,将催化剂固定于催化剂装填区,压制后催化剂表面与原料气混合槽底面平齐;
16.s2.将反应板置于反应器主体中,在其上依次放置密封圈、透光片和盖板,并用螺栓进行紧固,保证反应腔体的密封性;
17.s3.将光源置于反应器上方,使光束垂直于透光片入射;向反应器主体中换热槽通入换热介质,控制反应体系的温度;
18.s4.在低温、常压的反应条件下,将甲烷和氧化气按照一定比例混合,由进气通道进入反应腔体内,流经反应通道区时,在光照下与催化剂接触并发生反应,反应后的混合气体由出气通道流出,经冷凝分离出甲醇,未反应的气体组分可循环至进气通道前,并与原料气混合后继续反应。
19.作为一种优选的技术方案,所述原位压制模具为基座上加工与反应通道相匹配的压条,压条的高度大于反应通道的深度、长度大于反应通道的长度。
20.作为一种优选的技术方案,所述原位压制模具用3d打印方法加工制成,材料为树脂或聚合物材料。
21.本发明的有益效果如下:
22.(1)本发明光反应器的通道尺度小,比表面积大,强化了光催化甲烷直接氧化制甲醇过程的传质传热,加快反应速率,及时移出甲烷氧化释放的热量,同时可以精确控制物料的停留时间,避免因温度过高、反应时间过长而使甲醇过度氧化产生副产物,提高了目的产物甲醇的选择性,同时提高了催化剂的稳定性和使用寿命;
23.(2)本发明可实现连续的气固相光催化甲烷直接氧化制甲醇反应;
24.(3)本发明光反应器的高径比小,光在传输过程中衰减少,且光在催化剂床层上的
分布均匀;
25.(4)可根据实际需要灵活更换反应板,调整反应板上各区域和反应通道的形状和尺寸。相比于传统催化剂装填法,“粉末装填-原位压片”的催化剂装填方法操作方便,且催化剂容易卸载和回收;
26.(5)本发明为组合式结构,易于拆卸清洗。
附图说明
27.图1是本发明气固相连续光催化甲烷直接氧化制甲醇的反应器的结构示意图。
28.图2是图1的爆炸示意图。
29.图3是图2中反应板3的结构示意图。
30.图4是原位压制模具7的结构示意图。
具体实施方式
31.下面结合附图和实施例对本发明进一步详细说明,但本发明不限于下述的实施方式。
32.在图1~3中,本实施例的气固相连续光催化甲烷直接氧化制甲醇的反应器由盖板1、透光片2、反应板3、反应器主体4、密封圈5、底板6连接构成,圆形的底板6上粘接有圆柱形的反应器主体4,反应器主体4底部加工有换热槽j,底板6上加工有与换热槽j相连通的入口和出口,反应过程中通过底板6上的入口和出口向换热槽j内通入热蒸汽或热水为反应提供合适的温度,反应器主体4中部安装有反应板3,反应板3为反应板3本体上表面上从一端到另一端依次加工有相连通的原料气混合槽e、气体分布槽f、反应通道g区、气体收集槽h,原料气混合槽e为一长边为圆弧的长方形槽,原料气混合槽e底部加工有与进气通道d相连通的第一通气孔c,气体分布槽f为等腰梯形槽,气体收集槽h是等腰三角形槽,气体收集槽h底部加工有与出气通道b相连通的第二通气孔a,原料气混合槽e和气体分布槽f及气体收集槽h的深度相同,反应通道g区由16条间距相等且相互平行的反应通道g组成,反应通道g的底低于原料气混合槽e的底形成催化剂装填区,相邻两反应通道g之间的距离为1.5mm,反应通道g的宽度为1.5mm、深度为2mm、长度为36mm,反应通道g的底比原料气混合槽e的底低0.7mm,反应板3用3d打印方法加工制成,位于反应板3上方反应器主体4上安装有透光片2,反应板3与透光片2之间形成反应腔体,反应器主体4上加工有进气通道d和出气通道b,进气通道d和出气通道b的直径均为2mm,进气通道d通过第一通气孔c与反应腔体相连通,出气通道b通过第二通气孔a与反应腔体相连通,位于透光片2上方反应器主体4上通过螺纹紧固件固定连接有环形的盖板1。本实施例盖板1、反应板3、反应器主体4和底板6的材质均为不锈钢。
