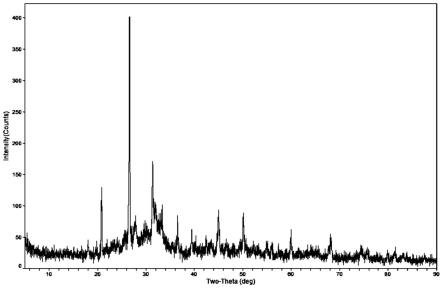
1.本发明涉及污泥资源化利用技术领域,尤其是涉及一种氰化氢脱除催化剂及其制备方法。
背景技术:2.随着污水处理规模的高速增长,我国污水污泥产量已超过3000万吨/年,亟需开发污泥安全处理处置与资源化利用技术。目前,污水污泥的处置方法包括厌氧发酵、焚烧、热解等,其中热解可获得中热值燃气和油、以及低重金属浸出毒性的热解炭,在实现高效安全处置的同时实现资源化利用。污泥氮含量较高,热解产生的挥发分中存在较多的hcn和nh3。当挥发分冷却后,这两种气体会富集在热解液的水相中。对热解液进行油水分离,分离出的废水中不仅会富集氨氮,还将存在剧毒且处理难度更大的cn-,带来较高处置成本和环境风险。
3.现有技术仅仅将氰离子从气相转移至洗涤液中,而洗涤液再生分离出的hcn还将带来后续处理问题。因此,亟需一种能够有效处理污泥热解过程中产生的氰化氢的方法。
技术实现要素:4.本发明的目的就是为了克服上述现有技术存在的缺陷而提供一种氰化氢脱除催化剂及其制备方法,制备得到的催化剂可以直接催化脱除污泥热解挥发分中的hcn,避免污泥热解挥发分冷凝后对其中hcn的二次处理,且对污泥热解挥发分中hcn的去除率达到为98%以上。
5.申请人对污泥热解的含氮污染物析出规律的前期研究中,发现污泥热解气中hcn的析出率达到3130mg/kg,折算到热解液中的cn-浓度达到10624mg/l,远超炼焦行业废水排放的限值。目前煤化工行业普遍采用真空碳酸盐法、as循环洗涤法等方法对焦炉煤气中的hcn进行脱除,但这些方法仅仅将氰离子从气相转移至洗涤液中,而洗涤液再生分离出的hcn还将带来后续处理问题。
6.本发明的目的可以通过以下技术方案来实现:
7.本发明的第一个目的是保护一种氰化氢脱除催化剂的制备方法,所述制备方法包括以下步骤:
8.s1:将氧化钙与湿污泥混合,经干化,粉碎、过筛后,得到半干污泥或干污泥;
9.s2:将半干污泥或干污泥送入热解反应器热解,得到热解半焦和热解挥发分,取其中所述热解半焦作为脱除氰化氢的催化剂。
10.进一步地,从s1中所述湿污泥原料中取样,经烘干、粉碎后得到干基污泥样品,并通过烘干过程的失重得到湿污泥的含水率m;
11.对干基污泥样品进行xrf分析,测得干污泥中磷、硅、硫、钙的质量分数ω(p)、ω(si)、ω(s)、ω(fe)、ω(ca);
12.s1中加入氧化钙的质量相对湿污泥质量的比例ω(cao-add)的范围为:
13.[ω(p)/31+ω(si)/28+ω(s)/32-ω(fe)/56-ω(ca)/40]
×
56/40
×
(1-m)《ω(cao-add)《[ω(p)/31+ω(si)/28+ω(s)/32+3
×
ω(fe)/56-ω(ca)/40]
×
56/40
×
(1-m)。
[0014]
进一步地,s1中加入氧化钙的质量相对湿污泥质量的比例ω(cao-add)的范围为:
[0015]
[ω(p)/31+ω(si)/28+ω(s)/32-ω(ca)/40]
×
56/40
×
(1-m)《ω(cao-add)《[ω(p)/31+ω(si)/28+ω(s)/32+2
×
ω(fe)/56-ω(ca)/40]
×
56/40
×
(1-m)。
[0016]
进一步地,s1中,所述湿污泥为来自污水处理厂经脱水后含水率70-90%的剩余污泥,优选含水率在75-85%之间的脱水污泥。
[0017]
进一步地,s1中,所述半干污泥含水率为30-50%,所述干污泥含水率为0-30%。
[0018]
进一步地,s1中,加入氧化钙的量为湿污泥质量的4.0%。
