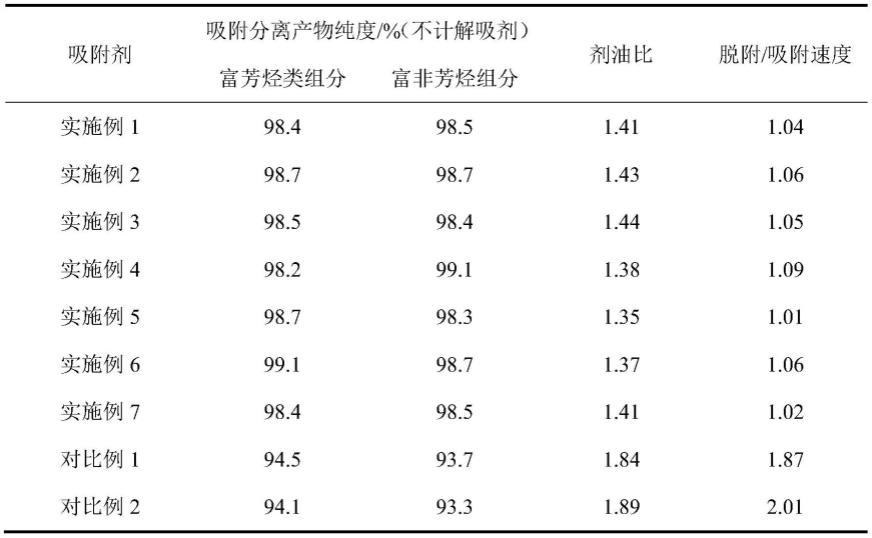
1.本发明涉及一种吸附分离汽柴油中芳烃的吸附剂及制备方法。
背景技术:2.经过近年来的持续发展,虽然我国炼化产业已成为国家经济命脉和安全的支柱产业,但面临产能过剩、产品同质化严重、企业发展创新不足、环保压力大和国外市场竞争严峻等诸多挑战,如何提质增效、增产高化工品、实现企业可持续发展,已成为炼化企业亟待解决的问题。“宜油则油、宜烯则烯、宜芳则芳”成为各大炼化企业追求的目标,但总体技术水平仍然不高,创新能力差,产品技术含量和附加值偏低,没有真正实现油品价值的最大化和合理利用。
3.通过模拟移动床(smb)对汽柴油进行吸附分离,得到高纯度芳烃和高纯度非芳烃组分,可以实现汽柴油组分的分子管理,更有针对性的应对市场需求变化,后续可耦合芳烃、非芳烃转化工艺,实现汽柴油向化工品的定向转化,提高经济效益。smb吸附分离工艺需要一定尺寸范围的球形颗粒吸附剂,成型后的吸附剂,含有大量粘结剂,会产生吸附容量小、吸附速率低、吸附效果差的问题。
4.专利cn106140078b公开了一种双金属芳烃吸附剂的制备方法,以硅酸钠、无机酸、去离子水和金属盐为原料制得的双金属芳烃吸附剂为球形颗粒,金属包括碱土金属和过渡金属,能够有效吸附溶剂油中的芳烃,芳烃脱除率大于95%,适用于高沸点溶剂油芳烃吸附分离。专利cn105536695b公开了一种吸附分离多环芳烃的吸附剂及制备方法,吸附剂由y分子筛载体以及按特定顺序交换在y分子筛载体上的金属离子组成,该吸附剂对多环芳烃具有较强的吸附能力,能有效的吸附分离柴油中的多环芳烃,脱除率可达到80%。专利cn105289466b公开了一种吸附分离柴油中多环芳烃的吸附剂及制备方法,吸附剂包含可调变孔径的硅胶或负载金属的改性硅胶,负载金属为cu、ni、al、fe、co、cr、ba、ag中一种或几种,对柴油中的多环芳烃具有较强的吸附能力,选择性较高,吸附剂可再生反复使用。
5.上述芳烃吸附剂的专利主要解决了芳烃吸附分离纯度的问题,但吸附分离解吸剂用量较大,芳烃脱附速度慢,吸附分离能耗高,会降低工业应用装置的经济效益。
技术实现要素:6.本发明所要解决的技术问题是芳烃在吸附剂中脱附速度慢,汽柴油芳烃吸附剂在应用过程中解吸剂用量大,分离能耗高,提供一种吸附分离汽柴油中芳烃的吸附剂及制备方法,该吸附剂具有高连通性氧化硅-金属氧化物骨架的芳烃吸附活性中心,在吸附分离汽柴油中芳烃的应用,剂油比(解吸剂/原料油)小于1.5,脱附/吸附速度小于1.2。
7.为解决上述技术问题,本发明通过以下技术方案来实现:
8.本发明提供了一种吸附分离汽柴油中芳烃的吸附剂的制备方法,该制备方法包括以下步骤:
9.1)以硅酸钠、金属盐及无机酸为原料合成氧化物凝胶,调节ph=5-12,然后进行过
滤、洗涤,再加入有机无机复合碱溶液中,调节ph值大于10,加热搅拌至溶解,团聚金属解聚,金属原子与硅原子重新配位,得到高分散金属氧化物溶胶;
10.2)将上述高分散金属氧化物溶胶与有机无机复合酸混合,调节ph值小于2.5,提高氧化硅-金属氧化物骨架连通性,然后升温老化得到活性氧化物凝胶;
11.3)将上述活性氧化物凝胶经过滤、洗涤、烘干、焙烧得到所述吸附分离汽柴油中芳烃的吸附剂;
12.所述吸附剂由活性氧化物组成,包括活性氧化硅和高分散金属氧化物,所述金属氧化物质量含量为0.5%-50%,所述金属氧化物为氧化锗、氧化锡、氧化钛、氧化锆、氧化锰、氧化钒中一种。