33.本实施例所述反应器用于气固相连续光催化甲烷直接氧化制甲醇的方法,由以下步骤组成:
34.s1.将0.43g催化剂粉末均匀地平铺于反应板3上的催化剂装填区,用原位压制模具7对催化剂粉末进行压制,将催化剂固定于催化剂装填区,压制后催化剂表面与原料气混合槽e底面平齐;
35.催化剂为掺杂了pt的moo3/hzsm-5(n
pt
/n
mo
=0.02)分子筛基催化剂;
36.原位压制模具7为圆形基座上加工与反应通道g相匹配的压条,相邻两压条之间的距离为1.55mm,压条的高度为3mm、长度为40mm、宽度为1.45mm,原位压制模具7的材料为树脂,用3d打印方法加工制成,如图4;
37.s2.将反应板3置于反应器主体4中,在其上依次放置密封圈5、透光片2和盖板1,并用螺栓进行紧固,保证反应腔体的密封性;
38.s3.将氙灯光源置于反应器上方,使光束垂直于透光片2入射;向反应器主体4的换热槽j通入80℃循环水,控制反应体系的温度;
39.s4.将甲烷、氧气和氮气按照8:1:10的体积比混合,总流率为75ml/min,由进气通道d进入反应腔体内,流经反应通道g区时,在光照下与催化剂接触并发生反应,反应后的混合气体由出气通道b流出,经冷凝分离出甲醇,未反应的气体组分可循环至进气通道d前,并与原料气混合后继续反应。
40.连续反应1h后,出口气体经气相色谱仪检测,甲烷转化率为67%,甲醇选择性为95%。
41.实施例2
42.在本实施例中,反应板3为反应板3本体上表面上从一端到另一端依次加工有相连通的原料气混合槽e、气体分布槽f、反应通道g区、气体收集槽h,原料气混合槽e是一长边为圆弧的长方形槽,原料气混合槽e底部加工有与进气通道d相连通的第一通气孔c,气体分布槽f是等腰梯形槽,气体收集槽h是等腰三角形槽,气体收集槽h底部加工有与出气通道b相连通的第二通气孔a,原料气混合槽e和气体分布槽f及气体收集槽h的深度相同,反应通道g区由1条反应通道g构成,反应通道g的底低于原料气混合槽e的底形成催化剂装填区,反应通道g的宽度为3mm、深度为3mm、长度为30mm,反应通道g的底比原料气混合槽e的底低1mm,反应板3用3d打印方法加工制成,材料为聚四氟。其他零部件及零部件的连接关系与实施例1相同。
43.本实施例的原位压制模具7为圆形基座上加工与反应通道g相匹配的压条,压条的高度为4.5mm、长度为34mm、宽度为2.95mm,相邻两压条之间的距离为3.05mm,原位压制模具7的材料为树脂,用3d打印方法加工制成。
44.本实施例的反应器用于气固相连续光催化甲烷直接氧化制甲醇的方法与实施例1相同。
45.实施例3
46.在本实施例中,反应板3为反应板3本体上表面上从一端到另一端依次加工有相连通的原料气混合槽e、气体分布槽f、反应通道g区、气体收集槽h,原料气混合槽e是一长边为圆弧的长方形槽,原料气混合槽e底部加工有与进气通道d相连通的第一通气孔c,气体分布槽f是等腰梯形槽,气体收集槽h是等腰三角形槽,气体收集槽h底部加工有与出气通道b相连通的第二通气孔a,原料气混合槽e和气体分布槽f及气体收集槽h的深度相同,反应通道g区由30条反应通道g构成,反应通道g的底低于原料气混合槽e的底形成催化剂装填区,反应通道g的宽度为0.5mm、深度为0.5mm、长度为40mm,反应通道g的底比原料气混合槽e的底低0.1mm,反应板3用3d打印方法加工制成,材料为钛合金。其他零部件及零部件的连接关系与实施例1相同。
47.本实施例的原位压制模具7为圆形基座上加工与反应通道g相匹配的压条,压条的
高度为1mm、长度为44mm、宽度为0.45mm,相邻两压条之间的距离为0.55mm,原位压制模具7的材料为聚四氟,用3d打印方法加工制成。
48.本实施例的反应器用于气固相连续光催化甲烷直接氧化制甲醇的方法与实施例1相同。