[0019]
进一步地,s1、s2中,得到的为半干污泥时,通过柱塞泵或螺杆泵将半干污泥送至热解反应器中;
[0020]
得到的为干污泥时,先将干污泥经粉碎、过筛,得到粒径在100mm以下的干污泥颗粒,之后将干污泥颗粒通过皮带输送机送入热解反应器中。
[0021]
进一步地,s2中,所述热解反应器为流化床反应器、螺旋推进反应器、回转窑中的一种,优选螺旋推进反应器和回转窑。
[0022]
进一步地,s2中,热解反应器的加热速率为10℃/min-100℃/s,优选50℃/min-10℃/s,加热终温650-850℃,优选700-800℃,在终温的停留时间为0-1h,优选5min-40min。
[0023]
进一步地,制备方法可具体为:加入相对湿污泥质量4%的氧化钙与含水80%的湿污泥混合,经干化后含水率为0%的污泥经粉碎、过筛后,获得粒径在100mm以下的干污泥颗粒,送入回转窑热解反应器中加热,加热速率为100℃/min,加热终温为750℃,在终温停留时间30min,热解半焦冷却后即获得脱hcn催化剂。该催化剂的单位质量铁的饱和磁化强度48.6amu/g且xrd图谱中具有在衍射角2θ=33.4
°
处的峰。
[0024]
本发明的第二个目的是提供一种通过上述制备方法得到的氰化氢脱除催化剂,所述氰化氢脱除催化剂的单位质量铁的饱和磁化强度》40amu/g。
[0025]
进一步地,所述催化剂的xrd图谱中具有在衍射角2θ=33.4
±
0.1
°
处的峰。
[0026]
与现有技术相比,本发明具有以下技术优势:
[0027]
使用该催化剂可以直接催化脱除污泥热解挥发分中的hcn,避免污泥热解挥发分冷凝后对其中hcn的二次处理,且对污泥热解挥发分中hcn的去除率达到为98%以上,挥发分冷凝后所得热解液中cn-的含量低至0.2mg/l。
附图说明
[0028]
图1为实施例2所得热解半焦的xrd图谱。
[0029]
图2为热解反应的反应产物说明图。
具体实施方式
[0030]
下面结合附图和具体实施例对本发明进行详细说明。本技术方案中如未明确说明的制备手段、材料、结构或组成配比等特征,均视为现有技术中公开的常见技术特征。
[0031]
实施例1
[0032]
湿污泥原料中取样,经烘干、粉碎后得到干污泥样品,对干燥前后的样品称重,得
到湿污泥含水率为80%。对干污泥进行xrf分析,测得干污泥中磷、硅、硫、钙的质量分数ω(p)、ω(si)、ω(s)、ω(fe)、ω(ca)。
[0033]
经xrf测得主要无机成分的元素含量如下(单位:%)
[0034][0035]
本实施例中制备方法具体为:s1:将氧化钙与湿污泥混合,经干化,粉碎、过筛后,得到半干污泥或干污泥;s2:将半干污泥或干污泥送入热解反应器热解,得到热解半焦和热解挥发分,取其中所述热解半焦作为脱除氰化氢的催化剂。
[0036]
实施例中可采用,如下具体实施方式:从s1中所述湿污泥原料中取样,经烘干、粉碎后得到干基污泥样品,并通过烘干过程的失重得到湿污泥的含水率m;
[0037]
对干基污泥样品进行xrf分析,测得干污泥中磷、硅、硫、钙的质量分数ω(p)、ω(si)、ω(s)、ω(fe)、ω(ca);s1中加入氧化钙的质量相对湿污泥质量的比例ω(cao-add)的范围为:
[0038]
[ω(p)/31+ω(si)/28+ω(s)/32-ω(fe)/56-ω(ca)/40]
×
56/40
×
(1-m)《ω(cao-add)《[ω(p)/31+ω(si)/28+ω(s)/32+3
×
ω(fe)/56-ω(ca)/40]
×
56/40
×
(1-m)。
[0039]