13.上述吸附剂的制备方法技术方案中,步骤1)所述的硅酸钠中二氧化硅质量分数为5-30%;所述金属盐为氯化锗、氯化锡、硫酸亚锡、氯化钛、硝酸钛、硫酸钛、氯化锆、硝酸锆、硫酸锆中一种;所述无机酸为盐酸、硝酸、硫酸、磷酸中一种,质量分数为5-20%;所述有机无机复合碱质量分数为5-20%,无机碱为氢氧化钠、氢氧化钾中一种,有机碱为三乙胺、正丁胺中一种,质量比无机碱:有机碱=1:(0.1-5),所述加热温度优选为50-100℃。
14.本发明所述的芳烃吸附制备方法中,步骤2)所述有机无机复合酸质量分数为5-20%,无机酸为盐酸、硝酸、硫酸、磷酸中一种,有机酸为乙酸、丙酸中一种,质量比无机酸:有机碱=1:(0.1-5),所述老化温度为20-80℃,老化时间1-20h。
15.本发明还提供了一种上述的制备方法得到吸附分离汽柴油中芳烃的吸附剂。
16.进一步,本发明还提供了上述吸附剂在吸附分离汽柴油中芳烃工艺中的应用。其中所述的吸附分离汽柴油中芳烃工艺优选为固定床吸附分离工艺、多塔并联吸附分离工艺、模拟移动床吸附分离工艺。
17.本发明吸附剂在吸附分离汽柴油中芳烃的应用中,所述模拟移动床吸附分离工艺为逆流模拟移动床吸附分离工艺,吸附床层为8-24层,优选8-16层,吸附分离温度为40-120℃,优选50-80℃,解吸剂为烷烃和芳烃的混合物,优选甲基环己烷和甲苯,其中甲苯质量分数为10%-50%。
18.本发明吸附剂在吸附分离汽柴油中芳烃的应用中,优选用于所述模拟移动床吸附分离汽柴油中芳烃工艺,产物芳烃组分纯度大于98%,非芳烃组分纯度大于98%,剂油比小于1.5,脱附/吸附速度小于1.2。
19.本发明的有益效果:通过本发明吸附剂在吸附分离汽柴油中芳烃的应用,分离能耗根据剂油比降低幅度计算,较常规金属改性氧化硅吸附剂降低20%。
具体实施方式
20.下面结合实施例对本发明技术方案作进一步说明,但并非仅限于这些例子。
21.实施例中吸附剂的评价性能数据的测定方法为:以汽柴油为原料,该馏分段芳烃含量为15-70%。将吸附剂装入模拟移动床中,芳烃吸附分离为逆流模拟移动床吸附分离工艺,吸附床层为8-24层,优选8-16层,吸附分离温度为40-120℃,优选50-80℃,解吸剂为烷烃和芳烃的混合物,优选甲基环己烷和甲苯,其中甲苯质量分数为10%-50%。从模拟移动床采出两股物料,一股物料为富含芳烃组分,另一股物料为富非芳烃组分,分析两股物料纯度及解吸比。
22.实施例1
23.(1)形成高分散金属氧化物溶胶:配制10kg质量分数为12%的硅酸钠溶液和适量质量分数为15%的稀硫酸溶液,将14.8g氯化锗溶解至稀硫酸溶液中,然后将稀硫酸溶液缓慢加入硅酸钠溶液中,加入过程中剧烈搅拌,调节ph值至7然后进行过滤-洗涤的到滤饼,再将滤饼与质量分数为5%的氢氧化钠-三乙胺复合碱溶液混合,其中,质量比氢氧化钠:三乙胺=1:2,调节ph值>10,升温至50℃,搅拌溶解,得到高分散金属氧化物溶胶。
24.(2)形成活性氧化硅凝胶;配置适量质量分数为5%的硫酸-乙酸复合酸溶液,其中,质量比硫酸:乙酸=1:5,与步骤(1)得到的高分散金属氧化物溶胶混合,调节ph值<2.5,升温至50℃,搅拌老化12h,得到活性氧化硅凝胶。
25.(3)将步骤(2)得到的活性氧化物凝胶经过滤、洗涤、150℃烘干12h、550℃焙烧4h,得到吸附分离汽柴油中芳烃的吸附剂。
26.(4)吸附剂评价:以加氢催化柴油为原料,芳烃组分质量分数为30.5%,将吸附剂装入模拟移动床中,芳烃吸附分离为逆流模拟移动床吸附分离工艺,吸附床层为12层,吸附分离温度为60℃,解吸剂甲基环己烷和甲苯,其中甲苯质量分数为20%。从模拟移动床采出两股物料,一股物料为富含芳烃组分,另一股物料为富含非芳烃组分,分析两股物料纯度及剂油比。评价结果见表1所示。
27.实施例2
28.(1)形成高分散金属氧化物溶胶:配制10kg质量分数为12%的硅酸钠溶液和适量质量分数为15%的稀盐酸溶液,将207.4g氯化锡溶解至稀盐酸溶液中,然后将稀盐酸溶液缓慢加入硅酸钠溶液中,加入过程中剧烈搅拌,调节ph值至8,然后进行过滤-洗涤的到滤饼,再将滤饼与质量分数为10%的氢氧化钠-正丁胺复合碱溶液混合,其中,质量比氢氧化钠:正丁胺=1:0.1,调节ph值>10,升温至80℃,搅拌溶解,得到高分散金属氧化物溶胶。
29.(2)形成活性氧化硅凝胶;配置适量质量分数为10%的盐酸-乙酸复合酸溶液,其中,质量比盐酸:乙酸=1:0.1,与步骤(1)得到的高分散金属氧化物溶胶混合,调节ph值<2.5,升温至80℃,搅拌老化1h,得到活性氧化硅凝胶。
30.(3)将步骤(2)得到的活性氧化物凝胶经过滤、洗涤、120℃烘干12h、500℃焙烧6h,得到吸附分离汽柴油中芳烃的吸附剂。
31.(4)吸附剂评价:与实施例1相同。
32.实施例3
33.(1)形成高分散金属氧化物溶胶:配制10kg质量分数为12%的硅酸钠溶液和适量质量分数为15%的稀硝酸溶液,将170.9g硫酸亚锡溶解至稀硝酸溶液中,然后将稀硝酸溶液缓慢加入硅酸钠溶液中,加入过程中剧烈搅拌,调节ph值至10,然后进行过滤-洗涤的到滤饼,再将滤饼与质量分数为15%的氢氧化钾-三乙胺复合碱溶液混合,其中,质量比氢氧化钾:三乙胺=1:5,调节ph值>10,升温至80℃,搅拌溶解,得到高分散金属氧化物溶胶。
34.(2)形成活性氧化硅凝胶;配置适量质量分数为10%的硝酸-丙酸复合酸溶液,其中,质量比硝酸:丙酸=1:1,与步骤(1)得到的高分散金属氧化物溶胶混合,调节ph值<2.5,将温度调至20℃,搅拌老化24h,得到活性氧化硅凝胶。
35.(3)将步骤(2)得到的活性氧化物凝胶经过滤、洗涤、150℃烘干12h、550℃焙烧4h,得到吸附分离汽柴油中芳烃的吸附剂。
36.(4)吸附剂评价:与实施例1相同。
37.实施例4
38.(1)形成高分散金属氧化物溶胶:配制10kg质量分数为12%的硅酸钠溶液和适量质量分数为15%的稀磷酸溶液,将853.6g氯化钛溶解至稀磷酸溶液中,然后将稀磷酸溶液缓慢加入硅酸钠溶液中,加入过程中剧烈搅拌,调节ph值至6,然后进行过滤-洗涤的到滤饼,再将滤饼与质量分数为20%的氢氧化钾-正丁胺复合碱溶液混合,其中,质量比氢氧化钾:正丁胺=1:1,调节ph值>10,升温至100℃,搅拌溶解,得到高分散金属氧化物溶胶。
39.(2)形成活性氧化硅凝胶;配置适量质量分数为20%的磷酸-乙酸复合酸溶液,其中,质量比磷酸:乙酸=1:1,与步骤(1)得到的高分散金属氧化物溶胶混合,调节ph值<2.5,将温度调至80℃,搅拌老化6h,得到活性氧化硅凝胶。
40.(3)将步骤(2)得到的活性氧化物凝胶经过滤、洗涤、150℃烘干12h、550℃焙烧4h,得到吸附分离汽柴油中芳烃的吸附剂。