为了实现更好的效果,可采取s1中加入氧化钙的质量相对湿污泥质量的比例ω(cao-add)的范围为:
[0040]
[ω(p)/31+ω(si)/28+ω(s)/32-ω(ca)/40]
×
56/40
×
(1-m)《ω(cao-add)《[ω(p)/31+ω(si)/28+ω(s)/32+2
×
ω(fe)/56-ω(ca)/40]
×
56/40
×
(1-m)。
[0041]
实施例2
[0042]
按实施例1的方法,将氧化钙与含水率80%的湿污泥混合,其中氧化钙的质量为湿污泥质量的4.0%,经干化后得到含水率为0的干污泥,经粉碎、过筛后,获得粒径在100mm以下的干污泥颗粒,送入回转窑热解反应器中加热。加热速率为100℃/min。加热终温为750℃,在终温停留时间30min。热解半焦冷却后即获得脱hcn催化剂。图1参见图1,该催化剂的单位质量铁的饱和磁化强度48.6amu/g且xrd图谱中具有在衍射角2θ=33.4
°
处的峰。
[0043]
实施例3
[0044]
按实施例1的方法,将氧化钙与含水率80%的湿污泥混合,其中氧化钙的质量为湿污泥质量的6.1%。经干化后得到含水率为10%的干污泥。经粉碎、过筛后,获得粒径在100mm以下的干污泥颗粒,送入回转窑热解反应器中加热。加热速率为100℃/min。加热终温为750℃,在终温停留时间15min。热解半焦冷却后即获得脱hcn催化剂。该催化剂的单位质量铁的饱和磁化强度52.4amu/g且xrd图谱中具有在衍射角2θ=33.4
°
处的峰。
[0045]
实施例4
[0046]
按实施例1的方法,将氧化钙与含水率80%的湿污泥混合,其中氧化钙的质量为湿污泥质量的2.7%。干化后含水率为40%的半干污泥,经粉碎、过筛后,获得粒径在100mm以下的干污泥颗粒,送入螺旋热解反应器中加热。加热速率为100℃/min。加热终温为750℃,在终温停留时间15min。热解半焦冷却后即获得脱hcn催化剂。该催化剂的单位质量铁的饱和磁化强度40.7amu/g且xrd图谱中具有在衍射角2θ=33.4
°
处的峰。
[0047]
实施例5
[0048]
如附图2所示,将污泥热解反应器与催化反应器相连接,将实施例2-4制得的热解
半焦催化剂50g置于催化反应器中,催化反应器温度为750℃。在热解反应器1中投入待处理市政污泥1kg,热解温度设为750℃,将热解反应器中污泥热解产生的高温挥发分经路径通入催化反应器中,反应空速为3000h-1
。将经催化剂后的挥发分通入冷凝器,得到不凝气和热解液,将热解液通过油水分离器分离,得到水相和油相,采用离子选择电极测量水相中cn-1
的浓度。为对比催化剂对hcn的分解效果,直接将热解反应器产生的挥发分经过路径b通入冷凝器、分离处不凝气后将热解液通入油水分离器分离,得到油相和水相,采用离子选择电极测量水相中cn-1
的浓度。结果如下表。
[0049]
样品实施例2实施例3实施例4不经催化反应的(路径b)水相质量(g)130130130不经催化反应的(路径b)水相cn-1
的浓度(mg/l)950095009500经催化反应的(路径a)水相质量(g)10010399经催化反应的(路径a)水相cn-1
的浓度(mg/l)0.130.100.15
[0050]
上述的对实施例的描述是为便于该技术领域的普通技术人员能理解和使用发明。熟悉本领域技术的人员显然可以容易地对这些实施例做出各种修改,并把在此说明的一般原理应用到其他实施例中而不必经过创造性的劳动。因此,本发明不限于上述实施例,本领域技术人员根据本发明的揭示,不脱离本发明范畴所做出的改进和修改都应该在本发明的保护范围之内。