41.(4)吸附剂评价:与实施例1相同。
42.实施例5
43.(1)形成高分散金属氧化物溶胶:配制10kg质量分数为12%的硅酸钠溶液和适量质量分数为15%的稀硫酸溶液,将1.8kg硫酸钛溶解至稀硫酸溶液中,然后将稀硫酸溶液缓慢加入硅酸钠溶液中,加入过程中剧烈搅拌,调节ph值至7,然后进行过滤-洗涤的到滤饼,再将滤饼与质量分数为20%的氢氧化钠-正丁胺复合碱溶液混合,其中,质量比氢氧化钠:正丁胺=1:0.5,调节ph值>10,升温至100℃,搅拌溶解,得到高分散金属氧化物溶胶。
44.(2)形成活性氧化硅凝胶;配置适量质量分数为20%的硫酸-丙酸复合酸溶液,其中,质量比硫酸:丙酸=1:5,与步骤(1)得到的高分散金属氧化物溶胶混合,调节ph值<2.5,将温度调至80℃,搅拌老化12h,得到活性氧化硅凝胶。
45.(3)将步骤(2)得到的活性氧化物凝胶经过滤、洗涤、120℃烘干12h、500℃焙烧8h,得到吸附分离汽柴油中芳烃的吸附剂。
46.(4)吸附剂评价:与实施例1相同。
47.实施例6
48.(1)形成高分散金属氧化物溶胶:配制10kg质量分数为12%的硅酸钠溶液和适量质量分数为15%的稀硫酸溶液,将276.9g硫酸锆溶解至稀硫酸溶液中,然后将稀硫酸溶液缓慢加入硅酸钠溶液中,加入过程中剧烈搅拌,调节ph值至10,然后进行过滤-洗涤的到滤饼,再将滤饼与质量分数为10%的氢氧化钠-正丁胺复合碱溶液混合,其中,质量比氢氧化钠:正丁胺=1:0.5,调节ph值>10,升温至80℃,搅拌溶解,得到高分散金属氧化物溶胶。
49.(2)形成活性氧化硅凝胶;配置适量质量分数为10%的硫酸-丙酸复合酸溶液,其中,质量比硫酸:丙酸=1:0.1,与步骤(1)得到的高分散金属氧化物溶胶混合,调节ph值<2.5,将温度调至60℃,搅拌老化12h,得到活性氧化硅凝胶。
50.(3)将步骤(2)得到的活性氧化物凝胶经过滤、洗涤、120℃烘干12h、500℃焙烧4h,得到吸附分离汽柴油中芳烃的吸附剂。
51.(4)吸附剂评价:与实施例1相同。
52.实施例7
53.(1)形成高分散金属氧化物溶胶:配制10kg质量分数为12%的硅酸钠溶液和适量
质量分数为15%的稀硫酸溶液,将418.2g硝酸锆溶解至稀硫酸溶液中,然后将稀硫酸溶液缓慢加入硅酸钠溶液中,加入过程中剧烈搅拌,调节ph值至10,然后进行过滤-洗涤的到滤饼,再将滤饼与质量分数为10%的氢氧化钠-正丁胺复合碱溶液混合,其中,质量比氢氧化钠:正丁胺=1:0.5,调节ph值>10,升温至80℃,搅拌溶解,得到高分散金属氧化物溶胶。
54.(2)形成活性氧化硅凝胶;配置适量质量分数为10%的硫酸-乙酸复合酸溶液,其中,质量比硫酸:乙酸=1:2,与步骤(1)得到的高分散金属氧化物溶胶混合,调节ph值<2.5,将温度调至60℃,搅拌老化12h,得到活性氧化硅凝胶。
55.(3)将步骤(2)得到的活性氧化物凝胶经过滤、洗涤、120℃烘干24h、600℃焙烧4h,得到吸附分离汽柴油中芳烃的吸附剂。
56.(4)吸附剂评价:与实施例1相同。
57.对比例1
58.采用金属盐浸渍负载方式制备的氧化硅吸附剂,金属负载量与实施例1相同,吸附剂评价与实施例1相同。
59.对比例2
60.采用金属盐浸渍负载方式制备的氧化硅吸附剂,金属负载量与实施例2相同,吸附剂评价与实施例1相同。
61.表1吸附剂评价结果
62.